3D printing support material settings
How to Get the Best Support Settings For Filament 3D Printing (Cura) – 3D Printerly
3D printing can get often complex, and you’re most likely to use support structures on your models from time to time. Whenever that happens, you need to make sure your support settings are calibrated appropriately. If not, your models can suffer a lot in terms of quality.
In this article, I’ll try to explain what support settings are and how you can get the best support settings for your 3D printer using the Cura software.
What Are Support Settings for 3D Printing in Cura?
Support settings in 3D printing are used to adjust how your supports are created. This can range from where supports will be created, to support density, support pattern, distances between the supports and the model, down to even support overhang angles. Default Cura settings work well mostly.
Supports are an important part of 3D printing especially for models that are complex, and have a lot of overarching parts. If you think of a 3D print in the shape of the letter “T”, the lines on the side would require support because it cannot print in midair.
A smart thing to do would be to change the orientation and have the extended overhangs flat on the build plate, leading to a situation where supports aren’t needed, but in many cases, you can’t avoid using supports.
When you do finally use supports on your models, there are plenty of support settings that you will find in your slicer, allowing you to make some useful changes to make your supports more practical.
One of these is creating your supports in a way that makes it easier to remove from the model afterwards. The specific setting that can help with this would be the “Support Interface Density” in Cura.
This setting basically changes how dense the top and bottom of the support structure will be.
If you decrease the Support Interface Density, your supports should be easier to remove, and vice versa.
We can also use a simpler setting that is not in the “Expert” category to make supports easier to remove which is the Support Z Distance which I’ll explain further in this article.
There are plenty of support settings in Cura that you’ll never have heard of, and usually won’t ever have to adjust, but some can be practical.
Many of these settings you won’t even see in Cura until you change your settings visibility view, ranging from Basic, Advanced, Expert, and Custom Selection. This is found by clicking the 3 lines on the right side of your Cura settings search box.
Here are some of the support settings that are in Cura for a better idea (settings visibility adjusted to “Advanced”):
- Support Structure – Choose between “Normal” supports or “Tree” supports (will explain “Tree” further in the article)
- Support Placement – Choose between supports created “Everywhere” or “Touching Buildplate”
- Support Overhang Angle – Minimum angle at which to create supports for overhanging parts
- Support Pattern – Pattern of the support structures
- Support Density – Determines how dense the support structures are
- Support Horizontal Expansion – Increases the width of supports
- Support Infill Layer Thickness – Layer height of infill within the supports (multiple of layer height)
- Gradual Support Infill Steps – Decreases density of supports along the bottom in steps
- Enable Support Interface – Enables several settings to adjust the layer directly between the support and the model (“Expert” visibility)
- Enable Support Roof – Produces a dense slab of material between the top of the support and the model
- Enable Support Floor – Produces a dense slab of material between the bottom of the support and the model
There are even more settings under the “Expert” visibility view in Cura.
Now that you see what support settings are and how they can be useful, let’s get into more detail about other support settings.
How Do I Get the Best Support Settings in Cura?
Here are some support settings in Cura that you may want to adjust if you want to get your support structures optimized.
- Support Structure
- Support Placement
- Support Overhang Angle
- Support Pattern
- Support Density
- Support Z Distance
- Enable Support Interface
- Gradual Support Infill Steps
Apart from these, you can usually leave the rest of the settings on default, and that will be just fine unless you have an advanced issue that needs to be addressed with your supports.
What is the Best Support Structure?
The first setting you get when viewing support settings in Cura is Support Structure, and you have either “Normal” or “Tree” to choose from here. This is the type of technique used to form support structures for your model.
For printing uncomplicated models that require standard overhangs, most people typically go with “Normal.” This is a setting where support structures are dropped straight down vertically and printed below the overhanging parts.
On the other hand, Tree supports are usually reserved for more complex models that have delicate/thin overhangs. I’ll explain Tree supports in more detail later on in this article.
Most people go with “Normal” since that’s pretty much the default setting for it and works fine for the majority of the models.
What is the Best Support Placement?
Support Placement is another essential setting where you can determine how support structures are placed. You can either select “Everywhere” or “Touching Buildplate.”
The difference between these two settings are pretty simple to understand.
When you choose “Touching Buildplate”, your supports will be produced on parts of the model where the support has a direct path to the build plate, without another part of the model getting in the way.
When you choose “Everywhere”, your supports will be produced all over the model, in line with what support settings you have set. It won’t matter if your part is complex and has twists and turns all around, your supports will be printed.
What is the Best Support Overhang Angle?
The Support Overhang Angle is the minimum angle that is needed for supported to be printed.
When you have an overhang of 0°, every single overhang will be created, while a Support Overhang Angle of 90° will won’t create anything in terms of supports.
The default value you’ll find in Cura is 45° which is right in the middle. The lower the angle, the more overhangs your printer will create, while the higher the angle, the fewer supports that will be made.
Depending on the performance and calibration of your 3D printer, you can successfully use a higher angle and still be fine with your 3D prints.
