3D printing technology images
500+ 3D Printing Pictures [HD]
500+ 3D Printing Pictures [HD] | Download Free Images on Unsplash- A framed photoPhotos 6.4k
- A stack of photosCollections 10k
- A group of peopleUsers 6
3d printer
machine
technology
electronic
computer
person
orthose
orthopedic
horizontal
electronics industry
professional occupation
seoul
대한민국
factory
germany
3dprinting
makery
development
plan - document
presentation - speech
3d printer
splint
barcelona
espanya
Hq background images
oldenburg
deutschland
work in progress
render
Hd 3d wallpapers
digital image
printing machine
maker
Hd yellow wallpapers
berlin
prusa
prusa mini
–––– –––– –––– – –––– – –––– –– – –– –––– – – –– ––– –– –––– – –.
uk
england
fabrication
laser
engraving laser
cutting laser
cnc machine
3d model
cnc
sweden
malmö
plastic
engineering
additive manufacture
Hd design wallpapers
orthopedics
custom-made
3d printed
Hd grey wallpapers
brace
cast
3d modeling
cnc milling
machine
orthotics
orthoses
ultimaker
Related collections
3D Printing
9 photos · Curated by Marc Hartkopf3D Printing
7 photos · Curated by Sonja Perdue3D Printing collage
30 photos · Curated by Sam Ouellettefrance
toulouse
printing service
horizontal
electronics industry
professional occupation
germany
3dprinting
makery
sweden
malmö
plastic
barcelona
espanya
Hq background images
Hd grey wallpapers
brace
cast
orthotics
orthoses
ultimaker
uk
england
fabrication
cnc machine
3d model
cnc
3d printer
splint
orthopedics
custom-made
3d printed
render
Hd 3d wallpapers
digital image
printing machine
maker
Hd yellow wallpapers
berlin
prusa
prusa mini
–––– –––– –––– – –––– – –––– –– – –– –––– – – –– ––– –– –––– – –.
seoul
대한민국
factory
laser
engraving laser
cutting laser
development
plan - document
presentation - speech
engineering
additive manufacture
Hd design wallpapers
Related collections
3D Printing
9 photos · Curated by Marc Hartkopf3D Printing
7 photos · Curated by Sonja Perdue3D Printing collage
30 photos · Curated by Sam Ouelletteoldenburg
deutschland
work in progress
3d modeling
cnc milling
machine
france
toulouse
printing service
Unsplash logoUnsplash+In collaboration with Getty Images
Unsplash+
Unlock
horizontal
electronics industry
professional occupation
Gavin Allanwood
uk
england
fabrication
–––– –––– –––– – –––– – –––– –– – –– –––– – – –– ––– –– –––– – –.
Minku Kang
seoul
대한민국
factory
Opt Lasers
laser
engraving laser
cutting laser
Kadir Celep
germany
3dprinting
makery
ZMorph All-in-One 3D Printers
cnc machine
3d model
cnc
Unsplash logoUnsplash+In collaboration with Getty Images
Unsplash+
Unlock
development
plan - document
presentation - speech
Karl Hörnfeldt
sweden
malmö
plastic
Tom Claes
3d printer
splint
Rob Wingate
engineering
additive manufacture
Hd design wallpapers
Andrea G
barcelona
espanya
Hq background images
Tom Claes
orthopedics
custom-made
3d printed
NEW DATA SERVICES
oldenburg
deutschland
work in progress
Tom Claes
Hd grey wallpapers
brace
cast
SIMON LEE
render
Hd 3d wallpapers
digital image
Osman Talha Dikyar
printing machine
maker
Hd yellow wallpapers
ZMorph All-in-One 3D Printers
3d modeling
cnc milling
machine
Kadir Celep
berlin
prusa
prusa mini
Tom Claes
orthotics
orthoses
ultimaker
eMotion Tech
france
toulouse
printing service
Browse premium images on iStock | 20% off at iStock
Unsplash logoMake something awesome
3d Printing - Bilder und Stockfotos
18. 290Bilder
- Bilder
- Fotos
- Grafiken
- Vektoren
- Videos
Niedrigster Preis
SignatureBeste Qualität
Durchstöbern Sie 18.290
3d printing Stock-Fotografie und Bilder. Oder starten Sie eine neue Suche, um noch mehr Stock-Fotografie und Bilder zu entdecken.person, die ein objekt hält, das auf einem pulver-3d-drucker aus pulverpolyamid gedruckt ist. - 3d printing stock-fotos und bilderPerson, die ein Objekt hält, das auf einem Pulver-3D-Drucker aus...
Person, die ein Objekt hält, das auf einem Pulver-3D-Drucker aus Pulverpolyamid gedruckt wurde. Graues Objekt, das unter Einwirkung des Thermodruckkopfes gebildet wurde. Neue 3D-Drucktechnologie Moderne neue fortschrittliche additive Technologie
3d-drucker druckt blaue formen auf einem blauen backgroun - 3d printing stock-fotos und bilder3D-Drucker druckt blaue Formen auf einem blauen Backgroun
künstlicher zahn auf medizinischem 3d-drucker.
Künstlicher Zahn auf medizinischem 3D-Drucker. 3D-Druck in der...
geschäftsmann auf verschwommenem hintergrund mit 3d-druck digitales hologramm 3d-rendering - 3d printing stock-fotos und bilderGeschäftsmann auf verschwommenem Hintergrund mit 3D-Druck...
junger ingenieur arbeitet an einem 3d-drucker - 3d printing stock-fotos und bilderJunger Ingenieur arbeitet an einem 3D-Drucker
3d-drucktechnologie verwandtes vektorbanner-designkonzept, moderner linienstil mit symbolen - 3d printing stock-grafiken, -clipart, -cartoons und -symbole3D-Drucktechnologie Verwandtes Vektorbanner-Designkonzept,...
3d druck-maschine - 3d printing stock-fotos und bilder3D Druck-Maschine
Dreidimensionale Druckmaschine
schüler lernen 3d-druck zu hause - 3d printing stock-fotos und bilderSchüler lernen 3D-Druck zu Hause
hand mit objekt auf 3d-drucker gedruckt nahaufnahme - 3d printing stock-fotos und bilderHand mit Objekt auf 3D-Drucker gedruckt Nahaufnahme
designer, die in einem 3d-druckstudio arbeiten und ein gedrucktes objekt betrachten - 3d printing stock-fotos und bilderDesigner, die in einem 3D-Druckstudio arbeiten und ein. ..
3D-Drucker-Jet-Motor gedruckt Modell Metall Kunststoff
filament für 3d-drucker. filament zum drucken von kunststoffteilen auf einem 3d-drucker. nahaufnahme - 3d printing stock-fotos und bilderFilament für 3D-Drucker. Filament zum Drucken von...
objekt auf metall-3d-drucker gedruckt - 3d printing stock-fotos und bilderObjekt auf Metall-3D-Drucker gedruckt
Objekt auf Metall-3D-Drucker gedruckt. Ein Modell, das in einer Lasersintermaschine aus nächster Nähe erstellt wurde. Konzept der industriellen Revolution 4.0. Fortschrittliche moderne Additivtechnologie.
metallprodukte, die durch metall-3d-druck hergestellt werden. moderne additive technologie. - 3d printing stock-fotos und bilderMetallprodukte, die durch Metall-3D-Druck hergestellt werden....
