3D printing filament moisture
What Effect Does Moisture Have on 3D Printer Filament Storage? (And how to fix it)
Table of Contents
Diagnosing the cause and precursors of 3D printed part failure is complex. Stringy prints, jams, bubbly uneven surface textures, improper extrusion flow, soft or brittle parts, and other common 3D printing build defects all inspire the same question…why do my 3D printed builds keep failing?
How Does Moisture Affect 3D Printing Filaments?
Because some 3D printing filaments are hygroscopic, meaning that they absorb moisture from the air, prolonged exposure to even moderately humid room air causes moisture saturation. After 150 hours in standard conditions, PLA filament may swell up to 40 micrometers before reaching its saturation point. 3D printers rely on tight tolerances and extremely small layer heights. Before the print even gets underway, an increased filament diameter of even 20 – 40 microns, (roughly the width of a human hair) can derail a build before it ever begins.
Indications of Possible Moisture Content in Failed 3D Printing Builds
- Filament cracks or makes popping noise as the filament is pushed through the extruded
- Holes in the top of parts
- Extruder tip bubbles with a tiny burst of steam, stringy or drooly
- The filament will not adhere to the print bed
- Repeated builds seem inconsistent or fail no changes in variables
- Extruder motor stops but filament keeps coming out
- Extruder motor starts but filament extrusion is delayed
- Parts become soft, fragile, and break easily
- Extruder jams
3D printing filament cabinets are the better, if not best moisture control solution for filament storage. Active dry cabinets control humidity and temperature which prevents moisture absorptions, even while in use.
An automatic humidity control cabinet with a hygrometer provides a quick and simple way to store 3D printer filament without hassle or baking. Changes in humidity directly affect air temperature, therefore automatically controlled drying environments exceed nearly all other methods for drying and storing 3D printing filament. The rear feed ports ensure your filament stays completely dry, easily accessible, and readily identified. Simply set the desired humidity level between low, medium, and high, and plug it in.
Humidity Before
Humidity After Powering On
What’s Wrong with Baking to Dry 3D Printer Filament?
While heat drying 3D printer filament in an oven is overwhelmingly accepted within the 3D printing community, time is a major consideration. PLA and Nylon filaments may take upwards of 4 – 8 hours to dry between 150°F and 200°F. The process is inefficient, and applying heat to thermoplastics with no ventilation is a questionable risk. Ultra fine particles (UFPs) and volatile organic particles (VOCs) infamous within chemicals like ABS during extrusion don’t account for residual substrates leftover from the manufacturing process, which could be activated during baking.
Problems with Dry Baking 3D Printing Filament
- Natural gas and propane fired ovens produce water vapor, therefore an electric resistance oven is required.
- Heating entire spools of filament is not recommended or advised, hence unspooling and respooling is required
- Unused filament will require rebaking if again exposed to ambient air
- Heat relaxes the stress in the filament, causing it to relax in the coiled state
- Overbaking can cause the filament to melt and stick to itself
The Impact of Moisture on 3D Printed Parts
See the Difference in 3D Printing Quality
For DIY and commercial applications that require large quantities of filaments spools, dry cabinets are a cost-effective option that eliminates baking completely. This image demonstrates the differences in print quality when printing with filaments stored in ambient (room) humidity vs. dry storage:
Flow Rate and Filament Moisture
Mass flow rate is directly correlated with the moisture content of 3D printed filament. Higher moisture content yields the lowest viscosity and the highest mass flow rate. While high flow rates are generally desirable, an unregulated flow rate leads to over extrusion.
Nylon, polycarbonate, and copolyester filaments all suffer ailments when exposed to moisture for extended periods of time.
PLAPLA is an organic material that readily absorbs moisture, and is extremely sensitive to trace water content. Moisture also affects the diameter of the filament when it in storage.
PVABecause PVA is a soluble support material, its ability to absorb water is a fundamental characteristic. Even mild humidity is enough to ruin an entire spool of unsealed filament.
NylonThe effect of moisture on nylon 3D printing filament is profound, as it may fully saturate in as little as 18 hours. READ: Important note about Nylon
3D printers provide a number of advantages over traditional manufacturing prototypes for small production runs or low volume end-use parts. Prototyping is empowered by repeatability, accelerated speed to market, and low-cost product testing. Dimensional and chemical stability of engineered thermoplastics in combination with advanced additive manufacturing technologies provide design freedom for geometries that were once unfeasibly complex.
