Chinese house 3d printing
Chinese Company Constructs the World's Tallest 3D Printed Building
Chinese Company Constructs the World's Tallest 3D Printed Building
Image via australiandesignreview.com- Written by Rory Stott
Once again, Chinese company WinSun Decoration Design Engineering Co has expanded the capabilities of 3D printing. After constructing ten houses in under twenty-four hours last year, now they are back with both the world's tallest 3D printed building - a five-story apartment block - and a 1,100 square meter mansion with internal and external decoration to boot.
On display in Suzhou Industrial Park in Jiangsu province, the two buildings represent new frontiers for 3D printed construction, finally demonstrating its potential for creating more traditional building typologies and therefore its suitability for use by mainstream developers.
+ 2
Image via www.The buildings were created using the same 6.6 by 10 meter tall printer which builds up layers of an "ink" made from a mixture of glass fibre, steel, cement, hardening agents and recycled construction waste. With this technology, WinSun is able to print out large sections of a building, which are then assembled together much like prefabricated concrete designs to create the final building.
Image via australiandesignreview.comIn a press conference attended by online 3D printing newspaper 3Ders.org, the Chief engineer of China Construction No.8 Engineering Bureau Ma Rongquan explained: "These two houses are in full compliance with the relevant national standards. It is safe, reliable, and features a good integration of architecture and decoration. But as there is no specific national standard for 3D printing architecture, we need to revise and improve such a standard for the future."
A close-up of the construction system. Image via www.3ders.orgThe company also announced a raft of signed contracts and future plans that will expand 3D printed buildings beyond the realm of construction experiments: the $160,000 mansion is the prototype for a set of ten that has been ordered by Taiwanese real estate company Tomson Group; a third house on display at Suzhou Industrial Park was just one of 20,000 ordered by the Egyptian Government; they also announced the creation of Winsun Global, a collaboration with an American firm that will seek to expand into countries around the world with the aim of providing cheap and efficient homes for low-income families, particularly in Africa and the Middle East.
Story via 3Ders.org and Australian Design Review
Image gallery
See allShow less
About this author
Rory Stott
Author
•••
Cite: Rory Stott. "Chinese Company Constructs the World's Tallest 3D Printed Building" 26 Jan 2015. ArchDaily. Accessed . <https://www.archdaily.com/591331/chinese-company-creates-the-world-s-tallest-3d-printed-building> ISSN 0719-8884
Top #TagsSave
世界上最受欢迎的建筑网站现已推出你的母语版本!
想浏览ArchDaily中国吗?
是否Did you know?
You'll now receive updates based on what you follow! Personalize your stream and start following your favorite authors, offices and users.
Go to my stream
Top #Tags
Chinese Construction Company 3D Prints an Entire Two-Story House On-Site in 45 Days - 3DPrint.
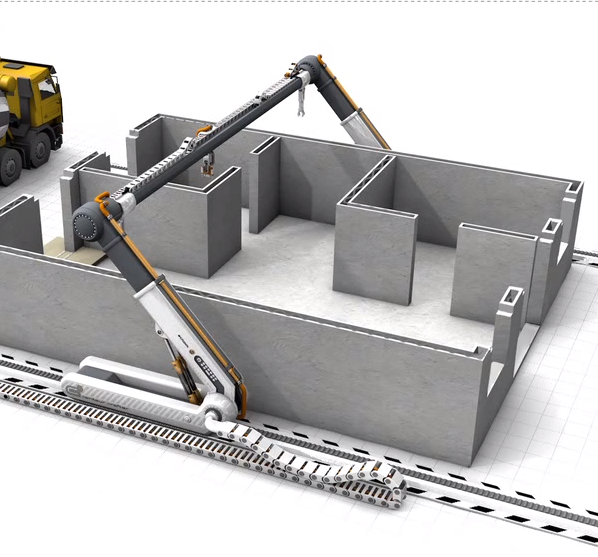
How long does it take to build a house? Obviously it depends on the size of the house and other factors, but somewhere around six or seven months is a good estimate. Chinese construction company HuaShang Tengda thinks that’s pretty funny, and have essentially laughed in the face of traditional construction by 3D printing a 400-square-meter, two-story house in a mere month and a half.
