Eco friendly 3d printing materials
Eco-friendly 3D filament guide - what are the possibilities and innovations
What is eco-friendly 3D filament?
Eco-friendly 3D filament is a new alternative to the classic plastic filament. 3D printing requires a lot of energy and often uses non-biodegradable materials. For example, ABS is made from petroleum. It is one of the most common 3D printing materials when it comes to filament extrusion.
However, innovations now offer the opportunity to 3D print ecologically and responsibly at a lower cost. Many biodegradable filaments, made from recycled materials, have been developed to be environmentally friendly and have become alternatives to plastic filaments.
By incorporating a biodegradable plastic base (in the form of fibers or powders), it is possible to create filaments that include a high percentage of organic material.
3D printing from recycled plastics
How to make 3D printing materials from plastic waste
Thanks to Tyler McNaney’s Filabot, or MIT’s Recyclebot, it is possible to create ecological filament at home by recycling plastic waste. These machines turn waste into a 3D filament that a 3D printer can use.
A bottle of milk recycled by the Filabot converts into 2.5 meters of 3D filament.
First, the machine crushes recyclable plastic waste (bottles, boxes, etc.) to transform it into plastic pellets (or granules). The recycling machine then heats and extrudes these pellets into the shape of filament. The filament is then wrapped around a spool so that it can be reused again by a 3D printer.
Reuse 3D printed objects and plastic print waste
3D printing requires patience and involves a lot of testing to perfectly configure a 3D printer and produce quality 3D models. Many of these tests result in print fails, extra material, supports, or simply old pieces that are no longer useful.
Plastic waste extruders such as the Filabot or ProtoCycler can recycle this plastic waste. This innovation, with its ecological aspect, also represents a big cost saving for the users who can reduce their 3D filament expenses.
Buy 3D filament made from recycled materials
The Dutch startup Refil sells 3D filament made from two recycled plastics, ABS and PET. These two plastics mainly come from plastic bottles and car dashboards. This award-winning innovation is called Refilament.
According to Refil’s co-founder Casper van der Meer, the recycled filament (free of toxic additives), boasts the same features as ordinary filament and is available at a price between 30 and 40 dollars a spool.
Black ABS 3D filament produced by Refil from old car dashboards.3D printing with biodegradable 3D filament
PLA, a cornstarch-based 3D printing material
With ABS, PLA is the most commonly used 3D printing material when it comes to filament deposition.
PLA is made from cornstarch. It is compatible with most 3D printers using extrusion 3D printing technology.
Unlike ABS, PLA is a biodegradable material. Thanks to its non-toxicity, PLA can also be used to 3D print objects that will be in contact with food.
The main weakness of PLA is its high sensitivity to moisture and its tendency to break rather than bend. It makes it more difficult to handle than ABS.
Green and blue frogs 3D printed from PLA.Sustainable 3D printing: paper, an alternative to plastic
Mcor Technologies (now CleanGreen 3D) is a 3D printer manufacturer that has successfully made 3D printing material from paper. Their Laminar 3D printing technology successively cuts sheets of paper and glues them onto each other to 3D print an object.
Paper is not as environmentally friendly as PLA, but it is a serious alternative to more toxic materials. It also costs much less: a ton of paper costs around €1,300 while a ton of PLA costs between €5,000 and €10,000.
Plant-based 3D printing materials
Many plant-based filaments have been developed, such as the soy-based FilaSoy or SeaWeed, a material made from seaweed. The Algix from 3DFuel is also available and is made from nuisance algae.
Wood is also a material that is used to make natural 3D filaments. For example, Laywood is made up of 40% of wood, which gives it a touch and appearance similar to wood.
ColorFabb has even developed two 100% organic filaments: the WoodFill made up of 70% PLA and 30% wood fiber, and the BambooFill, half bamboo, and half PLA.
Finally, oysters and coconuts have also been experimentally used to create new 3D filaments.
A small 3D printed elephant made with ColorFabb’s Woodfill material.3D printing with recycled building materials
3D printed houses made from recycled concrete
The Chinese company WinSun Decoration Design Engineering received attention in 2014 by 3D printing ten houses in less than 24 hours. These were 3D printed from a mix of cement, industrial waste, and recycled fiberglass. In 2015, they did it again, this time with a four-story building, and also succeeded in less than 24 hours.
In January 2018, the same company 3D printed bus stops at Fengjing Town in Shanghai.
In Amsterdam, a canal house was also 3D printed by DUS Architects in 2016. This house, designed in partnership with Henkel, is 3D printed with bioplastics. It consists of 80% ecological materials.
