Diy metal 3d printer
š² Metal 3D Printing at home!
š² Did you know that you can print 100% metal parts on your home 3D filament printer?
A hint: itās not like making a mold to cast molten metal ā much easier!
We show you how to print metal with your FDM printer and introduce you to all the 3D metal printing technologies that exist.
š What do you want to read?
Filament for printing metal parts
You may have noticed that some manufacturers sell filament with metal dust. These are materials that imitate the metal finish on your printed pieces.
But we are not talking about this, we are talking about filament that is printed in 3D and used to make 100% metallic printed parts.
What material is it? It is the BASF Ultrafuse filament from the German company BASF. It is a filament with a large amount of metallic dust that is printed with a conventional FDM 3D printer. After printing, the pieces have to follow a chemical washing and sintering process in an oven so that the metal powder is fused into a single solid metal piece.
Here is a video where you can see what results can be achieved with this type of 3D metal printing.
What is the filament made of? The content of the BASF Ultrafuse 316L filament is, as its name suggests, 316L stainless steel, a very popular steel used in applications where corrosion resistance is a critical feature, as it is more expensive and stronger than the most common stainless steel (304).
The filament coil contains 90% metal by mass; the rest of the material is the thermoplastic which makes it remain in thread form and flow through the printer extruder.
Examples of parts made with this filament
As you can see, the parts that go through the whole post-processing process have the characteristic lines of 3D layered printing and some filament sticking. The pieces can be sanded both in green (this is what the piece is called before it is washed and sintered) and in its final metallic form. They can also be polished, shot-blasted, etc.
The post-processing of the metal filament
As we said, with this filament we need a post-processing to obtain the final metal part.
The post-processing is usually done in an external company. Usually when you buy the coil it includes in its price the post-processing of the parts you manufacture with it. The technologies for post-processing of powder metal and plastic parts already exist for MIM (Metal Injection Molding) manufacturing, so it is possible to find suppliers who focus on these phases.
The process that the part goes through until it is a steel mass is as follows:
- Printing (green part). Printed on a conventional FFF printer with an abrasive resistant tip
- Washing/Debinding (brown part).
The printed part is immersed in an atmosphere of vaporized nitric acid (HNO3) and heated to remove the plastic from the part so that only the metal dust remains. The result is the phase known as the brown part.
- Sintering. The brown part is placed in an oven where it is subjected to high temperatures without melting it so that the powder particles are completely fused and almost 100% desiccated. During this process the part shrinks, so it is necessary to print it with a margin that is established in the design process.
š How to print metal on your own printer
Now the most important question: can I use any printer to print it? Yes, you can print with conventional FDM desktop printers: Ultimaker, BCN Sigma⦠in 1.75 and 3mm filament. The only thing you need is a steel nozzle to resist the abrasion of the metal filament.
These are the printing parameters of the BASF Ultrafuse 316L filament, judge for yourself:
How to print on metal? Just follow the manufacturerās instructionsAnd how much does it cost? Itās starting to be distributed and can be found at Matterhackers for $465 a reel.
ĀæDo you want to try 3D metal printing?
We have not yet been able to get hold of a BASF Ultrafuse coil to test it, but we are very interested in starting to print metal parts. If you want to ask us for a quote for this or any other project, just leave us a message and we will help you make it happen:
3D Metal Printer | Hackaday
April 13, 2022 by Al Williams
We are used to dealing with warping when printing with thermoplastics like ABS, but metal printers suffer from this problem, too. The University of Michigan has a new technology, SmartScan, that promises to reduce this problem. You can see a video about the technique, below.
The idea is to develop a thermal model of the printed part before laser sintering and then move the laser in such a way that heat doesnāt accumulate. The video shows how engraving metal in the traditional way causes the metal to warp as the laser heats up areas. Using the SmartScan thermal model, they were able to reduce deformation by almost half.
