3D printer material comparison
Ultimate Materials Guide - Tips for 3D Printing with PETG
Overview
PETG is a Glycol Modified version of Polyethylene Terephthalate (PET), which is commonly used to manufacture water bottles. It is a semi-rigid material with good impact resistance, but it has a slightly softer surface which makes it prone to wear. The material also benefits from great thermal characteristics, allowing the plastic to cool efficiently with almost negligible warpage. There are several variations of this material in the market including PETG, PETE, and PETT. The tips in this article will apply to all of these PET-based filaments.
- Glossy and smooth surface finish
- Adheres well to the bed with negligible warping
- Mostly odorless while printing
- Poor bridging characteristics
- Can produce thin hairs on the surface from stringing
Hardware Requirements
Before 3D printing with PET / PETG make sure your 3D printer meets the hardware requirements listed below to ensure the best print quality.
Bed
Temperature: 75-90 °C
Heated Bed Recommended
Enclosure Not Required
Build Surface
Glue Stick
Painter’s tape
Extruder
Temperature: 230-250 °C
No special hot-end required
Cooling
Part Cooling Fan Required
Best Practices
These tips will help you reduce the chances of common 3D printing issues associated with PET / PETG such as stringing, oozing, and poor bed adhesion.
Invest In a Good Build Surface
Some 3D printers come with a glass bed or blue painter’s tape installed on the bed. Although these surfaces might work fine for PETG, we recommend using a heated build platform for best results. The heated bed can significantly improve the first layer adhesion, making things much easier for future prints. Many of these heated beds come with a glass surface, allowing you to print directly on the bed without needing to apply any additional layers of tape or glue.
Calibrate Retraction Settings to Reduce Stringing
One of the few common issues that we see with PETG is stringing. These strings are thin hairs, similar to a spider web, that run between the different surface of your 3D print. Preventing these strings requires precisely calibrated retraction settings, so make sure to adjust your retraction distance and speed for the best results. Simplify3D also includes several useful features that can further reduce stringing. The first is called Coasting, which works by reducing the pressure in the nozzle right before the end of a segment. This way, when moving to the next segment, there is less pressure in the nozzle, so you are less likely to see stringing and oozing during that move. Another great option can be found on the Advanced tab of your Simplify3D process settings. By enabling the “avoid crossing outline for travel movements” option, the software will automatically adjust the travel movements of your print to stay on top of the interior of your model as much as possible. This means that the strings stay inside of your part where no one can see them, instead of being on the outside of your model.
If you are looking for more tips to reduce stringing, we have an entire section dedicated to this issue on our Print Quality Guide: How to Reduce Stringing and Oozing.
Optimize Extruder Settings to Prevent Blobs and Zits
When 3D printing at higher temperatures associated with PETG, you may notice small blobs or zits on the surface of your model. These print defects typically occur at the beginning or end of each segment, where the extruder has to suddenly start or stop extruding plastic. There are several ways to eliminate these print defects such as enabling “Extra Restart Distance” or “Coasting” options located in the Extruder tab. Simplify3D also includes an option to perform a dynamic retraction, where the filament is retracted while the extruder is still moving. This completely eliminates blobs that are typically formed from a stationary retraction. To learn more about these features and other tips for reducing blobs on the surface of your print, please refer to our Print Quality Guide.
Pro-Tips
- The glossy surface of PETG is especially useful when using rafts. The part separates easily from the raft and maintains a clean surface finish.
- Try disabling your part cooling fan for the first few layers of the print to prevent warping. This trick especially works well for larger prints.
Get Started with PET / PETG
Now that you are ready to start printing with PET / PETG, here are a few ideas to help you get started – from common applications to popular filament brands.
