Powder bed and inkjet head 3d printing
All About Powder Bed and Inkjet Head (PBIH) 3D Printing
Image credit: asharkyu/Shutterstock.com
Many modern industries benefit from a type of fabrication technique known as additive manufacturing or AM for short. In AM, components are built up from stock material in a selective process and is counter to the traditional subtractive manufacturing methods like cutting, drilling, milling, etc. AM can be done using numerous methods – to see a general overview of these types, read our article about the different types of 3D printing technologies. This article will expand upon powder bed and inkjet head (PBIH) 3D printing, a process that has quickly gained traction since its beginnings. This article will explain what PBIH is, how it works, its pros and cons as an AM technology, how to choose a PBIH machine, and the common applications of this process in modern industry.
What is Powder Bed and Inkjet Head (PBIH) 3D Printing?
PBIH 3D printing was developed and patented by the Massachusetts Institute of Technology in 1993 and is the first trademarked use of the term “3D printing”. PBIH is also known as binder jetting and drop-on-powder 3D printing, which all describe the same underlying process denoted by ISO/ASTM known as binder jetting. In PBIH, a liquid binder adhesive is sprayed onto a powder bed, binding particles together into a part in a layer-by-layer process. An inkjet head (not much different than those used in 2D printers) is used to selectively apply binder onto a variety of powdered materials, such as:
- Silica sand
- Sandstone
- PMMA
- Metal powders
- Gypsum
- Food-safe powders (starch/cellulose/sugar)
- Ceramic powders
- Chromite
and other custom blends.
The binder is applied layer-by-layer until the full part is contained within the powder bed, where it is then removed and post-processing is applied according to its material. PBIH is set apart from other processes, as it uses no energy source to fuse the powder together, unlike the processes found in fused deposition modeling (FDM), stereolithography (SLA), or powder bed fusion (PBF) techniques.
Post-processing is a vital step in PBIH printing, as it will bring the part to full strength and/or visual quality. These post-processing steps can include coating, sintering, infiltrating, painting, and other procedures which will protect the integrity of the print and ensures it reaches final part strength for its application.
How does PBIH Work?
Image credit: Christian Cavallo Consulting, LLC
Figure 1: Functional diagram of PBIH 3D printers. Note that this diagram is a functional representation and may not include all components of real-world PBIH systems.
Figure 1 displays the functional components of a PBIH system – this section will use the labels found in Figure 1 to explain how the PBIH process is used to create fully functional 3D parts.
PBIH begins by creating a 3D model and converting it into a printer-friendly format (typically an .STL file) and using a so-called slicing software to cut the model up into discrete layers. This file is then uploaded to the 3D printer, and the printer’s powder supply reservoir is filled with powdered material and the inkjet is connected to a reservoir of liquid adhesive.
Powdered material is elevated from the powder stock and is applied in a thin, even layer over the build platform by the powder roller/re-coater. The inkjet printhead, guided by the 3D model layers in X-Y directions, selectively applies a spray of binder adhesive to the powder. Once this first layer is solidified, the build platform increments down (on the Z-axis), and the powder stock increments up to allow the roller/re-coater to spread the next layer of powder. This process repeats until every layer has been printed, and the part is embedded in powder in the powder bed.
The part is left to fully solidify, and it is then removed from the powder and cleaned of excess material. Any leftover loose powder can be reclaimed for future prints, though some is wasted in the printing process and must be discarded. The part is post-processed according to material specifications, as it is in the so-called “green state” post-printing – meaning very brittle and prone to breaking. Post-processing is the most vital step for PBIH printing, as these procedures imbue the part with its final aesthetic and mechanical properties. The next sub-sections will explore some post-processing procedures for different PBIH materials.
Gypsum/Starch Post-Processing
Powders made of gypsum or starch were one of the first implemented materials in PBIH printing, and it is activated using a water-based adhesive. These prints are very porous and require a process known as infiltration, where material is forced into the negative spaces within the part via capillary action to increase its strength and surface finish. In plaster parts, this infiltrant is usually melted wax, cyanoacrylate glue (super glue), epoxy, or others which fill porous zones and increase the overall rigidity of a part. After infiltration, the part may be sanded to the desired surface finish and is generally ready for use.
Metal HPost-Processing
PBIH printers have recently gained popularity thanks to their use of metal composite powders, which are mixtures of metallic particles and binder material. Parts made from these mixtures are heated in an oven post-print, where the binders disintegrate in the heat and leave behind a fully metal part. The metal particles sinter together – or fuse without reaching their melting temperature – and leave behind a porous metal structure. Parts can be used right after sintering, but most parts undergo a further step and are infiltrated by another, low-melting temperature metal such as bronze. This creates a denser, stronger composite metal part that has an attractive surface finish.
An important note about metal PBIH parts is that they shrink considerably in the heating/consolidation process. Sintered parts shrink about 20% from their initial dimensions and infiltrated parts shrink up to 2%. This shrinkage can be factored in before printing begins, but the non-uniform nature of this deformation can lead to post-print inaccuracies. Also, while these prints are full metal, they are not as strong as those made from other metal 3D printing techniques such as SLM/DMLS, limiting their usage in high-end and rigorous applications (to read more about metal 3D printing, visit our article All About Selective Laser Melting 3D Printing).
Advantages & Limitations of PBIH
PBIH is a process that has some impressive benefits for AM applications, as well as notable issues. Below are brief lists of the pros and cons of using PBIH as an AM tool, and should help buyers determine if PBIH is the right tool for their needs.
