3D printing jacksonville
3D Printing Service Jacksonville, FL | Instant Quotes
Our 3D printing capabilities
We have over 90 3D printing shops in our network and are well known for manufacturing high-quality parts at competitive prices, from rapid prototyping with Fused Deposition Modeling (FDM) to functional end parts made with Selective Laser Sintering (SLS) or Multi Jet Fusion (MJF).
Gallery of 3D printed parts manufactured by Hubs
With over 65,000 customers from every industry, including aerospace, defense, robotics, medical, machinery, automotive and electronics, we have extensive experience meeting a diverse range of 3D printing requirements, from prototyping to production: Visual aids, concept models, injection-molding prototypes, form-fit & function prototypes, tooling and casting patterns, jigs, grips and fixtures, and durable end parts.
HP PA 12 - Dyed Black
Customer | True North Design |
Purpose | Structural and vacuum EOAT components |
Process | SLS / MJF |
Unit price | $69. |
Industry | Automotive |
Prototyping PLA
Customer | Allision Conner |
Purpose | End caps and cable strain relief for sheet metal enclosure |
Process | FDM |
Unit price | $7.92 / $4.72 / $2.80 |
Industry | Industrial Automation |
HP PA 12
Customer | US Hammer |
Description | A part for gasoline engine powered jackhammers |
Process | MJF |
Unit price | $22.18 |
Industry | Construction |
Markforged Onyx - Black
Customer | Autocom Manufacturing |
Purpose | A production part for 3D printed lathe gantry gripper fingers |
Process | FDM |
Unit price | $48.![]() |
Industry | Automotive |
PC Stratasys - white
Customer | Terumo medical corporation |
Purpose | Prototyping parts used for a disposable electrical device |
Process | FDM |
Unit price | $55.38 / $32.96 |
Industry | Medical |
Formlabs Clear Resin
Customer | Aversan Inc |
Purpose | A prototyping part of an injection molded component for an automated door mechanism |
Process | SLA |
Unit price | $29.83 |
Industry | Aerospace |
HP PA 12 - Dyed Black
Customer | True North Design |
Purpose | Structural and vacuum EOAT components |
Process | SLS / MJF |
Unit price | $69.![]() |
Industry | Automotive |
Prototyping PLA
Customer | Allision Conner |
Purpose | End caps and cable strain relief for sheet metal enclosure |
Process | FDM |
Unit price | $7.92 / $4.72 / $2.80 |
Industry | Industrial Automation |
HP PA 12
Customer | US Hammer |
Description | A part for gasoline engine powered jackhammers |
Process | MJF |
Unit price | $22.18 |
Industry | Construction |
Markforged Onyx - Black
Customer | Autocom Manufacturing |
Purpose | A production part for 3D printed lathe gantry gripper fingers |
Process | FDM |
Unit price | $48.![]() |
Industry | Automotive |
PC Stratasys - white
Customer | Terumo medical corporation |
Purpose | Prototyping parts used for a disposable electrical device |
Process | FDM |
Unit price | $55.38 / $32.96 |
Industry | Medical |
Formlabs Clear Resin
Customer | Aversan Inc |
Purpose | A prototyping part of an injection molded component for an automated door mechanism |
Process | SLA |
Unit price | $29.83 |
Industry | Aerospace |
HP PA 12 - Dyed Black
Customer | True North Design |
Purpose | Structural and vacuum EOAT components |
Process | SLS / MJF |
Unit price | $69.![]() |
Industry | Automotive |
Prototyping PLA
Customer | Allision Conner |
Purpose | End caps and cable strain relief for sheet metal enclosure |
Process | FDM |
Unit price | $7.92 / $4.72 / $2.80 |
Industry | Industrial Automation |
HP PA 12
Customer | US Hammer |
Description | A part for gasoline engine powered jackhammers |
Process | MJF |
Unit price | $22.18 |
Industry | Construction |
Markforged Onyx - Black
Customer | Autocom Manufacturing |
Purpose | A production part for 3D printed lathe gantry gripper fingers |
Process | FDM |
Unit price | $48.![]() |
Industry | Automotive |
PC Stratasys - white
Customer | Terumo medical corporation |
Purpose | Prototyping parts used for a disposable electrical device |
Process | FDM |
Unit price | $55.38 / $32.96 |
Industry | Medical |
Formlabs Clear Resin
Customer | Aversan Inc |
Purpose | A prototyping part of an injection molded component for an automated door mechanism |
Process | SLA |
Unit price | $29.83 |
Industry | Aerospace |
HP PA 12 - Dyed Black
Customer | True North Design |
Purpose | Structural and vacuum EOAT components |
Process | SLS / MJF |
Unit price | $69.![]() |
