Audi 3d printing
Innovations Right Out of the 3D Printer
- Home
- We are progress. With you.
- Working World
-
Innovations Right Out of the 3D Printer
Designing tools as-needed and printing them on demand — it sounds like “Mission Imprintable” or a fantasy, but it’s part of daily life for the 3D printing experts at Audi. Audi author Sina Feirer learned how the team works and how quickly the innovations from the 3D printer can be put into use during her print-it-yourself experience.
04/04/2019 Reading Time: 3 min
In the heart of the Audi R8 factory in the Böllinger Höfe, there’s a futuristic hotspot: the 3D printing center in the startup/analysis center. This is where I meet Waldemar Hirsch and Cem Gülaylar, the Audi 3D printing experts. My goal for the day: with their help, I want to design and print an auxiliary tool that I will put into the hands of a production employee only hours later.
The innovation factory: the 3D printer
For five years, they’ve been boldly printing what no one has printed before: each day, at least one auxiliary tool leaves the 3D printing center. The printed positioning guides, safety devices, and casting molds made by Waldemar’s team help their colleagues in the production department — quickly, inexpensively, and on-demand. The team has been so successful in their work that they will soon be founding their own department on-site, where they will really be able to get things going. The goal: a worldwide 3D printing network for the Volkswagen concern that will supply employees in all locations with printed innovations.
Waldemar Hirsch (left) and Cem Gülaylar (right) in the 3D printing center in the Böllinger Höfe.
An overview of 3D Printing
Among experts, 3D printing is known as "additive manufacturing.” Layer for layer, the 3D printer lays down the material to create new components. In contrast to traditional production methods, the material is applied bit by bit, rather than being removed as in milling, drilling, turning, or eroding. Materials such as plastic or metal are used.
A printed solution for every problem
It’s time to start the print-it-yourself attempt. We meet Marco, an employee from the Audi R8 assembly line. He explains his problem to us: during the subassembly of the brake calipers, a sensor needs to be screwed into place. An insertion aid that is specially designed for the sensor would make the subassembly considerably quicker and easier. No sooner said than printed! Almost, anyway. Now I’m faced with the most challenging part of the process: designing the piece to be printed in 3D.
The sensor’s location is not easy to reach.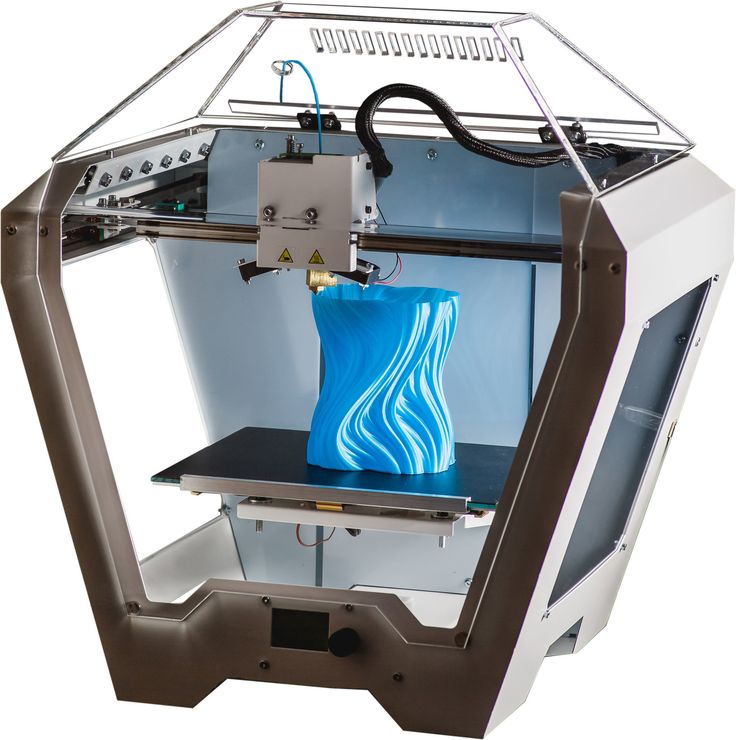
Every piece is unique
Everything that Waldemar and Cem make is one of a kind. They custom-make each and every auxiliary tool to meet a specific need, without templates. So we first head to the Tech.Lab in the team’s creative workshop to measure the part. Thanks to their many years of experience, Waldemar and Cem know exactly what matters in the design process: precision, simplicity, and user-friendliness. On the basis of the measurements, we then draw a 3D model of the auxiliary tool in a CAD (computer-aided design) program. With its help, we go from a sketch to virtual reality in just over 20 minutes. Our one-of-a-kind plastic part begins its journey.
