3D printer wheelchair
Designing the Wheelchair of The Future With 3D Printing
“I’ve even given up on going to the grocery store just two blocks away.”
When Satoshi Sugie, founder of WHILL, heard this phrase, he knew people deserved better. Today, he leads a wheelchair company whose mission is to deliver fun and innovation to pedestrian travel.
Building the next generation of wheelchairs wasn’t easy. WHILL’s engineers turned to Formlabs printers and a generative design process to push what the team could accomplish, resulting in a truly unique product.
Read on to hear from Mr. Yasuhiro Hirata on the development of the WHILL wheelchair.
Startups face an array of problems, chief among them time and cost pressure. This is especially true for hardware startups (we would know!) who are often trying to solve a brand new problem from scratch. One of the true tests of any startup is overcoming unforeseen hurdles, which are potentially expensive and time-consuming. WHILL faced numerous problems due to the complex parts required for their wheelchair, given that low volume part production can be a challenge with traditional manufacturing methods. In order for the company to survive, they had to find a way to reduce the cost of each wheelchair.
The company decided they need to quickly create prototypes for many of the complex wheelchair parts, and so turned to an outsourcing 3D printing firm. WHILL quickly learned the cost and speed limitations to outsourcing 3D printing; it wasn’t feasible for the team in the long-term. Mr. Hirata knew WHILL couldn’t complete the project without physical prototypes, so they decided to bring the 3D printing in-house.
"If you are not sure which shape is better, make it and verify it"
Mr. Hirata wasn’t impressed with some older fused filament fabrication (FFF) printers he had previously used. But he had been following the success of Formlabs, and decided to invest in one of our machines. WHILL introduced the first Formlabs printer to the team in 2016. Since then, it has been used for various projects and achieved exactly what the team needed: quick, high quality prototypes. Part prototypes directly touched by users are the most important. For such prototypes, he prints need to look and feel realistic, not cheap and hollow. In a Formlabs SLA printer, Mr. Hirata found exactly what he needed for end-use prototypes: high quality, detailed, and affordable parts.
The introduction of a high-definition 3D printer within the WHILL development team was indispensable in creating a final product. When conducting evaluations including tactile sensations, verification is meaningless unless the parts are of at least equal quality to the final-use mass-produced products. WHILL found the Formlabs parts to be an almost perfect stand-in, allowing for both internal and user testing on prototype wheelchairs.
"We try to make as many prototypes as possible for the parts that users touch, such as controllers, and verify them. If the prototypes are outsourced as in the past, the number of points to manufacture and the opportunities for study are limited due to budget and schedule constraints. With Form 2, there is a Flexible Resin with a tactile sensation close to that of actual mass-produced products, so we can model and verify high-precision prototypes without compromising the number.
"
Yasuhiro Hirata
The team used various resins on a single project, showcasing the versatility of a single Formlabs printer. While Flexible Resin was ideal for parts requiring tactile sensation, Clear Resin was used for translucent parts around the wheelchair display, while Tough Resin was used for parts that would undergo a bit more strength testing. Having one machine that can successfully print multiple parts in different materials depending on the use case is a major time and cost saving source for a hardware startup.
"Form 2 is not only accurate, but rarely breaks down. Thanks to this, we created prototypes of multiple variations every day and accumulated verification to contribute to quality improvement.” (Hirata)
Yasuhiro Hirata
Prototyping is more than just perfecting a single part. By testing various designs, multiple parts can be optimized and combined to achieve assembly consolidation. WHILL was able to reduce the final manufacturing cost of their wheelchair by decreasing the total number of parts in their product. This was a major breakthrough for the team made possible because of in-house 3D printing and complex generativity designed parts.
Generative Design is the process of using algorithms to create hundreds, or sometimes thousands, of optimized designs while considering key design goals, functions, space conditions, materials, manufacturing methods, and cost constraints.
The team at WHILLS wanted to create one, solid part for the middle of the wheelchair. They turned to generative design, and were able to analyze multiple designs at once. The issue with one-off complex designs is they can be expensive and not-feasible to build using traditional workflows.
"If you ignore the cost, you can use a light material such as carbon, but it is not realistic. When thinking about the goal of reducing the weight with a realistic material, the idea of trying a generative design came up. We needed to make prototypes of complex shapes in less time, but I think that could only be achieved with 3D printers and resins from Formlabs.
