3D rubber print
3D Print Rubber - 3D Printing Gaskets
Rubber and rubber-like materials are everywhere in modern industry. Soft materials like latex, silicone, and thermoplastic elastomer are useful in applications that demand flexibility and durability for industrial parts and consumer goods alike.
While rubber manufacturing has historically been the domain of casting and injection molding, modern advances in 3D printers and 3D printed materials have made additive manufacturing the ideal solution for producing small to medium quantities of rubber-like parts.
Our 3D printed rubber services can manufacture high-quality rubber-like parts in as few as two days―all you need is a 3D model! Start your project by getting a quote or keep reading to learn more.
Get a quote for your project using our quoting tools. Our engineers will review your project and get back to you 24 hours or less. 3D printed rubber parts ship in as few as two days!
3D Printed Rubber Applications, From Prototyping to Production
3D printed rubber parts can be used in place of molded rubber for just about any application. Like other methods of 3D printing, rubber prints accurately produce complex internal geometries like lattices and tubes at no extra cost, easily achieving designs that would be impossible with other types of manufacturing.
And because 3D printing doesn’t require any costly molds or tooling, 3D printed rubber parts can be manufactured in just a few days compared to multiple weeks of lead time for injection molding. This combination of high agility and no start-up costs allows rubber 3D printing to excel for both prototyping and small- to medium-sized production runs.
3D printed rubber is ideal for:
Prototypes
Gaskets
Seals
Hoses
Grips
Lids
Plugs
Connectors
Footwear
Tires
Medical Devices
Sporting Goods
Advantages of 3D Printed Rubber vs.
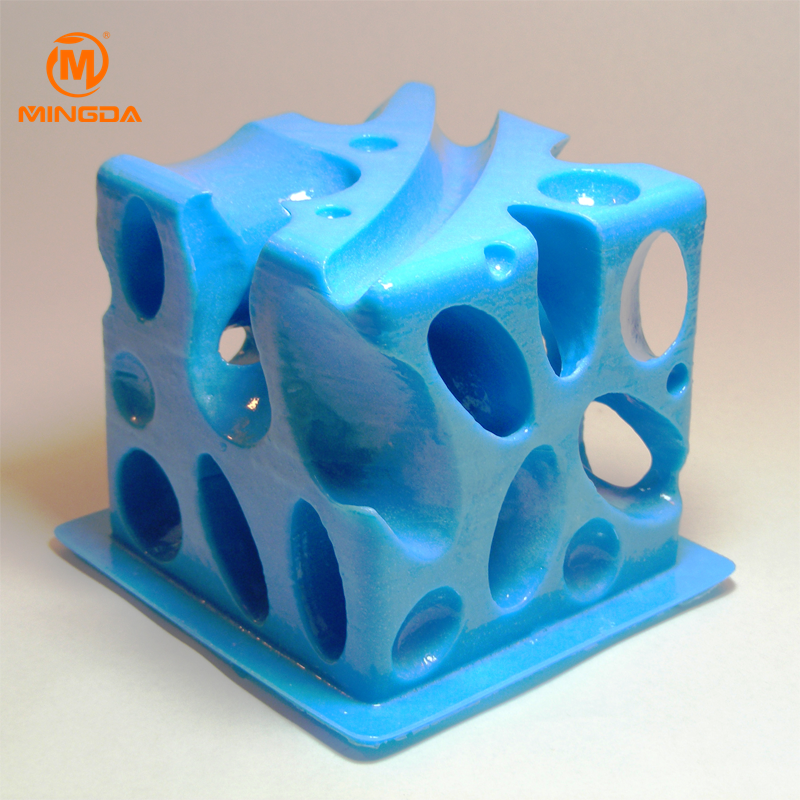
Traditionally, rubber manufacturing has required injection molding, casting, or sheet lamination. Rubber-like materials are far too soft to machine, and 3D printing was restricted to harder plastics for most of its development. Now, new developments in 3D printers and materials have opened up a wide range of new possibilities for 3D printed rubber products. So how does 3D printing compare to casting or injection molding for manufacturing rubber?
