Slc 3d printer
3D Resin and 3D Printer Lab
Make Salt Lake owes its existence to the 3D printer Lab. Years ago, when MSL was formed, the first tool purchased was a 3D printer. In fact, the very reason for starting the collective that eventually became Make Salt Lake was to split cost on a 3D printer and share it amongst the members. Since then, MSL has come a very long way with its 3D printer set up. Currently we have three 3D printers that can all run simultaneously. Two of them, adoringly named Frick and Frack, are custom built models, designed and constructed by one of our members. The other one is a Creality machine that has been modified by our 3D printing gurus and made into a much higher quality machine. All 3 are professional level machines that produce extremely accurate and high quality prints.
Frick and Frack, our two custom-made 3D printers were designed and put together by Thomas Dixon, a member of Make Salt Lake for many years. Their existence, in part, is due to the donation of two older, lower quality machines called ROBO 3D printers. Those two machines were disassembled and scavenged for parts while a third machine was put to work. A 3D printer put on loan to the space at the time was tasked with printing all of the parts for the new 3D printers. All of the brackets, clips, bracing, mounts, and just about every part that isn’t electronic was 3D printed using that loaned printer. Once Frick and Frack were completed, they have since been responsible for printing their own replacement parts and pieces.
What do you need to make a successful 3D print? Well, first you need the printer. We currently have 3 of those set up and running and available for our members to use. Then, you need the material. Members usually provide their own 3D printer filament, but we have many recommendations about where to get the right material, and what the best type would be for your project. Finally, you need a design. There are thousands of designs available on the internet through sites like Thingiverse and others. But we also have programs, like Fusion 360, Solidworks (coming soon), Adobe Illustrator, Inkscape, Slicer and more!
3D printers’ main limitations are your imagination! These printers can produce anything from meticulously designed machine parts, to masks and costumes, to models of the human brain. If you can design it, you can print it!
The 3D Print Lab has a certification class that is required before any member uses the equipment. The $5 certification class is held every other Saturday. You can sign up for the class by going to Meetup and navigating to the proper event.
Make Salt Lake was recently donated an incredibly generous gift by a member of our community: a complete set of Resin 3D printers and equipment. The donation consisted of a top of the line Form Labs 2 Resin Printer & a nearly brand new Form Labs 3 Resin Printer, both considered to be some of the best on the market. Additionally, we also received an alcohol washing station and a UV curing station. Essentially, this is everything MSL needs to open an entirely new capability at the space. Resin 3D printing uses UV light to harden resin into 3D printed pieces, rather than using melted filament. This process, while slower than filament printing, is incredibly detailed and allows for the manufacture of professionally intricate parts. The printers are available for member use after completing a certification class.
3D Printing Service for Salt Lake City, Utah
CapabilitiesCustom Online 3D Printing ServiceUtahSalt Lake City
High Quality Salt Lake City, Utah 3D Printing | 60+ Materials Available
Endless Options
Choose from millions of possible combinations of materials, finishes, tolerances, markings, and certifications for your order.
Easy to Use
Get your parts delivered right to your door without the hassle of sourcing, project management, logistics, or shipping.
Quality Assurance
Our number one job at Xometry is making your custom parts to your specifications.
Your Salt Lake City, Utah 3D Printing Service: 3D Prototypes and Production Parts
A Global Leader in Industrial-Grade 3D Printing
Xometry is an industry-leading 3D printing service. Whether you need prototypes or production parts, we can make them for you in as fast as a day. We are your one-stop-shop for accurate, precise custom 3D printed parts at a low cost. Upload your 3D CAD file to get a quote and lead time within seconds. We use the latest additive manufacturing processes to build affordable functional prototypes & end-use parts in over 60 metals and plastics.
We offer eight high-quality 3D printing processes including selective laser sintering, fused deposition modeling, stereolithography, direct metal laser sintering, polyjet, Carbon DLS, binder jet metal, and HP Multi Jet Fusion. We use commercial and industrial-grade printers such as Stratasys Fortus 900mc and Fortus 450 FDM, EOS Polymer Laser Sintering (SLS) and DMLS, Concept Laser, SLM Solutions, 3D Systems, ExOne, and more.
Xometry's High Quality 3D Printing Services
Selective Laser Sintering (SLS)
Selective Laser Sintering (SLS) is a powerful 3D printing technology that produces highly accurate and durable parts that are capable of being used directly in end-use, low-volume production, or for rapid prototyping.