Continue reading āReducing Warping In Metal 3D Printsā ā
Posted in 3d Printer hacksTagged 3D metal printer, 3d printingMarch 31, 2020 by Ted Yapo
If youāve seen both a fused filament fabrication (FFF) printer and a wire welder, you may have noticed that they work on a similar basic principle. Feedstock is supplied in filament form ā aka wire ā and melted to deposit on the work piece in order to build up either welds in the case of the welder, or 3D objects in the case of the printer. Of course, there are a number of difficulties that prevent you from simply substituting metal wire for your thermoplastic filament. But, it turns out these difficulties can be overcome with some serious effort. [Dominik Meffert] has done exactly this with his wire 3D printer project.
Extruder cold end using a standard feeder rollerFor his filament, [Dominik] chose standard welding wire, and has also experimented with stainless steel and flux-cored wires. Initially, he used a normal toothed gear as the mechanism in the stepper-driven cold end of his Bowden-tube extrusion mechanism, but found a standard wire feeder wheel from a welder worked better. This pinch-drive feeds the wire through a Bowden tube to the hot end.
In thermoplastic 3D printers, the material is melted in a chamber inside the hotend, then extruded through a nozzle to be deposited. Instead of trying to duplicate this arrangement for the metal wire, [Dominik] used a modified microwave oven transformer (MOT) to generate the low-voltage/high-amperage required to heat the wire restively. The heating is controlled through a phase-fired rectifier power controller that modulates the power on the input of the transformer. Conveniently, this controller is connected to the cooling fan output of the 3D printer board, allowing any standard slicer software to generate g-code for the metal printer.
To allow the wire to heat and melt, there must be a complete circuit from the transformer secondary. A standard welding nozzle matching the wire diameter is used as the electrode on the hot end, while a metal build plate serves as the other electrode. As you can imagine, getting the build plate ā and the first layer ā right is quite tricky, even more so than with plastic printers. In this case, added complications involve the fact that the printed object must maintain good electrical continuity with the plate, must not end up solidly welded down, and the fact that the 1450 °C molten steel tends to warp the plate.
Considering all the issues that have to be solved to make this all work, we are very impressed with [Dominikās] progress so far! Similar issues were solved years ago for the case of thermoplastic printers by a group of highly-motivated experimenters, and itās great to see a similar thing starting to happen with metal printing, especially using simple, readily-available materials.
This isnāt the only approach to DIY metal printing, though. We saw one that used electron beam melting (EBM) not too long ago.
Thanks to [Krzysztof] for the tip!
Posted in 3d Printer hacksTagged 3D metal printer, 3d prining, weldingSeptember 17, 2018 by Mike Szczys
Last week I went to the International Manufacturing Technology Show (IMTS) and it was incredible. This is a toy store for machinists and showcases the best of industrial automation. But one of the coolest trends I found at the show are all the techniques used to 3D print in metal. The best part is that many of the huge machines on display are actually running!
Itās probably better to refer to this as additive manufacturing, because the actual methods can be significantly different from your 3D printer. Below youāll find examples of three different approaches to this process. I had a great interview with a company doing actual 3D printing in metal using a nozzle-based delivery often called cladding. Thereās a demo video of powder layer printing using lasers. And a technique that uses binders as an intermediary step toward the final metal part. Letās take a look!
Continue reading ā3D Printing In Metal: The Laser And Metal Powder Printers We Saw At IMTSā ā
Posted in 3d Printer hacks, Engineering, Hackaday Columns, Laser Hacks, SliderTagged 3D metal printer, cladding, directed energy deposition, IMTS, IMTS 2018, laser cladding, laser sinteringSeptember 14, 2018 by Al Williams
You normally think of HP as producing inkjet and laser printers. But theyāve been quietly building 3D printers aimed at commercial customers. Now they are moving out with metal printersĀ called ā predictably ā the HP Metal Jet. The video (see below) is a little glitzy, but the basic idea is that print bars lay down powder on a 21-micron grid. A binding agent prints on the powder, presumably in a similar way to a conventional inkjet printer. A heat source then evaporates the liquid from the binder.
The process repeats for each layer until you remove the part and then sinter it using a third-party oven-like device. According to HP, their technique has more uniform material properties than fusing the powder on the bed with a laser. They also claim to be much faster than metal injection molding.
