Asu 3d printing lab
3D Print Submission - 3D Print and Laser Cutter Lab
To submit a project for printing, please follow these steps:
- Every file should be submitted with a separate form
- One part per file – multiple parts on a file cannot be manipulated independently
- Please provide infill percentage desired
- Please make sure measurements are correct and provided.
Go to the 3D Print Submission form, including all the details you prepared in Step 1.
PLEASE DOUBLE CHECK THAT THE FORM IS FILLED OUT CORRECTLY, WHAT IS SUBMITTED IS WHAT WILL BE PRINTED.
3D print submission form
When you receive an email stating your project is ready, feel free to stop by any time during our business hours.
Additional Information
Print Timeline: 3-5 business days
Please expect at least 1 business day for a reply to your email, and at minimum 2-3 business days for printing, depending on the queue.
Finals Week Print Timeline: 2+ weeks
3D printing is in huge demand during finals and the print queue often fills up two weeks in advance. Please submit your print request at least 10 days before it’s due.
Filament / Material
- FSE Students – MakerBot filament is available to FSE students for engineering class assignments. Please fill out a Print Submission Form with details about your class and your instructors name for approval. FSE students supplying their own 1.75mm PLA filament for personal projects can do so by checking “yes ” to supplying your own filament on the submission form.
- NON-FSE Students – We’re not a recharge center and you can request to have a lab assistant print your model using your own personal 1.75mm PLA material. Please fill out a Print Submission Form and check “yes” to using your own filament on the submission form.
Policies, terms and conditions
- All files MUST be ready to print; any last-minute changes or edits will require the student to complete these changes on their own, then return when changes are completed.
Lab assistants will not make any changes to your files.
- Submit files in .STL format. Lab Assistants will not convert files for students.
- Each individual piece of a model must be in its own file. For example, if a model consists of six parts then we should receive six files from the student. The only exception are duplicates. Example (needing 3 each of the same exact piece).
- The 3D print lab will print the submitted project after receiving approval from an FSE instructor or by the student for their personal project.
- Projects will be printed on the first available 3D printer in the lab.
- Reprints are not permitted if the project breaks due to bad design or physics; we will reprint the project after you made corrections to the design.
- Depending on the print queue, projects may take 2-10 business days before completed. We will provide an estimate of how long it will take to complete your project but there is no guarantee whether or not it will be completed by that time.
Be prepared for possible delays in the printing process.
- Some builds may require the student to split the part into several pieces and piece it together after being printed. Be prepared to assemble your project.
- Final print may have support material and may require clean up. FSE 3D print lab is not responsible for removing support material. You can remove support material with sand paper, wire cutters or other hand tools. FSE 3D print lab does not loan hand tools to remove support material.
- No one has permission to use the 3D printer to create material that is:
- Prohibited by local, state or federal law.
- Unsafe, harmful, dangerous or poses an immediate threat to the well-being of others.
- Obscene or otherwise inappropriate for University environment.
- In violation of another’s intellectual property rights. For example, the printer is not be used to reproduce material subject to trademark, patent or copyright protection.
- The lab reserves the right to refuse 3D print request.
- Only designated FSE student workers and volunteers will have hands-on access to the 3D printer.
3D Printing - 3D Print and Laser Cutter Lab
3D Printing
We are available for use by all Fulton Engineering students, clubs, and research groups. We supply the filament if your submission is for a class related project. Please fill out a Print Submission Form with details about your class and instructor. Personal projects, research projects and club projects are permitted however you will have to provide your own filament for the project. When filling out a Print Submission Form you will be able to identify whether or not this is a FSE class related project or a personal one.
Due to a high volume of prints in our queue, we are only accepting a maximum 5 submissions per person at a time. If you have more than 5 projects you wish to print, please wait until you receive the pick-up emails before you submit the next 5. Please drop off filament after you have submitted your projects through the online form.
Processing Times
On average our processing time is at minimum 5 business days from when we receive your print request. However, this varies greatly depending on the size of your project and the current length of the print queue. Please contact us for a more accurate timeframe.
- Print requests from students for a class project take priority (i.e. FSE100)
- 3D printing is in huge demand during finals and the print queue often fills up two weeks in advance. Please submit your print request at least 10 days before it’s due.
- Please allow at least one day for an email response.