An additive manufacturing layer technology, SLS involves the use of a high power laser (for example, a carbon dioxide laser) to fuse small particles of plastic powders into a mass that has a desired three-dimensional shape. The laser selectively fuses powdered material by scanning cross-sections generated from a 3-D digital description of the part (for example from a CAD file or scan data) on the surface of a powder bed. After each cross-section is scanned, the powder bed is lowered by one layer thickness, a new layer of material is applied on top, and the process is repeated until the part is completed.
Download the SLS Design Guide.
Stereolithography (SLA)
Stereolithography (SLA) is a robust 3D printing technology that produces extremely accurate and high-resolution parts that are capable of being used directly in end-use, low-volume production, or for rapid prototyping.
SLA is an additive manufacturing process that focuses an ultraviolet (UV) light on a vat of photopolymer resin. It offers higher resolution printing than many other 3D printing technologies, allowing customers to print parts with fine details and surface finishes. SLA 3D printing is a highly-versatile platform for making custom parts in prototype and production settings; often acting as a stand-in for injection-molded plastic parts.
Xometry offers both standard and high-resolution options for fine detail parts, and can also print larger sized parts and products, with some materials offering up to a 58" inch build area. In addition, Xometry's manufacturing partner network allows us to offer a larger variety of materials than other 3D printing companies - we offer a wide range of both Accura and Somos brand materials.
Download the SLA Design Guide.
Fused Deposition Modeling (FDM)
Fused Deposition Modeling (FDM) is a 3D printing technology widely known for its speed, accuracy, and competitive cost. A machine precisely extrudes melted plastic filament to create a part. Parts are very rigid, especially compared to Selective Laser Sintering (SLS), which makes them a great fit for projects with a rigidity requirement. Xometry's FDM solution offers large build volumes up to 24″ x 36″ x 36″, a variety of colors, and a diverse selection of production-grade thermoplastics — from ABS to Polycarbonate to Ultem.
Download the FDM Design Guide.
HP Multi Jet Fusion (HP MJF)
HP Multi Jet Fusion is a new 3D printing technology that produces highly accurate and durable parts that are capable of being used directly in end-use, low-volume production, or for rapid prototyping. Since the process uses well-established 2D printing ink-jetting, it has remarkably fast layer times compared to other powder bed fusion technologies.
Download the HP Multi Jet Fusion Design Guide.
PolyJet 3D (PJ3D)
PolyJet 3D is a 3D printing technology known for its customizable material properties and excellent surface finish. It works by jetting UV curable resin onto a build tray in a process that is somewhat similar to inkjet printing. PolyJet 3D printing offers one of the most advanced industrial 3D printing solutions available, producing parts with incredible precision and speed. It also supports a wide variety of build materials including rigid and rubber-like plastics. Xometry's PolyJet solution has a maximum build envelope of 19.3 × 15.4 × 7.9 in. (490 × 390 × 200 mm) in a variety of colors and materials.
Download the PolyJet 3D Design Guide.
Direct Metal Laser Sintering (DMLS)
Direct Metal Laser Sintering (DMLS) is an 3D metal printing technology that builds prototype and production metal parts from a CAD file using a laser to selectively fuse a fine metal powder in either stainless steel or aluminum materials. A DMLS machine is capable of producing highly complex features and all-in-one assemblies using metal materials that would be difficult to achieve with subtractive manufacturing techniques.
Our DMLS metal 3D printing service typically offers build volumes up to 250 x 250 x 325 mm, but we may be able to accommodate larger part volumes upon request in the quote. (See our Manufacturing Standards for more details) A good first step is to find out the cost of the parts you need using DMLS and compare them to other 3D printing processes and CNC machining.
Download the DMLS Design Guide.
Carbon DLS™
Carbon DLS™ uses digital light projection, oxygen-permeable optics, and programmable liquid resins to produce products with end-use durability, resolution and surface finish. This 3D printing technology is called Digital Light Synthesis™, or DLS for short. Another legacy term for the process is Continuous Liquid Interface Production (CLIP). Along with Carbon’s custom liquid resins, DLS unlocks new business opportunities and product designs previously impossible, including mass customization and on-demand inventory of end-use products.
Carbon bridges, and sometimes substitutes, for processes like Urethane Casting and Injection Molding service production, because the materials are urethane-based or epoxy-based, giving excellent mechanical properties. There are even elastomer and silicone resins that outperform most additive manufactured rubber-like materials.
The typical build area is 7.4” x 4. 6” x 12.8”. Parts with dimensions exceeding 4” x 4” x 6” will require manual review.
Download the Carbon DLS Design Guide.