Printing the wonderful world of Audi
The 3D printer is still missing the most important piece of the puzzle: the right filament, or “plastic thread.” We decide on PLA (polylactide) plastic. It is sturdy, inexpensive, and easy to print with, which makes it the perfect material for our assembly aid. We also choose a bright orange plastic thread, which will make it easier to find the small auxiliary tool in the assembly hall whenever it is needed. We insert the 3D printer filament and bring it up to working temperature. With delicate movements, the 220°C nozzle flies back and forth across the printing plate, building up the layers.
The 3D printing process in time-lapse. A 3D printer can print almost any shape, which means it can be used flexibly. It is truly the technology of the future!
Out of the printer and onto the assembly line
The 3D printer beeps. The auxiliary tool is finished—after only 90 minutes! It’s still a bit warm, and it feels smooth and incredibly light. When you look closer, you can still just barely see the individual printed layers. A masterpiece! And it’s even ready to use straight out of the printer, since it doesn’t need to cure. We bring the 3D printed auxiliary tool to Marco, who immediately tests it out. The installation goes perfectly; he is thrilled with his new tool.
From Neckarsulm to the world of 3D printing
It seems like anything is possible — uh, printable — in Neckarsulm. By locally producing the auxiliary tools, Audi saves itself long waiting times and long-haul shipping. Aside from that, the use of these printed innovations give them more flexibility as well as the ability to act quickly and with agility — and that’s what matters in day-to-day business. 3D printing has advantages for the company, but it is especially valuable for the employees. That’s because, when all is said and done, the 3D printed tools make their work easier. My personal conclusion: Vorsprung durch 3D printing!
Sina Feirer
I actually always wanted to be teacher for Sports and Latin. But then I completely fell in love with my rhetoric course and ended up in Tübingen. An exciting journey through the world of communication began. As a trainee at Audi, I dove into my next adventure!
Innovation Working World Story Working at Audi Smart Factory Audi Employees
Audi ramps up use of 3D printed hot form tooling at Ingolstadt factory
0Shares
German automobile manufacturer Audi has begun to use fully-additive manufactured hot form tooling at its Metal 3D Printing Centre in Ingolstadt.
By expanding its use of EOS 3D printing, Audi is now able to produce twelve different segments of four hot forming tools at the facility, which are later used to assemble car models such as the A4 saloon. The company’s move reflects its increased confidence in the reliability and quality of additive manufactured parts, and in future, it plans to utilize the technology to build its electric vehicles as well.
“The latest examples show that 3D printing has become an established part of operating materials production at Audi,” said Markus Glasser, Senior Vice President EMEA at EOS. “Audi is a partner we can work with to continue to drive the use of AM in automotive production – a key industry for us.”
Audi now 3D prints twelve different segments of hot forming tools at its Ingolstadt facility. Photo via EOS.“We’re especially proud that the tool segments made using AM are created exclusively using an industrial 3D printer from EOS.”
Audi’s 3D printing integration
Like many of its automotive rivals, Audi has utilized 3D printing within its production workflow for much longer than it has publically discussed. In 2015 it began to reveal the extent of its capabilities, using the technology to reproduce its 1936 Auto Union Type C Car. In the years since, the company has widened its application of the technology, and it acquired an SLM Solutions system for prototyping and creating components on-demand in 2018.
Audi followed this up by installing a Stratasys J750 system at its design center in Ingolstadt, using it to prototype tail light covers and accelerate design verification. On the tooling front, Audi has also found working closely with EOS to be particularly beneficial, and the companies’ engineers have been co-developing automotive 3D printed tooling applications for the last four years.
In that time, Audi has expanded production at its Volkswagen Böllinger Höfe facility, opening a separate 3D printing department with the aim of expediting its tool production. The new area includes four Ultimaker and MakerBot systems, which are specifically tasked with producing auxiliary tools for guiding machinery, as well as casting molds and safety devices.
With its latest application of 3D printing, Audi has now started to fully-print hot form tooling for use within its vehicle assembly process. While the carmaker has utilized EOS’ technology at its Ingolstadt facility since at least 2017, the move still represents a significant milestone, and a glimpse into its growing 3D printing capabilities.
Accelerating AM at Ingolstadt
At its Ingolstadt plant, Audi has essentially ditched conventional manufacturing in favour of 3D printing, when it comes to producing hot forming segments and high-pressure die casting tool inserts. Using EOS’ M400 3D printer, engineers at the facility’s design department are now able to create entire tools measuring up to 5m x 3m in area, or segments weighing up to a hefty 120kg.
