3D printed jet engine plans
Integza's latest 3D printing project: a working electric jet engine
0Shares
Tech Youtuber Integza has showcased his latest 3D printing project, a fully-functional electric jet engine built from scratch.
Loosely based on the design of a conventional turbojet engine, the miniature device doesn’t use jet fuel at all. Instead, it leverages an electric motor, a DIY body made of tin, and an entirely 3D printed compressor fan, generating enough thrust to move a skateboard.
Integza has been trying to 3D print a working jet engine (that doesn’t melt) for some time now, so his latest project is a step towards realizing his long-standing dream.
He said, “I’m very happy about the fact that I built a jet engine and it didn’t melt in the first ten seconds. I mean I’m so happy that I don’t even care about the fact that I accidentally burnt my microphone.”
The electric jet engine generated enough thrust to power a skateboard. Photo via Integza.The beauty of the turbojet engine
The turbojet engine is often regarded as the crème de la crème of jet engines.
What makes the engineering marvel so great is that it actually has a fairly simple working premise. A fast-spinning bladed compressor sucks in air, which is mixed with fuel and ignited in a combustion chamber. The exhaust from the reaction is then directed out the back of the engine, generating thrust.
Turbojet designs are also self-sustaining in that the energy from the exhaust is recycled back into the compressor to keep the entire assembly moving. This is done via a turbine at the back that’s connected to the compressor at the front. This rear turbine is placed in the path of the high-speed exhaust which spins it, in turn spinning the compressor at the front to create a feedback loop. This is also the basic idea behind turbochargers in cars.
While the theory behind turbojets is actually quite digestible, actually building one is an entirely different beast. For turbojets to work, all of the components need to be perfectly balanced and all of the turbines need to spin at up to 25,000RPM or more. This is impossible to achieve in a garage workshop so Integza simply replaced the rear turbine with an electric motor to power the compressor.
Building the electric jet engine
The first step of the project was to build the engine’s casing. For this, he had the idea of repurposing two butane canisters as they already had the right size and shape for the jet engine. Integza emptied the cans out and welded them together to create the body.
Next up was the compressor. Luckily, the compressor is stored in the cold part of the engine away from any heat, so it’s possible to simply 3D print the impeller blades using any run-of-the-mill polymer like ABS.
Now comes the tricky part: creating and controlling the combustion. It wasn’t enough to simply inject butane gas into the body and ignite it, as this would be far too inefficient to generate thrust. The engine needed a steady stream of low-speed, high-pressure air directed towards the back. To enable this, modern-day turbojets use a special type of combustion chamber called an annular combustion chamber, so Integza built his own using a DIY spot welder. He also built a low-cost spark plug for ignition.
Once assembled, he strapped the jet engine to a skateboard and connected it to a battery-powered electric motor to spin the compressor. Amazingly, it worked. Despite weighing in at only 325g, the electric jet engine generated enough thrust to push the 3.2kg skateboard (albeit at a snail’s pace).
Content creators like Integza provide an accessible way for us to learn more about 3D printing and its capabilities. Last year, he also used 3D printing technology to develop a low-cost functional rocket engine inspired by an old, experimental Nazi design. Based on the engine of a 1930s German aircraft called the Heinkel He 176, the 3D printed rocket engine doesn’t rely on burning fuel or combustion at all, instead generating its thrust via a volatile chemical reaction.
More recently, YouTuber Austen Hartley designed and 3D printed his own pair of custom, low-cost Crocs. Armed with nothing but a standard desktop FFF 3D printer and flexible TPU filament, the mechanical engineer even printed a few additional accessories to provide that much-needed flair, including a logo and a sports car spoiler.
Subscribe to the 3D Printing Industry newsletter for the latest news in additive manufacturing. You can also stay connected by following us on Twitter, liking us on Facebook, and tuning into the 3D Printing Industry YouTube Channel.
Looking for a career in additive manufacturing? Visit 3D Printing Jobs for a selection of roles in the industry.
Featured image shows Integza and his electric jet engine. Photo via Integza.
Tags Integza
Kubi Sertoglu
Kubi Sertoglu holds a degree in Mechanical Engineering, combining an affinity for writing with a technical background to deliver the latest news and reviews in additive manufacturing.
GE's 3D-Printed Airplane Engine Will Run This Year
The last time engineers designed a civilian turboprop engine from scratch for mass-production, humans had not yet landed on the moon. Unlike jet engines, turboprops typically power small commercial shuttles and personal aircraft, but they still represent a multibillion-dollar market. As a result, a new machine created by a team at GE Aviation is now causing a stir.That’s because their engine, called the Advanced Turboprop (ATP), will be the first commercial aircraft engine in history with a large portion of components made by additive manufacturing methods, which include 3D printing. The designers reduced 855 separate parts down to just 12.
