3D printing baltimore md
3D Printing Service for Baltimore, Maryland
CapabilitiesCustom Online 3D Printing ServiceMarylandBaltimore
High Quality Baltimore, Maryland 3D Printing | 60+ Materials Available
Endless Options
Choose from millions of possible combinations of materials, finishes, tolerances, markings, and certifications for your order.
Easy to Use
Get your parts delivered right to your door without the hassle of sourcing, project management, logistics, or shipping.
Quality Assurance
Our number one job at Xometry is making your custom parts to your specifications.
Your Baltimore, Maryland 3D Printing Service: 3D Prototypes and Production Parts
A Global Leader in Industrial-Grade 3D Printing
Xometry is an industry-leading 3D printing service. Whether you need prototypes or production parts, we can make them for you in as fast as a day. We are your one-stop-shop for accurate, precise custom 3D printed parts at a low cost. Upload your 3D CAD file to get a quote and lead time within seconds. We use the latest additive manufacturing processes to build affordable functional prototypes & end-use parts in over 60 metals and plastics.
We offer eight high-quality 3D printing processes including selective laser sintering, fused deposition modeling, stereolithography, direct metal laser sintering, polyjet, Carbon DLS, binder jet metal, and HP Multi Jet Fusion. We use commercial and industrial-grade printers such as Stratasys Fortus 900mc and Fortus 450 FDM, EOS Polymer Laser Sintering (SLS) and DMLS, Concept Laser, SLM Solutions, 3D Systems, ExOne, and more.
Xometry's High Quality 3D Printing Services
Selective Laser Sintering (SLS)
Selective Laser Sintering (SLS) is a powerful 3D printing technology that produces highly accurate and durable parts that are capable of being used directly in end-use, low-volume production, or for rapid prototyping.
An additive manufacturing layer technology, SLS involves the use of a high power laser (for example, a carbon dioxide laser) to fuse small particles of plastic powders into a mass that has a desired three-dimensional shape. The laser selectively fuses powdered material by scanning cross-sections generated from a 3-D digital description of the part (for example from a CAD file or scan data) on the surface of a powder bed. After each cross-section is scanned, the powder bed is lowered by one layer thickness, a new layer of material is applied on top, and the process is repeated until the part is completed.
Download the SLS Design Guide.
Stereolithography (SLA)
Stereolithography (SLA) is a robust 3D printing technology that produces extremely accurate and high-resolution parts that are capable of being used directly in end-use, low-volume production, or for rapid prototyping.
SLA is an additive manufacturing process that focuses an ultraviolet (UV) light on a vat of photopolymer resin. It offers higher resolution printing than many other 3D printing technologies, allowing customers to print parts with fine details and surface finishes. SLA 3D printing is a highly-versatile platform for making custom parts in prototype and production settings; often acting as a stand-in for injection-molded plastic parts.
Xometry offers both standard and high-resolution options for fine detail parts, and can also print larger sized parts and products, with some materials offering up to a 58" inch build area. In addition, Xometry's manufacturing partner network allows us to offer a larger variety of materials than other 3D printing companies - we offer a wide range of both Accura and Somos brand materials.
Download the SLA Design Guide.
Fused Deposition Modeling (FDM)
Fused Deposition Modeling (FDM) is a 3D printing technology widely known for its speed, accuracy, and competitive cost. A machine precisely extrudes melted plastic filament to create a part. Parts are very rigid, especially compared to Selective Laser Sintering (SLS), which makes them a great fit for projects with a rigidity requirement. Xometry's FDM solution offers large build volumes up to 24″ x 36″ x 36″, a variety of colors, and a diverse selection of production-grade thermoplastics — from ABS to Polycarbonate to Ultem.
Download the FDM Design Guide.
HP Multi Jet Fusion (HP MJF)
HP Multi Jet Fusion is a new 3D printing technology that produces highly accurate and durable parts that are capable of being used directly in end-use, low-volume production, or for rapid prototyping. Since the process uses well-established 2D printing ink-jetting, it has remarkably fast layer times compared to other powder bed fusion technologies.
Download the HP Multi Jet Fusion Design Guide.
PolyJet 3D (PJ3D)
PolyJet 3D is a 3D printing technology known for its customizable material properties and excellent surface finish. It works by jetting UV curable resin onto a build tray in a process that is somewhat similar to inkjet printing. PolyJet 3D printing offers one of the most advanced industrial 3D printing solutions available, producing parts with incredible precision and speed. It also supports a wide variety of build materials including rigid and rubber-like plastics. Xometry's PolyJet solution has a maximum build envelope of 19. 3 × 15.4 × 7.9 in. (490 × 390 × 200 mm) in a variety of colors and materials.
Download the PolyJet 3D Design Guide.
Direct Metal Laser Sintering (DMLS)
Direct Metal Laser Sintering (DMLS) is an 3D metal printing technology that builds prototype and production metal parts from a CAD file using a laser to selectively fuse a fine metal powder in either stainless steel or aluminum materials. A DMLS machine is capable of producing highly complex features and all-in-one assemblies using metal materials that would be difficult to achieve with subtractive manufacturing techniques.
Our DMLS metal 3D printing service typically offers build volumes up to 250 x 250 x 325 mm, but we may be able to accommodate larger part volumes upon request in the quote. (See our Manufacturing Standards for more details) A good first step is to find out the cost of the parts you need using DMLS and compare them to other 3D printing processes and CNC machining.