kreativer mann, der zwei 3d-gedruckte objekte in seinem büro hält - 3d printing stock-fotos und bilderKreativer Mann, der zwei 3D-gedruckte Objekte in seinem Büro hält
3d-drucker ausdruckt ein kompressrad für turbolader aus - 3d printing stock-fotos und bilder3D-Drucker ausdruckt ein Kompressrad für Turbolader aus
3D-Drucker beim Drucken eines Kompresserradmodells für Turbolader
arbeiten sie 3d-drucker nahaufnahme.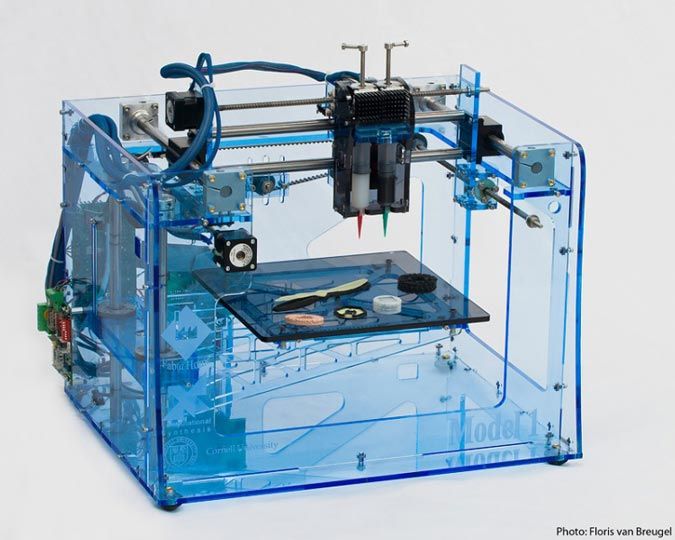
Arbeiten Sie 3D-Drucker Nahaufnahme. Drucken von 3D-Druckerobjekt.
Arbeit 3D-Drucker Nahaufnahme. Drucken von 3D-Drucker Objekt. Kunststoff-Drahtfilament. Moderne Drucktechnik. Fortschrittliche Additivtechnologie. Blaugraue Farbe
3d-drucker-blaupausen - 3d printing stock-grafiken, -clipart, -cartoons und -symbole3D-Drucker-Blaupausen
Stilisierte Vektorillustration von Blaupausen des 3D-Druckers
3d-drucktechnologie verwandtes vektorbanner-designkonzept, moderner linienstil mit symbolen - 3d printing stock-grafiken, -clipart, -cartoons und -symbole3D-Drucktechnologie Verwandtes Vektorbanner-Designkonzept,...
elektronische drei dimensionale kunststoff drucker während der arbeit, 3d drucken. - 3d printing stock-fotos und bilderElektronische drei dimensionale Kunststoff Drucker während der. ..
Moderner 3D-Drucker Druck Figur Nahaufnahme. Dunkel....
Moderner 3D-Druckerdruck Figur Nahaufnahme. Leerzeichen kopieren. Automatische dreidimensionale Durchführung der plastischen gelben Farbmodellierung im Labor. Fortschrittliche moderne Additivtechnologie
3 d drucker - 3d printing stock-fotos und bilder3 D Drucker
Dreidimensionale Druckmaschine
prisma 3d hintergrund zusammenfassung - 3d printing stock-grafiken, -clipart, -cartoons und -symbolePrisma 3D Hintergrund Zusammenfassung
prototypen des 3d-druckerdrucks - 3d printing stock-fotos und bilderPrototypen des 3D-Druckerdrucks
die turbinenteile bilden eine metall-3d-druckermaschine. - 3d printing stock-fotos und bilderDie Turbinenteile bilden eine Metall-3D-Druckermaschine.
Die Turbinenteile bilden eine 3D-Druckermaschine aus Metall. Der High-Tech-Metall-3D-Modellprozess durch additives Fertigungsverfahren
Drucken von 3D-Objekten
Nahaufnahme eines 3D-Druckers, der 3D-Objekte druckt.
3 d drucker, printing house - 3d printing stock-fotos und bilder3 d Drucker, Printing house
3D-Drucker, Druckerei.
sla 3d-drucker, laptop auf dem tisch in der werkstatt des additiven 3d-herstellers. 3d-druck isometrisches konzept. arbeitsplatz des engineerings. 3d-drucker gedrucktes computermodell auf laptop entworfen. prototyping von details. - 3d printing stock-grafiken, -clipart, -cartoons und -symboleSLA 3D-Drucker, Laptop auf dem Tisch in der Werkstatt des...
prototypen für den 3d-druckerdruck - 3d printing stock-fotos und bilderPrototypen für den 3D-Druckerdruck
3d-druck: zwei wissenschaftler arbeiten an einer slm-maschine (selective laser melting) für metall - 3d printing stock-fotos und bilder3D-Druck: Zwei Wissenschaftler arbeiten an einer SLM-Maschine (Sel
3d-gedruckte modelle mit komplexer geometrie, laserstrahlschmelzen - 3d printing stock-fotos und bilder3D-gedruckte Modelle mit komplexer Geometrie,. ..
3D-gedruckte Modelle mit komplexer Geometrie, additive Fertigung mit Tragstruktur
3d-polymer-bedruckte stiefel- oder schuhsohle, detailansicht von der seite - 3d printing stock-fotos und bilder3D-Polymer-bedruckte Stiefel- oder Schuhsohle, Detailansicht von...
graue orthopädische kunststoffprothese gedruckt auf pulver-3d-drucker für hand. - 3d printing stock-fotos und bilderGraue orthopädische Kunststoffprothese gedruckt auf Pulver-3D-Druc
zahntechniker entfernt kiefermodell aus einem 3d-drucker - 3d printing stock-fotos und bilderZahntechniker entfernt Kiefermodell aus einem 3D-Drucker
kunststoff-lüfter propeller 3d-druckverfahren - 3d printing stock-fotos und bilderKunststoff-Lüfter Propeller 3D-Druckverfahren
vektor futuristische welle. digitaltechnik. big data. - 3d printing stock-grafiken, -clipart, -cartoons und -symboleVektor futuristische Welle. Digitaltechnik. Big Data.
Futuristische Vektorwelle auf blauem Hintergrund. Digitale Technologien. Big Data.
3d vr DesignLinie Symbole. Vektor-Illustration enthalten Symbol -
3d-laserscanning. der ingenieur scannt das teil mit einem 3d-scanner. - 3d printing stock-fotos und bilder3D-Laserscanning. Der Ingenieur scannt das Teil mit einem 3D-Scann
abstrakte form - 3d printing stock-fotos und bilderAbstrakte Form
die 3d-druckmaschine fertigen das 3d-prototypmodell nach harzmaterial. - 3d printing stock-fotos und bilderDie 3D-Druckmaschine fertigen das 3D-Prototypmodell nach...
Die 3D-Druckmaschine macht den 3D-Prototyp Modell für Harzmaterial. Die Hi-Technologie für das Rapid-Prototyp-Verfahren per 3D-Druckmaschine.
engineering-technologie-konzept.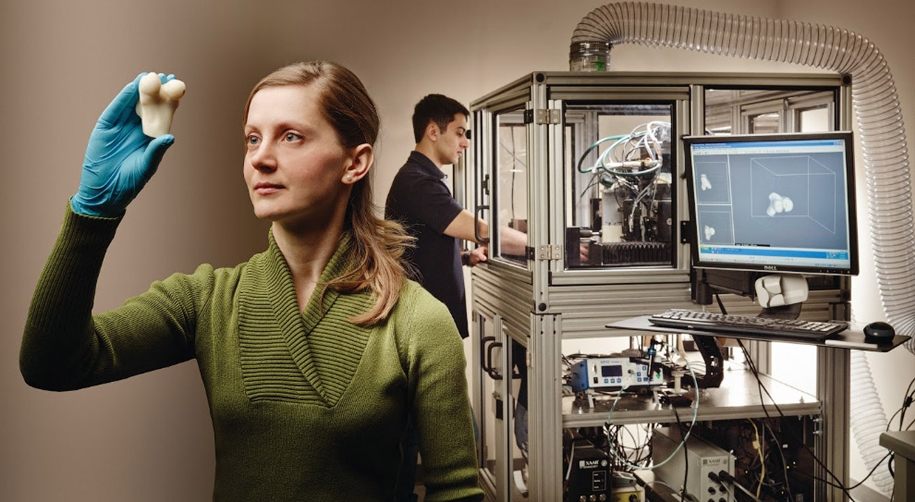
Engineering-Technologie-Konzept. CAD-System. Generatives Design...
nahaufnahme von 3d-drucker machen stück fleisch - 3d printing stock-fotos und bilderNahaufnahme von 3D-Drucker machen Stück Fleisch
erstaunt über den 3d-druck - 3d printing stock-fotos und bilderErstaunt über den 3D-Druck
Nahaufnahme eines 3D-Druckers, der 3D-Objekte druckt. Zwei Arbeiter beobachten den Prozess. Frauen hält 3D-Objekte in der Hand.