Industry | Automotive |
Prototyping PLA
Customer | Allision Conner |
Purpose | End caps and cable strain relief for sheet metal enclosure |
Process | FDM |
Unit price | $7.92 / $4.72 / $2.80 |
Industry | Industrial Automation |
HP PA 12
Customer | US Hammer |
Description | A part for gasoline engine powered jackhammers |
Process | MJF |
Unit price | $22.18 |
Industry | Construction |
Markforged Onyx - Black
Customer | Autocom Manufacturing |
Purpose | A production part for 3D printed lathe gantry gripper fingers |
Process | FDM |
Unit price | $48.![]() |
Industry | Automotive |
PC Stratasys - white
Customer | Terumo medical corporation |
Purpose | Prototyping parts used for a disposable electrical device |
Process | FDM |
Unit price | $55.38 / $32.96 |
Industry | Medical |
Formlabs Clear Resin
Customer | Aversan Inc |
Purpose | A prototyping part of an injection molded component for an automated door mechanism |
Process | SLA |
Unit price | $29.83 |
Industry | Aerospace |
HP PA 12 - Dyed Black
Customer | True North Design |
Purpose | Structural and vacuum EOAT components |
Process | SLS / MJF |
Unit price | $69.![]() |
Industry | Automotive |
Prototyping PLA
Customer | Allision Conner |
Purpose | End caps and cable strain relief for sheet metal enclosure |
Process | FDM |
Unit price | $7.92 / $4.72 / $2.80 |
Industry | Industrial Automation |
HP PA 12
Customer | US Hammer |
Description | A part for gasoline engine powered jackhammers |
Process | MJF |
Unit price | $22.18 |
Industry | Construction |
Markforged Onyx - Black
Customer | Autocom Manufacturing |
Purpose | A production part for 3D printed lathe gantry gripper fingers |
Process | FDM |
Unit price | $48.![]() |
Industry | Automotive |
PC Stratasys - white
Customer | Terumo medical corporation |
Purpose | Prototyping parts used for a disposable electrical device |
Process | FDM |
Unit price | $55.38 / $32.96 |
Industry | Medical |
Formlabs Clear Resin
Customer | Aversan Inc |
Purpose | A prototyping part of an injection molded component for an automated door mechanism |
Process | SLA |
Unit price | $29.83 |
Industry | Aerospace |
HP PA 12 - Dyed Black
Customer | True North Design |
Purpose | Structural and vacuum EOAT components |
Process | SLS / MJF |
Unit price | $69.![]() |
Industry | Automotive |
Prototyping PLA
Customer | Allision Conner |
Purpose | End caps and cable strain relief for sheet metal enclosure |
Process | FDM |
Unit price | $7.92 / $4.72 / $2.80 |
Industry | Industrial Automation |
HP PA 12
Customer | US Hammer |
Description | A part for gasoline engine powered jackhammers |
Process | MJF |
Unit price | $22.18 |
Industry | Construction |
Markforged Onyx - Black
Customer | Autocom Manufacturing |
Purpose | A production part for 3D printed lathe gantry gripper fingers |
Process | FDM |
Unit price | $48.![]() |
Industry | Automotive |
PC Stratasys - white
Customer | Terumo medical corporation |
Purpose | Prototyping parts used for a disposable electrical device |
Process | FDM |
Unit price | $55.38 / $32.96 |
Industry | Medical |
Formlabs Clear Resin
Customer | Aversan Inc |
Purpose | A prototyping part of an injection molded component for an automated door mechanism |
Process | SLA |
Unit price | $29.83 |
Industry | Aerospace |
HP PA 12 - Dyed Black
Customer | True North Design |
Purpose | Structural and vacuum EOAT components |
Process | SLS / MJF |
Unit price | $69.![]() |
Industry | Automotive |
Prototyping PLA
Customer | Allision Conner |
Purpose | End caps and cable strain relief for sheet metal enclosure |
Process | FDM |
Unit price | $7.92 / $4.72 / $2.80 |
Industry | Industrial Automation |
HP PA 12
Customer | US Hammer |
Description | A part for gasoline engine powered jackhammers |
Process | MJF |
Unit price | $22.18 |
Industry | Construction |
Markforged Onyx - Black
Customer | Autocom Manufacturing |
Purpose | A production part for 3D printed lathe gantry gripper fingers |
Process | FDM |
Unit price | $48.![]() |
Industry | Automotive |
PC Stratasys - white
Customer | Terumo medical corporation |
Purpose | Prototyping parts used for a disposable electrical device |
Process | FDM |
Unit price | $55.38 / $32.96 |
Industry | Medical |
Formlabs Clear Resin
Customer | Aversan Inc |
Purpose | A prototyping part of an injection molded component for an automated door mechanism |
Process | SLA |
Unit price | $29.83 |
Industry | Aerospace |
HP PA 12 - Dyed Black
