3D printing tools reddit
gettingstarted - 3dprinting
- Getting Started
- Why 3D Printing?
- Getting started with 3D Printing
- Where to get a model printed
- What printer to get
- Where to find models
- Material Choices
- Slicers
- Printing and Troubleshooting
- Post Processing
- How to make models
- Further Info
If you're new around here, welcome! We thought we'd put a few links together to springboard your foray into the fabulous (and sometimes frustrating!) world of 3D printing. :) |
---|
If you are contributing to this wiki please keep this page incredibly concise and extremely high level, keep further detail for the Detailed Info pages. |
Why 3D Printing?
3D printing (a.k.a Additive Manufacturing) is now pretty well established in industry as a prototyping tool, and is becoming more common as a process for creating finished custom or low-run parts.
In the home, printers can be a marvelous tool for solving practical household problems for example by repairing items, or creating new items that are fully customised for their position or use case. They also can be used for fun, and are popular for making tabletop gaming minis, and toys.
For inspiration browse the top posts of this subreddit.
Getting started with 3D Printing
The various types of 3D printing technologies all create real-world three-dimensional objects from digital models via the addition of material. These processes are able to produce novel structures that other manufacturing techniques cannot. Usually the 3D printing process looks like this:
Get a digital 3D model (by downloading or making one)
Slice it (use a program to generate instructions for the printer)
Print it (and troubleshoot it)
Post-process it (remove support material, clean up areas, paint etc)
Where to get a model printed
If you don't want to buy a printer (and you just want to have something printed), you can engage the help of a 3D printing service. Some popular choices include:
For a full list of service-providers (including design and model hosting services), please see the Services page.
What printer to get
If you're totally new to printing, the best place to ask for help when deciding what printer is right for you is our stickied monthly Purchase Advice Megathread.
Generally personal printers come in two main categories;
FDM (FFM) printers are best suited to larger objects and functional parts and work a bit like a like a hot glue gun that moves around, extruding plastic filament and building up an object layer by layer.
DLP (Layer Masking) printers are best suited to extremely detailed prints, and use light to cure resin in layers, masking it with an LCD screen.
There are, however, many other types of 3D printing technologies, which are explained here.
Where to find models
If you don't want to make your own models to print, there are many sites that host models for download. The more popular ones are:
Printables: upcoming and community-focused, feature-rich
Thingiverse: biggest model host, often buggy
Thangs: free models, which can be searched by geometry
My Mini Factory: free and paid models, guaranteed to print
GrabCad: functional/ technical models
YouMagine: Open source models
pinshape: free and paid models
yeggi: 3D model aggregator/search
CGTrader: free and paid models, not all of them made to be printed
A community-curated list of model host services can also be found on the services page.
The RepRap foundation also keeps a list of printable model-host services here.
When selecting a model you need to ensure they are manifold, here's an explanation of what that means and guide on fixing them. You can also try these free, automated services; Netfab, and Microsoft's tool
Material Choices
When you are just starting out with FDM 3D printing PLA is the recommended choice. It's very easy to work, relatively strong, with and comes without many of the safety concerns of other materials. A deeper discussion of materials can be found here.
If you are starting on a resin printer, check out our Resin Info page.
Slicers
Slicing software takes a 3d model and turns it into instructions for the 3D printer. The instructions are generally exported in GCode which essentially is a list of locations to move to, amount of filament to extrude, etc.
The popular choices for slicing software are:
Ultimaker Cura: free, open source, highly customisable. Getting Started, Full Manual
Prusa Slicer (Based on Slic3r), Beginning with Prusa Edition (old version)
There are, however, many other options, most of which are discussed here
Be sure to check the layer preview to see if it makes sense in your slicer before printing (no unsupported overhangs, no parts missing, etc). More info on the Slicers Page
Printing and Troubleshooting
Follow your manufacturer's instructions in setting up your printer and starting your first print. It's a good idea to print a test print first (usually printers come with one).
If it succeeds congrats on your first print! You can now start slicing and printing your own models or some calibration prints
If your print fails you can begin troubleshooting.
This video helps you get to know the parts of your machine, so you know what we're talking about! :)
By far the most common reason for prints failing is an issue with levelling/tramming:
Full-resolution printable copy can be found here.
This visual reference, and this video may also help.