Advantages of PBIH:
- PBIH is very efficient and cheap, being over 10x more economical, especially in metal printing
- If using multiple printheads, PBIH can print full-color parts
- Parts in PBIH printing do not need support structures, as the powder bed itself supports overhangs/complex areas, and it does not need to be fused to the build platform
- Because of its lack of heat, PBIH can produce very large parts with no threat of thermal distortions (in printing at least)
- PBIH is can easily handle low to medium batch production runs
Limitations of PBIH:
- Post-processing is time-consuming, difficult, and prone to introducing errors into an otherwise perfect print
- The mechanical properties of PBIH parts (especially metal parts) are much lower than other 3D printing technologies, limiting their uses in high-end applications
- The resolution of PBIH prints is low and the surface finish of parts is rough
- Material choice in PBIH is limited in comparison to other AM technologies
- The price point of PBIH printers to buy upfront may be hard to justify, considering its downsides ($50,000-$2 million)
Selection Criteria and Specifications
This section will explain some selection criteria to look out for when considering a PBIH printer. While not an exhaustive list of specifications, this section should detail the major areas of the printer and help narrow your list of available options based on quantifiable metrics.
Build Volume & Supported Materials
PBIH printers typically have build volumes ranges shown below, based on material:
PBIH printer type | Build volume ranges |
Metal PBIH printers | 400 x 250 x 250mm to 800 x 500 x 400mm |
Full color PBIH printers | 200 x 250 x 200mm to 500 x 380 x 230 mm |
Sand PBIH printer | 800 x 500 x 400 to 2200 x 1200 x 600mm |
The first decisions to make when considering a PBIH printer are what material you will use and how large it needs to be. Ask if a given PBIH machine can handle multiple materials, or if it is dedicated to a limited set of materials. Secondly, determine the largest part you will need to print and see if this printer can accommodate it in its build volume. Note that custom/non-standard build volumes exist which may be larger or smaller than the above-generalized values.
Dimensional Accuracy & Tolerances
Most printer spec sheets will provide the minimum tolerances and dimensional accuracy of printed parts- these values will determine how loyal your printer will be to its 3D print. These values, like build volume, also change with material:
PBIH printer type | Typical dimensional accuracy |
Metal PBIH printers | ±0.2mm |
Full color PBIH printers | ±0. |
Sand PBIH printer | ±0.3mm |
Note that these values are for the printing process and may not account for the shrinkage/deformation caused by post-processing. Understand how much “wiggle” room your part dimensions have and match it to the right printer that will not supersede these maximum boundaries of error.
Resolution & Layer Thickness
Along with dimensional accuracy, the overall resolution and layer thickness of a printer will determine how detailed the print will be. PBIH systems typically have a resolution of 400 x 400 droplets per inch (dpi) to 1200 x 1200 dpi, while their layer thickness varies with the material choice:
PBIH printer type | Typical layer thickness |
Metal PBIH printers | 35 - 50 μm |
Full color PBIH printers | 100 μm |
Sand PBIH printer | 200 - 400 μm |
Physical Dimensions, Price, & Embedded Electronics
PBIH printers can get as large as a cubic meter in size or greater – this may work for a factory setting but would be more challenging for smaller workspaces. Determine the allowable dimensions of the printer to maximize build space, but also consider size restraints on your work area. Also, determine a price point that is justifiable; many PBIH printers come with on-board computer terminals, control displays, and automation features that can quickly add to its cost. Embedded electronics such as these are great quality-of-life features but may not be necessary depending upon the application.
Applications of PBIH 3D Printing
PBIH has found some important applications industry as an AM technology, some that other printers could never accomplish. Below is a brief list of common applications of PBIH:
- Pharmaceutical tablets
- Food/temperature-sensitive substances
- Full-color parts production
- Non-structural metal components
- Large sand-casting cores and molds
- High volume, low-cost components
- Rapid prototyping
and much more.
Summary
This article presented an understanding of what powder bed and inkjet head 3D printing is and how it works. We hope this article has explained what PBIH is, how it works, and how it can benefit your manufacturing capabilities. For more information on related products, consult our other guides or visit the Thomas Supplier Discovery Platform to locate potential sources of supply or view details on specific products.
Sources:
- Powder bed and inkjet head 3D printing – HiSoUR – Hi So You Are
- Additive Manufacturing: Powdered Bed & Inkjet 3D Printing – Tata Technologies PLM Solutions (myigetit.com)
- Powder bed and inkjet head 3D printing - 3D Printing - 3D Printed (partcommunity.com)
- ExOne | Binder Jetting Technology
- Understanding the Seven Types of Additive Manufacturing (firetrace.com)
- What is Binder Jetting and how does binder jetting work (engineeringproductdesign.com)
- How 3D Printing Will Change Composites Manufacturing | Additive Manufacturing
- VX1000 - Multi material 3D printer for small series (voxeljet.
com)
- Metal Binder Jetting | Digital Alloys
Related Articles:
- The Best 3D Printers under $200
- The Best 3D Printing Software
- The Best 3D Printer Under $1000
- The Best 3D Printer Under $500
- All About Material Jetting
- All About Multi Jet Modeling (MJM) 3D Printing
- All About Fused Deposition Modeling
- All About Stereolithography 3D Printing
- All About Photopolymerization
- All About Sheet Lamination/Laminated Object Manufacturing
- All About Electron Beam Additive Manufacturing
- All About Direct Energy Deposition 3D Printing
- All About Binder Jetting 3D Printing
- All About Powder Bed Fusion 3D Printing
- All About Direct Metal Laser Sintering 3D Printing
- All About Selective Laser Sintering 3D Printing
- All About Selective Laser Melting 3D Printing
- All About Selective Heat Sintering 3D Printing
- All About Digital Light Processing 3D Printing
- All About Continuous Liquid Interface Production
More from Custom Manufacturing & Fabricating
Powder bed and inkjet head 3D printing – HiSoUR – Hi So You Are
Powder bed and inkjet 3D printing, known variously as “binder jetting” and “drop-on-powder” – or simply “3D printing” (3DP) – is a rapid prototyping and additive manufacturing technology for making objects described by digital data such as a CAD file.