"
Yasuhiro Hirata
The new, complex part was first printed in-house using Formlabs’ Castable Wax. The team used Autodesk Fusion 360 to create the main wheelchair body part, then prototyped the generative designed part in-house, something that highly impressed the team. The end result: WHILL was able to lighten the wheelchair frame alone by more than 40%.
WHILL is one of many companies that have made incredible products thanks to in-house rapid prototyping. Download our free rapid prototyping e-book to meet six other companies who changed their business after buying a Formlabs printer.
Download the Free Report
True-to-Life Prototype for the Concept Launch
Benjamin Hubert of design agency Layer collaborated with Materialise to create the prototype for the GO Wheelchair, the world’s first 3D-printed consumer wheelchair.
The GO Wheelchair is the first project under Layer’s new research division, LayerLAB, a new in-house division of Layer that facilitates experimentation and research into the future of physical and digital products. The result of intensive research with wheelchair users and medical professionals conducted by Layer, the agency sought to create a more human-centered vehicle to improve the everyday lives of users.
A True-to-Life Prototype
Layer collaborated with Materialise on the GO Wheelchair and launched the concept at Clerkenwell Design Week, London. Benjamin worked closely with Materialise on a prototype that would represent how the GO Wheelchair would look and function.
“We required the prototype to match our vision for the final product as closely as possible which meant we needed to work with a 3D printing partner that could advise us on the best methods for producing each part that would deliver accurate and representative results. ”— Benjamin Hubert, Layer Design
Working in collaboration with Benjamin, Materialise Project Manager Freddie Raven assessed each of the components and used his expertise in rapid prototyping processes to develop a solution. “The functional and aesthetic requirements of each part will influence the selection of the printing technology and materials used. Different technologies offer different benefits and advantages in terms of the finished result or part performance. This means it’s essential that we work in partnership to understand the needs of each part and ensure we deliver a solution that meets the specifications.”
The Printed Parts
The 3D-printed parts of the GO Wheelchair prototype included the seat with an integrated cushioning structure and the footrest.
The intricate seat structure, which needed a smooth surface and a black transparency finish was printed on Materialise’s proprietary Mammoth Stereolithography machine in TuskXC2700T. Stereolithography was selected due to its suitability for printing items with fine details or that require a smooth surface finish, and the mammoth machine, with a platform size of 2100mm x 680mm x 800mm, enabled the larger parts to be printed in one piece.
The foot plate was produced with Metal 3D Printing (M3DP) in Aluminum to demonstrate how the part would behave on a production-ready model and to provide strength and durability.
The cushioning structure that sits within the seat to provide comfort and support was produced with Laser Sintering in TPU material, selected for its flexibility and strength.
“We are really pleased with the end result, it’s exciting to see our designs brought to life. The collaboration with Materialise on the technologies and materials has been invaluable and enabled us to realize a prototype together that truly reflects our vision for the GO Wheelchair.”— Benjamin Hubert of design agency Layer collaborated with Materialise
For more on the GO Wheelchair visit the Layer website.
Case SupremeMotors | Printing strollers and snow scooters on a 3D printer
Application
.
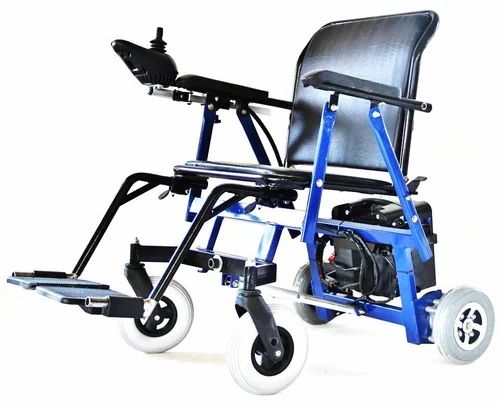
Today we will tell you about how a 3D printer helps in the development of unique products and why it is necessary to turn a tech startup into a successful growing company. nine0003
SupremeMotors specializes in the development of electric vehicles. Their products are a unique electric attachment that can turn an ordinary wheelchair into a mini car and a children's electric snowscooter.
The guys began their active work on the development of the project in 2017, they participated in various accelerators and exhibitions. As a result, all systems are assembled into a fast full-fledged electric snow scooter, which the buyer will receive. Nikolay Yudin, CEO of the company, used a part of the money won at that time on the show "Million Dollar Idea" to purchase the first Hercules and Ultimaker 3D printers. nine0003
Electric attachment mounted on a wheelchair
Now there are already 4 3D printers in the company's fleet:
+ Hercules
+ Rise
+ Ultimaker
+ Intamsys
Hercules 2018
Why was the purchase of a 3D printer so important even at the start of the project?