Customer | True North Design |
Purpose | Structural and vacuum EOAT components |
Process | SLS / MJF |
Unit price | $69.![]() |
Industry | Automotive |
Prototyping PLA
Customer | Allision Conner |
Purpose | End caps and cable strain relief for sheet metal enclosure |
Process | FDM |
Unit price | $7.92 / $4.72 / $2.80 |
Industry | Industrial Automation |
HP PA 12
Customer | US Hammer |
Description | A part for gasoline engine powered jackhammers |
Process | MJF |
Unit price | $22.18 |
Industry | Construction |
Markforged Onyx - Black
Customer | Autocom Manufacturing |
Purpose | A production part for 3D printed lathe gantry gripper fingers |
Process | FDM |
Unit price | $48.![]() |
Industry | Automotive |
PC Stratasys - white
Customer | Terumo medical corporation |
Purpose | Prototyping parts used for a disposable electrical device |
Process | FDM |
Unit price | $55.38 / $32.96 |
Industry | Medical |
Formlabs Clear Resin
Customer | Aversan Inc |
Purpose | A prototyping part of an injection molded component for an automated door mechanism |
Process | SLA |
Unit price | $29.83 |
Industry | Aerospace |
HP PA 12 - Dyed Black
Customer | True North Design |
Purpose | Structural and vacuum EOAT components |
Process | SLS / MJF |
Unit price | $69.![]() |
Industry | Automotive |
Prototyping PLA
Customer | Allision Conner |
Purpose | End caps and cable strain relief for sheet metal enclosure |
Process | FDM |
Unit price | $7.92 / $4.72 / $2.80 |
Industry | Industrial Automation |
HP PA 12
Customer | US Hammer |
Description | A part for gasoline engine powered jackhammers |
Process | MJF |
Unit price | $22.18 |
Industry | Construction |
Markforged Onyx - Black
Customer | Autocom Manufacturing |
Purpose | A production part for 3D printed lathe gantry gripper fingers |
Process | FDM |
Unit price | $48.![]() |
Industry | Automotive |
PC Stratasys - white
Customer | Terumo medical corporation |
Purpose | Prototyping parts used for a disposable electrical device |
Process | FDM |
Unit price | $55.38 / $32.96 |
Industry | Medical |
Formlabs Clear Resin
Customer | Aversan Inc |
Purpose | A prototyping part of an injection molded component for an automated door mechanism |
Process | SLA |
Unit price | $29.83 |
Industry | Aerospace |
HP PA 12 - Dyed Black
Customer | True North Design |
Purpose | Structural and vacuum EOAT components |
Process | SLS / MJF |
Unit price | $69.![]() |
Industry | Automotive |
Prototyping PLA
Customer | Allision Conner |
Purpose | End caps and cable strain relief for sheet metal enclosure |
Process | FDM |
Unit price | $7.92 / $4.72 / $2.80 |
Industry | Industrial Automation |
HP PA 12
Customer | US Hammer |
Description | A part for gasoline engine powered jackhammers |
Process | MJF |
Unit price | $22.18 |
Industry | Construction |
Markforged Onyx - Black
Customer | Autocom Manufacturing |
Purpose | A production part for 3D printed lathe gantry gripper fingers |
Process | FDM |
Unit price | $48.![]() |
Industry | Automotive |
PC Stratasys - white
Customer | Terumo medical corporation |
Purpose | Prototyping parts used for a disposable electrical device |
Process | FDM |
Unit price | $55.38 / $32.96 |
Industry | Medical |
Formlabs Clear Resin
Customer | Aversan Inc |
Purpose | A prototyping part of an injection molded component for an automated door mechanism |
Process | SLA |
Unit price | $29.83 |
Industry | Aerospace |
Instant, online 3D printing quotes
-
Upload a CAD to start (STEP, STP, IGES, IGS, SLDPRT, 3DM, SAT, STL, OBJ or X_T)
-
Price updates in real-time as you change materials, lead time, etc.
.
-
No hidden costs. Our instant quotes are not just indications, but the actual price, and include shipping and customs up front.
Learn about how our quoting algorithm works
Our ordering process
Receive instant quote
Upload your CAD to our online quoting platform
Confirm specs
Configure your part specifications and select a lead time that suits your schedule
Production
We select the best manufacturer for your order, and production begins immediately
Quality control
We take full responsibility for making sure your parts are manufactured according to our standards
Delivery
Our 3D printing service has been rated 4.9/5
Over 280 customers are satisfied with our 3D printing service.
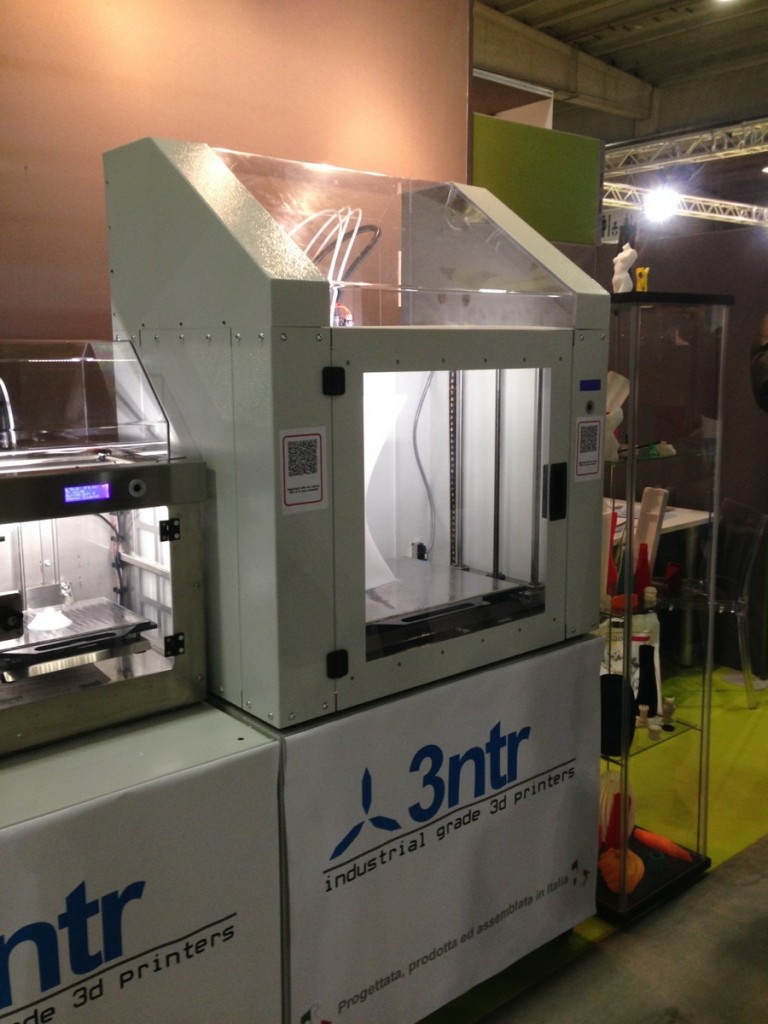
“Very accurate prototypes were received, including the 0.6 mm diameter eyelets. ”
“Great parts, arrived quickly. Good doing business.”
