Porsche 3d print
Porsche best 3D printing models・Cults
Porsche 909 Bergespyder Printable Car
€8.33
Porsche 918 Door Mirror in 1/24 scale
€1.88
Porsche Carrera GT Door Mirror in 1/24 scale
€1.88
Porsche 911 (996generation) GT3 Seat in 1/24 scale
€1.88
Porsche 911 (996generation) Door Mirror in 1/24 scale
€1.88
Porsche 911 (996) Steering Wheel in 1/24 scale
€1.88
Carrera 132 Porsche RSR GT3 rear wing
€5.17
Porsche 356 coupe 1948 PRINTABLE CAR BODY
€5.68
Porsche 356 coupe 1948 PRINTABLE CAR IN SEPARATE PARTS
€10. 23
Porsche 935 2019 PRINTABLE CAR BODY
€5.68
Porsche 935 2019 PRINTABLE CAR IN SEPARATE PARTS
€10.23
Porsche 918 spyder 2011 PRINTABLE CAR BODY
€5.68
Porsche 918 spyder 2011 PRINTABLE CAR IN SEPARATE PARTS
€10.23
Porsche 911 Turbo Coupe 2000 PRINTABLE CAR BODY
€5.68
Porsche 911 Turbo Coupe 2000 PRINTABLE CAR IN SEPARATE PARTS
€10.23
Porsche 906 Carrera 6 Coupe 1966 PRINTABLE CAR BODY
€5.68
Porsche 906 Carrera 6 Coupe 1966 PRINTABLE CAR IN SEPARATE PARTS
€10.23
Porsche 996 and 986 brake disks
€1
Posche Steering Wheel
€1. 50
Porsche Taycan
€4.50 -20% €3.60
GAZ 21 VOLGA cabriolet
€1.50 -20% €1.20
Gunther Werks 993 Cover
€14.12
Porsche 968 Turbo S Printable Body Car
€8.33
Porsche 911 Carrera 4
€7.06
Brazos limpiaparabrisas para RC1/28 1/10 ETC...Reescalable alto poligono
€1
Metamorphosis keychain - Porsche 911 GT3 RS
€3 -67% €0. 99
Porsche Cayenne
€5 -40% €3
Fuchs Wheel Cookie Cutter
Free
V6, V8 and V10 engines
€2.80 -50% €1.40
Pencil Cup Porsche 911 Carrera
€2
Metamorphosis keychain - Porsche 911 Turbo
€3 -67% €0.99
Wall decoration Porsche 911 model 996
€0.80
Metamorphosis keychain - Porsche Cayman S 2014
€3 -67% €0. 99
Porsche Beetle Fox rims
€20 -50% €10
Porsche 911 Turbo S
€5 -40% €3
Lego Style Brick Porsche 911 Turbo
€5
Porsche Macan
€5 -40% €3
Carrera 124 Porsche 911 RSR rear wing
€5.17
Retrovisor para Porsche Clasico TAMAÑO REAL o tamaño escala R/C 1/10 1/28....
€2
Mercedes 1999 CLR Coupe
€11. 29
Glickenhaus SCG007 Hypercar
Free
Porsche 550 1500 RS Spyder Printable Car
€12.50
Name led Carolina
€3
Metamorphosis keychain - Porsche 718 Boxster
€3 -67% €0.99
V10 engine print in place
€1.76 -50% €0.88
Keychain Porsche 911
€0.65
Porsche 928 GT Key
€112.02 -10% €100. 82
Mesa Porsche V1.0
Free
3D-printed pistons - Porsche Innovations
Innovative pistons created in a 3D printer have successfully completed their first endurance test in the engine of a 911 GT2 RS. Additive manufacturing processes (3D printing) enable the realisation of designs that are not feasible using conventional methods. It was therefore possible to optimise the piston structure to correspond to load conditions and also to integrate a cooling duct, while at the same time reducing each piston's weight by 10 per cent in comparison with a production forged piston. “This has allowed us to increase engine speed, lower the temperature load on the pistons and optimise combustion,” explains Frank Ickinger of Porsche's Advance Drive Development Department. “The result is more power and greater efficiency.” This means that a power increase of up to 30 PS is possible for the 515 kW (700 PS) Porsche 911 GT2 RS. The pistons have been developed as part of a cooperative project to develop an additive manufacturing process for highly-stressed drive components in which Porsche is working together with its supplier and development partner Mahle as well as the advanced technology company Trumpf. It has also been possible to include a further project partner in the form of the optical company Zeiss, which brings expertise in measurement and testing processes for additive manufacturing.
Optimised piston: lighter and with a higher load capacity thanks to its bionic design
The 911 GT2 RS is equipped with forged pistons as standard, but their potential for use in future high-performance engines is practically exhausted. Improvements have only been possible with changes that could no longer be realised using conventional production methods. In contrast, additive manufacturing makes it possible to implement a so-called bionic design in which material is only used in those locations where forces are transferred. For this topology optimisation, the engineers used a special design method that is matched to the specific conditions of 3D printing. Working with project partners Mahle and Trumpf, it has therefore been possible to reduce the weight of the pistons by 10 per cent and to validate the quality and performance capability of the topological structures with measurement technology from Zeiss. “We've always made sure that we always err on the safe side,” says Frank Ickinger. “Our simulations show that there is a potential weight saving of up to 20 per cent per piston.”