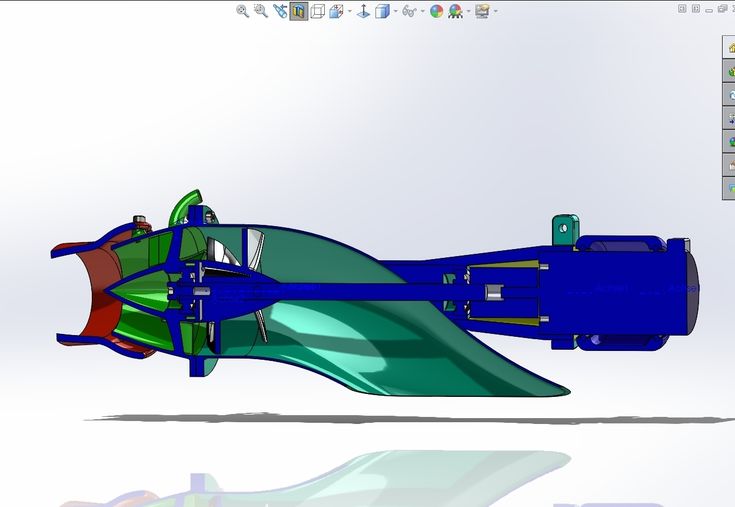
Engineers working on the ATP are planning to run it for the first time in a special test cell in Prague, Czech Republic, later this year. It should see its first test flight in late 2018, and full production is expected to begin in 2020. It will eventually provide the thrust for Cessna’s new single-engine, 10-person business aircraft design called Denali.
Additive manufacturing has helped the GE team bring the ATP from an idea to a working machine in record time. Announced in 2015, “the ATP is going from a dream to a reality in just two years,” says Gordie Follin, the executive manager of GE Aviation’s ATP program. The normal cycle to get to a running engine is usually twice as long, and it can take as much as 10 years to develop, Follin says. “With additive manufacturing, we’re disrupting the whole production cycle,” he says.
Overall, the 3D-printing effort will pay off by decreasing the finished ATP engine’s weight. The engine is 5 percent lighter, which means it will take the aircraft less fuel to attain the same speed. Design changes will allow the ATP to burn 20 percent less fuel and achieve 10 percent more power than its competitors.
Additive design, which accounts for 35 percent of the engine, is also disrupting maintenance because the ATP will have fewer assembled parts and opportunities for wear. The engine is expected to run 1,000 hours longer between overhauls compared to its competitors. “We’re no longer constrained by traditional design and engineering processes,” Follin says. “3D printing is letting us be more creative than we’ve ever been before.”
Follin’s group has already made all of the engine’s parts. They are now putting them together, adding instrumentation and getting ready to test critical sub-units.
Additive manufacturing also simplifies the supply chain and lowers the opportunities for delays. “These reductions are real,” Follin says. “We’re not putting so much effort into additive manufacturing because it’s a sexy new technology for its own sake. It’s demonstrably better. It lets us disrupt the process.”
GE has been aggressively developing its 3D-printing capabilities in recent years, so far spending $1 billion to mature the technology for its businesses. Last year, the company acquired two manufacturers of 3D-printing machines and launched GE Additive, a new GE business dedicated to supplying 3D printers, materials and engineering consulting services.
Additive manufacturing makes products stronger and more durable. In production aircraft engines, those investments have started paying dividends. CFM International, a joint venture between GE Aviation and Safran Aircraft Engines, is producing the advanced LEAP engine, which is being installed on Airbus’ and Boeing’s new fleet of narrow-body commercial airliners. Complex 3D-printed fuel nozzles on the engine contribute to LEAP’s 15 percent cut in fuel burn and emissions.
My seal is bright
We regularly write in the news (and you read) the adjective “printed”, which has become familiar, and it seems like everyone understands that we are talking about 3D printers. But the whole picture is not obtained; no, no, and the question will slip: “What can be printed on a 3D printer?” To use an exhaustive answer "a lot of things" with such a question is at least indecent. Therefore, together with Yota, we have selected several illustrative examples of 3D printing: from a coronary artery and a rocket engine to gadgets with meteorite chips. But first things first.
Organs, tissues and other medicine
3D printing allows even a relatively cheap printer to create objects with a high level of detail, which has proven useful in medical research. Vessels, cartilage, ovaries, and even an analogue of the cerebral cortex have already been printed on 3D printers. Despite the encouraging results, it is too early to say that humanity can print complex functional organs. Researchers have recently learned how to print shape-retaining prostheses with living cells, and 3D-printed blood vessels, although they are overgrown with capillaries, do it completely chaotically. But the current level of technology development is quite enough to print training ears for plastic surgeons.