Once you have your prints sticking and printing, these guides can help you identify and solve any other issues you're experiencing:
Our Troubleshooting and Calibration wiki page
A Printa Pro PrintaGuide
rigid.ink poster and visual guide
Matterhackers Troubleshooting Guide
Simplify 3D Visual Troubleshooting Guide
Ultimaker Visual Troubleshooting Guide
RepRap Wiki Pictorial Troubleshooting Guide and Descriptive Troubleshooting Guide, these are a bit more technical/ advanced
It's also worthwhile seeking information from the manufacturer of your machine.
You can try searching for similar issues that other folk have experienced in the following communities: /r/3Dprinting, /r/FixMyPrint, the 3D Printers Discord
If the above suggestions don't solve your issue then it's time to seek help from the community:
This video is a great overview on how to seek help with prints.
The best places to ask for help are here on /r/3Dprinting, /r/FixMyPrint, the 3D Printers Discord. When asking for help be sure to provide the following:
- A highly descriptive title (even if you don't know exactly what everything is officially called, please do your best to describe the issue in plain English. This not only helps you get the help you want, but also helps the rest of the community by keeping the sub searchable, so others can benefit from the help you receive.)
- Photos of the issue, screengrabs of the layer view in your slicer, screengrabs of the model itself.
- A description of what the machine was doing as it produced this issue.
- Your basic settings such as: nozzle and bed temperature, speed, nozzle/line width and later height, the printer you're using and the material you're printing in. Or better yet, a screengrab or an export of your settings (you can upload files free without an account here)
- Any other information you think could be relevant such as modifications or hypotheses.
Post Processing
Most prints need some work after they come off the printer to turn them into a finished part. Supports need to be removed, and surfaced may need to be smoothed. Here are some tutorials:
- How to finish 3D Prints guide
More info on the Post Processing page
How to make models
Can't find what you want online? Why not design and make it? Model-making software is split into 4 main categories, depending on your goal:
Full-resolution, printable copy here
These are just the top picks, model making is discussed in more depth on the Making Models page
More communities:
/u/Devtholt keeps a Multireddit of all 3d printing subreddits including some specifically for help, or tailored to certain printers or printer manufacturers.
Also has some subs that are related to 3D printing peripherally, such as /r/lasercutting and /r/CNC
3D Printers Discord great platform for troubleshooting and socialising.
RepRap Forums
Inside the Reddit group making 3D-printed face shields for healthcare workers
Impact
ByAJ Dellinger
Back in April, millions of people around the world were under lockdown in an attempt to stop the spread of coronavirus, and hospitals were in desperate need of personal protective equipment (PPE) for healthcare workers. On r/JerseyCity, a community on Reddit for residents of the city, a Redditor put out a call to action for all individuals and small businesses in the area with access to 3D printers and other tools. The user's goal: amass a team of volunteers to quickly make and deliver PPE to local hospitals in need. Within days, the Jersey City Rapid Maker Response Group (JCRMRG) was formed.
Justin Handsman, a consultant specializing in technology for derivatives traders, started the operation using a 3D printer to create about 20 face shields per day. He knew that with the help of other makers in the area, they could scale up that operation and provide a significant amount of support where it was needed most. At the time, New Jersey hospitals were suffering from a significant shortage of PPE. Strategy and operations specialist Ashley Strang, a member of JCRMRG, tells Mic that the organization was strategic in how it built its operation from the very start, knowing that a massive amount of PPE was needed.
Jersey City Rapid Maker Response Group"We started by building the systems we knew we'd need to scale — leveraging project management tools, defining roles, and structuring our digital workspace." She says that the group used online tools to organize, moving the conversation from Reddit to Discord for daily communications and holding regular meetings via Zoom. According to Strang, the JCRMRG team now consists of 75 volunteers who come from a variety of backgrounds, including small business owners and creators who want to lend a hand to frontline workers in need. Most of the team are helping with printing out masks. "We also have folks who've designed new 3D printed products and parts, and others who have written custom bots to streamline our volunteer intake," she says.
As the group ramped up its production, it started seeking funding for the project. The group set up a GoFundMe, which directs funds to the United Way of Hudson County. All of the donations are managed by the United Way, which uses the money to pay suppliers and vendors. Between their crowdsourced donations and direct partnerships, the group has raised over $90,000 to pay for materials and production costs of face shields.
To get the PPE to people in need, Strang said the group started performing outreach to local hospitals in Jersey City. "At the start of this, the ask was however much we could provide," she says. As they've become more established, Strang says hospital staff and nurses have contacted them directly about their needs. "Our volunteers deliver the shields directly to the hospital, sometimes meeting nurses or staff in the parking lot when the need is urgent." Since the team started operating mass production in mid-May, they have been able to take direct requests from hospitals and individual workers across other industries who are in need of shields.