Common Applications
- Water proof applications
- Snap fit components
- Planter Pot
Sample Projects
- Self-watering Planter
- Water Bottle
- Snap Fit Parts
Popular Brands
- ColorFabb PETG
- eSun PETG
- E3D Spoolworks Edge
- Hatchbox PETG
- HobbyKing PETG
Ultimate Materials Guide - 3D Printing Flexible Filament
Overview
Flexible filaments are made of Thermoplastic Elastomers (TPE) which are a blend of hard plastic and rubber. As the name suggests, this material is elastic in nature allowing the plastic to be stretched and flexed easily. There are several types of TPE, with Thermoplastic polyurethane (TPU) being the most commonly used among 3D printing filaments. In many cases, these terms are used interchangeably, along with popular brand names such as Ninjaflex. The degree of elasticity in the plastic depends on the type of TPE and the chemical formulation used by the manufacturer. For example, some filaments can be partially flexible like a car tire but others can be elastic and fully flexible like a rubber band. This guide will cover tips to help you with both of these variations of flexible filaments.
- Flexible and soft
- Excellent vibration dampening
- Long shelf life
- Good impact resistance
- Difficult to print
- Poor bridging characteristics
- Possibility of blobs and stringing
- May not work well on Bowden extruders
Hardware Requirements
Before 3D printing with flexible filaments, make sure your 3D printer meets the hardware requirements listed below to ensure the best print quality.
Bed
Temperature: 45-60 °C
Heated Bed Optional
Enclosure Not Required
Build Surface
PEI
Painter’s Tape
Extruder
Temperature: 225-245 °C
Direct Drive Extruder Recommended
Cooling
Part Cooling Fan Required
Best Practices
Flexible filaments come with many unique challenges that you want to be aware of. These tips will help you reduce the chances of common 3D printing issues such as clogging, kinking, and stringing.
Use Direct Drive Extruders
While some partially flexible filaments work fine with Bowden Extruders, most fully flexible filaments require a Direct Drive extruder for best results. The distance between the drive gear and the melt zone of the hot-end needs to be as short as possible to efficiently feed the filament into the nozzle. Additionally, the pathway through which the filament travels into the melt zone should have tight tolerances to prevent the filament from kinking or coiling inside. For these reasons, it is typically much easier to print flexible filaments with a Direct Drive extruder versus a Bowden extruder. If you are unsure about your 3D printer’s capabilities, you may want to check with the manufacturer to see if the extruder has been approved for use with flexible filaments.
Use Slow and Consistent Feed Rates
Flexible filaments typically print best using a slow and consistent feed rate. Because the material is elastic, it can be very difficult to control sudden changes in the print speed. Higher print speeds can cause the filament to compress and will most likely result in a jam. Slow and steady is the best approach. Simplify3D provides all of your feed rate settings on the Speeds tab of your process settings so that you can easily configure these values. Finding the optimal print speed for your material can take several attempts based on trial and error. We have seen that speeds of 1200 mm/min (20 mm/s) can be a good starting point for most materials.
Reduce Resistance from the Filament Spool
A few tweaks to your material spool can also make a big difference with flexible materials. Typically, your extruder will pull the filament into the nozzle, forcing the filament spool mounted on your printer to unwind a bit of plastic in the process. However, because flexible materials are elastic, this will stretch the filament out as it is being pulled in and can actually result in under-extrusion. Try mounting the spool above your printer so that the filament unwinds in a downward direction which can reduce the resistance. It can also be incredibly helpful to mount the spool’s hub on a bearing to allow the spool to spin as freely as possible.
Tune Your Retraction Settings
The elastic nature of flexible filament makes it sensitive to quick movements such as retractions. In order to successfully print the filament, you will need to optimize your retraction settings to reduce these movements. While you are first starting with this material, we would recommend disabling retraction completely. You can make this change in Simplify3D on the Extruders tab of your process settings. With retraction disabled, you can focus on finding the perfect speed and extrusion rates that allow you to reliably print your models. After you are more confident in these settings, you may wish to add a very small amount of retraction with a slower retraction speed to help with any potential oozing from the hot-end. Simplify3D also includes a unique option called Coasting, which will automatically help lower the pressure in the nozzle when you approach the end of a segment, which can significantly reduce blobs and stringing with these materials. If you want more information about other options that can help reduce hairs and stringing on your prints, we have an entire section on our Print Quality Guide dedicated to that issue: How to Reduce Stringing and Oozing.
