3D printer barrie
3D Printing Service Barrie | Instant Quotes Online
Our 3D printing capabilities
We have over 90 3D printing shops in our network and are well known for manufacturing high-quality parts at competitive prices, from rapid prototyping with Fused Deposition Modeling (FDM) to functional end parts made with Selective Laser Sintering (SLS) or Multi Jet Fusion (MJF).
Gallery of 3D printed parts manufactured by Hubs
With over 65,000 customers from every industry, including aerospace, defense, robotics, medical, machinery, automotive and electronics, we have extensive experience meeting a diverse range of 3D printing requirements, from prototyping to production: Visual aids, concept models, injection-molding prototypes, form-fit & function prototypes, tooling and casting patterns, jigs, grips and fixtures, and durable end parts.
HP PA 12 - Dyed Black
Customer | True North Design |
Purpose | Structural and vacuum EOAT components |
Process | SLS / MJF |
Unit price | $69. |
Industry | Automotive |
Prototyping PLA
Customer | Allision Conner |
Purpose | End caps and cable strain relief for sheet metal enclosure |
Process | FDM |
Unit price | $7.92 / $4.72 / $2.80 |
Industry | Industrial Automation |
HP PA 12
Customer | US Hammer |
Description | A part for gasoline engine powered jackhammers |
Process | MJF |
Unit price | $22.18 |
Industry | Construction |
Markforged Onyx - Black
Customer | Autocom Manufacturing |
Purpose | A production part for 3D printed lathe gantry gripper fingers |
Process | FDM |
Unit price | $48.![]() |
Industry | Automotive |
PC Stratasys - white
Customer | Terumo medical corporation |
Purpose | Prototyping parts used for a disposable electrical device |
Process | FDM |
Unit price | $55.38 / $32.96 |
Industry | Medical |
Formlabs Clear Resin
Customer | Aversan Inc |
Purpose | A prototyping part of an injection molded component for an automated door mechanism |
Process | SLA |
Unit price | $29.83 |
Industry | Aerospace |
HP PA 12 - Dyed Black
Customer | True North Design |
Purpose | Structural and vacuum EOAT components |
Process | SLS / MJF |
Unit price | $69.![]() |
Industry | Automotive |
Prototyping PLA
Customer | Allision Conner |
Purpose | End caps and cable strain relief for sheet metal enclosure |
Process | FDM |
Unit price | $7.92 / $4.72 / $2.80 |
Industry | Industrial Automation |
HP PA 12
Customer | US Hammer |
Description | A part for gasoline engine powered jackhammers |
Process | MJF |
Unit price | $22.18 |
Industry | Construction |
Markforged Onyx - Black
Customer | Autocom Manufacturing |
Purpose | A production part for 3D printed lathe gantry gripper fingers |
Process | FDM |
Unit price | $48.![]() |
Industry | Automotive |
PC Stratasys - white
Customer | Terumo medical corporation |
Purpose | Prototyping parts used for a disposable electrical device |
Process | FDM |
Unit price | $55.38 / $32.96 |
Industry | Medical |
Formlabs Clear Resin
Customer | Aversan Inc |
Purpose | A prototyping part of an injection molded component for an automated door mechanism |
Process | SLA |
Unit price | $29.83 |
Industry | Aerospace |
HP PA 12 - Dyed Black
Customer | True North Design |
Purpose | Structural and vacuum EOAT components |
Process | SLS / MJF |
Unit price | $69.![]() |
Industry | Automotive |
Prototyping PLA
Customer | Allision Conner |
Purpose | End caps and cable strain relief for sheet metal enclosure |
Process | FDM |
Unit price | $7.92 / $4.72 / $2.80 |
Industry | Industrial Automation |
HP PA 12
Customer | US Hammer |
Description | A part for gasoline engine powered jackhammers |
Process | MJF |
Unit price | $22.18 |
Industry | Construction |
Markforged Onyx - Black
Customer | Autocom Manufacturing |
Purpose | A production part for 3D printed lathe gantry gripper fingers |
Process | FDM |
Unit price | $48.![]() |
Industry | Automotive |
PC Stratasys - white
Customer | Terumo medical corporation |
Purpose | Prototyping parts used for a disposable electrical device |
Process | FDM |
Unit price | $55.38 / $32.96 |
Industry | Medical |
Formlabs Clear Resin
Customer | Aversan Inc |
Purpose | A prototyping part of an injection molded component for an automated door mechanism |
Process | SLA |
Unit price | $29.83 |
Industry | Aerospace |
HP PA 12 - Dyed Black
Customer | True North Design |
Purpose | Structural and vacuum EOAT components |
