3D printing surfboards
WYVE and its 3D printed eco-surfboards
Published on January 15, 2020 by Carlota V.
WYVE, previously known as HEXA Surfboard, is a young French company that has relied on 3D printing to design surfboards that are more environmentally friendly, customizable and with a transparent design. Aware of today’s ecological problems, the brand is totally rethinking the way it produces and distributes its boards by promoting local manufacturing, close to surf spots. It uses recycled and recyclable plastic waste to create tailor-made boards where the honeycomb core of the boards has been 3D printed. This allows the company to use less material whilst optimizing the solidity of its boards. We met the team to learn more about the process of designing a board and the impact of 3D printing on the surfing world.
3DN: Can you introduce yourself and your relationship with 3D technologies?
We are Léo, Sylvain and Mylène, friends for 10 years, passionate surfers and all three engineers by training. We are the co-founders of WYVE, a brand that is rethinking the way surfboards are made and distributed, notably thanks to 3D technologies. As engineers, we were introduced to digital modeling and optimization at an early age, but it’s really when we started prototyping our first surfboards that we were able to gain real expertise in 3D printing. We had the chance to prototype at the Fablab of the Ecole Polytechnique where we were able to train on a large 3D printer. In a few months, we were able to learn a lot and share our expertise with the other project leaders who were prototyping there.
The WYVE team | Credits: EuroSIMA – Stephane Robin
3DN: Why did you create WYVE?
If more than 80% of surfers feel very concerned about the future of oceans and the climate, especially when it comes to surfing, they are not ready to make any concessions on the performance of their equipment. The younger generation is all the more ready to combine ecology and innovation in their consumption for a simple, fluid and online experience.
The reality of surfboards is far from it today. The many intermediaries that line the production chain of boards produce carbon emissions linked to transport, toxic waste and accumulated margins have been blocking the sector’s ability to innovate since the 1960s. In a few figures: the components of a surfboard travel 10,000 km around the world before being used, a board is 95% derived from petrochemical materials, and more than 6 kg of toxic and carcinogenic waste is emitted for a board weighing barely 3 kg.
Credits: Mathilde Perriol
It is from this paradoxical observation that we decided to create WYVE, a brand that totally rethinks the way surfboards are produced and distributed. Thanks to advanced technologies such as 3D printing, we manufacture in one place, from recycled and recyclable plastic waste, high performance, custom-made, eco-responsible boards with an original transparent design! Available and simply customizable online, we want to allow the surfer who doesn’t have access to a shaper to ride the board of his dreams. The one that allows him not only to have pure sensations but also to progress!
3DN: Can you explain the process of making a board?
Starting with an online questionnaire for customization or simply custom dimensions, we start by designing the custom shape (dimensions and curves) of the board. We work on a customization algorithm that automatically translates measurement and feeling data into a custom design. Once the digital file of the shape is validated, we move on to the 3D printing of the heart of our board.
We are keen to develop our local production to limit our carbon impact linked to transport. We have our own large-format machines, close to the surf spots, and collaborate with specialized actors in the region. In terms of raw materials, our first models have been printed with PLA, known to be bio-sourced and easily usable in 3D printing. In parallel, we are developing the manufacture of the core of our boards from 100% recycled PET, ideally from the plastic waste that pollutes our oceans.
Credits: Auguste Fenez
Our time to print the heart of the board is several tens of hours, variable depending on the degree of personalization of the boards. Its honeycomb design maximizes the strength of the structure in relation to the amount of material used, and also highlights the board’s special transparent design. The heart of our board is then glazed with bio-sourced resin and fiberglass. Even though our resin is made in France and awarded the ECOBOARD Gold label, we focus a large part of our R&D to limit our use of both resin and fiberglass, which have an impact on the eco-responsibility of our boards.
All these steps are done in the same place, in our micro-factories, which are also designed to welcome our community of users to exchange with them and allow them to see and touch our boards.
3DN: Why did you choose 3D printing as a manufacturing method?
3D printing technologies are an excellent manufacturing method for us to meet our performance and customization requirements. Thanks to parametric design, we can precisely and efficiently adapt the shape of a board to the surfer.
But 3D printing is also an important asset in terms of eco-design. First of all, it allows us to produce much less waste. Indeed, we use FDM 3D printing technology, which is an additive technology: it’s the superimposition of layers of materials that make up our product. By using just the right amount of material, there is no toxic or unused waste, as is the case in more traditional board manufacturing. In addition, 3D printers can be used with a wide variety of materials, which for us mean more eco-friendly raw materials. Remember that the core of conventional high-performance boards is made of polyurethane, which makes them non-recyclable and emits very toxic gases.