Beijing-based HuaShang Tengda is a major competitor of fellow Chinese construction company WinSun, which we’ve followed in the past since they surprised us with their 3D printed homes, including a six-story apartment building and a mansion. Not long after that, WinSun’s reputation was tarnished by quite of bit of controversy when Dr. Berokh Khoshnevis, creator of the revolutionary Contour Crafting technique of 3D printing buildings, stated that the Shanghai company had blatantly stolen his patented technology and were passing it off as their own. Moreover, Dr. Khoshnevis said, WinSun’s claim that they were 3D printing entire homes was untrue; in fact, they were 3D printing small sections of walls and then cobbling them together on-site using other construction methods.
HuaShang Tengda appears to be something different altogether. Their two-story villa was printed entirely on-site in a unique process that looks quite different from other 3D printed construction techniques we’ve seen. The team first erects the frame of the house, complete with rebar support and plumbing pipes, and then prints over it with their gigantic 3D printer, which only recently completed testing after several years of development. The printer, as seen in the video below, has a sort of forked extruder that simultaneously lays concrete on both sides of the structural material, swallowing it up and encasing it securely within the walls.
The printing material itself is ordinary Class C30 concrete, an extremely tough, durable yet inexpensive material, and HuaShang Tengda states that any cement material can be used with the process, so that other construction firms can take advantage of what is locally available. Twenty tons of the concrete were used to print the 250cm-thick walls of the villa, and seismic testing showed that the structure should be capable of withstanding an earthquake as strong as 8 on the Richter scale – that’s a strength that has flattened cities.
The technology, according to HuaShang Tengda, was developed entirely in-house and is controlled by custom-designed software that consists of four “systems”: an electronic ingredient formulating system, a concrete mixing system, a transmission system and a 3D printing system. The versatile printer, the company says, can be used to print buildings of any size and shape, including high-rise apartment buildings as well as structures with unconventional shapes that wouldn’t be feasible with other construction methods.
“(This technology) will have immeasurable social benefits,” HuaShang Tengda states. “Particularly the use of the new rural construction can now improve farmers’ living conditions. Because of its speed, low cost, simple and environmentally friendly raw materials, (it can) generally improve the quality of people’s lives. If to be used in developing countries, international competitive bidding in a great competitive advantage, the use of mechanical devices to reduce administrative costs and operating costs.
”
I hesitate to use too many superlatives when talking about a new process, machine or material; we’ve heard a lot of 3D printing-related inventions described as being the next thing to turn a particular industry on its head, and that’s not always the case. WinSun’s claims turned out to be too good to be true, but HuaShang’s technology really does look like the real thing. Beyond the speed and low cost of the process, the fact that it can allegedly withstand all but the very strongest of earthquakes could save millions of lives – an idea that should be very appealing indeed to earthquake-prone China and many other regions. Watch the process for yourself below, and discuss further over in the Two-Story 3D Printed Villa forum at 3DPB.com.
[Images: HuaShang Tengda]
Stay up-to-date on all the latest news from the 3D printing industry and receive information and offers from third party vendors.
Tagged with: 3D concrete printing • 3d printed architecture • 3d printed building • 3d printed building materials • 3d printed buildings • 3d printed cement • 3d printed concrete • 3d printed construction • 3d printed house • china • concrete 3d printing • HuaShang Tengda • winsun
Please enable JavaScript to view the comments powered by Disqus.
3DNews Technologies and IT market. Interesting news from the high-tech world The most interesting in the reviews 01/23/2015 [10:45], Dmitry Prikhodko 3D printing technology is gradually becoming a not-so-outlandish way to produce both small components and large structures. A clear evolution of the capabilities of modern 3D printing can be seen in the construction activities of the Chinese company Winsun, which was the first to use this method to create small residential buildings in the vicinity of Shanghai, and now built a five-story residential building and a luxury villa of 1100 m2 using a 3D printer. 2 . 3DERS.ORG 3DPRINTERPLANS.info www.gizmag.com Metro.co were printed on a 3D printer Winsun, as noted above, has mastered the method of high-speed “printing” of simple structures as a trial step. Now Winsun, which decided to complicate the task, was able to demonstrate the promise of the considered 3D technology using the example of two new and more complex buildings. To realize the vision, the Winsun engineering team designed the printer to be 6.6 meters high, 10 meters wide and 40 meters long. The device produces separate solid blocks of future houses, which are assembled on site, strengthened with reinforcement and supplemented with insulating materials to meet all the necessary standards of modern construction. True, the manufacturer keeps a secret what the maximum dimensions of an element produced on their 3D printer can be, but given the demonstrated success, there is no reason to doubt the rationality of this method. The walls of a huge villa and a five-story house are made almost hollow, with zigzag elements inside to increase the reliability of the structure. The main advantage of the described construction method is the economic component, which makes it possible to reduce the consumption of building materials by 30–60% due to the use of recycled waste. The cost price of the presented villa for 1100 m 2 meters amounted to $161,000. www.wmshello.com The time required to perform the main work is also significantly reduced, which with the new technology can be reduced by 70%. Accordingly, 1.5-2 times less labor force will be required. At the same time, housing, despite the wording “waste” when referring to the composition of the printed blocks, is absolutely harmless to living and is considered environmentally friendly. The developers plan to make this method fundamental in the construction of multi-storey buildings and even skyscrapers. Sources: If you notice an error, select it with the mouse and press CTRL+ENTER. Related materials Permanent URL: https://3dnews.ru/908385 Headings: News Hardware, hard drives, storage systems, interfaces, NAS, high-tech interesting things, 3D technologies, Tags: 3d printing, 3d technology, 3d printer, construction, house, construction, creation, housing, Chinese manufacturers, China ← В past To the future → |
Read article - Construction 3D printing. 8 reasons why she will be an achievement
3D printing has long outgrown its initial capabilities of rapid prototyping and has evolved into a full-fledged manufacturing process known in the industry as additive manufacturing. It is being used to manufacture an ever-wider range of products, from dental implants to jet engine parts. Indeed, it was only a matter of time before she made it to the construction industry.