“Everything turned out as expected, thanks!”
“Great prints and communication! Perfectly balanced as everything should be. ”
“Fantastic service, awesome printing, and FAST! Will definitely order again!”
“Great quality on the parts and great communication. Would highly recommend!!”
“Outstanding. Great quality, service and turnaround. Very satisfied.”
“Items were printed according to the models I sent. Can't ask for much more than that! Thanks so much, came out great!”
“Excellent dimensional accuracy. Typically better than 0.002". Faster turn around than advertised.”
“Great work on these parts! I'm really happy with the customer service you guys provided as well. ”
“Excellent with printing quality and taking responsibility to reach the satisfied quality.”
“Very accommodating and helpful as always!”
“Fast, built to specification, and affordable. ”
“Only a couple minor print errors, overall the parts are what I need and fit together perfectly.”
“Very quick service. Short, sweet, and to the point. No complaints on my end”
“Loved it! Very prompt service & replies. ”
“Excellent work, and much faster than expected!”
“Awesome print quality, affordable pricing, rapid turn-around time, and very fast shipping! Will definitely use again for future 3D printing needs!”
“Would definitely use this service again! Fast, Great quality, matched my design perfectly.”
“Perfect! Thanks very much and have a great day.”
“Professional, helpful, perfect print, and a pleasure to work with. ”
“Excellent communication and response time. ”
“The prints are perfect. Ordered and received within a weeks time. Fast, reliable, and quality product and service.”
“Super fast service! Prints came out great!”
“Perfect prints. everything turned out great. ”
Show more reviews
Show less reviews
Teams build better parts
Create your Hubs team and start collaborating
Read more
The Hubs Standard - consistent quality, every time
Hubs takes the stress out of manufacturing by guaranteeing the quality and consistency of every part. Each order is dimensionally and visually inspected to make sure it meets the Hubs Standard.
3D printing materials
We can generate instant 3D printing quotes for 25+ plastics. For metal 3D-printed parts, you can request a quote from our parent company, Protolabs.
Available materials
SLS
PA 12 Glass filled PA 12
Desktop FDM
Prototyping PETG Prototyping ASA Prototyping TPU Prototyping ABS Prototyping PLA
Desktop SLA
Formlabs Standard Resin Formlabs Clear Resin Formlabs Tough Resin 2000 Formlabs Rigid Resin 4000 Formlabs Grey Pro Resin Formlabs Flexible Resin 80A Formlabs High Temp Resin Formlabs Durable Resin
MJF
HP PA 12 Glass filled HP PA 12
Industrial FDM
Markforged Onyx ABSplus Stratasys ULTEM 9085 Stratasys Stratasys ASA ABS M30 Stratasys ULTEM 1010 Stratasys
Industrial SLA
Accura 25 (PP-like) Accura ClearVue Accura Xtreme White 200 (ABS-like)
3D printing locations near Jacksonville, FL
Jacksonville, FL Gainesville, FL St. Augustine, FL
Ocala, FL Palm Coast, FL The Villages, FL
Daytona Beach, FL Leesburg, FL Brunswick, GA
Port Orange, FL
The 3D Printing Handbook
No one understands 3D printing like us - our founders literally wrote the book. Click here to download the sample chapters.
Buy the book from Amazon
FAQ's
How much does your 3D printing service cost?
The cost of your 3D printed parts depends on factors such as part volume, part complexity, choice of material, which 3D printing technology is used, and if any post processing is required. For more details on these cost factors, see our article on the cost of 3d printing. To check the cost of your 3D printed part, simply upload a CAD (.STL) file and select your material and 3D printing technology to receive a quote within seconds.
How do you guarantee the quality of my prints?
Your parts are made by experienced 3D printing shops within our network. All facilities are regularly audited to ensure they consistently meet the Hubs quality standard. We include a standardized inspection report with every order and offer a First Article Inspection service on orders of 100+ units.
We have partners in our network with the following certifications, available on request: ISO9001, ISO13485 and AS9100.
Follow this link to read more about our quality assurance measures.
How do I select the right 3D printing process for my prints?
You can select the right 3D printing process by examining which materials suit your need and what your use case is.
By material: if you already know which material you would like to use, selecting a 3D printing process is relatively easy, as many materials are technology specific.
By use case: once you know whether you need a functional or visual part, choosing a process is easy.
For more help, read our guide to selecting the right 3D printing process. Find out more about Fused Deposition Modeling (FDM), Selective Laser Sintering (SLS), Multi Jet Fusion (MJF) and Stereolithography (SLA).
How can I reduce the cost of my 3D prints?
In order to reduce the cost of your 3D prints you need to understand the impact certain factors have on cost. The main cost influencing factors are the material type, individual part volume, printing technology and post-processing requirements.
Once these have been decided, an easy way to further cut costs is to reduce the amount of material used. This can be done by decreasing the size of your model, hollowing it out, and eliminating the need for support structures.
To learn more, read our full guide on how to reduce the cost of 3D printing.
Where can I learn more about 3D printing?
Our knowledge base is full of in-depth design guidelines, explanations on process and surface finishes, and information on how to create and use CAD files. Our 3D printing content has been written by an expert team of engineers and technicians over the years.
See our complete engineering guide to 3D printing for a full breakdown of the different 3D printing technologies and materials. If you want even more 3D printing, then check out our acclaimed 3D printing handbook here.