Filament
We only provide filament for 3D prints that are required for FSE class projects. If your print request is for a research project, club, or a personal project outside of class we require you to provide your own filament. Please bring in your spool of filament after you have submitted your print request through the online form. If you have a particularly large print, you must bring in multiple rolls to make sure you have enough filament to complete your project(s). Please see the chart below to determine what diameter filament you need to provide:
Prusa 1.75mm Filament | Ultimaker S5 2.85mm Filament | Creality CR-10 S5 1.75mm Filament | |
---|---|---|---|
Soluble Supports | X | ||
Breakaway Supports | X | X | X |
PLA Filament | X | X | X |
ASA Filament | X | ||
TPU Filament | X | ||
PETG Filament | X | X | |
Nylon X Filament | X | ||
Nylon Filament | X | X | |
Max Build Plate Size | 250 x 210 x 210 mm | 330 x 240 x 300 mm | 500 x 500 x 500 mm |
**
We recommend purchasing filament from these brands:
MatterHackers
HatchBox
There are other brands available, however we have had the best success with the brands listed above. If you choose to bring in a brand of filament different from the ones listed, please be aware that we may have to reject the filament if it does not work well on our printers to prevent damage to them.
Please be sure to bring in the correct diameter filament for each printer:
- Our Ultimaker S5 printers require 2.85mm filament
- Our Prusa I3 MK3s+ printers require 1.75mm filament
- Our Stratasys Mojo uses only proprietary ABS filament
The following link provides a good rundown of the most commonly used types of filament and their best uses:
Types of 3D Printing Materials
ALL PRINT SUBMISSIONS ARE SUBJECT TO REJECTION.
Examples: boxes, flat sheets, shafts, and tiny threading.
Please contact us with any questions
12 available
Build Volume: 25 x 21 x 21cm (9. 84 x 8.3 x 8.3 in)
Material: PLA, PETG, TPU, & Nylon
1 available
Build Volume: 5.0 x 5.0 x 5.0 in
Material: ABS Black
Layer Thickness: .17 mm (.007 in)
- Every file should be submitted with a separate form
- One part per file – multiple parts on a file cannot be manipulated independently
- Please provide infill percentage desired
- Please make sure measurements are correct and provided.
Go to the 3D Print Submission form, including all the details you prepared in Step 1.
PLEASE DOUBLE CHECK THAT THE FORM IS FILLED OUT CORRECTLY, WHAT IS SUBMITTED IS WHAT WILL BE PRINTED.
3D Print Submission Form
If providing your own filament, please bring it in now.
When you receive an email stating your project is ready, feel free to stop by any time during our business hours.
Policies, terms and conditions
- All files MUST be ready to print; any last-minute changes or edits will require the student to complete these changes on their own, then return when changes are completed. Lab assistants will not make any changes to your files.
- Submit files in .STL format. Lab Assistants will not convert files for students.
- Each individual piece of a model must be in its own file. For example, if a model consists of six parts then we should receive six files from the student. The only exception are duplicates. Example (needing 3 each of the same exact piece).
- The 3D print lab will print the submitted project after receiving approval from an FSE instructor or by the student for their personal project.
- Projects will be printed on the first available 3D printer in the lab.
- Reprints are not permitted if the project breaks due to bad design or physics; we will reprint the project after you made corrections to the design.
- Depending on the print queue, projects may take 2-10 business days before completed. We will provide an estimate of how long it will take to complete your project but there is no guarantee whether or not it will be completed by that time. Be prepared for possible delays in the printing process.
- Some builds may require the student to split the part into several pieces and piece it together after being printed. Be prepared to assemble your project.
- Final print may have support material and may require clean up. FSE 3D print lab is not responsible for removing support material. You can remove support material with sand paper, wire cutters or other hand tools. FSE 3D print lab does not loan hand tools to remove support material.
- No one has permission to use the 3D printer to create material that is:
- Prohibited by local, state or federal law.
- Unsafe, harmful, dangerous or poses an immediate threat to the well-being of others.
- Obscene or otherwise inappropriate for University environment.
- In violation of another’s intellectual property rights. For example, the printer is not be used to reproduce material subject to trademark, patent or copyright protection.
- The lab reserves the right to refuse 3D print request.
- Only designated FSE student workers and volunteers will have hands-on access to the 3D printer.
3D printing laboratory - All about plastics - education, technology, perspectives
Prototyping and modeling using 3D printers has recently become more and more widespread. This is due not only to the development and cheapening of equipment for creating three-dimensional models, the emergence of new polymeric materials for three-dimensional printing, but also the emergence of the need for such modeling for medical products, aircraft parts, instrumentation, automotive and aircraft manufacturing, as well as souvenirs. and other areas. The use of polymeric materials for structural purposes for prototyping made it possible to produce not only models, but also small batches of technical products. nine0003
According to the recent study “3D Printing Market (2013-2020)” published by Markets and Markets (“M&M”), between 2013 and 2020, the annual growth of the 3D printing market will be 23%, resulting in will grow to 8.4 billion US dollars by 2020 (http://www.orgprint.com/wiki/3d-pechat/obzor-tehnologij-3D-pechati).