Many 3D printer hobbyists out there recommends a value around 50° for the Support Overhang Angle, to ensure your 3D prints still come out nicely and save a little material from less support structures.
I’d definitely test this out for your own 3D printer and see what works best for you.
A great way to test your 3D printer’s ability, as well as your overhang performance is to 3D print the Micro All-In-One 3D Printer Test (Thingiverse).
It doesn’t translate directly into what Support Overhang Angle you can use, but it does allow you to test your ability to increase it further.
What is the Best Support Pattern?
There are many support patterns to choose from in Cura, which gives us the option to customize how our supports are built up. Depending on what you are looking for, there is a best support pattern for you.
If you want supports that are sturdy and can hold up well, you’ll do well with the Triangles pattern which is the sturdiest of all patterns, while Grid also holds up well.
The Zig Zag pattern is the best support pattern for overhangs, along with the Lines pattern.
If you are wondering which support pattern is easiest to remove, I’d go with the Zig Zag pattern because it bends inwards, and pulls off in strips. Cura supports that are too strong should use a support pattern that’s easy to remove.
I’ll talk about the other support patterns further down in this article, so you can understand them a little better.
Support Pattern and Support Density (the next support setting to be discussed) share a link together. One Support Pattern’s density could produce more or less material within a 3D print.
For instance, the Gyroid Support Pattern with 5% infill could prove sufficient for a model while the Lines Support Pattern with the same infill may not hold up as good.
What is the Best Support Density?
Support Density in Cura is the rate at which support structures are filled with material. At higher values, the lines in support structures will be held close to each other, making it appear dense.
At lower values, the supports will be further apart, making the support structure less dense.
The default support density in Cura is 20%, which is fairly good for providing a sturdy support to your model. This is what most people go with, and it works just fine.
What you can do is actually lower your support density to 5-10% and have good support interface settings to ensure your support works well.
You usually won’t have to increase your support density up too high to have good supports.
When you increase your support density, it does improve overhangs and decreases sagging since the supports are connected together densely. You are less likely to see your support fail if there is an issue during the printing process.
The opposite side of increasing your support density is that your supports will be harder to remove due to more of an adhesion surface. You’ll also be using more material for the supports and your prints will take longer.
However, a great place to start is usually around 20%. You can go lower and higher both depending on the situation, but 20% density is a good rule of thumb to keep using your support structures with.
The support pattern has a significant effect on how much support density is actually provided, in terms of how much material is used. A 20% support density with the Lines pattern won’t be the same as with the Gyroid pattern.
What is the Best Support Z Distance?
The Support Z Distance is simply the distance from the top and bottom of your support to the 3D print itself. It provides you with clearance so you can remove your supports easier.
Getting this setting right is fairly easy because it is rounded up to a multiple of your layer height. Your default value within Cura will simply be equal to your layer height, though if you need more clearance, you can 2x the value.
One user who tried this out found that supports were a lot easier to remove. He printed with a layer height of 0.2mm and a Support Z Distance of 0.4mm.
You usually won’t have to change this setting, but it’s nice to know that it’s there if you want to make supports easier to remove.
Cura likes to call this setting “the most influential factor in how well the support adheres to the model.”
A high value of this distance allows for a bigger gap between the model and the support. This translates to easier post-processing and creates a smoother model surface due to the reduced contact area with the supports.
A low value is useful when you’re trying to support complex overhangs which is making the support print closer to the support, but supports will get harder to remove.
Try playing around with different values of these distances to find the perfect figure that works for you.
What is Enable Support Interface?
The Support Interface is simply a layer of support material between the normal supports and the model, otherwise seen as the contacting point. It is made to be denser than the actual supports because it requires more contact with the surfaces.
Cura should have this turned on by default, along with the “Enable Support Roof” and “Enable Support Floor” to generate those denser surfaces at the top and bottom of your supports.
Within these settings in the “Expert” view, you’ll also find Support Interface Thickness & Support Interface Density. With these settings, you can control how thick and dense the top and bottom connection points of your supports are.
What are Gradual Support Infill Steps?
Gradual Support Infill Steps are the number of times to reduce the support infill density by half as the infill goes from top to bottom. The highest density of infill will be at the top surfaces of the model, all the way up to your Support Infill Density setting.
People tend to leave this setting at 0, but you should try this setting out to save filament without reducing the functionality of your model. A good value to set is 3 for normal prints, while larger prints could be raised higher.
In the sphere of 3D printing, experimentation is key. By tinkering around with different support settings but staying within logical boundaries, you’ll eventually find out values that get you going remarkably. Patience is a must.
What you can do is install the “Cura Settings Guide” plug-in from the app’s interface. This is a great way for beginners to understand how the software works and what different settings actually stand for.
What is the Best Support Pattern for 3D Printing?
The best support pattern for 3D printing is the Zigzag pattern because it has a great balance of strength, speed, and ease of Removal.
When choosing the best support patterns for your 3D prints, I’d mostly stick to the Zigzag and the Lines pattern because of their balance of speed, strength, and ease of removal. Zigzag, in particular, is also the fastest to print versus other patterns.
