Affordable sls 3d printer
hardware selection and technology guide
What desktop SLS 3D printers are available on the market?
SLS (Selective Laser Sintering) is a 3D printing technology that uses a laser beam to sinter powdered material. This technique enables the 3D printing of detailed functional parts and prototypes.
Five to ten years ago, SLS technology was exclusive to large, industrial additive manufacturing systems. In recent years, a more compact SLS 3D printer niche has been slowly emerging, with lower prices and office-friendly formats.
Starting at around $6,000, these benchtop or desktop SLS 3D printers enable SMEs to access accurate and advanced in-house prototyping without having to rely on external 3D printing services. They are able to print with powder materials such as Nylon, TPE, and other thermoplastics.
In this guide, we take a closer look at which desktop SLS printers are available on the market from brands like Sintratec, Sinterit, and Formlabs.
The best desktop SLS printers for professionals
Brand | Product | Build size | Country | Price Approximate starting prices based on supplier-provided information and public data. Prices may vary by region, over time and do not include additional products or services (taxes, shipping, accessories, training, installation, …). | |
---|---|---|---|---|---|
Sintratec | Sintratec Kit | 110 × 110 × 110 mm4.33 × 4.33 × 4.33 in | – | $ 5,9994 990 €5,321 £894,187 ¥ | Quote |
Natural Robotics | VIT SLS | 250 × 250 × 300 mm9.84 × 9.84 × 11.81 in | Spain | $ 12,90011 000 €11,443 £1,922,822 ¥ | Quote |
Sinterit | Lisa | 150 × 200 × 150 mm5.91 × 7.87 × 5.91 in | – | $ 12,9957 990 €11,527 £1,936,983 ¥ | Quote |
Sinterit | Lisa Pro This product has been reviewed by our team. | 150 × 200 × 260 mm5.![]() | – | $ 17,99011 990 €15,958 £2,681,517 ¥ | Quote |
Formlabs | Fuse 1 | 165 × 165 × 320 mm6.5 × 6.5 × 12.6 in | – | $ 18,49918 499 €16,409 £2,757,387 ¥ | Quote |
RED ROCK 3D | RED ROCK | 180 × 180 × 180 mm7.09 × 7.09 × 7.09 in | – | upon request | Quote |
Expand to see more specs
The products in the table are ranked by price (low to high).
Brand | Product | Build size | Country | Price Approximate starting prices based on supplier-provided information and public data. Prices may vary by region, over time and do not include additional products or services (taxes, shipping, accessories, training, installation, …). | |
---|---|---|---|---|---|
Sintratec | Sintratec Kit | 110 × 110 × 110 mm4.33 × 4.33 × 4.33 in | – | $ 5,9994 990 €5,321 £894,187 ¥ | Get a quote |
Natural Robotics | VIT SLS | 250 × 250 × 300 mm9.![]() | Spain | $ 12,90011 000 €11,443 £1,922,822 ¥ | Get a quote |
Sinterit | Lisa | 150 × 200 × 150 mm5.91 × 7.87 × 5.91 in | – | $ 12,9957 990 €11,527 £1,936,983 ¥ | Get a quote |
Sinterit | Lisa Pro This product has been reviewed by our team. | 150 × 200 × 260 mm5.91 × 7.87 × 10.24 in | – | $ 17,99011 990 €15,958 £2,681,517 ¥ | Get a quote |
Formlabs | Fuse 1 | 165 × 165 × 320 mm6.5 × 6.5 × 12.6 in | – | $ 18,49918 499 €16,409 £2,757,387 ¥ | Get a quote |
RED ROCK 3D | RED ROCK | 180 × 180 × 180 mm7.09 × 7.09 × 7.09 in | – | upon request | Get a quote |
What is SLS (Selective Laser Sintering) technology?
Up until early 2014, Carl Deckard from Structured Polymers held a patent on Selective Laser Sintering 3D printing technology. Selective Laser Sintering (SLS) is part of the Powder Bed Fusion family of 3D printing technologies.
How does Selective Laser Sintering work?
This technology uses a laser to sinter powdered material. In other words, a powerful laser beam selectively melts and fuses tiny powder particles together.
SLS 3D printing technology. Source: SculpteoOnce a layer is finished, more powder is rolled and spread onto the print bed. The process repeats itself layer after layer. The excess powder stays in the powder bed, thus automatically providing support for the object and its intricacies (though supports are still needed when it comes to metal 3D printing).
When the 3D printing process is finished and the powder bed has cooled down, the objects can be removed. The excess powder material is then to be brushed off to reveal the final part. Aside from powder removal, the parts require little to no post-processing for basic applications.
Overview of the best desktop SLS printers
The Sinterit Lisa is a plug-and-play desktop SLS 3D printer made by Polish manufacturer Sinterit. It is one of the most affordable SLS 3D printers actually available on the market.
This 3D printer offers a relatively large build volume for a desktop 3D printer, and even more so for an SLS 3D printer in this price range. With the Lisa it is possible to 3D print flexible material (Flexa Black/Grey) or rigid, strong material (PA12).
Contact manufacturer Get a quote Add to comparison
In comparison with the regular Lisa, the Lisa Pro boasts various upgrades and features. For starters, the Pro version is equipped with a Nitrogen chamber, for wider material compatibility.
The Lisa Pro SLS printer also provides a bigger print volume as well as a larger touchscreen than the Lisa.