History
This technology was first developed at the Massachusetts Institute of Technology in 1993 and in 1995 Z Corporation obtained an exclusive license. The term “Three-Dimensional Printing” was trademarked by the same.
Description
As in many other additive manufacturing processes the part to be printed is built up from many thin cross sections of the 3D model. An inkjet print head moves across a bed of powder, selectively depositing a liquid binding material. A thin layer of powder is spread across the completed section and the process is repeated with each layer adhering to the last.
When the model is complete, unbound powder is automatically and/or manually removed in a process called “de-powdering” and may be reused to some extent.
The de-powdered part could optionally be subjected to various infiltrants or other treatments to produce properties desired in the final part.
Technology
In 3D printing, the workpieces are built up layer by layer. 3D data (eg CAD data) is used to calculate the geometry to be generated for each individual layer. In 3D printing, a powder or granule layer is applied to a height-adjustable table and glued by means of a binder at the points that belong to the workpiece. This is similar to a conventional inkjet printer, a printheadused, which applies the binder instead of ink. Subsequently, the table is lowered by one layer thickness and applied a new powder layer. This is repeated until the workpiece is completely formed, which is then completely hidden by the surrounding powder. Thereafter, the supernatant powder is returned for further use, the workpiece is removed from the printer and freed from powder residues.
The process principle is thus similar to the selective laser melting, in which a metal powder is locally melted by a laser.
Materials
In the original implementations, starch and gypsum plaster fill the powder bed, the liquid “binder” being mostly water to activate the plaster. The binder also includes dyes (for color printing), and additives to adjust viscosity, surface tension, and boiling point to match print head specifications. The resulting plaster parts typically lack “green strength” and require infiltration by melted wax, cyanoacrylate glue, epoxy, etc. before regular handling.
While not necessarily employing conventional inkjet technology, various other powder-binder combinations may be deployed to form objects by chemical or mechanical means. The resulting parts may then be subjected to different post-processing regimes, such as infiltration or bakeout. This may be done, for example, to eliminate the mechanical binder (e.g., by burning) and consolidate the core material (e.g., by melting), or to form a composite material blending the properties of powder and binder. Depending on the material, full color printing may or may not be an option. As of 2014, inventors and manufacturers have developed systems for forming objects from sand and calcium carbonate (forming a synthetic marble), acrylic powder and cyanoacrylate, ceramic powder and a liquid binder, sugar and water (for making candies), etc. One of the first commercially available products that incorporated the use of Graphene, was a powdered composite used in powder bed inkjet head 3D printing.
3D printing technology has a limited potential to vary material properties in a single build, but is generally limited by the use of a common core material. In the original Z Corporation systems, cross-sections are typically printed with solid outlines (forming a solid shell) and a lower-density interior pattern to speed printing and ensure dimensional stability as the part cures.
Characteristics
In addition to volumetric color by use of multiple print heads and colored binder, the 3D printing process is generally faster than other additive manufacturing technologies such as fused deposition modeling material jetting which require 100% of build and support material to be deposited at the desired resolution. In 3D printing, the bulk of each printed layer, regardless of complexity, is deposited by the same, rapid spreading process.
As with other powder-bed technologies, support structures are generally not required because loose powder supports overhanging features and stacked or suspended objects. The elimination of printed support structures can reduce build time and material use and simplify both equipment and post-processing. However, de-powdering itself can be a delicate, messy, and time-consuming task. Some machines therefore automate de-powdering and powder recycling to what extent feasible. Since the entire build volume is filled with powder, as with stereolithography, means to evacuate a hollow part must be accommodated in the design.
Like other powder-bed processes, surface finish and accuracy, object density, and—depending on the material and process—part strength may be inferior to technologies such as stereolithography (SLA) or selective laser sintering (SLS). Although “stair-stepping” and asymmetrical dimensional properties are features of 3D printing as most other layered manufacturing processes, 3D printing materials are generally consolidated in such a way that minimizes the difference between vertical and in-plane resolution. The process also lends itself to rasterization of layers at target resolutions, a fast process that can accommodate intersecting solids and other data artifacts.
Powder bed and inkjet 3D printers typically range in price from $50,000 to $2,000,000 however there is a hobbyist DIY kit selling from $800 to convert a consumer FDM printer to powder/inkjet printer.
Advantages and disadvantages
Theoretically, all materials can be used as long as they can be glued to the binder. In particular, foods or temperature-sensitive substances such as medicines can be processed. In addition, it is possible to use different binders within a single workpiece to create areas with different mechanical properties. As a binder, numerous substances can be used, for. For example, those based on water, synthetic resin or living cells. In principle, the powders do not have to be identical in every layer.
In addition, in Binder Jetting, similar to laser sintering, no support material is necessary because the workpiece is carried by the powder during the production process.
However, 3D printing does not provide a very strong workpiece. Especially when using metals as materials, the workpieces must be subsequently removed from the binder and sintered to ensure sufficient strength. This leads to shrinkage, so that the final geometry is difficult to set in advance, but this is basically manageable with enough experience.
Source from Wikipedia
Machine tool Powder bed and inkjet head 3D printing Manufacturing Selective laser melting, honeycomb technology, metal, 3D Printing, selective Laser Melting png
Machine tool Powder bed and inkjet head 3D printing Manufacturing Selective laser melting, honeycomb technology, metal, 3D printing, selective laser melting pngtags
- metal,
- 3D printing,
- selective laser melting,
- seal,
- printer,
- bed powder and inkjet head 3d printing,
- production,
- machine,
- laser scanning,
- laser cut,
- laser,
- dmg Mori Aktiengesellschaft,
- additive Production,
- honeycomb technology,
- png,
- transparent,
- free download
About this PNG
- Image size
- 630x472px
- File size
- 140.