Credits: Ethan Jones
In addition, 3D printing is an excellent way to make fully custom-made surfboards. The high level of customization, which makes our surfboards unique and tailored to the surfer, is a key element in their environmental impact. In terms of use, they meet the current needs of the surfer but also his future needs in terms of technical progress. A better adapted surfboard indirectly has a lighter impact on the environment as it will last you longer. And since our surfboards are made to measure, there is no stock or overproduction. Finally, 3D printing allows us to build surfboards that are more durable and repairable.
We are aware that 3D printing does not solve all environmental issues, especially in terms of energy consumption. That’s why we are also working on optimizing the printing time of a surfboard to minimize our energy consumption, on two levels. The first level is to optimize the components of our machines when printing our designs to improve our printing speed. Indeed, speeding up the printing process means producing more surfboards with the same amount of energy. And the second level is to digitally optimize the file defining the printer’s movements to build a surfboard.
3DN: Why is a WYVE surfboard more durable than another board? Is it recyclable?
First of all, a WYVE surfboard is stronger than a classic board with a layer of foam, especially because of its honeycomb structure. Secondly, it is easier to repair. As the inside of our board is hollow, our simple valve system makes it easy to empty the board in case of water infiltration. It is then sufficient to plug the hole classically. Since there is no foam inside, the core does not rot in contact with water.
3D printing provides a transparent design
Moreover, the core of our boards is recyclable! If your surfboard is badly damaged, we are committed to recovering the materials it contains in order to recycle the plastic and create new surfboards. That’s why we start a work of education and material recovery with our users to encourage them to recycle their boards.
Finally, we strongly believe that the durability of our surfboards is also very much linked to the suitability it has with its owner. Indeed, a surfboard that is perfectly adapted to its owner is more likely to be used correctly and for longer than a surfboard with a more random shape.
3DN: Any last words for our readers?
Join our community on the networks to come and test our boards and don’t hesitate to come and see us in our offices in Anglet! You can find more information HERE.
What do you think of the WYVE surfboards? Let us know in a comment below or on our Facebook and Twitter pages! And remember to sign up for our free weekly Newsletter, to get all the latest news in 3D printing send straight to your inbox!
Shaping the Revolution: 3D Printed Surfboards Are Here
The tried and tested method of moulding and mowing foam into the shape of a surfboard has existed for the better part of half a century. But now, as 3D printing has moved well beyond the prototyping phase, it was only a matter of time before that technology translated over to surfing.
Wyve, a France-based company operating out of Anglet (about 30 mins south of Hossegor) are using 3D printers to shape a whole range of surfboards, that utilise an internal hexagonal structure, filled with air (yes, air) rather than using traditional foam blanks.
The lineup of Wyve Surfboards - quick; before you get into the article, what do you think of the aesthetic?
© 2023 - Clara Groussin.
The boards are still glassed with fibreglass, but the whole process promises to remove around 30 per cent of the greenhouse gasses emitted when shaping with a PU or PE-based blank.
As with all new tech that enters the surf-sphere, there's bound to be a number of nay-sayers – yet, this technology could be a significant shift forward in producing surfboards. As the bosses at Wyve say, 'they're not here to replace the art of shaping but hope this method will sit alongside what's come before, offering a viable alternative', much like wooden, hand-shaped crafts.
Naturally, we had questions. So we tapped up Wyve's Léo Kerhir to ask...
Let's take it from the top; how did you come up with the designs for 3D printing a surfboard?
LK: Léo Bouffier and Sylvain Fleury started thinking about it three-years-ago. Surfboards are known to be polluting the atmosphere and basically haven’t changed much over the past 60-years in the way they are built. They came up with the 3D-printing solution as the means to make more durable surfboards with cleaner materials, while pushing further the level of high-performance in surfboards.
The hexagonal design is thought to be three-times more resistant than a foam blank while keeping the needed flexibility. It went through a lot of research and development to reach the ideal design.
Still a load of shaping knowledge goes into making these unique shapes, it's just sculpted out by a 3D printer.
© 2023 - Clara Groussin.
Sounds promising, what’s the feedback like?
Feedback is great! We’ve been working with local talents to test our boards on a regular basis and get feedback on top of our internal mechanical tests.
Testing and iterating has been the key to reach the level of high-performance we have today. Overall, surfers feel a much better wave entry and speed generation than with their everyday boards as well as a great strength impression of the board. We are still learning a lot from the tests in the water and keep improving.Pictures and edits speak more than words.
That's interesting, what's different about them then? What makes them tougher?
They are different in many ways. We replace the traditional foam blank by a 3D-printed bio-based plastic internal structure. While we still use fibreglass and bio-based resin, it is air inside the structure. Hexagons connect to each other and that allows the air to go through.