Our review at Sinterit headquarters: Sinterit Lisa Pro review
Contact manufacturer Get a quote Add to comparison
The Sintratec Kit started out as an Indiegogo crowdfunding campaign in 2014. It is one of the most affordable SLS 3D printers available today.
The Kit requires around four days of assembly. Users can freely adjust the laser’s height, speed, and temperature in order to try out different materials.
Contact manufacturer Get a quote Add to comparison
Formlabs, originally an SLA 3D printer manufacturer, introduced their first SLS 3D printer – the Fuse 1 – mid 2017. It is officially available since January 2021.
The printer works with Formlab’s PreForm software, and features two separate build chambers. This enables users to immediately launch a second build once the first job is complete.
After the printing process, the chamber can be directly placed as-is in the Fuse Sift, an all-in-one sieving machine that collects unused powder and prepares it for future builds by mixing it with fresh powder. The Fuse 1 can work with up to 70% of recycled powder, so each new build only requires 30% of fresh material (which costs around $100/kg).
Contact manufacturer Get a quote Add to comparison
Note: Natural Robotics launched the VIT SLS via Kickstarter in 2017. As of January 2021, some backers are stating that they still haven’t received their printers, although the company claims to be shipping products.
The VIT SLS offers a relatively large build volume compared to the other 3D printers in this range.
Contact manufacturer Get a quote Add to comparison
Note: This 3D printer is only available in a limited geographical region.
RED ROCK 3D is a new 3D printer manufacturer from Russia. Its RED ROCK SLS 3D printer offers a relatively large build volume compared to most of the other desktop SLS 3D printers in this selection.
Little information about this SLS 3D printer is available on the RED ROCK 3D website, which hasn’t been updated in a while (as of January 2021).
Contact manufacturer Get a quote Add to comparison
Compact industrial-grade SLS 3D printers: our picks
The following printers are larger than the benchtop SLS printers from our main selection but are still relatively compact considering the usual size of industrial SLS systems.
The Sintratec S2 is an all-in-one modular and scalable SLS 3D printing system with an onboard camera and large, intuitive touchscreen. It integrates a material preparation module as well as a depowdering station for semi-automatic workflows.
Optional stations include a blasting station, vortex unit, and a polishing station, enabling easier part post-processing.
Contact manufacturer Get a quote Add to comparison
The SnowWhite 2 features a powerful CO₂ laser that is able to sinter a range of materials including PA 12, PA 11, and TPU, as well as powder loaded with carbon or glass fiber or even aluminum.
All unused powder can be recycled. The printer can be powered up in ten minutes and the minimum amount of powder required to start a print is 300g.
Contact manufacturer Get a quote Add to comparison
XYZprinting’s range of products is one of the industry’s most diverse in terms of technology, suiting both consumers and businesses.
The MfgPro230 xS is an open-source system, meaning that its powerful 30W CO2 can print with any powder that’s available on the market. Hence, users can experiment with different types of Nylons and TPU materials, and even light-colored ones, which is not the case with entry-level SLS printers.
Contact manufacturer Get a quote Add to comparison
Released in 2020, the Gravity SLS 3D printer by Swedish manufacturer Wematter is the most recent printer in our selection. The printer features integrated powder recycling and easy material handling with user-friendly packaging.
Wematter’s cloud-based slicing software automatically optimizes the build area, packing parts efficiently and as close together as possible thanks to advanced algorithms.
Contact manufacturer Get a quote Add to comparison
Benefits and limits of SLS 3D printing
Main benefits of SLS 3D printing
No need for support: 3D printing complex and functional parts
Since unused powder remains in the powder bed, it naturally acts as support for the following sintered layers. This support, which is present all over, allows the 3D printing of very complex and/or functional parts and prototypes.
It’s also possible to 3D print objects within objects, also known as nesting. This is not possible with other 3D printing technologies such as FFF and FDM (extrusion) or SLA and DLP (resins).
Multiple layers of parts to be 3D printed with SLS technology. Source: SinteritWaste reduction
It is possible to re-use powder that has not been sintered. This significantly reduces material waste and costs compared to other 3D printing techniques. Also, no material is wasted on support structures.
Main limitations of powder SLS 3D printing
Just like any technology, SLS 3D printing has its downsides.
Porosity/rough surface
SLS 3D printed objects are porous, though it is possible to apply sealant to alter their sandy, granular-like surfaces.
Expensive material
The price for one kilogram of PA12 powder can range from around $55 to about $180.
Logistics and post-processing
Due to the volatile nature of powder, extra caution is required when handling the material and taking the final 3D print out of the powder bed. The prints must be depowdered; either manually, which is time-consuming, or with a dedicated powder removal solution.
SLS vs FDM vs SLA
SLS vs FDM (FFF)
Compared to Fused Filament Fabrication, SLS can:
- achieve higher quality prints
- provide thinner layers and wall thicknesses
- generate complex 3D prints without the need for support
However, Selective Laser Sintering 3D printers offer much less material choice (and colors).
SLS vs SLA
Compared to stereolithography 3D printing technology, Selective Laser sintering offers:
- thinner wall thicknesses
- complex 3D prints without support structures
That being said, SLS 3D prints have rougher surfaces than SLA 3D prints.
SLS 3D printing: what materials are available?