49KB
- MIME type
- Image/png
resize PNG
width(px)
height(px)
License
Non-Commercial Use, DMCA Contact Us
- Inkjet printing press Large-format printer Printing press, printer, electronics, digital, banner png 3908x2620px 1.96MB
- Laser cutting Laser engraving Computer CNC machine, textile, engraving, machine png 676x653px 290.15KB
- Paper 3D printer Xerox Printer, printer, electronics, computer, business png 1024x580px 454.4KB
- Laser cutting Laser engraving Fiber laser, others, angle, furniture, laser png 700x505px 317.4KB
- Machine Heidelberger Druckmaschinen Printing press Laser cutting, printer, electronics, banner, digital Printing png 3264x2448px 2.43MB
- Printer paper CMYK color model, Printer, supplies, electronics, happy Birthday Vector Images png 2430x2422px 291.84KB
- Laser cutting Laser engraving 3D printing, others, angle, rectangle, 3D Printing png 700x700px 19.87KB
- Hewlett-Packard Laser printing Printer HP LaserJet Pro P1102, hewlett-packard, electronics, computer, monochrome png 640x481px 281.27KB
- Hewlett Packard Enterprise Inkjet printing HP Slate 500 Laptop Laser printing, HP printers, angle, electronics, computer png 790x856px 635.58KB
- Large-format printing printer Dye-sublimation printer MIMAKI ENGINEERING CO., LTD., others, ink, lithography, printer png 1186x1023px 369.19KB
- Rapid prototyping 3D printing Prototype Computer Icons, printing, rectangle, black, business png 900x900px 11.85KB
- Selective laser sintering machine 3D printing Selective laser melting, printer, electronics, public Relations, industry png 1200x748px 266.11KB
- photocopier machine business stationery copier, copier, angle, people, canon png 1000x1000px 299.
65KB
- Machine tool Laser cutting Laser processing, plotter, engraving, computer Numerical Control, machine png 1500x1500px 1.32MB
- Hewlett-Packard Multifunction Printer HP LaserJet Pro M227 MFP Laser printing, Multifunction printer, canon, electronic Device, fax png 1000x750px 166.47KB
- Hewlett Packard Enterprise printer Laser printing Toner cartridge HP LaserJet, printer, white, electronics, ink Cartridge png 2898x2280px 1.16MB
- Laser cutting Laser engraving 3D printing, Laser cutting, electronics, engraving, electronic Device png 802x401px 204.53KB
- Label printer Barcode printer Thermal printing, printer, electronics, label, retail png 755x756px 471.57KB
- Metal, Laser Cutting, Computer Numerical Control, Machine Tool, Fiber Laser, CNC Router, Sheet Metal, Laser Engraving, Laser Cutting, Computer Numerical Control, Computer Monitor Accessory png 1067x497px 235.22KB
- Laser cutting Computer Icons Metal, laser, angle, rectangle, service png 1200x1200px 54.17KB
- Laser cutting Fiber Laser Laser engraving, cutting machine, engraving, metal, metal png 900x600px 357.18KB
- Large-format printer Offset printing Vinyl banners Digital printing, printer, ink, electronics, digital png 1024x625px 430.
24KB
- Dot-matrix printing Epson dot-matrix printer, printer, electronics, computer, electronic Device png 1130x1188px 306.42KB
- Laser cutting 3D printing Industry, technology, electronics, text, service png 512x512px 4.92KB
- Laser cutting Machining, Laser cutting, symmetry, monochrome, steel png 640x640px 161.21KB
- Xerox multi-function printer copier Paper, printer, angle, electronics, ink Cartridge png 469x500px 154.71KB
- Multi-function printer Hewlett Packard Enterprise HP LaserJet HP Deskjet, HP Printers, electronics, black, electronic Device png 742x742px 204.
63KB
- Barcode printer Label printer Zebra Technologies Printing, zebra, electronics, animals, label png 945x945px 205.87KB
- Multi-function printer copier Konica Minolta scanner, printer, electronics, electronic Device, fax png 600x840px 477.22KB
- 3D printing Selective laser sintering Selective laser melting Material, powders, angle, electronics, material png 960x500px 90.64KB
- 3D printing Metal Selective melting laser printer, printer, electronics, material, metal png 800x633px 488.57KB
- 3D printing Metal 3D Systems Manufacturing, metal surface, steel, material, metal png 940x940px 294.
63KB
- 3D printing filament 3D Kreator Business, printer, 3D Computer Graphics, people, small Appliance png 662x668px 361.91KB
- Paper printer Laser printing Toner, Cartoon printer, cartoon Character, supplies, ink Cartridge png 2252x1574px 646.74KB
- Machine tool Laser cutting Laser engraving, technology, angle, electronics, material png 1498x1497px 698.22KB
- Textile Folding Machine Woven fabric, textile, office, fabric png 700x611px 414.62KB
- 3D printing Stereolithography Formlabs Fused filament fabrication, printer, electronics, 3D Computer Graphics, orange png 1200x800px 389.
91KB
- 3D printing 3D modeling Printer Paper, printer, blue, angle, electronics png 800x600px 7.27KB
- Robot welding Robot welding Machine KUKA, address, electronics, metal, industry png 1000x1200px 1.58MB
- Multi-function printer Small office/home office Inkjet printing, SCAN, electronics, canon, office png 3000x2823px 2.57MB
- Laser printing Printer driver Multi-function printer, printer, computer Network, electronics, monochrome png 619x473px 192.26KB
- Canon paper Printer driver Inkjet printing, Inkjet Printers, computer Network, ink, electronics png 3100x2300px 845.