Short Lead Times and No Setup Costs
Injection molding requires machined metal molds that cost tens of thousands of dollars and take months to produce. Any design changes require new tools, making adjustments extremely expensive and time-consuming.
In contrast, 3D printing requires no tooling or other setup costs and can begin production immediately. This leads to parts that can be manufactured in as little as one day and much greater affordability at low quantities, making 3D printing Moreover, design changes are easy and can be executed at no additional cost.
The Best Choice for Rubber Prototypes
When it comes to product development, 3D printed rubber is a godsend. Even under the most ideal conditions, traditional technologies take weeks of lead time and tens of thousands of dollars for each new design.
Because 3D printing doesn’t require any tooling or setup, 3D printed parts can quickly be designed and redesigned at no additional cost. This agility has made 3D printing an indispensable part of prototyping and product development.
A Question of Quantity
As a result of these differences in lead times and setup costs, 3D printing is much more economical for small- to medium-volume production, while casting and injection molding provide greater value for productions of 1000 parts or more.
Although metal molds are expensive, molded parts become very cheap to produce once the tooling is made. When those initial costs are spread out over thousands of parts, individual part costs plummet, making injection molding the least expensive technology around for high-volume manufacturing.
3D printing, on the other hand, generally stops providing additional per part savings once part quantities exceed the capacity of a single machine. As a result, 3D printing has a much flatter cost curve that makes it a great option for small to medium quantities but significantly less economical for large production runs.
Unlimited Design Possibilities
Rubber 3D printing can easily achieve complicated designs that would simply not be possible with other manufacturing technologies. From interior cavities and lattices to variable wall thicknesses, organic shapes and built-in hoses—all of which are difficult or impossible to create with injection molding—3D printed rubber parts unlock endless new design options. You can even combine multi-part assemblies into single pieces, saving costs and improving functionality.
Plus, 3D printed parts can be highly customized, down to single parts at a time, without additional costs. This is especially useful for industries like medicine or athletics that have a high demand for products customized to each individual user. Needless to say, this would be extraordinarily expensive with casting or injection molding.
To learn more about the unique design capabilities of 3D printing, check out our Design for Additive Manufacturing (DfAM) Guide.
Is It Really Rubber?
3D Printed Rubber Materials
The answer to whether 3D printed rubber is really rubber depends who you ask. There are a lot of materials that are referred to as rubber: thermoplastic polyurethane, thermoplastic elastomer, silicone, and, of course, natural rubber!
Natural rubber, also known as latex, cannot be liquefied and re-solidified in the manner required by 3D printers. However, thermoplastic elastomers can achieve similar levels of flexibility and softness to rubber and have the thermal properties necessary for 3D printing.
The most effective rubber-like materials for 3D printing are thermoplastic polyurethane (TPU) and thermoplastic elastomer (TPE). It’s important to note, however, that both TPU and TPE refer to multiple materials. In fact, TPU is really a type of TPE―distinguished by its use of polyurethane and increased hardness.
Thermoplastic Polyurethane (TPU)
Thermoplastic polyurethane (TPU) is valued by engineers for its flexibility and strength. It’s in mass production consumer products ranging from automobiles to tennis shoes. Not only does TPU’s hardness (Shore 85A to 95A) make it easy to manufacture, but it also provides higher abrasion, chemical and thermal resistance. Moreover, its resistance to oil and grease makes it a great fit for hoses, gaskets and seals. While not as soft as natural rubber, printed TPU can achieve thinner walls than molded parts (0.5mm or 0.020″) to create a similar level of flexibility.
TPU can be 3D printed with Multi Jet Fusion and is widely used in transportation, medicine, home goods, footwear and apparel, heavy industrial, consumer electronics, and more.
Rubber Printing Services
Multi Jet Fusion (MJF)
Multi Jet Fusion 3D printing is the fastest, most affordable, and most effective option for most 3D printing projects. It is also the newest printing technology to allow rubber printing, with TPU01 options available in black or gray.