3d-fertigungsdrucker während der arbeit - 3d printing stock-fotos und bilder3D-Fertigungsdrucker während der Arbeit
rufen sie low poly wireframe auf blauem, dunklem hintergrund an. kommunikationstelefon von punkten, linien und dreiecken. telekommunikationstechnisches konzept.
Rufen Sie Low Poly Wireframe auf blauem, dunklem Hintergrund an....
junger designer während seiner arbeit im labor - 3d printing stock-fotos und bilderJunger Designer während seiner Arbeit im Labor
3d-gedruckte modelle mit komplexer geometrie, laserstrahlschmelzen - 3d printing stock-fotos und bilder3D-gedruckte Modelle mit komplexer Geometrie,...
3D-gedruckte Modelle mit komplexer Geometrie, additive Fertigung mit Tragstruktur
objekt aus metallpulver auf metall-3d-drucker, arbeitskammer gedruckt. - 3d printing stock-fotos und bilderObjekt aus Metallpulver auf Metall-3D-Drucker, Arbeitskammer...
bunte helle reihe von spool-3d-druckerfilament black metal hintergrund - 3d printing stock-fotos und bilderBunte helle Reihe von Spool-3d-Druckerfilament Black Metal...
drei dimensionale druckmaschine - 3d printing stock-fotos und bilderDrei dimensionale Druckmaschine
kreative start-up-team bei der arbeit von 3d-druckern.
Kreative Start-Up-Team bei der Arbeit von 3D-Druckern.
Diversity-Startup-Business-Team, das per 3D-Drucker zusammenarbeitet. Gedruckte Objekte betrachten und diskutieren. Selektiver Fokus auf den 3D-Druckerdruck, der ein Objekt mit dem Kreativteam im Hintergrund druckt.
3d-drucker druck blau grau facettiert geometrische formen blauer hintergrund - 3d printing stock-fotos und bilder3D-Drucker Druck blau grau facettiert geometrische Formen blauer...
3d-drucker aus einem photopolymer-material. - 3d printing stock-fotos und bilder3D-Drucker aus einem Photopolymer-Material.
3d-druck farbsymbol im dunklen modus mit additiven herstellung (am) drucktechnologie glyphensymbole: druckermaschine, digitaler computer cad prototyp, kunststoff-würfel-modell, materialien, zubehör. - 3d printing stock-grafiken, -clipart, -cartoons und -symbole3D-Druck Farbsymbol im dunklen Modus mit additiven Herstellung (AM
designer, der im büro arbeitet 3d-druck eines projekts - 3d printing stock-fotos und bilderDesigner, der im Büro arbeitet 3D-Druck eines Projekts
Lateinamerikanische Designerin, die im Büro arbeitet 3D-Druck eines Projekts
minimalistischer blauer hintergrund mit welliger 3d-linie - 3d printing stock-grafiken, -clipart, -cartoons und -symboleMinimalistischer blauer Hintergrund mit welliger 3D-Linie
3d-drucker.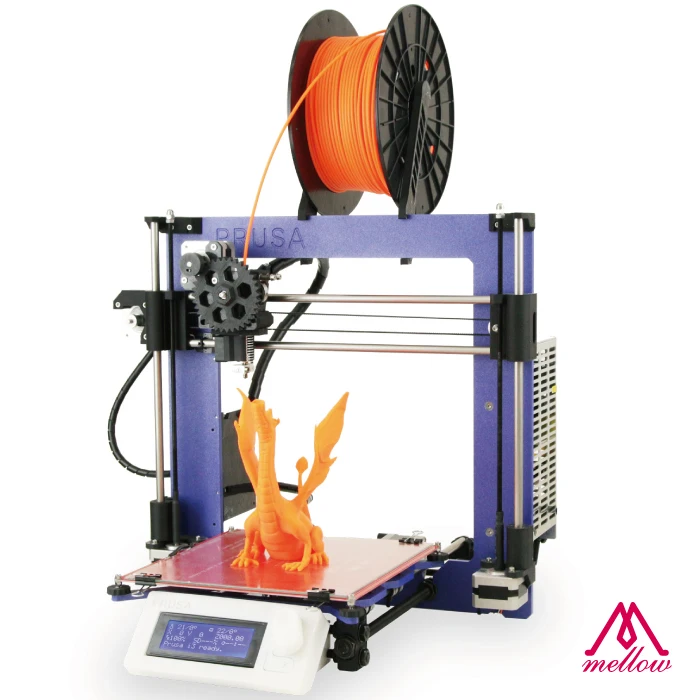
3D-Drucker. 3D-Druck
3D-Drucker, Vektorillustration
scheiben für cad-cam fräsen zähne - 3d printing stock-fotos und bilderScheiben für CAD-Cam Fräsen Zähne
Scheiben für CAD CAM geschnitzte Zähne Nahaufnahme
3d gedrucktsportsportschuh - 3d printing stock-fotos und bilder3D gedrucktsportSportschuh
3D-Druckermaschine druckt Leistungsschuh zu Hause.
3 d drucker, printing house. - 3d printing stock-fotos und bilder3 d Drucker, Printing house.
von 100All about 3D printing. additive manufacturing. Basic concepts.
- 1 Technology
- 2 Terminology
- 3 Fundamentals
- 4 Printing Technologies
- 5 3D printers
- 6 Application
- 7 Domestic and hobby use
- 8 Clothing
- 9 3D bioprinting
- 10 3D printing of implants and medical devices
- 11 3D printing services
- 12 Research into new applications
- 13 Intellectual Property
- 14 Influence of 3D printing
- 15 Space research
- 16 Social change
- 17 Firearms
Technology
Charles Hull - the father of modern 3D printing
3D printing is based on the concept of building an object in successive layers that display the contours of the model. In fact, 3D printing is the complete opposite of traditional mechanical production and processing methods such as milling or cutting, where the appearance of the product is formed by removing excess material (so-called "subtractive manufacturing").
3D printers are computer-controlled machines that build parts in an additive way. Although 3D printing technology appeared in the 80s of the last century, 3D printers were widely used commercially only in the early 2010s. The first viable 3D printer was created by Charles Hull, one of the founders of 3D Systems Corporation. At the beginning of the 21st century, there was a significant increase in sales, which led to a sharp drop in the cost of devices. According to the consulting firm Wohlers Associates, the global market for 3D printers and related services reached $2.2 billion in 2012, growing by 29%.% compared to 2011.
3D printing technologies are used for prototyping and distributed manufacturing in architecture, construction, industrial design, automotive, aerospace, military-industrial, engineering and medical industries, bioengineering (to create artificial fabrics), fashion and footwear, jewelry, in education, geographic information systems, food industry and many other areas. According to research, open source home 3D printers will allow you to win back the capital costs of your own purchase through the economy of household production of items.