09KB
- Printer Laser printing Toner refill Toner cartridge, printer, ink, electronics, ink Cartridge png 600x600px 197.65KB
- Laser engraving Laser cutting Epilog Laser, others, engraving, business, laser png 800x626px 375.51KB
- Manufacturing Support Implementation Technical Support Computer project, others, angle, service, computer png 591x591px 38.79KB
- 3D Circle, 3D Printing, Manufacturing, Digital Light Processing, Stereolithography, Selective Laser Melting, Powder Coat And Inkjet Head 3D Printing, Manufacturing, 3d Computer Graphics, 3d Printing, Area png 1728x1728px 90.22KB
- Machine tool Laser cutting Laser engraving, others, miscellaneous, textile, machine png 2477x1859px 883.13KB
- Laser engraving Laser cutting, laser, miscellaneous, angle, laser png 1244x1052px 736.67KB
- Laser scanning scanner Faro Technologies Inc 3D scanner, others, 3D Computer Graphics, surveyor, laser png 768x632px 159.51KB
- Label printer Barcode printer Printing, scanner, ribbon, electronics, label png 1200x1216px 1.39MB
What is 3D printing?
Contents
- What is 3D printing and how does it work?
- What is 3D printing?
- Additive Manufacturing vs. Traditional (Subtractive) Manufacturing
- Benefits of 3D Printing
- How Does 3D Printing Work?
- Various types of 3D printing technologies
- Preformed layer melting
- Directed energy release
- Materials used in 3D printing
- Finishing work
- How is 3D printing used and what can be done with a 3D printer?
- Types of 3D printers
One of the most revolutionary ideas that has influenced manufacturing in the 21st century is the concept of 3D printing. 3D printing technology, also known as additive manufacturing, makes it possible to manufacture parts, structures, and products using a layer-by-layer technique controlled directly from a set of computer-based design instructions.
This approach offers several advantages over more traditional manufacturing techniques that rely on cutting tools to remove material to produce a structure with the desired dimensions and features specified in the CAD model.
The market for 3D printing services has grown significantly since its inception in the early 1980s. According to data released by a German company specializing in market and consumer data, the global market for 3D printing products and services was $12.6 billion in 2020 and is expected to reach $37.2 billion by 2026.
In this article, we will provide a complete breakdown of 3D printing and look at what it is, how it works, what types of 3D printing technologies are used, what types of materials can be used, and what products can be created.
What is 3D printing?
3D printing is a term used to refer to a number of specific technologies that allow the creation of a form by adding material one layer at a time until a finished product is produced.
The term 3D printing likely originated from one of the earliest technologies to be introduced to the field, known as Fused Deposition Modeling, or FDM for short.
This name was applied because the FDM method worked very much like a 2D inkjet printer that sprays ink onto paper in layers in a row at a time.
It is also important to recognize that the earliest 3D printing technologies were more consumer-oriented and were not considered to have commercial value as industrial manufacturing technologies .
The term "additive manufacturing" is a broader term that tends to be more associated with industrial applications of technology, such as prototyping or large-scale mass production of products, as opposed to more consumer-oriented uses.
While the underlying technologies may be basically the same, the size, throughput, speed, print resolution, and equipment cost will clearly differ when industrial or commercial applications are considered.
However, in this article we will use these terms more or less synonymously. It should be noted that a third term sometimes used in connection with 3D printing is direct manufacturing , referring to the fact that the process involved creates "tool free" parts directly from the CAD model.
Additive Manufacturing vs. Traditional (Subtractive) Manufacturing
The key difference that distinguishes 3D printing from traditional manufacturing technology is the use of an "additive" process versus a "subtractive" (removal, subtractive) process.
Traditional manufacturing techniques that are used to make parts are usually based on the idea that raw materials are processed into the desired shape with the desired characteristics using cutting tools.
Thus, the starting material, sometimes referred to as "blank", is larger than the desired final dimensions of the part and is "reduced" during the cutting process until the final dimensions are reached.
Therefore, the term "subtractive" applies to these processes, whether they involve milling, turning, milling, drilling, or other machining methods. Material is removed in the process to create the proper size and function for the part.
3D printing, by contrast, is "additive" in nature. No stock is used to cut the material from - instead the printer feeds the raw material, which is added layer at a time as needed to make the part.
The 3D image of the desired part or product, taken from the CAD model, is "cut" into a series of thin vertical layers, which are printed one on top of the other in succession, with each layer joining the previous or lower one, merging together to form the final product.
Depending on the printing technology used and the material from which the part is made, there are some differences in specifics, but in general this description gives an understanding of the main difference between the additive 3D printing process and the subtractive printing process.
Advantages of 3D printing
When comparing the additive process with the traditional subtractive process, some of the advantages of 3D printing over traditional manufacturing methods are immediately apparent.
Efficient use of material
Since the 3D printing process does not use cutting tools to remove excess material as in subtractive processes, material is used efficiently and less waste is generated.
It is estimated that around 98% of the material used in 3D printing ends up being used to create finished parts. Eliminates the need for lubricants and coolants holes.
These used cutting tools often operate at high speeds, are subject to frictional forces that require lubricant and coolant to be applied to the workpiece and tool to reduce tool wear. The methods used in additive manufacturing largely eliminate this requirement.
Greater portability and flexibility
Conventional equipment used in subtractive manufacturing operations takes up a large area and is not designed to be moved. Consequently, manufacturing operations must be centralized and parts must be delivered where needed, increasing delays and costs.
Many 3D printers are smaller and can be easily deployed to remote locations, allowing parts to be made where needed, such as making replacement components wherever the final product is deployed.