MJF prints combine industrial strength, accurate fine details and a high-quality finish to create parts that are equally suited to industrial parts and commercial products. With lead times as little as one day, MJF is the premier printing option for prototypes and small- to medium-sized production runs.
Start Rubber 3D Printing Today
If you need rubber manufacturing for your business, RapidMade can help you take your projects from 3D models to high-quality 3D printed rubber parts in as few as two days. When you work with RapidMade, you get a team of 3D printed experts dedicated to helping you succeed.
Learn more about our 3D Printing Services and get started today by requesting a quote. We’ll review your project and get back to you within one day!
What's possible and what isn't
Natural rubber, harvested from the rubber tree, is a highly desirable elastomer used in everything from waterproof boots to electrical insulation. But rubber is difficult to manipulate and shape. Once hardened, the gummy material can’t be melted back into a liquid state suitable for extrusion.
Fortunately, the desirable properties of rubber — flexibility, abrasion resistance, vibration dampening — can be approximated with other types of 3D printing material, using various 3D printing technologies.
This article takes a closer look at the ins and outs of 3D printed “rubber”, examining options like 3D printable filaments and resins, as well as new possibilities like 3D printed silicone.
Natural rubber is harvested from trees and cannot be 3D printed
When people talk about rubbers, they might be referring strictly to natural rubber — sometimes called India rubber or latex — which is an organic material harvested from the rubber tree, or they might be using the term in a slightly looser sense to describe elastomers, which are a large and varied group of elastic polymers.
So if we want to ask whether it is possible to 3D print rubber, we need to differentiate between natural rubber (specific) and elastomers (broad). In short, it is not possible to 3D print natural rubber because the material cannot be melted, cured, or manipulated in a way that is useful for any currently recognized 3D printing process.[1] With the right knowledge and equipment, however, it is possible to 3D print elastomers.
3D printable elastomers include flexible filaments like thermoplastic polyurethane (TPU) for fused deposition modeling and flexible resins for vat photopolymerization. In many cases, material suppliers offer these materials in different levels of flexibility, as the hardness level can be modified chemically.[2]
In recent years, a handful of companies have even found ways to 3D print silicone rubber — a material more valuable than typical 3D printable elastomers due to its biocompatibility.
Fused deposition modeling (FDM) is the most common 3D printing process, as it is compatible with a range of affordable thermoplastic materials like PLA, ABS, and PETG.
Although these materials offer different levels of rigidity, none of them is particularly flexible. The exception within the catalog of FDM materials is a category of thermoplastics called thermoplastic elastomers (TPE), the most notable of which is thermoplastic polyurethane (TPU). The printing characteristics of TPU and other elastomers are vastly different to those of stiff materials like PLA: although they have very low tensile strength, these materials possess properties like flexibility, impact resistance, high elongation at break, and good shock absorption.
There is a catch though. Flexible materials can be much harder to print than rigid ones, often producing blobs and stringing while offering poor bridging capabilities. To mitigate these problems, a direct drive extruder is required, and the printer should be configured with a slow feed rate and minimal retraction.
Common rubber-like filaments include:
TPE filament
TPU filament
Soft PLA filament
Flexible filaments are suitable for 3D printed parts like flexible prototypes, seals, soft-grip handles, smartphone cases, flip-flops, shoe soles, and vibration dampeners.
Flexible filaments like TPU have rubber-like properties
FDM is not suitable for all 3D printing projects, as it produces a substandard surface finish and limited level of detail. Fortunately, it is also possible to use flexible materials for vat photopolymerization processes — stereolithography (SLA) and digital light processing (DLP), for example — which typically offer superior smoothness and part resolution. Although less common than FDM, these technologies can be found in many consumer-level desktop machines.
An advantage of using flexible resins is that they are much more printer-friendly than flexible filaments, as the light-curing process is not susceptible to issues like blobs and stringing. However, photopolymerization printers and resins are more expensive than FDM hardware and filaments. Flexible resins are not easily categorizable, as each formulation is unique to the specific material developer.
Flexible resins are suitable for 3D printed parts like flexible prototypes, gaskets, seals, soft-grip handles, wearables, and stretchable enclosures.