Continue reading āHP Rolls Out Metal 3D Printersā ā
Posted in 3d Printer hacks, NewsTagged 3D metal printer, 3d printing, 3d printing metal, HPApril 12, 2018 by Brian McEvoy
Machinists are expected to make functional items from stock material, at least hatās the one-line job description even though it glosses over many important details. [Eclix] wanted a birthday gift for his girlfriend that wasnāt just jewelry, indeed he wanted jewelry made with his own hands. After all, nothing in his skillset prohibits him from making beautiful things. He admits there were mistakes, but in the end, he came up with a recipe for two pairs of earrings, one set with sapphires and one with diamonds.
He set the gems in sterling silver which was machined to have sockets the exact diameter and depth of the stones. The back end of the rods were machined down to form the post for the clutch making each earring a single piece of metal and a single gemstone. Maintaining a single piece also eliminates the need for welding or soldering which is messy according to the pictures.
This type of cross-discipline skill is one of the things that gives Hackaday its variety. In that regard, consider the art store for your hacking needs and donāt forget the humble library.
Posted in how-to, Tool Hacks, Wearable HacksTagged 3D metal printer, brass, diamond, gold, jewelry, posts, sapphire, scrolls, silverMay 24, 2016 by Bob Baddeley
Published only 3 days before our article on how it is high time for direct metal 3D printers, the folks at Harvard have mastered 3D metal printing in midair with no support (as well as time travel apparently). Because it hardens so quickly, support isnāt necessary, and curves, sharp angles, and sophisticated shapes are possible.
The material is silver nanoparticles extruded out of a nozzle, and shortly after leaving it is blasted with a carefully programmed laser that solidifies the material. The trick is that the laser canāt focus on the tip of the nozzleĀ or else heat transfer would solidify the ink inside the nozzle and clog it. In the video you can see the flash from the laser following slightly behind. The extrusion diameter is thinner than a hair, so donāt expect to be building large structures with this yet.
If you want big metal 3D printing, you should probably stick to the welders attached to robotic arms.
Continue reading ā3D Printing Metal In Mid Airā ā
Posted in 3d Printer hacks, SliderTagged 3D metal printer, 3d prining, 3d printed metal, 3d printing with metal, Harvard University, metal, Wyss InstituteJanuary 14, 2016 by Elliot Williams
It seems backwards, but engineers from Northwestern University have made 3D printing metal easier (and eventually cheaper) by adding extra production steps to the procedure. (Paper available in PDF).
Laser sintering works by laying down a thin layer of metal powder and then hitting it with a strong enough laser to sinter the particles together. (Sintering sticks the grains together without getting the metal hot enough to melt it.) The rapid local heating and cooling required to build up 3D objects expands and cools the metal, and can result in stresses inside the resulting object.
The Northwestern team still lays down layers of powder, but glues the layers together with a quick-drying polymer instead of fusing them with a laser. Once the full model is printed, they then sinter it in one piece in an oven.
3D-printed copper lattice. Credit: Ramille Shah and David DunandThe advantages of adding this extra step are higher printing speed ā squirting the liquid out of syringe heads can be faster than fusing metal particles with a laser ā and increased structural integrity because the whole model is heated and cooled at one time. A fringe benefit is that the model is still a bit flexible before firing, opening up possibilities for printing a flat model and then bending it into shape before sintering.
And if that werenāt enough, the team figured that theyād add a third step to the procedure to allow it to be used with rust (iron oxide) as the starting powder. They print the rust and polymer model, then un-rust the iron using hydrogen, and then fire it as before. Why rust? Do you know anything cheaper to use as a raw material?
What do you think? The basic idea may even be DIYable ā glue metal particles together and heat them up enough to stick. Not in my microwave oven, though. Weād love to see a more energy-efficient 3D metal printer.
Thanks to [Joe] for the tip!