The second goal was the integration of an annular cooling duct behind the piston rings. This duct has a special cross-sectional shape and is closed like a tube apart from inlet and outlet openings for oil. Such a structure can be produced only by means of an additive manufacturing process. Thanks to this additional cooling, the temperature of the component has been reduced by more than 20 degrees in the piston ring area, which is subject to extreme thermal loads. The combination of all these measures makes for optimised combustion with higher pressures and temperatures, resulting in greater efficiency. “This is a good example of how the combustion engine still has future potential,” says Frank Ickinger.
Technology know-how from Mahle, 3D printing expertise from Trumpf, measurement and testing process from Zeiss
Porsche has relied on the competence of Mahle in the development of the 3D-printed pistons, just as it did for the production forged pistons in the 911 GT2 RS. The technology company has developed a weldable powder for additive manufacturing from their proprietary Mahle aluminium alloy M174+. The characteristic values of the printed material are comparable with those of the cast material for production pistons. In order to assess the suitability of the powder for the manufacturing process, it was subjected to multiple quality tests in cooperation with measurement technology specialists from Zeiss, including inspection by light microscope, scanning electron microscope and X-ray microscope.
The advanced technology company Trumpf was responsible for the development of the production process and printing. High-precision Trumpf TruPrint 3000 machines welded the powder layer by layer using the laser metal fusion process (LMF), also known as laser powder bed fusion (LPBF). In this process, the powder is fused by laser beam in a thickness in the µm range (0.02-0.1 millimetres), thus building up the piston layer by layer. The piston blanks are produced in this way with approximately 1,200 layers taking in the region of 12 hours. Testing using different non-destructive methods such as computer tomography, 3D scanning and microscopy, as well as analysis of dissected pistons, was undertaken with partners Mahle, Trumpf and Zeiss. These tests confirmed that the quality of the printed pistons did not differ from that of cast pistons.
Six pistons were then installed in a 911 GT2 RS engine for practical testing, which was subjected to a 200-hour endurance test on a test rig under the toughest of conditions. The test programme simulated 24 hours on a high-speed track, which included approximately 6,000 kilometres at an average speed of 250 km/h, including stops for refuelling. There were also 135 hours at full load and around 25 hours under drag load with different engine speeds in each case. The end result was that all pistons passed the test.
The development of piston production using additive manufacturing specifically for high-performance derivatives does not just show the opportunities available for exploiting previously unused potential, but can also offer enormous time savings in development. Due to the omission of the tool-making process necessary for cast pistons, it is therefore possible to reduce the procurement time for prototype pistons by over 30 per cent.
New possibilities, but also new design engineering requirements
3D printing opens up a host of new possibilities both for the optimisation of existing processes and also the development of future technology. “Things that have not been possible before can now be realised,” enthuses Frank Ickinger. This is also true for highly-stressed components, as is shown by the example of the 911 GT2 RS piston. Its lower weight and higher thermal resistance directly benefit the driver in that engine speed can be increased due to a reduction in oscillating masses. “An extra 300 rpm equates to around 30 PS more,” calculates Frank Ickinger. The torsional vibration damper can then be made smaller, thereby making the engine even more free-revving. Increased thermal resistance due to the lower temperature permits higher combustion pressures and even more advanced ignition timing – both factors that increase power and efficiency.
However, this extended design freedom does also go hand in hand with new design requirements, which include the engineers having to take into account the way that the components are produced layer by layer by fusion. “If there are overhangs with an angle of more than around 45 degrees, for example, it is necessary to incorporate support structures in order to stabilise the geometry and prevent distortion,” explains Frank Ickinger. “Otherwise, there is a risk of warping or bulging in an upward direction, which could damage the recoater used to apply the powder layer, with the result that the build process has to be aborted.” The goal is to generate as few supporting structures as possible because these usually have to be removed again later. Trumpf's expertise in the area of 3D printing has also made it possible to implement other design guidelines with respect to manufacturability and economic efficiency, such as minimising the number of support structures.
Working alongside Porsche development engineers, the design realisation of the optimised piston structure was tackled by the experts from Mahle. The technology group has been exploring the possibilities offered by additive manufacturing for many years already. Using CAD software, Mahle reproduced the structures that had been created as part of the topology optimisation. The innovative cooling duct was then defined, described by Frank Ickinger as “a perfect example of functional integration". The design data was then subjected to a finite element simulation and analysed with respect to the resistance to failure, service life and temperature loading of the virtual piston. The additional annular cooling duct at the level of the piston rings proved to be particularly advantageous, causing a reduction in temperature by over 20 degrees in the area with the highest thermal load under the exhaust valves. The optimum design that satisfied all requirements was finally achieved after several design and calculation loops. On this basis, the engineers then created a production model and drawings for final machining.
Powder material developed from cast alloy
In parallel to the design engineering process, the experts from Mahle determined a suitable material. The cast alloy M174+ proved to offer the best prerequisites so the piston specialists developed the powder for the additive manufacturing process from this. In order to test its suitability for additive manufacturing, the powder was first analysed by Mahle and Trumpf by means of flowability and bulk density measurements as well as other measurements to determine the moisture content and grain size distribution. In order to detect pores in the powder grains, the experts examined the surfaces in metallographic sections. Gaseous contamination was determined by means of carrier hot gas extraction. In addition, the grain properties in relation to contamination, particle form, particle size distribution and gas inclusions were analysed by Zeiss's measurement technology experts by means of light microscopy, scanning electron microscopy and X-ray computer tomography. It was also important at this point to analyse the behaviour and structure of the powder with respect to multiple use, an important aspect for recycling and sustainability.
The powder also did not show any changes relevant for the component properties in the case of multiple use. The goal was to be able to guarantee a homogeneous powder layer with reproducible powder characteristics in the subsequent build process.