Metal Binder Jetting
With binder jetting, an inkjet print head quickly deposits a bonding agent onto a thin layer of powdered particles -- either metal, sand, ceramics or composites. This process is repeated, layer-by-layer, using a map from a digital design file, until the object is complete. Binder jetting is offered through our Digital RFQ Marketplace through Xometry's partnership with ExOne.
Download the Binder Jetting Design Guide.
Locations near Salt Lake City, Utah
Provo
UtahGrand Junction
ColoradoBoise
IdahoMeridian
IdahoLaramie
WyomingBozeman
MontanaBoulder
ColoradoFort Collins
ColoradoLas Vegas
NevadaHenderson
NevadaCheyenne
WyomingDenver
ColoradoAurora
ColoradoBillings
MontanaColorado Springs
ColoradoHelena
MontanaSparks
NevadaReno
NevadaCarson City
NevadaAlbuquerque
New Mexico
Ready to start making custom 3D printed parts?
0003 City Frankfurt Am MainAach B TrierAach, HegauAachenAalenAarbergenAasbuettelAbbenrodeAbenbergAbensbergAbentheuerAbrahamAbsbergAbstattAbtsbessingenAbtsgmuendAbtsteinachAbtswindAbtweilerAchbergAchernAchimAchslachAchstettenAchtAchtelsbachAchterwehrAchtrupAckendorfAddebuellAdelbergAdelebsenAdelheidsdorfAdelmannsfeldenAdelschlagAdelsdorfAdelsheimAdelshofen, Kr FuerstenfeldbruckAdelshofen, MittelfrAdelsriedAdelzhausenAdenauAdenbachAdenbuettelAdendorfAderstedtAdlersteigeAdligstadtAdlkofenAdmannshagen-BargeshagenAdorf/Vogtl. AebtissinwischAerzenAffalterbachAffingAffinghausenAfflerAgathenburgAgethorstAglasterhausenAhamAhausAhausenAhlbeckAhlden (Aller)Ahlefeld-BistenseeAhlenAhlerstedtAhlsdorfAhlstaedtAhnatalAhnebyAhnsbeckAhnsenAholfingAholmingAhorn, BadenAhorn, Kr CoburgAhorntalAhrbrueckAhrensboekAhrensburgAhrensfeldeAhrenshagen-DaskowAhrenshoeftAhrenstedtAhrenvioelAhrenvioelfeldAicha Vorm WaldAichachAichelbergAichenAichhaldenAichstettenAichtalAichwaldAidenbachAidhausenAidlingenAiglsbachAilertchenAindl ing
Comparison of 3D printing technologies: FDM, SLA and SLS
Additive manufacturing or 3D printing reduces costs, saves time and expands the technological possibilities in product development. 3D printing technologies offer versatile solutions for applications ranging from rapid concept and functional prototypes in the field of prototyping to fixtures and clamps or even final parts in manufacturing.
Over the past few years, high resolution 3D printers have become more affordable, more reliable and easier to use. As a result, more companies have been able to use 3D printing technology, but choosing between different competing 3D printing solutions can be difficult.
Which technology is right for your needs? What materials are available for her? What equipment and training is needed to get started? What are the costs and payback?
In this article, we take a closer look at three of today's most well-known plastic 3D printing technologies: Fused Deposition Modeling (FDM), Stereolithography (SLA), and Selective Laser Sintering (SLS).
Choosing between FDM and SLA 3D printer? Check out our detailed comparison of FDM and SLA technologies.
You can download this high resolution infographic here.
VIDEO MANUAL
Can't find the 3D printing technology that best suits your needs? In this video tutorial, we compare Fused Deposition Modeling (FDM), Stereolithography (SLA), and Selective Laser Sintering (SLS) technologies in terms of the top factors to consider when purchasing.
Watch Video
Fused Deposition Modeling (FDM), also known as Fused Filament Manufacturing (FFF), is the most widely used form of 3D printing at the consumer level, fueled by the rise of consumer 3D printers. On FDM printers, models are made by melting and extruding a thermoplastic filament, which the printer's nozzle applies layer by layer to the model being built.
The FDM method uses a range of standard plastics such as ABS, PLA and their various blends. It is well suited for making basic experimental models, as well as for quickly and inexpensively prototyping simple parts, such as parts that are usually machined.
FDM models often show layer lines and may have inaccuracies around complex features. This sample was printed on a Stratasys uPrint FDM industrial 3D printer with soluble support structures (printer price starting at $15,900).