The other Support Patterns include:
- Lines
Lines closely resembles Zigzag and is one of the best Support Patterns as well. It is, however, stronger than Zigzag and makes for support structures that will be a bit harder to remove. On the plus side, you get solid supports.
- Grid
The Grid Support Pattern forms support structures in the shape of two sets of straight lines perpendicular to each other. This is followed by consistent overlapping that goes on to form squares.
Grid produces average overhang quality but is highly recommended for strong, reliable supports. However, since there will be little flexibility, supports can get rather difficult to remove.
- Triangles
The Triangles pattern is the strongest of all support patterns. It forms an array of equilateral triangles that allow it to exhibit little to no flexibility.
It produces bad quality overhang angles and will be the most difficult support structures to remove from your prints.
- Concentric
The Concentric Support Pattern is great for cylindrical shapes and spheres. They are easy to remove and will bend towards the inside with minimal effort.
However, the Concentric pattern is known to mess up here and there, oftentimes leaving the support suspended in midair.
- Cross
The Cross Support Pattern is the easiest to remove out of all the Support Patterns in Cura. It exhibits cross-like shapes in your support structures and draws a fractional pattern in general.
Cross isn’t the one to use when you require sturdy and firm supports.
- Gyroid
The Gyroid pattern is strong and reliable. It features a wave-like pattern across the volume of the support structure and provides equal support to all the lines of the overhang.
Gyroid is highly recommended when printing with soluble support materials. The air comprising a single volume allows the solvent to quickly reach the internals of the support structure, allowing it to dissolve faster.
Different patterns have varying strengths and weaknesses.
Many people agree that Zigzag is the best Support Pattern that Cura has to offer. It’s fairly sturdy, reliable, and exceptionally easy to remove at the end of the print.
Lines is also another popular Support Pattern that many people choose to work with as well.
How to Get Custom Supports Settings Perfect in Cura
Cura has now provided access to custom supports, a feature which used to be reserved for Simplify3D which is a premium slicer.
We can access custom supports by downloading a plugin within the Cura software called Cylindrical Custom Supports, found in the Marketplace on the top right of the app.
Once you find the plugin and download it, you’ll be prompted to restart Cura where you’ll then have access to these very practical custom supports. I’ve used them successfully on many prints now, they work great.
One of the best things about it is how all you need is to click in one area, then click on another, and you’ll create a custom support between those two clicks.
You can easily customize the shape, size, max. size, type, and even setting on the Y direction. These aren’t just for show as you can really create some high level supports very quickly for your models.
For support shapes you can use the:
- Cylinder
- Cube
- Abutment
- Freeform
- Custom
Your standard support settings that you set will apply such as infill density and pattern.
Check out the video below to see a visual tutorial behind how these custom supports work.
Best Cura Tree Support Settings for Cura
For the best Tree support settings, most people recommend a Branch Angle of anywhere between 40-50°. For Branch Diameter, 2-3mm is a great place to start. Moreover, you want to make sure your Branch Distance is set to at least 6mm.
Here are the rest of the Tree support settings you can find under the “Experimental” tab in Cura.
- Tree Support Branch Diameter Angle – the angle of a branch’s diameter growing towards the bottom (defaults at 5°)
- Tree Support Collision Resolution – determines the accuracy of collision avoidance in branches (defaults same as Support Line Width)
I wrote an article called How to Use Cura Experimental Settings for 3D Printing which you can check out.
The video below by CHEP goes into some detail about Tree Supports.
For Branch Diameter Angle, many users have set it to 5°. We want this angle to be oriented in such a way so that the tree support can stand strong without wobbling or shaking.
For Tree Support Collision Resolution, 0.2mm is a good figure to start with. Increasing it further could make the tree branches appear low in quality, but you will be saving more time. Try experimenting to see what works for you.
Tree supports are Cura’s unique way of generating support structures for your model.
If normal supports are taking a long amount of time for a part that’s relatively small, you might want to consider Tree supports, but that’s not the only reason why you should do that.
These tend to use less filament and post-processing is undeniably the best part of Tree supports. What they do is envelop the model and form branches that collectively create a shell around the model.
Since those branches only support selected areas of the model and form a shell-like shape afterwards, they usually pop right off with little to no effort and increases the chance of a smoother surface quality.
However, I recommend using Tree supports for models that are complex. For simpler models like parts of a 3D printer with average overhangs, Tree supports won’t be ideal.
You’ll have to evaluate yourself whether what model is a good candidate for Cura’s distinct support generating technique.
Best Cura Support Settings for Miniatures
For printing miniatures, a 60° Support Overhang Angle is safe and effective. You’re also best off using the Lines Support Pattern for more details in your minis. Additionally, keep the Support Density to its default value (i. e. 20%) and that should get you off to a good start.
Using tree supports for miniatures is really popular because they tend to have more complex shapes and details, especially when there are swords, axes, extended limbs involved, and things of that nature.
One user mentioned how he takes the STL file of his miniatures, imports them into Meshmixer, then has the software generate some high quality tree supports. After that, you can simply export the updated file back into an STL and slice it in Cura.