We have an extensive range of online resources developed to help engineers improve their capabilities.
Introductory guides
Design guides
Material guides
Applications
CAD & file preparation
Post processing & finishing
Our other manufacturing capabilities
CNC machining
CNC machining
Milling (3-, 4- & full 5-axis), turning and post-processing
-
50+ metals and plastics & 10 surface finishes
-
Tolerances down to ±.
0008” (0.020 mm)
-
Lead times from 5 business days
See our CNC machining services
Put your 3D printed parts into production today
Get an instant 3D printing quote
3D Printing Service for Jacksonville, Florida
CapabilitiesCustom Online 3D Printing ServiceFloridaJacksonville
High Quality Jacksonville, Florida 3D Printing | 60+ Materials Available
Endless Options
Choose from millions of possible combinations of materials, finishes, tolerances, markings, and certifications for your order.
Easy to Use
Get your parts delivered right to your door without the hassle of sourcing, project management, logistics, or shipping.
Quality Assurance
Our number one job at Xometry is making your custom parts to your specifications.
Your Jacksonville, Florida 3D Printing Service: 3D Prototypes and Production Parts
A Global Leader in Industrial-Grade 3D Printing
Xometry is an industry-leading 3D printing service. Whether you need prototypes or production parts, we can make them for you in as fast as a day. We are your one-stop-shop for accurate, precise custom 3D printed parts at a low cost. Upload your 3D CAD file to get a quote and lead time within seconds. We use the latest additive manufacturing processes to build affordable functional prototypes & end-use parts in over 60 metals and plastics.
We offer eight high-quality 3D printing processes including selective laser sintering, fused deposition modeling, stereolithography, direct metal laser sintering, polyjet, Carbon DLS, binder jet metal, and HP Multi Jet Fusion. We use commercial and industrial-grade printers such as Stratasys Fortus 900mc and Fortus 450 FDM, EOS Polymer Laser Sintering (SLS) and DMLS, Concept Laser, SLM Solutions, 3D Systems, ExOne, and more.
Xometry's High Quality 3D Printing Services
Selective Laser Sintering (SLS)
Selective Laser Sintering (SLS) is a powerful 3D printing technology that produces highly accurate and durable parts that are capable of being used directly in end-use, low-volume production, or for rapid prototyping.
An additive manufacturing layer technology, SLS involves the use of a high power laser (for example, a carbon dioxide laser) to fuse small particles of plastic powders into a mass that has a desired three-dimensional shape. The laser selectively fuses powdered material by scanning cross-sections generated from a 3-D digital description of the part (for example from a CAD file or scan data) on the surface of a powder bed. After each cross-section is scanned, the powder bed is lowered by one layer thickness, a new layer of material is applied on top, and the process is repeated until the part is completed.
Download the SLS Design Guide.
Stereolithography (SLA)
Stereolithography (SLA) is a robust 3D printing technology that produces extremely accurate and high-resolution parts that are capable of being used directly in end-use, low-volume production, or for rapid prototyping.
SLA is an additive manufacturing process that focuses an ultraviolet (UV) light on a vat of photopolymer resin. It offers higher resolution printing than many other 3D printing technologies, allowing customers to print parts with fine details and surface finishes. SLA 3D printing is a highly-versatile platform for making custom parts in prototype and production settings; often acting as a stand-in for injection-molded plastic parts.
Xometry offers both standard and high-resolution options for fine detail parts, and can also print larger sized parts and products, with some materials offering up to a 58" inch build area. In addition, Xometry's manufacturing partner network allows us to offer a larger variety of materials than other 3D printing companies - we offer a wide range of both Accura and Somos brand materials.
Download the SLA Design Guide.
Fused Deposition Modeling (FDM)
Fused Deposition Modeling (FDM) is a 3D printing technology widely known for its speed, accuracy, and competitive cost. A machine precisely extrudes melted plastic filament to create a part. Parts are very rigid, especially compared to Selective Laser Sintering (SLS), which makes them a great fit for projects with a rigidity requirement. Xometry's FDM solution offers large build volumes up to 24″ x 36″ x 36″, a variety of colors, and a diverse selection of production-grade thermoplastics — from ABS to Polycarbonate to Ultem.
Download the FDM Design Guide.
HP Multi Jet Fusion (HP MJF)
HP Multi Jet Fusion is a new 3D printing technology that produces highly accurate and durable parts that are capable of being used directly in end-use, low-volume production, or for rapid prototyping. Since the process uses well-established 2D printing ink-jetting, it has remarkably fast layer times compared to other powder bed fusion technologies.
Download the HP Multi Jet Fusion Design Guide.
PolyJet 3D (PJ3D)
PolyJet 3D is a 3D printing technology known for its customizable material properties and excellent surface finish. It works by jetting UV curable resin onto a build tray in a process that is somewhat similar to inkjet printing. PolyJet 3D printing offers one of the most advanced industrial 3D printing solutions available, producing parts with incredible precision and speed. It also supports a wide variety of build materials including rigid and rubber-like plastics. Xometry's PolyJet solution has a maximum build envelope of 19.3 × 15.4 × 7.9 in. (490 × 390 × 200 mm) in a variety of colors and materials.
Download the PolyJet 3D Design Guide.
Direct Metal Laser Sintering (DMLS)
Direct Metal Laser Sintering (DMLS) is an 3D metal printing technology that builds prototype and production metal parts from a CAD file using a laser to selectively fuse a fine metal powder in either stainless steel or aluminum materials. A DMLS machine is capable of producing highly complex features and all-in-one assemblies using metal materials that would be difficult to achieve with subtractive manufacturing techniques.