Process | SLS / MJF |
Unit price | $69.![]() |
Industry | Automotive |
Prototyping PLA
Customer | Allision Conner |
Purpose | End caps and cable strain relief for sheet metal enclosure |
Process | FDM |
Unit price | $7.92 / $4.72 / $2.80 |
Industry | Industrial Automation |
HP PA 12
Customer | US Hammer |
Description | A part for gasoline engine powered jackhammers |
Process | MJF |
Unit price | $22.18 |
Industry | Construction |
Markforged Onyx - Black
Customer | Autocom Manufacturing |
Purpose | A production part for 3D printed lathe gantry gripper fingers |
Process | FDM |
Unit price | $48.![]() |
Industry | Automotive |
PC Stratasys - white
Customer | Terumo medical corporation |
Purpose | Prototyping parts used for a disposable electrical device |
Process | FDM |
Unit price | $55.38 / $32.96 |
Industry | Medical |
Formlabs Clear Resin
Customer | Aversan Inc |
Purpose | A prototyping part of an injection molded component for an automated door mechanism |
Process | SLA |
Unit price | $29.83 |
Industry | Aerospace |
HP PA 12 - Dyed Black
Customer | True North Design |
Purpose | Structural and vacuum EOAT components |
Process | SLS / MJF |
Unit price | $69.![]() |
Industry | Automotive |
Prototyping PLA
Customer | Allision Conner |
Purpose | End caps and cable strain relief for sheet metal enclosure |
Process | FDM |
Unit price | $7.92 / $4.72 / $2.80 |
Industry | Industrial Automation |
HP PA 12
Customer | US Hammer |
Description | A part for gasoline engine powered jackhammers |
Process | MJF |
Unit price | $22.18 |
Industry | Construction |
Markforged Onyx - Black
Customer | Autocom Manufacturing |
Purpose | A production part for 3D printed lathe gantry gripper fingers |
Process | FDM |
Unit price | $48.![]() |
Industry | Automotive |
PC Stratasys - white
Customer | Terumo medical corporation |
Purpose | Prototyping parts used for a disposable electrical device |
Process | FDM |
Unit price | $55.38 / $32.96 |
Industry | Medical |
Formlabs Clear Resin
Customer | Aversan Inc |
Purpose | A prototyping part of an injection molded component for an automated door mechanism |
Process | SLA |
Unit price | $29.83 |
Industry | Aerospace |
HP PA 12 - Dyed Black
Customer | True North Design |
Purpose | Structural and vacuum EOAT components |
Process | SLS / MJF |
Unit price | $69.![]() |
Industry | Automotive |
Prototyping PLA
Customer | Allision Conner |
Purpose | End caps and cable strain relief for sheet metal enclosure |
Process | FDM |
Unit price | $7.92 / $4.72 / $2.80 |
Industry | Industrial Automation |
HP PA 12
Customer | US Hammer |
Description | A part for gasoline engine powered jackhammers |
Process | MJF |
Unit price | $22.18 |
Industry | Construction |
Markforged Onyx - Black
Customer | Autocom Manufacturing |
Purpose | A production part for 3D printed lathe gantry gripper fingers |
Process | FDM |
Unit price | $48.![]() |
Industry | Automotive |
PC Stratasys - white
Customer | Terumo medical corporation |
Purpose | Prototyping parts used for a disposable electrical device |
Process | FDM |
Unit price | $55.38 / $32.96 |
Industry | Medical |
Formlabs Clear Resin
Customer | Aversan Inc |
Purpose | A prototyping part of an injection molded component for an automated door mechanism |
Process | SLA |
Unit price | $29.83 |
Industry | Aerospace |
HP PA 12 - Dyed Black
Customer | True North Design |
Purpose | Structural and vacuum EOAT components |
Process | SLS / MJF |
Unit price | $69.![]() |
Industry | Automotive |
Prototyping PLA
Customer | Allision Conner |
Purpose | End caps and cable strain relief for sheet metal enclosure |
Process | FDM |
Unit price | $7.92 / $4.72 / $2.80 |
Industry | Industrial Automation |
HP PA 12
Customer | US Hammer |
Description | A part for gasoline engine powered jackhammers |
Process | MJF |
Unit price | $22.18 |
Industry | Construction |
Markforged Onyx - Black
Customer | Autocom Manufacturing |
Purpose | A production part for 3D printed lathe gantry gripper fingers |
Process | FDM |
Unit price | $48.![]() |
Industry | Automotive |
PC Stratasys - white
Customer | Terumo medical corporation |
Purpose | Prototyping parts used for a disposable electrical device |
Process | FDM |
Unit price | $55.38 / $32.96 |
Industry | Medical |
Formlabs Clear Resin
Customer | Aversan Inc |
Purpose | A prototyping part of an injection molded component for an automated door mechanism |