Terminology
Additive manufacturing involves the construction of objects by adding the necessary material, and not by removing excess, as is the case with subtractive methods
The term "additive manufacturing" refers to the technology of creating objects by applying successive layers material. Models made using the additive method can be used at any stage of production - both for the production of prototypes (so-called rapid prototyping) and as finished products themselves (so-called rapid production).
In manufacturing, especially machining, the term "subtractive" implies more traditional methods and is a retronym coined in recent years to distinguish between traditional methods and new additive methods. Although traditional manufacturing has used essentially "additive" methods for centuries (such as riveting, welding, and screwing), they lack a 3D information technology component. Machining, on the other hand, (the production of parts of an exact shape), as a rule, is based on subtractive methods - filing, milling, drilling and grinding.
The term "stereolithography" was defined by Charles Hull in a 1984 patent as "a system for generating three-dimensional objects by layering".
Fundamentals
3D printed models
3D models are created by hand-held computer graphic design or 3D scanning. Hand modeling, or the preparation of geometric data for the creation of 3D computer graphics, is somewhat like sculpture. 3D scanning is the automatic collection and analysis of data from a real object, namely shape, color and other characteristics, with subsequent conversion into a digital three-dimensional model.
Both manual and automatic creation of 3D printed models can be difficult for the average user. In this regard, 3D printed marketplaces have become widespread in recent years. Some of the more popular examples include Shapeways, Thingiverse, and Threeding.
3D printing
The following digital models are used as drawings for 3D printed objects , powder, paper or sheet material, building a 3D model from a series of cross sections. These layers, corresponding to virtual cross-sections in the CAD model, are connected or fused together to create an object of a given shape. The main advantage of this method is the ability to create geometric shapes of almost unlimited complexity.
"Resolution" of the printer means the thickness of the applied layers (Z-axis) and the accuracy of positioning the print head in the horizontal plane (along the X and Y axes). Resolution is measured in DPI (dots per inch) or micrometers (the obsolete term is "micron"). Typical layer thicknesses are 100µm (250 DPI), although some devices like the Objet Connex and 3D Systems ProJet are capable of printing layers as thin as 16µm (1600 DPI). The resolution on the X and Y axes is similar to that of conventional 2D laser printers. A typical particle size is about 50-100µm (510 to 250 DPI) in diameter.
One of the methods for obtaining a digital model is 3D scanning. Pictured here is a MakerBot Digitizer
3D Scanner Building a model using modern technology takes hours to days, depending on the method used and the size and complexity of the model. Industrial additive systems can typically reduce the time to a few hours, but it all depends on the type of plant, as well as the size and number of models produced at the same time.
Traditional manufacturing methods such as injection molding can be less expensive when producing large batches of polymer products, but additive manufacturing has advantages in small batch production, allowing for higher production rates and design flexibility, along with increased cost per unit produced. In addition, desktop 3D printers allow designers and developers to create concept models and prototypes without leaving the office.
Machining
FDM Type 3D Printers
Although the resolution of the printers is adequate for most projects, printing slightly oversized objects and then subtractively machining them with high-precision tools allows you to create models of increased accuracy.
The LUMEX Avance-25 is an example of devices with a similar combined manufacturing and processing method. Some additive manufacturing methods allow for the use of multiple materials, as well as different colors, within a single production run. Many of the 3D printers use "supports" or "supports" during printing. Supports are needed to build model fragments that are not in contact with the underlying layers or the working platform. The supports themselves are not part of the given model, and upon completion of printing, they either break off (in the case of using the same material as for printing the model itself), or dissolve (usually in water or acetone - depending on the material used to create the supports). ).
Printing technologies
Since the late 1970s, several 3D printing methods have come into being. The first printers were large, expensive and very limited.
Complete skull with supports not yet removed
A wide variety of additive manufacturing methods are now available. The main differences are in the layering method and consumables used. Some methods rely on melting or softening materials to create layers: these include selective laser sintering (SLS), selective laser melting (SLM), direct metal laser sintering (DMLS), fusing deposition printing (FDM or FFF). Another trend has been the production of solid models by polymerization of liquid materials, known as stereolithography (SLA).
In the case of lamination of sheet materials (LOM), thin layers of material are cut to the required contour, and then joined into a single whole. Paper, polymers and metals can be used as LOM materials. Each of these methods has its own advantages and disadvantages, which is why some companies offer a choice of consumables for building a model - polymer or powder. LOM printers often use regular office paper to build durable prototypes. The key points when choosing the right device are the speed of printing, the price of a 3D printer, the cost of printed prototypes, as well as the cost and range of compatible consumables.
Printers that produce full-fledged metal models are quite expensive, but it is possible to use less expensive devices for the production of molds and subsequent casting of metal parts.
The main methods of additive manufacturing are presented in the table:
| ||
Method | Technology | Materials used |
Extrusion | Fused deposition modeling (FDM or FFF) | Thermoplastics (such as polylactide (PLA), acrylonitrile butadiene styrene (ABS), etc.![]() |
Wire | Manufacture of arbitrary shapes by electron beam fusing (EBFȝ) | Virtually all metal alloys |
Powder | Direct Metal Laser Sintering (DMLS) | Virtually all metal alloys |
Electron Beam Melting (EBM) | Titanium alloys | |
Selective laser melting (SLM) | Titanium alloys, cobalt-chromium alloys, stainless steel, aluminum | |
Selective heat sintering (SHS) | Powder thermoplastics | |
Selective laser sintering (SLS) | Thermoplastics, metal powders, ceramic powders | |
Inkjet | 3D Inkjet Printing (3DP) | Gypsum, plastics, metal powders, sand mixtures |
Lamination | Lamination Object Manufacturing (LOM) | Paper, metal foil, plastic film |
Polymerization | Stereolithography (SLA) | Photopolymers |
Digital LED Projection (DLP) | Photopolymers |
Extrusion Printing
Fused Deposition Modeling (FDM/FFF) was developed by S. Scott Trump in the late 1980s and commercialized in the 1990s by Stratasys, a company of which Trump is credited as one of the founders. Due to the expiration of the patent, there is a large community of open source 3D printer developers as well as commercial organizations using the technology. As a consequence, the cost of devices has decreased by two orders of magnitude since the invention of the technology.
3D printers range from simple do-it-yourself printers to plastic...
Fusion printing process involves the creation of layers by extrusion of a fast-curing material in the form of microdrops or thin jets. Typically, consumable material (such as thermoplastic) comes in the form of spools from which the material is fed into a printhead called an "extruder". The extruder heats the material to its melting temperature, followed by extrusion of the molten mass through a nozzle. The extruder itself is driven by stepper motors or servomotors to position the print head in three planes. The movement of the extruder is controlled by a manufacturing software (CAM) linked to a microcontroller.
A variety of polymers are used as consumables, including acrylonitrile butadiene styrene (ABS), polycarbonate (PC), polylactide (PLA), high pressure polyethylene (HDPE), polycarbonate-ABS blends, polyphenylene sulfone (PPSU), etc. Typically, polymer supplied in the form of a filler made of pure plastic. There are several projects in the 3D printing enthusiast community that aim to recycle used plastic into materials for 3D printing. The projects are based on the production of consumables using shredders and melters.
FDM/FFF technology has certain limitations on the complexity of the generated geometric shapes. For example, the creation of suspended structures (such as stalactites) is impossible by itself, due to the lack of necessary support. This limitation is compensated by the creation of temporary support structures that are removed after printing is completed.
Powder print
Selective sintering of powder materials is one of the additive manufacturing methods. Model layers are drawn (sintered) in a thin layer of powdered material, after which the work platform is lowered and a new layer of powder is applied. The process is repeated until a complete model is obtained. The unused material remains in the working chamber and serves to support the overhanging layers without requiring the creation of special supports.
