Cold spray 3d printing
Intro To Additive Manufacturing & Cold Spray
A simple way to understand additive manufacturing is to build a structure layer by layer. It’s like a stack of pancakes, but on a much more technical scale. Additive manufacturing methods deposit layers of material (often plastics, metals, or ceramic) to create a final form.
The VRC Cold Spray system is your ideal choice for metal additive manufacturing. It’s easy to be trained. It’s mobile. Contact us today for training and a quote.
What Is Additive Manufacturing?
Let us start by considering “regular” manufacturing. Subtractive manufacturing (machining), starts with a block of material and removes areas by cutting, milling, or sawing until the final geometry has been reached. Casting uses premade molds to shape molten material. In contrast, additive manufacturing builds parts from scratch by adding material where needed, without the use of molds. It has evolved into a highly effective and trustworthy method for manufacturing.
A prevalent format of additive manufacturing is also known as 3D printing. Often used to create prototypes, 3D prints are typically made of plastic.
These prints begin as a computer-aided design file (CAD file), which is then processed by a 3D printer to create the finished piece. When creating a CAD file for 3D printing, you do not have to work within typical manufacturing limitations. You can let go of worries regarding mold direction or machining limitations.
Once the file is created and sent to the 3D printer for processing, the machine heats your print material and extrudes it as a tiny strand, slowly building up your model. This type of 3D printing is generally known as material extrusion.
Additive Manufacturing With Metal3D printing and other additive manufacturing processes can utilize materials other than plastic, notably metals including high-performance titanium alloys. 3D printing can create high-quality surfaces and functional parts from this and many other metals including stainless steel, Inconel 625, copper, aluminum alloys, and many others.
Recent innovations in the field have led to an explosion of growth and opened a wide array of new ways to utilize 3D printing. Amazingly, it is now possible for you to 3D print with metal. Even jewelry makers use powders made of precious metals to 3D print one-of-a-kind pieces.
Manufacturers utilize metal 3D printing to create functional molds, replacement parts, and bespoke customizations. Over the past 40 method years, metal additive manufacturing has evolved into a highly effective and trustworthy metal coating, creation, and part repair.
Reducing Waste With Additive ManufacturingManufacturers worldwide use metal 3D printing and additive manufacturing methods to produce various products while reducing manufacturing waste. Traditional manufacturing methods often cut and trim away material, creating excessive waste. It’s no longer a sustainable option to waste valuable materials during your creation process. Because 3D printing is an additive manufacturing technology, you do not need to worry about creating excessive waste. You can count on additive manufacturing to be a highly effective and sustainable option.
Modern ideas of additive manufacturing and the Cold Spray process were initially introduced in the 1980s to apply an enhanced coating to parts and provide a repair method. 3D printing and cold spray technologies have grown in popularity and evolved into a highly sophisticated manufacturing method.
VRC Cold Spray Additive Manufacturing Is Fast And EffectiveCold spray additive manufacturing technology utilizes a process by which metal particles are deposited to create a continuous coating on a substrate. The process can create a single-layer coating or combine many layers to build up a part.
When the particles hit the substrate accelerated by a gas stream, the material underneath is unaffected by the process. After building up a coating or repairing a part with the cold spray process, the result can then be machine-finished, if needed. Heat treatments are not needed but can be performed if desired.
The tiny metal particles are stacked together and interlock as they are deposited onto the surface, creating a strong, metallurgical bond without the need for melting or deforming the material.
What Can You Do With VRC Cold Spray Technology?
Many industries are using VRC Cold Spray technology to help solve difficult problems more quickly than ever before. Technicians can use cold spray systems to deposit metals onto sensitive or difficult-to-weld surfaces. It is an excellent process to gently repair damaged areas on parts instead of using traditional methods that may heat and deform your product.
VRC Cold Spray technology can also combine materials that were never before compatible, restore surfaces, and perhaps most impressively, rebuild entire features on a part. You are unlocking a new world of exciting possibilities with the help of VRC Cold Spray technology.