Our goal isn’t to replace all the traditional surfboard manufacturers or local shapers, but to offer something different to the market
There is a pressure valve on the tail that regulates by itself. The second use of the valve is in case of a ding. A traditional surfboard would soak the water and go yellow or soft after some time. We are able to drain the water out thanks to the valve. The bio-based plastic is hydrophobic so it doesn’t soak water.
About the structure itself, we are able to control the parameters such as the flex, mass repartition, strength in some key parts. ... Weight wise, we are similar to PU boards.
Last but not least, it is way different – you can see through it!
Look! You can still get barrelled on a 3D printed board!
© 2023 - Ian Thurtell.
You'll get a good look at what's below you. Walk us through the process – how long do they take to make?
Once the shape is decided by the customer, it goes to parametric design, then the 3D-printing starts. The machine will melt the bio-based plastic filament to drop it layer-by-layer, building the whole internal core of the surfboard. It takes between 20 and 50 hours of printing depending on the shape, the machines are running all day.
The remaining parts of the process are pretty similar to traditional surfboard glassing. We use fibreglass and bio-based epoxy. All boards are vacuum-bagged during the glassing process to have the strongest coat possible.
We have one particular process to glass it, which is the major change with traditional glassing.
Still the traditional route of glassing.
© 2023 - Marion Martoglio.
If people are interested and want to order, would they go for their regular dimensions – or is it like-for-like?
Even though one of the main bits of feedback was that the paddling ease is better and they're more buoyancy than a traditional surfboard, we recommend surfers stick to their regular dimensions. That's because surfing these boards is relatively similar to their normal boards.
Do you think this a viable future for shaping? Feels as if it'll sit alongside traditional methods.
3D-printing offers tons of possibilities in terms of materials, weight, flex, mass-repartition and so on. On top of it, it is extremely precise to build custom boards on a large scale. We are convinced, 3D-printing is the future for intermediary to high-level surfboards since it allows surfers to reach better performance and new surfing feelings.
© 2023 - Leo Kehrir.
We all know shaping surfboards is not environmentally friendly – we touched on it before, but how do these boards compare on the eco-scale?
Regarding the internal core, we use bio-based plastic filament, that is called PLA. For the resin, it is 50 per cent bio-based. Our goal, on top of building surfboards with cleaner materials, is to build stronger boards that last longer.
Talking math, the Wyve manufacturing process emits 30 per cent less greenhouse gases than the traditional methods. Moreover, the board lifetime is twice longer than a PU or PE surfboard. We recently did a life cycle assessment of our process to help us improve even more, since it is extremely important to us since the very beginning.
When it comes to surfboard shaping, it is an art form. Some would see this as removing the art from the process. But there’s still a lot that that goes into 3D printing – do you think purists will ever try a 3D board – and how do you overcome some of the nay-sayers who are no doubt going to start saying ‘nothing is better than foam boards?'
There’s still a lot of hand-work that goes into the process. We are still designing the shapes and working on them in the same software as shapers. Then, the “post 3D-printing part” is just as important - we have a unique way of glassing our boards.
We are located in Anglet, France, with a lot of shapers around. They've all warmly welcomed us when we arrived here back in early 2020.
Nothing is better than making surfers try our boards to overcome those stereotypes. We make a lot of board test events and lend some testing boards to surfers that ask. Working with young athletes, local talents or free surfers has been the key as well. The goal is to show surfers that they can surf just as good, if not better, than with their traditional boards.
© 2023 - Lou Ceyrolle.
What’s the mission for the Hexa Surfboard? Is it to be a global company?
If we are delivering all over Europe for now, the other surfing continents are just around the corner. We have built one micro-factory in Anglet, which allows us to deliver boards over Europe.
Our goal in 2022 and in the years to come is to duplicate this “micro-factory” system in different countries, close to surfers and surf spots. We are already working with talented surfers worldwide.
Where can surfboard shaping go from here?
Our goal isn’t to replace all the traditional surfboard manufacturers or local shapers, but to offer something different to the market, in terms of technology, materials and surfing feelings.
Our approach is complementary to shapers since we work on the inner structure of the surfboard core. We definitely respect the art of shaping and are open to collaborate with some shapers to push the high-performance future together.
© 2023 - Helene Cascarino.
