Arburg freeformer 3d printer
Arburg Releases Larger and Softer 3D Printers ahead of Formnext 2022 - 3DPrint.com
Arburg, the German family-owned injection molding giant, has been playing in the 3D printing space for a number of years now. In addition to manufacturing its Freeformer pellet printers that are built like a tank, it also acquired German RepRap and transmogrified it into the innovatiQ line, a series of gantry-based material extrusion printers. Previously, Arburg demonstrated that it was serious about 3D printing by opening a center in Shanghai and showcasing fused deposition modeling (FDM) with PEEK.
Freemformer 3D Printer with 2.5X Build Volume
The company is now disclosing that it will display a new Freefomer system, as well as the latest innovatiQ 3D printer, at Formnext 2022. The Freeformer line relies on extruding pellets onto a moving motion table, creating parts with high quality material properties at with low material cost. Print times can be slow, however, and components do look a bit rougher than those made with other technologies. This is an industrial tool meant to print parts.
The Freeformer 300-3X
Now, Arburg is releasing its 750-3X printer, which has 2.5 times the build volume than the previous model at 330 x 230 x 230 mm. Meanwhile, the air flow and circulation are said to be kept stable in the system. The printer also has “optimised melt pressure generators for dosing and injecting ,which use servo motors from AMKmotion,” an Arburg firm. Furthermore, the company has enhanced the 3D printing of lattices by speeding that process up by 55 percent. This will considerably enlarge the capabilities of the Freeformer line.
The Freeformer 200-3X
Additionally, the company is offering the Freeformer 200-3X, a “soft” 3D printer that has a reduced price compared to its predecessor. This machine has optimized equipment for soft parts, including integrated material drying, necessary for processing soft materials. The company will also show off parts that combine soft and hard materials and high temperature parts. Traditionally, soft materials have been difficult to print using material extrusion. Furthermore, the company has a new innovatiQ TiQ2 printer, a filament based system for industrial applications.
Arburg at Formnext
At Formnext, Arburg will be in Hall 12.1 at Stand D61, about which Dr. Victor Roman, Managing Director of ARBURGadditive said, “As the world’s leading trade fair, Formnext is one of the most important trade fairs of all for us and our markets, That is why we will be there with a fittingly extensive presence.”
Last year, Arburg had a very extensive presence at Formnext, indeed. It’s nice to have a traditional injection molding firm take such an interest in our industry. Arburg has a deep experience with polymers and with melting thermoplastics. It also makes machines that really last a long time. The company also has an extensive roster of clients, with which it has had long relationships.
Arburg´s system architecture is quite novel and thus has hindered adoption so far. For particular geometries the firm has a very solid offering. By focusing on soft materials, it could come up with solid value propositions in that area. This can be done both on its Freeformers and on its innovatiQ systems, which include machines for use with traditional filament and others optimized for liquid dispensing. This allows these systems to print silicone, a potentially very lucrative market.
Through its focus on pellets, Arburg has shown us from the beginning that it is willing to forgo margins in order to fight itself into our sector and win market share. The company is also more than willing to see things from the customers´ perspective and realize that high filament costs will keep our industry in its infancy. That central idea really makes me grateful for Arburg´s continued development in 3D printing.
Subscribe to Our Email Newsletter
Stay up-to-date on all the latest news from the 3D printing industry and receive information and offers from third party vendors.
Tagged with: Arburg • fdm • formnext 2022 • Freeformer • Freeformer 750-3X • innovatiQ TiQ2 • new 3d printers • PEEK
Please enable JavaScript to view the comments powered by Disqus.
Arburg Introduces PEEK 3D Printing and In-Process Monitoring at RAPID + TCT - 3DPrint.com
RAPD+TCT 2022 is just around the corner and among the attendees is Arburg is ready to show off advances made to its Arburg Plastic Freeforming (APF) technology. At the event, the German leader in injection molding and 3D printing technology, will be displaying a standard Freeformer 300-3X alongside a specialty version of the system capable of processing high-temperature materials. Additionally, the company will be presenting its ProcessLog app, for tracking and documenting 3D printing jobs in detail.
The Advantages of APF
APF is distinguished using a piezoelectric screw to deposit individual droplets of polymer material at rates of up to 200 droplets per second with diameters of 0. 2 and 0.4mm. Because commercially accessible pellets are employed, the approach is amenable to a far broader range of materials that manufacturers are likely already familiar with and might be used for mass manufacturing. Because filaments are much more expensive than injection molding pellets, this dramatically cuts part costs.