Cold spray technology does not use heat to bond metal particles, which is hugely beneficial in the additive process. Instead, the force and pressure at which these particles are deposited onto the surface create plastic deformation and mechanical interlocking during deposition. Without heat, there are fewer defects and decreased oxidation. The science behind VRC Cold Spray makes an almost perfect surface quality on your products and parts. With VRC Cold Spray, you will have an easy way to repair and build upon surfaces with virtually no adverse effects to the materials’ surface.
Helping You Achieve Your Manufacturing GoalsCold spray can fix machining mistakes, and it’s the only option in many situations. It is an advantageous and time-conscious solution for part renewal and repair. It’s portable and can save you thousands (or even millions) of dollars on critical repairs. You might remember a situation when even a small mistake resulted in the loss of time for your project.
With VRC Cold Spray, you can fix these little mistakes quickly to get your project moving again. With the convenience and portability of VRC Cold Spray, you can save time and money.
The VRC Cold Spray system is ideal for cold spray additive manufacturing. It’s easy to be trained. It’s mobile. Contact us today for training and a quote.
SPEE3D's cold spray 3D printing technology selected for US Navy MaintenX exercise
0Shares
Australian metal 3D printer manufacturer SPEE3D has been chosen by the US Navy to supply its ‘MAINTENX’ maintenance technology engagement exercise.
As part of the initiative, SPEE3D’s systems are set to be deployed both at port and by sea, during the US Navy’s ANTX-Coastal Trident 2022 technical demonstrations. Through the R&D program, the US Armed Forces branch aims to assess the potential of metal 3D printing, as a means of carrying out ship battle damage repairs, and reducing its reliance on traditional supply chains at risk of disruption.
“We are thrilled to collaborate with the US Naval Warfare Centers to test and validate our unique metal 3D printing capability,” said Byron Kennedy, CEO of SPEE3D. “We understand their operational challenges both on land and sea, and look forward to strengthening our existing relationships with the US Department of Defense (DoD) as a trusted partner.”
The WARPSPEE3D 3D printer. Image via SPEE3D.SPEE3D’s Cold Spray technology
Established by engineers Byron Kennedy and Steven Camilleri, SPEE3D is a manufacturer whose business revolves around its proprietary Cold Spray technology. Unlike ordinary metal 3D printing, which relies on high-powered lasers and expensive gasses, the company’s process uses the power of kinetic energy instead, to jet powders with sufficient velocity to deform and fuse them with substrates on impact.
Marketed in the form of its LightSPEE3D and WarpSPEE3D units, the firm’s technology is capable of producing parts up to 1000mm x 700mm in size and 40kg in weight, at speeds it says are 100 to 1000 times faster than traditional metal 3D printers.
So far, the high throughput of these machines has attracted the interest of everyone from on-demand part manufacturers to rocket builders. Early in 2021, service provider 3D in Metal installed a WarpSPEE3D 3D printer at its El Salvador complex, enabling it to better meet Latin American demand for spare metal parts, before SPEE3D gained funding to help develop low-cost 3D printed rocket engines.
Cold Spray technology has also proven adept at meeting military demand for a means of producing spares on-site, out in the field. The Australian Army has been one of the most extensive users of SPEE3D’s systems in such applications, and following a string of successful 3D printing trials last year, Kennedy hailed the “bigger, longer and more remote” tests as a validation of their potential in defense.
Likewise, the US military has shown increasing interest in SPEE3D’s portfolio, with Phillips Federal’s Center of Innovation upgrading to a WarpSPEE3D earlier in 2022. This followed the inaugural Defense Strategies Institute Award for Expeditionary and Tactical 3D Printing Excellence, which the firm won in recognition for its achievements in using its technology to support the US DoD’s mission priorities.