Cost savings
Many traditional manufacturing processes such as casting, stamping or injection molding require an upfront investment in tools such as creating a die or mold whenever a new part is designed for production.
In addition, these initial costs may be repeated if a design change is required after the initial die or mold has been made.
In terms of initial costs, the cost of acquiring high performance CNC equipment used in traditional manufacturing can be significant.
Additive manufacturing, as a direct manufacturing process, can create products without the intermediate design and manufacture of a mold or stamping die, thereby saving the costs associated with the initial tooling steps of traditional manufacturing.
And the cost of acquiring a 3D printer is much less than the equivalent costs that would be incurred to purchase traditional equipment such as lathes.
How does 3D printing work?
The process of 3D printing a part or product begins with a graphical representation of the object to be printed, usually as a 3D CAD model. Before the 3D printer can start printing the part, the graphical model needs to be processed using special software known as slicer software.
As the name suggests, this software takes a 3D model and generates a set of instructions for the printer, creating individual thin vertical layers or design fragments. Depending on the complexity of the object being printed and the resolution of the printer, the slicer software creates a large number of these layers.
A set of instructions for creating each layer of the product is then sent to the printer in sequence, and the printer will use the instructions to print each layer of the design before moving on to the next layer.
Gradually the part or product builds up on top of the substrate as the print head or nozzles are directed to place the material according to the design features and dimensions.
The substrate that the object rests on moves slightly vertically after each layer is added, preparing the printer for the next layer. The process continues until all layers have been printed.
Another key feature of the slicer software is to add instructions to the instruction set to create any necessary elements of the support structure. These elements are not part of the original design, but are required when the object is printed to ensure that the final design elements are rendered as required.
Because 3D printing requires the addition of material, which often has the consistency of a thick liquid or melted wax, the part will not be fully structurally stable until the material has cooled and solidified.
For example, printing a part that contains a hole may require the addition of a temporary support post because you cannot distribute liquid material through an air gap without allowing it to sag or sag. After cooling, the support structures can be removed from the printed part as part of secondary finishing operations.
Since there are a number of different 3D printing technologies, the printing process will differ depending on the technology used by the particular printer. But in general, the description above gives a general idea of how 3D printing works and how a 3D printer creates parts from an original graphic design.
Various types of 3D printing technologies
Since its introduction in the 1980s, the field of 3D printing has expanded and grown significantly. While Fused Deposition Modeling or FDM was one of the first methodologies developed, other new technologies were soon developed and introduced to the market.
In 2012, ASTM International created a standard terminology to describe various 3D printing technologies. They created seven broad categories associated with the discipline of additive manufacturing, namely:0006
Material extrusion
In material extrusion, thermoplastic material is fed into a heated nozzle and then deposited on a substrate or surface called a building platform.
Examples of specific technologies that fall under the category of material extrusion include deposition modeling or FDM and fused filament fabrication (FFF).
Photopolymerization
Photopolymerization begins with a liquid light-sensitive plastic material called a photopolymer that is exposed in a controlled manner to some form of light energy to cure and cure the liquid polymer into the desired part.
There are several technologies of this type, each using a variation of the light curing process, some using an ultraviolet laser and others using light frequencies in the visible spectrum.
Common photopolymerization techniques include stereolithography (SLA), digital light processing (DLP), and continuous fluid interface manufacturing (CLIP™).
Binder Injection
Binder Jetting or Binder Jet Printing is a category of 3D printing that uses a liquid chemical binder to bond particles of a base material, which is usually in powder form.
Examples of technologies that use binder spraying include powder bed 3D printing with inkjet head (PBIH), gypsum-based 3D printing, and color inkjet printing (CJP).
Pre-bed melting
Powder bed fusion processes are similar to binder spray processes in that a powdered or granular material is fused together to form the desired part.
The key difference between the two categories is that powder bed fusion joins the material using a thermal process rather than a chemical binder. Thermal energy is applied to the material using a laser, an electron beam, or other methods depending on the specific 3D printing technology used.
These technologies enable metal 3D printing, and the five most common examples that fall under the category of powder bed fusion include selective laser sintering (SLS), direct metal laser sintering (DMLS), selective laser melting (SLM), electron beam melting (EBM) and selective thermal sintering (SHS).
Directed energy release
Directed energy deposition processes also use thermal energy to bind material, but they do so at much higher energy levels and are used with metals whose melting points are higher than those of polymers.
Technologies that fall under the category of directed energy deposition include laser metal deposition (LMD) and electron beam additive manufacturing (EBAM).
Material Inkjet
Material inkjet processes, as the name implies, use nozzles, similar to those used in inkjet printers, to spray thermoset photopolymer material onto a build platform and then cure the material using a UV light source. radiation.
Some of these processes, also known as Multi Jet Fusion and Polyjetting, use multiple jets to apply material and allow parts made from multiple materials to be easily printed, allowing shapes to be created from different materials in a single print. operation. The most common material jetting technology is known as multi-jet modeling (MJM).
Sheet lamination
The last category of 3D printing processes is known as sheet lamination. Sheet lamination joins together thin layers of material in the form of sheets using either chemical binders or ultrasonic welding, depending on the material used.
The two most common examples of a sheet laminating process are known as Laminated Object Manufacturing (LOM) and Ultrasonic Compaction (UC).
The table below provides a summary of each of the seven categories of 3D printing processes and shows the related technologies that fall under each category.
The table also provides a brief overview of how these printing technologies work and links to our respective guides for a deeper understanding of each of these technologies.