In a matter of months, the upstart group of makers went from one person making about 20 shields a day to a collective capable of producing as many as 50,000 face shields per week as funding allows. Since launching its operations in April, JCRMRG has produced more than 75,000 total face shields, which have been distributed to hospitals and facilities throughout New Jersey, New York, and beyond. Strang says the group has also provided thousands of 3D printed ear savers (straps that wrap around a person’s head so masks aren’t always resting on their ears) to the medical staff at Jersey City Medical Center, Christ Hospital, Hoboken University Medical Center, and Valley Health System.
A new partnership secured by the volunteer team will stretch their efforts far beyond just New Jersey and the East Coast. This week, JCRMRG announced a partnership with the New Jersey-based Lixil Group Corporation. The company will help JCRMRG with the production and distribution of face shields for first responders and medical workers. According to the group, the support of Lixil will enable JCRMRG to produce as many as 50,000 shields per week. Strang says they plan on leveraging the corporation's teams and facilities across the country to distribute PPE across the U.S.
The growth of JCRMRG speaks both to how challenging the pandemic has been for healthcare workers and how beneficial a collective of people who want to help can be. "Hearing back from the folks who have used the shields has been one of the most fulfilling parts of this experience," Strang said. "We've gotten a touching thank you email from a nursing home employee, a text from an EMT saying these were by far the best shields they've received, and one ICU staff, unprompted, sent us a group photo of their shift team in our shields thanking us for our donation. "
🎸 Best 3D Printable Musical Instruments・Cults
🎸 Best 3D Printable Musical Instruments
3D Printable Musical Instruments
Celebrate music with this selection of the best musical instrument STL files. Be it strings or wind instruments, there is something here for all music lovers. Download paid or free 3D models, send them to your slicer for GCode preparation and upload this file to your 3D printer. Then all you have to do is find a song to play :)
GuitarPicks
Free
3D printed Violin • VLNLAB: VLA (Viola)
Free
Guitar Pick
Free
GuitarPickHolder
Free
Recorder (Music instrument)
Free
Ocarina
Free
Acoustic Violin 4/4 - Stridivarius Fiddle
Free
3D printed Violin • VLNLAB: VLN (Violin 4/4)
Free
Mediator - Guitar
Free
Playable Ukulele - Printable w/ no Supports
Free
Ukulele Wall Mount
Free
Parametric Mouthpiece 2.
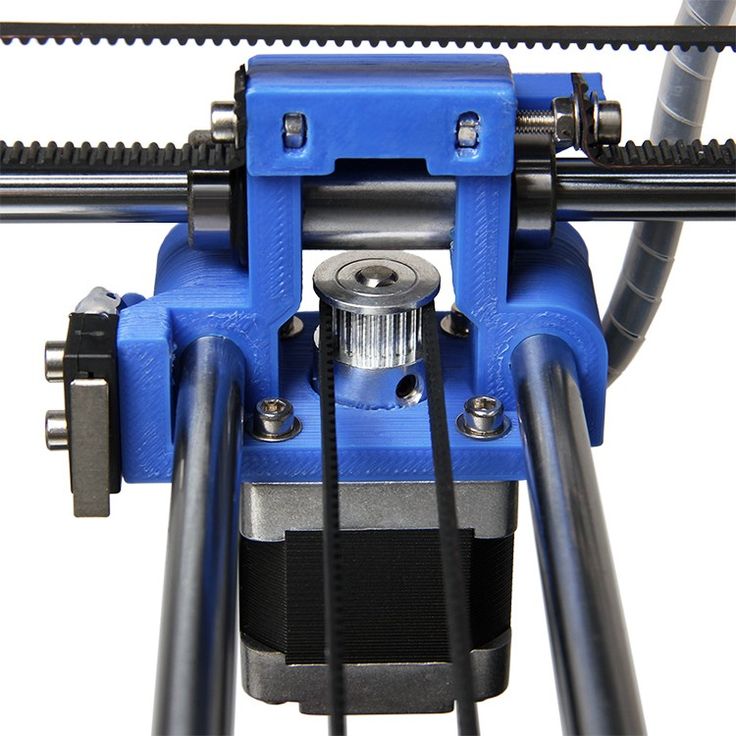
Free
Panflute
Free
Guitar / Amp knob w/ Celtic Skull (These go to 11!)
