Arkema 3d printing
3D Printing Solutions by Arkema
A market leading product portfolioLiquid
resinsRadiation curing
3D printerLearn more
Thermoplastic
powdersPower bed fusion
Learn more
Thermoplastic
pelletsFilament extrusion
3D printing filament extrusionLearn more
A leading portfolio of solutions for each of the major 3D printing technologiesArkema offers its customers the most extensive range of materials dedicated to 3D printing. Led by flagship brands such as Sartomer’s N3xtDimension® resins, Rilsan® bio-based polyamides, Kynar® fluoropolymers, and Kepstan® PEKK resins, Arkema’s product offering spans all major additive manufacturing processes – UV curing, powder bed fusion and extrusion.
Arkema can respond effectively to a broad list of specifications for mechanical and thermal resistance, flexibility, transparency, color and durability.
White paper: Expanding Industrial Applications of Additive Manufacturing with Advanced Material Solutions- Why additive manufacturing is revolutionary for industries?
- What are the highest performing materials for additive manufacturing in industrial application?
- How to democratize additive manufacturing?
The high-performance materials for 3D printing are evolving in tandem with advancement of additive-manufacturing technology. The material research and development in additive manufacturing is rooted in the understanding of the past practices and bridging the gap between traditional and emerging technologies.
dowload white paper
A better use of material propertiesThe promises of 3D printing over traditional manufacturing techniques are well known: faster development cycle, freedom of design and personalization, lighter parts, less waste and less assembly, decentralized manufacturing… In other words, 3D printing helps manufacturers use less, longer and smarter.
Use lessHow to use less material and get lighter parts through a combination of modeling and material innovation.
Use longerHow to use material longer through better resistance to impact, by introducing nanostructuration technology to engineer a new generation of photocurable resins.
How to combine continuous fiber technology and filament fabrication to further push the frontiers of lightweighting.
Save time during design phaseThe ability to reliably simulate part behavior is key in predicting an optimal design and making the most of 3D printing. We can recommend to our customers the best trade off between cost and properties for each part, and are dedicated to being at the forefront of simulation tools.
LEARN MORE
Collaborative developmentWe partner with our customers to develop custom materials and resins for their unique end-use applications. With our dedicated team of scientists and our three global centers of excellence, for each of the printing technologies, we have enabled the success for our customers in numerous markets.
lean more
Global capability, local expertiseWe are ready to support our partners globally. Our teams are actively investing in all three regions – Europe, Asia, and North America – to serve you better. Our worldwide presence enables us to provide quick, local expertise from customized solution design to implementation
Learn more
Case study - 3D printing
3D printed and tailor-made: orthopedic insoles made with advanced bio-circular polyamide 11
read the study
Our specific offering for other industries:
3D printing – Arkema.com
Thanks to its expertise in polyamide powders, acrylate resins and high performance polymers, Arkema grows from strength to strength in 3D printing.
The global 3D printing market (also known as additive manufacturing) reached $4.7 billion in 2015. The market is expected to grow by 20% per year until 2020. Professional and industrial applications account for 85% of the total market.
3D printing offers total freedom of design for complex parts and eliminates the need for molds, which are often time consuming and expensive to develop.
The resulting flexibility and time-saving also mean significant financial savings for design offices and industrial companies when it comes to producing prototypes and limited runs. 3D printing technology could totally revolutionize our methods of production and our consumer habits.
Chemical World TourAs part of the 5th season of the Chemical World Tour, Léa, a student journalist, and Benoit, an engineering student, take us behind the scenes of 3D printing.
Arkema's materials for
laser sinteringArkema is developing high performance materials for the main 3D printing technologies currently being used by professionals
The Group produces two ranges of fine polyamide powders that offer excellent mechanical properties for Laser Sintering, a manufacturing technique that uses a laser beam to fuse together thermoplastic powders layer by layer:
- Orgasol® Invent Smooth provides a smooth high quality finish, excellent detail and efficient recycling of leftover powder.