Another plastic 3D printing process suitable for the production of high-quality, rubber-like parts is selective laser sintering (SLS). Although SLS is generally limited to professional and industrial applications, it provides good results using materials like TPE and TPU. Print quality is superior to FDM, and larger parts can be made when compared to vat photopolymerization.
Individuals and smaller companies can still obtain TPE/TPU parts made using the SLS additive manufacturing process by using a 3D printing service.
Other professional-grade additive manufacturing processes that use flexible materials are traditional material jetting and Multi Jet Fusion from HP.
Widely available 3D printing technologies like FDM and SLA are not capable of 3D printing silicone rubber — a high-value elastomer with useful characteristics like biocompatibility, thermal stability, and UV resistance. However, some companies have developed novel technologies for printing silicone, with promising results.
Silicone rubber starts out in liquid form, and can only be turned solid by curing, vulcanization, or catalyzation. To print silicone, the liquid must be selectively deposited (in a drop-on-demand manner, for example) and then solidified using one of the three processes. A further stage of curing is then usually required to achieve full strength.
Silicone 3D printing is not particularly accessible, and some technologies are still in early development. However, it holds promise in areas like medical 3D printing.
The properties of rubber that make it unsuitable for FDM 3D printing also apply — to a limited extent — to injection molding, as both technologies depend on heating up plastics to melting point then allowing them to cool and re-solidify.
Like 3D printing, injection molding can make flexible parts using materials like TPU, which can be processed like a rigid thermoplastic (i.e. melted, formed, then cooled) while still offering flexibility and other rubber-adjacent characteristics.
That being said, liquid silicone injection molding, a specific variant of the injection molding process that does not apply high levels of heat, has the additional benefit of being able to process liquid silicone rubber (LSR) for items like medical devices.
FDM 3D printers cannot extrude LSR because the material has a viscosity similar to water. In liquid silicone injection molding, however, the two components of LSR can be mixed together then cured within the injection mold. Despite initially being in a fluid state, the silicone will hold its shape, because it is enclosed on all sides by the mold (unlike with 3D printing, where the part must support itself as it is being built).[3]
Liquid silicone injection molding even offers greater design freedom than plastic injection molding, as silicone parts are flexible enough to be removed from the mold without the use of draft angles. However, the high viscosity of the silicone leads to a high degree of flash — material seeping through the parting line.
3D printing and injection molding have their own advantages and disadvantages when it comes to making flexible parts, as shown below.
3D printing | Injection molding | ||
Advantages | Disadvantages | Advantages | Disadvantages |
Affordable even in low quantities | Limited range of materials | Highly scalable | High tooling costs |
High level of geometrical freedom | Surface quality and detail limitations | Suitable for liquid silicone rubber | Geometrical limitations |
Injection molding is a good alternative to 3D printing when making flexible parts
An alternative to directly printing flexible parts or injection molding flexible materials is 3D printing rigid molds — using a heat-resistant material like ABS — that can then be filled with a material like liquid silicone. This process combines some of the advantages of 3D printing and molding, and is inexpensive.
Molds can be designed using CAD software and fabricated like any 3D printed part. The cavity is coated with mold release spray then filled with the two parts of the liquid silicone, with curing taking around 90 minutes. A vacuum chamber may be used to de-gas the silicone, preventing the buildup of air bubbles.
This technique is slower than directly 3D printing elastomers, but silicone is much more flexible than printable materials like TPU, in addition to having unique benefits like biocompatibility.[4] The printed molds can also be reused.
If your parts must be made from rubber at all costs, then 3D printing is probably not the way to go. Techniques like rubber compression molding are more suitable for manufacturing natural rubber parts, as the material does not need melting.
3D printing does, however, offer several viable options for printing high-performance rubber-like parts with desirable characteristics like flexibility, impact resistance, and shock absorption. Flexible FDM filaments like TPU are great for tough prototypes and simple items like soft-touch grips, while flexible resins are suitable for slightly more intricate components. Rigid 3D printed molds are also a great means of quickly casting silicone parts.