Given the size and complexity of the tooling produced, the process can take as long as 20 days, meaning that the reliability of EOS’ machine has been crucial to the technology’s integration. What’s more, using 3D printing, Audi’s crew has been able to create tooling with highly-complex cooling channels, reducing their lead times in the process.
At present, the new tooling is being utilized within Audi’s press shop, to help make body panels for cars such as its A4 saloon. Several hundred thousand parts have already been produced using the tools, and installed on selected models, and the company has now made it clear that it intends to take a similar approach to building its electric vehicles in future.
“We are now reaping the fruits of years of development within Audi’s production organization,” said Matthias Herker, Technical Project Manager at Audi’s Metal 3D Printing Centre. “Whenever conventional manufacturing methods reach their limit, we use additive manufacturing, which lets us meet quality standards and comply with production times.”
Advances in automotive AM
Automotive firms such as Ford have utilized additive manufacturing for prototyping since the commercial launch of the very first 3D printers, and it acquired one of the first 3D Systems SLA 3D printers produced in the 1980s. In subsequent years, advances in 3D printing has increasingly enabled carmakers to create jigs, fixtures, tooling, and more recently, low volumes of specialized parts on-demand.
In January 2021, for instance, product design firm CALLUM used MakerBot’s METHOD X 3D printer to create components for a limited edition Aston Martin. Adopting the system enabled the design company to manufacture prototypes, tooling, and spare parts for R-Reforged’s one-off reimagining in-house with reduced lead times.
On a similar note, Porsche worked with TRUMPF and MAHLE in July 2020, to 3D print optimized pistons for the engine of its 911 supercar. Using an AI-led additive manufacturing process, the automotive firm was able to reduce the pistons’ weight by 10%, and add 30 BHP to the engine’s horsepower.
Elsewhere, Groupe Renault has sought to integrate 3D printing into its upcoming sustainable automotive ‘Re-Factory.’ Although the facility will primarily focus on reducing waste by recycling and retrofitting vehicles, it will also house a a dedicated spare parts additive manufacturing service.
To stay up to date with the latest 3D printing news, don’t forget to subscribe to the 3D Printing Industry newsletter or follow us on Twitter or liking our page on Facebook.
Are you looking for a job in the additive manufacturing industry? Visit 3D Printing Jobs for a selection of roles in the industry.
Featured image shows Audi’s TechDay Smart Factory. Photo via EOS.
Tags Aston Martin Audi CALLUM EOS Ford Groupe Renault MAHLE Makerbot Markus Glasser Matthias Herker Porsche R-Reforged SLM Solutions Trumpf Ultimaker Volkswagen
Paul Hanaphy
Paul is a history and journalism graduate with a passion for finding the latest scoop in technology news.
How 3D printing is used in everyday life on the Audi
3D printing allows you to create a large number of auxiliary tools. It is for this reason that the Audi team regularly uses 3D printing to make their work easier. Today, Audi employees have a large number of additional tools that have been created using 3D printing.
The photo shows an example - a new part is hidden in the SLS powder layer. The advantages of this method are particularly fast and economical production. nine0003
Who knows, maybe in a few years we'll just print our clothes, our jewelry, or even our food? In any case, printing has become indispensable in Audi production over the past years.
3D printers were first used at Audi in 1999 for modelling, at that time still in their infancy. Since then, 3D printing has developed rapidly, allowing the technology to be used in development, manufacturing, assembly or design. Four years ago, a team led by Thomas Kaiser and Waldemar Hirsch at the Audi R8 think-tank started a small project to get hands-on with a 3D printer. nine0003
3D printing has been integrated into the daily routine Audi
Audi employees were surprised at how easily printed work tools can optimize production processes. They are steadily developing 3D printing technology together with colleagues from various departments. The 3D printer began to print positioning aids, fixtures, pen holders, adapters, molds, and more.
Fundamentals of 3D printing
3D printing is referred to in the professional world as additive manufacturing. Layer by layer, the 3D printer places material on top of each other, creating a new element. Unlike conventional manufacturing methods, the material is gradually applied and not removed. During the use of conventional methods for manufacturing a part, for example, during milling, drilling, turning or blurring, part of the material is removed. nine0003
Since 2013, Audi employees have printed several hundred ideas and projects, many of which have become indispensable tools for their colleagues. For 3D printers, it is important to consider the individual needs of all departments: “In addition to ergonomic assistants for production, we also provide day-to-day assistance to office workers. It could be pen holders or an optimization for the robot vacuum cleaner that cleans our offices,” says Waldemar Hirsch. Meanwhile, a whole community has formed around the topic of 3D printing. nine0003
From an idea through computer design to a 3D printed ventilation grill, Tech.Lab staff guides you through the entire process of creating a new element.