3D printing is a technology for creating three-dimensional objects from a digital sample (CAD) by layer-by-layer application of additive materials. 3D printing methods include stereolithography (SLA), powder laser sintering (SLS), electron beam melting (EBM), layer-by-layer printing with molten polymer thread (FDM), formation of three-dimensional models from layer-by-layer sheet material (LOM) and others. nine0003
Initially, 3D printing was used exclusively for prototyping objects, but recently a radical step has been taken towards production. Automotive, aerospace, medical, and consumer products are among the industries that are actively embracing 3D printing. According to M&M, 3D printing in medicine and aerospace will grow exponentially in the near future. 3D printing has significant growth potential, it is indispensable where piece production of personalized products is needed. nine0003
This article touches upon some aspects of 3D printing, which is carried out by layer-by-layer printing with a melted polymer thread (rod).
Layer-by-layer printing with a molten polymer thread , also known as Fused Deposition Modeling or simply FDM, is used to obtain single products that are close in their functional characteristics to serial products, as well as for the manufacture of investment molds for casting metals.
The main polymer materials used in FDM technology in Russia are ABS plastic, PLA (polylactide), to a lesser extent polyamide (PA-12 or PA-11), TPU, PET-G and a number of other polymers. Almost all polymeric materials are imported. nine0003
High impact polystyrene (HIPS) is used as support polymers. This material is used for printing ABS plastic, PMMA, PET-G. Polyvinyl alcohol PVA (PVOH, PVA or PVAL) is also used as a support polymer, however, due to the water solubility of this polymer, it is more difficult to obtain a thread from it, modification of the standard technology is required.
At the Interplastica-2018 exhibition, work was announced on the synthesis of special grades of structural polymer materials for 3D printers at the Kabardino-Balkarian State University (PSU, PFS, etc.). In the report of KNRTU (Kazan), the topic of using PP filament for 3D printing was mentioned, which is not surprising, since in the Republic of Tatarstan a wide range of PP grades is produced by Nizhnekamskneftekhim PJSC. The problem with polyolefins in printing is associated with poor adhesion to the 3D printer substrate and high shrinkage when cooled. nine0003
FDM printing technology is as follows: a polymer thread is fed into a heated head with a controlled temperature, in the head it is heated to a melt state and the resulting thermoplastic modeling material is fed with high precision in thin layers onto the working surface of a 3D printer. The layers are applied on top of each other, joined together and cooled, gradually forming the finished product.
The diameter of the nozzle through which a thread with a diameter of 3 or more often 1.75 mm is fed is 0.3-0.4 mm in the first case, and 0.1-0.3 mm in the second case. Therefore, the requirements for a polymer thread should be quite stringent in terms of sizing (thickness variation), stability of rheological properties (melt flow), melt purity (presence of impurities or contaminants). nine0003
1 shows the scheme of printing polymer thread FDM
1. Flow chart of 3D printing by FDM polymer filament printing.
The production of thread (rod) for FDM technology is carried out on extrusion plants for extruding rod, including a dryer, an extruder, usually a single-strand extrusion head, a calibrator (if necessary), a cooling bath, a gauge for the thickness (diameter) of the thread, 2 (rarely 4 -x positional) bar winder on the coil. There is a lot of information on the Internet about homemade filament extruders, as a rule, of low productivity and low quality filament. However, the production of thread must be carried out on specialized extrusion lines. nine0003
A diagram of such a line is shown in fig. 2.
Fig. 2. Extrusion plant for the production of polymer thread
I would like to note that for the wide development of FDM technology in our country, it is necessary to clearly define the characteristics of polymer materials that determine the possibility of their use in 3D printing technology with a polymer thread, as well as to synthesize or modify industrial polymers in order to obtaining material with the required characteristics. In particular, both thermophysical properties (for example, the thermal diffusivity coefficient, which determines the cooling rate of the material), and rheological properties (fluidity at different temperatures), as well as temperature parameters of the weldability of layers depending on the properties of the feedstock, etc., should be taken into account. nine0003
3D printing in chemistry - Ananikov Laboratory AnanikovLab.