[1] Drossel WG, Ihlemann J, Landgraf R, Oelsch E, Schmidt M. Basic research for additive manufacturing of rubber. Polymers. 2020 Oct;12(10):2266.
[2] What is TPU? [Internet]. Lubrizol. [cited 2021Oct19]. Available from: https://www.lubrizol.com/Engineered-Polymers/About/What-is-TPU
[3] Bont M, Barry C, Johnston S. A review of liquid silicone rubber injection molding: Process variables and process modeling. Polymer Engineering & Science. 2021 Feb;61(2):331-47.
[4] Fallahi D, Mirzadeh H, Khorasani MT. Physical, mechanical, and biocompatibility evaluation of three different types of silicone rubber. Journal of applied polymer science. 2003 Jun 6;88(10):2522-9.
Best Models for 3D Printing D0%B5%D0%Bd%D1%82%D0%B0・Cults
Loading objects for the 3D printer %D1%80%D0%B5%D0%B7%D0%B8%D0%Bd%D0%Be% D0%B2%D0%B0%D1%8f%20%D0%Bb%D0%B5%D0%Bd%D1%82%D0%B0
Xtool D1 Z-axis height adjuster
4. 44 €
Sink for drip tray
1,90 €
Drill shell
€1.90
Dreamer Shell
1,90 €
Digital Cortex
€1.90
Decadent sink
1.90 €
sink with dawn chimes
1,90 €
Ctenophore shell
€1.90
Raspberry shell
1,90 €
Clapperboard shell
1,90 €
Convertible shell
1.90 €
Shell for rivals
1,90 €
Constriction sheath
1. 90 €
Pastry casing
1,90 €
Shell Coalition
1.90 €
Washbasin "Clean Lines"
1,90 €
Chiropteran shell
1,90 €
Champion jacket
1,90 €
Shell Challenger
2 €
Celestial Shell
1.90 €
Castaways Shell
2 €
Caramel apple shell
2 €
Canopus shell
2 €
CamNav TTN Shell
€1.90
Calavera shell
1,90 €
Cabana shell
1,90 €
Shell Bushwhacker
1,90 €
Wisdom's Exploded Shell
€1. 90
Floating shell
1,90 €
Displacer sink
€1.90
Bright Cycle Shell
1,90 €
Shell rock
1,90 €
beautiful air shell
1,90 €
Battle-worn shell
1.90 €
Backshell
€1.90
Spinning shell
1,90 €
Awakened Shell
€1.90
August sink
1,90 €
Atlas Shell
1,90 €
Astrological sink
1. 90 €
Forged shell Armory
1,90 €
Pitch Archipelago
1.90 €
Shell of the Archangels
2 €
Arc shell
€1.90
Aoki Fass Shell
1,90 €
An almost mighty shell
€1.90
Shell "Alchemical Dawn"
1,90 €
Adonis Shell
1.90 €
3D printing with rubber material on 3D printer SkyOne
SkyOne
Loading
07/06/2018
3562
3D printing
0007
Don't want
11
Article applies to printers:
SkyOne Traditionally, rubber and rubber-like products are made by pressing and vulcanizing in a mould. However, it should be noted that this common method of manufacturing rubber casings has a significant drawback. It lies in the fact that vulcanization is carried out on presses that have low productivity, and exposure of individual parts during vulcanization reaches up to 1 hour. The high cost of a complex mold is also a limiting factor.
The high flexibility of the plastic makes it possible to print complex 3D shapes, and the resistance to complex chemical compounds is indispensable in technical fields. Today, flexible plastic is used in medicine, automotive, manufacturing and everyday life. Combining the properties of rubber and silicone, the material has also become indispensable in the souvenir and gaming fields.
8 Article comments
More interesting articles
XcLxAd
Loading
03/10/2023
5196
35
Subscribe to the author
Subscribe
Don't want
This is a Neutric powerCON 250V 20A socket box, not what you think!
Read more
Risen
Loading
03/10/2023
3707
16
Follow author
Follow
Don't want
Hello %username%.