Main desktop SLS 3D printing powders
Most desktop SLS 3D printers use Polyamide (PA) powdered material, also known as Nylon. The main PA powders available on the market are:
- Nylon PA12
- Nylon PA11
Then, there are composite or “charged” powders, meaning that different materials are mixed with PA. The most common are the following:
- Alumide: PA mixed with aluminum (shiny, metallic appearance)
- Carbonamide: PA reinforced with carbon fiber (stiff and lightweight)
- Nylon 3200: PA filled with glass (more chemical and heat resistant than PA12)
There is also PEBA 2031, a flexible, rubbery, and resistant plastic powder. Some manufacturers produce elastic 3D printing powders (such as Sinterit’s Flexa Black and Flexa Grey) to 3D print shock absorbers, clothing parts, bellows, etc.
Nylon SLS 3D printing material
Nylon, or Polyamide (PA), is the most common powdered material used by SLS 3D printers. It boasts many interesting characteristics:
- Lightweight: Polyamide is a lightweight 3D printing material.
- Robust: this material can bear loads or be used for mechanical parts.
- Flexible: Nylon can bend and come back to its original form.
- Resistance: PA offers good heat and chemical resistance.
Manufacturers generally sell their own, branded powder material.
SLS 3D printing in general
Desktop SLS printers are limited to plastics when it comes to material choice. However, when using larger, more expensive powder industrial 3D printers, it is possible to 3D print metal powder. Some industrial SLS 3D printers are also able to 3D print ceramics.
How to Compare SLS 3D Printer Prices
The Formlabs Fuse 1+ 30W selective laser sintering (SLS) 3D printer
Since its invention in the 1980s, selective laser sintering (SLS) 3D printing has been used by large manufacturers for prototyping and small batch production. Only recently, however, have SLS 3D printer prices become affordable for small to medium manufacturers. The growing number of SLS 3D printers deployed globally speaks to the high part quality, low cost per part, and production readiness of this technology.
SLS 3D printing is an additive manufacturing technology in which a thin layer of plastic powder particles is sintered by a high-powered laser in the shape of a cross-section of the 3D file. The printer then spreads another thin coat of these particles across the build chamber, and the laser sinters that, gradually building these layers into the final part. In plastic powder bed fusion 3D printers, the powder bed supports the parts as they’re being constructed, eliminating the need for the support structures necessary in most other forms of 3D printing, and enabling complex constructions with overhangs, internal channels, and interlocking features. The lack of support structures also means that post-processing parts is easier and less labor-intensive, enabling parts to be produced consistently at a larger scale.
Because the SLS technology requires a high-powered laser, a high level of precision, and tight control throughout the printing process, even the cheapest SLS printer is more expensive than most fused deposition modeling (FDM) and many stereolithography (SLA) printers. But even with these higher initial costs, bringing an SLS 3D printer in-house can result in a positive ROI within just a few months thanks to the high productivity and the lower costs of new industrial benchtop solutions.
In this article, we’ll compare the prices of different SLS 3D printers, and provide a complete overview of the cost of selective laser sintering printing, from initial purchase price to ongoing maintenance, material purchases, and more.
White Paper
In this white paper, we evaluate the value proposition of bringing SLS 3D printers in-house, in comparison with outsourcing SLS parts from a service bureau.
Download the White Paper
Historically, SLS printers were complex, bulky, and expensive systems, only accessible for industrial giants with large manufacturing facilities. In the last five years have benchtop options made it possible for small and medium manufacturers to access the power and productivity that SLS 3D printing provides.
When comparing benchtop SLS solutions like the Fuse Series to traditional industrial options, there are several factors to take into account, namely purchase price, size, ease of use, infrastructure requirements, and ongoing costs. In the following table, we cover these factors in a comparison between benchtop industrial SLS (the Formlabs Fuse 1+ 30W) and traditional SLS (based on EOS’s and 3D System’s product range).
Fuse Series: Benchtop Industrial SLS 3D Printers | Traditional Industrial SLS 3D Printers | |
---|---|---|
Price | Starting at $18,500 for the Fuse 1, $28,000 for the Fuse 1+ 30W | $200,000-$500,000+ |
Print Volume | Up to 165 x 165 x 300 mm | Up to 550 x 550 x 750 mm |
Pros | Affordable High-quality parts High throughput Multiple material options Simplified workflow Small footprint Low maintenance | Large build volume High-quality parts High throughput Multiple material options |
Cons | Smaller build volume | Expensive machinery Large footprint Facility requirements High maintenance Requires a dedicated operator |
White Paper
In this white paper, we evaluate the value proposition of bringing SLS 3D printers in-house, in comparison with outsourcing SLS parts from a service bureau.
Download the White Paper
The cost of SLS ownership is not limited to only the printer hardware itself—there are also the accessory systems, maintenance, and service to consider. Printers themselves can range from $10,000 for DIY solutions, to $500,000+ for the most expensive large-format industrial printers.
Formlabs was the first manufacturer to make industrial quality printing available at the affordable end of the spectrum; the Fuse 1 costs only $18,999 and the Fuse 1+ 30W costs $27,499, while delivering parts of comparable quality to traditional industrial SLS options. However, regardless of which print engine is purchased, there are post-print steps that must be completed for usable parts.