Optimize Your Travel Movements
Retractions can be particularly troublesome for flexible materials, so it is typically best to minimize the number of retractions required for your print. Simplify3D has a great feature that was built specifically for this situation. Instead of moving in a straight line from point A to B, the software will actually choose a completely new path when moving between these points, with the goal of staying within the interior of your object so that there won’t be any oozing or stringing. With this unique feature enabled, you can greatly reduce the amount of retractions required for your print and significantly improve your print quality. To use this feature, click on the Advanced tab of your process settings, and enable the “Avoid crossing outline for travel movement” option.
Pro-Tips
- Optimize the feed rate by printing at lower layer heights in the 0.1mm – 0.2mm range. The lower layer height requires less plastic, so it allows your extruder to use a lower feed-rate, relieving the burden on the filament.
- Try to avoid using rafts with flexible materials, as the base layers of the raft have higher extrusion rates which may create issues.
- If you are designing a flexible part that needs to fit on top of another object, try using a negative tolerance between the parts so that the flexible part will need to stretch to fit over the other object snugly.
Get Started with Flexible Filaments
Now that you’re ready to start printing with flexible materials, we have a few tips to help you get started. View some typical applications below, try out a few of our sample projects, or choose a popular filament brand to purchase for your next project.
Common Applications
- Vibration dampening
- Grip Sleeves
- Phone cases
Sample Projects
- RC Car Tire
- Phone case
- Bike Handle
Popular Brands
- NinjaTek Ninjaflex, Armadillo, Cheetah
- Polymaker PolyFlex
- eSun TPE
- Sainsmart Flexible TPU
3D printing material comparison
3D printing material comparison
3dunitprint2022-02-07T14:43:04+03:00
3dunitprint Knowledge base 0 comments
ABS - PLASTIC
Acrylonitrile butadiene styrene (ABS) is one of the most popular plastics. It is an easily accessible, durable and lightweight material. ABS plastic comes in a wide range of colors. Its strength and ease of processing have led it to become the most popular of the engineering polymers. nine0006
Manufacturing techniques: FDM
- Rugged
- Flexible
- Easy to process
- Resistant to everyday chemicals
- Temperature resistant
- High print shrinkage
- “Plastic” smell when printed
- Not suitable for food contact
Strength
90%
Cost
20%
Moisture resistance
70%
Ultraviolet resistance
40%
Chemical resistance
9000 varieties of sugar cane and tapioca), which makes it biodegradable. This is a simple material for 3D printing, when heated, it releases a pleasant sweet aroma. For this reason, many people prefer its ABS. nine0006Manufacturing techniques: FDM
- Eco-friendly, biodegradable
- Food contact
- Hard, durable
- Low shrinkage
- High surface quality
- Low softening point 50°C
- Narrow temperature range (-20 to +40°C)
- Short-lived
- Fragile
Strength
75%
Cost
20%
Moisture resistance
20%
Ultraviolet 6,000,0007,0006,000 9000 (polyethylene terephthalate glycol) is a modified Polyethylene terephthalate (PET), most of the people on the planet know this plastic as a water bottle material. This material is the second alternative to ABS, it does not emit caustic fumes when melted, while remaining strong and flexible. nine0006
Manufacturing techniques: FDM
- Odorless printing
- UV resistance
- Wide operating temperature range.
- Good slip and impact resistance
- Non-toxic, can be printed on products intended for contact with food.
- Strength and softening point lower than ABS.
- High printing temperature quickly destroys the PTFE insert in the hot end
- Scratches more than ABS.