The most common methods are based on laser sintering: selective laser sintering (SLS) for working with metals and polymers (e.g. polyamide (PA), glass fiber reinforced polyamide (PA-GF), glass fiber (GF), polyetheretherketone) (PEEK), polystyrene (PS), alumide, carbon fiber reinforced polyamide (Carbonmide), elastomers) and direct metal laser sintering (DMLS).
... to expensive industrial plants working with metals
Selective Laser Sintering (SLS) was developed and patented by Carl Deckard and Joseph Beeman of the University of Texas at Austin in the mid-1080s under the auspices of the Defense Advanced Research Projects Agency (DARPA). A similar method was patented by R. F. Householder in 1979, but has not been commercialized.
Selective laser melting (SLM) is characterized by the fact that it does not sinter, but actually melts the powder at the points of contact with a powerful laser beam, allowing you to create high-density materials that are similar in terms of mechanical characteristics to products made by traditional methods.
Electron Beam Melting (EBM) is a similar method for the additive manufacturing of metal parts (eg titanium alloys) but using electron beams instead of lasers. EBM is based on melting metal powders layer by layer in a vacuum chamber. In contrast to sintering at temperatures below melting thresholds, models made by electron beam melting are characterized by solidity with a corresponding high strength.
Finally, there is the 3D inkjet printing method. In this case, a binder is applied to thin layers of powder (gypsum or plastic) in accordance with the contours of successive layers of the digital model. The process is repeated until the finished model is obtained. The technology provides a wide range of applications, including the creation of color models, suspended structures, the use of elastomers. The design of models can be strengthened by subsequent impregnation with wax or polymers.
Lamination
FDM 3D printers are the most popular among hobbyists and enthusiasts
Some printers use paper as a material for building models, thereby reducing the cost of printing. Such devices experienced the peak of popularity in the 1990s. The technology consists in cutting out the layers of the model from paper using a carbon dioxide laser with simultaneous lamination of the contours to form the finished product.
In 2005, Mcor Technologies Ltd developed a variant of the technology that uses plain office paper, a tungsten carbide blade instead of a laser, and selective adhesive application.
There are also device variants that laminate thin metal and plastic sheets.
Photopolymerization
3D printing allows you to create functional monolithic parts of complex geometric shapes, like this jet nozzle
Stereolithography technology was patented by Charles Hull in 1986. Photopolymerization is primarily used in stereolithography (SLA) to create solid objects from liquid materials. This method differs significantly from previous attempts, from the sculptural portraits of François Willem (1830-1905) to photopolymerization by the Matsubara method (1974).
The Digital Projection Method (DLP) uses liquid photopolymer resins that are cured by exposure to ultraviolet light emitted from digital projectors in a coated working chamber. After the material has hardened, the working platform is immersed to a depth equal to the thickness of one layer, and the liquid polymer is irradiated again. The procedure is repeated until the completion of the model building. An example of a rapid prototyping system using digital LED projectors is the EnvisionTEC Perfactory.
Inkjet printers (eg Objet PolyJet) spray thin layers (16-30µm) of photopolymer onto the build platform until a complete model is obtained. Each layer is irradiated with an ultraviolet beam until hardened. The result is a model ready for immediate use. The gel-like support material used to support the components of geometrically complex models is removed after the model has been handcrafted and washed. The technology allows the use of elastomers.
Ultra-precise detailing of models can be achieved using multiphoton polymerization. This method is reduced to drawing the contours of a three-dimensional object with a focused laser beam. Due to non-linear photoexcitation, the material solidifies only at the focusing points of the laser beam. This method makes it easy to achieve resolutions above 100 µm, as well as build complex structures with moving and interacting parts.
Another popular method is curing with LED projectors or "projection stereolithography".
Projection stereolithography
This method involves dividing a 3D digital model into horizontal layers, converting each layer into a 2D projection similar to photomasks. The 2D images are projected onto successive layers of photopolymer resin that harden according to the projected contours.
In some systems, the projectors are located at the bottom, helping to level the surface of the photopolymer material when the model moves vertically (in this case, the build platform with the applied layers moves up, rather than sinking into the material) and reduces the production cycle to minutes instead of hours.
The technology allows you to create models with layers of several materials with different curing rates.
Some commercial models, such as the Objet Connex, apply resin using small nozzles.
3D printers
Industrial plants
Industrial adoption of additive manufacturing is proceeding at a rapid pace. For example, US-Israeli joint venture Stratasys supplies $2,000 to $500,000 additive manufacturing machines, while General Electric uses high-end machines to produce gas turbine parts.
Home appliances
LOM takes papier-mâché to the next level The development of 3D printers for home use is being pursued by a growing number of companies and enthusiasts. Most of the work is done by amateurs for their own and public needs, with help from the academic community and hackers.
The oldest and longest running project in the desktop 3D printer category is RepRap. The RepRap project aims to create free and open source (FOSH) 3D printers provided under the GNU General Public License. RepRap devices are capable of printing custom-designed plastic components that can be used to build clones of the original device. Individual RepRap devices have been successfully applied to the production of printed circuit boards and metal parts.
Due to the open access to drawings of RepRap printers, many of the projects adopt the technical solutions of analogues, thus creating a semblance of an ecosystem consisting mostly of freely modifiable devices. The wide availability of open source designs only encourages variations. On the other hand, there is a significant variation in the level of quality and complexity of both the designs themselves and the devices manufactured on their basis. The rapid development of open source 3D printers is leading to a rise in popularity and the emergence of public and commercial portals (such as Thingiverse or Cubify) offering a variety of printable 3D designs. In addition, the development of technology contributes to the sustainable development of local economies through the possibility of using locally available materials for the production of printers.
Stereolithographic 3D printers are often used in dental prosthetics
The cost of 3D printers has been declining at a significant rate since about 2010: devices that cost $20,000 at the time are now $1,000 or less. Many companies and individual developers are already offering budget RepRap kits under $500. The Fab@Home open source project has led to the development of general purpose printers capable of printing anything that can be squeezed through a nozzle, from chocolate to silicone putty and chemicals.
Printers based on this design have been available as kits since 2012 for around $2,000. Some 3D printers, including the mUVe 3D and Lumifold, are designed to be as affordable as possible from the start, with the Peachy Printer being priced around $100. .
Professional Kickstarter funded printers often perform well: Rapide 3D printers are quiet and fumes free at $1499. 3D Doodler's '3D Printing Pen' Raised $2.3M in Kickstarter donations, with a selling price of $99 for the device itself. True, it is difficult to call the 3D Doodler a full-fledged 3D printer.
3D Systems Cube is a popular consumer 3D printer
As prices drop, 3D printers are becoming more attractive for home production. In addition, home use of 3D printing technologies can reduce the environmental footprint of industry by reducing the volume of consumables and the energy and fuel costs of transporting materials and goods.
Parallel to the creation of home 3D-printing devices, the development of devices for processing household waste into printed materials, the so-called. Recyclebot. For example, the commercial model Filastrucer was designed to recycle plastic waste (shampoo bottles, milk containers) into inexpensive consumables for RepRap printers. Such methods of household disposal are not only practical, but also have a positive impact on the ecological situation.
The development and customization of RepRap 3D printers has created a new category of semi-professional printers for small businesses. Manufacturers such as Solidoodle, RoBo and RepRapPro offer kits for under $1,000. The accuracy of these devices is between industrial and consumer printers. Recently, high-performance printers using a delta-shaped coordinate system, or the so-called "delta robots", are gaining popularity. Some companies offer software to support printers made by other companies.
Application
The use of LED projectors helps reduce the cost of stereolithography printers. In the illustration DLP printer Nova
3D printing allows you to equalize the cost of producing one part and mass production, which poses a threat to large-scale economies. The impact of 3D printing may be similar to the introduction of manufacture. In the 1450s, no one could predict the consequences of the printing press, in the 1750s, no one took the steam engine seriously, and transistors 19The 50s seemed like a curious innovation. But the technology continues to evolve and is likely to have an impact on every scientific and industrial branch with which it comes into contact.