For the first test specimens, Trumpf used additive manufacturing to produce simple geometric shapes such as cuboids and pins as material samples in order to determine the characteristics of the material. Several build jobs were performed in advance in order to find the optimum process parameters of the machine for this material. The results of the material characteristic analysis were consistently positive, the samples exhibiting largely uniformly distributed and round porosity with pore sizes between five and 50 µm. After the usual heat treatment, the test specimens' hardness was approximately the same as that of cast pistons. The physical characteristics were also similar to those of the cast material. Thermal expansion was slightly lower, for example, and the reversed bending fatigue strength values matched those of cast materials at 150 degrees Celsius and 300 degrees Celsius. The characteristics of the additively manufactured samples even exceeded those of conventionally cast material samples in some cases.
Additive manufacturing with Trumpf expertise
Design engineering and material development took place in close co-operation with the experts from Trumpf. The company – which, like Porsche and Mahle, has its home in the Stuttgart region – is a pioneer in the field of 3D printing with metal. Together with the Fraunhofer Institute for Laser Technology in Aachen, Trumpf has been conducting research in the area of laser metal fusion (LMF), also known as laser powder bed fusion, since 1999. Trumpf launched its first LMF machine on the market in 2004. The experts from the company were therefore predestined to develop the optimum parameters for printing the components.
Trumpf used a precision machine from its TruPrint 3000 series to manufacture the pistons. In the LMF process, the components are built up gradually in a powder bed. This takes place in the process chamber where the supply cylinder, build cylinder, and overflow cylinder are located next to one another in one axis. The process starts by the recoater shifting the powder from the supply container over the build cylinder, thus creating a powder layer. Excess powder lands in the overflow container. The laser beam then heats the powder surface corresponding to the part contour and melts it into a solid metal layer which is bonded with the already fused layers underneath. In the next step, the build cylinder is lowered and the recoater applies the next powder layer, a process that is repeated until the component has been completely generated. Finally, the powder that has not been fused is removed from the build cylinder in an unpacking station. This exposes the component and it can be removed from the substrate plate.
Tests confirm the uncompromising quality of the printed pistons
Building up parts layer by layer is the key to manufacturing shapes and structures that are not possible with conventional production methods such as casting or milling. “The piston from this co-operative project is an example of how we can create added value with 3D printing. The process permits the creation of parts with special properties and which are both lightweight and stable at the same time. Almost all industries can benefit from this. In addition to the automotive industry, Trumpf products are aimed above all at the aviation and aerospace, medical technology and energy sectors,” says Trumpf project manager Steffen Rübling. The TruPrint 3000 machine was ideal for production of the pistons thanks to its 30-centimetre-diameter cylindrical build area, which enable the production of five 104-mm diameter pistons simultaneously. The Trumpf experts were also able to show that productivity could be increased by a factor of up to three with the TruPrint 5000 system, which is equipped with three lasers.
The first samples of the high-performance pistons from the printer were analysed in detail. In addition to tests performed by Mahle and Trumpf, project partner Zeiss applied the same methods used for testing the first material samples: metallographic sections, light microscopy, X-ray spectroscopy and computer tomography. The scanned data of the piston blank were compared with the CAD data to determine whether the geometry had changed during the manufacturing process. The deviations were in the tolerance range of a cast piston and were therefore acceptable. Another important point was the interior of the cooling duct and whether there was still powder or welding residue present that could become detached during operation. This was also not the case due to the correspondingly adapted design. The high-resolution computer tomography inspection performed by Zeiss made it possible to search for defects such as small cracks or inclusions in advance so that the pistons could be released for further tests. Even small defects were marked by means of a special process known as the microdefect history so that these could be examined again non-destructively after the first tests, if necessary. In addition to examination of the metallographic sections, porosity and density were also determined for samples and cut-out sections of the piston using the buoyancy method, in which the lower the gas content, the lower the buoyancy force.
With a density of over 99.5 per cent, the pistons had the same value as cast components. Machining of the pistons at Mahle also did not reveal any disadvantages compared with cast M174+ material. The first test was then started on a hydropulser at Mahle where the piston was supported at the piston pin bore and loaded until failure. The number of completed load cycles was above the required number, so the test was therefore passed. The second test performed was the so-called boss tear-off test. In this test, the force required to tear off the piston pin boss is determined and the force value was also found to be in the same range as for cast pistons. The practical load test in a 911 GT2 RS engine finally confirmed the uncompromising quality of the additively manufactured pistons – and their potential for increasing performance and efficiency.
Additively manufactured twin-jet nozzles with improved jet quality
In order to supply oil to both this annular duct and, as on the production piston, the piston crown, a further component was produced using the 3D printer, which was a twin-jet oil nozzle made of stainless steel. “Production using conventional technology would have become very complex due to the geometry,” explains Porsche engineer Marco Klampfl. Manufacturing such a twin-jet nozzle conventionally would have meant realising a complex brazed or milled design, which also could not have been used in the engine package.
For this reason, the engineers designed an S-shaped and forked oil guide which was manufactured additively from stainless steel powder. This component was brazed together with the tube support and check valve to produce a piston nozzle. “Concerns that the oil jet quality might suffer due to poorer surface properties in 3D printing were not confirmed,” says Marco Klampfl. “In fact, the opposite was true, and we were able to show in comparative measurements that the jet quality was actually improved by further functional integration.”