- Absorbs moisture from the air
Strength
90%
Cost
30%
,0007 (polycarbonate) is a high strength material designed for harsh environments and engineering applications. It has extremely high thermal deflection and impact resistance. Polycarbonate also has a high glass transition temperature of -150° Celsius. This means that it will maintain its structural integrity up to this temperature, parts made with this material show significantly improved mechanical strength compared to ABS and PLA.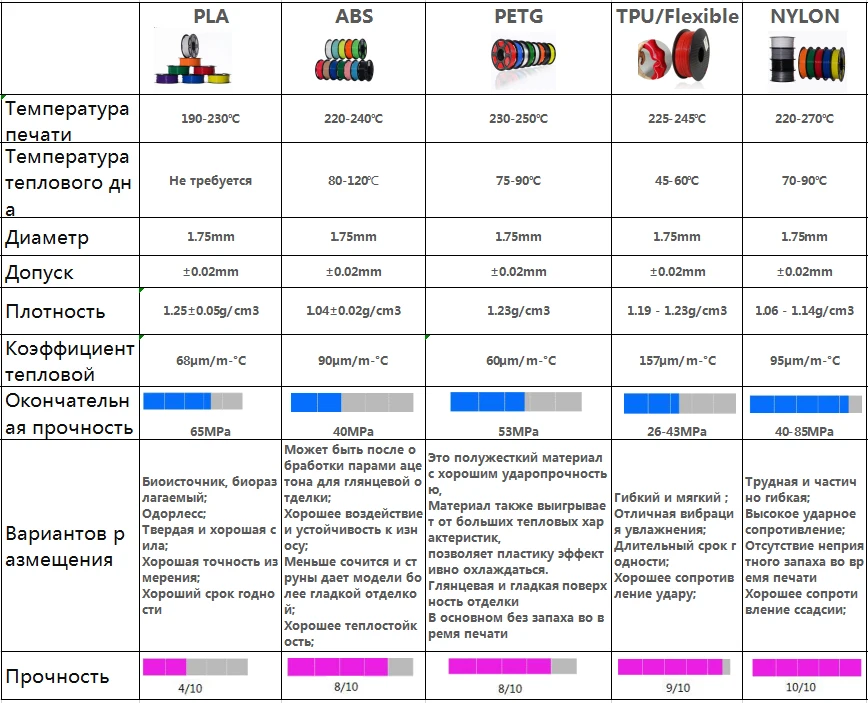
Manufacturing techniques: FDM
- Impact resistance
- High temperature resistant
- Naturally transparent
- Flexibility
- Durability
- Tendency to warp
- Very high print temperature required
- High tendency to shrink during printing
- Absorbs moisture from the air, which can cause print defects
Strength
%
Cost
45%
Moisture resistance
55%
Ultraviolet 9000% 9000% 9000% 9000% 9000 9000 is a dissolvable support material commonly used with ABS. When used as a support material, it can be dissolved in d-Limonene leaving the print free of any defects caused by the removal of supports. HIPS has many of the same printing properties as ABS, making it a logical partner for dual extrusion. This material is more stable and slightly lighter than ABS, making it an excellent choice for parts that wear quickly or are used to print lighter products. nine0006
Manufacturing techniques: FDM
- Low cost
- Impact resistant
- Waterproof
- Lightweight
- Soluble with d-limonene
- Heated deck required
- Closed chamber recommended
- High Print Temperature
- Ventilation required
Strength
80%
Cost
10%
Moisture resistance
80%
Ultraviolet 6,0006
70%
Chemical resistance
9000% %Flexible - plastic
flexible (flexible threads) are elaborated from thermopias (TPE), which are a mixture of hard plastic and rubber. This material is elastic in nature, which allows it to stretch and flex easily. There are several types of TPE, with thermoplastic polyurethane (TPU) being the most commonly used among 3D printing filaments. The degree of elasticity of the plastic depends on the type of TPE and the chemical composition used by the manufacturer. For example, some threads may be partially flexible, like a car tire, while others may be elastic and fully flexible, like a rubber band. nine0006
Manufacturing techniques: FDM
- Flexible and soft
- Excellent vibration damping
- Long shelf life
- Impact properties
- Hard to print
- Difficulty in removing supports
- Not suitable for all 3D printers
Strength
80%
Cost
60%
Moisture resistance
80%
Dustyness to ultraviolet
70%
Chemical resistance
70%
% Photopolymers are liquid resins, they usually consist of epoxy resin or a combination of acrylic and metakril monomers . When exposed to UV radiation, these monomers quickly form molecular bonds with each other and turn into a solid polymer. The main modern technologies where photopolymers are used are SLA/DLP and PolyJet. Resin 3D printing is also an additive process, just like FDM printing. This means that the process is based on a layer-by-layer building process, where one layer forms molecular bonds with the next layer. This process is repeated until the entire model is recreated. nine0006