SLS 3D printers provide the benefit of support-less printing, and though this eliminates the need for painstaking removal of support structures, there is still a removal step for the layer of unsintered powder coating the parts. For this step, an accessory system is integral. Almost every SLS manufacturer supplies a post-processing and powder recovery station, which itself can vary greatly in price, from $8,999 for the Formlabs Fuse Sift, to $50,000 for EOS’s solutions. There is a second-hand market for the traditional industrial powder recovery and post-processing machines, but it is still difficult to find a working unit for less than $40,000.
For all SLS printers on the market, there are options for service plans and maintenance contracts, some voluntary, others mandatory. For traditional industrial machines, most service contracts are priced at around 10% of the machine cost—enough to purchase a Fuse Series printer each year. Additionally, industrial printer service plans often have a mandatory renewal every year, creating yet another ongoing cost.
The most popular material for SLS 3D printing is nylon, a rugged engineering thermoplastic used for strong, lightweight functional parts, as their main material option. Nylon composites are also very common, and some manufacturers also offer more flexible options like TPU. The cost of these materials varies between manufacturers, but most price their nylon materials at around $100/kg, with discounts available at larger volumes.
Though prices for raw materials are similar across different manufacturers, the ongoing cost of using those materials can change based on the efficiency of the workflow. This efficiency depends on two factors: packing density and refresh rate.
Packing densities of benchtop SLS printers like the Fuse Series, can often reach 30%, leading to a zero waste printing workflow. The zero waste printing workflow relies on an equilibrium between packing density and refresh rate. Refresh rate refers to the amount of fresh powder necessary for each new build. Most SLS refresh rates are between 30%-50%, though some industrial systems have refresh rates of only 20%.
What matters most for ongoing consumables cost, however, is not refresh rate alone, but the balance of refresh rate and packing density. When they are equal or when the latter is higher, only sintered powder needs to be replaced by fresh powder, and all powder eventually gets used, leading to zero waste and the most efficient use of funds.
The self-supporting nature of powder-bed printing eliminates the laborious process of removing supports from parts printed on FDM or SLA machines, but there is still hands-on labor involved, as the parts must be depowdered in some type of post-processing set-up. Some solutions are also highly complex, requiring maintenance and a long list of workflow steps between each print.
The Fuse Sift machine simplifies the powder removal, recycling, and mixing workflows.
For large traditional SLS systems, the printer and post-processing machine require a dedicated technician to operate them, and in some cases, additional units are needed for powder recycling steps. For these traditional SLS systems, both printer and post-processing machine also require at least a full working day of cleaning and depowdering before switching to a new type of powder. Cost calculations should factor in both the additional labor time as well as the loss in potential production during the downtime necessary for cleaning. The Formlabs Fuse Series system requires only four hours when switching between Nylon 12 Powders and Nylon 11 Powders, and half that when switching between materials using the same base component, e.g. between Nylon 12 Powder and Nylon 12 GF Powder.
Low-cost SLS options, like some DIY solutions, have no post-processing accessories, and thus require much more time spent by an operator on depowdering, mixing, recycling, and labor. Their less intuitive workflows also create many ongoing manual tasks.
The Formlabs Fuse Series printers combine the streamlined workflow of traditional SLS with the manageable footprint of less expensive options. The Fuse Series printers and Fuse Sift can slot in easily to an existing workspace, and the Fuse Sift makes depowdering, recycling, all powder management tasks easy and intuitive, freeing up time for more important tasks.
The Formlabs ROI calculator makes budgeting for an SLS 3D printer easy by breaking down the purchase price of hardware, materials, labor, and all other costs, and calculating the cost per part based on a certain production volume. You can also use the tool to compare time and cost savings with SLS 3D printing versus alternatives like outsourcing or other production methods.
Calculate Your Savings
SLS is an ideal way to prototype functional, strong, and industrial-quality parts quickly and inexpensively, and to manufacture low volume or custom end-use parts. Many manufacturers, engineers, and product designers are already relying on SLS parts, whether they produce them in-house or through a service bureau.
For the majority of the time that the technology has been available, outsourcing was the only way to get SLS parts for most businesses—it was simply too expensive to afford an in-house unit for all but the largest manufacturers. And even now, outsourcing SLS 3D printing can be advantageous in certain scenarios, namely for one-off parts or when a new company simply does not have enough funding to purchase a powerful SLS 3D printer. Service bureaus can provide a stopgap solution for prototyping or even very low volume production. But now that in-house, high-quality SLS is within reach, it’s worth looking into the cost of SLS 3D printing for small and medium manufacturers as well.
An in-house Fuse 1+30W printer can be purchased for one-tenth the cost of traditional SLS systems, creating an opportunity to gain control of more of the manufacturing process. Once established in-house, Fuse Series printers often deliver a positive ROI in as little as five weeks for production cases, and two to three months for prototyping. Businesses can eliminate their reliance on outsourcing, speed up their prototyping or low-volume production, and reduce variables like shipping time in their timelines. In a recent whitepaper, we analyzed six different prototyping and production scenarios to determine exactly how quickly businesses can pay off the cost of the Fuse 1+ 30W by printing in-house, such as the following:
Material: Nylon 12
Build: Two parts for each assembly, four total parts
Fuse 1+ 30W In-House | Service Bureau SLS | |
---|---|---|
Print Time | 13h 10m | |
Cooling | 13h 45m | |
Sift Time (labor time for post-processing) | 40m | |
Total Time | 27h 35m | 7-10 business days |
Materials Cost | $50 | |
Labor Cost | $11.![]() | |
Total Cost | $61.22 | $752.50 |
Cost Per Part | $15.31 | $188.13 |
The total time required to produce these prototypes would allow in-house SLS users to run five full production runs each week, printing ten iterations of the two-part drill casing assembly. Compared to a single iteration every two weeks when outsourcing, an in-house SLS printer opens up opportunities for true iteration. Each new model could have a different aesthetic, alternatives for the grip’s design, or screw threads placed in different spots, and then be presented physically to an approval team the very next day.