Process | SLA |
Unit price | $29.83 |
Industry | Aerospace |
HP PA 12 - Dyed Black
Customer | True North Design |
Purpose | Structural and vacuum EOAT components |
Process | SLS / MJF |
Unit price | $69.![]() |
Industry | Automotive |
Prototyping PLA
Customer | Allision Conner |
Purpose | End caps and cable strain relief for sheet metal enclosure |
Process | FDM |
Unit price | $7.92 / $4.72 / $2.80 |
Industry | Industrial Automation |
HP PA 12
Customer | US Hammer |
Description | A part for gasoline engine powered jackhammers |
Process | MJF |
Unit price | $22.18 |
Industry | Construction |
Markforged Onyx - Black
Customer | Autocom Manufacturing |
Purpose | A production part for 3D printed lathe gantry gripper fingers |
Process | FDM |
Unit price | $48.![]() |
Industry | Automotive |
PC Stratasys - white
Customer | Terumo medical corporation |
Purpose | Prototyping parts used for a disposable electrical device |
Process | FDM |
Unit price | $55.38 / $32.96 |
Industry | Medical |
Formlabs Clear Resin
Customer | Aversan Inc |
Purpose | A prototyping part of an injection molded component for an automated door mechanism |
Process | SLA |
Unit price | $29.83 |
Industry | Aerospace |
HP PA 12 - Dyed Black
Customer | True North Design |
Purpose | Structural and vacuum EOAT components |
Process | SLS / MJF |
Unit price | $69.![]() |
Industry | Automotive |
Prototyping PLA
Customer | Allision Conner |
Purpose | End caps and cable strain relief for sheet metal enclosure |
Process | FDM |
Unit price | $7.92 / $4.72 / $2.80 |
Industry | Industrial Automation |
HP PA 12
Customer | US Hammer |
Description | A part for gasoline engine powered jackhammers |
Process | MJF |
Unit price | $22.18 |
Industry | Construction |
Markforged Onyx - Black
Customer | Autocom Manufacturing |
Purpose | A production part for 3D printed lathe gantry gripper fingers |
Process | FDM |
Unit price | $48.![]() |
Industry | Automotive |
PC Stratasys - white
Customer | Terumo medical corporation |
Purpose | Prototyping parts used for a disposable electrical device |
Process | FDM |
Unit price | $55.38 / $32.96 |
Industry | Medical |
Formlabs Clear Resin
Customer | Aversan Inc |
Purpose | A prototyping part of an injection molded component for an automated door mechanism |
Process | SLA |
Unit price | $29.83 |
Industry | Aerospace |
HP PA 12 - Dyed Black
Customer | True North Design |
Purpose | Structural and vacuum EOAT components |
Process | SLS / MJF |
Unit price | $69.![]() |
Industry | Automotive |
Prototyping PLA
Customer | Allision Conner |
Purpose | End caps and cable strain relief for sheet metal enclosure |
Process | FDM |
Unit price | $7.92 / $4.72 / $2.80 |
Industry | Industrial Automation |
HP PA 12
Customer | US Hammer |
Description | A part for gasoline engine powered jackhammers |
Process | MJF |
Unit price | $22.18 |
Industry | Construction |
Markforged Onyx - Black
Customer | Autocom Manufacturing |
Purpose | A production part for 3D printed lathe gantry gripper fingers |
Process | FDM |
Unit price | $48.![]() |
Industry | Automotive |
PC Stratasys - white
Customer | Terumo medical corporation |
Purpose | Prototyping parts used for a disposable electrical device |
Process | FDM |
Unit price | $55.38 / $32.96 |
Industry | Medical |
Formlabs Clear Resin
Customer | Aversan Inc |
Purpose | A prototyping part of an injection molded component for an automated door mechanism |
Process | SLA |
Unit price | $29.83 |
Industry | Aerospace |
Instant, online 3D printing quotes
-
Upload a CAD to start (STEP, STP, IGES, IGS, SLDPRT, 3DM, SAT, STL, OBJ or X_T)
-
Price updates in real-time as you change materials, lead time, etc.
.
-
No hidden costs. Our instant quotes are not just indications, but the actual price, and include shipping and customs up front.
Learn about how our quoting algorithm works
Our ordering process
Receive instant quote
Upload your CAD to our online quoting platform
Confirm specs
Configure your part specifications and select a lead time that suits your schedule
Production
We select the best manufacturer for your order, and production begins immediately
Quality control
We take full responsibility for making sure your parts are manufactured according to our standards
Delivery
Our 3D printing service has been rated 4.9/5
Over 299 customers are satisfied with our 3D printing service.