Wide spectrum of applications for 3D printing at Porsche
Additive manufacturing offers great potential for Porsche in the area of product and process innovation as well as for new fields of business. Lightweight construction and functional integration are examples of product innovation, while agile development and flexible production are benefits in the area of process innovation. New business fields include personalisation as well as new offerings for customers and spare parts. This manufacturing technology is technically and economically interesting for Porsche specifically for special and small production runs as well as for motor sport. Additive manufacturing processes are also ideal for physically producing structures that have been designed and optimised by means of artificial intelligence (AI).
Porsche already uses additive manufacturing processes in several areas and is actively engaged in their further development. For example, since May, a 3D-printed body form full bucket seat has been available for the 911 and 718 variants used in motor sport. Here, the central section of the seat, in other words the cushion and backrest surfaces, is partly produced by a 3D printer. Customers will be able to choose between three firmness levels (hard, medium or soft) for the comfort layer in the future. Porsche Classic also uses additive processes to reproduce plastic, steel and alloy parts that had ceased to be available. As an example, the release lever for the clutch of the Porsche 959 today comes as a spare part from a 3D printer. Around 20 reproduced parts for Porsche classic models are currently manufactured using additive processes. The quality requirements of the original production period apply to all parts as a minimum specification but the new parts normally meet even higher standards. Porsche sees the overall success of the project as confirmation that it remains on the right track with regards to 3D printing. Due to the comparatively high costs per component, additive manufacturing is currently suitable only for parts required in small quantities where there would otherwise also be high tooling costs. Since Porsche frequently offers small series and special-edition models, “we are also considering producing pistons using the LMF process as standard for a complete special series of high-performance engines,” reveals Frank Ickinger.
Because there still used to be question marks about additive manufacturing for highly-stressed drive components in particular, the development engineer adds: “From design to production and through to finish machining, there are a great many new parameters and influencing variables that do not exist with traditional methods of production. We are going to need to reliably master all of them in order to achieve uniform quality so there is still plenty of work to be done for a series production process in the automotive industry.”
Many projects in development, part reproduction and performance enhancement
As part of the cooperation with Mahle and Trumpf, an additional charge-air cooler was produced as a further component. This was integrated into the air pipe connecting the turbocharger and charge-air cooler. Thanks to the possibilities offered by 3D printing, the charge-air cooler has a much larger surface area for heat transfer, which permits optimisation of the flow routing and cooling. The effect is that the intake air is cooler and the engine's power and efficiency are increased.
The potential benefits of additive manufacturing are also being investigated and assessed in the area of electric drives. “Using the example of a highly-integrated electric axle, we were able to also show the potential improvements not only in the product but also in its development process. By applying new design methods, it has been possible to double the rigidity of the drive and reduce its weight by around ten per cent. Thermal management was also significantly improved by the integration of a transmission heat exchanger while 12 components being built in allowed the omission of 30 screws, 12 seals and numerous other parts. This does not just create advantages in packaging, but also significantly reduces assembly work. "These measures made it possible to reduce the production time by almost 20 minutes,” explains Falk Heilfort from the Advance Drive Development Department. In addition, the use of copper as a printing material results in interesting concepts that offer great potential for electric motors. The topic of cooling can also be taken to a new level for pulse-controlled inverters and motors.
“For us developers, 3D printing offers a host of other benefits,” adds Frank Ickinger. Since new components can be manufactured without forming tools, this considerably shortens procurement times, and the time saved means that more variants can be tested. On balance, test parts can actually be less expensive because there are no tooling costs. Tools themselves can also be produced in an additive manufacturing process. As an example, an injection mould with integrated cooling allows the optimisation of the cycle times of conventional production methods. In addition to metal, 3D printing can also be used to print plastic parts and complex sand cores for casting processes such as for cylinder heads, crankcases and electric motor housings, making it possible to achieve significant benefits in the area of cooling.
However, in spite of the rapid further development of additive manufacturing processes, there are currently still major restrictions relating to them. Firstly, there are the costs, which remain economically justifiable only for smaller quantities, depending on the component in question. Secondly, the size of the component is a further limiting factor because it is not yet possible to manufacture larger parts in the process chamber of printers currently available. In addition, it is necessary to extend the range of materials both for plastics and metals. Finally, additive manufacturing still has to qualify itself for (small) series production processes in the automotive industry in terms of quality and reproducibility as well as economic efficiency.
“However, I am certain that additive manufacturing will be an established part of automotive development and production in 10 years' time at the latest,” says Frank Ickinger.
3D-printed pistons - Porsche Innovations
The new 3D-printed pistons have passed their first high-load test in the 911 GT2 RS engine. Additive technologies (3D printing) allow you to create designs that cannot be obtained using traditional methods. Thus, the piston structure has been optimized according to the load level and a cooling channel has been added, but at the same time, the mass has been reduced by 10 percent compared to the standard forged piston. “In this way, we can increase the speed, reduce the thermal stress on the pistons and optimize the combustion process,” explains Frank Ickinger, who represents the pre-development of drive systems at Porsche. “The result is increased power and efficiency.” For 911 GT2 RS with 515 kW (700 hp) can achieve a total increase of 30 hp. The new pistons are being created as part of a collaborative development effort in additive manufacturing for the production of highly stressed drive components. In doing so, Porsche cooperates with Mahle as a supplier and development partner, and the high-tech company Trumpf. Also, Zeiss, a company specializing in optical technology, with extensive experience in the production of control and measuring equipment, was attracted to the project. nine0003
Optimized pistons: lighter and stronger thanks to bionic design.