Check out my article Best 3D Print Miniature Settings for Quality.
You can get mixed results with this. It’s worth a try, but for the most part, I’d stick with Cura. Depending on the model, selecting your Support Placement to Touching Buildplate can make sense, so they won’t build on top of your miniature.
Using normal supports can work, especially if you create your own custom supports, but tree supports do work really great for detailed minis. In some cases, tree supports can have difficulty coming into contact with the model.
If you experience this, try making your line width equal to your layer height.
Another thing to add is to make sure you are using a good orientation in order to minimize supports. The right rotation and angle for your 3D printed miniatures can make a significant difference in how it turns out.
The video below by 3D Printed Tabletop is great for dialing in your settings to print some amazing miniatures. It usually comes down to a small layer height and printing at a low speed.
If you can tune your 3D printer to successfully 3D print some good overhang angles, you can reduce the number of supports. As mentioned above, a good overhang angle is 50°, but if you can stretch to 60°, it will make for fewer supports.
The Support Z Distance is another important setting to be wary of when printing minis. Depending on your model and other settings, this can vary, but a value of 0.25mm seems to work as a general standard for many profiles I’ve seen while researching around.
High-quality minis require carefully optimized settings, and while it’s difficult to print them perfectly right from the get-go, trial-and-error will gradually get you there.
In addition, another setting called Support Line Width appearing under the “Quality” tab in Cura seems to play a role here. Decreasing its value would reduce the gap between your Tree support and model.
How Do I Fix Cura Support Settings That Are Too Strong?
To fix supports that are too strong, you should decrease your support density, as well as use the Zigzag support pattern. Increasing your Support Z Distance is a great method of making supports easier to remove. I’d also create your own custom supports, so they can be built as little as necessary.
The Support Z Distance can affect directly how hard or easy it is to remove supports from your model.
Found under “Expert” settings, Support Z Distance has two subsections – the Top Distance and the Bottom Distance. The values of these change in accordance with what you put under the main Support Z Distance setting.
You want the Z Distance value to be 2x your layer height so there is extra space between your model and the supports. This should make the supports a lot easier to remove, as well as being enough to properly support your model.
If you don’t want to use custom supports for any reason, like there are too many supports to add, you can use another feature in Cura called Support Blockers.
It is used to remove supports where you don’t want them to be created.
Whenever you slice a model on Cura, the software determines where support structures will be placed. However, if you see that support isn’t needed at a particular point, you could use the Support Blocker to remove unwanted supports.
It’s fairly simple, but you can get a better explanation by watching the video below.
Adding and Modifying Support Structures
In this tutorial, we will explain everything you need to know about support structures. These thin, break-away structures are used to support steep overhangs and cantilevered sections of your model. The Support Generation Tool makes it easy to add, move, or delete supports. The supports appear as individual pillars in the software, but are constructed as a network of interconnected pieces for easy removal from your model.
When to Use Supports
When do you need supports? Supports are used when models have steep overhangs or unsupported areas. For example, if you printed an arch, the very center of this arch might require support material because when your printer tries to print that top layer, there would be nothing else supporting it from below. If you tried to print this arch without support material, you might notice that the top layers of the arch seem to sag and droop because there is nothing to support the molten plastic as it is extruded out of the nozzle.
A general rule of thumb is that most extrusion-based printers can support overhang angles less than 45 degrees. At these shallow angles, the majority of the plastic layer is supported by the previous layer below it. If you go to steeper overhang angles, you might start to notice the edges of your layer begin to deform, and that is when you might want to consider adding support material to the part.
To begin, let’s look at a common model that can help identify what types of overhang angles your printer can support. The Massive Overhang Test by thingster can help identify what types of angles your printer can smoothly produce. If you try to print this part on your machine, you will probably notice that the 60-70 degree sections will not be as smooth as you would like. The performance of these overhangs will depend on your layer height, temperature, material, and several other factors, but this test part will help establish a useful baseline of what types of angles your machine can support. As an example, let’s assume that your massive overhang test print shows that any angle greater than 45 degrees would start to require support material. We will use this information in the next part of the tutorial.
How to Add Supports
When you encounter a model that will require support material, Simplify3D makes it easy to add them to your print. Let’s start by importing a model that we know will require support. We will be using alien000′s Moai statue. Note that this model is fairly large, so you probably want to scale it down to about 25% of its original size after you import it into the software (if you need help with this step, please read our Importing and Manipulating Models tutorial). When looking at this model, it is clear that there are several areas that will probably violate our 45 degree overhang angle limit. Add a new FFF process, or edit an existing one, in order to print the Moai model. To add support material for this model, open the settings for your FFF process and enable the Generate Support Material option. If you click Prepare to Print!, you will notice that the software has already added the necessary support structures for the nose, chin, eyebrows, and ears.