Download the DMLS Design Guide.
Carbon DLS™
Carbon DLS™ uses digital light projection, oxygen-permeable optics, and programmable liquid resins to produce products with end-use durability, resolution and surface finish. This 3D printing technology is called Digital Light Synthesis™, or DLS for short. Another legacy term for the process is Continuous Liquid Interface Production (CLIP). Along with Carbon’s custom liquid resins, DLS unlocks new business opportunities and product designs previously impossible, including mass customization and on-demand inventory of end-use products.
Carbon bridges, and sometimes substitutes, for processes like Urethane Casting and Injection Molding service production, because the materials are urethane-based or epoxy-based, giving excellent mechanical properties. There are even elastomer and silicone resins that outperform most additive manufactured rubber-like materials.
The typical build area is 7.4” x 4.6” x 12.8”. Parts with dimensions exceeding 4” x 4” x 6” will require manual review.
Download the Carbon DLS Design Guide.
Metal Binder Jetting
With binder jetting, an inkjet print head quickly deposits a bonding agent onto a thin layer of powdered particles -- either metal, sand, ceramics or composites. This process is repeated, layer-by-layer, using a map from a digital design file, until the object is complete. Binder jetting is offered through our Digital RFQ Marketplace through Xometry's partnership with ExOne.
Download the Binder Jetting Design Guide.
Locations near Baltimore, Maryland
Annapolis
MarylandCollege Park
MarylandSilver Spring
MarylandBethesda
MarylandArlington
VirginiaAlexandria
VirginiaLancaster
PennsylvaniaHagerstown
MarylandWilmington
DelawareHarrisburg
PennsylvaniaPhiladelphia
PennsylvaniaAllentown
PennsylvaniaState College
PennsylvaniaPrinceton
New JerseyAltoona
PennsylvaniaRichmond
VirginiaCharlottesville
VirginiaJohnstown
PennsylvaniaNewport News
VirginiaScranton
Pennsylvania
Ready to start making custom 3D printed parts?
3D Printing Service Baltimore, MD | Instant Quotes Online
Our 3D printing capabilities
We have over 90 3D printing shops in our network and are well known for manufacturing high-quality parts at competitive prices, from rapid prototyping with Fused Deposition Modeling (FDM) to functional end parts made with Selective Laser Sintering (SLS) or Multi Jet Fusion (MJF).
Gallery of 3D printed parts manufactured by Hubs
With over 65,000 customers from every industry, including aerospace, defense, robotics, medical, machinery, automotive and electronics, we have extensive experience meeting a diverse range of 3D printing requirements, from prototyping to production: Visual aids, concept models, injection-molding prototypes, form-fit & function prototypes, tooling and casting patterns, jigs, grips and fixtures, and durable end parts.
HP PA 12 - Dyed Black
Customer | True North Design |
Purpose | Structural and vacuum EOAT components |
Process | SLS / MJF |
Unit price | $69.23 / $34.33 |
Industry | Automotive |
Prototyping PLA
Customer | Allision Conner |
Purpose | End caps and cable strain relief for sheet metal enclosure |
Process | FDM |
Unit price | $7.![]() |
Industry | Industrial Automation |
HP PA 12
Customer | US Hammer |
Description | A part for gasoline engine powered jackhammers |
Process | MJF |
Unit price | $22.18 |
Industry | Construction |
Markforged Onyx - Black
Customer | Autocom Manufacturing |
Purpose | A production part for 3D printed lathe gantry gripper fingers |
Process | FDM |
Unit price | $48.86 |
Industry | Automotive |
PC Stratasys - white
Customer | Terumo medical corporation |
Purpose | Prototyping parts used for a disposable electrical device |
Process | FDM |
Unit price | $55.![]() |
Industry | Medical |
Formlabs Clear Resin
Customer | Aversan Inc |
Purpose | A prototyping part of an injection molded component for an automated door mechanism |
Process | SLA |
Unit price | $29.83 |
Industry | Aerospace |
HP PA 12 - Dyed Black
Customer | True North Design |
Purpose | Structural and vacuum EOAT components |
Process | SLS / MJF |
Unit price | $69.23 / $34.33 |
Industry | Automotive |
Prototyping PLA
Customer | Allision Conner |
Purpose | End caps and cable strain relief for sheet metal enclosure |
Process | FDM |
Unit price | $7.![]() |
Industry | Industrial Automation |
HP PA 12
Customer | US Hammer |
Description | A part for gasoline engine powered jackhammers |
Process | MJF |
Unit price | $22.18 |
Industry | Construction |
Markforged Onyx - Black
Customer | Autocom Manufacturing |
Purpose | A production part for 3D printed lathe gantry gripper fingers |
Process | FDM |
Unit price | $48.86 |
Industry | Automotive |
PC Stratasys - white
Customer | Terumo medical corporation |
Purpose | Prototyping parts used for a disposable electrical device |
Process | FDM |
Unit price | $55.![]() |
Industry | Medical |
Formlabs Clear Resin
Customer | Aversan Inc |
Purpose | A prototyping part of an injection molded component for an automated door mechanism |