Manufacturing techniques: SLA/DLP , Polyjet
- High detail
- Smooth surface
- Faster printing process
- Finished product uniform in all axes
- High material cost
- More labor intensive removal of supports
- More limited choice of materials nine0035
- High detail
- High strength
- Finished part flat surface
- Supports not required
- Fast printing process
- High material cost
- Rough surface (can be removed with post-processing)
- Limited materials
- Available in one color (white)
- Minimum number of supports
- Wide choice of materials
- High detail
- Finished products strong and light
- High cost of materials
- Special storage conditions for powders
- Long print time
- Mandatory post-processing nine0020 High power consumption
- Some general information
- Main features
- Precision
- Smell
- Storage
- Finally
- Where to buy ABS
- Where to buy PLA
- Where to buy SBS
- Where to buy PETG
Strength
80%
Cost
75%
Moisture resistance
80%
Dustyness to ultraviolet 9000,000% 9000% 9000% 9000 9000 is one of the most popular 3D printing materials used by professional 3D printing companies. Polyamide is the reference material in the technology of SLS-laser sintering of plastic powder. This technology is used for rapid prototyping and rapid production. With this technology it is possible to create complex three-dimensional objects that can be used as prototypes or as functional parts. nine0429 Given its flexibility and strength, nylon is an indispensable material for a wide range of applications from engineering to art. Nylon (polyamide) parts have a rough surface that can be polished to a smooth finish. Nylon is stronger than all other types of plastics, making it an ideal material for 3D printing products that require good tensile strength and mechanical strength.
Manufacturing techniques: SLS
Strength
90%
Cost
90%
Moisture resistance
65%
Ultraviolet resistance
9000% 9000 nickel, titanium) are metals that are ground to particles and are pre-base materials for most 3D printing processes producing metal parts.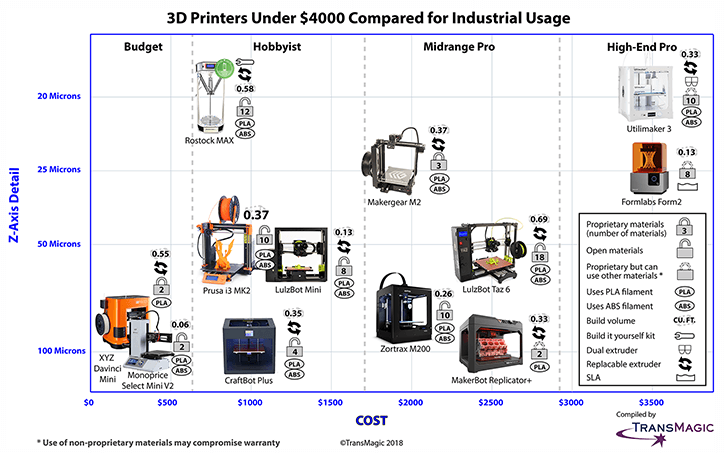
Manufacturing techniques: SLM
strength
100%
Cost
100%
Moisture resistance
100%
Dustyness to ultraviolet
9000 9000 9000Author
3dunitprint
Comparison of ABS, PLA, SBS, PETG.
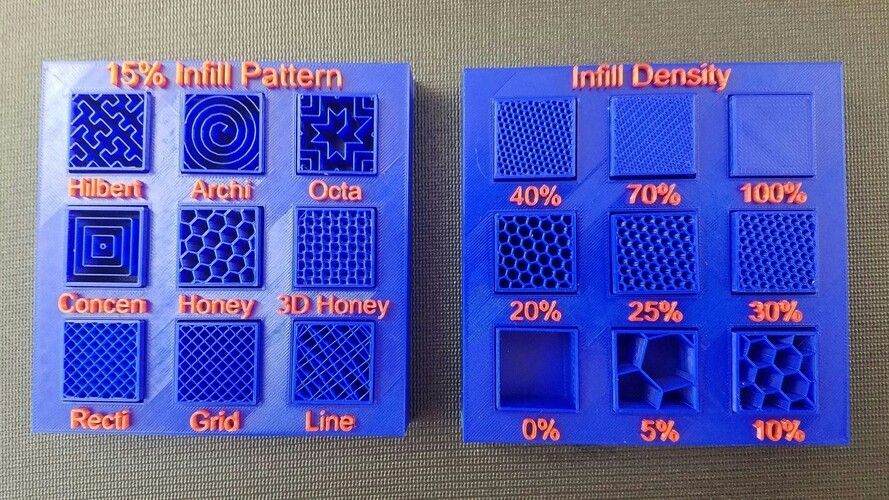
Table of contents
Some background information
There are many materials that have been explored for their applicability in 3D printing, and ABS, PLA, SBS and PETG are currently dominating this niche. nine0551
They are all thermoplastics, i.e. they become soft and plastic when heated, and harden when cooled. This process can be repeated many times. The susceptibility to melting and processing is precisely the property that has made thermoplastics a leader in everyday use and has led to the fact that most of the types of plastic that we encounter in everyday life are thermoplastics.