How to Modify Where Support Material is Placed
While the software makes this process extremely easy, it also offers additional options if you want more control over where the support material is placed. For example, what if you didn’t want to print support material inside the Moai statue’s nose? Maybe you have printed this model before and the nose printed well without the support material. If you could remove the support material from this location, it would give you less to clean up at the end of the print. To do this, first we need to return to the model view. If you were previously looking at a line-by-line G-Code preview, be sure to exit the preview so that you are looking at the raw digital model of the Moai statue. To open the support generation toolbar, go to Tools > Customize Support Structures, or click the very last icon in the toolbar on the right side of the screen.
The support generation toolbar consists of several sections. The top section contains all of the automatic support generation options that allow the software to give you a recommendation about where it thinks support material is needed. This can save a lot of time by giving you a starting point for any later modifications. You can also change the Support Type from Normal to From Build Platform Only, which will only generate supports that are touching the build plate, which can be useful if the supports generated will be trapped within the part or otherwise difficult to remove. Once you select an option, press the Generate Automatic Supports button. This will produce a preview of the recommended support structures based on the overhang angle that you specify. This preview shows a series of vertical pillars that represent where support structures would be needed. Note that the pillar shape is simply a preview. The actual print will still use the same back-and-forth webbing pattern that you saw earlier in the G-Code preview. The only other option in this section is the support pillar resolution, which determines the size of each individual support pillar. If you have a very complex model with lots of tiny features, you might want to use a smaller value like 1-2mm. In this case, the features are all large and pronounced, so a resolution between 4-6mm should be fine. A larger resolution also makes the pillars easier to interact with.
The next section in the support generation toolbar includes a few options that will help us manually add or delete existing support material locations. We can combine these tools to get the perfect support material layout for our model. We mentioned earlier that we might want to remove the support material under the Moai statue’s nose. To do this, simply press the “Remove existing supports” button and then left-click the support pillars on the screen that you wish to delete. When you are done removing these pillars, click the “Remove existing supports” button again to exit that mode. If you want to add support material in new areas of the model, the process is very similar. In this case, you would click the “Add new support structures” button and then click on the locations where you would like the new support pillars to be placed. As before, click the button a second time when you are finished to exit that editing mode.
Saving Your Factory File
After you have made several changes to your model’s support structures, you may want to save your work so that you reload it later on. The best way to do this is to simply save a “factory file” for your current workspace. The factory file will contain your imported STL file, the support structures you have created, any FFF processes you have defined, and even the orientation and positioning of the models on your build table surface. It is a great way to save all of your work so that you can pick up right where you left off or to share your file with a friend who has a similar machine. To save a factory file, go to File > Save Factory File As. You also have the option to save the support structures by themselves from within the support generation toolbar, but this is typically not recommended as it will not include the relative placement of the original STL file.
When you view your supports on your monitor, they appear as individual pillars, but when they are constructed, the supports will be constructed to form a network. These support networks are easy to remove from your part! In the image on the left, you can see supports as they are added, previewed, constructed and removed.
Advanced Support Settings
There are additional FFF settings that are available to control how the actual support structures will be printed. To display these options, click Show Advanced in the bottom left of your FFF settings. This will bring up several additional tabs that contain many of the advanced settings that are used to produce your prints.
Click on the Support tab to see the various settings that control how your support material is printed. Notice that the Automatic Placement section includes the exact same options that were found in the support generation toolbar. If you do not need to manually edit the support structures for your model, you can simply configure these settings appropriately and let the software automatically generate the support structures without needing to open the Customize Support Structures window like we did previously.
The Separation from Part section includes all of the settings that determine how easily the support material will break away from your final solid part. The horizontal offset will determine how much spacing there is between the support structures and the outline of your part. If you are having trouble removing your support material, you may want to increase this setting so that there is a larger gap between the support and the part. A value between 0.2-0.4mm is usually sufficient. Once you have entered the desired values, click Save so that the next model preparation will use the updated settings.
Congratulations! You have now covered everything you need to know about adding and modifying support structures in the Simplify3D Software! The ability to modify where these break-away structures are placed can make a big impact in the quality of your prints and can save you a lot of post-processing time.
View the Complete Article Library
How to optimize the settings of supports (calipers) in Cura
3DPrintStory     3D printing process     How to optimize support (caliper) settings in Cura
All Fused Deposition Modeling (FDM) 3D printers create objects by extruding thermoplastic material layer by layer. Therefore, each layer must be supported by the layer below it. When there is no layer under a part of the 3D model (as in the case of overhangs and bridges), support structures may be needed. They are printed with the main model and removed during post-processing.
You might be thinking, "That doesn't sound too scary." However, the word "support" horrifies many 3D printer users. Some even consider it almost profanity. After all, support structures not only require more material, but they are also known to negatively affect surface quality and are difficult to remove.
Unfortunately, some models simply need supports. But this does not mean that we cannot optimize them by changing the appropriate settings.
In this article, we will first talk about when you need support and when you don't. Then we'll look at some of the important caliper settings in Cura to tweak them for the best results.
Note . This article is written specifically for Ultimaker Cura users, but the basic principles behind the settings can be applied to various other slicers.
Do you need calipers?