Process | SLA |
Unit price | $29.83 |
Industry | Aerospace |
HP PA 12 - Dyed Black
Customer | True North Design |
Purpose | Structural and vacuum EOAT components |
Process | SLS / MJF |
Unit price | $69.23 / $34.33 |
Industry | Automotive |
Prototyping PLA
Customer | Allision Conner |
Purpose | End caps and cable strain relief for sheet metal enclosure |
Process | FDM |
Unit price | $7.![]() |
Industry | Industrial Automation |
HP PA 12
Customer | US Hammer |
Description | A part for gasoline engine powered jackhammers |
Process | MJF |
Unit price | $22.18 |
Industry | Construction |
Markforged Onyx - Black
Customer | Autocom Manufacturing |
Purpose | A production part for 3D printed lathe gantry gripper fingers |
Process | FDM |
Unit price | $48.86 |
Industry | Automotive |
PC Stratasys - white
Customer | Terumo medical corporation |
Purpose | Prototyping parts used for a disposable electrical device |
Process | FDM |
Unit price | $55.![]() |
Industry | Medical |
Formlabs Clear Resin
Customer | Aversan Inc |
Purpose | A prototyping part of an injection molded component for an automated door mechanism |
Process | SLA |
Unit price | $29.83 |
Industry | Aerospace |
HP PA 12 - Dyed Black
Customer | True North Design |
Purpose | Structural and vacuum EOAT components |
Process | SLS / MJF |
Unit price | $69.23 / $34.33 |
Industry | Automotive |
Prototyping PLA
Customer | Allision Conner |
Purpose | End caps and cable strain relief for sheet metal enclosure |
Process | FDM |
Unit price | $7.![]() |
Industry | Industrial Automation |
HP PA 12
Customer | US Hammer |
Description | A part for gasoline engine powered jackhammers |
Process | MJF |
Unit price | $22.18 |
Industry | Construction |
Markforged Onyx - Black
Customer | Autocom Manufacturing |
Purpose | A production part for 3D printed lathe gantry gripper fingers |
Process | FDM |
Unit price | $48.86 |
Industry | Automotive |
PC Stratasys - white
Customer | Terumo medical corporation |
Purpose | Prototyping parts used for a disposable electrical device |
Process | FDM |
Unit price | $55.![]() |
Industry | Medical |
Formlabs Clear Resin
Customer | Aversan Inc |
Purpose | A prototyping part of an injection molded component for an automated door mechanism |
Process | SLA |
Unit price | $29.83 |
Industry | Aerospace |
HP PA 12 - Dyed Black
Customer | True North Design |
Purpose | Structural and vacuum EOAT components |
Process | SLS / MJF |
Unit price | $69.23 / $34.33 |
Industry | Automotive |
Prototyping PLA
Customer | Allision Conner |
Purpose | End caps and cable strain relief for sheet metal enclosure |
Process | FDM |
Unit price | $7.![]() |
Industry | Industrial Automation |
HP PA 12
Customer | US Hammer |
Description | A part for gasoline engine powered jackhammers |
Process | MJF |
Unit price | $22.18 |
Industry | Construction |
Markforged Onyx - Black
Customer | Autocom Manufacturing |
Purpose | A production part for 3D printed lathe gantry gripper fingers |
Process | FDM |
Unit price | $48.86 |
Industry | Automotive |
PC Stratasys - white
Customer | Terumo medical corporation |
Purpose | Prototyping parts used for a disposable electrical device |
Process | FDM |
Unit price | $55.![]() |
Industry | Medical |
Formlabs Clear Resin
Customer | Aversan Inc |
Purpose | A prototyping part of an injection molded component for an automated door mechanism |
Process | SLA |
Unit price | $29.83 |
Industry | Aerospace |
HP PA 12 - Dyed Black
Customer | True North Design |
Purpose | Structural and vacuum EOAT components |
Process | SLS / MJF |
Unit price | $69.23 / $34.33 |
Industry | Automotive |
Prototyping PLA
Customer | Allision Conner |
Purpose | End caps and cable strain relief for sheet metal enclosure |
Process | FDM |
Unit price | $7.![]() |
Industry | Industrial Automation |
HP PA 12
Customer | US Hammer |
Description | A part for gasoline engine powered jackhammers |
Process | MJF |
Unit price | $22.18 |
Industry | Construction |
Markforged Onyx - Black
Customer | Autocom Manufacturing |
Purpose | A production part for 3D printed lathe gantry gripper fingers |
Process | FDM |
Unit price | $48.86 |
Industry | Automotive |
PC Stratasys - white
Customer | Terumo medical corporation |
Purpose | Prototyping parts used for a disposable electrical device |
Process | FDM |
Unit price | $55.![]() |
Industry | Medical |
Formlabs Clear Resin
Customer | Aversan Inc |
Purpose | A prototyping part of an injection molded component for an automated door mechanism |
Process | SLA |
Unit price | $29.83 |
Industry | Aerospace |
HP PA 12 - Dyed Black
Customer | True North Design |
Purpose | Structural and vacuum EOAT components |
Process | SLS / MJF |
Unit price | $69.23 / $34.33 |
Industry | Automotive |
Prototyping PLA
Customer | Allision Conner |
Purpose | End caps and cable strain relief for sheet metal enclosure |
Process | FDM |
Unit price | $7.![]() |
Industry | Industrial Automation |
HP PA 12
Customer | US Hammer |
Description | A part for gasoline engine powered jackhammers |