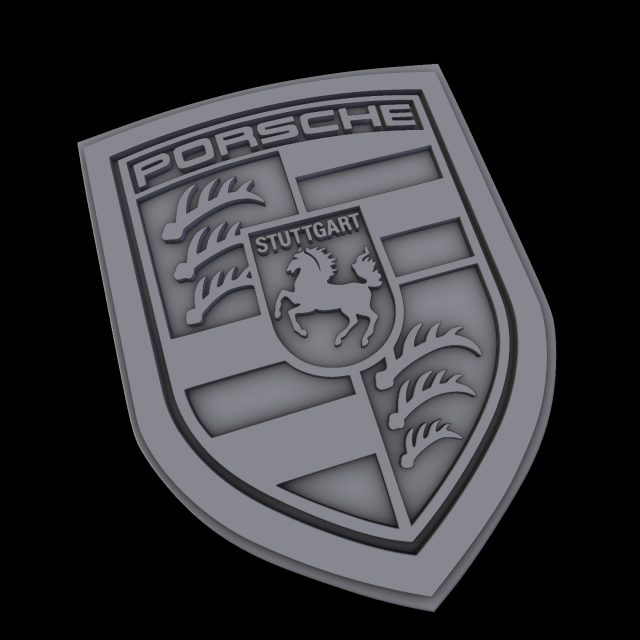
The 911 GT2 RS is equipped as standard with forged pistons, which have almost exhausted their potential for future high-performance engines. Only changes that cannot be implemented using traditional production methods can improve the situation. Thus, additive technologies make it possible to apply the so-called bionic design, that is, to use the material only in those places where it is really needed. In order to optimize the topology in this way, engineers use a special design technique that takes into account the special requirements of 3D printing. Working together with partner companies, Mahle and Trumpf, the piston weight has been reduced by 10 percent and the topological structures are of high quality and efficiency thanks to the use of Zeiss measuring technology. “At the same time, reliability was a priority for us,” says Frank Eckinger. “Our tests show that real weight savings per piston can be up to 20 percent.” nine0003
The second goal was to integrate an annular cooling channel behind the piston rings. This channel has a special cross-section, and it, like a tube, has a closed design, with the exception of two holes for oil inlet and outlet. Such a solution can only be implemented using additive technology. Thanks to the additional cooling, the temperature in the area of the piston rings, which is subjected to particularly high thermal stress, is reduced by more than 20 degrees. All of these measures combine to optimize the combustion process at higher pressures and temperatures, resulting in increased efficiency. "This is an example," says Frank Eckinger, "that the potential of the internal combustion engine is far from exhausted." nine0003
Mahle technology, Trumpf 3D printing expertise, Zeiss test and measurement technology
As with the production forged pistons for the 911 GT2 RS, Porsche is relying on Mahle's experience in 3D printing pistons. This technology concern has developed a weldable powder for additive manufacturing based on its own M174+ aluminum alloy. The characteristics of the printed material are comparable to the characteristics of the casting from which serial pistons are made. In order to assess the suitability of the powder for production, it was repeatedly tested by the measuring technicians from Zeiss, who used light microscopy, scanning electron microscopy and X-ray microscopy, among others. nine0003
The high-tech company Trumpf took over the development of the production process and printing. Trumpf's TruPrint 3000 precision machines welded the powder layer by layer using what is known as the Laser Metal Fusion (LMF) additive laser sintering process, sometimes also referred to as Laser Powder Bed Fusion (LPBF). In this case, the laser beam welds a layer of powder of micrometer thickness (0.02-0.1 mm) and thus prints the piston step by step. In 12 hours, approximately 1200 layers are used to create a blank for the piston. Verification using various non-destructive testing methods such as computed tomography, 3D scanning and microscopy, as well as analysis of cut pistons, was carried out together with partners - Mahle, Trumpf and Zeiss. At the same time, it turned out that the quality of the printed pistons does not differ from the quality of the cast parts. nine0003
Six pistons were installed in a 911 GT2 RS engine for practical testing. At the stand, he passed a long 200-hour test in the most severe conditions. The test program simulated a 24-hour race on a high-speed highway: about 6,000 kilometers at an average speed of 250 km/h, including gas stops. In addition, the engine ran for about 135 hours at full load and about 25 hours with additional traction at various speeds. Result: All pistons passed this test. nine0003
Additive manufacturing of pistons specifically for high performance models not only opens up hitherto untapped possibilities, but also provides exceptional savings in development time. For example, by eliminating the tooling required for castings, the time it takes to produce piston prototypes is reduced by more than 30 percent.
New possibilities and new design requirements.