The US Navy’s ANTX-CT trial
Cold Spray technology’s latest military trial will see it deployed as part of ANTX-Coastal Trident, an operational R&D program designed to identify technologies which address US maritime security concerns. Led by the Naval Surface Warfare Center’s Port Hueneme Division, as well as partners like Matter Labs, the 2022 edition of the annual exercises will take place at the Ventura County Naval Base.
In order to pursue its aims of ‘expanding the advantage’ of the naval warfighter and meeting its operational needs via new technologies, the US Navy arm is set to carry out tests of novel approaches to maritime threat mitigation, data-driven decision support, AI, VR, unmanned systems and in-service maintenance later this year.
SPEE3D’s role in the initiative will be to demonstrate the potential of its technology as a portable solution to the latter, that can be deployed as needed to create parts on-demand. According to Kennedy, the firm’s machines are capable of rapidly producing large-scale components “that would otherwise take weeks or even months to manufacture,” while doing so outside of a lab, in hostile environments.
These claims will now be put to the test onboard the US Navy’s Self Defense Test Ship (SDTS), which is currently stationed at Port Hueneme, California, from August 22 to September 2, 2022.
ExOne’s portable 3D printing factory. Image via ExOne.Addressing naval deployability needs
The US Navy has invested heavily in the R&D and utilization of 3D printing technologies, particularly those with the potential to reinforce its supply chain, and enable its service people to produce spare components when deployed at sea.
Desktop Metal subsidiary ExOne, for instance, has been contracted by the Defense Logistics Agency (DLA) to develop a portable 3D printing factory for the US DoD. Set to be housed inside a 40-foot shipping container, the compact production pod is set to contain everything needed to manufacture spares, and be deployable by land, air and sea.
INTAMSYS has developed a similar system for the Royal Netherlands Navy, in the shape of its AMCOD 3D printing mobile repair center. Composed of a FUNMAT HT and two FUNMAT Pro 410 3D printers inside a shipping container, the module is designed to help reduce the dependence of Dutch military vessels on traditional supply chains, as well as minimize any downtime caused by part shortages.
Mid-last year, Aurora Labs also began 3D printing stainless steel maritime components as part of an initiative carried out alongside BAE Systems Maritime Australia. Having been identified as a possible provider of powder bed fusion (PBF) technologies, the firm was charged with producing parts designed for fitting onboard nine Australian Navy frigates, before evaluating their commercial viability.
To stay up to date with the latest 3D printing news, don’t forget to subscribe to the 3D Printing Industry newsletter or follow us on Twitter or liking our page on Facebook.
For a deeper dive into additive manufacturing, you can now subscribe to our Youtube channel, featuring discussion, debriefs, and shots of 3D printing in-action.
Are you looking for a job in the additive manufacturing industry? Visit 3D Printing Jobs for a selection of roles in the industry.
Featured image shows the WARPSPEE3D 3D printer. Image via SPEE3D.
Tags 3D in Metal ANTX-Coastal Trident 2022 Aurora Labs Australian Army BAE Systems Maritime Australia Byron Kennedy Defense Logistics Agency Defense Strategies Institute Desktop Metal Exone Intamsys Matter Labs Naval Surface Warfare Phillips Federal's Center of Innovation Royal Netherlands Navy SPEE3D US Navy
Paul Hanaphy
Paul is a history and journalism graduate with a passion for finding the latest scoop in technology news.
GE improves additive systems based on gas dynamic spraying
News
General Electric Corporation is developing scalable 3D printers based on cold gas dynamic spraying technology.