At RAPID + TCT in Detroit, two Freeformer 300-3X machines will additively manufacture sophisticated functional parts. Image courtesy of Arburg.
Arburg has begun expanding both its presence in additive manufacturing (AM) and in North America. With the acquisition of German RepRap, it gained a series of industrial fused filament fabrication machines, as well as silicone deposition technology. Through a partnership with Würth Additive, it began distributing its products in North America.
High-Temperature 3D Printing
The firm’s attendance at North America’s largest AM trade show furthers Arburg’s marketing efforts in the region. In particular, the company will be showcasing the ability of the Freeformer 300-3X to reach 200° Celsius, allowing it to process high temperature materials, such as ULTEM and PEEK. ULTEM 9085, for instance, is a permanently flame-retardant, low-smoke material approved for aerospace applications. The Freeformer 300-3X can also 3D print biocompatible, resorbable, sterilizable and FDA-approved original materials.
A high-temperature Freeformer 300-3X can process PEE, into such items as individualized skull implants, including support material. Image courtesy of Arburg.
The system features optimized temperature management, including cooling necessary for proper printing. This is particularly important for the axis drives, ensuring the precise positioning of the print along the x, y and z axes. Altogether, the Freeformer is capable of printing parts that achieve 95 percent strength in the X- and Y-axes.
Moreover, the printer can be made suitable for clean room applications with only some minor tweaks. This makes it possible to 3D print implantable and biocompatible parts. At RAPID + TCT, the Freeformer will showcase these possibilities by processing a medically approved PEEK granulate.
Process Monitoring
Additionally, Arburg will present its ProcessLog app, which captures process and build job data and displays it in a clear, visual manner. This information is documented and traced on a per-part basis. The data can be viewed over the course of an entire build, including granular information related to material pressure, screw position, droplet frequency and discharge rate. By reliably documenting the printing process and production of each part, manufacturers can ensure traceability for products in safety-relevant applications. Additionally, multiple Freeformer machines can be networked together using an Industrial Internet of Things tool, such as the “arburgXworld” customer portal.
All Freeformers can be networked with the “arburgXworld” customer portal. The specially developed “ProcessLog” app allows a wide range of process and build job data for APF parts to be displayed in clear graphical form, documented, and traced on a part-specific basis. Image courtesy of Arburg.
Arburg at RAPID + TCT
Outside of high-temperature materials and the ProcessLog app, Arburg will demonstrate flexible materials, polypropylene parts, and hard and soft combinations at RAPID + TCT. Thanks to post-processing partner OTEC, the company will also showcase 3D printed parts with surface quality that match those made with injection molding through the use of vibratory finishing and barrel tumbling.
Arburg suggests that the North American market will benefit from access to local and remote service, process monitoring, as well support for customer orders and processing customer-specific materials. As the German company is already well-established in the industrial manufacturing space, it suggests that it applies its expertise across the entire value chain, in turn, ensuring industrial quality in AM from the start. To learn more, visit the Arburg website or see APF in person at Booth #2108 at RAPID + TCT.
Subscribe to Our Email Newsletter
Stay up-to-date on all the latest news from the 3D printing industry and receive information and offers from third party vendors.
Tagged with: Arburg • Arburg Plastic Freeforming • Freeformer • Freeformer 300-3X • injection molding • medical 3d printing • PEEK • RAPD+TCT 2022
Please enable JavaScript to view the comments powered by Disqus.
Industrial 3D printers Total Z
FDM and SLS 3D printers, drying and post-processing equipment
About company
FDM 3D printers
Industrial 3D printers Total Z PRO series
450-PRO 950-PRO
Total Z High Performance LPRO Series 3D Printers
1000-PRO-LL
Total Z G3 Series Desktop 3D Printers
250-G3 250-G3 (2X) XL250-G3(2X)
Total Z G5 Series Desktop 3D Printers
G5
SLS 3D printers Total Z
SLS-250
Portal systems for 3D printing with granules
Total Z AnyForm FGF
Total Z machines for drying and post-processing
Total Z D5Vacuum drying chambers
Help prepare plastic for printing. Remove moisture from hygroscopic materials. Reduce the risk of plastic "boiling", extruder breakage, deterioration of the surface quality of the product.
Watch →
Total Z MPC-310Acetone baths
Equipment for chemical post-processing of finished objects. Helps to achieve a glossy and smooth product surface.
Watch →
Total Z UB-450; 500; 650; 950; 1200;Ultrasonic baths
Machines for physical and chemical post-processing of models. Remove the supporting plastic from the surface of finished products. They clean the material in places inaccessible for manual processing.