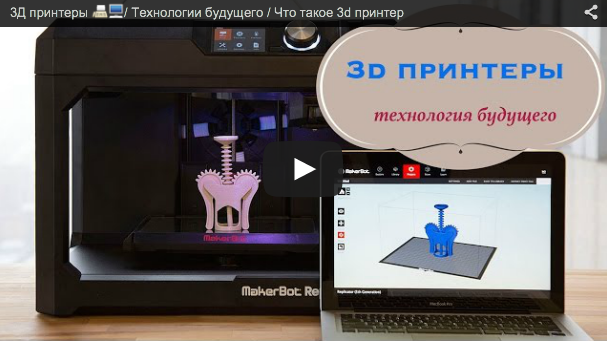
“Great quality service. Fast print (couple of days) and flexible pick up. ”
“Very accommodating, with frequent and open communication regarding the status and quality of the parts. ”
“Great service. Fast turnaround and parts quality great and as expected.”
“Lightning fast service and delivery. Will definitely use again.”
“Very Helpful as always! Great Parts! Would Highly Recommend!”
“Excellent product, communication and quality.”
“Great communication, fast pickup. Great transaction.”
“Great prints! Everything was well done. Thanks!”
“The print was very well done and completed quickly. I will use this company again in the future.”
“Very straightforward print, no issues, great print quality!”
“Excellent service and quality. Will order again.”
“No issues, quick print time. Easy to deal with. ”
“Remarkable quality
Very Precise Printer
I have a good amount of experience with 3D printers and this is the best home manufacturing i have come across.
Two thumbs up!”
“Great turnaround time and prompt replies!”
“Happy with the service, first time using, was not disappointed.”
“Very helpful. Very knowledgeable. Great experience. The did what I was looking for perfectly. Thank you. ”
“Great service provider. Went above the call of duty. Highly recommended. ”
“Parts were made quickly and at a fair price”
“The prints came out fantastic, very smooth and crisp. He kept me updated every step of the way. Thank you again!”
“Amazing service and incredibly fast delivery. I was super happy and surprised when I came home to the package already printed in such short time. High recommended!”
“Good experience, highly recommended and will use again.”
“Good results, quality as expected, communication was fast and technically very competent. ”
“The printed part is working well in its intended application. Service provided was excellent in all aspects.”
“Good communication, fast and ressourceful. Highly recommended.”
“Prints were completed very quickly. Responsive and helpful when I had questions. Great service!”
Show more reviews
Show less reviews
Teams build better parts
Create your Hubs team and start collaborating
Read more
The Hubs Standard - consistent quality, every time
Hubs takes the stress out of manufacturing by guaranteeing the quality and consistency of every part. Each order is dimensionally and visually inspected to make sure it meets the Hubs Standard.
3D printing materials
We can generate instant 3D printing quotes for 25+ plastics. For metal 3D-printed parts, you can request a quote from our parent company, Protolabs.
Available materials
SLS
PA 12 Glass filled PA 12
Desktop FDM
Prototyping PETG Prototyping ASA Prototyping TPU Prototyping ABS Prototyping PLA
Desktop SLA
Formlabs Standard Resin Formlabs Clear Resin Formlabs Tough Resin 2000 Formlabs Rigid Resin 4000 Formlabs Grey Pro Resin Formlabs Flexible Resin 80A Formlabs High Temp Resin Formlabs Durable Resin
MJF
HP PA 12 Glass filled HP PA 12
Industrial FDM
Markforged Onyx ABSplus Stratasys ULTEM 9085 Stratasys Stratasys ASA ABS M30 Stratasys ULTEM 1010 Stratasys
Industrial SLA
Accura 25 (PP-like) Accura ClearVue Accura Xtreme White 200 (ABS-like)
3D printing locations near Barrie
Brampton Barrie Mississauga
Oakville Toronto Markham
Coquitlam Kitchener Hamilton
Oshawa
The 3D Printing Handbook
No one understands 3D printing like us - our founders literally wrote the book. Click here to download the sample chapters.
Buy the book from Amazon
FAQ's
How much does your 3D printing service cost?
The cost of your 3D printed parts depends on factors such as part volume, part complexity, choice of material, which 3D printing technology is used, and if any post processing is required. For more details on these cost factors, see our article on the cost of 3d printing. To check the cost of your 3D printed part, simply upload a CAD (.STL) file and select your material and 3D printing technology to receive a quote within seconds.
How do you guarantee the quality of my prints?
Your parts are made by experienced 3D printing shops within our network. All facilities are regularly audited to ensure they consistently meet the Hubs quality standard. We include a standardized inspection report with every order and offer a First Article Inspection service on orders of 100+ units.
We have partners in our network with the following certifications, available on request: ISO9001, ISO13485 and AS9100.
Follow this link to read more about our quality assurance measures.
How do I select the right 3D printing process for my prints?
You can select the right 3D printing process by examining which materials suit your need and what your use case is.
By material: if you already know which material you would like to use, selecting a 3D printing process is relatively easy, as many materials are technology specific.
By use case: once you know whether you need a functional or visual part, choosing a process is easy.