3D printing opens up many new possibilities for both optimizing existing technologies and developing new technologies. "What was previously impossible is now a reality," says Frank Ickinger. This also applies to highly loaded components such as pistons 911 GT2 RS. The lower mass and higher thermal stability benefit the driver: the reduction of the oscillating masses allows the speed to be increased. “A 300 rpm increase means 30 hp more,” Frank Eckinger calculates. Torsional vibration dampers can be smaller, making the engine even more revving. Greater thermal stability due to lower temperatures allows for higher combustion pressures and earlier ignition timing, resulting in improved engine output and economy. nine0003
However, greater design freedom comes with new design requirements. So, engineers have to carefully monitor the creation of the part - layer by layer. “If, for example, protrusions are provided at an angle of more than 45 degrees, then so-called support structures must be used to prevent deformation,” explains Frank Eckinger. to terminate the process. At the same time, the use of support structures should be kept to a minimum, since later they still have to be removed for the most part. There are a number of requirements not only in terms of the fabrication process itself, but also in terms of economy, such as minimizing the use of support structures, which can be achieved thanks to Trumpf's experience in 3D printing. nine0003
Mahle teamed up with Porsche engineers to optimize piston design. The technology concern has been dealing with the problems of additive manufacturing for several years. The CAD software allowed Mahle to model the structures that were created during the topology optimization. The cooling channel was then dimensioned, which according to Frank Ickinger is "a brilliant example of functional integration". The design data was then verified using the finite element method, and the virtual pistons were tested for reliability, service life and thermal stability. At the same time, the most expedient solution was to create an additional cooling channel at the height of the piston rings: in the most thermally loaded area under the exhaust valves, the temperature dropped by more than 20 degrees. As a result of numerous calculations and development cycles, an optimal design was finally created that met all the requirements. On this basis, engineers created a prototype and drawings for production. nine0003
Cast alloy powder material
Parallel to the design process, the Mahle experts were looking for the right material. M174+ casting alloy offered the best basic conditions. From it, piston specialists have obtained a powder for additive manufacturing. To test whether it meets the requirements of additive manufacturing, Mahle and Trumpf first tested the powder by measuring its flow and bulk density, moisture content and grain distribution. To recognize pores in powder grains, experts examined their surface using metallographic sections. With the help of the so-called high-temperature gas extraction, the presence of gaseous contaminants was determined. In addition, Zeiss measurement technicians used light microscopy, scanning electron microscopy and X-ray microscopy to check for grain contamination, particle shape, particle distribution and gas inclusions. At the same time, it was important to analyze the behavior and structure of the powder during repeated use, which is an important point in terms of recycling and environmental compliance. Even with repeated use, the powder did not show any significant changes that could affect the quality of the parts made from it. The aim was to ensure that the powder layer was uniform and reproducible later in production. nine0003
As early prototypes, Trumpf AM produced simple geometries such as cubes and rods for material analysis and characterization. At the same time, many samples were created in order to find the optimal settings for printers using this material. The results of the determination of the parameters were extremely positive: all samples were characterized by evenly distributed round pores ranging in size from 5 to 50 µm. The strength of the samples after conventional heat treatment was at the level of cast pistons. Also, physical indicators were at the level of cast parts. So, the thermal expansion was somewhat lower, the fatigue limit under alternating loads at 150 and 300 degrees Celsius corresponded to the level of the cast material, and in some respects the printed samples even surpassed it. nine0003
Trumpf additive manufacturing and expertise
Design and material selection issues were handled in collaboration with Trumpf. This company, which, like Porsche and Mahle, is located near Stuttgart, is a pioneer in the field of metal 3D printing. Since 1999, Trumpf has been conducting research in the field of additive laser sintering (Laser Metall Fusion, LMF) together with the Frauenhof Institute for Laser Technology in Aachen. In 2004, the company introduced its first LMF printer to the market. Therefore, hardly anyone could better choose the optimal parameters for printing parts. nine0003
For the production of pistons, Trumpf used a high-precision printer from the TruPrint 3000 series. The LMF method involves the production of parts in layers. The whole process takes place in a special chamber. In it, on the same axis next to each other, there are filling, working and assembly cylinders. The process begins with the device feeding the powder from the filling tank through the working cylinder and depositing a layer of powder. Excess powder falls into a collection container. Then the laser beam, in accordance with the contour of the part, heats the surface of the powder and welds it, turning it into a solid layer of metal and bonding with the layers already existing below. At the next stage, the working cylinder is lowered and the device applies the next layer of powder. This process is repeated until the part is completely printed. The unused powder is then removed from the working cylinder, after which the part can be detached. nine0003
Tests confirm the uncompromising quality of printed pistons
Layer-by-layer production allows the creation of shapes and structures that would be impossible to produce using traditional methods such as casting or milling. "The collaborative piston demonstrates the benefits of 3D printing. The proposed method allows the production of parts with special properties, while being light and strong. They can be used in almost all industries. Trumpf does not only work for the automotive industry. Its customers include also firms from the aerospace, medical and energy industries," says Stefen Rübling, Project Manager at Trumpf. The TruPrint 3000 printer, with its 30 cm diameter cylindrical working chamber, was ideal for the production of pistons: their 104 mm diameter made it possible to produce five parts at the same time. Trumpf also showed that when using the TruPrint 5000, which uses three lasers, productivity increases by almost three times. nine0003
The first high-tech pistons produced by the printer have been carefully studied. In addition to the studies at Mahle and Trumpf, project partner Zeiss used the same control methods as in testing the first samples of the material: metallographic sections, light microscopy, X-ray spectroscopy and computed tomography. The scanned data for the piston blank was compared to the CAD data to check if the geometry had changed during production. The detected deviations did not exceed the tolerances for the cast piston and thus corresponded to the norm. Another important point was the quality of the inside of the cooling channel. Were there any particles of powder or welding that could disrupt the operation of the channel? Here, no violations were found. Zeiss' high-resolution computed tomography machines made it possible to look for defects such as small cracks or inclusions in advance, and thus prepare the basis for further tests. Even the smallest signs of defects were “marked” thanks to a special microdefectoscopy method, so that after the first tests, doubtful places could be examined without destroying the part. To determine the porosity and density, in addition to the so-called metallographic sections, the method of flotation of samples and parts of the piston was used: the less gas they contained, the less the buoyancy force. With a density of more than 99.5 percent of the printed pistons were flush with the cast parts. Also, the piston processing at Mahle showed no disadvantages compared to the M174+ cast material. After that, the first test was carried out at Mahle - using a hydropulsor.