See 5 models →
Our capabilities
The equipment complies with Russian and international standards
Consumables for printers and equipment are always in stock
We participate in R&D, cooperate with research institutes
We work with defense enterprises and government customers
Operational warranty service
Departure and training on the territory of the customer
Implemented projects by industry
Aviation industry and special products
Supply of an industrial 3D printer for the project of the MS-21 passenger aircraft of Irkut Corporation.
Supply of high-temperature 3D equipment for the laboratory of additive technologies of VIAM.
Supply of a 3D printer for printing with experimental materials for the production of the Central Institute of Aviation Motors.
Shipbuilding
Selection of samples of engineering plastic for the project of printing body elements for a shipyard.
Auto industry
Supply of equipment for 3D prototyping to the plant of the AvtoVAZ group.
Rocket and space
Supply of the first production equipment for 3D printing to the Center for Additive Technologies of JSC RCC Progress.
Foundry
Fabrication of a matrix using FDM 3D printing for the production of piece metal parts that have been discontinued or to replace parts with a long delivery time.
Education
Production of a desktop 3D printer for schoolchildren and students in collaboration with a team of developers of teaching materials for classrooms.
Electronics
Implementation of 3D equipment at the Simvol East Kazakhstan region.
Prototyping of lighting equipment for the Pyaterochka grocery store chain.
Agroprom
Complex equipping of the research agro-engineering center with equipment.
Aviation industry and special products
Supply of an industrial 3D printer for the project of the MS-21 passenger aircraft of Irkut Corporation.
Supply of high-temperature 3D equipment for the laboratory of additive technologies of VIAM.
Supply of a 3D printer for printing with experimental materials for the production of the Central Institute of Aviation Motors.
Shipbuilding
Selection of samples of engineering plastic for the project of printing body elements for a shipyard.
Auto industry
Supply of equipment for 3D prototyping to the plant of the AvtoVAZ group.
Rocket and space
Supply of the first production equipment for 3D printing to the Center for Additive Technologies of JSC RCC Progress.
Foundry
Fabrication of a matrix using FDM 3D printing for the production of piece metal parts that have been discontinued or to replace parts with a long delivery time.
Education
Production of desktop 3D printers for schoolchildren and students in collaboration with a team of developers of teaching materials for classrooms.
Electronics
Implementation of 3D equipment at the Simvol East Kazakhstan region.
Prototyping of lighting equipment for the Pyaterochka grocery store chain.
Agroprom
Complex equipping of the research agro-engineering center with equipment.
Services
3D printing
Casting
Reverse engineering
prototyping
Upcoming Events
New models of Total Z industrial 3D printing systems in Moscow at the Interplastica exhibition
Interplastica is a key event for the plastics and rubber market, which annually brings together experts from all over the world at one business platform.
The Total Z team will take part in the Rosmould-2023 exhibition
Total Z equipment can be viewed in the specialized 3D-TECH section, which will bring together leaders in the field of additive technologies and 3D printing.
company's news
Total Z desktop 3D printers were presented in the innovative space Timiryazevka Boiling Point
November 7, 2022Total Z at Technoforum 2022 as part of the Skolkovo team
October 31, 2022Total Z at the INNOPROM-2022 exhibition in Yekaterinburg
July 15, 2022More news
Total Z presented a system for high-speed 3D printing with granules at the Metalworking-2022 exhibition
June 6, 2022
Total Z equipment undergoes EU
certification February 14, 2022We are trusted
Large Format Raise3D RMF500 for 3D Printing with Carbon Fiber Reinforced Materials
Last autumn, the well-known Chinese manufacturer of 3D printers, Raise3D, announced the creation of a new 3D printer for small-scale production in the industrial sector - RMF500 . The unique feature of the novelty is the combination of the ability to print with carbon fiber reinforced material (colloquially carbon fiber), wide format and affordability .
We all know that high technology is becoming more accessible every day, and the RMF500 is a prime example of this. There have been systems on the 3D printing market for several years that print carbon fiber composites of similar quality, but, unfortunately, they are not available to all companies due to the very high cost and supply problems. For example, such professional 3D printers are produced by the American company Stratasys - Fortus 450mc, but they are equipped with less technological features and are much more expensive.
Let's take a closer look at what the RMF500 is and how it differs from other 3D printers.
The RMF500 is specifically designed for printing complex parts with high durability. It will enable 3D printing companies to expand their product portfolio with carbon fiber and fiberglass end parts. Both materials specially developed by Raise3D, such as PA12 CF, and materials from other manufacturers approved by Raise3D under the Open Filament Program (OFP) will work. Parts made of carbon and fiberglass are more rigid, durable, resistant to heat and shock than parts made of other plastics. For carbon and fiberglass printing, the RMF500 uses silicon carbide nozzles with a hardness of more than 60 HRC.