Process | MJF |
Unit price | $22.18 |
Industry | Construction |
Markforged Onyx - Black
Customer | Autocom Manufacturing |
Purpose | A production part for 3D printed lathe gantry gripper fingers |
Process | FDM |
Unit price | $48.86 |
Industry | Automotive |
PC Stratasys - white
Customer | Terumo medical corporation |
Purpose | Prototyping parts used for a disposable electrical device |
Process | FDM |
Unit price | $55.![]() |
Industry | Medical |
Formlabs Clear Resin
Customer | Aversan Inc |
Purpose | A prototyping part of an injection molded component for an automated door mechanism |
Process | SLA |
Unit price | $29.83 |
Industry | Aerospace |
HP PA 12 - Dyed Black
Customer | True North Design |
Purpose | Structural and vacuum EOAT components |
Process | SLS / MJF |
Unit price | $69.23 / $34.33 |
Industry | Automotive |
Prototyping PLA
Customer | Allision Conner |
Purpose | End caps and cable strain relief for sheet metal enclosure |
Process | FDM |
Unit price | $7.![]() |
Industry | Industrial Automation |
HP PA 12
Customer | US Hammer |
Description | A part for gasoline engine powered jackhammers |
Process | MJF |
Unit price | $22.18 |
Industry | Construction |
Markforged Onyx - Black
Customer | Autocom Manufacturing |
Purpose | A production part for 3D printed lathe gantry gripper fingers |
Process | FDM |
Unit price | $48.86 |
Industry | Automotive |
PC Stratasys - white
Customer | Terumo medical corporation |
Purpose | Prototyping parts used for a disposable electrical device |
Process | FDM |
Unit price | $55.![]() |
Industry | Medical |
Formlabs Clear Resin
Customer | Aversan Inc |
Purpose | A prototyping part of an injection molded component for an automated door mechanism |
Process | SLA |
Unit price | $29.83 |
Industry | Aerospace |
HP PA 12 - Dyed Black
Customer | True North Design |
Purpose | Structural and vacuum EOAT components |
Process | SLS / MJF |
Unit price | $69.23 / $34.33 |
Industry | Automotive |
Prototyping PLA
Customer | Allision Conner |
Purpose | End caps and cable strain relief for sheet metal enclosure |
Process | FDM |
Unit price | $7.![]() |
Industry | Industrial Automation |
HP PA 12
Customer | US Hammer |
Description | A part for gasoline engine powered jackhammers |
Process | MJF |
Unit price | $22.18 |
Industry | Construction |
Markforged Onyx - Black
Customer | Autocom Manufacturing |
Purpose | A production part for 3D printed lathe gantry gripper fingers |
Process | FDM |
Unit price | $48.86 |
Industry | Automotive |
PC Stratasys - white
Customer | Terumo medical corporation |
Purpose | Prototyping parts used for a disposable electrical device |
Process | FDM |
Unit price | $55.![]() |
Industry | Medical |
Formlabs Clear Resin
Customer | Aversan Inc |
Purpose | A prototyping part of an injection molded component for an automated door mechanism |
Process | SLA |
Unit price | $29.83 |
Industry | Aerospace |
HP PA 12 - Dyed Black
Customer | True North Design |
Purpose | Structural and vacuum EOAT components |
Process | SLS / MJF |
Unit price | $69.23 / $34.33 |
Industry | Automotive |
Prototyping PLA
Customer | Allision Conner |
Purpose | End caps and cable strain relief for sheet metal enclosure |
Process | FDM |
Unit price | $7.![]() |
Industry | Industrial Automation |
HP PA 12
Customer | US Hammer |
Description | A part for gasoline engine powered jackhammers |
Process | MJF |
Unit price | $22.18 |
Industry | Construction |
Markforged Onyx - Black
Customer | Autocom Manufacturing |
Purpose | A production part for 3D printed lathe gantry gripper fingers |
Process | FDM |
Unit price | $48.86 |
Industry | Automotive |
PC Stratasys - white
Customer | Terumo medical corporation |
Purpose | Prototyping parts used for a disposable electrical device |
Process | FDM |
Unit price | $55.![]() |
Industry | Medical |
Formlabs Clear Resin
Customer | Aversan Inc |
Purpose | A prototyping part of an injection molded component for an automated door mechanism |
Process | SLA |
Unit price | $29.83 |
Industry | Aerospace |
Instant, online 3D printing quotes
-
Upload a CAD to start (STEP, STP, IGES, IGS, SLDPRT, 3DM, SAT, STL, OBJ or X_T)
-
Price updates in real-time as you change materials, lead time, etc..
-
No hidden costs. Our instant quotes are not just indications, but the actual price, and include shipping and customs up front.
Learn about how our quoting algorithm works
Our ordering process
Receive instant quote
Upload your CAD to our online quoting platform
Confirm specs
Configure your part specifications and select a lead time that suits your schedule
Production
We select the best manufacturer for your order, and production begins immediately
Quality control
We take full responsibility for making sure your parts are manufactured according to our standards
Delivery
Our 3D printing service has been rated 4.9/5
Over 246 customers are satisfied with our 3D printing service.
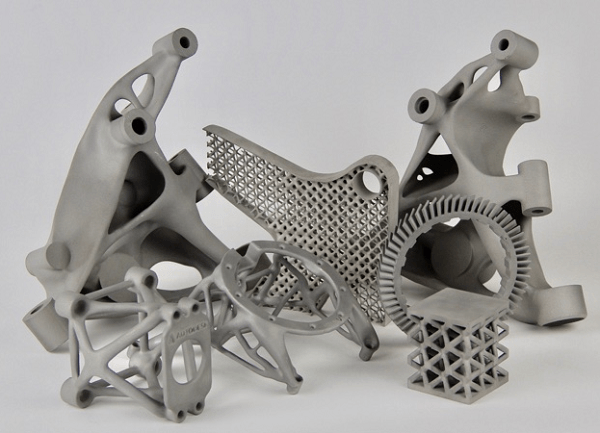
“Very responsive, high quality parts. Parts done a day early! Will use again!”
