Abs filament 3d printing
Ultimate Materials Guide - Tips for 3D Printing with ABS
Overview
ABS (Acrylonitrile Butadiene Styrene) has a long history in the 3D printing world. This material was one of the first plastics to be used with industrial 3D printers. Many years later, ABS is still a very popular material thanks to its low cost and good mechanical properties. ABS is known for its toughness and impact resistance, allowing you to print durable parts that will hold up to extra usage and wear. LEGO building blocks are made from this material for that same reason! ABS also has a higher glass transition temperature, which means the material can withstand much higher temperatures before it begins to deform. This makes ABS a great choice for outdoor or high temperature applications. When printing with ABS, be sure to use an open space with good ventilation, as the material tends to have a slight odor. ABS also tends to contract quite a bit as it cools, so controlling the temperature of your build volume and the part inside can have major benefits.
- Low Cost
- Good impact and wear resistance
- Less oozing and stringing gives models smoother finish
- Good heat resistance
- Heavy warping
- Needs heated bed or heated chamber
- Produces a pungent odor while printing
- Parts tend to shrink leading to dimensional inaccuracy
Hardware Requirements
Before 3D printing with ABS make sure your 3D Printer meets the hardware requirements listed below to ensure the best print quality.
Bed
Temperature: 95-110 °C
Heated Bed Required
Enclosure Recommended
Build Surface
Kapton tape
ABS Slurry
Extruder
Temperature: 220-250 °C
No special hot-end required
Cooling
Part Cooling Fan Not Required
Best Practices
These tips will help you reduce the chances of common 3D printing issues associated with ABS such as warping and fumes.
Control Warping
One of the most common print quality issues with ABS is warping. As the plastic cools from its extrusion temperature down to the room temperature, this change in temperature causes the plastic to shrink and contract. This can be particularly troublesome for the first layer, as this change in size can frequently cause the part to separate from the bed, ruining the print. You can minimize this effect using a proper build surface heated to 110º C. The build platform will transfer some of its heat to the first few layers of your part, which will prevent them from shrinking and separating from the bed. It is also common to set the extruder temperature about 10 to 20 degrees higher for the first few layers of your print, which can also help reduce the risk of separation. Simplify3D gives you complete control over your bed and extruder temperatures, so you easily set the desired values on a per-layer basis using the Temperature tab of your process settings. While these changes can help with the bottom layers of your print, taller parts may have issues as the layers get further away from the bed.
When printing larger parts, consider adding an enclosure around your printer to maintain a higher temperature around your print. The enclosure can also prevent wind drafts that could rapidly cool the part during printing. If you’ve followed these steps, but you’re still having trouble with warping and separation, our Print Quality Guide has an entire section dedicated to warping which can give you even more information on the topic: How to Prevent Warping.
Using Brims and Rafts
When printing large parts, or thin delicate parts, you may find that you still have trouble getting these parts to properly adhere to the bed. In these cases, adding a brim or a raft to your print can be a great way to anchor these part to the build platform and prevent warping. A brim will add several rings of plastic around your model on the first few layers, creating extra surface area to hold down the edges of your part. Using a raft will actually print an entirely new plastic structure underneath your print, which can be removed after the print is completed. The rafts in Simplify3D were heavily optimized for Version 4.0 allowing them to print faster and use more material, but you may still find that a brim is faster for larger parts. If you want to learn more about these options, we have an in-depth article that explains all of the differences between rafts, skirts, and brims to help you get started.
Print In a Well Ventilated Area
Printing with ABS is known to produce a strong odor with fumes that could potentially be harmful if inhaled in large quantities. Avoid confined spaces and place your printer in a well-ventilated area to avoid these issues. Newer 3D printers may include a separate air-filtration system or HEPA filter that can deal with these fumes right from the source. If you printer doesn’t include these features or you’re limited in where you can place it, consider opening a window or using a flexible air duct from your local hardware store to help route the fumes outside.
Pro-Tips
- Bed adhesion can be improved by using an ABS slurry.
You can make this slurry on your own by mixing small pieces of ABS filament with acetone and applying the mixture on the bed. There are also several pre-packaged versions of the product that can be purchased.
- When doing a dual extrusion print, PLA can be a good break-away support material as it does not adhere strongly to ABS.
Get Started with ABS
Here are a few tips to help you get started with ABS. You can view some common applications below, select from a typical sample project, or even view popular filament brands if you’re looking to stock up on this low cost material.