FDM printers have the lowest resolution and accuracy of SLA or SLS and are not the best option for printing complex designs or parts with complex features. Surface quality can be improved by chemical and mechanical polishing processes. To address these issues, industrial FDM 3D printers use soluble support structures and offer a wider range of engineering thermoplastics, but they are also expensive.
FDM printers do not handle complex designs or parts with complex features well (left) compared to SLA printers (right).
Invented in the 1980s, stereolithography is the world's first 3D printing technology and is still one of the most popular technologies among professionals today. SLA printers use a process called photopolymerization, which is the conversion of liquid polymers into hardened plastic using a laser.
See stereolithography in action.
Models printed on SLA printers have the highest resolution and accuracy, the sharpest detail and the smoothest surface of all plastic 3D printing technologies, but the main advantage of the SLA method is its versatility. Materials manufacturers have developed innovative formulas for SLA polymers with a wide range of optical, mechanical and thermal properties that match those of standard, engineering and industrial thermoplastics.
Models created with SLA technology have sharp edges, a smooth surface and almost invisible layer lines. This sample was printed on a Formlabs Form 3 Desktop Stereolithographic 3D Printer (price starting at $3499).
SLA is an excellent option for making highly detailed prototypes that require tight tolerances and smooth surfaces such as molds, templates and functional parts. SLA technology is widely used in industries ranging from engineering and design to manufacturing, dentistry, jewelry, modeling, and education.
White Paper
Download our in-depth white paper to learn how SLA printing works, why thousands of professionals use it today, and how this 3D printing technology can be useful in your work.
Download white paper
free sample
Experience Formlabs print quality firsthand. We will send a free 3D printing sample directly to your office.
Request a free sample
Selective laser sintering is the most common additive manufacturing technology used in industry.