The savings when compared to a service bureau are close to $700, which equals over 90% savings for each round, meaning a Fuse 1+ 30W user could achieve positive ROI in just over three months and a little over one year if it’s used just once a week.
The prototype drill, printed on an in-house Fuse 1+ 30W printer (left), and ordered from a service bureau with an MJF (HP) printer (center), and an SLS (EOS) printer (right).
However, not only rapid prototyping applications created such fast positive ROI. In our whitepaper we also analyzed the savings created by in-house low volume end-use parts and manufacturing aids, finding that the savings created by making these in-house paid off the cost of the printer in similarly quick timelines.
White Paper
In this white paper, we evaluate the value proposition of bringing SLS 3D printers in-house, in comparison with outsourcing SLS parts from a service bureau.
Download the White Paper
SLS 3D printing used to be too expensive for most businesses to bring in-house—both due to the cost of the hardware itself as well as the ongoing costs of materials, service plans, and maintenance needs.
Now, SLS in-house is within reach, with accessible hardware costs, and streamlined workflows that reduce continued operating costs. While it’s still a more expensive technology than FDM or SLA, SLS 3D printers have enormous potential for manufacturers to create value. The high throughput and outstanding part quality enable businesses to shorten the time to market through rapid iteration and low-volume production, and reduce reliance on external manufacturers for tooling and replacement parts. Fast, efficient, and high-quality 3D printing can pay back the cost of the printer quickly, especially when compared to other solutions like outsourcing.
The Formlabs Fuse Series printers produce parts of comparable quality as traditional large SLS machines, with affordable prices, similar material selections, and more efficient powder recycling systems. Both in terms of upfront printer price and ongoing costs, Fuse Series printers are the most accessible way to bring high-quality, industrial-grade parts in-house.
Meet the Fuse Series
Sintratec Introduces Cheapest $5,000 SLS 3D Printer
Archive
Subscribe Author
Subscribe
Don't Wanna
1
900starter Systems announced that Norge 3-Dick Systems will be introducing two inexpensively soon Selective Laser Sintering (SLS) Ice1 and Ice9 printers start at $13,000.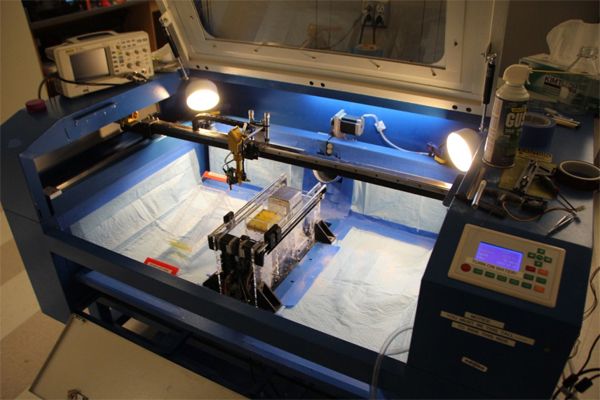
Sintratec was founded by Josha Zeltner, Christian von Burg and Dominik Soleniki. For two years now, they have been working on a 3D printer using selective laser sintering technology. In October, a fundraising campaign for Sintratec's patented technology kicks off on Indiegogo. Below are the main specifications of the future 3D printer (more information will be posted closer to the launch date of the crowdfunding campaign):
- Working volume: 130 mm x 130 mm x 130 mm
- Dimensions: 500 mm x 500 mm x 300 mm
- Layer thickness: depends on the powder to be sintered.
Most powders have a granule size of 40-80 microns. This determines the minimum layer thickness. Maximum thickness can reach 150 microns
- Print speed: For ideal results, print speed should not exceed 70 mm/s
Printing powder, predominantly nylon. The laser fuses it layer by layer, while the platform gradually sinks down. With this printing method, no support material is required, since the powder that remains on the platform around the product itself performs the function of support. When people hear "laser sintering", they immediately imagine the process of fusing metals. However, the Sintratec 3D printer does not print with metal powders. As Dominic Solensky explains:
“Printing with metals is incredible. However, it is very dangerous, requires an inert atmosphere and safety precautions, which will immediately affect the final cost of a 3D printer.”
Sintratec hopes the 3D Printer DIY Kits will cost Indiegogo sponsors a reasonable €3,999 ($5,277) or so, though the company will have to sell at least 60 Indiegogo 3D printers or raise €240,000 to do so.
Below is a video showing the Sintratec 3D printer in action:
Article prepared for 3DToday.ru
Article comments
More interesting articles
4
Subscribe to the author
Subscribe
Don't want
One of the most promising and least developed areas of 3D printing is bioprinting. Whole a...
Read more
4
Subscribe to the author
Subscribe
Don't want
The progress of 3D printing in recent years has gained such a rapid speed that we will soon stop...