Common Applications
- Cases or Project Enclosures
- Toys or Action Figures
- Automotive hardware
Sample Projects
- Lego Bricks
- Door Catch
- Fidget Spinner
Popular Brands
- Hatchbox ABS
- FormFutura ABS pro, EasyFil ABS, TitanX
- eSun ABS, ABS+
- HobbyKing ABS
PLA vs.
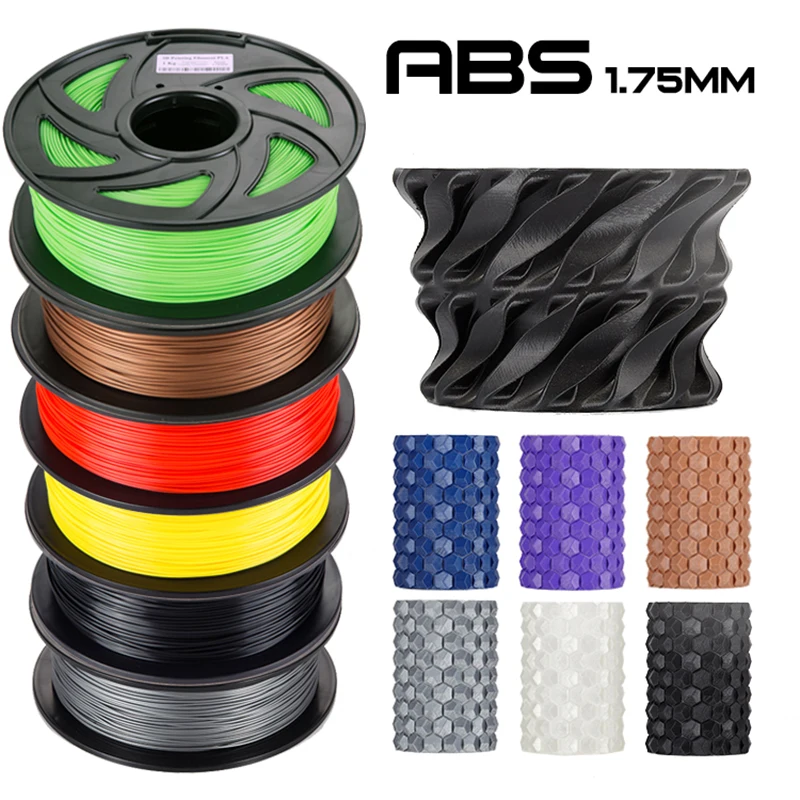
PLA and ABS filaments are the most commonly used ones out there.
But which one should you pick? And are there other filament options for your application?
The power of 3D printing is the ability to produce impossible designs that lead to enhanced functionality and performance. While it’s important to evaluate different technologies and processes, never underestimate material selection and capabilities.
With so many different 3D printing options in the marketplace and countless material options available, what makes the most sense for you? In this post we will compare several FDM materials and how these thermoplastics can be augmented to service a wider range of manufacturing applications. PLA vs. ABS, ASA, PLX, PRO HT, HI-TEMP, Carbon Fiber, Bio-ABS, and more.
ABS Filament
The most commonly used 3D printing material is ABS (Acrylonitrile Butadiene Styrene). ABS variations are used in every industry imaginable (transportation, consumer products, electronics, etc.). For example, plastic components make up 50 percent of a vehicle’s volume, but only about 10 percent of its weight. Therefore, prototypers, product developers, and production engineers feel comfortable printing materials that mimic the end-use product or purpose. 3D printing with ABS is an acceptable and easy solution for many manufacturers.
- Excellent mechanical strength and durability properties
- Cost effective & recyclable
- Better heat performance compared to PLA
- Great for 3D printing prototypes that require multiple iterations or low volume production requests
PLA Filament & PLX
Second only to ABS, PLA (Polylactic Acid) is a highly preferred 3D printing material because it is inexpensive, easy to use, and accessible on many platforms. Compared to ABS, PLA has slightly better tensile strength properties but generally doesn’t have enough flex strength. Both materials are comparable when it comes to pricing. However, under the right conditions, PLA is biodegradable and oftentimes used for food and packaging products making it rather attractive for many consumer product industries. In many instances, PLA is the preferred material choice. PLX, a PLA derivative, was recently introduced by BigRep and available on all platforms. PLX prints up to 80% faster and produces excellent surface features, eliminating the need for post processing.