- Rilsan® Invent Natural, is 100% sustainably biosourced and can be used to create parts with unmatched mechanical properties.
Arkema is also working to develop a range of specific grade of Kepstan® PEKK powders, -an advanced performance polymer- that can be used in laser sintering processes to make parts exhibiting extreme toughness.
Prototypes, limited runs and spare parts are increasingly being produced using Laser sintering techniques in the medical sector (dental implants, orthotic devices, and surgical guides) and in industry (aerospace, automotive, sports, and equipment). Smooth finish, complex and mechanically resilient components: laser sintering is opening the way to unlimited creativity!
Sartomer's innovative resins for 3D printing
In November 2016, Sartomer launched N3xtDimensionTM, a new range of photocure 3D printing materials that yields ultra-high-definition prototypes and parts with superior mechanical properties. N3xtDimensionTM materials may take 3D printing from prototyping to mass production. Welcome to the N3xtDimensionTM!
We're the only supplier that can respond effectively to a broad list of specifications for mechanical and thermal resistance, flexibility, transparency, color and durability.
Sumeet Jain, Arkema’s Global Business Director for 3D Printing Solutions
Complex object printed in stereolithography
Complex object printed in stereolithography
Complex object printed in stereolithography
More information aboutOther Arkema's lightweight materials:
Ultra high performance thermoplastics for transportation
Learn more on our thermoplastics renault-twizy-crop800x601.pngThermoplastic composites, a genuine alternative to thermoset composites
Learn more on our thermoplastic composites ark9759_2030-crop3201x2402.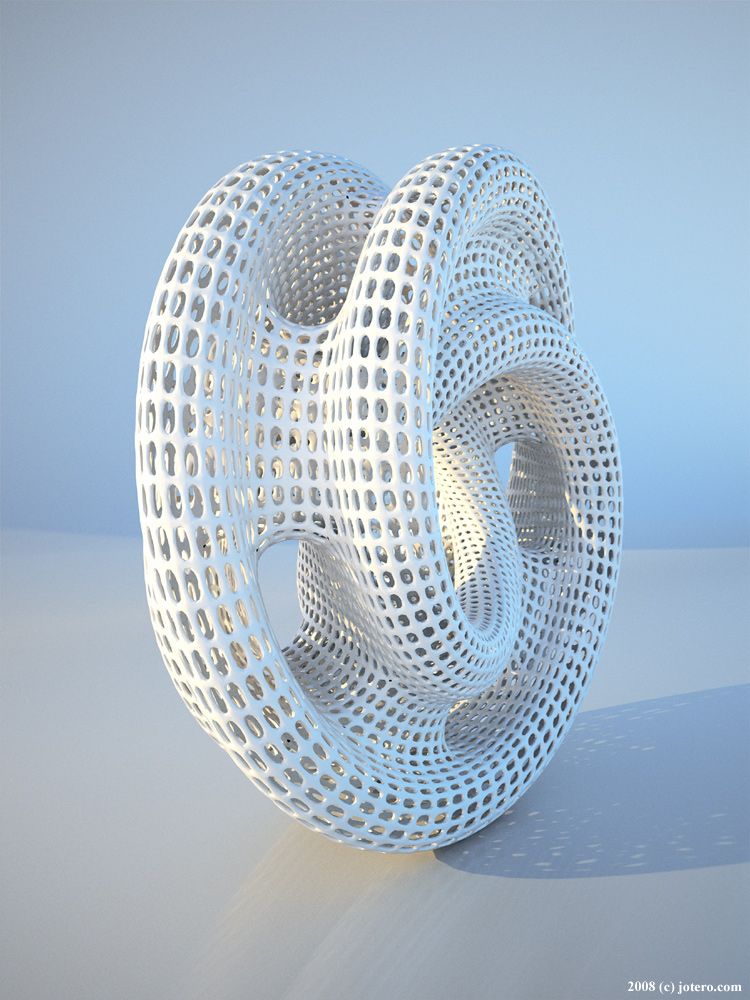
Our carbon nanotubes and sturdy copolymers
Learn more on our nanomaterials nanostrength-crop1200x900.jpgEssentium released a filament of tight engineering plastic PEKK
News
Sign up for
Subscribe
I do not want
2
Texas developer and manufacturer of 3D printers, added to a company assortment of refinery of the TURMEN PEKK).