Examples: two innovative projects to recycle plastic waste
An eco-friendly 3D printer launched by Coca-Cola, 3D Systems, and will.i.am
will. i.am, who was previously creative director of the 3D printer manufacturer 3D Systems, had teamed up with Coca-Cola to create Ekocycle. The Ekocycle is a 3D printer that uses a 3D filament, of which 25% is made from recycled plastic bottles.
“Ekocycle’s goal is to collaborate with the world’s most influential brands and use technology, art, and fashion to change an entire culture. It’s the beginning of a more sustainable lifestyle through 3D printing. Waste is waste only if we waste it.”
will.i.am
Ekocycle will be able to 3D print objects with a build volume of one hundred cubic centimeters, with a minimum layer thickness of 70 microns.
Three 500ml Coca-Cola bottles are needed to make one Ekocycle cartridge. The available colors Coca-Cola’s emblematic colors: red, black, and white.
will.i.am, a founding member of the Black Eyed Peas and 3D Systems’ previous artistic director, presenting the Ekocycle eco-friendly 3D printer.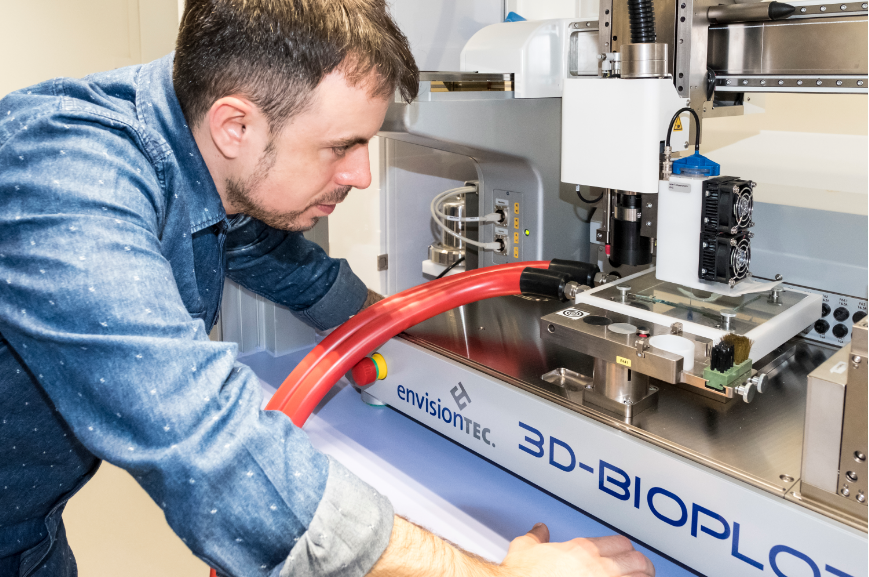
Clean beaches and 3D printed souvenirs of the sea
In 2014, two Swiss entrepreneurs, Jennifer Gadient and Fabian Wyss, launched the Seafood Project. This project aimed to clean the beaches of France, Spain, and Morocco by recycling all plastic waste into 3D printed objects.
The couple left France in October 2014 and drove down to Morocco in their van, in which they had all the necessary equipment for 3D printing.
On the beaches, they recovered plugs, bottles, and other plastic waste. With the help of an extruder and a shredder, they transformed this waste into 3D filament. They then 3D printed objects with an Ultimaker 3D printer and sold them on their website.
Picture of Jennifer Gadient and Fabian Wyss in front of their van, equipped with a 3D printer to recycle plastic waste from beaches.Eco-Friendly 3D Printing Filament Supplier
We are a US company providing 3D printer filaments, 3D printers, Consultative Print Services, and Specialized Coatings that meet our customers’ priorities using sustainable methods. The company’s innovative solutions are for educational and industrial professionals that demand materials whose quality and value are the best on and for planet Earth.
- Our products are developed and manufactured in the USA
- Our products are developed with materials that support environmental stewardship and sustainability
- Project and Product Design Capabilities for custom products, part/product concept, printing services
- Always innovating with the latest filament materials – Check out The Terrafilum Ecologic ABS Filament!
Read More
We use our experience in plastics to manufacture high-quality wire rope coatings to protect your cable from the elements.
More Information
Exclusive videos from our online conference where Jeremy Simon (3D Universe), Matt Griffin (Ultimaker), and Chris Jackson (Terrafilum) share which materials are available for use in 3D printing, how they perform, and what they are commonly used for.
Read More
Not too long ago, the printing speed and limited output of 3-D printers made them suitable only for rapid prototyping. But in the coming years, 3-D printers will be at the heart of full-scale production capabilities in several industries.
Read More
Terrafilum™ is satisfying clients’ 3D printing needs with one of the highest quality eco-friendly filament solutions.
Read More
We provide a quality product using earth friendly materials that would have found a home in a landfill.