Read more
3
Subscribe to the author
Subscribe
Don't want
More and more RepRap 3D printers based on modeling technology are on the market today. ..
Read more
Read blogs
How much does a 3D printer cost?
3D printing is a one-stop solution for a wide range of applications, from high-resolution model production to rapid prototyping, rapid tooling for traditional manufacturing processes, production of aids and end-use models.
However, when you consider investing in a 3D printer, the viability of a solution usually boils down to a simple question: Is it cost-effective for your business? How much does a 3D printer cost and how much time and money can it save your business? nine0003
3D printer prices range from $200 to $500,000 depending on the printing process, materials, and complexity of the solution.
In this guide, we'll break down 3D printing costs by technology, compare outsourcing versus in-house manufacturing, list factors to consider when calculating the cost of each model, and look at what else to look for when comparing different solutions. for 3D printing and other production methods. nine0003
Interactive
This interactive ROI tool will help you find out how much time and money you can save by 3D printing with a Formlabs 3D printer.
Calculate your costs
Three of the most well-known plastic 3D printing technologies today are Fused Deposition Modeling (FDM), Stereolithography (SLA), and Selective Laser Sintering (SLS).
Each technology has its advantages and disadvantages - take a look at the infographic:
Download this high resolution infographic here. Interested in learning more about FDM, SLA and SLS 3D printing technologies? Check out our detailed guide.
Prices for 3D printers have dropped significantly in recent years, and today all three technologies are available in compact, low cost systems.
FDM generally produces models at a lower cost if you only print relatively simple prototypes in limited numbers. SLA technology offers higher resolution and quality, as well as a wide choice of 3D printing materials at a slightly higher price. But this difference is quickly offset when you print complex designs or larger batches due to the less labor-intensive post-processing process. Finally, SLS technology is the most cost effective for medium to high volume production of high quality functional models. nine0003
Comparing the total cost of different 3D printers by price tags alone will not give you a complete picture of how the cost of a 3D printer and a printed model will compare. The cost of 3D printing materials and labor significantly affects the cost of a model, depending on the application and your production needs.
Let's look at the different factors and costs for each process.
FDM, also known as Fused Filament Manufacturing (FFF), is a printing method where the parts of a model are made by melting and extruding a thermoplastic filament, which the printer's nozzle applies layer by layer onto the model being made. nine0003
FDM is the most popular form of consumer grade 3D printing, fueled by the proliferation of hobbyist 3D printers. However, professional and industrial FDM printers are also popular among professionals.
The cheapest 3D printers are FDM printers. DIY kits for FDM 3D printers start at $200. However, most of these models are more like toys or DIY projects that require a significant amount of time to build, set up and calibrate. The quality of the print largely depends on the success of these operations. In addition, machines require repairs and regular maintenance to keep them working, so they are more suitable for people with a higher engineering education who have a lot of time and patience. nine0003
Hobbyist FDM 3D printers cost between $500 and $1,500, come pre-assembled or unassembled, require less setup, but have the same disadvantages as the cheapest 3D printers. More expensive models are capable of large print volumes and work with a wide variety of materials besides low temperature ones such as PLA.
Professional 3D FDM printers start at $2,500 and large format professional FDM printers are available from $4,000. The cost of the most modern industrial FDM printers can exceed 10,000 US dollars. Most of these printers come pre-assembled and calibrated in the box, or they can be automatically calibrated. Printers in this category offer better print quality, a wider range of media, higher print volumes, improved reliability, and ease of use and maintenance. In addition, professional 3D printer manufacturers offer customer support services for troubleshooting. nine0003
Material costs for FDM 3D printing range from $50 to $150/kg for most standard and engineering filaments, and $100 to $200/kg for auxiliary materials. There are also cheaper alternatives, but they are of lower quality.
In addition, FDM printing can be very labor intensive. Successful printing of complex models requires support structures that must be removed manually or dissolved in water. To obtain a high quality surface and remove layer lines, lengthy manual post-processing of models, such as sanding, is necessary. nine0003
SLA 3D printers use the process of photopolymerization, that is, the conversion of liquid polymers into hardened plastic using a laser. SLA is one of the most popular processes among professionals due to its high resolution, accuracy and material versatility.
Models printed on SLA printers have the highest precision, sharpest detail and smoothest surface possible of any plastic 3D printing technology. But the main advantage of the SLA method is its versatility. SLA polymers have a wide range of optical, mechanical and thermal properties that match those of standard, engineering and industrial thermoplastics. nine0003
SLA 3D printers can handle a wide range of resin materials for a wide variety of applications.
SLA used to be used only in large and complex industrial 3D printers costing over $200,000, but the process is now much more affordable. With the Formlabs Form 3+ Printer, businesses can now use industrial quality SLA printing for as little as $3,750. With Form 3L, large format SLA printing starts at just $11,000. nine0003
Stereolithographic 3D printers will be shipped in a box assembled and calibrated. These are professional tools that are highly reliable and require virtually no maintenance. Technical support is also always available. It provides troubleshooting in a critical situation (but its probability is extremely small).
Most standard and engineered polymers for SLA technology cost between $149 and $200 per liter. nine0003
SLA printers are easy to use and many workflow steps such as rinsing and final curing can be automated to reduce labor costs. Printed models have a high quality surface immediately after printing and require only simple post-processing to remove supporting structures.