Our DMLS metal 3D printing service typically offers build volumes up to 250 x 250 x 325 mm, but we may be able to accommodate larger part volumes upon request in the quote. (See our Manufacturing Standards for more details) A good first step is to find out the cost of the parts you need using DMLS and compare them to other 3D printing processes and CNC machining.
Download the DMLS Design Guide.
Carbon DLS™
Carbon DLS™ uses digital light projection, oxygen-permeable optics, and programmable liquid resins to produce products with end-use durability, resolution and surface finish. This 3D printing technology is called Digital Light Synthesis™, or DLS for short. Another legacy term for the process is Continuous Liquid Interface Production (CLIP). Along with Carbon’s custom liquid resins, DLS unlocks new business opportunities and product designs previously impossible, including mass customization and on-demand inventory of end-use products.
Carbon bridges, and sometimes substitutes, for processes like Urethane Casting and Injection Molding service production, because the materials are urethane-based or epoxy-based, giving excellent mechanical properties. There are even elastomer and silicone resins that outperform most additive manufactured rubber-like materials.
The typical build area is 7.4” x 4. 6” x 12.8”. Parts with dimensions exceeding 4” x 4” x 6” will require manual review.
Download the Carbon DLS Design Guide.
Metal Binder Jetting
With binder jetting, an inkjet print head quickly deposits a bonding agent onto a thin layer of powdered particles -- either metal, sand, ceramics or composites. This process is repeated, layer-by-layer, using a map from a digital design file, until the object is complete. Binder jetting is offered through our Digital RFQ Marketplace through Xometry's partnership with ExOne.
Download the Binder Jetting Design Guide.
Locations near Jacksonville, Florida
Gainesville
FloridaOrlando
FloridaSavannah
GeorgiaTallahassee
FloridaTampa
FloridaClearwater
FloridaSaint Petersburg
FloridaCharleston
South CarolinaMacon
GeorgiaSarasota
FloridaAugusta
GeorgiaPort Saint Lucie
FloridaColumbia
South CarolinaCape Coral
FloridaAthens
GeorgiaAtlanta
GeorgiaBoca Raton
FloridaFort Lauderdale
FloridaMontgomery
AlabamaGreenville
South Carolina
Ready to start making custom 3D printed parts?
Made in Space, Inc.
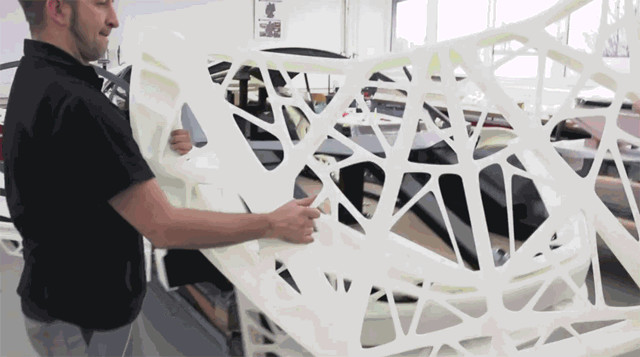
Made in Space, Inc. (MIS ) is an American company specializing in the design and manufacture of 3D printers for use in microgravity. Headquartered in Jacksonville, Florida, the Made In Space 3D Printer (Zero-G Printer) was the first manufacturing device to be used in space.
Contents
- 1 History
- 2 Zero-G 3D printing demonstration
- 3 Golden plate of John Lomberg
- 4 Additative production installation
- 5 Plastic processing for 3D printer
- 6 Production of large-sized structures in space
- 7 fiber optics
- 8 Other lessons
- 9 See also
History
Made In Space was founded in August 2010 by Aaron Kemmer, Jason Dunn, Mike Chen, and Michael Snyder during the Singularity University Graduate Program. Their main mission is to enable humanity to become a multi-planetary species. In the spring of 2011, Made In Space opened a 3D printing lab at NASA's Ames Research Center at Moffett Field in Mountain View, California. That summer, they qualified for a suborbital flight for the printer as part of the NASA Flight Opportunities Program. From July to September 2011, the Made In Space team performed over 400 test parabolas in microgravity on NASA's reduced gravity aircraft ("Comet Vomit"), proving its 3D printing in microgravity. With this proven concept, Made In Space received a Phase 1 Small Business Innovation Research (SBIR) grant to test a 3D printer design on the International Space Station (ISS). [3]
In January 2013, Made In Space received an order to participate in the second phase of SBIR for the construction and flight qualification of an additive manufacturing facility with their 3D printer for the International Space Station (ISS). [4] In February 2013, stage 3 was scheduled to deliver their 3D printer to the ISS.
In May 2014, NASA awarded Made In Space a Phase 1 contract to SBIR for the development of a waste recycling device for use with the ISS 3D printer and for their micropit project. Shortly thereafter, Made In Space was awarded the ISS Space Flight Awareness Award. This award recognizes "teams that have significantly improved the efficiency, cost, or capability of spaceflight." [5]
In June 2014, Made In Space demonstrated its manufacturing capabilities in space at the White House Maker Faire. [6]
On September 21, 2014 at 1:52 am ET (0552 GMT), the Made In Space Zero-G printer was launched from Cape Canaveral, Florida to the ISS aboard a SpaceX CRS-4. On November 17th, astronaut Barry "Butch" Wilmore unpacked the 3D printer from its launch package. November 24 at approximately 13:28. PST, Made In Space has successfully printed the first part ever made in space. On December 11, 2014, the first functional application for the Made In Space printer was announced: a buckle designed by NASA astronaut Yvonne Cagle. This buckle is a piece of exercise equipment to help reduce muscle loss in zero gravity.
