Connex500 3d printer
Connex500 3D Printer | The Best 3D Printer, Multi-Material, Multi-Functional, Objet
| |
The Connex500™ is the first 3D printing system that jets multiple model materials simultaneously. It offers the completely unique ability to print parts and assemblies made of multiple model materials, with different mechanical or physical properties, all in a single build. Taking the revolution even further, the Connex500™ can also fabricate Digital Materials™ on the fly, enabling users to create composite materials that have preset combinations of mechanical properties.
Based on Objet’s breakthrough PolyJet Matrix™ Technology, the Connex500 3D printing system simultaneously prints two FullCure model materials and creates an extensive range of Digital Materials. It can also print a single material from any of the original seven FullCure model materials.
|
|
By printing with Digital Materials, the Connex500™ allows you to print parts with specific Shore A values to match the values of the intended production materials. This capability opens up new opportunities, bringing you much closer to realizing the final product at an early stage, including feasibility testing and over-molding process simulation.
Parts produced on the Connex500™ have smooth and durable surfaces, with exceptionally fine details and an outstanding surface finish. The superior productivity, high quality output and unique multi-material printing capabilities of the Connex500™ enable you to closely emulate the look, feel and function of an exceptionally wide variety of end products.
Connex500 3D Printer Features & Benefits
Closer-than-ever simulation of end 3D model products.
Simultaneously prints parts with different mechanical properties, opening the way to cutting down on development time and cost, throughout the design cycle.
|
|
-
Enables close emulation of the look, feel and function of final products, facilitating selection of the end-product materials
-
Enables printed prototypes that are very close to the end part in terms of mechanical properties and material combinations, e.
g. over-molding and double injection
-
Saves days of simulating and preparing complex and expensive molds for double injection
-
Eliminates the need for silicon molds used for testing by enabling most of the testing to be done on an early stage, prototypes printed overnight
-
Saves costs and time on applications that would usually involve gluing separate parts made of different materials, or gluing several small pieces to make a large part
-
Improves communication between different groups and decision makers in the company, such as R&D, internal/external customers, engineering, marketing, sales, and management
The Connex500™ 3D Printer offers superb productivity
-
Large-size build tray of 500 x 400 x 200mm drastically reduces time on part simulation:
-
Prints large parts in a single build, saving gluing time
-
Prints numerous small parts, made of the same or different materials, together, saving printing time
-
Up to 20mm/hour/strip
-
Easy switching between High Quality, High Speed and Digital Material printing modes enables flexibility according to resource availability and technical specifications
-
Full weekend unattended operation, using Jumbo (4 X 3.
6KG) material cartridges (with at least 72 hours of non-stop build capacity)
The Connex500™ 3D Printing System allows a wide choice of materials
-
Uses Objet’s FullCure® photopolymer model and support materials, offering a wide variety of mechanical and physical properties, and easy support removal
-
Creates a wide variety of Digital Materials™ -- Composite materials made up of two FullCure model materials integrated in specific concentrations and structures to provide the desired mechanical properties
The Connex500™ 3D Printing System offers a variety of build process and printing modes
-
Advanced 3D printing capabilities enabling versatile multi-material printing options:
-
Multi Material Parts – Parts printed using multiple FullCure model materials; eliminates the need to design, print and glue together separate model parts to make a complete model, leading to dramatic savings in printing and post-processing time
-
Digital Materials – Composite materials made up of any two FullCure model materials integrated in specific concentrations and structures to provide the desired mechanical properties; enables close simulation of the target product materials for early-stage testing
-
Mixed Tray – Different parts made with different materials in a single build; saves time on materials replacement and provides an answer for multiple users
-
Easy switching between three printing modes – provides a versatile answer for a virtually unlimited variety of applications:
-
Digital Material (DM) printing mode operates at 12 mm per hour in 30 micron-layers, providing the ability to print parts made of multiple model materials, including Digital Materials
-
High Quality (HQ) printing mode builds single-material parts at 12 mm per hour in 16-micron (0.