The earliest application of additive manufacturing can be considered rapid prototyping, aimed at reducing the development time of new parts and devices compared to earlier subtractive methods (too slow and expensive). The improvement of additive manufacturing technologies leads to their spread in various fields of science and industry. The production of parts previously only available through machining is now possible through additive methods, and at a better price.
Applications include breadboarding, prototyping, molding, architecture, education, mapping, healthcare, retail, etc.
Industrial applications:
Rapid prototyping: Industrial 3D printers have been used for rapid prototyping and research since the early 1980s . As a rule, these are quite large installations using powder metals, sand mixtures, plastics and paper. Such devices are often used by universities and commercial companies.
Advances in rapid prototyping have led to the creation of materials suitable for the production of final products, which in turn has contributed to the development of 3D production of finished products as an alternative to traditional methods. One of the advantages of fast production is the relatively low cost of manufacturing small batches.
Rapid production: Rapid production remains a fairly new method whose possibilities have not yet been fully explored. Nevertheless, many experts tend to consider rapid production a new level of technology. Some of the most promising areas for rapid prototyping to adapt to rapid manufacturing are selective laser sintering (SLS) and direct metal sintering (DMLS).
Bulk customization: Some companies offer services for customizing objects using simplified software and then creating unique custom 3D models. One of the most popular areas was the manufacture of cell phone cases. In particular, Nokia has made publicly available the designs of its phone cases for user customization and 3D printing.
Mass production: The current low print speed of 3D printers limits their use in mass production. To combat this shortcoming, some FDM devices are equipped with multiple extruders, allowing you to print different colors, different polymers, and even create several models at the same time. In general, this approach increases productivity without requiring the use of multiple printers - a single microcontroller is enough to operate multiple printheads.
Devices with multiple extruders allow the creation of several identical objects from only one digital model, but at the same time allow the use of different materials and colors. The print speed increases in proportion to the number of print heads. In addition, certain energy savings are achieved through the use of a common working chamber, which often requires heating. Together, these two points reduce the cost of the process.
Many printers are equipped with dual printheads, however this configuration is only used for printing single models in different colors and materials.
Consumer and hobby use
Today, consumer 3D printing mainly attracts the attention of enthusiasts and hobbyists, while practical use is rather limited. However, 3D printers have already been used to print working mechanical clocks, woodworking gears, jewelry, and more. Home 3D printing websites often offer designs for hooks, doorknobs, massage tools, and more.
3D printing is also being used in hobby veterinary medicine and zoology – in 2013, a 3D printed prosthesis allowed a duckling to stand up, and hermit crabs love stylish 3D printed shells. 3D printers are widely used for the domestic production of jewelry - necklaces, rings, handbags, etc.
The Fab@Home open project aims to develop general purpose home printers. The devices have been tested in research environments using the latest 3D printing technologies for the production of chemical compounds. The printer can print any material suitable for extrusion from a syringe in the form of a liquid or paste. The development is aimed at the possibility of home production of medicines and household chemicals in remote areas of residence.
Student project OpenReflex resulted in a design for an analog SLR camera suitable for 3D printing.
Clothing
3D printing is gaining ground in the fashion world as couturiers use printers to experiment with swimwear, shoes and dresses. Commercial applications include rapid prototyping and 3D printing of professional athletic shoes - the Vapor Laser Talon for soccer players and New Balance for track and field athletes.
3D bioprinting
EBM titanium medical implants
3D printing is currently being researched by biotech companies and academic institutions. The research is aimed at exploring the possibility of using inkjet/drip 3D printing in tissue engineering to create artificial organs. The technology is based on the application of layers of living cells on a gel substrate or sugar matrix, with a gradual layer-by-layer build-up to create three-dimensional structures, including vascular systems. The first 3D tissue printing production system based on NovoGen bioprinting technology was introduced in 2009year. A number of terms are used to describe this research area: organ printing, bioprinting, computer tissue engineering, etc.
One of the pioneers of 3D printing, research company Organovo, conducts laboratory research and develops the production of functional 3D human tissue samples for use in medical and therapeutic research. For bioprinting, the company uses a NovoGen MMX 3D printer. Organovo believes that bioprinting will speed up the testing of new medicines before clinical trials, saving time and money invested in drug development. In the long term, Organovo hopes to adapt bioprinting technology for graft and surgical applications.
3D printing of implants and medical devices
3D printing is used to create implants and devices used in medicine. Successful surgeries include examples such as titanium pelvic and jaw implants and plastic tracheal splints. The most widespread use of 3D printing is expected in the production of hearing aids and dentistry. In March 2014, Swansea surgeons used 3D printing to reconstruct the face of a motorcyclist who was seriously injured in a road accident.
3D printing services
Some companies offer online 3D printing services available to individuals and industrial companies. The customer is required to upload a 3D design to the site, after which the model is printed using industrial installations. The finished product is either delivered to the customer or subject to pickup.
Exploring new applications
3D printing makes it possible to create fully functional metal products, including weapons.
Future applications of 3D printing may include the creation of open source scientific equipment for use in open laboratories and other scientific applications - fossil reconstruction in paleontology, the creation of duplicates of priceless archaeological artifacts, the reconstruction of bones and body parts for forensic analysis, the reconstruction of heavily damaged evidence collected from crime scenes. The technology is also being considered for application in construction.
In 2005, academic journals began to publish materials on the possibility of using 3D printing technologies in art. In 2007, the Wall Street Journal and Time magazine included 3D design in their list of the 100 most significant achievements of the year. The Victoria and Albert Museum at the London Design Festival in 2011 presented an exhibition by Murray Moss entitled "Industrial Revolution 2.0: how the material world materializes again", dedicated to 3D printing technologies.
In 2012, a University of Glasgow pilot project showed that 3D printing could be used to produce chemical compounds, including hitherto unknown ones. The project printed chemical storage vessels into which “chemical ink” was injected using additive machines and then reacted. The viability of the technology was proven by the production of new compounds, but a specific practical application was not pursued during the experiment. Cornell Creative Machines has confirmed the feasibility of creating food products using hydrocolloid 3D printing. Professor Leroy Cronin of the University of Glasgow has suggested using "chemical ink" to print medicines.
The use of 3D scanning technology makes it possible to create replicas of real objects without the use of casting methods, which are costly, difficult to perform and can have a destructive effect in cases of precious and fragile objects of cultural heritage.
An additional example of 3D printing technologies being developed is the use of additive manufacturing in construction. This could make it possible to accelerate the pace of construction while reducing costs. In particular, the possibility of using technology to build space colonies is being considered. For example, the Sinterhab project aims to explore the possibility of additive manufacturing of lunar bases using lunar regolith as the main building material. Instead of using binding materials, the possibility of microwave sintering of regolith into solid building blocks is being considered.
Additive manufacturing allows you to create waveguides, sleeves and bends in terahertz devices. The high geometric complexity of such products could not be achieved by traditional production methods. A commercially available professional EDEN 260V setup was used to create structures with a resolution of 100 microns. The printed structures were galvanized with gold to create a terahertz plasmonic apparatus.
China has allocated nearly $500 million. for the development of 10 national institutes for the development of 3D printing technologies. In 2013, Chinese scientists began printing living cartilage, liver and kidney tissue using specialized 3D bioprinters. Researchers at Hangzhou Dianqi University have even developed their own 3D bioprinter for this challenging task, dubbed Regenovo. One of Regenovo's developers, Xu Mingeng, said it takes less than an hour for the printer to produce a small sample of liver tissue or a four to five inch sample of ear cartilage. Xu predicts the emergence of the first full-fledged printed artificial organs within the next 10-20 years. That same year, researchers at the Belgian Hasselt University successfully printed a new jaw for an 83-year-old woman. After the implant is implanted, the patient can chew, talk and breathe normally.