Free
pick guitar
Free
Small Ocarina Stand
Free
guitar / amp knob goes to 11 w/ Gargoyle head
Free
Blazing Ukulele
Free
351 Guitar Pick
Free
Maracas
Free
Yet Another Guitar String Winder 2
Free
Guitar Pick Holder with Sponge Spring
Free
Printable trumpet / horn
Free
Ghostly Pro-Audio Fader, Crossfader, and Knob assortment for mixers, midi, dj, etc
Free
Guy Manuel from Daft Punk Helmet
Free
Playable Guitar - Printable Without Supports
Free
Mini Flute
Free
One-Piece Ukulele
Free
Geartar
Free
GuitarPicks(part2)
Free
Jinghu (Chinese Bowed Instrument)
Free
Clarinet Mouthpiece 1.

Free
Ringing Bell
Free
Palm Whistle
Free
CelticMandolinIncenseHolder
Free
Balalaika (Russian Stringed Instrument)
Free
The Division Bell Statue | Pink Floyd
2.76 €
VITTEL FLUTE
Free
Wall bracket for guitar
1 €
Ukulele Unipeg
Free
Functional Electric Guitar 3D Printing Project!!!
€9.55
Guitarz - Tunable and Playble Mini Guitars
Free
Custom 3d printed Ukulele
Free
Trumpet straight mute
Free
10 inch e-drum pad with small 3d printer
Free
guitar knob goes to 11 with demon skull
Free
Ukulele Stand
Free
8 inch e-drum pad with small 3d printer
Free
Blazing Ukulele
Dragon Ocarina and Whistle
Guitar pick | Peak of Destiny
Playable Ukulele - Printable w/ no Supports
Discover our selection of the best music-related 3D printer files. All these STL files are 3D printable, so just download them, warm up your 3D printer. This collection has been created by selecting the best 3D models from the 3D Cults object library.
3D printing is progressing day by day, allowing manufacturers to even 3D print musical instruments. We used to know tools made with professional 3D printers, but now some tools can be made with a desktop 3D printer.
In this collection you can download several 3D models of musical accessories, from simple objects to more complex ones: picks, guitars, flutes, ocarinas, ukuleles, violins, pianos, drums, etc.
Examples of positive and negative uses of a 3D printer
Every year 3D printing becomes more and more popular. The 3D printer, as a tool for turning a digital model into a physical object, is gaining popularity, outperforming other production methods in many ways due to its affordability.
But do not forget that a 3D printer is just a tool. A lot depends on how this tool will be used.
Available 3D printing technologies
All 3D technologies can be conditionally divided into 4 types.
Layer by layer welding with molten material.
The principle of operation is similar to the familiar glue gun. The print media is melted to a semi-liquid state in the print head and applied with a nozzle to the print surface where it solidifies. This is how the finished 3D model “grows” layer by layer on the printing table. Not only thermoplastics can be used as consumables, but, for example, chocolate, icing, concrete, etc.
This is the most common type of printer. Inexpensive FDM printers are often used as home assistants. This is facilitated by an inexpensive price and a variety of consumables.
Selective curing of resin (photopolymer printers).
The material used is a photopolymer resin that hardens under the influence of UV radiation. As a source of UV radiation, a thin laser beam, a DLP projector or an LCD screen with a UV matrix, or any other design can be used. For example, some industrial 3D printers apply a photopolymer using thin nozzles and immediately illuminate it with a UV lamp.
Previously, these printers were quite expensive. Today, with advances in technology, photopolymer 3D printing has become affordable and photoresin printers have become popular as home hobby printers.
Selective bonding of powdered material.
On the print head of the printer there are several nozzles through which a binder is supplied, which is selectively applied to the powdered material. Various materials can be used as a material: for example, gypsum or metal powders. But gypsum is most often used.
Since dye can be added to the "glue" during printing, such printers are usually used for the production of color demonstration models or souvenirs.
Laser sintering of powder materials.
The youngest technology, but with great potential for use in large-scale industries. With the help of a laser or a heated print head, selective sintering of the metal powder occurs in an environment filled with an inert gas.
These are already serious industrial printers that are used for the production of functional metal assemblies and parts. Currently, such 3D printers are actively used in the aerospace industry.
Unethical use
3D piracy
Where there is duplication of objects, there are always disputes about copyright and piracy.
The production of any product is a long and painstaking work, and often more than one person. Before you get a finished decorative product, for example, a figurine, you need to think through everything to the smallest detail. Usually, before modeling, the artist draws a lot of sketches, the details of clothing and accessories are thought out. Only after that the 3D modeler gets to work and begins painstakingly recreating the 3D model.