Shop Now
Terrafilum™ has been awarded the recognition of “Top 10 3D Printing Solution Providers of 2019” by Manufacturing Technology Insights.
Read More
Terrafilum Engineered Filaments started with one idea in mind: to develop and provide 3D printer users the highest-quality, eco-friendly 3D printing filament solutions on the market. We set out to exceed all our customers’ 3D printing needs. We have accomplished that goal, and we do it right here in America!
We’ve taken great care to create several types of recycled, and recyclable filaments to meet any level of demand required by our clients… big or small. Whether your project requires custom filaments for large-scale industrial projects or needs to meet strict engineering design requirements, we have you covered from start to finish. When you purchase premium quality sustainable 3D printing filament from Terrafilum, you will receive a product that has been carefully tested. During this testing, we ensure that the appropriate amount of recycled material has been used to create an environmentally filament that remains stable throughout the printing process.
Like you, we also love our planet. That’s why we have painstakingly considered the environmental impact our products could have on our environment. We determined that using recycled plastic for 3D printing is a fantastic solution. We are happy to provide our clients with a recycling program that ensures the maximum amount of material that might otherwise be discarded as waste, is returned to us where it is recycled and repurposed into more of our wonderful product.
We intend to stay on the leading edge of this exciting new industry with our eco-friendly 3D printing filament. We will continue to stay earth conscious while developing newer, cleaner, and more sustainable solutions for all of our clients’ 3D printing needs.
Featured Product Videos
PLA ABS
PLA-TPE
PLA-TPU
TOUGH PLA
Finding What Fits Your Needs
The possibilities for creating stunning, accurate, 3D printed products, and art pieces are limitless! Terrafilum carries a complete line of recycled filaments that cater to any project no matter the size, or complexity.
If you are already a seasoned professional with your own 3D print shop, we have exactly the type of recycled filaments required to meet the tough demands of a custom manufacturing, injection moldings, and those tricky, hard to build products that leap from the minds of your Design Engineers.
Maybe you’re simply a hobbyist who wants to learn more about what can be done with a 3D printer, or maybe you already make a custom product that you sell online and want to improve on existing designs, or create new products and aren’t sure what your next step should be.
Terrafilum offers complete guidance with a full team of Consultants (link to consultant page here, maybe?) standing by ready to help you take the next step in growing, and improving your product line. No matter where you are in your 3D printing journey, Terrafilum is ready to serve and help you bring your customize vision to life.
Contact Us
Spools For The Eco-Minded
Anytime an innovation takes place that finds a new use for plastic derived from petroleum there is going to be concern over the damage that might be caused to our already struggling environment. The good news is that the 3D community is hitting this issue head-on from these early stages of development.
Terrafilum is dedicated to offering the safest, most environmentally sustainable solutions to polymer waste on the market today. From the actual filament itself to the very spool it comes with, we are striving to use as much recycled material as we can possibly pack into our product. We have even developed an unused materials return program to ensure that as little of our product ends up in your local landfill as possible!
All we need you to do is to package up your unused, unwanted, or wasted material and send it back so that we may recycle it into new products. Even prototypes that didn’t quite make the cut can now be re-introduced to your product line as a perfectly finished product by recycling the material. It’s that easy!
Together we will move 3D printing forward into a waste-free future where anything can be printed without any harm to Mother Earth.
For you… for our future…. and for our planet!
Spools For The Eco-Minded
Anytime an innovation takes place that finds a new use for plastic derived from petroleum there is going to be concern over the damage that might be caused to our already struggling environment. The good news is that the 3D community is hitting this issue head-on from these early stages of development.
Terrafilum is dedicated to offering the safest, most environmentally sustainable solutions to polymer waste on the market today. From the actual filament itself to the very spool it comes with, we are striving to use as much recycled material as we can possibly pack into our product. We have even developed an unused materials return program to ensure that as little of our product ends up in your local landfill as possible!
All we need you to do is to package up your unused, unwanted, or wasted material and send it back so that we may recycle it into new products. Even prototypes that didn’t quite make the cut can now be re-introduced to your product line as a perfectly finished product by recycling the material. It’s that easy!
Together we will move 3D printing forward into a waste-free future where anything can be printed without any harm to Mother Earth.
For you… for our future… and for our planet!