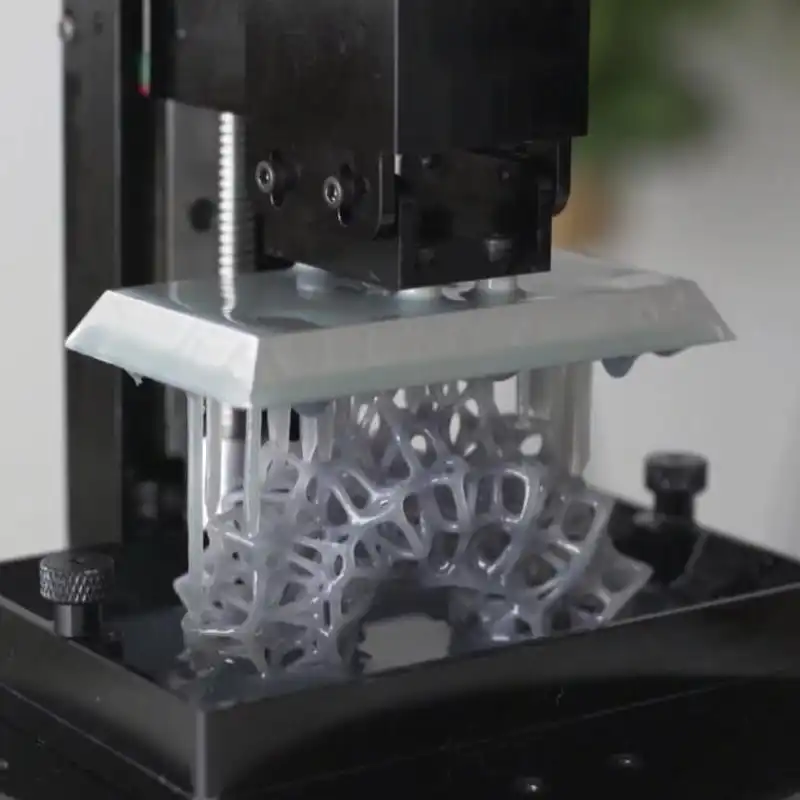
There is nothing fundamentally new in the gas-dynamic spraying of metal powders: the first studies were carried out back in the 80s by the Institute of Theoretical and Applied Mechanics of the Siberian Branch of the Russian Academy of Sciences, and today the technology is widely used in the repair of metal products and for applying protective coatings. Interestingly, the technology caught the attention of the additive industry, after which attempts began to make the technique more accurate for the sake of building complex shapes, and not just applying metal layers.
In Australia, two companies are working on the development of 3D printers based on gas dynamic spraying: Titomic intends to conduct industrial tests of additive installations next year, and SPEE3D has already launched production of LightSPEE3D industrial 3D printers ( in the illustration above ). In the US, work is being done in a slightly different direction. For example, engineers at the University of Akron, Ohio and AMES are collaborating on additive installations based on industrial robotic arms that provide multi-axis positioning. The same idea appealed to General Electric specialists because of not only high production flexibility, but also scalability.
The underlying principle of gas-dynamic spraying is simple: metal powder particles are accelerated to supersonic speeds, and upon impact with the surface, kinetic energy is converted into thermal energy with accompanying plastic deformation and diffusion. A couple of points are important here: firstly, the density of the resulting coatings or products is very high. Secondly, there is no significant heating of the product itself, which eliminates the possibility of the formation of hot cracks, although the particles themselves, when colliding at four times the speed of sound, become white-hot. Powders are protected from oxidation by an accelerating flow of inert gas. The main problem is to obtain high-precision parts, which would reduce the intensity of machining of printed parts to the finished form.
General Electric engineers strive to achieve the highest possible geometric complexity of the grown workpieces through positioning using two six-axis robotic arms. One "hand" holds the substrate with the part to be grown, and the second one carries out the spraying. This approach eliminates the need for support structures, reduces machining time and reduces waste. At the same time, engineers rely on 3D scanning and self-learning algorithms to improve the efficiency and quality of the process. Joseph Vinciquerra, an employee of the artificial intelligence laboratory, helps this team.
“Imagine that you paint the same picture forty thousand times a year. All of them will have some differences, even if the drawing is done by a machine. Some attempts will be better, some worse, but we can learn from the differences. If you analyze and correct in real time, the quality of each new picture will increase,” explains Joseph.