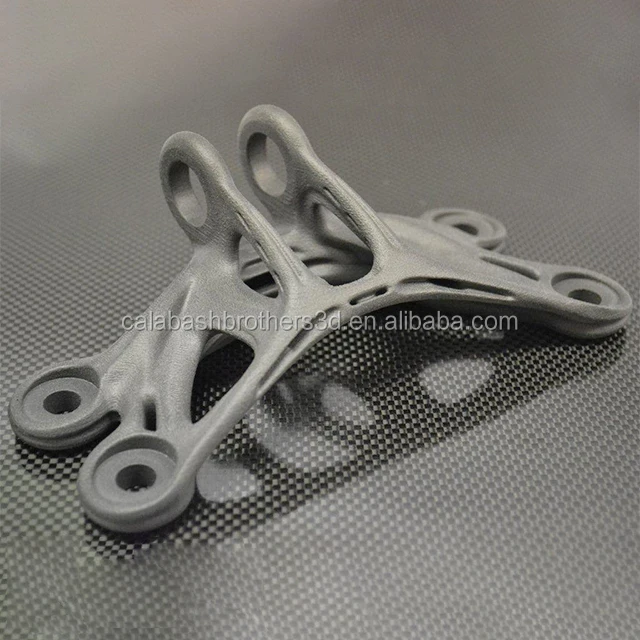

Melting in preformed layer
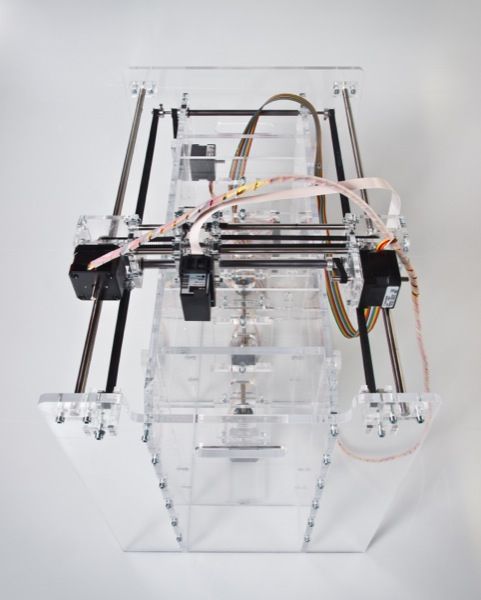
Directional Energy Release
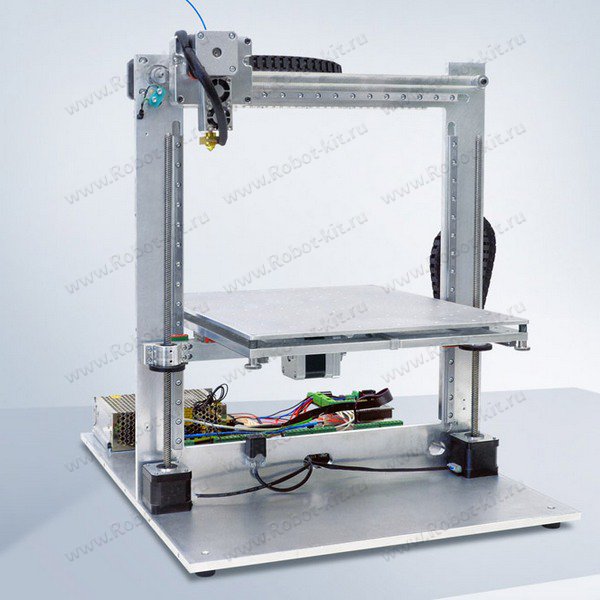
Materials used in 3D printing
Historically, the material of choice for use in 3D printers has been polymers due to their low cost, ductility and ease of fabrication. Data released by Statista shows that as of July 2018, about ¾ of the materials most commonly used in 3D printing worldwide fall into this category.
Advances in additive manufacturing have meant that a wider range of materials are available for use today. This includes metals such as titanium and stainless steel, as well as ceramics and plaster.
But as the use of 3D printing has expanded to include more than just an alternative for producing parts, the list of materials used in printers has also expanded.
While plastics/polymers have taken the lead so far, other material options are also showing an increase in their use. According to Statista, growth in sales of metals, ceramics and other non-plastic/polymer materials will exceed the compound annual growth rate (CAGR) of both of these standard materials.
Below is a brief overview of many of the most commonly used material options in additive manufacturing. These materials have been grouped into plastics, powders, resins, metals, and others.
Plastics
Plastics used in 3D printing include the following:
- PLA or polylactic acid is an environmentally friendly material that comes from sources such as sugar cane or corn starch. It has a low melting point and is easy to work with.
- ABS, or Acrylonitrile Butadiene Styrene, is available in several colors and is popular as a material for craftsmen and hobbyists to use. This material is sometimes referred to as "Lego plastic" due to its use in building toy blocks for which the Danish manufacturer is well known.
- PVA, or polyvinyl alcohol plastic, is often used to print temporary support structures that must subsequently be dissolved in post-print operations. It is also used in inexpensive printers for home use to create decorative items where structural strength is not required, or to print items for temporary use.
- Nylon, also called polyamide, is a synthetic thermoplastic known for its durability, limited tendency to warp, and ability to accept dyes or dye. It is often used with FDM 3D printing and FFF 3D printing.
- PET/PETG, which stands for polyethylene terephthalate (where G stands for glycol modified), is used as a printed material in a modified form and provides flexibility, strength and resistance to high temperatures and mechanical stress.
- PC or polycarbonate is a material that requires printers with a higher nozzle temperature.
- ASA, or Acrylonitrile Styrene Acrylate, is an alternative to ABS, often used in automotive printing, and offers a strong, solid part that is durable.
For FDM printers, these materials are typically filaments extruded into thin cross sections and wound onto spools.
Resins
Resin materials are used in light curing printing technologies such as stereolithography (SLA), digital light processing (DLP) and continuous fluid interface manufacturing (CLIP™).