0006 inch) layers
-
High Speed (HS) printing mode, for single-material parts, runs at 20 mm per hour in 30 micron (0.001 inch)-layers
-
User-defined selection of exact materials, printing speed and resolution needed for individual parts
The Connex500™ 3D Printer offers outstanding quality, accuracy
Assures high quality for all your parts, even those with complex geometries.
-
Highest resolution, with identical X & Y resolution of 600 DPI
-
Exceptionally fine details and an outstanding smooth surface finish
-
Thin walls down to 0.6mm (0.024”)
-
Horizontal layers of 16µ (0.0006”)
-
Ultra-fine details in all dimensions
-
Highly precise printing – maximum tolerance of 0.
3mm over large models
The Connex500™ 3D Printing System enables Clean, smooth surfaces
-
Easy-to-remove support material enables complex geometries
-
Creates smooth exterior and interior surfaces, including cavities, without the remnants characteristic of rigid support structures
-
Eliminates finishing and post-build processing
|
Technical Specifications
Tray size (XxYxZ)
500 x 400 x 200mm
(19.7 x 15.7 x 7.9 inches) |
Net build size (XxYxZ)
490 x 390 x 200mm
(19.3 x 15.4 x 7.9 inches) |
Layer thickness (Z-axis)
Horizontal build layers down to 16-micron |
Build Resolution
X-axis: 600 dpi :42 µ
Y-axis: 600 dpi :42 µ
Z-axis: 1600 dpi :16 µ |
Printing Modes
-
Digital Material (DM):
30-micron (0. 001 inch)
-
High Quality (HQ):
16-micron (0.0006 inch)
-
High Speed (HS):
30-micron (0.001 inch)
|
Accuracy
0.1-0.3mm (0.004-0.01 inch) typical (accuracy varies according to geometry, part orientation and print size) |
Modeling Material
• FullCure720 Model transparent
• VeroWhite Opaque material
• VeroBlue Opaque material
• VeroGray Opaque material
• VeroBlack Opaque material
• DurusWhite Polypropylene-like material
• TangoGray, rubber-like flexible material
• TangoBlack, rubber-like flexible material
• TangoPlus, rubber-like flexible material - High Speed & DM mode
• TangoBlackPlus, rubber-like flexible material - High Speed & DM mode |
Digital Materials
Wide range of composite materials fabricated on the fly |
Support Material
•FullCure705 Support
•Non-toxic gel-like photopolymer •support easily removed by WaterJet |
Materials Cartridges
• Four sealed 3. 6 kg (7.9 lb.) cartridges
•Two different model materials loaded •Front loading for quick replacement
•Tango family and DurusWhite also available as 1.44kg (3.17lb) net weight in 3.6 kg casing. |
Power Requirements
110 – 240 VAC 50/60 Hz
1.5 KW single phase |
Machine Dimensions (WxDxH)
1420mm x 1120mm x 1130mm
(55.9 x 44.1 x 44.5 inch) |
Machine weight
Net 500kg.
Gross (in crate) 580kg (Net 1102lb. Gross (in crate) 1279lb.) |
Software Objet Studio™ for Connex500 features:
• Part separation into subassemblies
• Suggested build orientation and speed, Auto-place
• Automatic real time support structure generation
• Slicing on the fly
• Network Version
|
Input Format
STL, SLC and objDF File |
Operational Environment
Temperature 18°C to 22°C
(64. 5°F to 71.5°F)
Relative Humidity 30-70% |
CADMatrix™ Add-in
CADMatrix add-in enables designers and engineers to seamlessly assign Objet model materials to multi-part, multi-material designs within CAD software*, thus allowing for increased control of 3D model validation.* CAD software: CADMatrix ™ is compatible with the following: Pro/ENGINEER®, SolidWorks, AutoDesk Inventor |
Special Facility Requirements
– None |
Print heads
8 units |
Network Communication
LAN - TCP/IP |
Compatibility
Windows XP, Windows Vista |
|
| |
|
Stratasys - Computer Aided Technology
3D Printers
From 3D printers to 3D production systems, Stratasys machines let you quickly build working models or end-use thermoplastic parts from your desktop or factory floor.