The first example of the practical application of the developed system was the repair of the GE-9 gas turbine aircraft engine gearbox carried out in October0 - the most powerful aircraft power plant in the world. Engineers are not limited to one repair, for example, experimenting with 3D printing of turbine blades. How it works, see the videos:
Do you have interesting news? Share your developments with us, and we will tell the whole world about them! We are waiting for your ideas at news@3Dtoday. ru.
Follow author
Follow
Don't want
2
More interesting articles
13
Subscribe to the author
Subscribe
Don't want
Last Saturday, September 24, the third 3Dtoday Fest took place in St. Petersburg...
Read more
9
Subscribe to the author
Subscribe
Don't want
The project is experiential and symbolic: the structure was erected by 3D4Art to celebrate...
Read more
sarkazm
Loading
04/01/2016
39738
68
Subscribe to the author
Subscribe
Don't want
News from the world of printing in a short line
FDplast announced the release of a free. ..
Read more
Copper 3D Printing - Complete Guide
Copper is one of the newest and most promising areas of metal 3D printing for everything from electric motors to heat sinks.
Previously, copper 3D printing was a challenge due to the metal's reflectivity and high thermal conductivity, but advances in printers and materials have largely resolved these early problems. Today, 3D printed copper propulsion systems send rockets into space, 3D printed copper heatsinks cool processors, and 3D printed copper coils boost the performance of electric motors.
3D printed copper parts (Source: Trumpf)
Why 3D print copper?
Copper has always been a very useful metal due to its ability to conduct heat and electricity, resist corrosion and even kill bacteria and viruses. Demand for complex copper parts is on the rise as 3D printing opens up even more uses and possibilities for this metal.
3D printing (also known as additive manufacturing) allows the creation of exceptionally complex shapes, fine details, internal structures and lattice inserts that are not possible with any other form of metal fabrication. These capabilities reduce weight, increase efficiency, and reduce fabrication and assembly times, as multi-component assemblies can be 3D printed as a single unit.
Additive Metallurgy
3D printing also allows this relatively expensive metal to be produced more efficiently, reducing waste by using only the amount of material needed to make each part. For companies interested in copper 3D printing, reducing raw material costs is critical.
If you already produce custom copper parts, 3D printing can significantly reduce your production costs while optimizing part performance.
Markforged 3D printed copper heatsink (Source: Markforged)
Although there aren't many 3D printers that can print copper, there is still a wide variety of printing technologies and prices.
FDM printers using copper-filled plastic filament can produce copper jewelry, decorative items, and other parts that are almost 100% copper. While for more advanced production, 3D printers using copper powder, rods or copper polymer slurry produce industrial parts with excellent mechanical and conductive properties, which can meet international standards such as IACS (International Annealed Copper Standard).
Let's look at what types of printers can work with copper today.
Trumpf's TruPrint 1000 Green Edition 3D printer
several equipment manufacturers have recently included copper in their material list. Since copper is highly reflective, laser processing of the powder has been a hurdle for manufacturers. However, this technology and materials have evolved to solve this problem.
3D printer manufacturer Trumpf, for example, has developed an industrial green laser that can 3D print materials such as copper, copper alloys, and precious metals that are difficult to process with infrared waves.
Two powder layer technologies for metal 3D printing, DMLS (Direct Metal Laser Sintering) and EBM (Electron Beam Melting), work by depositing a thin layer of copper powder onto a platform inside the printer. The powder heats up while lasers or electron beams draw the first layer of the part. When the particles in the layer fuse, the platform is lowered slightly into the assembly chamber, and fresh powder is poured on top, and the process is repeated. Some of the copper powder left over from the process can be recycled for use in the next print.