Posted in 3d Printer hacks, SliderTagged 3D metal printer, 3d printing, metal printing, rust, selective laser sintering, slsHomemade metal 3D printer, but something went wrong / Sudo Null IT News
Hello everyone, my name is Sergey. In this article, we will talk about 3D printing with metal, more precisely, about my attempt to implement 3D printing with metal.
Very often, people who are interested in or engaged in any activity, no matter what, stumble upon something completely new and previously unknown to them, something that can help develop/improve their main activity. A similar situation happened to me. nine0003
Surfing the expanses of your Internet, I came across a wonderful technology for vacuum deposition of metals on various materials. On HabrƩ there is an interesting article about this technology. In addition, on many other resources it was said that the evaporated metal moves towards the target in a straight line.
Many resources0003
And then I thought, what if I spray metal in the place I need, gradually increasing the thickness? I looked for information about whether someone did this - I did not find it.
Registered on a forum where sprayers gather together and began to disturb them with questions like: is it possible to build up a āfilmā with a thickness of 1 or more millimeters. To which I caught a lot of misunderstanding what it was for, but received a positive answer. nine0003
General information received, you can begin to prepare for experiments.
It is known from various articles and documents that a vacuum of no more than 10ā»Ā² Pa is needed. For comparison, the order of magnitude - the pressure that gives a household vacuum pump (Value and others) - about 4 Pa āā(measured value), i.e. pressure is 400 times greater than necessary. How to deal with it and what to do? To achieve low pressures, turbomolecular vacuum pumps are used, they work in parallel with the foreline pump and, literally by molecules, capture the remaining air from the chamber. The process is not fast. The pump looks like this. nine0003
We installed a pump, it pumps out air and everything seems to be fine, but how to find out the pressure? For this I chose an ionization vacuum gauge.
In fact, nothing else is needed, except for the chamber and evaporator. I did not find a ready-made affordable (in terms of finances) camera, therefore, I decided to make my own. It is of a small volume (about 8-10 liters) in order for the air to be pumped out faster. Usually, the chambers have a spherical shape, in my case it is, on the contrary, elongated, in order to be able to set the ātargetā (the place where the metal is deposited) at different distances from the evaporator. In addition, the camera has a lot of flanges for connecting all kinds of inputs/outputs and sensors. I modeled the camera in a well-known CAD program, drew drawings and transferred it to production. nine0003
Current leads and conductors I made from a brass bar and a brass rod, bought on the local market. (Juno, who is from St. Petersburg).
In the photo below, a tungsten boat is fixed between two conductors.
The bottom part looks like this. The photo shows the cooling tubes of the current leads. Subsequently, I abandoned them, due to the simplification of the system.
Assembling the camera did not take much effort and complexity. It is much more difficult to achieve vacuum retention in this chamber. To do this, I polished the flanges and all mating surfaces to avoid the slightest leakage through the rubber seal (in the photo below, I processed only the top flange). nine0003
As it turned out later, the weld is not airtight at all (meaning for low vacuum). I, out of inexperience, assumed that by pumping a pressure of 300 kPa into the chamber and immersing it in a bath of water, I would carefully find all the leaks and eliminate them. Yes, at the first stage I did just that, but the pressure in the chamber did not fall below 10-2 Pa, there were leaks. Interestingly, before the start of the test, at a pressure in the chamber of 300 kPa, bubbles emerged from the welds with an intensity of approximately 1 bubble (diameter 2-3 mm) in 30-40 seconds. And those were big losses that I eliminated. But what to do with minimal vacuum losses that cannot be tracked in "kitchen" conditions? nine0003
The solution was close. To do this, all you need is a mass spectrometer.
The idea is simple ā the investigated chamber or container is connected to the vacuum chamber of the spectrometer. Air is pumped out, on the graph they look for extraneous peaks of any gases. After that, helium is supplied locally, to the places of possible leakage. It is helium, because its penetrating power is higher and the helium peak can be easily tracked on the spectrum. As soon as helium enters the chamber through a micro-hole, it is immediately visible on the spectrum. nine0003
I drove twice and looked for leaks twice. Now the chamber with the installed pump is hermetic and it is possible to carry out experiments further, having previously assembled all the components of the system on the rack.