To determine if you need support structures, there are a few things to consider:
- 45 degree rule (overhangs): if overhangs are more than 45 degrees (from vertical), they will need support. To test your 3D printer's capabilities in terms of maximum overhang angles, try printing this test 3D model. When your 3D printer stops printing adequately at a certain stick-out angle, that's the angle you need to use additional supports to reach.
- 5mm rule (bridges): if bridges are wider than 5mm, they may need support. Of course, not all 3D printers are the same. Some can print over long distances. Others can hardly print thinner ones. Try printing this test model to see if your 3D printer needs calipers. You'll know the maximum bridge length you need after which calipers are needed when you see that the bridges in the test model start to sag.
Once you've decided you need calipers, let's take a look at the Cura settings to get the most out of them.
Support Settings
Cura has several settings to help you optimize the support of your 3D models. Here's where to start:
When you first open Cura, click "Custom" in "Print Settings". Here you can adjust settings that are otherwise hidden in the "Recommended Settings" section.
Right click and select "Configure Setting Visibility"
Select "Check All".
You can now see all the settings that Ultimaker provides in Cura. Scroll down to support settings, click "Generate Support", and now we can start tweaking the support settings for your 3D model!
Support Placement
After you click "Generate Support", the first setting will be "Support Placement". Here you can select "Everywhere" or "Touching Buildplate". You probably guessed that this determines whether supports are printed everywhere (where necessary) or based only on the desktop.
In most cases, it's better to choose "Touching Buildplate" because supports all over the surface of your 3D model can cause nasty imperfections on the surface of the finished product.
However, sometimes supports are needed everywhere. This is the case with really complex models that cannot be printed without additional calipers.
Support Overhang Angle
With the "Support Overhang Angle" setting you can specify the maximum overhang angle above which you want to use the supports. As mentioned earlier, the default angle is usually 45 degrees. However, this angle may be different for your particular 3D printer. So you should first check this parameter using a test 3D model.
By the way, this angle may also differ depending on the features of a particular 3D model. 0 degrees is the generation of calipers for each minimum angle of overhang, 89 is the minimum of supports, respectively.
Support Patterns
Ultimaker Cura supports various "Support Pattern" patterns. Each of the templates balances strength and ease of removal.
Quick and easy
- Zig-zag (zigzag) - the fastest in execution and the easiest to remove.
- Lines is an evolution of the previous template. They are still great, easy-to-remove supports, but are slightly stronger than zig-zags and usually don't come off in one piece.
- Concentric - best for models that are close to spheres or cylinders. As a rule, it is slightly stronger than zigzags and lines.
Note that due to the unidirectionality of the above three patterns, they tend to be more vulnerable. For example, vibrations and thin support structures can cause the nozzle to not align perfectly with previous layers, which can cause problems in the long run.
What's more, if these patterns are even slightly caught by the moving nozzle, they can break away from the surface below and collapse like an accordion!
Robust
and grid (grid) and triangle (triangle) are excellent templates for obtaining strong supports. They are resistant to vibration, but increase 3D printing time and generally have better contact with supporting surfaces. This can make post-processing difficult.
Support Density
"Support density" is very similar to fill density in the sense that you choose a compromise between strength, speed and ease of removal.
High density support structures are generally more rigid and can withstand vibration. In addition, the increased contact with the lugs makes the high density supports ideal for intricate or detailed supports. With high densities, expect stronger support, but more material usage, longer print times, and more complex post-processing.
Low density bearings are ideal for general bearing surfaces that do not require many contact points. Low density calipers are more likely to react to vibration during 3D printing, but they reduce material cost, 3D printing time, and ease of removal.
Caliper density of 20% is a great value to start with, but feel free to change this value to suit the needs of your 3D model.
Z Distance
This important parameter determines the distance from the top and bottom of the supports to the 3D model. This parameter consists of two sections: upper distance and lower distance.
A high value for these distances allows for a larger clearance between the model and the support, which simplifies post-processing and creates a smoother 3D model surface due to fewer contact points. A low value is useful when you are trying to support complex protrusions that require high detail. However, with a low support value, it is more difficult to remove.
As with many settings, experiment with these distances to find the perfect fit for your 3D printer.
X/Y Distance
X/Y Distance is very similar to Z Distance. This setting adjusts the horizontal distance between the model and its support.
Again, the further the distance, the easier it is to remove the support. The shorter the distance, the stronger the support structure.
As a rule, a larger X/Y distance means a better surface quality in vertical sections. If the vertical parts on your models are uneven due to adjacent supports, try increasing the X/Y distance.
A smaller X/Y distance will result in better support for overhangs, namely those located near vertical surfaces. However, they can cause defects in vertical surfaces and complicate post-processing.
Support Distance Priority
Depending on the type of plumb line you are trying to print, the Z distance may conflict with the X/Y distance. In Cura, however, you can set the priority in these distances so that in the event of a conflict, the most important is preserved.
It's generally better to have Z override X/Y because the Z distance is what the model actually supports. However, you can always change this override setting if the specific 3D model requires it.
You can also set the minimum X/Y distance. Then, even when the Z distance takes precedence, the minimum X/Y distance is still kept.