Simply put, houses built with a 3D construction printer are built by layering the material. The paste-like concrete mix is extruded through the nozzle, creating walls from scratch one layer at a time.
At first glance, this does not seem complicated, but in fact it is not. While the prospects for such a construction process are enormous, it is still in the very early stages of development, but has already shown promising results and has quickly attracted media attention.
The question is, is the hype around 3D construction printing really deserved? In this article, we will delve into this topic and show why we believe 3D printed homes could be the next big thing.
Construction speed
3D printing a house is significantly faster compared to traditional building methods. While the actual timeline is highly dependent on the size of the project, in most cases, construction takes only a few days.
Take, for example, the first fully 3D printed house in America, built by construction company ICON for the nonprofit New Story in 2018. The 33-square-foot house in Texas took about 47 hours of print time to create, spanning several days.
Just two years later, another American company built a huge 177 square meter home in just 8 days, taking just 48 hours of total printing time. However, remember that 3D printers can only create exterior and interior walls.
However, according to SQ4D, the company responsible for the project, this is 40% less compared to conventional building technologies. While this may seem insignificant at first glance, 3D construction printing is still an evolving technology that still has a lot to improve. So, most likely, the construction time will be reduced even more.
Fewer builders
At construction sites, 3D printing requires fewer workers than traditional sites as the printing equipment does most of the work.
Traditional construction requires many stages, including a whole team of five to six people who unload, transport and mix materials before laying the structures. Once set up, the concrete 3D printer only needs a few people to monitor and control the process.
For example, for the aforementioned house of 177 sq. meters from SQ4D will require only 3 people on site, which, according to the company, will replace a team of more than 20 unskilled workers. This shows just how well this whole process is automated, and why 3D construction printers are such a promising alternative.
In addition, fewer workers on site also result in fewer work-related injuries and deaths. According to OSHA statistics, construction alone is the cause of death for one in five workers in the US. If done responsibly, 3D printers can help reduce these numbers significantly.
Lower construction cost
It is believed that 3D oven houses are cheaper to build, but this is somewhat debatable as mass building 3D printers are expensive equipment and still have many limitations. But let's stick to facts and figures.
We've already established that 3D printing a home is faster than traditional building, and as they say, time is money. Less time spent on site means both equipment and workers are more quickly available for other projects, theoretically doubling construction volume compared to today.
Add this to the greatly reduced number of workers required. In addition, the raw materials used by some 3D printers can be partially assembled on site, reducing the costs associated with finding, storing, and transporting them to the site.
Now let's get down to the numbers: Apis Cor's 40 sq. m in Russia, according to rumors, cost about $ 10,000, including all windows, roofing, wiring and interior decoration. This is shockingly small. ICON is currently working on 60-square-meter homes that are planned to cost as little as $4,000.
Yes, 3D printing construction equipment is still very expensive, like any other cutting-edge technology, but there is a lot of room for improvement, and as the technology advances, the costs associated with equipment and operation will undoubtedly decrease.
Unique building possibilities
3D printing opens up unique building opportunities that would be either impossible or too expensive to implement with conventional building technologies.