General view of the incredible installation.
Starting up the plant and checking it comes down to maintaining the lowest possible pressure. The foreline pump is started first.
The pressure after the operation of the foreline pump can be seen in the picture below. nine0003
After the pressure is established (does not change). You can launch "heavy artillery" - a turbomolecular pump. It reduces the pressure by another 3 orders of magnitude.
The time has come for experiments, what I have been going for so long and what I have been waiting for so long.
First experiment.
Place a small amount of silver into the boat fixed between the conductors. Above the boat I install a steam conduit - a soldered tin cylinder, which, as I thought, should limit the spread of metal through the chamber. Above the steam conduit there is a lid with a hole of 2 mm, behind the lid there is a target on which the metal should condense. It is a pity that there are no photos left, but the vacuum chamber was completely dusty. There was not a single place where there was no applied layer of metal. In the photo below, itās not a different planet at all, but silver sprayed onto the inner surface of the wall. nine0003
Second experiment.
I thought it was because of the large gaps between the boat and the steam line. The solution was born immediately and quickly. I took two boats and combined them so that a shell was obtained. I placed silver inside, and cut a hole with a diameter of 2 mm in the upper half.
And he began to heat up the whole thing. But, I did not take into account the rigidity of the boats and the rigidity of the current leads. The shells parted a little and a gap formed between them, through which steam also flew in all directions. nine0003
As a result - spraying in the entire volume of the chamber. In the photo below there is a viewing window, the boat in which was slightly above half, but the window was completely dusty.
Third experiment.
After a little thought and grief, I thought that the container with the evaporated metal should be airtight and with only one outlet, but how and what to make it. From tungsten - very expensive and difficult to process. The way out has been found! Graphite is an excellent material for making a crucible, let's call it that. On the ad site, I found an ad for the sale of graphite bars from the contact whiskers of a trolleybus, cut out a bar with a hole in the center and made a cover for it. In the photo below - just a bar with a hole for the material (without a cover). nine0003
And in this photo already in the chamber with the lid installed (the hole in the lid is 1 mm in diameter).
Under the spoiler are a few photos with a short period of time, from which you can see how dusty the viewing window is.
Loss of transparency
It is obvious that in this case, too, there was no success, to my great regret. All three experiments were carried out with a gradual increase in temperature from the state when evaporation does not occur. nine0003
A small video in which the information is presented in a slightly different way, in a different form and volume.
Video link
www.youtube.com/watch?v=4yWQOWIG1qw
Unfortunately, it was not possible to get what was intended, but, on the other hand, invaluable experience was gained in the design and manufacture of vacuum equipment. Most of this experience I have shared with you and I would be very grateful if you express your opinion on this issue.
Thank you all and good luck.
Home metal 3D printer is already a reality
3D printing
It is extremely rare for a 3D printer to appear in the 3D printing industry, the principle of which is based on a completely new approach. Today we can print products from hundreds of different materials, but when it comes to metals, the prices for 3D printers become simply sky-high. Only very large companies can afford "metal" 3D printers because they start at $250,000. But progress does not stand still, and someday anyone will be able to purchase such a miracle of technology and print metal products without leaving home.