Basic features
In addition to the fact that objects must be accurately manufactured, they must perform the necessary functions. nine0551
ABS can take on many different polymeric forms and can be molded into many different properties. Overall, it is durable and somewhat more pliable than PLA plastic. Natural ABS has a beige (milky) hue before coloring. Plasticity of ABS makes it easy to create elements of various connections and fasteners. It is easily sanded and processed. It is important to note that ABS dissolves in acetone, which allows parts to be bonded and a very smooth surface to be achieved. nine0006
PLA plastic is created from a wide variety of agricultural products - corn, potatoes, sugar beets, etc. – and is considered more environmentally friendly than oil-based ABS. It was originally used to make food packaging and is easily recycled in industrial composting plants. It won't decompose in your backyard compost pile Test PLA for durability In its natural state it is transparent and can be dyed, resulting in varying degrees of transparency. PLA is just as strong but more rigid than ABS, making it harder to use for joining different elements. Printed objects tend to be smoother and shinier. PLA is slightly harder to sand and machine than ABS. PLA dissolves in methylene chloride (dichloromethane). The lower melting point makes PLA unsuitable for a number of situations - for example, in a day in a heated car interior, parts from it can deform and “leak”. nine0006
SBS Its strength, ductility and heat resistance make it the material of choice in engineering and mechanical applications. The modulus of elasticity is much less than that of ABS. That is, the printed parts are more flexible. Elongation at break >250%. The thread, unlike ABS, does not break, not to mention PLA, which is the most brittle of the materials considered. SBS has a flexible structure. It will not break off or break off when printing. Even if the bar is fed into your extruder at an angle of 90 degrees! The material is transparent (93% light transmission). The coloring of the material gives a very beautiful effect. It is processed and dissolved by Limonene, Dichloromethane, solvent. SBS is ideal for printing lampshades, glassware prototypes, bottles, etc.
PETG PETG is said to combine the advantages of ABS for strength, heat resistance, durability, and PLA for ease of use in printing. It is slightly more flexible than ABS and PLA, but more rigid than SBS. The fusion of the layers is usually excellent. Low heat shrink. You can not be so afraid of distortions in the size of printouts. nine0006
Precision
All these materials can be used to create precise spatial features. There are, however, certain nuances that should be kept in mind with regard to the types of plastic in question.
ABS With ABS, the only significant problem is the plastic wrapping when in contact with the print surface. This problem can be easily eliminated by heating the print surface itself, which should be smooth, flat and clean. In addition, some resort to additional tricks, such as applying a mixture of ABS and acetone to the surface or spraying it with hairspray. Fixpad coating for 3d printer and film for 3d printer table give good results. nine0006
Heating of the table is needed to ensure the phase state of contact between the plastic and the table - it must be in a state of elastic deformability - for ABS this is the range of 105-230 degrees. At a temperature below, it crystallizes and exfoliates, and above it, it passes into a state of viscous fluidity and also exfoliates. But usually the table is heated to only 70 degrees. The heating of the table provides the task of maintaining the entire volume of the product at the temperature of elastic deformability with a minimum layer-by-layer gradient. But if the product is large enough - more than 5 cm, this condition can be fully ensured only in a closed print chamber, which is almost never observed in RepRap. nine0006
PLA Compared to ABS, PLA layers curl much less. This makes it possible to print without heating the table and use the blue 3M adhesive tape beloved by many, but which was recently discontinued, but replaced by the universal fixpad coating. Eliminating the heated substrate entirely can still result in some curling of large layers - although not always. When heated, PLA undergoes more significant phase changes and becomes more fluid. With active cooling, when printing, you can achieve sharper elements and corners - without the risk of creating a fragile object. The increased fluidity also provides better adhesion between the layers, and the result is more durable. How to avoid nozzle clogging in a 3D printer. nine0006
SBS Resistant to open air and drafts. Sticks well to the table. It is possible to print on a cold table. SBS Watson is well suited for printing large layouts. Excellent interlaminar adhesion (sticking between layers) adds strength to printed products. Plastic is approved for the manufacture of medical devices and children's toys.