In this case, the piston was taken by the hole for the piston pin and subjected to a load until destruction. The number of load changes exceeded the required value, and thus the test was passed. The second test was called the "boss pull-off test". In its course, the force that is necessary to tear off the piston bosses was determined. And in this case, the value was within the acceptable range, like cast pistons. Real load tests in the engine 9The 11 GT2 RS proved the uncompromising quality of the printed pistons – and their potential for improved power and economy.
High quality printed double jet nozzles
In order to supply this annular channel with oil, as well as to supply oil, as with serial pistons, to the bottom of the piston, another part was created on a 3D printer: a stainless steel double jet nozzle. "Manufacturing using conventional technology would have been too complicated due to the geometry," explains Porsche engineer Marco Klampfl. To create a twin-jet nozzle by conventional methods would require a complex procedure using soldering and milling. In addition, it would be impossible to use it in the engine. nine0003
So the engineers designed an S-shaped bifurcated oil passage that was additively fabricated from stainless steel powder. This part with a tubular base and a check valve was soldered to the piston cooling nozzle. "Doubts that the quality of the oil jet would suffer due to poor surface quality as a result of 3D printing were not confirmed," states Marco Klumpf. "On the contrary, comparative measurements showed that the quality of the jets was even higher due to functional integration." nine0003
A wide range of 3D printing applications at Porsche
Additive manufacturing opens up a wide range of opportunities for Porsche in new products, technologies and business areas. Product innovations include the use of lightweight designs and functional integration techniques, while new processes include faster development and flexible manufacturing. Among the new business areas, individualization, new offers for customers and the production of spare parts attract attention. This technology is of technical and economic interest to Porsche, especially in the production of special models and small series. In addition, additive technologies are ideal for producing structures that are designed and optimized using artificial intelligence. nine0003
Porsche already uses additive technologies in many areas and is actively working to improve them further. For example, since May, a 3D-printed bucket seat has been offered for the 911 and 718 used in motorsports. The central part of the seat, i.e. cushions and backrests, is partly 3D printed. In the future, customers will be able to choose from three levels of seat firmness (hard, medium, soft). The Porsche Classic division uses additive manufacturing to produce plastic, steel and light metal parts that were previously not available to order. For example, the Porsche 9 clutch release lever59, which is used as a spare part, is now 3D printed. Currently, about 20 parts for classic Porsche cars are produced using additive technologies. All manufactured parts are required to meet at least the quality standards of the original production period, but generally meet higher standards. The success of the project is regarded by Porsche as a confirmation of the correctness of the chosen path in the field of 3D printing. Due to the relatively high cost of manufacturing parts, additive technologies are currently used only for the manufacture of small batches of components that, under normal conditions, require the additional use of expensive tools. Since Porsche is constantly producing small series and special models, the company, according to Frank Ickinger, is thinking, for example, of mass-producing pistons for the entire special series of high-performance engines using the LMF method. However, it is in the field of production of highly loaded drive elements using additive technology that many questions remain to be answered. “Designing, manufacturing and finishing parts involve many new parameters and methods that are not available in the classical approach.
Being able to master new technologies with confidence is crucial to ensure consistently high quality,” emphasizes the development specialist. we still have a lot to do." nine0003
New designs, new manufacturing solutions and increased efficiency
In cooperation with Mahle and Trumpf, another part has been created - an additional charge air cooler that is integrated in the channel between the turbocharger and the intercooler. Thanks to the possibilities of 3D printing, the cooler has a significantly larger heat-absorbing area. This allows you to optimize flow dynamics and cooling. The result: the intake air becomes cooler, power and efficiency increase. nine0003
The potential of additive technologies is also being explored and evaluated in relation to electric drives. “Using a highly integrated electric drive, we can demonstrate not only the potential of the product itself, but also the development possibilities. The use of new design methods has doubled the rigidity of the drive and reduced the weight by about 10 percent. In addition, the integrated gearbox heat exchanger has significantly improved the performance of the thermal management system "The integration of 12 assemblies saves 30 screws, 12 seals and many other parts. This not only improves the layout, but also significantly reduces assembly costs. All these measures saved 20 minutes in production," explains Falk Heilfort from Drive Development. In addition, the use of copper for printing creates interesting ideas that open up new opportunities for creating electric motors. Also, the topic of cooling for pulsed inverters and electric machines was taken to a new level. nine0003
"For us developers, 3D printing has a number of advantages," adds Frank Eckinger. Since the parts are produced without the use of special equipment required for shaping, significant time can be saved during production, and this allows more options to be tested. As a result, prototypes can turn out to be even more cost-effective, since there are no costs for special equipment. By the way, the equipment itself can also be produced using additive technologies. An injection mold with an integrated cooling channel allows conventional production techniques to be optimized in terms of cycle times. 3D printing allows not only working with metal, but also producing plastic parts and complex sand cores, for example, for casting cylinder heads, crankcases and electric motor cases, and thus provide significant cooling benefits. nine0003
Despite the rapid development of additive technologies, there are still many restrictions on their way. On the one hand, this is the cost, which is justified only when producing a small number of parts, and on the other hand, this is the size of the parts. Indeed, large parts simply do not fit into the working chambers of modern printers. Further, it is necessary to expand the choice of materials - both plastic and metal. Finally, additive manufacturing must prove its economic viability for the (small) batch production of automobiles, both in terms of quality and reproducibility. nine0003
"But I am sure that within 10 years, additive manufacturing will become an integral part of the development and production of vehicles," says Frank Eckinger.