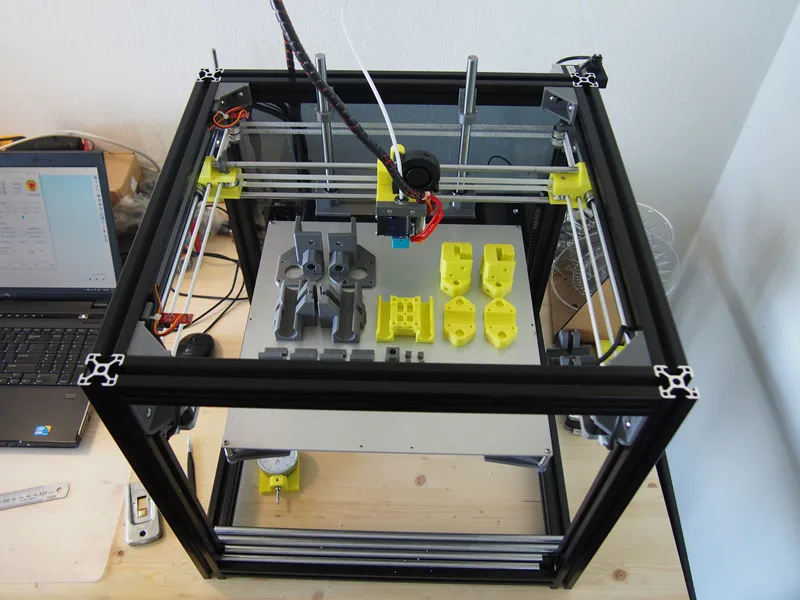
The first steps have already been taken. Take, for example, the project of the Argentine engineer Gaston Accardi. Accardi has been into 3D printing for over 12 years and was one of the first to bring the technology to South America. Somehow he had an idea to make a completely new 3D printer, but due to a busy schedule, he put off work on the project for five years. And a couple of weeks ago, he finally managed to find time.
āThis device is a galvanic 3D metal printer,ā says Accardi. ā Layer-by-layer deposition of metal in the right places occurs due to an electrochemical reaction. A wide variety of metals can be used, as well as alloys, conductive materials, and semiconductors. But most importantly, it is a very cheap method.ā nine0163By "cheap" Accardi means "very cheap". The fact is that he assembled a working prototype of the printer for just ... $ 2 (no, no, this is not a typo). So how does this unique 3D printer work?
So, galvanization is the process of coating one metal with another by means of electrolysis.
There is no hint of laser sintering, stereolithography, or fused filament technology in Accardi's 3D printer. Instead, the most common electrical plating is used here. nine0003
In fact, galvanization is possible with a power supply and two poles. One field is connected to the part you want to plate, the other is connected to the metal that will be electrodeposited. You will also need an electrically conductive solution, usually sulfuric acid or lemon juice is used for this purpose. If galvanizing is done with copper, then for best results it should simply be added to the solution.
āA few minutes after you start running current through the solution, the copper starts to coat the piece,ā explains Accardi. āBoth of the electrodes you use must be electrically conductive.ā nine0163The principle of operation of Accardi's 3D printer is based on the galvanization method, but he has further improved it. He took a marker, pulled out a rod from it and poured a solution of acid copper into it.
Then he brought one field (copper electrode wire) inside the marker. Under the influence of an electric current, copper ions are released from the acid in the marker, pass through its tip and settle on the surface of the printing platform, which is coated with conductive silver and connected to another field. The result is a layer of metal. nine0003
āYou can actually write with brass,ā says Accardi. āAnd if you keep writing the same letters over and over again, they gradually grow in height and become voluminous.āThe marker can be filled with almost any conductive and semi-conductive metal, be it titanium, gold, iron, platinum, nickel, chromium or alloys such as bronze. Accardi said he bought a 4-axis CNC machine and plans to install his electroplating system on it. As a result, he should get something like a regular FFF 3D printer, only metal will be used here instead of molten plastic. nine0003
Although the prototype cost only $2, Accardi is looking for investors to help him create a more advanced device worthy of buyers' attention.
āI am a multi-disciplinary inventor,ā he says. āLife is like a puzzle. You have to find as many pieces of the puzzle as you can and then start putting them together."Accardi believes that $100,000 will be enough for him to implement his idea and then put the printer into production and sale. If he succeeds, then the cost of a 3D printer will fluctuate around $ 1,000-2,000. nine0003
Accardi plans to build a device with multiple markers that can print with different metals at the same time. He also wants to try filling one of the markers with conductive silver ink so that the printer can print metals on non-conductive surfaces as well. We decipher: a plastic object is taken and placed inside the printer; conductive silver paint is applied to it; Different metals are applied to silver paint through a process of galvanization.
Accardi believes that his printer will help people create unique electronic devices, such as "smart prostheses" that will detect temperature and pressure.
![]()
Learn more