At least there are no problems with pills - here 3D printing helps to experiment with the dosage and shape of the pills, which directly affects the release rate of the drug. In addition, at a quite applied level, 3D printing can be used in dentistry - one brave and confident student even corrected an overbite with the help of self-made aligners.
Separately, it is worth highlighting the topic of making prostheses. 3D scanners and printers help to quickly produce fairly complex prostheses tailored to the size and needs of the patient. Moreover, if we are talking about a lost limb, then for hands, for example, there are already a sufficient number of ready-made models that only need to be adjusted in size - thus, the patient receives a complex and comfortable prosthesis almost at the price of plastic. There are even volunteer organizations that are engaged in the manufacture of free 3D printed prostheses of various levels of complexity.
Do not think that people help only their own kind - 3D printing is also actively used to create artificial limbs for animals. Of course, our favorite character is a turtle with titanium jaws, but we were just as worried about a husky named Derby, who got prosthetic forepaws printed, and Cassidy, a kitten with a 3D printed wheelchair. By the way, Cassidy is doing well - judging by the latest video, the kitten has grown up, cheerfully slides her back on the tiles and even plays with other cats. And on our list of good stories, there is a whole collection of birds: a toucan, a pelican and a macaw, which had prosthetic beaks printed, as well as a duck with printed prosthetic legs.
Works of art and zootropes
Without a doubt, the most prominent example of the use of 3D printing in the art world is the creation of a portrait called "The Next Rembrandt". The algorithm that controlled the operation of the 3D printer printed with special ink in 13 layers of paint - in this way it was possible to convey the relief of a real portrait in oil.
Of course, 3D printers can do more than just paint pictures. Designers use them with might and main in their projects, including when creating clothes - there is a “live” cape that looks like a porcupine skin. She is covered in 3D printed needles and changes shape in response to the gaze of a person of the opposite sex.
Or you can make the 3D printer itself the main element of an art project. So, for example, did Dutch designers who recorded sound on clay. To the table of a clay 3D printer, the designers attached a speaker that rhythmically emits low-frequency sounds. It turned out a kind of system for translating speaker vibrations into the texture of the printed product.
If you want something monumental, then 3D printing can help here too. The Swiss adapted an impromptu 3D printer to create a real sculpture from rubble and rope. The extruder lays the rope, and a layer of crushed stone is poured on top - a real layer-by-layer synthesis.
It is worth mentioning the little-known art of creating zootropes - moving sculptures. Working with a single 3D model in a 3D editor should be much easier than making dozens of figures by hand. Or a few hundred, as in the All Things Fall zootrope, which was inspired by Rubens' painting The Massacre of the Innocents and consists of more than 350 figures.
Jet engine and gear hydraulic machine
Of course, the ability to quickly prototype a complex part has delighted engineers and designers working with machines of all levels. The prospects for the manufacture of metal parts look especially interesting, because when metal powder is sintered by a laser, there is practically no waste, and the nodes are often strong enough for practical use.
NASA, for example, began testing 3D printed rocket engine parts three years ago, gradually increasing the number of printed parts in the experimental engine. In December 2015, the agency successfully tested a rocket engine with about 75 percent of its parts made using 3D printing. ESA is also trying to keep up - last summer, Europeans tested a jet engine with 3D printed platinum parts.
The cost-effectiveness of 3D printing in the production of metal parts has convinced some companies to use additive technologies not only in prototypes but also in series production. Airbus, for example, recently received two production turbojet bypass engines that have printed fuel injectors. The military does not lag behind civilian aircraft manufacturers - we even had detailed material on this topic. In short, the military is going to print not only spare parts for bombers, but also drones in the field.
How about ready-to-use hydraulics? Specialists from the Laboratory of Information Technology and Artificial Intelligence at the Massachusetts Institute of Technology have already mastered the method of producing ready-made hydraulic units that do not need to be pumped or refueled - they work directly from the printer. Multiple nozzles allow you to simultaneously print rigid and elastic parts of the body, as well as immediately pour liquid. The result was a gear hydraulic machine and a completely working hexapod, on which an electric motor was attached and it started to move.
And more recently, 3D printers have learned how to print phased antenna arrays, so cheap radars for military and civilian equipment are also just around the corner. I would like to believe that this will accelerate the development of active security systems in cars and the radar will no longer be installed only in front for reasons of economy.