PETG Likewise, not afraid of open air and drafts. Sticks well to the table. Heating the table is not necessary, but may be useful, especially if distortion of large parts is detected. It is quite possible to print without heating, but you will have to tinker with the settings a bit. Very strong and durable material. nine0006
Smell
ABS When printing with ABS, there is often a strong smell of hot plastic. Some complain about it, others do not notice or do not consider it too unpleasant. In order to reduce odor, adequate ventilation should be provided in small spaces, as well as ensuring that the ABS is sufficiently clean, free from impurities, and heated to the required temperature in the correct extruder.
PLA Bioplastic, polylactide, or in other words, lactic acid polymer. Produced by synthesis from plant materials containing starch (or sugar), such as corn, sugar cane, cereals. When heated, it emits the smell of sweetish cooking oil. This, of course, is not the smell of grandmother's pies, but many consider it much more pleasant than the smell of heated plastic. nine0006
SBS does not smell during printing. People with a very delicate sense of smell can catch a slight smell (from some dyes) within a radius of 30 cm from the hot end, but nothing more. Transparent has no smell at all.
PETG is practically odorless, at least much less than ABS
Storage
Both ABS, PLA and SBS give the best results if the materials are isolated from the atmosphere to prevent the ingress of moisture from the air during storage and before use. nine0551
This does not mean that the plastic will degrade if left on the shelf for a week in a store, but prolonged storage in a humid environment can adversely affect both the printing process and the final product. ABS and PLA are best stored in vacuum or tightly closed packaging to avoid excessive moisture in the materials.
Wet ABS may start to bubble and splatter when printed, affecting the appearance, accuracy and strength of the resulting object, and there is a risk of clogging the nozzle with exfoliating plastic. ABS is easily dried in warm (preferably dry) air, such as in an electric oven at 70 degrees. nine0006
PLA reacts slightly differently to moisture. In addition to bubbles and nozzle clogging, because PLA reacts chemically with water at high temperatures and depolymerizes, discolouration and degradation of printed parts may occur. Although PLA can also be easily dried in a conventional oven (50-60°C), it should be noted that this may change the degree of crystallization of the plastic, resulting in changes in temperature and other extrusion characteristics. For many 3D printers, this is a major problem. nine0006
SBS does not absorb moisture! You can store it simply in a bag (so as not to gather dust). The rod does not become brittle from contact with moisture. You can also print dishes from it, contact with cold food products is allowed.
PETG is virtually unaffected by normal ambient humidity, so printing and storage are no problem. And yet, it is good that the filament is stored in as dry a place as possible, next to the silicate bags. nine0006
In conclusion
Summarizing and simplifying the thousands of reasons why one plastic should be preferred over another, here's a quick summary.
ABS Often preferred in engineering and professional applications due to its strength, ductility, ease of processing and high temperature resistance. Heated ABS, like any petroleum-based plastic, has an unpleasant odor to many. The need for a heated substrate makes it almost unusable for satisfactory print quality on some printers. nine0006
PLA The wide range of available colors, translucency levels, and the resulting glossy surface make this plastic attractive for art objects and household utensils. Many people have in mind the vegetable origin of this plastic and prefer its semi-sweet smell to the smell of ABS. With the right cooling regimen, PLA print speeds are faster, layers are thinner, and corners are sharper.