Selective Laser Sintering (SLS) 3D printers use a high power laser to sinter fine polymer powder particles. The unsprayed powder supports the model during printing and eliminates the need for special support structures. This makes SLS ideal for complex geometries, including internal features, grooves, thin walls, and negative taper. nine0003
Models produced using SLS printing have excellent mechanical characteristics - their strength can be compared with the strength of injection molded parts. As a result, SLS technology is the most popular plastic 3D printing process for industrial applications.
SLS printed nylon models are ideal for a range of functional applications, from consumer product design to healthcare applications.
Like SLA, SLS was previously only available in large format, complex 3D printing systems costing $200,000 or more. With the Formlabs Fuse 1 stereolithography printer, businesses can now solve industrial-scale tasks with SLS technology starting at $18,500. The complete kit, which includes the post-processing and powder recovery system, costs $31,845.
As with SLA printers, stereolithographic printers are shipped assembled and calibrated in the box. They are reliable and can operate 24/7. The package includes in-depth training and fast technical support. nine0003
SLS nylon print materials cost about US$100/kg. SLS does not require supporting structures and unused powder can be reused, reducing material costs.
SLS is the least labor-intensive plastic 3D printing process in the production environment, because the printed models are of high quality right away, and to remove excess powder, they simply need to be cleaned.
There are several processes for 3D printing not only plastics but also metals. nine0003
Metal FDM printers are similar in design to traditional FDM printers, but use extruded metal rods held together by a resin binder. The finished parts of the model are sintered in an oven to remove the binder.
SLM and DMLS printers are similar to SLS printers, but instead of polymer powders, they fuse metal powder particles layer by layer using a laser. 3D printers based on SLM and DMLS technologies can create strong, precise and complex metal products, making this process ideal for the aerospace, automotive and medical industries. nine0003
Prices for metal 3D printers have also begun to decline, ranging from $100,000 to $1 million today. However, these systems are still out of reach for most businesses.
SLA 3D printing is available as an alternative for casting workflows that allow metal models to be produced cheaper and faster than traditional methods and provide greater design freedom.
Technical report
Get design guides for 3D printing samples, see the step-by-step direct investment casting process, and study guides for indirect investment casting and sand casting.
Download white paper
Different plastic and metal 3D printing processes have unique qualities that make them suitable for different applications. Below is a comparison of different printing technologies.
Fused Deposition Modeling (FDM) | Stereolithography (SLA) | Selective Laser Sintering (SLS) | Metal FDM Printing | Selective Laser Melting (SLM) | Metal Direct Laser Sintering (SLM6) | ||||
---|---|---|---|---|---|---|---|---|---|
PRODUCATION | ★cle | ★ opa | ★cle | ★cle | ★ Looking ★☆ | ★ opa | ★ opa | ★cle | ★ opa |
Surgery | ★ op ★ opa ☆ | ★ Look | ★ opa | ||||||
performance | ★cle | ★cle | ★ opa | ☆A ☆ | ★ opa | ||||
Simplicity of use | ★ opa | ★ opa | ★cle | ★cle | ★ ☆☆☆☆ | ||||
to ~ 300 to ~ 3 x 300 x 600 mm (Desktop and Workshop 3D printers) | Up to ~300 x 335 x 200 mm (Desktop and Workshop 3D printers) | Up to 165 x 165 x 300 mm (3D - workshop printers) | Up to 300 x 200 x 200 mm | Up to 400 x 400 x 400 mm | |||||
Price range | DIY kits for 3D printers start at $200, while hobby printers cost $500-1500.![]() | Professional desktop printers start at $3,750, while high-volume large format desktop printers are available from $11,000. nine0200 | Workshop industrial printers start at $18,500 and traditional industrial printers start at $100,000. | Metal FDM printers start at $100,000, but complete solutions including an oven are much more expensive. | DMLS/SLM solutions start at around $200,000. These printers require special infrastructure conditions, which can further increase costs. | ||||
Cost of materials | US$50-150/kg for most standard and engineering yarns and US$100-200/kg for auxiliary materials. | $50-150/L for most standard and engineering polymers. | $100/kg for nylon. SLS does not require supporting structures and unused powder can be reused, reducing material costs. | Depends on material and technology.![]() | Depends on material and technology. Significantly higher than plastic. nine0200 | ||||
Labor | Manual removal of support structures (soluble support structures may be used in some cases). Long post-processing is required to obtain a high quality surface. | Washing and final polymerization (both can be automated). Simple post-processing to remove supporting structures. | Easy cleaning to remove excess powder. | Washing and sintering (both can be automated). It is possible to use mechanical processing and other types of surface treatment. nine0200 | Stress relief, support structure removal, heat treatment, and mechanical and other surface treatments. | ||||
Materials | Standard thermoplastics such as ABS, PLA and their various blends. | Various polymers (thermosetting plastics). Standard, engineering (similar to ABS and PP, similar to silicone, flexible, heat resistant, rigid), injection molding, dental and medical (biocompatible).![]() | Engineering thermoplastics - typically nylon and its composites (nylon 12 biocompatible + sterilizable). | Stainless steel, tool steel, inconel, copper, titanium. | Stainless steel, tool steel, titanium, cobalt-chromium, copper, aluminium, nickel alloys. | ||||
Applications | Basic experimental models, low cost rapid prototyping of simple parts. | Prototypes with a high level of detail requiring tight tolerances and smooth surfaces: molds, tooling, templates, medical models and functional parts. nine0200 | Complex geometries, functional prototypes, low volume production or limited trial production. | Strong and durable models, tools and production aids. | Strong and durable models with complex geometries; ideal for the aerospace, automotive and medical industries. |
When calculating the cost of one model, the cost of ownership of equipment, material costs and labor costs are usually taken into account. It is important to understand the factors that affect each of these cost components, as well as the questions to ask in order to evaluate alternative production methods and uncover hidden costs. nine0003
Hardware ownership costs are fixed costs: 3D printer price, service contracts, installation and maintenance. These amounts must be paid whether your printer is idle or produces dozens of models per week.