December 12, 2014 Cooper Hewitt, Smithsonian Design Museum reopened after three years of renovations. The Made In Space 3D Printer was one of their re-opening exhibits at the "Tools: Expanding Our Reach" showroom. [7] The Zero-G Printer was presented along with replicas of 13 of the first 21 objects printed in space, and a replica of the plate attached to the printer, which was created by John Lomberg, the artist who created the Voyager Golden Record.
On December 17, 2014, the first uplink-related tool, a ratchet, was made on the ISS. All other products made earlier were printed before launch, and the files were available via SD Card launched along with the printer. The ratchet files were sent from the Made In Space office to the ISS space station. It took four hours to print the ratchet. [8]
On September 27, 2018, the company announced an agreement with local authorities to open its European subsidiary in Luxembourg. Made in space, Europe will work to develop a low cost modular robotic arm for space applications. [9]
On January 17, 2020, Florida Gov. Ron DeSantis announced that the company's headquarters will be relocated from Mountain View, California to Jacksonville, Florida. The relocation and headquarters expansion will require more than $3 million in new capital investment for Jacksonville. [10]
Made in Space was acquired in June 2020 by Redwire [11] (a newly formed company from the merger of Deep Space System and Adcole Space). [12]
Zero-G Demonstration 3D Printing
In May 2013, it was announced that NASA and Made In Space had sent the first 3D printer into space, known as Zero-G Demonstration 3D printing (also known as 3D printing in the Zero-G experiment or 3D printing in Zero-G). The scientific goal of this experiment was to prove that a 3D printer could be designed for use in zero gravity. This experiment "is the first step towards establishing an on-demand machine shop in space, an essential component for crewed deep space flight and space manufacturing." [13]
Zero-G 3D printing integrated into a microgravity (MSG) glove box is a proof-of-concept experiment. It involves printing multiple copies of the planned elements to test several variables including dimensions, layer adhesion, tear strength, flexibility, and compressive strength. These items, known as "coupons", will be tested by the American Society for Testing and Materials (ASTM) and compared to Earth-printed copies. A comparison of these coupons for space and ground production will be used to further improve 3D printing in space. [13]
John Lomberg's Gold Plate
Inspired by John Lomberg working on Voyager Gold Recording Lomberg worked with Made In Space to create the Gold Plate to commemorate the first production of something in space. It is attached from the inside so it can be seen through the front viewing window. [ citation needed ]
The Golden Plate features images that symbolize both the Zero Gravity 3D Printing project and the people who played an important role in its implementation. These features include 27 stars that represent 16 key contributors from the Marshall Space Flight Center; 10 Key Employees of Made In Space, Inc. and John Lomberg; a comet symbolizing all the other people who support "Made in Space"; and Star Trek The character Jean-Luc Picard's binary phrase "Make it like this" symbolizes the functionality that a 3D printer brings to the ISS. [ citation needed ]
Additive Manufacturing Unit
In April 2016, an additive manufacturing unit was installed on board the ISS. It is designed to be available for use by NASA as well as other government agencies, academic institutions, and businesses. [14] It can currently print 10 x 10 x 14 cm objects in three different polymers, including acrylonitrile butadiene styrene (ABS), high density polyethylene (HDPE), and polyetherimide/polycarbonate composite (PEI-PC). [15]
3D printer plastic recycling
In 2014, NASA selected Made In Space as one of several companies that developed a 3D printing material recycler on the ISS. [16] In the subsequent request, Made In Space was not selected for Phase II SBIR. [17] [18]
Large Structure Manufacturing in Space
Made In Space is working with Northrop Grumman and Seafaring to build and demonstrate Archinaut, a versatile robotic system for precision manufacturing and assembly in space. [19] Archinaut will enable space-based fabrication and assembly of frame structures for large telescopes, the repair, enlargement or repurposing of existing spacecraft, and the robotic assembly of new space stations. MIS is currently ground-testing a central spar that can be slid onto the folded solar arrays and locked in place. A demonstration flight is expected in 2022 on the Elektron rocket. [19]
The company released video demonstrations of Archinaut's robotics assembly and robotics development lab, as well as animations demonstrating Archinaut's space-based assembly and manufacturing capabilities. [20] [21] [22]
Fiber optics
Years of experimental payloads produce test quantities of ZBLAN fiber optics. Based on the results of initial experiments and market demand, Made In Space plans to develop and operate large-scale microgravity manufacturing facilities for ZBLAN and other microgravity materials. MIS teamed up with ThorLabs to develop fiber optics. The advantage of microgravity-produced fiber optics is much lower signal loss, which is beneficial for long-distance communications, medical research, supercomputing, and many other industries and applications. [23]
Other activities
In 2018, MIS was awarded a 24-month extension of the Small Business Innovation Research award for its Vulcan and Industrial Crystallization Facility (ICF). The Vulcan Advanced Hybrid Manufacturing System is an additive and subtractive manufacturing technology being developed for space applications. [24] Vulcan enables precision-machined metal parts to be produced in the field of use, such as the International Space Station or future manned space platforms. ICF at the International Space Station will also produce reusable optical crystals for use in microgravity space. Optical crystals are used in industries such as computers and data processing systems. [25] The MIS recycling facility is expected to be sent to the International Space Station in late 2019. The facility will take plastic waste and waste plastic parts and physically convert them into spools of raw materials for a space station additive manufacturing facility used to make parts in space. [26]
See also
- Space Portal
- San Francisco Bay Area Portal 9 Werner, Debra (October 21, 2019). "Made in space to launch a commercial recycler to the space station." SpaceNews . Retrieved October 22, 2019.