Mar 28, 2022
We collect and reuse ALL types of unbroken 3D printing spools There are 3 ways to be green: If you’re local, please feel free to drop them off at our facility. If you would like to get them out of your maker space, please collect 6 or more spools, box them, note the...
read more
Apr 21, 2021
Terrafilum® Engineered Filaments is proud to announce its new biodegradable Terrafilum® & EcoLogic® ABS Eco-One® filament. Terrafilum® Engineered Filaments (https://www.Terrafilum.com) is a US company that provides 3D printer filament solutions that intersect...
read more
Mar 23, 2021
Terrafilum® Engineered Filaments is proud to announce the inclusion of ASA Filament in its line of products. The filament will currently be available in black, white, and natural colors. To build and strengthen their 3D Filament business, Terrafilum® has added ASA...
read more
Contact Us
Your Name (required)
Your Email (required)
Your Message
Eco-friendly use of 3D printers in the home and industry
Vegetarianism, electric cars, green energy. Increasingly, people are beginning to think about the destructive impact of humanity and production on nature.
Global warming (this is especially noticeable in the last decade), pollution of the world's oceans, garbage dumps, the extinction of some animal species or even entire ecosystems. If you do not start to fight this today, then in a hundred years, hardly anything will remain of the former natural greatness.
3D printing, due to its versatility, helps many scientists and enthusiasts in various fields in solving large and global problems, for the conservation and ecosystems of our still green planet.
Sustainable production
First of all, 3D printers help to make production more environmentally friendly. Using 3D printing instead of traditional manufacturing methods helps reduce waste and greenhouse gas emissions.
Air Emission Reduction
Smoke, garbage, gases, toxic fumes are frequent "companions" of traditional production methods. However, they can be significantly reduced or completely eliminated if a 3D printer is working in the workplace or at home.
Mass production vs. 3D printing
At first glance, it seems that mass production is less harmful to nature than piece-by-piece production on a 3D printer. But it turned out that this is not entirely true. Joshua Pierce and colleagues traced the life cycle of three household items - an orange juicer, parts from a children's designer and a drainpipe segment.
Joshua Pierce, Michigan Technological University Scientist USA
It turned out that the production of, at first glance, such ordinary household items consumes a huge amount of resources - the extraction of raw materials and their processing, production, storage and delivery to the final consumer. In mass production, stamping or casting is usually used, after which plastic scraps are sure to remain.
3D printing can significantly reduce the production chain, and consequently, energy costs (by about 40-60%). After all, 3D printing (provided that the client has his own printer) does not require delivery - it is enough to send a digital 3D model. Printing can be more accurate and leave less plastic waste behind. A 3D printer can even produce hollow or lattice parts that are technically impossible to mass-produce by injection molding or moulding.
Reduced fuel consumption
In the world, more and more manufacturers of cars and motorcycles are beginning to develop the direction of electric motors. There are new and more affordable electric vehicles, the infrastructure for the maintenance of electrical engineering is developing. Many countries set themselves the goal of reducing the use of fossil fuels as much as possible in the near future.
Strati 3D printed electric car
But unfortunately, abandoning fossil fuels in the next few decades is a utopia. But 3D printing is already helping to at least reduce the amount of fuel consumed. This is achieved due to the maximum lightening of the weight of both the machine itself and the mechanical components of the internal combustion engine (internal combustion engine).
Engine hood hinge, 3D printed on the left and sheet metal on the right
Sustainable production
3D printing helps not only to reduce industrial emissions into the atmosphere, but also helps to find and implement new ideas. After all, each owner of a 3D printer can himself model and manufacture a device or object that, in his opinion, will help to resist climate change.
Eco glasses
Disposable plastic cups are a headache for environmentalists around the world. According to statistics, the average person uses a plastic cup for 15 minutes, and it will take from 400 to 450 years to decompose in the garbage.
Plastic, due to its properties, is difficult to replace, especially in the food industry, but some enthusiasts are trying to do it. Jun Aizaki thinks he can solve this problem with pumpkins.
HyO-Cups or natural cups
Even prehistoric people adapted to use bottle gourds as reservoirs for water. Thanks to the 3D printed shapes, you can give almost any shape to a growing pumpkin.
gourd in the form of a jug
Animal rescue
3D printers are actively helping our smaller brothers. In addition to medical uses such as prosthetics, 3D printing helps preserve and restore entire ecosystems.
Animal prostheses
The biggest challenge in animal prosthetics is the creation of an often miniaturized but lightweight and precise prosthesis. Manually or by other methods, this is sometimes impossible. In this case, the only way out is 3D printing.
Curano Cat
Curano the cat lived a full life for 9 years, delighting his owners, until he got cancer. Curano's owners did everything possible to save their pet and although the cancer receded, Curano's back left leg was badly damaged. Amputation of the leg could create new problems and it was decided to try to replace the patella with an implant.
The miniature implant was 3D printed from a cobalt-chromium alloy using DMLS (Direct Laser Sintering) technology. It was impossible to manufacture by any other means, because the implant must not only be miniature and durable, but also completely repeat the complex relief for high-quality integration into the bone.