For more help, read our guide to selecting the right 3D printing process. Find out more about Fused Deposition Modeling (FDM), Selective Laser Sintering (SLS), Multi Jet Fusion (MJF) and Stereolithography (SLA).
How can I reduce the cost of my 3D prints?
In order to reduce the cost of your 3D prints you need to understand the impact certain factors have on cost. The main cost influencing factors are the material type, individual part volume, printing technology and post-processing requirements.
Once these have been decided, an easy way to further cut costs is to reduce the amount of material used. This can be done by decreasing the size of your model, hollowing it out, and eliminating the need for support structures.
To learn more, read our full guide on how to reduce the cost of 3D printing.
Where can I learn more about 3D printing?
Our knowledge base is full of in-depth design guidelines, explanations on process and surface finishes, and information on how to create and use CAD files. Our 3D printing content has been written by an expert team of engineers and technicians over the years.
See our complete engineering guide to 3D printing for a full breakdown of the different 3D printing technologies and materials. If you want even more 3D printing, then check out our acclaimed 3D printing handbook here.
We have an extensive range of online resources developed to help engineers improve their capabilities.
Introductory guides
Design guides
Material guides
Applications
CAD & file preparation
Post processing & finishing
Our other manufacturing capabilities
CNC machining
CNC machining
Milling (3-, 4- & full 5-axis), turning and post-processing
-
50+ metals and plastics & 10 surface finishes
-
Tolerances down to ±.0008” (0.020 mm)
-
Lead times from 5 business days
See our CNC machining services
Put your 3D printed parts into production today
Get an instant 3D printing quote
Welcome to 3D Printing - Barrie Public Library
Registration now closed
Welcome to 3D Printing
for Kids!
2020-05-02 14:30:00 2020-05-02 15:30:00 America/New_York Welcome to 3D Printing Learn the basics of 3D design using Tinkercad. com and the library's own 3D printer. Painswick Branch -
Saturday, May 02
2:30pm - 3:30pm
Add to Calendar 2020-05-02 14:30:00 2020-05-02 15:30:00 America/New_York Welcome to 3D Printing Learn the basics of 3D design using Tinkercad.com and the library's own 3D printer. Painswick Branch -
Painswick Branch
Learn the basics of 3D design using Tinkercad. com and the library's own 3D printer.
We'll talk about some ways that 3D printing is being used today and then you can design and print your own object using 3D design apps. Participants can choose to print the object they design in the workshop, or keep working and come back later for a free 3D print. 3D printing jobs can take several hours, so all prints will be printed later and can be picked up after the program. Ages 9+ (7+ with a parent or older sibling).
AGE GROUP: | School-Aged Kids |
EVENT TYPE: | Computer Help |
TAGS: | |
Painswick Branch
[email protected]
Phone: 705.728.1010
Mon, Dec 05 | 9:30AM to 5:00PM |
Tue, Dec 06 | 9:30AM to 9:00PM |
Wed, Dec 07 | 9:00AM to 9:00PM |
Thu, Dec 08 | 9:30AM to 9:00PM |
Fri, Dec 09 | 9:30AM to 9:00PM |
Sat, Dec 10 | 9:30AM to 5:00PM |
Sun, Dec 11 | 9:30PM to 5:00PM |
previous
this week
next
About the branch
Our Painswick Branch is located in the south end of Barrie, near the corner of Big Bay Point Road and Yonge Street. The building and facilities are fully accessible. Enjoy the bright and sunny reading lounge, use our complimentary wifi, experiment with technology and maker tools, or book a room for your next event.
Upcoming events
Friday Flicks
Fri, Dec 09, 6:30pm - 8:30pm
Massie Family Community Room
Storytime
Tue, Dec 13, 10:00am - 10:30am
Massie Family Community Room
Cricut Coach
Wed, Dec 14, 2:30pm - 3:30pm
This event is full
Baby Goose
Thu, Dec 15, 10:00am - 11:00am
Ukulele Meet Up!
Thu, Dec 15, 2:00pm - 3:00pm
Massie Family Community Room
Tech Coach
Thu, Dec 15, 2:00pm - 3:00pm
This event is full
Friday Flicks
Fri, Dec 16, 6:30pm - 8:30pm
Massie Family Community Room
Cricut Coach
Wed, Dec 21, 2:30pm - 3:30pm
This event is full
Ukulele Meet Up!