“Very happy with the quality of the prints. Vendor easy to work with and very responsive”
“Excellent Work! I like the finishing, good job.”
“Great communication and the print came out great. ”
“Nice print and delivered earlier than estimated. ”
“Fast service, the product is perfect, they finished the work next day.”
“My 7'' Daenerys Bust is printed perfectly. They finish my job within 2 days time frame and I highly recommend their services to everyone who is looking for professional 3D printing service. ”
“Super fast turnaround and the print job turned out great. Thanks!”
“I love this product and quality was so good. ”
“Great print! Professional packaging and communication as well!”
“Excellent customer service and quality of print!”
“Excellent work. Optimised toolpaths created strong parts.”
“Quality parts and quick service. Thank you! I hope yo use your services again.”
“Great communication and wonderful print quality!”
“fast and excellent quality and customer service. I will order something from you in the future.”
“You did a good job, fast and clear/clean, thank you.”
“Excellent quality parts and extremely fast turnaround time. Highly recommended. ”
“Quality is excellent, and customer service was unbeatable--actually turned it around in one day, faster than promised. Highly recommended.”
“The parts look great and arrived very quickly!”
“Great prints, outstanding communication. ”
“Great printer. Knowledgable, happy to help, great to work with. Very fast!”
“Excellent prints, would definitely use again!”
“Easy to do business with. Great communicator. Keep me informed during the entire printing process.”
“This turned out even better than I expected! Excellent work!”
“Great! Everything came as expected and super fast. I would definitely order from this maker again. ”
Show more reviews
Show less reviews
Teams build better parts
Create your Hubs team and start collaborating
Read more
The Hubs Standard - consistent quality, every time
Hubs takes the stress out of manufacturing by guaranteeing the quality and consistency of every part. Each order is dimensionally and visually inspected to make sure it meets the Hubs Standard.
3D printing materials
We can generate instant 3D printing quotes for 25+ plastics. For metal 3D-printed parts, you can request a quote from our parent company, Protolabs.
Available materials
SLS
PA 12 Glass filled PA 12
Desktop FDM
Prototyping PETG Prototyping ASA Prototyping TPU Prototyping ABS Prototyping PLA
Desktop SLA
Formlabs Standard Resin Formlabs Clear Resin Formlabs Tough Resin 2000 Formlabs Rigid Resin 4000 Formlabs Grey Pro Resin Formlabs Flexible Resin 80A Formlabs High Temp Resin Formlabs Durable Resin
MJF
HP PA 12 Glass filled HP PA 12
Industrial FDM
Markforged Onyx ABSplus Stratasys ULTEM 9085 Stratasys Stratasys ASA ABS M30 Stratasys ULTEM 1010 Stratasys
Industrial SLA
Accura 25 (PP-like) Accura ClearVue Accura Xtreme White 200 (ABS-like)
3D printing locations near Baltimore, MD
Silver Spring, MD Wheaton, MD Washington, DC
Bethesda, MD Aspen Hill, MD North Bethesda, MD
Arlington, VA Rockville, MD Alexandria, VA
Columbia, MD
The 3D Printing Handbook
No one understands 3D printing like us - our founders literally wrote the book. Click here to download the sample chapters.
Buy the book from Amazon
FAQ's
How much does your 3D printing service cost?
The cost of your 3D printed parts depends on factors such as part volume, part complexity, choice of material, which 3D printing technology is used, and if any post processing is required. For more details on these cost factors, see our article on the cost of 3d printing. To check the cost of your 3D printed part, simply upload a CAD (.STL) file and select your material and 3D printing technology to receive a quote within seconds.
How do you guarantee the quality of my prints?
Your parts are made by experienced 3D printing shops within our network. All facilities are regularly audited to ensure they consistently meet the Hubs quality standard. We include a standardized inspection report with every order and offer a First Article Inspection service on orders of 100+ units.
We have partners in our network with the following certifications, available on request: ISO9001, ISO13485 and AS9100.
Follow this link to read more about our quality assurance measures.
How do I select the right 3D printing process for my prints?
You can select the right 3D printing process by examining which materials suit your need and what your use case is.
By material: if you already know which material you would like to use, selecting a 3D printing process is relatively easy, as many materials are technology specific.
By use case: once you know whether you need a functional or visual part, choosing a process is easy.
For more help, read our guide to selecting the right 3D printing process. Find out more about Fused Deposition Modeling (FDM), Selective Laser Sintering (SLS), Multi Jet Fusion (MJF) and Stereolithography (SLA).
How can I reduce the cost of my 3D prints?
In order to reduce the cost of your 3D prints you need to understand the impact certain factors have on cost. The main cost influencing factors are the material type, individual part volume, printing technology and post-processing requirements.
Once these have been decided, an easy way to further cut costs is to reduce the amount of material used. This can be done by decreasing the size of your model, hollowing it out, and eliminating the need for support structures.
To learn more, read our full guide on how to reduce the cost of 3D printing.