Functional models are often redesigned by engineers after the prototype has been made. There can be a very long way between the initial idea and a stable working mechanism. And it’s very disappointing when such work is simply copied and posted in the public domain.
LEGO
It was one of the first mass manifestations of "3D piracy". At that time, 3D printing was only gaining popularity, and many users, having printed a dozen figurines, were looking for a useful application for a 3D printer. Given the low plastic consumption, the printed LEGO blocks were very inexpensive.
3D printed LEGO bricks
Despite the far from ideal surface, many were satisfied with such a copy. Some have argued that the accuracy of a home FDM printer is not enough for the bricks to fit well with the original LEGO, but for most users everything fit perfectly.
At the moment, LEGO is actively removing models that copy the original sizes of the famous bricks and men from the network. On popular sites, only custom elements of LEGO-men and LECO are left that are not the original size.
Custom heads for LEGO little men
Games Workshop
Games Workshop, which produce the most expensive table soldiers in the world, sued Thomas Valenti (USA) back in 2012. Thomas has modeled, printed and made publicly available several miniatures inspired by the Warhammer universe. The court sided with Games Workshop and the models had to be removed.
3D Printed Chaplain
Warhammer 40k Chaplain 3D Model
Games Workshop went one step further by banning fans from creating art and other work based on the original settings and characters. As a boycott, users of the Warhammer 40,000 section on Reddit are proposing to abandon the company's products as much as possible - print game figures on 3D printers, use paints from other companies, or switch to other universes.
Hollywood
The production of modern films is not a cheap pleasure, and film companies try to recoup their costs not only by showing them in cinemas, but, for example, by producing souvenirs.
DreamWorks has an entire consumer goods division that helps recoup the cost of a movie if it fails at the box office. Film companies recognize that fan-made productions often surpass the official "souvenir" in accuracy and detail.
DC Universe Batman fan model
Many film companies are closely following the development of 3D printed merchandise, but do not yet know how to respond. For example, Paramount Pictures, Marvel Studios and Warner Bros. They themselves began to upload models for 3D printing to the network, before the release of new films.
Weapon Seal
Weapon Seal
24-year-old law student Cody Wilson was the first to make a gun on a 3D printer. Cody designed and 3D printed a combat pistol on his own. After 8 years, the idea of making firearms using 3D printing has not only not died out, but flared up with a bright fire.
It started in Texas in 2012. It was there that the company Defense Distributed was registered, the ideology of which was the development of models of firearms that anyone could make on a home 3D printer.
Guns
Liberator
The first “swallow” was the Liberator - a compact plastic pistol printed on a 3D printer from ABS plastic. The only thing that could not be made on a 3D printer was the striker, which was successfully replaced by an ordinary nail. The first printed pistol was made on a Stratasys Dimension SST 3D printer.
Liberator - the name is borrowed from a cheap pistol that was developed in 1942 in the USA.
The Liberator fired a fairly weak .380 ACP round and could only last a dozen rounds at most.
Failed Liberator
Zig Zag
In the spring of 2014, a video appeared on the Internet with a man shooting from a plastic revolver with a huge drum. The video greatly stirred up all of Japan.
Zig Zag
Unknown was Yoshitomo Imura (Yoshitomo Imura) - 28-year-old employee of the Shonan Institute of Technology. Despite Imuru's claim that he fired blanks on the tape, he was arrested and sentenced to 2 years in prison.
The Zig Zag design was a reimagining of revolvers popular in the 19th century, which used a rotating .38 caliber barrel block mounted on a pistol grip.
Washbear
In 2015, mechanical engineering student James Patrick posted a video online showing a 3D printed PM522 Washbear in operation.
PM522 Washbear
The PM522 visually resembled a children's pistol from a science fiction movie, but at the same time the pistol had a strong and rigid frame. Washbear is also safer than its predecessors. At rest, the firing mechanism was not in line with the primer, so the PM522 was protected from accidental firing, for example, if dropped. The only metal part was the nail that replaced the striker.
Rifle
Grizzly
Canadian with the nickname CanadianGunNut, ThreeD Ukulele or simply Matthew, inspired by the Liberator project, designed and posted his project - Grizzly. Grizzly is an ABS+ plastic rifle. It took the Canadian 3 days to design the rifle and another 27 hours to manufacture it using a Stratasys Dimension 1200es industrial 3D printer.