Thu, Dec 22, 2:00pm - 3:00pm
Massie Family Community Room
Tech Coach
Thu, Dec 22, 2:00pm - 3:00pm
This event is full
Friday Flicks
Fri, Dec 23, 6:30pm - 8:30pm
Massie Family Community Room
Cricut Coach
Wed, Dec 28, 2:30pm - 3:30pm
This event is full
Tech Coach
Thu, Dec 29, 2:00pm - 3:00pm
This event is full
Friday Flicks
Fri, Dec 30, 2:30pm - 4:30pm
Massie Family Community Room
Friday Flicks
Fri, Dec 30, 6:30pm - 8:30pm
Massie Family Community Room
Friday Flicks
Fri, Jan 06, 2:30pm - 4:30pm
Massie Family Community Room
Friday Flicks
Fri, Jan 06, 6:30pm - 8:30pm
Massie Family Community Room
Family Flicks
Sat, Jan 07, 2:30pm - 4:30pm
Massie Family Community Room
See all events
Swiss chocolate manufacturer makes it easy to create chocolates with a 3D printer
- Technology
- Clara Minack Author
Swiss company Barry Callebaut, which produces chocolate for Nestle and Hershey, has created a technology for 3D printing candies. The development will make it possible to move away from the practice of making complex-shaped sweets by the piece, and will make such a product more affordable.
Swiss-based Barry Callebaut has created a 3D printer capable of producing thousands of chocolates in a short amount of time. She plans to take orders from hotels, patisseries, coffee shops and other companies that want to wow their customers.
Finished reading here
The food industry already has examples of the use of 3D printing, notes American Forbes. However, Barry Callebaut's technology allows you to put the creation of chocolate on a stream, which will make such a product more affordable due to the scale of production.
Barry Callebaut will produce chocolate on a 3D printer under the Mona Lisa brand. At the same time, customers will be able to come up with their own design, shape and size. As a result, they will receive products that can be used in signature desserts, hot drinks and pastries. According to the head of innovation Pablo Perversi, this is in line with the current trend towards personalization. In addition, it will be of interest to consumers who want to share pictures on Instagram, and will satisfy the demand for premium products, Perversi said. “It is important that these will not be single orders as before. We can produce on a larger scale,” he said.
Bloomberg names the Swiss company as the unofficial producer of a quarter of the world's chocolate. Among the clients of the company from Zurich are Nestle, Unilever and Hershey. Those who want to buy such chocolate in the store will have to wait a few years. According to Perversi, at first his company will be engaged in the production of gourmet products, then it will move on to cooperation with manufacturers.
Perversi does not rule out that in the future 3D printers from Barry Callebaut will find themselves in the ordinary kitchen, next to the coffee makers familiar to consumers. “The idea of having a chocolate printing machine in the house with capsules that allow you to do something is just great. We have not yet reached this point, but we have opportunities for this, and we will study them,” Perversi said.
- Traditions of success. Recipes from the 19th century helped an unknown chocolate manufacturer get rich
- 10 brands of chocolate with the most unusual flavors
-
Clara Minack
Author
#Barry Callebaut #chocolate #3D Printer
Forbes Newsletter
Funding, Investing, Business & Technology Essentials
3D Printing a House: How to 3D Print a House
Will we all go to a 3D printer instead of builders in a progressive version of the future for a new house?
3D printing is one of the most talked about technologies of the last decade. Some see it as the beginning of the third industrial revolution, others are more inclined to see the flaws. So how realistic is 3D printing houses? In this article, we will talk about the level of development of 3D printing in different countries and look at the fragile pavilions made of composite material in China; concrete pillars in Italy, inspired by classical architecture, and "thinking" houses in Germany.
Eva Zimmermann
Archived: This is one of the articles in our "most popular" section
What is 3 D -print? 3D printing technology was invented by American engineer Chuck Hull. He patented the process in 1986 and first called it stereolithography. The method involved joining molecules with a laser to transform polymers into solid forms.
The first use of 3D printing was found in the automotive industry - with its help they began to make so-called "rapid prototypes". The main advantage of the technology was that from now on it was not necessary to cast molds, which significantly reduced design costs. In addition, compared to sawing a prototype out of wood, there is significantly less waste, because before all the remaining material had to be disposed of. In a 3D printer, objects are printed in layers, somewhat repeating the idea of inkjet printing on paper. Only the process is repeated many times, and instead of ink, a harder material is taken. With a slight shift between the layers, a volume appears, or, as they say now, a 3D effect.
Materials used in 3D printing range from synthetic resins and plastics (most commonly) to steel and concrete. Today, compact models of 3D printers are increasingly appearing in design studios, schools, and even in private homes.
Eva Zimmermann
Large-scale application 3 D printing in China
China is a country where superlatives are considered a sign of progress in all areas of life. Therefore, it is not surprising that the largest architectural object created using a 3D printer appeared in this country. The Volcano Pavilion (pictured) opened to the public in 2015 during Beijing Design Week 2015. The architects of the project were Xu Feng and Yu Lei. Of course, the 8.08 m long and 2.88 m high pavilion was not printed in one go. In fact, it was assembled from 1023 individual parts, each of which was printed on a 3D printer.