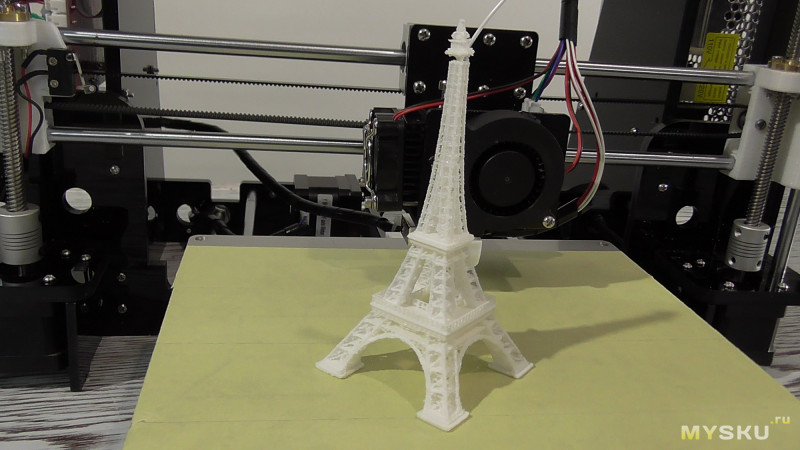
The cheapest, simplest, and most common 3D printing method is Fused Deposition Modeling (FDM). In the vast majority of cases, this method uses the direction of the polymer: the polymer in the form of a thread with a diameter of about 2 mm, wound on a spool, is fed into a small extruder, where it melts and is extruded (pressed) through the nozzle already in the form of a thin thread, from which the layers of the future part are formed. . The nozzle opening diameter and layer thickness together determine the resolution of an FDM printer. The design of such a 3D printer is relatively simple, so these devices are produced by many companies and their cost is low compared to 3D printers designed for printing by other additive methods. A significant advantage of FDM technology is the low cost of consumables, which are various polymers: acrylonitrile butadiene styrene (ABS), biodegradable polylactide (PLA), polyethylene terephthalate (PET), polypropylene (PP), nylon, polycarbonate, etc. nine0003
The process of 3D printing of chemical equipment elements from chemically resistant plastic using an FDM 3D printer.
The polymer filament deposition method has an average spatial resolution (usually 0.1 - 0.2 mm) and makes it possible to manufacture parts of various shapes and levels of complexity (Fig. 1). The enormous possibilities of 3D printing make it a very promising technology in education and science. Piece-by-piece production of unique laboratory equipment, visual aids (Fig. 2), mock-ups, models (including working mechanisms with moving parts) - all this is feasible even with the widely available FDM printing method. nine0003
Fig. 1. Attached spiral channel made from two different resins in a single 3D print run with two extruders running in sync. Finished products and a 3D model are shown.
Fig. 2. Ball-and-stick model of a molecule made by FDM printing from PLA plastic. To obtain a higher quality, the model was made in parts with subsequent assembly.
The high chemical resistance of some polymers (such as polypropylene, nylon, polyethylene terephthalate) in combination with the FDM printing method is well suited for the manufacture of small chemical laboratory equipment and chemical-technological laboratory installations. However, the real potential of 3D printing is not realized in the manufacture of standard laboratory equipment that can be bought, but in the creation of special products, such as chemical reactors, mixers and other elements of chemical installations, developed in-house for unique experiments. nine0003
The layering technology is mature enough to reproduce even the fine details of small chemical equipment. For example, Figure 3 shows a photograph of a mixer with three inlets and one outlet. The diameter of the internal channels of this mixer is only 2 mm. The conical notches on the inlet pipes are clearly visible, and the height of these notches is 0.5 mm. To increase the mixing efficiency, a miniature helical fin is made inside the central outlet channel. Of course, this is not yet the same thing as shoeing a flea, but everything is moving towards this. The manufacturing time of the mixer was 30 minutes. Try to make such a micro-mixer in half an hour using conventional methods! nine0003
Fig. 3. Mixer-tee in the working chamber of a 3D printer, made of polyethylene terephthalate using the FDM method.
Fig. 4. Chemical microreactor with a complex labyrinth channel inside, made of PET by FDM printing. The individual parts of the reactor and the assembly are shown.
The ability to manufacture products with a complex internal structure, as already noted, is one of the main advantages of 3D printing. This possibility is well illustrated in Figure 4, which shows a complete chemical reactor the size of a matchbox. Like the "adult" chemical reactor, this "baby" has a shell, a lid connected by bolts to the shell, and a gasket to seal the working space. It is enough to look under the lid to see the complexity of the inner world of this worker of science: a labyrinth channel is organized inside the reactor, forcing the reaction mixture entering the shell through the side pipe to move along a complex trajectory, so that the reaction time is optimal to obtain the desired products. There are small baffles at the bottom of the labyrinth channel to keep the finely dispersed catalyst from being washed out quickly. The reaction products leave the reactor through the lower branch pipe. nine0003
Microreactors can consist of any number of elements, each of which is individually manufactured using 3D printing (Fig. 5). Individual elements (Fig. 6) are eventually combined into workable chemical plants (Fig. 7).
Fig. 5. Microreactor, consisting of a shell, a lid, a catalytic cartridge and a replaceable nozzle. The individual parts of the reactor, the reactor assembly and a three-dimensional model of the assembly are shown.
nine0003
Fig. 6. Mixer and zigzag microreactor made of PET.
Fig. 7. Laboratory chemical plant assembled from a microreactor and mixer, created by FDM printing methods.
3D printing can significantly speed up experimental chemical research, because it makes it possible to manufacture even complex multi-component chemical equipment right in the laboratory without significant material costs.