Like the better known polyetheretherketone (PEEK, PEEK), PEEK has high strength, dimensional stability, heat, chemical and fire resistance. The main advantage over PEEK is the lower degree of crystallization. Both polymers fall into the category of semi-crystalline, but PECK is closer in properties to amorphous polymers. In practice, this means that PECK is less prone to deformation due to heat shrinkage.
Due to the high glass transition temperature, PECC also requires high temperature additive systems with extrusion temperatures in the range of 340-400°C. In terms of chemical resistance, PECC outperforms another popular engineering thermoplastic in the industrial environment - polyesterimide, best known under the Ultem brand of the Saudi chemical company SABIC.
The Essentium PEKK filament is made from the raw materials of the French chemical company Arkema - Kepstan 6002 resin. In parallel with the new filament, Essentium also offers a new hardware development - a high-temperature FDM 3D printer HSE 280i HT with "real" IDEX kinematics. Unlike other additive systems with IDEX, this machine uses independent positioning of the extruders in both the X and Y directions. This scheme allows you to print not only two identical or mirror products at the same time, but also parts of completely different shapes. To work with refractory plastics, the system is equipped with high-temperature hot ends and a heat chamber with active background temperature control.
“Industries like aerospace and automotive are looking to additive technologies to reduce production times without sacrificing quality. Combining a range of high performance materials such as PEKK with the capabilities of the HSE 280i, our open additive ecosystem provides industry players with a unique opportunity to quickly produce complex parts for extreme operating conditions. These additive manufacturing innovations are a game-changer for manufacturers looking to improve efficiency and reduce time to market,” said Essentium Vice President Brandon Sweeney.
Detailed information about Essentium's offers is available on the official website.
Do you have interesting news? Share your developments with us, and we will tell the whole world about them! We are waiting for your ideas at [email protected].
PEKK PECK Essentium
Follow the author
Subscribe
Don't want
2
More interesting articles
5
Subscribe to the author
Subscribe
Don't want
Researchers from Peter the Great St. Petersburg Polytechnic University have developed an algorithm...
Read more
5
Subscribe to the author
Subscribe
Don't want to
Specialists of Skat 3D Prototyping and 3D Printing Center launched additive manufacturing of orthopedic...
Read more
82
Subscribe to the author
Subscribe
Don't want
Collaboration 3D
We are pleased to present you our joint development with Speci...
Read more
BCN3D Introduces Viscous Lithography Manufacturing (VLM)™ New 3D Printing Technology
• BCN3D's new VLM technology aims to unlock manufacturing autonomy, where companies must have the tools to develop and manufacture their own products and have full control over the additive manufacturing (AM) lifecycle.
• Viscous Lithography Manufacturing (VLM)™ is the first 3D printing technology that simultaneously delivers superior part quality, high production capacity, and affordable, friction-free work.
• Specialty materials company Arkema, with which BCN3D has entered into a joint development agreement, claims VLM paves the way for thermosetting resins to further advance mass production and production of functional parts.
• Innovators will be able to unlock the potential of VLM with real 3D printed parts as part of the VLM Technology Implementation Program at a dedicated application technology center run by AM experts active in Saint Gobain and Prodrive demonstrate the benefits of this technology.
Yesterday, March 2, 2022, BCN3D announced a new 3D printing technology that will evolve alongside FDM solutions: Viscous Lithography Manufacturing (VLM)™. This never-before-seen technology was developed specifically to realize BCN3D's concept of creating autonomous production, where all manufacturers can fully control every step of the production process using AM solutions. VLM technology is a breakthrough that is the result of three years of R&D work by the BCN3D development team as a way to overcome obstacles such as initial investment in money or space, non-compliance of mechanical properties with standards, or inability to large-scale production. It is this fresh look at using high viscosity resins to improve mechanical properties, combined with a huge leap in performance and availability, that ultimately fits the bill for unlocking manufacturing autonomy.