Save money and get products to market faster with accurate, do-it-yourself 3D printing.
Looking to purchase Stratasys?
We have Stratasys 3D Printers and 3D Printing Materials available in our store.
Go to CATI Store
Polyjet
PolyJet 3D printing technology is a powerful additive manufacturing method patented by Stratasys. Featuring 16-micron layers with accuracy as high as 0.1 mm for smooth surfaces, thin walls and complex geometries, it is the only 3D printing technology that supports a range of materials with properties from rubber to rigid and transparent to opaque in the same build.
FDM
Fused Deposition Modeling (FDM) Technology is a powerful Stratasys-patented additive manufacturing method.
SAF
Processed with SAF™ technology on the Stratasys h450 3D printer, Stratasys High Yield PA11 delivers production-grade plastic parts for high-volume demands — driving new areas of business growth.
SAF technology empowers a powder-based additive manufacturing process that employs industrial-grade technology to achieve higher levels of production of end-use parts. SAF technology uses an infrared-sensitive HAF (High Absorbing Fluid) to fuse particles of polymer powder together in discreet layers to build parts.
P3
Programmable PhotoPolymerization P3™ technology, an evolution of digital light processing (DLP) is ushering in a new era in 3D printing: the mass production of functional end-use parts.
StereoLithography
The reliable and proven Neo series of 3D printers build high-quality parts with superior surface quality, accuracy and detail.
Perfect for designers, engineers and part providers, the Neo is a dependable system for customers requiring high volume and large part printing.
Every element of the Neo has been carefully considered, always with the customer needs in mind. From manufacturing the Neo with best-in-class components for greater reliability to regular user-driven software updates, the customer is always at the core of the Neo’s development.
Healthcare
The Faster Way to Better Medical Devices. 3D Printing of patient specific or general anatomies, for production tools, Planning, testing & training, in the fields of Dental and Medical.
Validate device performance on patient-derived 3D printed anatomical models versus existing models such as animals and cadavers. Based on real patient imaging, 3D printed models mimic a variety of tissue properties in a single print.
Stratasys Medical 3D Printing Solutions can help you accelerate product development from 3D printed concept models to preclinical testing allowing manufacturers to gain certainty, test anywhere, and mitigate cost overruns.
Related articles on our blog
See More Articles
Ready to meet the dream team?
Let's Talk
Objet500 Connex 3D printer from the manufacturer Stratasys Ltd - reviews of the owners of the 3D printer, description, characteristics, photos, printed models on the Objet500 Connex
3D printer Description of the Objet500 Connex 3D printer
Objet Connex500 - provides realistic products combining the limitless possibilities of over 100 different materials with the highest level of productivity and a large print chamber.
The Objet500 Connex combines high prototyping speed with very thin layers, allowing you to quickly and accurately create large parts or even multiple parts made from different materials. The Objet500 Connex printer offers all the benefits of Connex's innovative multi-material 3D printing technology in a 500x400x200mm print chamber, spacious enough to accommodate large models or a large number of parts.
About the printer "Objet500 Connex"
Thanks to the patented PolyJet multi-material printing technology, the Objet500 Connex printer can create models from 14 different materials within a single job. This feature provides a high level of realism in the visualization of the final product. This system is ideal for designers and engineers who want to effectively demonstrate different materials in complex or prefabricated products. materials With the widest range of over 100 materials, including over 90 digital materials that are created during the printing of the model, the Objet500 Connex printer allows you to simulate various mechanical and physical properties (from rubber to rigid; from opaque to transparent; from standard to ABS).