Where can I learn more about 3D printing?
Our knowledge base is full of in-depth design guidelines, explanations on process and surface finishes, and information on how to create and use CAD files. Our 3D printing content has been written by an expert team of engineers and technicians over the years.
See our complete engineering guide to 3D printing for a full breakdown of the different 3D printing technologies and materials. If you want even more 3D printing, then check out our acclaimed 3D printing handbook here.
We have an extensive range of online resources developed to help engineers improve their capabilities.
Introductory guides
Design guides
Material guides
Applications
CAD & file preparation
Post processing & finishing
Our other manufacturing capabilities
CNC machining
CNC machining
Milling (3-, 4- & full 5-axis), turning and post-processing
-
50+ metals and plastics & 10 surface finishes
-
Tolerances down to ±.0008” (0.020 mm)
-
Lead times from 5 business days
See our CNC machining services
Put your 3D printed parts into production today
Get an instant 3D printing quote
3D technologies in medicine | 3d modeling in medicine: using a 3d printer to print implants
The article will discuss how 3D printing has gone beyond education and science. Even today, 3D technologies are able to help doctors save lives: we talk about all areas of 3D printing in medicine in our review.
Prospects for the development of 3D printing in medicine
Medicine was one of the first industries that decided to use the potential of 3D printers for practical purposes. Moving from simple to complex, leading physicians have been looking for ways to introduce additive printing into medical practice.
The creators of 3D printers also did not stand still, developing materials ideal for printing dental implants, prostheses, prototypes of human organs, and even found a way to print with biological material.
Fun fact: The first implant was printed in 2012 by the LayerWise Corporation. At the same time, doctors performed the world's first operation to implant a titanium lower jaw, which was printed on a 3D printer.
Nowadays, 3D printing is used in almost all branches of medicine: dentistry, prosthetics, eye surgery and microsurgery, gynecology and many others.
Medical 3D modeling
Medical 3D modeling allows you to create 3D models. The technology has found application in aesthetic dentistry, oncology, otolaryngology and other fields.
Additively printed 3D models coupled with computed tomography have become one of the indispensable advances in the medical field. Three-dimensional images of diseased organs are transformed into a high-quality image, and then converted into 3D models.
Modeling makes it possible to prepare for the operation with the highest quality and to study the features of the disease. For example, when preparing for an operation to remove a tumor, doctors carefully study the size, shape, and outline of the neoplasm in three dimensions in order to understand what tactics to choose during the operation.
Preparation for surgery using 3D modeling is carried out according to the following algorithm:
- scanning of the desired organ/tumor;
- creation of a three-dimensional image by the program;
- prototype printing;
- model study;
- choice of treatment or operation.
Thus, modern 3D printers help doctors to properly prepare for the operation. Of course, the technology is also used in other areas of medicine, but we decided to focus on oncology in order to demonstrate how invaluable help 3D printers can provide in saving lives.
Technologies for growing organs and tissues
Modern technologies have made it possible to carry out three-dimensional printing of cells, biocompatible materials and their auxiliary components in order to further create fully functional living tissues based on them. The technology is called 3D bioprinting, which has found its application in regenerative medicine and has significantly simplified and reduced the cost of transplantation of vital tissues and organs.
Bioengineer Thomas Boland at Clemson University in South Carolina (USA) independently modified Lexmark and HP printers to try to print human DNA fragments. The study showed that the size of DNA cells is similar to the size of a drop of standard ink and is about 10 microns. Further experiments showed that 90% of cells remain viable during the bioprinting process. In 2003, the scientist patented bioprinting, the first successful printing occurred in 2006.
The first successful experiment in 3D printing of human organs took place in 2006. Scientists at the Wake Forest Institute for Regenerative Medicine designed and printed seven bladders for patient volunteers.
Scientists-bioengineers took patient stem cells as a basis, with the help of which future organs were printed. Donor tissue samples stored in a special sealed chamber were applied by an extruder over a 3D model of the bladder, heated to the natural temperature of the human body.
Results: Eight weeks later, during intensive growth, the cells began to divide and recreate the bladder.
Depending on the selected 3D printer, the donor material is dosed from the dispenser. This approach is used to print soft tissues with low cell density. For example, when printing pieces of skin or soft cartilage. The method of layer-by-layer fusing is used for printing bone implants.
Seal of human hearts
A team of scientists from ETH Zurich Switzerland in 2017 made the world's first 3D printed heart, very small: its prototype weighs only 390 grams and withstands about three thousand contractions, but it is created from human fat cells and connective tissue. The breakthrough of physicians is that before them, synthetic substances were used to create human hearts.
Scientists from Switzerland have been able to develop a prototype of the heart, which will be as similar as possible to the human organ. The heart consists of two ventricles, which are separated by a special chamber that replaces the heart muscle. The air pump deflates and inflates the chamber, allowing fluid to be pumped through the heart.
The cornea was first printed on a 3D printer. The material is called bioink. Using the simplest 3D bioprinter in the university's arsenal, doctors have successfully printed forms that are as similar as possible to human corneas.