Join Distance
The Join Distance allows you to set the maximum horizontal distance between support structures. When two support structures are closer together than this value, they will be printed as one structure. The higher the value of this distance, the faster the supports will connect. If the support structures are particularly thin, this can help provide more support for the 3D model.
However, if you set the value too high, the support structures can become tight and difficult to remove.
Horizontal Expansion
When the support surfaces are very thin, it is difficult for your 3D printer to create strong structures in a small area. The "Horizontal Expansion" option allows you to set the horizontal expansion so that even small anchor areas are adequately supported.
Entering a large value for this setting will always result in stronger supports, but this setting requires your 3D printer to use more material.
Towers
For very small protrusions, Cura allows you to print towers that taper at the top to support areas smaller than the minimum diameter you set (other areas will use regular support structures.)
the towers were not too weak, they had a larger diameter than the area they supported. You can always change this diameter in Cura. You can also adjust the angle at which your towers rise to a certain point to make the towers flatter or sharper.
CURA settings. Programs for preparing 3D printing. / Articles
Share:
Cura is designed to translate 3D models into G-code and print on a 3D printer. Source
Cura is designed to translate 3D models into G-code and print on a 3D printer.
Download
Settings for 3D printer Mendel90 and similar
Cura first launch
Choosing your 3D printer
We set the dimensions of the press area
Setting up printing parameters
General settings
Print quality
1 - thickness of the seal layer. Depends on nozzle diameter. Good quality - 1/2 nozzle diameter. The best quality is 1/4 nozzle diameter.
2 - Wall thickness. Must be a multiple of the nozzle diameter. Single wall - worse appearance, but better strength if the filling is 100%.
3 - Rollback (Retract). Suction of the melt of plastic, when moving to another island of printing.
Infill
4 - Thickness of the top and bottom of the part. The thickness of the top affects if the percentage of filling of the part is low and the thread sags a lot. There may be torn holes and frozen threads of plastic sticking out.
5 - Percent complete part. The density of the lattice inside the part. 0% - there will be a hollow part. Needed for strength and support of the upper layers.
Speed and temperature
6 - Print speed. Taken into account if detailed settings are not specified on the "Advanced" tab.
7 - Nozzle temperature. Depends on the type of plastic. ABS 210-270C, PLA 180-210C.
8 - Table temperature. ABS 105-115C. For PLA 70C on Kapton tape and 0C on blue tape.
Support
9 - Type of support. Support is needed for overhanging and sloping surfaces of the workpiece to prevent sagging threads:
None - do not use support.
From the surface - support to a minimum.
Everywhere - support to the maximum.
10 - Type of strengthening of adhesion (sticking) to the table:
None - nothing. Only circles around part
Border - an increase in the area of \u200b\u200bthe part for better adhesion to the table and protection against corners coming off. It is configured in the "Advanced" tab.
The substrate is a lattice multilayer substrate for the part. Used for parts with a small area of contact with the table. It is configured in the "Advanced" tab.
Rod (filament, thread)
11 - The diameter of the rod used. You need to measure with a caliper for accuracy.
12 - Percentage change in the amount of filament extruded from the nozzle. Adjustable for each coil of plastic individually. If the gaps between the threads on the fill - you need to increase, if the part turns into a mess - you need to reduce.
Advanced Settings Tab
Printer (Nozzle)
1 - Nozzle Orifice Diameter
Rollback (Retract)
2 - Rollback speed of the bar. At high speed, the extruder bolt can rip off the bar layer and lose traction.
3 - Retract length. If, when the nozzle moves to the next part of the part, a thread flows out of the nozzle, you need to increase the parameter.
Quality (First coat)
4 - Thickness of the first coat. Depends on the curvature of the table and the diameter of the nozzle.
5 - Width of the first layer in percent. affects the quality of adhesion. Higher is better. If there are gaps between the threads on the first layer, you need to add%.
Speed (Detailed print speed setting)
7 - Idler transition speed, no plastic extrusion. At idle, it can touch hardened protruding plastic threads. Minimum speed 80 mm/s.
8 - First layer print speed. Below is better. Recommended speed 20 mm/s.
9 - Part fill rate. Can be more. Usually 60-120 mm/s.
10 - Decrease the speed for a smooth top surface.
11 - Outline printing speed. At 20 mm/s excellent surface quality is obtained.
12 - The speed of printing the inner layers of the contour. Average between fill rate and outer outline print speed. At high speed, it affects the quality of the outer contour.
Cooldown
13 – Minimum layer print time, gives the layer time to cool before moving on to the next layer. If a layer is laid too fast, the 3D printer will slow down the layer to match the specified time. I usually set it to 20 seconds.
14 - Turn on the fan to cool the part while printing. Used only for PLA-like plastics. On ABS it impairs the adhesion of the layers.