Clothing and motorcycle
3D printing doesn't have to be rigorous or scientific medical, additive technologies also have quite domestic applications. A house, clothes, and a motorcycle have already been printed on a 3D printer. Why is there this motorcycle, in 2017 we were promised a serial 3D printed electric car! However, if the production model does not please the eye and the soul asks for an exclusive, then you can always print a supercar.
If you are not a fan of the concept of personal transport at all and want to print something smaller, then a gummies sorter, a tea set made of tea or the world's smallest circular saw will always come in handy on the farm.
What about meteorites and 3D printing? Yota suggests printing a cover for it when ordering a modem - and this is where the meteorite, which we talked about at the beginning of the material, comes in handy. On a separate site, you can independently break off pieces from a virtual meteorite and choose an inscription on the case. Further, according to your 3D model, a case will already be printed, into which particles of the real Seimchan iron-stone meteorite will be added at the production stage. Such is the symbiosis of the Internet, 3D printing and ancient space rock.
If you're still not impressed with the possibilities of 3D printing, then don't forget that, after all, you can always print a 3D printer on a 3D printer.
Nikolay Vorontsov
✈️ The best 3D files for 3D printing planes and aircraft ・Cults
✈️ The best 3D files for 3D printing planes and aircraft
-print. You can print beautiful airplane models to decorate your home or even do some modeling. As a result of 3D printing and connecting various parts, your aircraft can even fly for real. This is a great way to show your child how an airplane works and talk about the different models: CESSNA, Airbus, Boeing, etc.
RC plane - Eclipson model A free version by Eclipson
Free
F5 Tiger 1/64 easy to print scale model
Free
Free RC Airplane
Free
Pilot Baby - 3D printed reproduction of a vintage RC sport model.
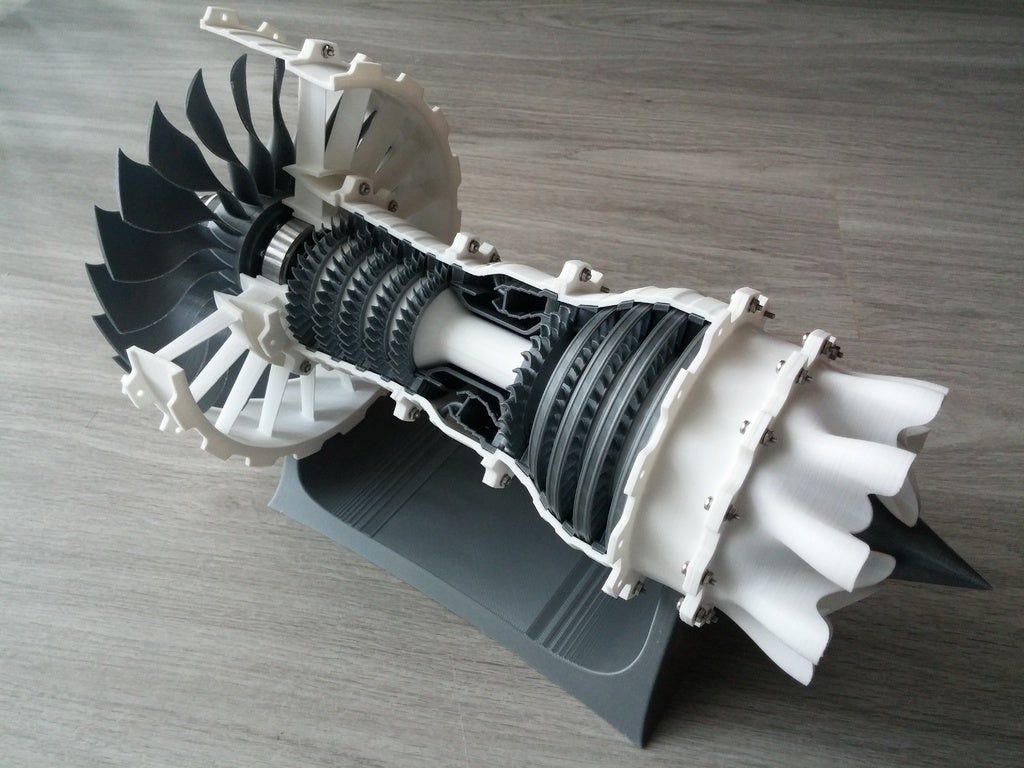
Free
Build your own aircraft engine
Free
RAF WW II Spitfire
Free
Easy to print T-38 Talon aircraft scale model (esc: 1/64)
Free
Plane
Free
RC airplane Wing - Eclipson Model Y
Free
F117 Nighthawk
Free
MD80 AIRCRAFT SCALE MODEL
Free
RC plane fuselage - Eclipson model Z
Free
Airbus A220-100 - 1:144 - Free
Free
Zlin Z-242 frame model (esc: 1/64) (No 3D print, CNC routing)
Free
Cessna 172 Skyhawk 1:72
2 €
Ultimate Biplane 10-300S
Free
Turboprop Engine
Free
Boeing 777-200 1:750
Free
Easy to print Cessna Citation SII 1/64 aircraft scale model
Free
Porco Rosso Savoia S.