PA12 CF filament is the result of a long-term development by Raise3D engineers. This is a carbon fiber reinforced filament with increased stiffness and reduced shrinkage and does not require a thermostatic print chamber. The parts obtained from it are light and extremely durable, sometimes they can even be used instead of metal. In addition, the company has developed the PPA GF glass-filled filament specifically for the RMF500 and plans to launch PET-CF, ASA-GF, PPSU-GF and PP plastics for medical use. Raise3D promises that all fiber reinforced plastics will be competitively priced.
The RMF500 has a huge building area 500x500x500mm. The size of the build area matters in the production of large parts and small-scale production. For comparison, the print area of the Fortus 450mc is 406x355x406mm.
In the photo: printing a large model with carbon fiber in the RMF500 3D printer from Raise3D.
Repeatability and print speed are very important for low volume production. The maximum print speed of the RMF500, according to the manufacturer, can reach 300 mm/s. Positioning accuracy along the XY axis - 1 micron, along the Z axis - 0.09765 microns.
Synchronous feedback control with 1 µm accuracy reduces speed fluctuations as motor load changes, further improving accuracy. Stability and repeatability of printing has long been a hallmark of Raise3D printers. The FFF technology on which this 3D printer is based allows the production of parts with a high degree of repeatability, high positioning accuracy and uniform extrusion. The RMF500 can quickly print large batches of identical parts.
Pictured: production of lots from a large number of parts on the RMF500.
The printer has a printing system with two independent IDEX extruders. It allows you to print with one or two extruders at once. The RMF500 can run two jobs at the same time, further increasing productivity and task speed. The extruders are manufactured using high temperature alloys and industrial ceramic composite materials. These characteristics provide stable and high extrusion speed up to 500 g/h.
The RMF500 has a strong design . The one-piece frame is made of hardened steel. Stainless steel linear guides have a design load of approx. 100 kg. The bearing of the linear guides has minimal backlash and does not require frequent maintenance.
An important detail - Raise3D has developed special support material for printing with reinforced plastic PA12 CF, which can be easily detached.
Pictured: Parts printed on the RMF500 with PA12 CF filament with special proprietary support.
The RMF500 is equipped with four large compartments for plastic spools. Switching between the main and auxiliary compartments occurs automatically. This feature reduces the amount of time spent threading the filament. The humidity control system keeps the relative humidity in the chamber below 5%, preventing humid air from entering from outside.
What else is there in the RMF500 from nice additional options. The front of the printer has a large 13.3-inch touch screen. Supports connection, management and printing via Wi-Fi and LAN. There is a reliable auto-calibration system from Raise3D.
Carbon fiber printed parts are strong enough to be used in the automotive and aerospace industries. Of course, they will not replace functional parts that have a special load, but their scope can be very wide. Raise3D has already presented the results of the first RMF500 printing and its application.
Pictured: Functional parts, accessory tools and fixtures, car décor printed on the RMF500.
Pictured: Functional parts, accessories and aerospace prototype printed on the RMF500.
In the photo: on the left is a prototype of the hinged window mechanism (details are printed with metal filament and carbon), on the right is a carbon fixture. Carbon parts printed on RMF500, metal parts printed on Metalfuse. Printing with fiber-filled plastics does not require a heated chamber, peak power consumption is less than 3 kW. The average power consumption per unit of print area of the RMF500 is 60% lower than the competition.
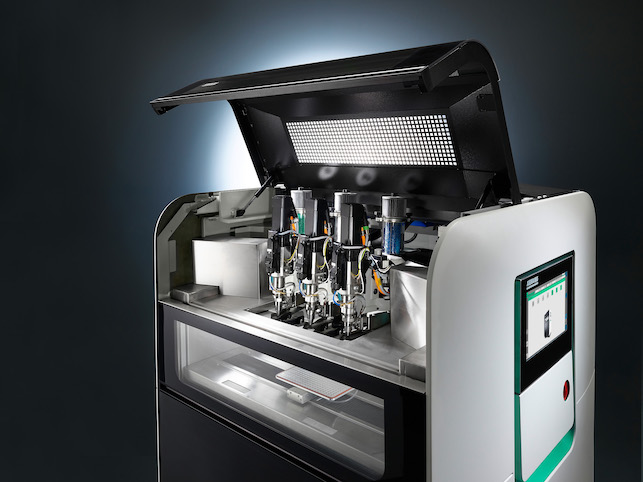