Holly horse
Holly is a ten year old mare who suffered from laminitis.
Laminitis is a disease of artiodactyls resulting from poor circulation of the hoof plates. Due to laminitis, Holly experienced severe pain in her legs, not only when walking, but also when standing.
Veterinarian Luke Wells-Smith heard of successful attempts to make custom titanium horseshoes for racing horses.
3D printed titanium horseshoes
The guys from the Australian National Science Center were imbued with Holly's misfortune and decided to help. In collaboration with a equine orthopedist, special horseshoes were created for Holly. They made it possible to lighten the hoof and more evenly distribute the load on the legs.
Holly's hoof scan
The new shoes helped Holly start not only walking without pain, but also running.
Akut sea turtle
The collision with the propeller of the boat was unfortunate for the Akut-3 sea turtle. Most of the upper and lower jaws were missing. This meant almost guaranteed slow death for the tortoise, but she was lucky.
The Tortoise Research and Rehabilitation Research and Rehabilitation Center, where the turtle ended up, turned to the Turkish company Btech, which specializes in medical 3D printing. Btech was able to scan and fabricate the missing part of the Akut jaw from titanium.
3D model of the prosthesis for Akut on the left and the finished prosthesis on the right
The surgeons succeeded in implanting the turtle's titanium jaw, and after a successful rehabilitation, it can be released into the wild.
Turtle with prosthesis
Cleopatra tortoise
Nicola Novelli picked up and left a small land tortoise. But due to malnutrition, the shell of the turtle, Nicola called her Cleopatra, was deformed (had the shape of a pyramid) and thinned. If the shell had cracked, then Cleopatra could have died from an infection.
Cleopatra's deformed, pyramidal shell
Nicola approached Colorado Tech University with a request to make a prosthesis for Cleopatra. Specialists from the university and a 3D printing company in Denver scanned and made a shell overlay from polylactide, a biodegradable, biocompatible polymer. Due to the complex relief of the shell, the model had to be printed in parts.
Cleopatra with escutcheon
Since Cleopatra is still a teenager and will continue to grow with age, the “prosthesis” will have to be changed periodically.
Hermit crab houses
In the wild, it's bad to be small and weak. But hermit crabs were able to adapt and use empty shells of gastropod mollusks as a reliable shelter.
Hermit crabs
Due to the pollution of the beaches, many hermit crabs, in search of a new "house", fell into deadly traps from plastic bags, bottles, canisters and died. And natural shelters are becoming less and less. Hermit crabs have to use plastic garbage, which is not at all suitable for this.
Hermit crabs use rubbish as a home
Some enthusiasts are trying to help the unfortunate crustaceans and are trying to make them a worthy replacement house.
For example, MakerBot employees created the project "Shelter", where they offer anyone who wants to design a 3D model of a shelter for a hermit crab. The best works will be 3D printed and tested by crayfish.
From concept to implementation of 3D printed crayfish houses
But the Japanese artist Aki Yamomata, inspired by the idea of a peaceful exchange of land between countries, implemented a project of printed transparent houses for hermit crabs in the form of small towns.
Cancer in a new home made with photopolymer printer
To make sure the new inhabitants liked the houses, they were based on tomographic images of shells, finalized in a 3D editor. Finished models are made of transparent resin on a photopolymer printer.
Conservation and support of ecosystems
In addition to prosthetics, 3D printing helps, although not to avoid some environmental disasters, but at least to slow them down. And this can give scientists more time to figure out the reasons and reach out to people.
Great Barrier Reef
It is the largest and oldest coral reef in the world. It is so huge that it can be seen from space (the area of the Great Barrier Reef is about 344,400 square kilometers). In addition, corals are home to many species of fish and other marine life.
Great Barrier Reef from space
But despite its gigantic size, it is endangered. Due to rising water temperatures, pollution of the world's oceans and climate change, the endosymbiotic algae that give corals their bright color are slowly dying out.
Scientists from the University of Sydney are using 3D scanning and 3D printing to save the Great Barrier Reef. Using 3D scanning, a detailed map of the reef was built. With it, you can track and predict the most vulnerable places.
Using a 3D printer, scientists are making a variety of structures that can support the Great Barrier Reef. For example, sections are printed that serve as a home for algae-eating fish that kill corals. Previously, special blocks or prepared, sunken ships were used for this purpose, but 3D printing makes it possible to imitate the natural structure of the reef much more accurately.
Sandcrete mix artificial reef
Restoring dead ecosystems
Scientists plan to use this technology not only to maintain existing ecosystems, but also to restore those that have disappeared. After all, to date, about a third of the world's coral reefs have been destroyed.