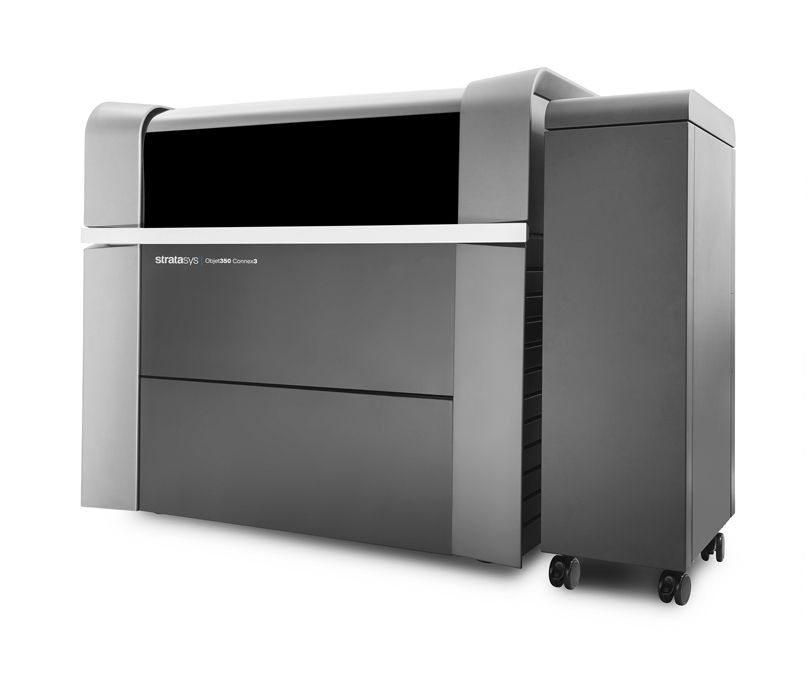
The main materials include the following. Transparent material (VeroClear) for checking the fit and measuring the profiles of transparent detailed components and simulating transparent thermoplastics such as PMMA A range of elastic materials (Tango series) that are suitable for a range of products requiring a non-slip or soft surface Clear material (RGD720) that mimics conventional plastics for products that require dimensional stability and a smooth surface A range of opaque rigid materials (Vero series) in a variety of colors including white, grey, blue and black Polypropylene-like material (DurusWhite) for creating snap-on products similar to polypropylene Objet composite digital materials include the following. Digital ABS (material RGD5160-DM, made from RGD515 and RGD535), which mimics ABS engineering plastics and combines high temperature resistance and high strength. Digital ABS2 has the same properties plus increased stiffness and strength in wall thicknesses below 1.
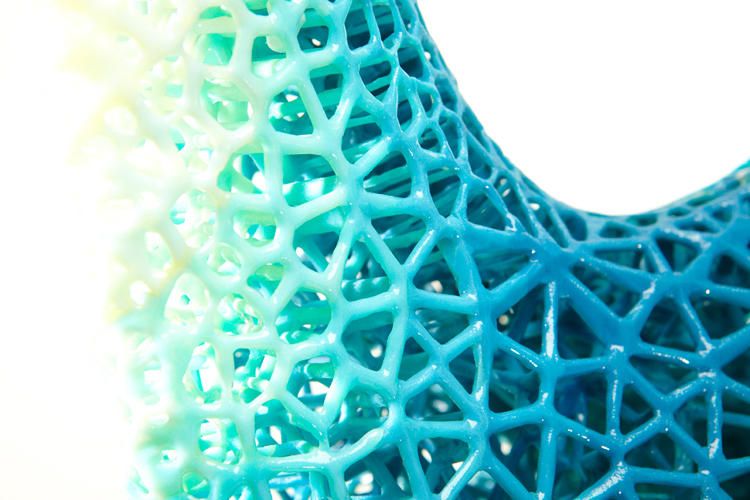
2mm Heat resistant material for extended functionality testing, use in hot air and water flow, static use and model building for exhibitions Transparent shadows and swatches Opaque hard shadows Various reinforcing elastic materials High temperature resistant polypropylene
A Brief History of 3D Printers
Now three-dimensional printing is rapidly gaining popularity and many people think that it was born quite recently. In fact, only the name “3D printer” has recently been born.