Selective Laser Sintering (SLS) 3D printers use a high power laser to sinter fine polymer powder particles. The unsprayed powder supports the model during printing and eliminates the need for special support structures. This makes SLS ideal for complex geometries, including internal features, grooves, thin walls, and negative taper. Models produced using SLS printing have excellent mechanical characteristics: their strength can be compared with the strength of injection molded parts.
Models created with SLS technology have a slightly rough surface, but almost no visible layer lines. This sample was printed on the Formlabs Fuse 1 SLS workshop 3D printer (price starting at $18,500).
The most common selective laser sintering material is nylon, a popular engineering thermoplastic with excellent mechanical properties. Nylon is light, strong and flexible, resistant to impact, heat, chemicals, UV radiation, water and dirt.
The combination of low part cost, high productivity, and widely used materials makes SLS a popular method for engineering functional prototyping and a cost-effective alternative to injection molding in cases where production runs are limited.
White Paper
Looking for a 3D printer to create durable, functional models? Download our white paper to learn how selective laser sintering (SLS) technology works and why it is popular in 3D printing for functional prototypes and end-use products.
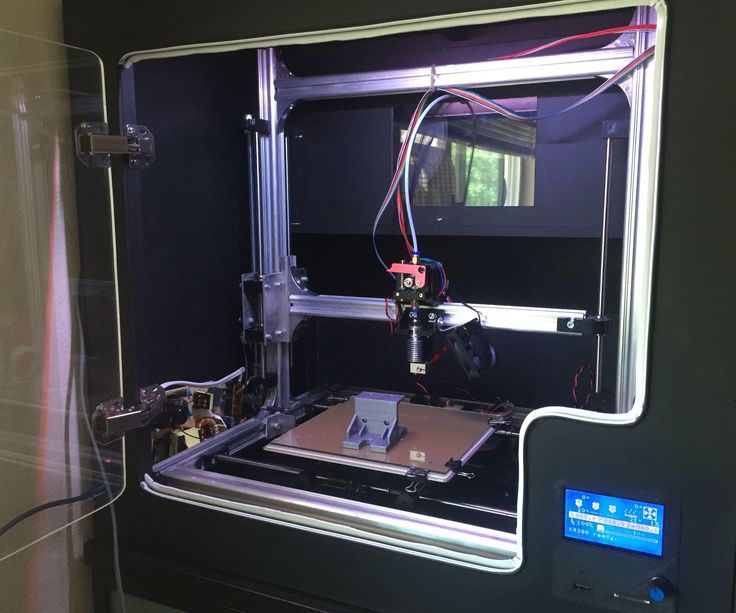
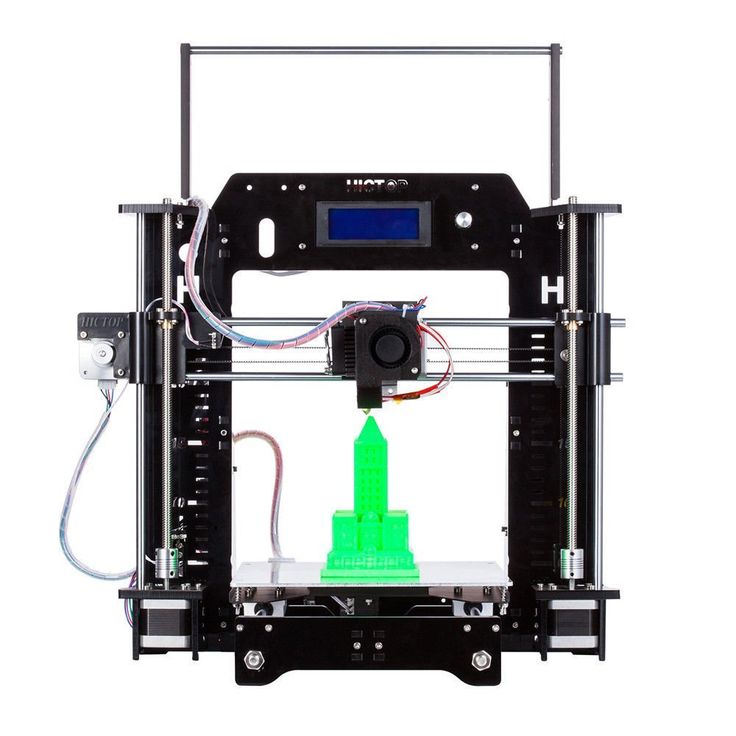
Either way, you should choose the technology that best suits your business. Prices have dropped significantly in recent years, and today all three technologies are offered in compact and affordable systems.
3D printing costing doesn't end with initial equipment costs. Material and labor costs have a significant impact on the cost of each part, depending on the application and production needs.
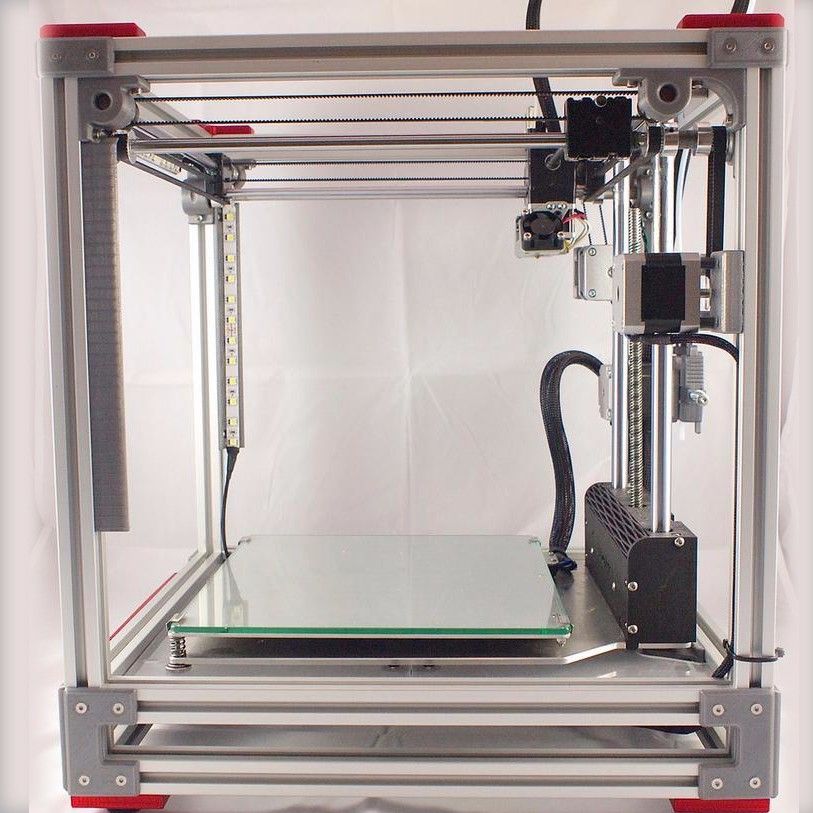
INTERACTIVE MATERIAL
Try our interactive ROI tool to see how much time and money you can save by printing with Formlabs 3D printers.
Calculate savings
FDM, SLA and SLS printed ski goggle frame prototypes (left to right).
We hope this article has helped you narrow down your search for the 3D printing technology best suited to your needs.