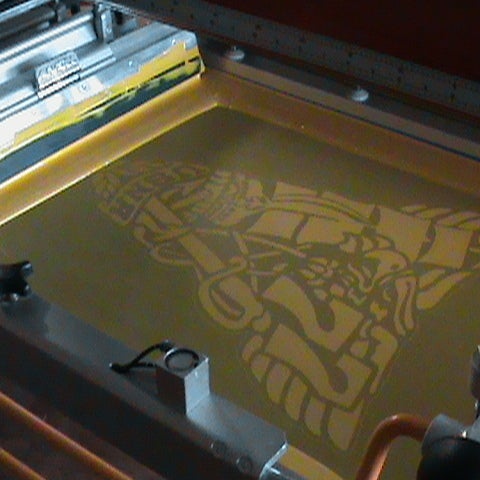
The stem cells printed with bio-ink began to grow, transforming into a human cornea. Swiss bioengineers have been able to demonstrate that they can print corneas that fit the unique dimensions of the human cornea. The characteristics of the printed tissue were taken from the real cornea. The researchers scanned the patient's eye and were then able to print a cornea that perfectly matched the size and shape.
3D printed middle ear for hearing restoration
In 2017 Radiological Society of North America, Dr. Jeffrey Hirsch at the University of Maryland in Baltimore, USA. The CT scan images were converted into 3D printed prostheses. With their help, surgeons placed four different-sized implants in human ears.
As part of the experiment, four surgeons alternately injected prototypes into four different human middle ears. The fact that all doctors were able to perfectly match the printed prosthesis to the temporal bone is amazing: with a conventional middle ear prosthesis, the chances of a successful operation are reduced to 1: 1296.
Orthopedic corsets
2014, Stanford University, USA 3D Systems, James Policy, Robert Jensen - created a unique exoskeleton.
Doctors tested a 3D printed corset on 22 patients treated at Auckland Children's Hospital. It turned out that the corset not only perfectly corrects scoliosis, but also likes little patients. In addition, in 2014, 3D Systems again made a splash by demonstrating a unique exoskeleton. With his help, the paralyzed girl was able to get to her feet.
In dentistry
1990, 2012, Align Technology, Layer Wise, USA
The first attempts to introduce additive technologies into dentistry were crowned with relative success. With the help of the first 3D printers, scientists were able to print mouthguards for teeth. It took scientists about 20 years to make the first dental implant. In 2012, a titanium mandible was implanted for the first time, made using a dental 3D printer.
Nowadays, 3D technologies have become an integral part of dentistry: dentures, orthodontic models, correction plates and veneers are printed using 3D printers.
Mobile Infection Detector Print
A group of American engineers and scientists, USA, 2017.
Scientists have developed a unique complex for diagnosing infectious diseases. As a mobile detector, a simple cell phone is used, in which a diagnostic chip is implanted.
The Mobile Infection Detector is indispensable in resource-constrained settings. In addition, the system allows for personalized treatment of the infected and timely monitoring of the epidemiological situation. The time for obtaining results is similar to the time for conducting such tests under standard laboratory conditions.
Seal of the ovaries
Scientists at Northwestern University Chicago, USA, 2017.
Doctors and scientists have developed a unique artificial ovary that allows a woman to fully restore her reproductive function.
In this study, a 3D-printed ovary prosthesis was implanted in a sterile laboratory mouse. Subsequently, mice were born who not only survived, but were able to produce offspring. It is not yet clear whether it will be possible to replace such an ovary in a woman, since human follicles grow much faster.
Skull
Doctors from Chung-Ang University, South Korea, 2016.
Doctors were able to print a three-dimensional model of the skull and implant it in a person. The operation helped to save a human life: a part of the patient's skull was removed due to cerebral edema.
Scientists have printed a piece of the skull from pure titanium. This material is recognized as one of the best in the creation of implants. The metal has a low probability of rejection by the body.
3D printed surgical instruments invented
Research team, Walter Reed Medical Center, 2006-2014.
Scientists have invented 3D-printed surgical instruments, which are still widely used in medicine and the educational process of medical students: 3D anatomical prototypes, visual teaching aids, prostheses.
Medicines
Pharmaceutical company Aprecia Pharmaceuticals, USA, 2015.
The first 3D printed drug was Spritam. A few years later, the British biotechnology corporation FabRx appeared in London, introducing 3D printing in the manufacture of pharmaceuticals. Not too many examples came out, since there are only a few companies using additive technologies in pharmacology.
Individual sensors
Scientists at Washington University in St. Louis USA, 2016.
Scientists used scanned copies of the hearts of experimental animals to print 3D prototypes around which movable and flexible individual silicone sensors were placed.
3D volumetric sensors can be removed from the printed prototype and attached to the human heart. Such sensors can monitor the work of the heart muscle in order to prevent heart attacks, strokes and other dangerous diseases. And although so far individual sensors are used only outside, scientists do not deny the possibility of introducing them directly into the human body.
Spain starts printing ventilators on 3D printers
Leitat Technological Center laboratory, Spain, 2020.
Invented an inexpensive ventilator that can be 3D printed.
The 3D printed ventilator is almost ready for mass production. The price of the device is about €500. Scientists plan that soon they will be able to get approval from the government and set up production, providing the country with the necessary amount of equipment.
HP Inc. began 3D printing medical products to combat coronavirus
HP Corporation, USA, 2020.
As part of the fight against the coronavirus pandemic, HP Inc. launched the production of 3D parts for ventilators and other equipment, as well as essential goods for both ordinary citizens and medical institutions. The corporation called on the help of its partners around the world to set up and optimize the mass production of essential goods as quickly as possible.
Products have already been successfully tested. The company produces the following groups of products: protective masks, face shields, mask holders, disposable earplugs, respirators, devices for safe window opening.