Although this achievement was awarded the Guinness Book of Records, it also showed that the scope of 3D printing is still very limited. To create an entire house on a 3D printer, the printer must be gigantic, or at least be able to drive along specially constructed scaffolding. Scale is the reason why 3D printing is still in its infancy when it comes to architecture.
Eva Zimmermann
How to print a whole house
In Amsterdam, however, DUS Architects is currently printing layer by layer a house called the Canal House. Completion of the project is scheduled for 2017.
“China is also printing entire houses,” says Dr. Jane Barry, associate professor at the Spatial Information Architecture Laboratory at the Royal Melbourne University of Technology. “Although at this stage they still look raw. ” She is referring to a project by Winsun, which has already printed several concrete houses in China. This project is most often cited as an example when it comes to 3D printing in construction. Representatives of the company declare significant savings. So, compared to traditional construction, the printing of a new house requires 60% less materials, 70% less time and 80% less labor costs. The printer itself at the same time has gigantic dimensions - 150x10x6.6 m!
Eva Zimmermann
Or shut down the building process
“It's all about what you mean by 3D printing,” says Benedikt Gotze, public relations specialist for the Association of German Architects (Bund Deutscher Architekten). His expert opinion on 3D printing in architecture is far from universal euphoria: “The idea of printing entire houses is a childish fantasy, this will never happen. But what will really happen is the digital control of the production of building parts in factories, from where they will, as before, be delivered to construction sites. Chinese 3D houses, which are so often cited as an example, seem to me an unnecessary measure in the struggle for everyone's attention.
Professor Jane Barry from Melbourne Tech says: “The main advantage of 3D printing is not mass production, but the ability to create individual designs and the variety of options. At our university, we pay special attention to printing from metals, for example, in the production of key elements of building structures to individual measurements. If you reduce the amount of material in the finished product, then its weight and the overall load on the foundation will decrease accordingly, not to mention saving the energy expended. In this area, 3D printing is a real find, because the production of key elements of the house structure in another way, such as casting, can be very expensive, and with the new technology, for much less cost, you can even print a few spare parts in case of repairs.
Benedikt Gotze questions the practicality of the very idea of 3D printing houses: “All this enthusiasm reminds me of manned space flights – doable, but is it necessary? Omega is still building advertisements for Speedmaster watches based on the fact that they went to the moon. ”
But the British architectural firm Foster & Partners and the European Space Research Agency can argue with Gotze about flights to the moon. Together they are exploring ideas for applying 3D printing to a lunar base as part of the Lunar Habitation project, which is expected to be completed by 2024.
Eva Zimmermann
Back to Earth
While Foster & Partners' lunar base is arguably the most ambitious program in existence, there are projects on Earth that deserve your attention. One of them is the bridge in Amsterdam, which was the result of a collaboration between designer Joris Laarman, MX3D, which makes 3D printers that print steel objects, and CAD software developer Autodesk.
Looking at this photo, it might look like the new steel bridge is being built right on site, over the Oudezijds Achterburgwal canal, but it's actually being made in a workshop. Work began in the fall of 2015 in a huge space rented by MX3D. Through trial and error, employees try to print the entire structure. Completion is scheduled for 2017, which means that in just a year we will see the first real steel bridge, fully 3D printed and open to the public - another race for a world record.
Eva Zimmermann
This little detail shows how the bridge will look after the 3D printing process is complete. Two undoubted advantages of steel printing are that, compared to casting, the contours are more organic and fluid, and the absence of the need to make injection molds significantly reduces the cost of production.
WASProject
Fine concrete printing in Italy
The collaboration between the University of Naples and WASP, a modern technology company, has combined the beauty of Italian architecture with modular construction techniques.
WASP was founded in 2012 by Italian entrepreneur Massimo Moretti. Its main activity is to promote energy-efficient building methods and support the production of building modules on site. Together with the University of Naples, its specialists have developed concrete supports that can be 3D printed and used in a wide variety of construction projects.
Domenico Asprone (pictured), assistant professor of structural design at the University of Naples, took part in this project as a structural engineer: “The idea was to print a curved concrete support, optimizing the amount of concrete used and reducing the cost of producing a complex formwork. The approach is based on dividing the support into several concrete segments, which are printed separately and then assembled into a single monolithic element, along with steel reinforcement, according to the Lego principle. This method is designed to facilitate the production of complex parts with a wide variety of profiles, which in turn will lead to greater creative freedom for design engineers,” he says.
WASProject
“The segments are printed individually. As soon as the concrete hardens a little, reinforcing bars are inserted into them, reinforcing the beam and combining several segments into a whole support,” says Domenico.
Simultaneously with the already established production, WASP specialists are developing a technology for one-time printing of reinforced poles 3.2 m long. To this end, they use concrete with a lower viscosity index. “We have more than a century of history in the production of concrete products. We just adapted existing technologies for 3D printing,” says Domenico. “Today, we use cement and other binders, such as environmentally friendly clay-based compounds (geopolymers), to create waterproof products that are suitable for building gutters.”