Free STL file Surfboard・3D printed model for download・Cults
Best 3D Printer Files in the Miscellaneous Category
Ale Maria
Free
1/10 scale tool cabinet with sliding door
1. 50 €
Naked bike V-twins Ducati style
5 €
Christmas house
6.78 €
Meeseeks box from Rick and Morty
15 €
Helly, Robocar Poli
0.62 €
Mate Goku (Dragon Ball)
Free
Wheel cooler 1/10 scale
2 €
Bestsellers in Miscellaneous category
Wednesday item
3.93 €
CHRISTMAS TREE v2
1,50 €
Mickey Christmas night light Litophane
3,50 €
Wednesday Addams, The Thing, The Thing
5 €
Addams Thing
1. 99 €
THING-ENVIRONMENT-COMPANY-HD-PRINT
1,30 €
Giarados - articulated sea serpent
1,50 €
Articulated Raykuaza Flexible Dragon Pokémon
1 €
THING Addams
€8.55
Key holder for middle finger
1 €
SlingHAMMER - repeating crossbow pistol for steel balls 6mm 8mm 10mm or 12mm
12.50 €
Mate Qatar 2022 FIFA World Cup
10 € -50% 5 €
hinged shenron
3 €
4th planet Fighting pre-Olympic god
12 €
Keychain Studded Tumbler with removable screw top Pill Box Square STL file for 3D printing
2. 61 €
Christmas house
6.78 €
Do you want to support Cults?
Do you like Cults and want to help us continue our journey on our own ? Please note that we are a small team of 3 people, so it is very easy to support us in maintaining activities and creating future developments of . Here are 4 solutions available to everyone:
-
AD: Disable your AdBlock banner blocker and click on our banner ads. nine0006
-
AFFILIATION: Shop online with our affiliate links here Amazon.
-
DONATIONS: If you want, you can donate via PayPal here.
-
* INVITE FRIENDS: * Invite your friends, discover the platform and great 3D files shared by the community!
Free 3D file Mechanical surfboard・3D printing object to download・Cults
Skateboard with fingers
0. 62 €
Buff Duck
Free
Pizza
Free
Skateboard with fingers
Free
Headset holder
Free
nine0007 Platypus PerryFree
Mobile print 001
Free
Electric eye
Free
The best files for 3D printers in the Tools category
Book box with sword hinge
Free
nine0007 Best choice 9 pieces precision screwdriver set holder2,85 €
Deactivated
3D Printer Cabinet / Enclosure
2. 99 €
covid 19 mask frame
free
Seal at the location of the control valve! nine0008
Free
Animated Eye Candy Bowl Upgrade
Free
Bestsellers in the Tools category
Armadillo - flexible wire conduit
1.69 €
PRECISE DIAL INDICATOR 3D PRINT DIY
1.91 €
nine0007 Rapid print paint bottle rack (6 sizes)2.83 €
Generativ Design Y-Filamentsplitter Bambulab AMS-Extern RS-CONCEPTS
2,50 €
Shrek Pooping Toothpaste Topper
2.85 €
Business card embossing system
3 €
nine0007 ARTEMIS -> Shop for Alligator 2 || 6.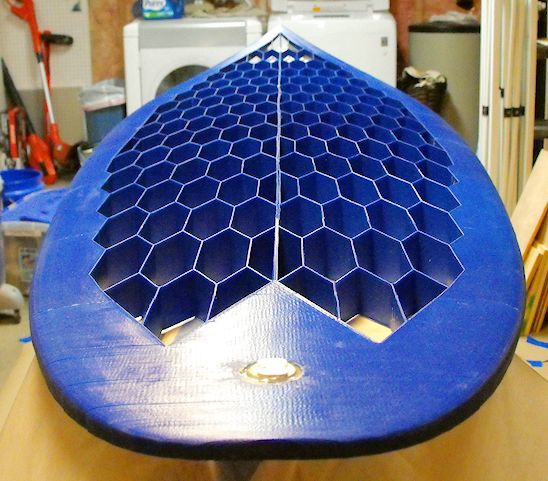
6.25 €
Ender 3, 3 V2, 3 pro, 3 max, dual 40mm axial fan hot end duct / fang. CR-10, Micro Swiss direct drive and bowden compatible. No support required for printing
1.58 €
Cut-Man - PET bottle cutter with handle!
€3.49
nine0007 Quick print stackable parts containers / storage boxes2.83 €
UNIVERSAL BED LEVELING INDICATOR FOR VERY ALL PRINTERS
2,39 €
Bit holder Spartan 4 mm Hex
1,80 €
Ender 3 Briss fang Gen2, red lizard, spider, nf crazy, dragonfly, etc.
1.75 €
Ratchet holders - magnetic - holders for tool box organization
2,70 €
Ender 3 S1 BEST cable guide - vertical
2,50 €
PET-Machine, make your own plastic bottle filament at home!
15 €
Do you want to support Cults? nine0005
Do you like Cults and want to help us continue our journey on our own ? Please note that we are a small team of 3 people, so it is very easy to support us in maintaining activities and creating future developments of .