- Biodegradable
- Up to 80% faster extrusion throughput
- Tensile strength (ISO 527) | 48 MPa
- Key industries: Consumer products, food packaging, prototyping, form, fit, and function
ASA Filament
ASA (Acrylonitrile Styrene Acrylate) is an ABS alternative material with improved weather resistance properties that make it ideal for many outdoor applications. Compared to ABS, ASA has better mechanical properties, superior aesthetics, and it’s UV resistant. Printing with ASA is advantageous for industrial and end-use parts, oftentimes used for automotive, sporting goods, and consumer appliances. The downside is that ASA is slightly more expensive than ABS and produces toxic smoke when burned. Many UAV (unmanned aerial vehicle) developers will prototype with ASA material and even consider using it in the final product due to its UV stability and weather resistance.
- Enhanced UV stability
- Ideal for outdoor applications
- Improved aesthetics compared to ABS and PLA
- Key industries: Consumer products, defense applications, automotive, and aviation
PRO HT: High Temperature Filament
PRO HT, BigRep’s flagship material, is the most popular filament amongst BigRep customers and users. With a softening resistance up to 115 °C, it has significant increase in temperature resistance compared to the average PLA, making it ideal for practical, end-use applications. In addition, PRO HT is FDA compliant for food safety and meets all requirements of EU Directives for food contact. Derived from organic compounds, PRO HT is biodegradable under the correct conditions and has a much lower ecological impact than other plastics derived from fossil fuels. Most common applications include consumer products, packaging, general prototyping, manufacturing and low production tooling.
- Simple to print and easy post processing
- Low warping and shrinkage
- Biodegradable
- Heat resistance up to 115 °C
HI-TEMP CF: Carbon Fiber Filament
Carbon fiber materials are unique and fairly new to the 3D printing industry. Highly stiff and incredibly durable, HI-TEMP CF is heat resistant up to 115 °C and perfect for many tooling applications. For example, thermoforming, pattern and mold making will use HI-TEMP CF for class A surface finish and low moisture absorption.
Compared to many other thermoplastics, the carbon fiber attributes provide significant strength capabilities (>65 MPa) and is recommended as a superior alternative to ASA for functional prototyping or production. HI-TEMP CF is robust and resilient to withstand harsh manufacturing environments.
- Jigs, Fixtures, and Tooling
- Automotive prototyping and production
- Assembly line, manufacturing, and production
- Tensile strength (ISO 527) | 65 MPa
Positioning jig for car production 3D printed with HI-TEMP CF
Conclusion
How to truly maximize the right filament for your application? When it comes to general prototyping, all of these materials can be considered and will most likely yield positive results for your product development. However, prototyping goes beyond just form, fit and function so we recommend taking a deeper dive into specific material characteristics to determine which makes the most sense for you. When it comes to production, it’s very important to consider the mechanical properties of your chosen material and how it will perform. Tooling or end-use products are required to meet certain standards and more often than not, sacrifices cannot be made.
To simplify, we recommend:
- PLA and ABS for simple prototype development.
- If you own BigRep 3D printer equipment, reach out to us to learn about PLX and the time savings it can provide.
- If you’re looking for UV stability or slightly better strength performance for prototyping or production, we recommend ASA.
- Finally, PRO HT and HI-TEMP CF are the most robust materials for low volume production, tooling or any other application that requires parts to perform in harsh environments.
Check out our wide range of 3D printing filaments and find the right material for your application:
Filaments
About the author:
Dominik Stürzer
SEO Manager
Dominik is a mechanical engineer whose passion to share knowledge turned him to content creation. His first 3D prints started in university. Back then the 3D printers were big on the outside and small on the inside. With BigRep the machines are finally big in their possibilities.
ABS for 3D printing
The high strength of ABS makes it suitable for structural applications
ABS (Acrylonitrile Butadiene Styrene, ABS) is a high-impact thermoplastic that has become very popular in industry and additive manufacturing.
The excellent mechanical and physical properties of ABS plastic make it possible to use this material to create all kinds of objects of practical value. ABS plastic is widely used in the automotive, medical and souvenir industries, in the production of sports equipment, plumbing, bank cards, furniture, toys, etc.
The relatively low cost of ABS plastic and the relative ease of use as a consumable have led to ABS's high popularity among 3D printing enthusiasts. ABS is one of the most popular materials for FDM/FFF printing.
Safety ABS
ABS is relatively safe and does not pose a threat under normal conditions. However, heating ABS releases toxic acrylonitrile fumes, which means you need to take some precautions when 3D printing. Evaporation is generally low due to the relatively slow material consumption of FDM printing. To ensure a completely safe environment, only good ventilation of the room or an extractor is required. It is also worth bearing in mind that ABS plastic reacts with ethanol, which leads to the release of styrene.
Do not use finished ABS products to store hot food and drinks or alcohol at any temperature.