Add up all projected fixed costs over the lifetime of the equipment, then divide by the number of models you plan to make. As a rule, the higher the performance and efficiency of your 3D printer, the lower the cost of ownership of equipment per model. nine0003
In recent years, desktop 3D printers have shown excellent results in reducing the cost of ownership of equipment. With a price 10 to 100 times lower than traditional industrial 3D printers and the ability to produce thousands of models over a lifetime, the cost of ownership can be negligible.
Questions:
-
Are there installation, training or additional initial costs other than the cost of the machine itself? nine0003
-
Do I need to sign a (mandatory) service contract? What does it include?
-
What accessories and tools are needed to make the final models?
-
What kind of maintenance is required for the machine to function properly? What is the expected annual maintenance cost? Will it change with an increase in production volumes?
The 3D printing raw materials and consumables you need to create models at an affordable price. These costs largely depend on the number of models you produce. nine0003
When calculating the cost of materials, determine how much material is required to create one model, and multiply this figure by the cost of the material. Count the amount of waste and any other consumables. As production grows, the cost of ownership of equipment decreases, and the cost of 3D printing materials tends to become more balanced.
Be sure to check what materials you need to create specific models, as the cost of 3D printing consumables can vary greatly. Please note that some 3D printers only work with their proprietary materials and thus limit your ability to use third party materials. nine0003
Questions:
-
What is the cost of each type of 3D printing material?
-
How much material is required to create one particular model, including waste?
-
What is the shelf life of the materials?
-
Do I need other consumables to create models?
-
Can the machine work with third-party materials?
While 3D printing can replace complex traditional manufacturing methods and provide significant time savings, depending on the 3D printing technology, it can still be quite labor intensive. nine0003
Professional desktop 3D printers are generally optimized for ease of use. DIY kits for 3D printers and hobby printers often require additional effort to adjust settings, while regular maintenance or material changes on traditional industrial machines can involve time-consuming tasks that require the assistance of a skilled operator.
Post-processing workflows vary depending on the 3D printing process, but in most cases include cleaning up models and removing support structures or excess material. However, there are solutions to automate some specific tasks. For example, Formlabs Form Wash and Form Cure simplify the wash and finish process for Formlabs SLA 3D printers, while Fuse Sift offers a turnkey post-processing and powder recovery system for the Fuse 1 SLS printer. nine0003
More complex processes such as SLA and SLS do not take long to achieve high quality models, while FDM models require lengthy manual post-processing to improve quality and remove layer lines.
Questions:
-
What is the whole model production workflow? What specific steps are required to set up printing, change materials, and post-process models?
nine0018 -
How long does it take to post-process one particular model?
-
Are there any tools or devices available to automate some of these tasks?
Outsource production orders to third-party service bureaus or labs when you use 3D printing only occasionally or to produce large models in non-standard materials. Typically, the bureau has several in-house 3D printing processes such as SLA, SLS, FDM, as well as metal 3D printers. They can also provide advice on a variety of materials and offer additional services such as design or improved finishes. nine0003
The main disadvantages of outsourcing are the high cost and duration of production. One of the main advantages of 3D printing is its speed compared to traditional production methods. But it is noticeably reduced if the delivery of the model produced by the involved organization takes several days or even weeks. And as demand and capacity grow, the costs of outsourcing are rising rapidly.
Desktop 3D printers are the perfect solution for fast model production. Depending on the number of parts needed and the volume of prints, the investment in a professional 3D printer can pay for itself in just a few months. nine0003
With desktop and workshop printers, you can pay for the capacity that matches your business needs and scale your production by adding more devices as demand grows, without the heavy investment of a large format 3D printer. Using multiple 3D printers also allows you to print models from different materials at the same time. But if there is a need for the production of large parts or the use of non-standard materials, service bureaus can come to the rescue. nine0003
Investment, material and labor costs are relatively easy to calculate. But what about indirect costs and hard-to-calculate factors that affect your business? Let's look at some of the main considerations when comparing a desktop 3D printer to outsourcing or other manufacturing methods.
Save time: What if you could get products to market a few months faster? Or reduce the delivery time of your products by a few days or weeks? 3D printing simplifies traditional prototyping and manufacturing workflows, helping you save time and stay ahead of the competition. nine0003
Best results: 3D printing allows you to create more iterations, overcome failures faster and produce better end products. Troubleshooting a design early on also helps avoid costly redesign and the use of additional tools.
Interaction: Having high-quality prototypes and models allows you to communicate more effectively with customers, clients, suppliers and other stakeholders. Avoid misunderstandings and costly mistakes. nine0003
Intellectual property protection: Do you work with confidential information? Making your own models means you don't have to transfer intellectual property (IP) to third parties, reducing the risk of IP leakage or theft.