- Vertical motor pitch: 10 microns
- Layer thickness: 100 microns
- Horizontal resolution: 270 microns
- Print speed: 10 seconds per 0.
1 mm thick layer.
- Dimensions: 620*600*480 mm.
- 3.2" touchscreen display
- Ways to transfer the instruction file from a computer: Wi-fi, Ethernet, USB
- Operating system support: Windows XP/7/8.x, Mac OSX and Linux Ubuntu
High Volume, High Speed Photolithographic 3D Printer
Archive
Jacksonville, Florida-based Tangible Engineering is committed to making photolithographic 3D printing more accessible with the launch of its Solidator desktop photolithographic 3D printer. When developing this printer, the Tangible Engineering team focused on three criteria: the size of the working area, speed and resolution (quality).
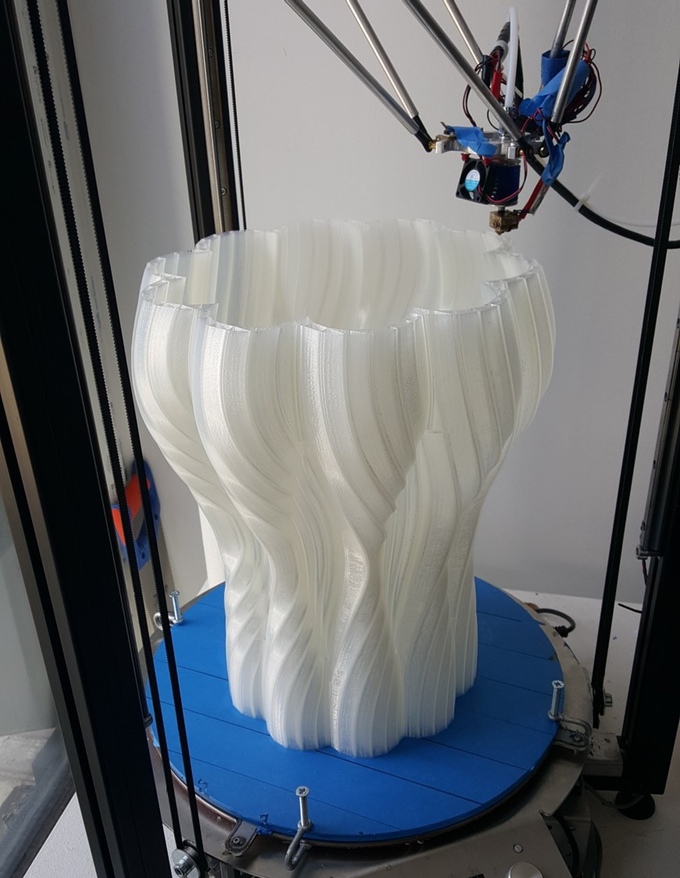
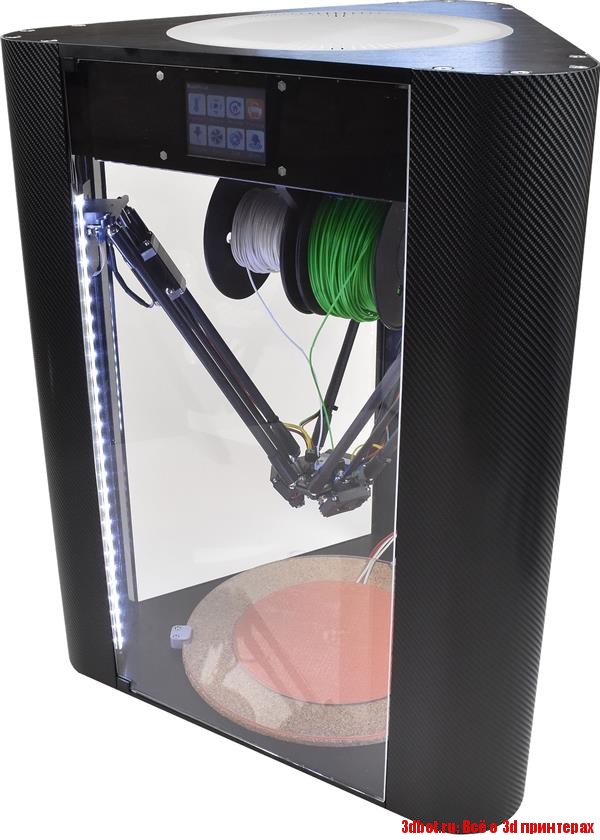
The declared cost of this miracle - 4950 dollars apiece. However, compared to the prices of other photolithographic printers of this level, this is not a bad price. For more details, see the KickStarter page. If you would like to have a high-precision photolithographic printer, but are not ready to pay a pretty tidy sum for it, and you like to work with your hands, we recommend that you look at an article about a stereolithographic 3D printer, the drawings and assembly instructions of which the author posted in the public domain so that everyone can assemble a high resolution 3D printer. Article prepared for 3dtoday.ru
Follow author
Follow
Don't want
Article comments
More interesting articles
6
Subscribe to the author
Subscribe
Don't want
One of the latest developments in 3D printing devices has been the advent of extruders.