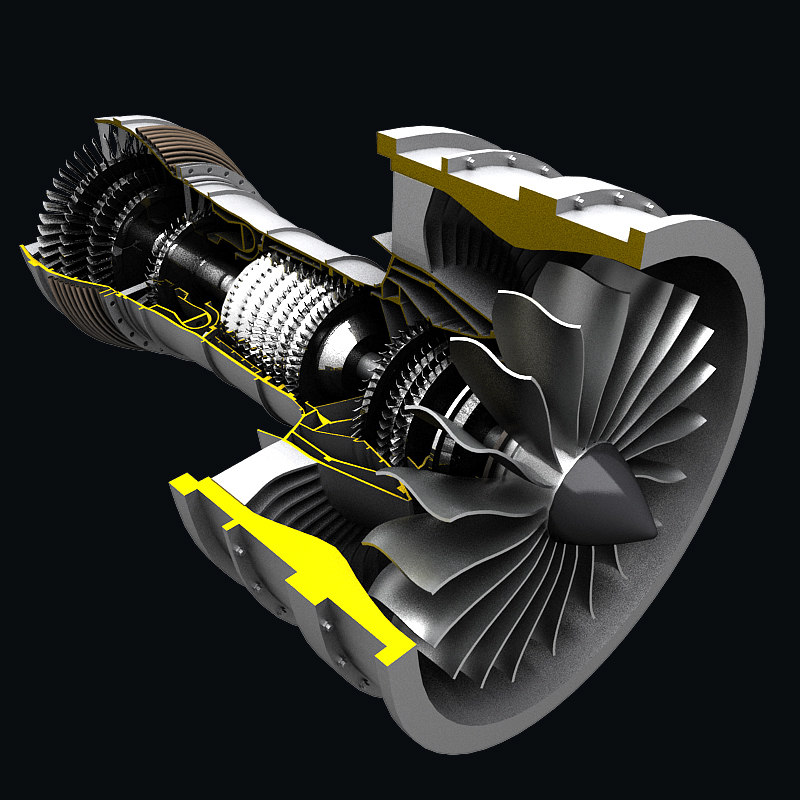
Free
Aero Commander 500S
Free
Model plane
Free
SOFIA, the Stratospheric Observatory for Infrared Astronomy
Free
Das Liddle Stik RC Airplane
Free
Antonov An-225
Free
Easy to print Aero L-39 Albatros aircraft scale model
Free
Aircraft
Free
Lancer B1 Bomber
Free
WW II RAF Spitfire Sliced
Free
PIPE ECHAPEMENT SPITFIRE
Free
A02 C-3D aircraft
Free
P-51D Mustang - Sally AURI
Free
First Take Off of a fully printed (FDM) sailplane.

Free
Ercoupe Golden Age Aircraft
Free
RAF Mosquito WW II
Free
Le Rhone spinning radial dummy engine for RC planes
Free
Little Jet Plane
Free
RAF Lightning
Free
Floonda - free 3d printed Freestyle Glider 1335mm Wingspan (Vasemode)
Free
Mobile device Barron Red
2.41 €
Transport Aircraft Toy Puzzle
Free
Speedy "Red Mini Wing" RC Plane
Free
"Red Swan" the biggest fully printed Flying Wing
Free
Antonov An-32
Free
Antonov An-124
Free
Touristic plane
Free
Skewer Fighter Jet (F-86 Saber)
Free
EL-39 - RC half-scale jet for 120 mm EDF
17. 25 €
Hawker Tempest V WW2 Fighter
Airbus A220-100 - 1:144 - Free
Airbus A220-100 - 1:144 - Free
Aichi D3A2
Here is our selection of of the best aircraft 3D files, all of these great cars from the Cults and 3D file libraries are perfectly 3D printable for .
This collection includes free 3D files of all types of aircraft. There are many aircraft models of the most prestigious brands, such as Boeing , Airbus , Cessna or Antonov .
Professional 3D printing of has gained a lot of development in the world of aeronautics mainly for very specific applications. For example, this technology makes it possible to create very strong and much lighter parts compared to traditional manufacturing processes.