Additional print settings
inclusion of additional settings
Detailed settings
The same settings appear in the Mini menu "Advanced"
Retract - absorption of plastic thread
9000.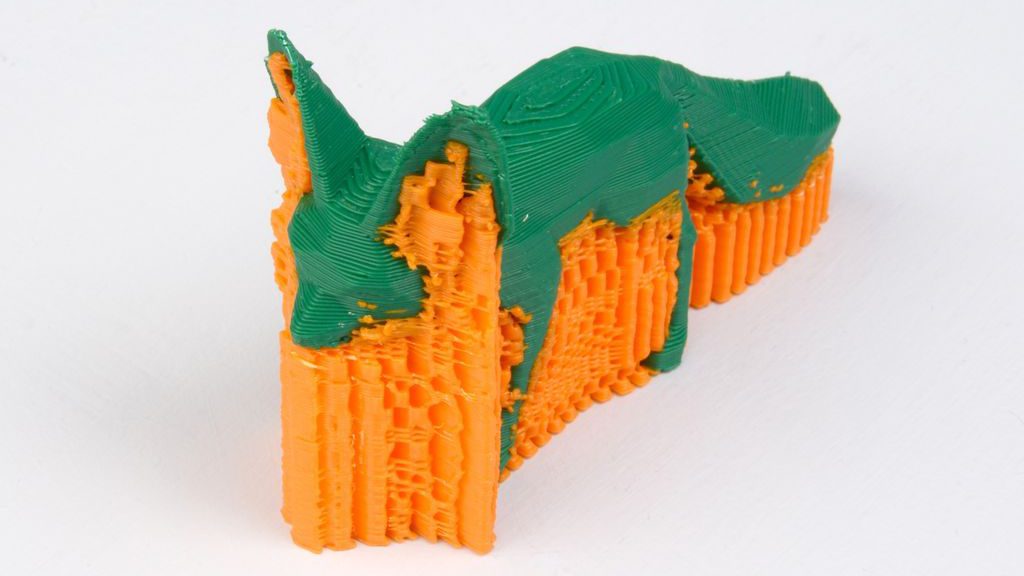
Outline (Skirt) - extrudes plastic around part to prepare nozzle for part
10.3 — Number of plastic extrusion rings around the part.
Workpiece cooling
14.1 — At what height to turn on workpiece cooling.
14.2 - Minimum cooling fan speed.
14.3 - Maximum fan speed.
14.4 - Minimum threading speed limitation.
14.5 — Move the nozzle away from the part for better cooling. The time after which to retract the nozzle is configured in Detailed settings\Cooling\Minimum time per layer (sec.).
Fill
5.1 — Fill the upper layer. For printing empty and open parts (vases, glasses).
5.3 Percentage of thread overlap. For better adhesion of the threads between them.
Supports
9.1 - Structure of supports:
Grid - lattice,
Lines - lines. Easier to remove.
9.2 — Angle of slope at which supports begin to form. I put 60 degrees.
9.3 — Density of the support structure, in percent.
9.4 — Distance from part walls to supports along XY axes. The smaller, the more difficult it is to remove support.
9.5 — Distance from the bottom surface of the part to supports along the Z axis.
Brim — Increase in the area of contact between the part and the table
10.1 — Width of the field, in thread lines.
Underlay (Raft) - needed for printing parts with a small touch area with a table
10.2 - Adjusting Raft parameters0198
15 - Automatic correction of some errors 3D model
Additional menus on the Basic tab "Basic" repeat the settings of "Detailed" settings
An additional menu on the "Advanced" tab "Advanced" repeats the settings of "Detailed settings"
Save settings to a file and restore
Desktop manipulation
Desktop window
1 — View of the part on the desktop.
2 - Download file and add 3D model to desktop.
3 - Start printing on a 3D printer or save the G-code of the program to an SD card or hard disk, for offline printing from an SD card.
4 — Estimated time to print the part.
5 Calculated bar length for this part.
6 - Calculated weight of the part with all additional structures.
7 - Part view options.
8 - View the loaded 3D model of the part.
9 - Layered view of the part with all additional structures.
1 - Layered view of the part with all additional structures.
2 — Total number of layers of the part.
3 — Viewed layer.
4 - Internal filling structure.
5 — Structure of supports.
6 — Appearance of the skirt, with all settings.
Rotation of the part along the axes
When you left-click on a part on the desktop, icons appear in the lower left corner:
1 — Rotate the part along the axis. Drag the selected axis with the left mouse button.
2 — Rotation angle is displayed.
3 - Reset to home position.
4 — Alignment of the bottom plane of the part, relative to the work table.
Modify part dimensions
1 — Modify dimensions icon.
2 — Drag with the left mouse button pressed to change the dimensions of the part.
3 - Reset changes.
4 - Maximum dimensions.
Reflection of the part in planes
Before printing
Entering the settings
Change the appearance of the interface
Cura program interface in the style of the Pronterface program, during printing.
Change the starting G-code
1 - Here we can change the XYZ coordinates of the initial exit of the nozzle above the table
2 - Here we adjust the amount of extruded plastic (E). A positive value is to squeeze out, a negative value is to retract. Extrusion is needed to fill the nozzle with melt before printing, so that there is no gap at the beginning of the print.