In Bahrain, sandstone-like 3D printing has created unique structures to support coral growth and restore damaged reefs. These structures have a more natural shape than previously used structures and do not have the acidity of concrete.
Intellectual property
Section of liver tissue printed by Organovo, which is working to improve 3D printing technology for the production of artificial organs
3D printing has been around for decades, and many aspects of the technology are subject to patents, copyrights, and trademark protection. However, from a legal point of view, it is not entirely clear how intellectual property protection laws will be applied in practice if 3D printers become widely used.
distribution and will be used in household production of goods for personal use, non-commercial use or for sale.
Any of the protective measures may negatively affect the distribution of designs used in 3D printing or the sale of printed products. The use of protected technologies may require the permission of the owner, which in turn will require the payment of royalties.
Patents cover certain processes, devices, and materials. The duration of patents varies from country to country.
Often, copyright extends to the expression of ideas in the form of material objects and lasts for the life of the author, plus 70 years. Thus, if someone creates a statue and obtains copyright, it will be illegal to distribute designs for printing of an identical or similar statue.
Influence of 3D printing
Additive manufacturing requires manufacturing companies to be flexible and constantly improve available technologies to stay competitive. Advocates of additive manufacturing predict that the opposition between 3D printing and globalization will escalate as home production displaces trade in goods between consumers and large manufacturers. In reality, the integration of additive technologies into commercial production serves as a complement to traditional subtractive methods, rather than a complete replacement for the latter.
Space exploration
In 2010, work began on the application of 3D printing in zero gravity and low gravity. The main goal is to create hand tools and more complex devices "as needed" instead of using valuable cargo volume and fuel to deliver finished products to orbit.
Even NASA is interested in 3D printing
At the same time, NASA is conducting joint tests with Made in Space to assess the potential of 3D printing to reduce the cost and increase the efficiency of space exploration. Nasa's additive-manufactured rocket parts were successfully tested in July 2013, with two fuel injectors performing on par with conventionally produced parts during operational tests subjecting the parts to temperatures of around 3,300°C and high pressure levels. It is noteworthy that NASA is preparing to launch a 3D printer into space: the agency is going to demonstrate the possibility of creating spare parts directly in orbit, instead of expensive transportation from the ground.
Social change
The topic of social and cultural change as a result of the introduction of commercially available additive technologies has been discussed by writers and sociologists since the 1950s. One of the most interesting assumptions was the possible blurring of boundaries between everyday life and workplaces as a result of the massive introduction of 3D printers into the home. It also points to the ease of transferring digital designs, which, in combination with local production, will help reduce the need for global transportation. Finally, copyright protection may change to reflect the ease of additive manufacturing of many products.
Firearms
In 2012, US company Defense Distributed released plans to create a "design of a functional plastic weapon that could be downloaded and played by anyone with access to a 3D printer." Defense Distributed has developed a 3D printed version of the receiver for the AR-15 rifle, capable of withstanding more than 650 shots, and a 30-round magazine for the M-16 rifle. The AR-15 has two receivers (lower and upper), but legal registration is tied to the lower receiver, which is stamped with a serial number. Shortly after Defense Distributed created the first working drawings for the production of plastic weapons in May 2013, the US State Department requested that the instructions be removed from the company's website.
The distribution of blueprints by Defense Distributed has fueled discussion about the possible impact of 3D printing and digital processing devices on the effectiveness of gun control. However, the fight against the proliferation of digital weapon models will inevitably face the same problems as attempts to prevent the trade in pirated content.
Go to the 3D Printing Encyclopedia home page0001
3D printing opens up fundamentally new opportunities for humanity, and all this is thanks to a wide pool of technologies that are constantly being improved. Today there are already more than ten of them, and we are sure that the flight of inquisitive engineering thought will not stop there. In the meantime, let's briefly review the key features of the 3D prototyping methods at our disposal.
FDM - layer by layer deposition.
FDM (Fused Deposition Modeling) is the simplest and most common 3D prototyping technology in additive and industrial manufacturing, thanks to which general-purpose 3D printers have become available not only to commercial and industrial organizations, but also to individuals. She appeared at 1988 in the kitchen of Scott Crump, the talented designer who two years later created the world leader in 3D hardware and 3D printing solutions, Stratasys. The print file is created mainly in the STL format, which allows you to segment the virtual model into layers. It is supported by all CAD CAD programs and is considered universal. The software package necessarily contains a slicer that reads data from the original layout and cuts it into layers. The consumable material in this printing technology is a plastic filament, which, when it enters the extruder, is heated to the melting temperature and dosed through the nozzle onto the working surface of the 3D printer. So layer by layer, the thickness of which depends on the capabilities of the printer, a finished object is grown on the desktop, the contours and geometry of which exactly correspond to a virtual prototype that until recently existed only on a computer screen. A wide range of plastic filament, presented on the modern market of consumables for 3D printing, makes it possible to produce finished products and their fragments of various sizes, types and purposes, determined by the physical and chemical properties of the material.
SLA - stereolithography
This additive technology is based on the printing of models and their fragments from liquid photopolymer resins, cured under the influence of an ultraviolet laser or a similar energy source. Stereolithography is the very first 3D printing technology, invented in 1984 and patented in 1986 by Charles Hull, who designed the world's first apparatus for making dense physical objects by layering a liquid photopolymer. As in the case of a plastic thread, the model is grown by layer-by-layer laser drawing of the outlines of the model - at the points of contact with the laser, the photopolymer freezes. As each layer is formed, the work platform is immersed in a tank filled with liquid resin to level the surface. This cycle is repeated as many times as needed to complete the prototyping process. The main advantage of stereolithography is its high accuracy; the layer thickness, depending on the capabilities of the printer, can reach 15 microns, which is several times thinner than a hair. This explains the demand for SLA in digital medicine, in particular dentistry, and jewelry. Industrial models of printers for SLA printing allow you to create objects up to several meters in size.
SLM - Selective Laser Melting
This additive prototyping method is based on the use of a high power fiber laser. The main consumable material is a powder metal alloy. The developers of this technology are employees of the Institute for Laser Technology Wilhelm Meiners, Konrad Wissenbach and employees of F&S Stereolithographietechnik GmbH Dieter Schwarz and Matthias Fokele. An interesting fact is that Schwartz still works in the former F&S, which eventually turned into SLM Solutions GmbH, and Fokele created the main competitor of this company, ReaLizer GmbH. But back to technology. SLM allows you to print objects with an accuracy of 20-100 microns; a layout in STL format is used as a drawing of a future product. A thin layer of powder is applied to the working surface, which is located in a chamber filled with an inert gas (mainly argon). The complete absence of metal contact with oxygen prevents its oxidation, which makes it possible to work even with titanium alloys that are difficult in terms of processing. Each new layer is fused with the previous one under the influence of a laser beam directed in the coordinate plane. Stainless and tool steel, gold, silver, aluminum, titanium and alloys based on cobalt and chromium are used as consumables. This technology is considered the best for manufacturing thin-walled objects with complex geometry, which are successfully used in the engineering, aerospace, automotive, and medicine industries. The most similar technologies are direct metal laser sintering (DMLS) and electron beam melting (EBM).