Medical masks in Russia began to be printed on a 3D printer
Temporum, Russia, 2020.
Temporum has developed its own mask printing technology. Products are created using reliable FDM technology: the model is built up in layers from a pre-melted filament. The company uses PETG as the plastic. This is the safest material from which excellent reusable masks are obtained. The user only needs to change the internal filter in a timely manner.
Results: 3D printed reusable masks are much more profitable than their disposable counterparts. Considering the fact that the company recommends using regular cotton pads instead of filters, buying such a mask becomes very profitable. Temporum is reportedly already in talks to mass-produce printed masks.
Hospitals in Italy began purchasing 3D printed devices
Hospitals in northern Italy, 2020
When hospitals in Northern Italy experienced a severe shortage of spare parts for resuscitation machines during the coronavirus pandemic, Massimo Temporelli, founder of FabLab, offered his help to hospitals left without the necessary equipment. The company provided medical institutions with cheap but high-quality breathing tubes for intensive care units. FabLab came to the aid of Isinnova, which brought a 3D printer directly to the hospital. A few hours later, the doctors received the necessary spare parts.
As a result, about 10 patients in an Italian hospital survived thanks to a device for which a valve was printed on a 3D printer. If the companies did not come to the aid of doctors, the resuscitation system would have to be turned off, which would lead to the inevitable death of patients. Other Italian companies have not stood aside: hospitals are already using 3D parts for ventilators, made using the technology of powder sintering under the action of a polymer laser.
Creation of 3D models of organs before surgeries in Dubai
Dubai Health Authority, DHA.
In October 2016, major medical institutions in Dubai purchased 3D printers. With the help of devices, doctors planned to create the most accurate prototypes of patients' organs. Thanks to the new technology, surgeons have been able to study diseased organs before surgery, increasing the efficiency and accuracy of surgical intervention. What's more, most of Dubai's hospitals are already equipped with additive printing equipment for teeth, bone prostheses and human organ models, which doctors need in preparation for operations.
It is expected that by 2030 the vast majority of medical institutions in Dubai will be equipped with 3D printers. Doctors note that three-dimensional technologies have significantly simplified the process of preparing for operations and minimized the likelihood of medical errors.
Liver
Scientists from the University of Kyushu, Japan, 2017.
Japanese scientists were able to 3D print a biotransplantation tissue of the liver, which was successfully transplanted into the body of a rat. Doctors are sure that soon they will be able to print organs for people.
Scientists conducted a unique experiment, creating a "scalable" liver tissue. To create it, they needed to connect hundreds of hepatic-renal spheroids, a 3D printer helped them in this. A system for fixing liver tissue using needle arrays helped researchers ensure proper circulation of blood and oxygen through the liver, successfully avoiding organ ischemia.
In recent years, additive technologies have been developing at a cosmic speed. If earlier users purchased a 3D printer as an unusual toy, now devices are also used in medicine, and in a way that neither scientists nor doctors could think of before. 3D printers not only simplify work, but also help doctors save lives. Our review proves this: 3D technologies are used in almost all areas of medicine. Perhaps someday people will stop waiting for years for donor organs, and doctors will be able to print the desired prototype right in the hospital.
- 05 May 2020
- 17957
Get expert advice
Lockheed Martin patents 3D diamond printing / Sudo Null IT News
Products of any shape! The author wanted to insert a diamond tyrannosaurus rex, but Google did not find a suitable picture. Photo Source: Crystal Fox
Lockheed Martin, one of the world's largest aerospace manufacturers, filed for a patent on April 4 for a new 3D printing technology, artificial diamond 3D printing.
Material from 3dprintingindustry.com translated for you Top 3D Shop .
In a patent application, inventor David G. Findlay describes a new 3D printing process that uses a ceramic-bonding polymer and nanoparticle filler to create synthetic diamond objects in almost any shape imaginable.
About technology
David G. Findley:
“The method consists of layering layers of ceramic powder and bonding them with pre-dissolved polymer.
After layering is completed, the object is heated to at least the polymer decomposition temperature, which is lower than the powder sintering temperature.”
Image: U.S. Patent and Trademark Office, Lockheed Martin
Although the printer will most likely be used to make drills, cutters and perhaps even light armor, its arrival could be great news for jewelers who can create diamonds of almost any shape.
About Lockheed Martin
Quiet supersonic vehicle for NASA. Source: Lockheed Martin
Headquartered in Bethesda, Maryland, USA, Lockheed Martin is a global security and aerospace company with approximately 98,000 employees worldwide. The company is engaged in research, design, development, production, integration and support of modern technological systems, products and services.
US Air Force F-35 fighter. Source: nationalinterest.org
What else do 3D printing and diamonds have in common? to increase the production of parts for diamond industry equipment.
The company used to cover its 3D printing needs with third parties, but the addition of two machines means round-the-clock production at its diamond research center in Maidenhead, UK.
3D printers are being used to create automated methods for checking and sorting diamonds, and to prototype parts for new equipment.
De Beers Technologies Senior Mechanical Engineer Andrew Portsmouth:
“Whenever I have an idea, my first thought is 'will it work'? Now we can print a prototype overnight, test it the next day, find out the features and flaws, make changes and print the corrected one by the next morning to repeat all the tests. It's impossible to put into words how much 3D printing speeds up development."
Optical measuring cell housing.
Learn more