ABS Specification
Glass Transition Temperature | About 105°C |
Flexural strength | 41 MPa |
Tensile strength | 22 MPa |
Tensile modulus | 1627 MPa |
Elongation | 6% |
Shrinkage on cooling | Up to 0.![]() |
Material density | Approx. 1.05 g/cm³ |
Please note that the actual dimensions of the 3D printed ABS will depend on the manufacturer's specifications. In many cases, ABS is blended with other thermoplastics (such as polystyrene), resulting in changes in extrusion temperature, resistance to certain solvents, etc.
Advantages and disadvantages of ABS
The main disadvantage of ABS is its relatively low resistance to direct sunlight. In addition, the potential toxicity of the material somewhat limits its use in the manufacture of toys, food packaging and medical instruments.
A wide range of colors is demonstrated with Lego bricks made from ABS plastic
At the same time, ABS plastic has a number of positive qualities:
- Almost unlimited colors
- Moisture resistant
- Acid resistance
- Oil resistance
- Relatively high heat resistance, reaching up to 115°C in some material grades
- Non-toxic at relatively low temperatures and in the absence of alcohol exposure
- Increased impact resistance
- High elasticity
- High durability in the absence of direct sunlight
- Easy to machine
- Good affordability
- High solubility in acetone
Use in 3D printing
The result of processing a model from ABS plastic with acetone vapor
Printing with ABS plastic is associated with certain technological difficulties due to a rather high tendency to shrink, that is, to loss of volume during cooling. As a result, the formation of deformations and delamination of models is possible. This point is taken into account by manufacturers optimizing 3D printers for ABS printing by installing heated work platforms and providing varying degrees of climate control in the working chamber. Some methods for dealing with deformations are described in the section "How to avoid deformation of models when 3D printing".
In addition to being machinable, ABS is easily soluble in acetone and some other solvents, which makes it possible to produce fairly large models from component parts by gluing. In addition, the processing of finished models with acetone vapor allows you to smooth the outer surfaces and achieve complete tightness. For more information on processing with acetone, see the "Processing 3D Printed Models" section.
Go to the main page of the 3D Printing Encyclopedia
PLA and ABS for 3D printing: what's the difference?
3DPrintStory    3D printing process    PLA and ABS for 3D printing: what's the difference?
PLA or ABS: Which one to use and when? The article reveals the difference between these plastics and shows the areas of their use.
Some of the most popular plastics for 3D printing using Fused Deposition Modeling (FDM) technology are ABS and PLA. Both are thermoplastics. This means that they become malleable when heated - so you can shape them and when cooled they will retain their shape. Both materials are made into bars that you can feed into your 3D printer's extruder. The printing process when using ABS and PLA is very similar.
Despite their apparent similarity, ABS and PLA are different. Some 3D printers can only print with PLA plastic at all.
ABS and PLA - brief definitions
PLA (PolyLactic Acid) is a biopolymer, i.e. a biodegradable plastic. It is made from renewable materials such as cornstarch or sugar cane. In addition to 3D printing, PLA is used for packaging, plastic bottles and cups. It is considered to be more environmentally friendly compared to ABS.
ABS (Acrylonitrile-Butadiene Styrene) oil-based plastic. This is a tough material that is used to create household appliances, electrical equipment and even Lego bricks.
Comparison of the main characteristics of the PLA and ABS
The table below shows the main characteristics of PLA and ABS plastic:
Parameter | PLA | ABS | MELT FLOT FLAT FLAT FLAT FLAT FLAT FLAT FLAT FLOW / 10 min. | 9.7 cm3 / 10 min.0002 | 70-82 190-220 ° C | 230-250 ° C |
Recommended print temperature | 50-70 ° C (not to gnaw) | 80-120 ° C (be sure to warn) |
What does each of the above characteristics mean?
- Melt flow index characterizes the ease of flow of the molten polymer. It is measured in the amount of material that passes through a capillary of a certain diameter and length in 10 minutes.
- The glass transition temperature is the point at which a hard and brittle material becomes molten or elastic with increasing temperature. This is an important characteristic if you are printing a model that will interact with hot water or drinks: for example, a PLA coffee mug is not a good idea.
ABS plastic in this case is also a bad option: see the "Recommended Applications" section below.
- The pour point characterizes the limit of resistance to heat: at temperatures above this, the object will bend. If your 3D printer is equipped with a heated table, the temperature of this table must be below this temperature; otherwise, the object is deformed during 3D printing.
- Melting point (or melting point) - everything is obvious here - the temperature at which the material begins to melt.