Thanks to 3D printing, there is a chance to at least slightly improve the situation. Using the new Modular Artificial Reef Structures (MARS for short) technology, scientists are trying to introduce 3D printed structures that can become a home for reefs.
Artificial “reef” on the left - recently installed, on the right - after some time
The advantage of such block structures is the ease of installation. Indeed, for their immersion and installation, cranes or other equipment are not required. Several divers can deliver them to the bottom in separate blocks. Each block has hollow sections that are filled with rebar and special concrete for durability.
Modular system installed
One of the largest 3D printed "coral reefs" has already been placed in the Maldives.
Waste reduction
In addition to restoring ecosystems, it is necessary to reduce household waste emissions. And here 3D printing becomes a valuable assistant.
Cora Ball
Cora Ball is a development of the Rozalia Project. The Cora Ball is a small plastic ball that picks up the microfibers that spill from our clothes during the wash. This way, dirt and fibers that may have entered waterways and oceans will remain in the bin. After all, these microparticles can be eaten by fish and other animals.
Prototype Cora Ball
Although mass production was planned to be done by molding, the first batches and prototypes of Cora Ball were made on a 3D printer.
The second life of broken things
Any mechanism wears out and fails over time. Often, to restore the working capacity of the mechanism, it is enough to make a small plastic part. So thanks to 3D printing, many things do not end up in a landfill, further polluting our planet, but get a second life.
RU machine
Radio-controlled cars have long become not only children's toys. Many adults do not mind remembering their childhood and racing on an impromptu track.
RU machine
The weak point of all RC machines is the plastic suspension. For expensive replica models, you can almost always find spare parts, but for rare or Chinese models, they are not.
Instead of throwing away an almost working toy, you can make a broken element on a 3D printer. When modeling, you can even increase the strength of the part by adding stiffeners in weak places.
Rear hub of 1/18 scale car
Some enthusiasts 3D print the entire chassis. This makes it easy to replace broken elements and quickly refine and correct design flaws.
3D printed RC car chassis
The second life of the meat grinder
Even such seemingly eternal things as a metal meat grinder can break. The most annoying thing is that a part that does not have a strong load has broken.
Clamping nut for a meat grinder, made on a 3D printer
A variety of materials allows you to print on a 3D printer a replacement for almost any plastic part. It can be a gear for a blender, a plastic handle for a washing machine and much more.
In some situations, when the model is rare and old, there are no even original used spare parts. 3D printing allows you to give your favorite home appliance many more years of life, instead of rotting in a landfill.
Vehicle seal
Sometimes a small, cheap piece breaks in an important knot. But the manufacturer sells the necessary spare part only in the collection. Because of this, you have to not only overpay for the necessary part, but also throw away the unnecessary, albeit almost working, mechanism.
Washer nozzle for Toyota Avensis - 3D printed on the left, original on the right
A 3D printer becomes a “lifesaver” if you need to make a spare part that is already difficult or impossible to get. For example, this part is no longer produced, but the BU option could not be found or the delivery will cost more than the part itself.
Green Energy
The transition to green energy is an important step in reducing emissions of greenhouse (and not only) gases into the atmosphere.
Wind energy
Wind energy is a renewable and “clean” energy source. Despite some disadvantages (variability of wind power and therefore uneven power generation), it is promising for some countries. For example, in Denmark, in 2019, windmills generated 48% of the electricity consumed.
There are several options for wind turbines - with a vertical and horizontal axis of rotation.
Main types of wind turbines
Vertical-axial wind turbines have a lower efficiency compared to horizontal-axial ones, but their use requires that the wind speed be more than 6 m/s. In Russia, the average annual wind speed does not exceed 5 m/s, so wind turbines with a vertical axis are more often used.
Home wind generator
In Russia, "clean" energy sources are not very popular because of their high price. 3D printing helps enthusiasts design and build low-cost models of wind turbines.
3D printed home wind turbine
In an apartment building, there is hardly a place where a wind generator will be effective, but for example, in a country house, it can be a good helper in case of a power outage.
Wind turbine production optimization
An industrial wind generator is a complex mechanism of gigantic size.
Industrial wind turbine blade
Using only 3D modeling techniques, it can be difficult to correctly calculate all parameters. Thanks to 3D printers, it is possible to create a miniature copy of a wind turbine and test it in a wind tunnel. This helps to optimize and refine the design of wind generators, making them more efficient.
Prototype wind turbine being tested in wind tunnel
And some companies offer to print towers for wind turbines on a 3D printer. GE Renewable Energy, 3D printing specialists COBOD and LafargeHolcim (a manufacturer of cement and other building materials) have teamed up to develop the world's tallest wind turbine towers. This will reduce the cost of installing wind turbines and make them higher (200 meters instead of 100) than from other materials.