When creating a new product, it is very important to have a visual prototype to make sure that all the parts fit together and the dimensions are taken into account correctly, and no defects will be revealed when the product is used by the consumer. 3D printing allows you to create a product layout of any size from different materials and for any purpose many times. nine0003
So, 3D printing helped the SupremeMotors team create their first product. All parts of the plug-in were designed in SOLIDWORKS, printed on a 3D printer, then finalized and printed again. There was even a full-size version and a tire for the wheel, which were assembled and attached to the electric drive and tested near the office. This made it possible to choose the best one from several versions of the model and send it to production in China. Now the company sells this plug-in device in 15 countries of the world. nine0003
Plug-in mock-ups
This special accessory has been developed to ensure that customers do not have to deal with the installation themselves. SupremeMotors 3D-prints it and gives it to its dealers so they can quickly and correctly install the power adapter on users' wheelchairs.
Power Attachment Tool
SupremeMotors use 3D printing not only for design, but also for manufacturing. In a children's snow scooter, printed parts are used as part of the design, of course, of the product used by the consumer. nine0003
The guys develop their own product, but some parts are much cheaper to buy, as they fit the device perfectly and there is no point in developing them separately. Because of this, it becomes necessary to connect standard and unique parts of the product; for this, various fasteners, connecting links and cases are printed on the Hercules 2018 3D printer.
Hercules 2018 Kids Electric Snow Scooter was bought simply because the seller recommended it as fast, inexpensive and easy to use, but it turned out to be the best fit for the production of parts. nine0003
The guys use PTG to print fasteners between standard and custom-designed parts, and Ultem is used to print parts that bear the heaviest wear. As a result, all systems are assembled into a fast full-fledged electric snow scooter that the buyer will receive.
The idea behind the wheelchair is that it should be custom-made for its user. Nikolay has a dream to print the entire stroller on a 3D printer, the details of the stroller should be so light and strong that they can be actively moved around, but at the moment there are no materials that meet the required ratio of strength and lightness. The field of additive technologies is constantly developing, we hope that this idea will be implemented soon. nine0003
***
Subscribe to our YouTube channel Additive Kitchen!
Follow our news on social networks vk, instagram, fb
Go to our website where you can learn more about Hercules and R.O.M.A 3D printers
Our director also has a Telegram chat where you can find insider information about our developments and about 3D printing in general
***
British designer makes wheelchairs more comfortable with 3D printing
- case
Special gloves were made for more comfortable use of the Layer wheelchair Photo: video fragment Benjamin Hubert’s Layer designs “world’s first” 3D-printed consumer wheelchair Youtube channel Dezeen.
- May 27, 2016
- 1 min
- nine0088
-
Download in PDF
Alexander Tsygankov
Journalist by education, worked for several years in an environmental organization.
British studio Layer has demonstrated a design for a custom wheelchair that can be 3D printed. The project is called Go and offers a stroller with an individual seat and footrest. nine0003
Biometric data is collected from the future user and entered into the 3D printer, after which printing is carried out. The seat is printed with two materials, one of which provides vibration absorption from impacts. The footrest is made of titanium alloy. The company also made an app for wheelchair users, with which you can customize the stroller for yourself.
Previously, a wheelchair seat for basketball players who took part in the London Paralympic Games in 2012 was made using 3D printers. nine0003
There are also projects in Russia that try to solve the technical problems that wheelchair users have. So, graduates of the Novosibirsk State Technical University have developed an all-terrain wheelchair CaterWil , which climbs the stairs without special devices and overcomes the obstacles of the "inaccessible" environment. The project team posted the idea on Boomstarter , but the campaign failed to raise the amount needed to develop the project. nine0003
Most Popular
- Article
General principles and rules
- Interview
Philosopher Oksana Timofeeva on ideas for Russian and global activism in 2023 and more
nine0084The question that mankind has been looking for an answer to since the Old Testament times is now especially relevant for activists
Stay in touch with us, regardless of algorithms
Telegram channel E-mail newsletter RSS feed How to beat the algorithms: read the instructions on how to prioritize social media content and connect an RSS feed.