Some say that in order to get the most out of any 3D printing process, the high degree of design freedom afforded by these technologies must be taken into account. This also applies to construction and architecture, where innovation and creativity are especially encouraged.
3D printing allows you to create complex shapes and forms without any extra effort. For example, a concrete 3D printer can create intricately curved walls just as easily as straight ones. Unconventional architecture can improve the appearance of buildings and even optimize interior space.
Take, for example, the "Office of the Future" in Dubai, 3D printed by the Chinese company Winsun, which houses the Dubai Futures Foundation. The curved appearance would require an excessive amount of work to recreate using traditional building techniques.
Engineers can also get creative as the print media can be finely tuned to achieve the best properties. From a finished batch, concrete is already a first-class building material, resistant to most environmental influences such as fire and moisture, as well as an excellent thermal insulator for cold and warm weather.
High material efficiency
The 3D printing process is more efficient in terms of energy and material use compared to traditional construction.
3D printers produce less waste because they only use the right amount of material to create designs: there is no waste from cutting or cutting materials. In addition, since concrete-based raw materials are not shaped, any leftovers can and should be used in the next building.
In addition, raw materials can be made from recycled materials. Back in 2014, the Chinese company Winsun was able to build at least 10 houses in one day using only recycled concrete material, while the Italian 3D printing company WASP made a house from natural mud mixed with waste from local rice production, which included crushed straw and rice husks.
3D printers also consume less energy compared to the entire production chain of conventional construction. Consider all the energy needed to transport raw materials and move entire crews of workers daily to the construction site. By reducing labor intensity and sourcing materials in situ, 3D printing can be more sustainable in the long run.
Situational applicability
Overall, 3D printers can play a central role in various scenarios around the world. All the key points we've covered so far - reducing time, cost, manpower, expanding unique capabilities and efficiency - show how this technology can be very useful in certain situations.
Developing countries constantly face housing problems. The ability to provide enough quality homes at affordable prices is a key factor in sustainable economic development. The relatively fast process of building 3D printers could potentially solve the problems of the homeless in the short term.
This is exactly what New Story and ICON are trying to achieve in Mexico, in Tabasco. The idea is to create the very first community of 3D printed houses for local families who currently live in extreme poverty. A total of 50 fully 3D printed houses of 50 square meters will be built.
3D printed houses can also be useful in situations of humanitarian crisis, especially after natural disasters when houses are tragically destroyed by earthquakes, fires or tsunamis. Communities affected by such events end up with labor and material shortages, not to mention logistical problems. Restoration with 3D printing could be an effective and cheap solution to at least start rebuilding these communities.
Lastly, 3D printing could also make space exploration like Mars possible. The idea is to send automated 3D printing equipment to the red planet, and since the raw materials could be collected locally, the printers could start building living quarters long before the first humans arrived. No wonder NASA is so interested in this technology.
Industry shift and investment
Construction 3D printing not only attracts the attention of industry leaders and investors, it also attracts their money!
The construction 3D printing market has been growing steadily in recent years. Concrete 3D printer maker COBOD reported earnings in just its second year of operation in 2019, which is a huge achievement for any company and more considering how raw this particular market is still.
After 2020, the coronavirus crisis has affected most industries around the world, and construction 3D printing is no exception. However, it seems to be a suitable solution for such cases, given the reduction in the number of workers on site. For this and other reasons, the global construction 3D printing market is expected to grow from $350M in 2022 to $11B in 2027.
You don't have to take our word for it. Just remember that industry leaders are at the top because they understand the market, while big investors only invest their money in real and really promising technologies. 3D printed houses are the next big thing in technology.
Global distribution
3D printed houses are already a reality and they are rapidly spreading around the world.
While 3D printed houses are often seen in architecture competitions or as concept designs, there are plenty of real-life residential structures that are already in use. Take, for example, the Lewis Grand Hotel in the Philippines with 140 sq. meters, completely made using 3D printing, including bedrooms and living rooms.
Governments are also involved in this. In 2019, Russian company Apis Cor built the largest 3D printed building to date. Two-story building with an area of 640 sq. m is currently home to Dubai Municipality, being the second government building to be 3D printed after the aforementioned Office of the Future.
In Europe, the 3D printed Yhnova House became one of the first residential buildings in the world in 2018 when the Ramdani family moved in. The structure was designed by the University of Nantes using its own proprietary equipment, and the 92 sqm structure was 3D printed. meters took no more than 54 hours.
The next time you hear about 3D printed homes, remember that although it is still an evolving technology, it has shown great results and is already being used around the world.