3D printed wind turbine tower
After all, the higher the wind generator, the more electricity it can generate in a year. For example, a 5 MW turbine at a height of 80 meters will generate approximately 15.1 GWh per year. The same turbine at a height of 160 meters - 20.2 GWh per year, which is 30% more.
Solar energy
Solar energy is obtained using special panels, consisting of photovoltaic cells, in which a series of physical and chemical processes take place under the influence of sunlight. There are several types of solar cells - monocrystalline, polycrystalline, amorphous (flexible, film).
In Russia, solar batteries are not very common due to the unprofitability of use in high latitudes.
Currently, developments are underway for the production of panels on a 3D printer, but the main use of 3D printing in solar energy is to print prototypes and accessories for panels.
Accessories for solar panels
South Dakota-based Peppermint Energy created FORTY2. FORTY2 is a portable solar panel with enough power to run a laptop, lighting, etc.
For the production of a prototype case, 3D printing was used on an industrial Stratasys printer. Thanks to 3D printing, it was possible to quickly produce several functional prototypes of the case and remove all the shortcomings.
For example, the first version of FORTY was too bulky and inconvenient to transport. The original design was greatly simplified. The use of a 3D printer has reduced production costs by about $250,000.
Hydropower
Most renewable energy sources (solar, wind) are fickle. Electricity obtained in this way must be “stabilized” - stored in batteries.
Water in this regard is more predictable. Industrial hydroelectric power plants have a number of disadvantages. For example, flood risk, desertification, human migration, etc. Small hydro-generators, in general, are devoid of the shortcomings of their industrial counterparts and do not have such a devastating effect on the environment.
Vortex turbine
The Belgian startup team Turbulent is trying to create a compact hydroelectric generator that is enough to provide electricity to 1-2 private houses. This will help people who are far from the power grid to provide their homes with electricity using the energy of streams or small rivers.
Hydro generator prototype from Turbulent
To make the turbine more accessible and cheaper, 3D printing has been chosen as a manufacturing method. According to statistics, 1.3 billion people do not have access to electricity networks, even more residents have constant power outages and are forced to use other, not environmentally friendly, energy sources (for example, gasoline / diesel generators).
River turbine
Ted Christopher spent several years developing a prototype river turbine capable of generating electricity without impacting the environment. The result of his developments was the Volturn system, named after the god of the river in Greek mythology.
The Volturn has a horizontal design that generates power and deflects river debris such as rocks, plants or logs.
The prototype was 3D printed and tested in local rivers. 5 turbines combined into a single system will be able to provide electricity to about 40 houses.
Plastic recycling
Plastic. Its properties, for the modern world, become both a salvation and a curse for the environment. On the one hand, plastic products are light and durable, you do not need to spend a lot of time on their manufacture. At the same time, not all types of plastic can be recycled. On average, a plastic product can decompose from 400 to 700 years, and unfortunately plastic rots not only in landfills, but also pollutes nature and the oceans.
Filament recycling
During 3D printing, plastic debris is inevitably left behind. These can be model supports or broken products, during the printing of which something went wrong.
3D printing failed
But used plastic can be shredded, mixed with fresh pellets, and reused (as long as the plastic is not biodegradable). In this case, 3D printing becomes almost waste-free.
On the Internet, you can find many options for home machines for the production of plastic thread. It can be a self-assembly machine, partially printed on a 3D printer.
Home self-assembly filament machine
Or a finished machine made at the factory. Pellets for plastic production can be easily ordered online.
Home filament machine
Plastic bottle filament
In addition to recycling used filament, enthusiasts have learned to print even from plastic bottles.
Homemade machine for making plastic thread from plastic bottles
Every day, around 100 million plastic bottles are used and thrown away around the world, and only 20% of them are recycled or reused. A plastic bottle can take up to 450 years to decompose! The use of plastic bottles as a material for a 3D printer will give them a new life in the form of useful things for the home.
Bottle printed spool
3D printed bottle gear
From one bottle, from 15 to 30 grams of plastic filament is obtained.
Totals
3D printers still have a long way to go to become truly sustainable, but even now, despite the imperfection of the technology, they can help reduce environmental pollution.
Already now, thanks to 3D printing, many good deeds are being done - it is possible to improve production technologies, even if only a little, to reduce the amount of emissions into the atmosphere and, of course, to try to restore the fragile natural balance.
It is important to remember that a 3D printer is just a tool and it depends only on the consciousness of a person whether it will be useful or continue to replenish landfills with unnecessary plastic waste.