- 3D printing temperatures are typically higher than melting temperatures, as the plastic must be melted (not just started melting) as it is fed through the extruder nozzle.
Mechanical and physical properties
PLA is more brittle and has a higher surface hardness. More prone to breakage during bending. Acetone treatment (to improve surface smoothness) is not possible.
The illustration below shows a key printed in ABS.
When printed at the manufacturer's recommended temperatures, ABS parts will be much harder and more resistant to impact and stress than PLA. That is, ABS is better suited for printing mechanical components and parts and objects with high resistance to aggressive environments. In addition, ABS parts are more flexible and bend rather than break under external pressure. ABS is better malleable, post-processing is easier. Printed models can be sanded, painted. They can be treated with acetone to get a smooth, shiny surface.
Easy to 3D print
In general, PLA is best for beginners to get into 3D printing. ABS plastic is more prone to the standard 3D printing problem of shrinkage (i.e. when the first layers cool too quickly and begin to curl around the edges, causing the model to come off the table at the corners). Printing ABS plastic will require experimentation to find the optimal settings.
PLA has another drawback - it tends to clog the nozzle of the extruder, as it is more sticky and expands more when melted. To avoid clogging the nozzle, it is recommended to follow the manufacturer's instructions. The layers lay down well and are unlikely to be bent around the edges. The printed product is easier to separate from the table than similar ones made of ABS plastic. Heated bed is optional (but can improve print quality if used correctly). The 3D printer doesn't have to be kept in a closed case (but again, using a case can result in better results). To increase the adhesion of the table, it is recommended to use special tape (also known as 3D printing tape).
ABS tends to shrink more than PLA.
Printing with ABS plastic takes place at higher temperatures than PLA, which greatly reduces the chance of nozzle clogging. In addition, less force is required to feed the material into the nozzle. Since ABS shrinks as it cools, the part can come off the table (especially when 3D printing tall models). To avoid this, it is necessary to use a heated table. It is desirable that the printer has a case. Since the grip on the table is worse than that of PLA, various problems can arise. To improve adhesion to the table, it is recommended to use Kapton tape (withstands temperatures up to 400ºC). True, tape is expensive, so there is an alternative option - spray hairspray on the table before printing.
Storage conditions
Both plastics (PLA/ABS) absorb moisture from the air. To avoid this, the air is pumped out during packaging. Manufacturers of materials for 3D printing recommend using spools as quickly as possible, as quality begins to suffer over time. Unpacked material should be stored in a dry place.
If PLA is stored for a long time, you may notice bubbles during 3D printing. Doing so may clog the nozzle and degrade the surface quality of the printed product. While wet PLA can be dried under warm air, heat can degrade the material's structure and change thermal properties, which will affect print temperatures.
When printing with damp ABS, bubbles may also occur. If you dry it with warm (but not too much) air, for example, using a food dehydrator, the thermal properties of the plastic will not change.
Vapors and odor
When you 3D print with resins (PLA/ABS), you will smell. The smell depends on the media used and the printing temperature.
PLA smells almost pleasant, some people liken this smell to warmed waffles or sweets.
ABS smells bad when heated. Some complain of headaches and even nausea due to 3D printing. If you are printing indoors, good ventilation is recommended.
Degradability and durability
PLA is biodegradable - it is made from plant materials. Since it needs a little heat to decompose, you can safely throw it into the trash containers.
ABS does not biodegrade but can be recycled.
Both materials (PLA/ABS) degrade when exposed to sunlight and moisture. ABS is more stable and more chemical resistant than PLA.
What to choose?
Both materials are available in different colors; there are even translucent materials. Some specialty materials are only available as a mixture based on PLA. This is wood, metal, etc.
The photo below shows ColorFabb's "Bamboofill". The material contains 80% PLA and 20% bamboo sawdust.
Prices for PLA and ABS
Prices are in the same range, but as a rule, PLA plastic is a bit more expensive. Naturally, PLA plastics with impurities of wood or other materials are more expensive.
Recommended Applications
PLA is widely used in 3D printing, such as household items, gadgets and toys. It's great if flexibility isn't your primary requirement. In this it is inferior to ABS. On the other hand, it is biocompatible and can be safely used in accessories that interact with the skin.
Due to its relatively low melting point, PLA is not suitable for objects that are exposed to heat. When heated above 60ºC, PLA plastic products begin to lose their shape. Do not use PLA in objects that are exposed to sunlight for a long time or are in cars.
ABS is best suited for objects that are exposed to high temperatures, can be dropped or can take bending loads.