They fall under the general category of bath photopolymerization described earlier, where the material is in a liquid state prior to curing with UV laser radiation or other visible light frequencies.
Metals
Metal 3D printing is done using processes that produce higher levels of thermal energy due to the higher temperatures required to sinter or fuse these materials into a solid part of the desired shape.
Powder welding technologies such as selective laser sintering (SLS), direct metal laser sintering (DMLS), selective laser melting (SLM), electron beam melting (EBM) and selective thermal sintering (SHS) are used with metals.
Directed energy deposition technologies such as laser metal deposition (LMD) and electron beam additive manufacturing (EBAM) can also be used with metals.
common materials include:
- Stainless steel
- Gold
- Nickel
- Aluminum
Depending on the specific printing technology, metals can be in the form of powders or wires.
Other materials
There are other materials that are also used in 3D printing, including graphene, graphite, carbon fiber, and special alloys such as nitinol, which is made from nickel and titanium and is used in medical devices.
Finishing work
After the print operation is completed and the part is removed from the 3D printer, some finishing work may be required before the product can be used. The extent to which finishing is needed depends on a variety of factors, including:
- Intended use of the item
- Specific process and printer type used
- Printer resolution
- Material used to print the part
- Approval drawing requirements
3D printed parts and products final processing is applied. These activities include grinding, painting, machining, heat treatment, painting, varnishing, grinding, drilling, milling, turning and others.
Also of note is the fact that over the past two years just over 70% of manufacturers have reported leaving the part unfinished, meaning no finish has been applied.
This may be indicative of an improvement in process quality over time that has reduced the need for finishing, or may be indicative of another result such as a shift in product types from those requiring finishing to others where such secondary operations were not carried out. significant.
This may be the case when moving towards products for more decorative purposes rather than more functional uses driven by technical specifications for tolerances and surface flatness.
This may also reflect the use of technology for rapid prototyping and proof of concept, where the focus is not so much on the final appearance of the part as on whether the prototype, as built, will fit the intended need.
How is 3D printing used and what can be done with a 3D printer?
Evidence from multiple sources points to the versatility of 3D printing as a technology that can be applied to a variety of industries and products.
One commonly cited use of this technology is the ability to rapidly prototype early engineering models and validate conceptual design mockups.
According to the survey data published by Statista, the applications that were most used by the respondents were:
- Prototyping
- Proof of concept
- Manufacturing
- Research/education/R&D
- Mechanical parts
- Tools
/dental devices/dentures. Mass production was mentioned, but not as often.
Other data published by Hubs, a Protolabs company, in their of the Additive Manufacturing Trends Report 2021 , shed light on some additional trends related to 3D printing related to COVID-19 and the use of this technology in general. Among the findings from the surveys were the following key data summarized in the report:
- The pandemic may have slowed the pace of market growth, but it has not stopped the slowdown in its overall usage. About 50% of respondents said their use has not changed during COVID, while 33% indicated an increase in use during the pandemic.
- Users reported prototyping (47%), fixtures and fittings (21%), and aesthetic/functional end pieces (29%) as the most frequently cited 3D printing applications.
- With these mentioned uses, 64% of 3D printing production runs were 1 to 10 parts, 22% were 11 to 50 parts, and 8% were 51 to 100 parts. This aligns with the main use for prototyping and print proof of concept mentioned earlier. In the future, there will be an increase in the use of technology as a means to increase production cycles.
- Finally, when asked about barriers to wider use of 3D printing, respondents indicated that the top factors preventing wider use are:
- Limited experience (19%)
- Material choices are low (14%).
It is interesting to note that there are additional applications for 3D printing in environments and industries beyond traditional industrial part production. Among them is the use of 3D printing using various materials such as concrete, human skin and food.
- Construction firms have developed large-scale 3D printers that can create structures such as houses and bridges using concrete as a material.
- Researchers are experimenting with 3D printers to develop ways to use skin cells to create printable inks that can create human skin with all of its inner layers as an alternative means of creating tissue to help burn victims.
- Apparel and footwear manufacturers are looking to additive manufacturing as a means to allow consumers to create clothing tailored to their needs, wishes and sizes, as an alternative to off-the-shelf options.
- Food is seen as another arena in which 3D printing will play an increasingly important role as kitchens begin to experiment with using 3D printers to produce edible food and unique shapes that would otherwise be impossible to produce.
The future of additive manufacturing is ripe for expanding the scope and depth of what can be printed.
Types of 3D printers
Various types of existing 3D printers implement one of the printing technologies mentioned earlier. The price range and sophistication of the machines range from low-cost models intended for consumer use to industrial 3D printers that can handle high-volume parts production, metal-based parts, or tighter tolerance requirements.
There are certain printer options and specifications to consider when choosing a 3D printer for an application.
Printer manufacturers often provide guidance in the form of web applications or downloadable white papers to help understand the 3D printer market. One such example provided by BCN3D suggests that general factors, including these, should be weighed against needs when considering purchasing a 3D printer:
- Build Volume - Determines the maximum model dimensions that can be printed.
- Layer Resolution - represents the distance between successive layers along the Z axis of the printer and determines the resolution of the model along the Z axis. Smaller nozzle sizes provide more resolution and detail that can be printed in the XY plane.
- Print Speed - Measures the speed at which media can be deposited or applied to form a printed object. Lower speeds can provide better quality, but the trade-off is that it takes longer to print.
- Multiple Extrusion - Some printers may provide multiple extruders that may support the ability to print different materials or colors at the same time. It may also allow the necessary support structures to be printed, which allow complex geometries to be printed.
- Printer Materials - Determine if the printer is compatible with the specific materials required by the application.
- Print surface - The surface on which the printed material is applied, sometimes called the build plate or substrate.
Learn more