Hirsch, Kaiser and Gülaylar created the so-called Tech.Lab as a workplace: a glazed office next to R8 products. Modern wooden furniture, boards, plants and colorful armchairs give the room a creative vibe. They often do mental reviews of their projects. Here they capture their thoughts on boards and colored stickers. The Tech.Lab door is open to all employees. Nearly every day, colleagues with very different tasks knock on the glass to pitch new ideas to three print experts. “One of our goals is to further optimize workflows in production, for example to make them even more ergonomic,” Kaiser explains. nine0003
Day-to-day fixtures already developed by the team
Cabin mounting adapter
Depending on whether the vehicle is right hand drive or left hand drive, employees must install cab elements inside the vehicle differently. So-called paddles were printed for 3D experts. These are colorful plastic adapters that employees place on the manipulator for installation in the cab. As a result, they can optimally mount the dashboard in the vehicle. nine0003
And, since the cabin installation works differently in right and left hand engines, the paddles are of different colors depending on the type of vehicle. The development team has also released a deployment box for adapters so that every paddle is always in the right place.
The colorful adapters used help the assembler to facilitate the specific position of the elements in the cab (right or left hand drive).
Assembly positioner
The so-called roll bar in the Audi R8 Spyder provides the necessary rigidity to the vehicle and is located behind the seats. During assembly, employees must position the rack at exactly the correct height in the vehicle so that they can then place the storage compartment between the seats and achieve optimal clearance dimensions. The 3D printing experts have developed a positioning tool to perfectly fit the cross bar. It places the rack exactly in the right position. nine0003
3D printing has been used by Department I/E-V36 Modellbau since 1999. Since then, the technology has expanded dramatically, from plastic-printed prototypes to mass-produced components made from a wide variety of materials.
Screwing, grouting, tightening, ratcheting: Audi R8 assemblers use various tools on the vehicle every day.
To avoid accidental scratching of the components, the 3D team came up with a protection element. They designed negative molds out of plastic, printed them, and then poured them with liquid silicone. nine0003
This is how individual cases for individual instruments were created. They optimally protect the vehicle from possible damage during assembly.
Ratchet guard
When installing the drive shafts in the wheel housing on the gearbox, Audi R8 staff use a screwdriver and an auxiliary device with a large ratchet. To prevent the ratchet from turning in the direction of screwing, the creative team printed a small helper. The result is a green plastic element that ensures that the so-called ratchet switch is pressed in one direction and cannot be accidentally slipped. nine0003
The small green auxiliary is a plastic guard that ensures that the ratchet switch is pressed in one direction, and thus the ratchet cannot be rotated in the screwing direction.
Welding aid
Everyone knows that if you keep your hand under tension often, at some point, symptoms of tension or overload will occur. To counteract this and actively promote ergonomics, the print specialists have developed a plastic element for working with welding equipment: a black fabric strap holds the welding gun securely. Thus, the worker does not need to hold it tightly, but he can relax his fingers. The printed plastic part provides comfort on the inside of the arm, connects the welder to the back of the arm and thus serves as a support that takes stress off the tendon during welding. The idea was developed by 3D printing specialists together with the body shop staff. nine0003
To protect welders from the unpleasant consequences of overloading the hand, 3D printing specialists have developed a special device.
Translation of the article - https://blog.audi.de/wie-3d-druck-im-arbeitsalltag-unterstuetzt/.
Audi historic car replica / 3d printing / 3Dmag.org
To show the world the possibilities of metal 3D printing, Audi Toolmaking decided to go in a very unusual way, namely to recreate the Auto Union Type C 19 racing car.36 years old in 1:2 scale. For several years, this car was considered the fastest racing car in the world.
Using selective laser sintering (SLS) all metal parts of the structure were obtained. By the way, this method is most common in metal 3D printing: a high-powered laser is used to melt samples into a thin powder material. So, with a replica of Auto Union, the metal powder consisted of grains ranging in size from 15 to 40 thousandths of a millimeter!
The Concept Laser M2 Cusing was used for printing, an industrial 3D printer that is capable of producing parts 240 mm long and 200 mm high. The powder material yields steel and aluminum parts that are denser and of better quality than conventional injection molded or hot stamped components.
Audi, in coalition with the Volkswagen Group, has long turned their attention to 3D technology, and in particular to metal printing. “We are promoting new manufacturing technologies at Audi Toolmaking and the Volkswagen Group. Together with research partners, we are constantly exploring the boundaries of new processes and one of our goals is to use metal 3D printers in mass production.” nine0003
Related entries:
-
hedin
3d printing → Manufacturing center from Ford 0 - Learn more