"If 3D printing is to be the future of manufacturing and lead us to local manufacturing, personalization, supply chain control and sustainability, then all industry players must move in this direction. We at BCN3D believe that today is the first step in achieve this goal through the new Viscous Lithography Manufacturing (VLM) technology. We want to show 3D printing in a new light so that it becomes the core of production" - Xavier M. Faneka, BCN3D CEO.
High viscosity resins for superior printed part performance
VLM is a proprietary lithography-based 3D printing process in which thin layers of highly viscous resins are applied to a transparent transfer film, allowing high performance parts to be produced quickly and inexpensively. What sets VLM apart from other resin technologies on the market is its ability to process resins with viscosities up to 50 times the industry standard.
The mechanical system allows the resin to be laminated on both sides of the film, allowing strategies to be applied to speed up print times or even to combine different resins for multi-material parts and easily removable support structures.
Without the strict limits of low viscosity, chemical companies have the freedom to formulate as a whole new set of ingredients and modifiers can be added to the resin to achieve the desired effect on thermal and mechanical properties. VLM processes resins that provide 3x more impact resistance for tough materials and a 200% increase in tensile strength compared to industry standard formulations.
Specialty materials company Arkema has participated in this process by entering into a joint development agreement (JDA), in which the two companies jointly develop new materials that use VLM features to achieve properties not achievable in other 3D printing processes resin based. As a key global player in the 3D printing industry and a pioneer in the development of high performance photocurable resins, Arkema has used decades of experience to provide the highest quality VLM resins.
"With VLM's proven ability to handle high viscosity resins, we see great promise in developing new building blocks and creating revolutionary formulations to meet application requirements that have not yet been achieved with existing photocuring technologies" , - Hélène Egret, European 3D Market Manager Arkema company.
BCN3D also partnered with Prodrive, a world-renowned motorsports and technology company that was one of the world's first pilots of VLM technology. They were assembling VLM-produced end parts mounted directly on off-road vehicles.
"VLM technology seemingly combines all the best features of various additive manufacturing technologies and even offers some unique advantages. For Prodrive, materials are the key to creating durable end-use parts. VLM allows us to continue to use engineered materials, we know and love, but instead with much finer resolution in all three directions, and the material is much more uniform, making the finished parts much more like traditional injection molded parts" . - Callum Harper, Prodrive Design Engineer
Highest performance and availability
By using a UV light source and an LCD screen, VLM ensures a constant print time for each layer, whether we are printing one or 100 parts at a time. What's more, since this method isn't limited by vat sizes, tricky temperatures, or tricky components, all that's needed to scale up is a larger LCD screen. This combination of fast build times and high surface area makes VLM the most productive additive manufacturing solution on the market.
BCN3D's collaboration with automotive glass manufacturer Saint Gobain illustrates these benefits perfectly, where 7,000 positioners were produced in 7 days using VLM technology, at a cost of 0. 79 euros per piece and a subsequent annual saving of 70,000 euros.
“VLM technology has allowed us to see significant improvements in the future. Our main goal is to reduce our dependence on external mechanization suppliers and do it in-house with technologies like VLM. This is what would give us the possibility of industrial autonomy.0035 . – Alberto Rodriguez Fernandez, world class production manager at Saint Gobain.
Uninterrupted work accessible to all
It's undeniable that 3D printing has evolved from a rapid prototyping tool into a clear trend in manufacturing - all that's been missing is an affordable solution to cover all corners of manufacturing, from small to medium businesses. Unlocking manufacturing autonomy with 3D printing should be available not only to Fortune 500 companies, but to every enterprise that designs and manufactures concepts or products in any industry.