Copper additive manufacturing powder from GNK Powder Metallurgy (Source: GNK)
Copper-bonded 3D inkjet printers
Copper powder bonded with a liquid binder and sintered in a furnace is a 3D printing technique known as binder inkjet printing that allows parts to be obtained without the use of an auxiliary material. Bond jetting is a no-heat process in which a bonding layer is sprayed between each layer of metal; the binder is then removed during the sintering process.
Binder blasting is a popular additive manufacturing method for high volume metal parts.
Featured image of
FDM Metal-on-Copper Deposition 3D Printers The most economical approach to 3D printing copper parts is to use machines that extrude the filament. Metal filament for printing metal parts consists of a plastic base with metal particles evenly interspersed in it. Virtually any Fused Deposition Modeling (FDM) printer can print near-solid metal parts using a polymer filament filled with copper powder. Currently, there is only one option on the market - from the manufacturer of threads The Virtual Foundry. The company claims that its copper filament is suitable for printing on any filament 3D printer with a hardened nozzle and a hot end that can reach temperatures of up to 225ºC. However, the parts do not become metal immediately after printing and require additional post-printing steps to melt the resin binder and leave only the metal. Other types of copper thread contain enough real copper particles to be polished and given a metal-like weight, but are for decorative purposes. A company in Chile called Copper3D produces a copper-filled filament that produces parts that do not have metal parts, but parts that have the antibacterial and antimicrobial properties of copper. In addition to the mainstream FDM printers, two other filament-extruding printers also offer copper, but they use their own proprietary materials. Desktop Metal uses a bonded metal filament, while Markforged uses a similar metal powder bonded into a plastic matrix. The printers from these manufacturers produce all-metal parts designed for industrial use, such as machine tools, induction coils, heat sinks, and functional prototypes. Cold spray and DED copper 3D printers WarpSpee3D cold spray 3D printer (Source: Spee3D) Although these two methods of metal 3D printing are not usually combined together, we are combining them here due to their general application for coating metal parts with another metal and for layering metal parts with metal powder. Directed Energy Deposition (DED) is a system developed by Optomec of New Mexico to create, improve and repair metal parts. Spee3D's WarpSpee3D process is unique in its use of supersonic 3D deposition to produce parts from a range of metal powder materials, including copper and aluminum. Cold spray is an additive manufacturing technique in which metal powder is injected into a supersonic pressurized gas stream. Instead of melting the metal, cold spraying holds it together in a process called plastic deformation. Companies such as Spee3D are using cold spray technology to apply an antimicrobial copper coating to doors, handrails and touch panels intended for use in hospitals, schools and other public places. Cold spray is also the fastest metal 3D printing method. Spee3D printed a 17.9kg (17.9kg) pure copper aerospace rocket nozzle lining (pictured below) on WarpSpee3D in about three hours at a cost of just $716, according to the company. One of the disadvantages of DED and cold spray is that they are limited in the production of complex geometries. Rocket nozzle copper plating, engineer's spark-free copper hammer and copper cable clamp, 3D printed by Spee3D (Source: Spee3D) Photopolymerization Holo) Metal DLP 3D printing is similar to resin 3D printing in that it uses UV light projected onto a photosensitive slurry to cure layer by layer. Instead of resin, metal DLP printers use a liquid polymer filled with metal powder and a small amount of binder. After the parts are printed, they have to go through several more stages before they become the final metal parts. Metallic DLP printing is valued for fine detail. California startup Holo recently completed a facility where it plans to 3D print pure copper parts on its proprietary 3D printers that are not for sale. Copper interspersed filament for copper parts is a unique type of composite filament that, when used correctly, produces strong, chemically resistant, and near-solid metal parts.
NASA is even testing the filament for use in "interplanetary microbial contamination," according to the company.
Like SLS, in DED, high-power lasers build up 3D structures in layers, creating parts with high density and strength, ideal for mechanical applications. In 2019Optomec developed a new copper DED process to produce heat exchangers for use in the aerospace, chemical and other industries.
Parts like this are usually made from solid forged copper, which takes weeks and costs tens of thousands of dollars.
Learn more