What are the future plans of WASP? In the near future, they are going to print a footbridge similar to Joris Laarman's design in Holland, but not from steel, but from concrete.
CJSC SPETSAVIA 3D printing of buildings
Decorative parts from Russia
Like the Italian company WASP, the Russian manufacturer Spetsavia uses 3D printers to print concrete products.
Construction contractors are among the main clients of this company. CEO Alexander Maslov talks about the products that can be printed on his printers: “Printers of the 06044 series can print individual structural elements up to 12.3 m long. This is more than enough to print products of complex shape for the construction and design of all kinds of towers, arches, partitions and other decorative elements of buildings. Already today we have experience in printing such elements of landscape design as a small swimming pool and a children's playground. Also, the printer can be used to print fireplaces, stoves, barbecues and other refractory products from kaolin mixtures.
CJSC SPETSAVIA 3D printing of buildings
According to Alexander, from a technical point of view, it would be possible to print the whole house, but still he treats this idea pragmatically: “As far as I understand, we are talking about printing individual elements and their subsequent assembly at the construction site. The advantage of this method is that you can move the production of parts indoors and thereby reduce the effects of temperature, humidity, and so on. And the disadvantages are in the cost of transportation and extended construction time. Plus, the assembly of individual elements is a technologically complex process that requires additional solutions to strengthen the structure.”
Despite the fact that Alexander considers himself a pragmatist and prefers not to look too far ahead, he still admits that new building technologies, like the one offered by his company, will become an integral part of any construction project in a few years.
A bold vision for the future from Germany
Professor Akim Menges is the head of the renowned Institute for Computational Design at the University of Stuttgart. The real possibilities of the new technology are already being applied here in full and are the subject of study in his research projects. He knows better than anyone that innovation is an invitation to leave behind all old ideas. “First, you use the latest invention to build traditional objects, as they did in China, where familiar-looking houses are built using 3D printers,” says Akim Menges. “But at the second stage of development, structures appear that can only be created through new technology.”
This means, for example, that "3D printing will make it possible to use complex geometries in construction without increasing cost or labor." “Awareness of this fact will set a new direction in design,” explains the professor. The advent of 3D modeling software has already changed the aesthetics of architecture, and 3D printing is the next step in that direction.
In addition, the printed elements may physically have heterogeneous layers. “We have the ability to create very complex parts with gradient characteristics,” says Professor Menges. “That is, the finished object can be soft on one side and hard on the other, due to the fact that different materials are loaded into the multifunctional printer right during the printing process. ”
Eva Zimmermann
Buildings that can think
Prof. Menges is currently developing building parts that can change shape, just like in nature. “Just imagine a pinecone. When it grows on a tree, its scales are closed, but when it falls to the ground and dries, they open like petals, he says. “With 3D printing, we can simulate this effect by using different materials, soft and hard, that respond differently to atmospheric changes, such as humidity. In this way, we can create building parts that will adapt to climatic conditions without the need for forced control using manual or electronic mechanisms.” The photo shows a prototype of one of these parts.
Many people go one step further. “Today there is a lot of talk about Industry 4.0, in other words, the fourth industrial revolution,” says Professor Menges. “It involves the mutual penetration of the material and digital world through the so-called cyber-physical systems. ” In such systems, software is connected to mechanical and electronic components through a data infrastructure, such as the Internet (adherents of this idea love the phrase “Internet of things”). This kind of building technology could completely change the way we live, the whole everyday world we know.
Eva Zimmermann
Conclusion: 3D - euphoria or a sober look at the future?
Fans of the new technology are literally pushing us to the threshold of a new era. If scientists start sharing their designs and the technology is available to everyone, 3D printing can really change the world. The production of necessary items can move into kitchens and living rooms, and then we will pollute the environment less, since the need to transport and deliver goods will decrease many times over.
But if we talk about architecture, here size continues to be a serious obstacle to the further development of technology. In addition, the list of building materials that can be refilled into 3D printers is still very limited.
Dr. Jane Barry also talks about the serious competition of technologies in the construction industry: “I imagine that in the next ten years 3D printing will develop in parallel with other technologies, but I would not invest my own money in it, but in wood construction,” this is the most obvious trend.” In her opinion, laminated wood with a longitudinal-transverse arrangement of layers is like “plywood on steroids”. Such a material is somewhat reminiscent of concrete in the sense that it is possible to build a whole house from it, without an internal frame. This means that houses can potentially be built faster and cheaper. “I'm not saying these technologies can't coexist,” she adds. “At the end of the day, a 3D printer can also be filled with wood-based material.”
We still have a lot to explore and experience. We may not be printing houses on the Moon in the near future, but 3D printing will definitely make it possible to build houses with more complex geometries.