Grizzly 9 Rifle0286
The first version of the Grizzly had a smooth and straight .22 barrel. But this turned out to be not a very good decision, and the barrel cracked after the first shot. Subsequently, Matthew replaced the barrel with a tapered barrel with rifling inside.
Plastic “cutting” could not affect the ballistics of the bullet in any way, but added strength to the barrel.
Shotgun
Liberator 12k
The Liberator 12k is a 12-round shotgun made by a well-known, in narrow circles, enthusiast in the world of 3D printing - Jeff Rodriguez.
Liberator 12k
Rodriguez managed to create a simple and at the same time reliable design, "mixing" a pistol and a pump-action shotgun in the design of the Liberator 12k. A huge plus for manufacturing and reliability was the absence of small parts in the shotgun mechanism.
Since the plastic was not strong enough, Rodriguez reinforced the design of the Liberator 12k with metal pins and added metal tubes inside the barrel and drum. The metal parts were purchased from a regular hardware store, so anyone could easily make a Liberator 12k with their home 3D printer.
Semi-automatic weapons
Shuty-MP1
The first sign was the Shuty-MP1, a semi-automatic pistol made by an amateur gunsmith with the nickname Derwood, in April 2017.
Shuty-MP1
Shuty AP-9
The Shuty AP-9 still uses a pistol barrel, but the trigger and return spring are taken from the civilian version of the M16. This improved the reliability of the rifle.
Ethical use
Despite the negative examples of application, 3D printing is actively used in many areas, helping to save time and create products that cannot be produced by other methods.
Medicine
Implants
Metal-printing 3D printers are actively used in medicine for the manufacture of titanium implants. For example, a patient needs to have a hip joint implant made. According to the results of CT, the necessary area of bone tissue replacement is agreed with the doctors and a prosthesis model is created that is ideal for this patient. After all approvals, the finished model is sent for printing.
3D model of implant
The main areas of 3D printing of implants in medicine are maxillofacial surgery, traumatology, orthopedics, oncology and veterinary medicine. A big advantage over the classical methods of manufacturing implants is the ability to create a cellular or porous structure. This allows for better integration of the prosthesis into the bone tissue.
Samples of printed implants and pins
Dentures
The manufacture of even a relatively simple traction prosthesis is a rather laborious and lengthy process. 3D printing has reduced costs and accelerated the production of prostheses. In addition, it became possible to customize the prosthesis.
Customized child prostheses
Some enthusiasts model and make models and detailed instructions for assembling traction prosthetic hands and fingers publicly available so that any user can print and make a prosthesis at home.
Simple Traction Hand Model
Production
Building custom drones
Aerialtronics is a small Dutch company that specializes in building unique, customized drones. Aerialtronics manufactures and develops unique drones, the characteristics of which can vary depending on the needs of the customer.
Initially, a basic concept model was designed, which consists of a platform and a set of elements that can be changed at the request of the customer. Changes can affect almost any part of the drone. The customer can choose the number of motors and their power, payload, flight time, supported software and much more.
Aerialtronics base model
But any, even minor changes in the characteristics and design of the drone required the manufacture of new elements and design changes. Classical manufacturing methods turned out to be quite laborious and long. To save time and money, a Stratasys uPrint SE Plus 3D printer was purchased.
Drone Assembly
Thanks to 3D printing, not only has production been accelerated, but more time has been devoted to improving individual components, because the finished model is ready the next morning. Rapid manufacturing allows you to print a part, test it, make the necessary changes to the 3D model and make a new sample. Aerialtronics engineers manage to produce and test 8-10 variants of a part in a few days in order to achieve maximum quality.
Prototyping
Gas turbine prototyping.
Prototyping by traditional methods is often time consuming and expensive. Because of this, the price of an error in calculations and 3D modeling can be very expensive.
For example, the production of turbine engine parts is usually based on careful preparatory calculations, but even this does not always prevent errors in the production of a test prototype. After all, even the most modern software methods cannot replace physical tests. But due to the high cost (over $20,000), it becomes impossible to produce multiple prototypes for testing.
Turbine Technologies (Wisconsin, USA) and its subsidiary Kutrieb Research have found a way out - 3D printing. Thanks to the 3D Systems ProJet 3D printer, it was possible to reduce the cost of prototyping by about 10 times to $2,000.
3D model and printed part of turbine
A turbine model is printed on a wax 3D printer, tested and then cast from metal. In addition to the cost, it was possible to significantly speed up production.