Green materials: 8 new products to reduce carbon emissions
Sustainable Materials: 8 New Products to Reduce Carbon Emissions
The future of the construction industry will undoubtedly include "reducing carbon emissions" as a must. In addition to local primary materials, more and more new materials are becoming available. New materials can be developed in a number of ways, including low-carbon replacement, recycling, productivity improvements, and 3D printing. The new materials will not only be more sustainable and enable new building methods, but will also influence the starting point and direction of design concepts, leading to new buildings with new perceptions and spaces.
1. Low carbon replacement
In the building materials industry, low carbon building materials are the main way to reduce carbon emissions at source. Most of the new low-carbon materials are bio-based materials using renewable biomass or bio-derived raw materials, a new class of materials produced by biological, chemical and physical means such as dried luffa fibers, corn. Stems, mycelium, microalgae and so on. The use of biological or plant materials rather than fossil materials is an important solution to reduce plastic (waste), prevent settling, capture CO2 and reuse agricultural waste.
Dried Louffa Fibers
The Living Pavilion
Living's contribution to the 2021 Venice Biennale, The Alive Pavilion, explores the potential of multi-species architecture and the best ways to use the micro-organisms that surround us. Dried fibers of luffa, a fast-growing, inexpensive vegetable grown on vines in tropical and subtropical regions, are used to create the "Alive" exhibit. The surface of the luffa fibers creates a durable organic material that is well suited to harbor a range of microorganisms and is easily modified to create panels or partitions for architectural projects.
Mycelium Panel
Growing Pavilion / New Company Hero
The Growing Pavilion is a temporary Dutch Design Week space made from mushroom mycelium panels supported by a timber frame. The temporary pavilion was designed by set designer and artist Pascal Lebuc in collaboration with Krown Design, the studio of Eric Clarenbeck of Amsterdam-based Biobased Creations. The pavilion showcases its unique organic textures and colors to the public, giving biomaterials a new aesthetic meaning.
2. Recycling
To achieve sustainable development, the problem of waste must be addressed through research into the recycling and reuse of materials. Construction waste from iterations of urban renewal, ceramic waste from pottery manufacturing, hard-to-decompose plastics, and so on.
Ecopixel® Recycled Thermoplastic Waste
ALEX Chaise Longue
Atelier Mendini and Ecopixel have collaborated on a bold new project for the plastics recycling industry, combining "pixel blocks and recycled plastic". The part consists of several "pixel" blocks sized 24×24 mm. At 120°C, this material melts indefinitely without changing its original properties. It's actually a material made entirely from recycled low-density polyethylene, which means it can be remelted indefinitely without losing its properties.
Recycled Ceramic Tile
"Regeneration Tree" / YI DESIGN
Clay is the main component of both ceramic tiles and clay tiles. More than 10 million tons of ceramics are discarded in China every year, and this solid waste not only consumes a lot of land resources and energy such as coal, but also has serious carbon emissions that exceed the norms and cause significant environmental damage. Disposal of ceramic waste has become a problem. Created in collaboration with Italian architect Aldo Chibik, the recycled tree at Design China Beijing showcases visitors a uniquely designed building material made from recycled ceramic waste, as well as showcases design ideas on how to solve China's serious waste management problem. The recycled ceramic tiles have been collected, examined, crushed, crushed, mixed and tested in the laboratory.
3. Increasing Productivity
Due to their performance deficiencies, materials such as wood have been gradually replaced by steel and cement, but the revival of old materials is not lost due to technological means to improve their performance.
Wooden Bamboo
Living Garden / MAD Architects
"Wood Bamboo" is a new material made from bamboo that is reorganized and reinforced with bamboo and a high performance bamboo fiber based composite material developed in China and manufactured according to the patented technology of the Chinese Academy of Forestry. The tensile strength of "wooden bamboo" is three times that of steel of the same weight, while the cost of mass production is about the same, and the expected service life is up to 50 years, hence the name "wooden bamboo".
I-mesh Textile
Expo 2020 Dubai / I-mesh
I-mesh is a technical and environmentally friendly construction textile. It is made from durable, high performance fibers and can be used both indoors and outdoors. Carbon fiber, fiberglass, cheiron, aramid, and basalt fiber are woven into a web-like material using resin-impregnated threads.
4. 3D printing
The development of 3D printing technology has changed the perception of architecture and expanded the possibilities of design. The exploration of materials for 3D printing has led to the creation of architectural spaces with different textures and feel. 3D printing is also extremely useful for reducing carbon emissions in terms of material and labor use.
Fibre-reinforced concrete
3D printed robot-printed concrete book cabin / Team of Professor Xu Weiguo
The materials used to print the cabin are fiber-reinforced concrete developed by the team, in which no steel rods are added and no formwork is used. Cabin printing uses 2 sets of robotic arm printing systems, one for in-place printing of the building foundation and main structure, the other for pre-printing in place of the arched wall and domed roof.