Innovative pistons from a 3D printer for increased power and efficiency
Collaboration: Porsche develops new 3D printing methods together with Mahle and Trumpf. nine0003
- add to media cartremove from media cart
- download
- open close nine0084
Stuttgart. 3D printing technology is already being used at Porsche in prototyping, in the production of spare parts for classic sports cars and in other areas. Now, the sports car manufacturer, together with Mahle and Trumpf, has entered a new phase in the application of additive manufacturing methods - for the first time, 3D-printed pistons have been successfully used in the high-performance engine of the top model 911 GT2 RS.
3D printing makes it possible to produce pistons with an optimized structure that takes into account the characteristics of the load. As a result, experimental pistons were 10 percent lighter than serial forged counterparts. In addition, they have an integrated closed channel in the bottom, which would be impossible to obtain using conventional production methods. “With the new, lighter pistons, we can increase the speed, reduce the thermal stress on the pistons and optimize the combustion process,” explains Frank Ickinger, from Porsche Pre-Development for Drive Systems. - Thus, the power of a 700-horsepower engine with two turbines can be increased by 30 hp. while at the same time being more economical. nine0003
Innovative 3D printed pistons for more power and efficiency 911 GT2 RS
Layering allows for new, improved designs
There are a number of different technologies used in 3D printing. All of them are based on the principle of building a part in layers without the need to use special tools or molds. This allows you to produce parts of almost any geometry. Information about the design is fed into the printer directly from the computer. In addition, additive technologies are ideal for producing structures that are designed and optimized using artificial intelligence. Pistons 9The 11 GT2 RSs were created using the so-called additive laser sintering (Laser Metall Fusion, LMF) method from high-purity metal powder. The laser beam goes along the contour of the part, heats the layer of powder and produces its sintering. Porsche is implementing the joint project in cooperation with its partners Mahle and Trumpf. The quality and efficiency of the obtained parts have been confirmed by the measurement technology specialists from Zeiss.
Metal laser melting process
Wide range of applications and new potentials of 3D printing at Porsche
Porsche uses additive manufacturing methods in various areas. For example, since May, a 3D-printed bucket seat has been offered for the 911 and 718 model ranges. In the future, customers will be able to choose from three levels of seat firmness (hard, medium, soft). In addition, Porsche Classic uses additive manufacturing to produce plastic, steel and light metal parts that were not previously available to order. For example, the Porsche 9 clutch release lever59 is being 3D printed today. Currently, about 20 parts for classic Porsche cars are produced using additive technologies. This technology is of technical and economic interest to Porsche in the production of special models and small series, as well as in motorsport. In this way, 3D printing opens up a wide range of new product and technology opportunities for Porsche to offer unique, customized solutions and improve customer satisfaction. nine0003
Photos are available from the Porsche Newsroom (https://newsroom.porsche.com/en.html) and from the Porsche press database (https://press.ru.porsche.com). Learn more about 3D printing at https://media.porsche.com/mediakit/porsche-innovationen/de.
Director of Public Relations and Press
Oksana Khartonyuk
E-mail: [email protected]
- add to media cartremove from media cart nine0084
- download
Related content
Porsche sets a new lap record of 6:43.
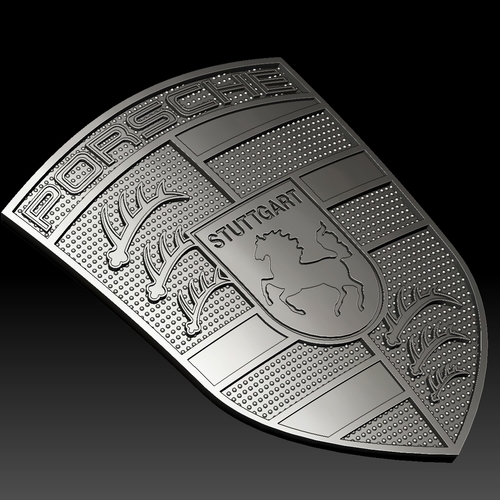
On the 20.8 km Nürburgring Nordschleife, Porsche set a new lap record for a production road-legal sports car: The 911 GT2 RS with the Manthey Performance Package completed the lap in 6:43,300 minutes.
Porsche Newsroom is Porsche's official information service for journalists, bloggers and online communities. nine0003
Official website of Porsche AG: www.porsche.com
© 2022 Dr. Ing. h.c. F. Porsche AG. Legal notice. Personal data processing policy.
* Data determined using the Euro 5 method (715/2007/EC and 692/2008/EC) in the NEFZ (European driving cycle). The information does not refer to an individual vehicle and is not part of the offer, but only serves to compare different types of vehicles. For more information, please contact your authorized Porsche dealer. nine0003
Terms of use Porsche News
1. All information contained in the Porsche News database, including but not limited to texts, images, audio and video documents, is protected by copyright or other laws protecting intellectual property. This information is provided for use by journalists as a source for their own publications in the media and is not intended for commercial use, in particular for advertising purposes. Transfer of texts, images, audio and video materials to unauthorized third parties is prohibited. nine0003
2. All logos and trademarks mentioned in the Porsche News database are the property of Dr. Eng. x.s. F. Porsche Joint Stock Company (hereinafter Porsche AG), unless otherwise stated.
3. All contents of the Porsche News database have been compiled and edited with care. However, the information may contain discrepancies and inaccuracies. Porsche AG accepts no liability for the results obtained from the use of the information provided, in particular with regard to accuracy, currency and completeness.