Previously, these devices were called 3D prototyping machines. And the technology is older than many of its current admirers.
Here is a brief history of the development of 3D printing:
1984 : American Charles Hull developed "stereolithography" (SLA) technology for printing 3D objects from digital models of photopolymerizable composite materials (PPC).
1985 — Mikhailo Feigen proposed layer-by-layer formation of three-dimensional models from sheet material: films, polyester, composites, plastic, paper, etc.
, fastening the layers together using a heated roller. This technology is called Lamination Object Manufacturing (LOM).
In fact, the sheets are glued to each other, and the laser cuts out the outline.
1986 - Obtained a patent for "Stereolithography" (SLA) technology. Developed in 1984 year.
In the same year, Charles Hull founded 3D Systems and developed the first commercial 3D printer. Which is unpretentiously called - "installation for stereolithography."
1986 - Drs. Carl Descartes and Joe Beeman at the University of Texas at Austin developed and patented Selective Laser Sintering (SLS).
1987 - The Israeli company Cubital developed the Layered Compaction Technology (SGC).
1988 - 3D Systems developed the SLA-250 model, which was put into mass production for a wide range of users.
1988 - FDM (Fusible Material Decomposition Modeling) invented by Scott Crump.
The most widely used technology today. It is used in most "home" 3D printers.
1989 - Scott Crump founded Stratasys.
1991 — Stratasys released the first Dimension series 3D printer with an extruding print head (FDM).
1991 - Helisys sold its first laminated object manufacturing (LOM) machine
1992 - Stratasys sold its first FDM machine, the "3D Modeler".
1992 - DTM sold its first selective laser firing system (SLS)
1993 - Solidscape was formed. Now one of the leading manufacturers.
1995 - The term "3D printing" was coined at the Massachusetts Institute of Technology.
1995 - Z Corporation has received an exclusive license from MIT to use 3DP (Printing by Bonding Powder).
1996 - Stratasys introduced "Genisys".
1996 - Z Corporation introduced the Z402.
1996 - 3D Systems introduced the Actua 2100. This rapid prototyping device was the first to use the name "zd-printer".
1997 - EOS was sold to stereolithography competitor 3D Systems. And they became monopolists.
2005 - Z Corporation released the Spectrum Z510. It was the first 3D printer on the market with high quality color printing (3DP).
2006 - Reprap project opened under GNU General Public License.
2008 - Released the first version of Reprap, "a printer that can produce itself." At that time, he could produce about 50% of the necessary parts.
2008 - Objet Geometries Ltd, developed the Connex500 printer, which prints in several different materials at once (3DP). Now the number of materials has exceeded 100.
2010 - Urbee: The first car to be built with giant 3D printers Dimension 3D Printers and Fortus 3D Production Systems.
2010 - Organovo medical company. Inc announced the creation of a technology for printing artificial blood vessels.
2010 - The Fluid Interfaces Group of scientists from the Massachusetts Institute of Technology introduced the first 3D printer for creating products - "Cornucopia". At the moment, the development has not received significant development.
2011 - The Dutch manufacturer of 3D printers Ultimaker has developed a three-dimensional printing speed of up to 350 mm per second.
Really good, although accuracy suffered from speed. Now this figure is already so surprising.
2011 - Led by the University of Exeter and Brunel University and Delcam, researchers have created the first chocolate 3D printer. In fact, this is FDM again, the difficulty was only in the development of the composition.
2011 — University of Southampton engineers create the first 3D printed airplane. The difficulty was rather in designing the model in such a way that it could be printed. The model flew great.
2011 - Vienna University of Technology introduced the smallest, lightest and cheapest 3D printer in terms of printing cost. Working on the additive technology of photopolymerization of photosensitive resin, weighing 1.5 kilograms and costing about 1200 euros.
2012 — 3D Systems launched the 3D Cube personal 3D printer for home use.