SLS - Selective Laser Sintering
Another additive manufacturing technology used for printing functional prototypes and small-scale production. Its essence lies in the sequential layer-by-layer sintering of powder consumables using high-power lasers. SLS is sometimes confused with SLM, but the difference between the two methods is enormous. The first provides only partial melting of the powder raw material, the degree of which is sufficient to ensure reliable adhesion of the layers. The second is based on complete melting and is used for the production of monolithic models. The founders of SLS are Carl Deckard and Joseph Beeman, employees of the University of Texas localized in Austin, working on projects of national importance, including defense ones. Powdered plastics and metals are processed by one or more carbon dioxide (usually) lasers - sintered to form a physical object. Its contours are gradually drawn in accordance with the digital model. One of the features of objects made by this method is that their density is determined not by the duration of irradiation, but by the maximum energy of the emitter. Another characteristic feature is the complete absence of the need to use a support structure, which is typical for FDM and SLA, since the support of the hinged elements of the future model is provided by unused material.
DMLS - direct laser sintering
This technique was developed by the well-known Munich company EOS and is used for the production of metal products. The file in STL format, already well known to us, is divided into drawings before starting printing, each of them is one of the layers created when building the model. The sintering of metal powder is provided by sufficiently powerful fiber-optic lasers. A small amount of metal is fed into the build chamber and leveled using a special roller. The laser head moves along the contours specified in the drawing and sinters fresh powder in accordance with the contour of the future product, and so on until the finished object is in front of you. The main charm of this technology is its high accuracy, the layer thickness reaches 20 microns (for comparison, most personal FDM printers have a maximum accuracy of 100 microns). Increasing the number of lasers can significantly reduce prototyping time without sacrificing accuracy - today it is one of the most productive professional industrial technologies.
EBM - Electron Beam Melting
Electron Beam Melting is another additive technology for working with metals, somewhat similar to SLM technology, but with higher productivity. The key difference from other rapid prototyping methods is that in this case, instead of a laser, an electron emitter is used as an energy source. During the melting process, a high-power electron beam affects the metal powder, which is located in the vacuum building chamber. The layers of the future object are grown gradually, without contact with oxygen and other active gases, which ensures the high density and strength of the final product. This is the main advantage of EBM, which can give odds to all other additive technologies for working with powder consumables.
LOM – 3D lamination
This method was developed by the world-famous 3D company Helisys Inc and belongs to rapid prototyping technologies. Its essence is in the sequential layer-by-layer bonding of film or sheet materials (metal foil, plastic and even paper). The contour of each new layer is determined by the laser cutting parameters. The printing process is as follows: the first layer of material with a pre-applied adhesive layer is placed on the working platform, the laser draws the contour of the future product, the excess material is cut off, the platform with the finished layer is moved down, a new sheet is fed into the camera. Of course, the resolution is inferior to stereolithography or selective laser sintering, but on the other hand, three-dimensional lamination makes it possible to produce dense and large-sized products that respond well to post-processing. The features of LOM include the need for post-processing of the finished object, as well as the fact that the layer thickness depends on the selected production material. This is the most accessible and inexpensive method of 3D prototyping due to the low cost of consumables.
SGC
This 3D printing technology originated in 1986 in Israel. It is based on high-precision layer-by-layer construction of a model using photopolymer resins and subsequent UV irradiation of a physical photomask of the future product, or on the so-called mask (hence the name). As a result, the material polymerizes, the excess is removed from the working chamber, and all cavities are filled with wax. At the end of each stage of model building, surface machining is possible, after which the printing process is resumed. At the very end of the process, it is necessary to melt the wax. The polymer resins used as consumables are similar in density and viscosity to ABS plastic. This makes it possible not to use supporting structures in the printing process, as in SLA prototyping, and, in addition to high accuracy in the horizontal plane, to achieve high resolution in the vertical. It should be noted that today SGC in its pure form is practically not used - it was replaced by a more advanced FTI technology, reminiscent of digital LED printing.
DLP - Digital LED Printing
Today, this relatively young technology is considered one of the most worthy alternatives to laser stereolithography - it is also based on the processing of photopolymer resins, allowing for amazing accuracy in prototyping. Instead of lasers, DLP printers use LED light projectors that form not only the contour of the future model, but the entire layer. DLP technology is in demand in digital dentistry, souvenir production, in the field of free design and jewelry, 3D printers working in it are gradually replacing SLA equipment. The advantages include excellent accuracy (up to 15 microns), a wide range of mechanical and physico-chemical characteristics of photopolymer resins and a large selection of colors.
MJM - Multi-Jet Modeling
This additive manufacturing technology is proprietary - it was developed and patented by the world famous company 3D Systems for use in the ProJet line of professional 3D printers. The uniqueness of this method is that it combines all the best features of FDM, SLA and 3DP (three-dimensional inkjet printing) technologies. The range of consumables is quite wide - it includes thermoplastics and waxes that gradually solidify as the model cools, as well as photopolymer resins that polymerize under UV exposure. Wax can also be used to build auxiliary support elements, and its low cost significantly reduces the cost of prototyping. MJM printers are indispensable in the production of samples and parts, the requirements for accuracy of which are high. They are in demand in digital dentistry, jewelry, engineering, and industrial design.
3DP - inkjet 3D printing. 3D printing technologies.
This method, developed by the Massachusetts Institute of Technology, is one of the oldest; it owes its distribution to the Z Corporation, which was subsequently absorbed by 3D Systems. Like any additive technology, 3DP works in the key of layer-by-layer construction of a model or powder consumable of any type and purpose. After evenly distributing each new layer of powder over the working surface, the print head applies a binder to it. Each subsequent layer is glued to the previous one, forming a complete model. The very first 3DP printers used gypsum as a consumable; today, in addition to dyes and sealants, extruders also do an excellent job with plastics, sand mixtures, and some metal alloys. The technology itself is inexpensive, but in most cases the product requires additional post-processing and improvement of strength characteristics. Another advantage of the method is the absence of the need to use support structures, as in FDM and SLA technologies. 3DP and its modifications are used in a wide range of fields, in particular in bioprinting aimed at growing organic tissue.
CJP - color inkjet
CJP is a type of 3DP that uses powder consumables that are printed with a resin binder on a thin layer when printed. This technology can easily create multi-colored models with impressive geometric complexity, while unused raw materials can be used as a support structure or collected at the end of a print session for further use. Basically, CJP printers work with various plastics - from those resembling silicone and rubber in their characteristics to impact-resistant and thermally stable materials. Basically, equipment of this type is used in industrial and architectural design, animation. With a relatively low cost of production, the advantages of this technology also lie in high accuracy in the reproduction of geometry and the ability to create multi-color products.
SHS - selective heat sintering
Like other technologies based on melting, this method involves the sintering of plastic or metal powder under the influence of a source of thermal energy - this is the only significant difference from the classic SLS. At the end of the formation of each layer, the working platform goes down, after which a new thin layer of consumable material is applied to the surface using a roller mechanism. Layer sintering is contour, it corresponds to the virtual model. Such 3D printers have a lower energy efficiency and can only work with selected consumables - plastics and low-melting metals, which limits their scope. However, they are popular in the field of industrial design and custom production of objects with high demands on detail.
EBF
3 - Production Electron Beam Melting This is a highly advanced, state-of-the-art additive method developed by NASA to produce models that are of such high quality that they do not require post-processing and can be used immediately for their intended purpose. The key feature of EBF 3 is the gradual addition of material, which significantly reduces its consumption and at the same time ensures high accuracy in layering. As a result of printing, you get an almost finished product - it is characterized by accuracy in geometric compliance with a virtual prototype, excellent density and surface quality. The chamber for melting metal (the main consumable) is vacuum, the contour is fixed by a moving electron beam, a thin metal wire is fed to the focus point. The metal instantly solidifies, which makes the printing process even faster. In this technology, it is possible to print high-precision, geometrically complex objects ranging in size from a couple of millimeters to a couple of meters.
SDL - selective deposition lamination
Lamination using selective deposition has nothing to do with the LOM technology already familiar to us - in SDL, cutting is performed with specialized blades, and only certain fragments of the future object are glued using a printer.