Designers assemble, hold, feel, and check a part for fit and function before spending tens-of-thousands on casts or injection molds. Avoiding contract manufacturers means designs stay in-house, trade secrets avoid spoil, and product teams receive immediate feedback critical functions. Importantly, designs that were born to fail, fail first, and fail fast, before unforeseen design constraints send projects to the scrap yard after months of time and millions of dollars dumped into R&D.
Part orientation, minimum thickness, geometry restrictions, support structure, material properties: When it comes to achieving the most functional 3D printed parts, you’ve thought of it all. Inadequate air flow, differential cooling, material constraints, and non-uniform thermal gradients: they all contribute to the common ailments like heat distortion, extrusion failure, and part curling during 3D printing. But what about part failure contributions that extend beyond the chamber or print tray? Storage environments and post processing techniques also contribute to the final quality of 3D printed parts.
Share this Article:
Share on facebook
Share on twitter
Share on reddit
Share on print
Mitch Walleser
Mitch is a contributing writer for Production Automation Corporation. PAC is a factory-direct distributor of products and environmental solutions for industrial and critical requirements within electronics, medical device, life science, pharmaceutical, and general manufacturing industries. Mitch has worked with manufacturing engineers, in-house specialists, and factory experts to highlight and uncover manufacturing solutions. His background includes 3D printing, electronics, and cleanroom manufacturing.
Was this post helpful?
PrevPreviousHow to Remove 3D Printing Support Material Faster and Improve Final Quality
NextFilament Storage Cabinets for 3D PrintingNext
Recent Posts
Search Posts
Search for:
About Production Automation
Production Automation Corporation (that’s us) is an essential business supplier for medical device, cleanroom, and general manufacturing industries.
All products featured on the PAC blog are available through the www.gotopac.com webstore. Online orders are shipped and fulfilled Monday – Friday from PAC warehouses in California, Minnesota, and Texas.
Production Automation Corporation (PAC) stands 100% behind a product catalog of over 40,000 products, which includes support for factory warranties, value added services, and returns. Get help from a PAC sales rep during business hours via email, phone, or live chat.
Shop Online: www.gotopac.com
Toll Free: (888) 903-0333
Email: [email protected]
Office Hours: 8am - 5pm CST
The great enemy of the filaments for 3D printing
Humidity is the water that permeates a body or vapor present in the atmosphere. For all living beings, water is the most necessary to survive, even more than food, but for non-living elements, humidity is usually a source of problems, since it causes the oxidation and degradation of many materials. In the case of 3D printing, more specifically in the filaments, the concentration of excessive humidity can cause a long list of problems, all with the same end, a 3D printing failed.
The effects of attracting water can lead to the following problems: increased fragility, increased diameter (possible problems with printers with Bowden type extrusion system), filament degradation, breaking filament, etc. It is also necessary to take into account the fact that the filaments that have absorbed water will have a higher temperature for the extrusion. Remember to avoid having the filaments placed in the printer if you are not going to print. They can get stuck in the extruder because when absorbing water they get fat and increase in diameter.
The following map shows the average annual relative humidity (percentage ratio between the actual amount of water vapor contained in the air and what it would need to contain to saturate at the same temperature), a value that is obtained from the average humidity registered in the twelve months of the year. The relative humidity is very different depending on which part of the European geography you are, being more pronounced in the northern part of the continent.
Image 1: Map of relative humidity in Europe. Source: NeoGAF
The main consequences of moisture in a filament are:
- Degradation of the filament: The hygroscopic filaments are prone to absorb water to a great extent, since the water molecules are attached to the polymer molecules, forming strong intermolecular bonds.
These links can cause internal micro-breaks that weaken the filament structure itself.
- Extruder / HotEnd jam: The humidity of water concentrated in the filament when heated in the HotEnd evaporates, causing gaps inside the filament, turning it into a paste that clogs the barrel (Heat Break) or the nozzle. This problem is very common when using nylon filaments with high humidity percentages (> 20 %).
- Low quality 3D prints (resistance and finishing): The union of the aforementioned results in 3D prints with many problems, both mechanically and superficially. The gaps between layers (not always visible to the naked eye) caused by the evaporation of water, are critical points, where cracks are easily generated by applying low values of force. When the concentration of humidity is marked, the holes mentioned above, cause a rough and whitish surface finish.
Image 2: Problems generated by humidity.
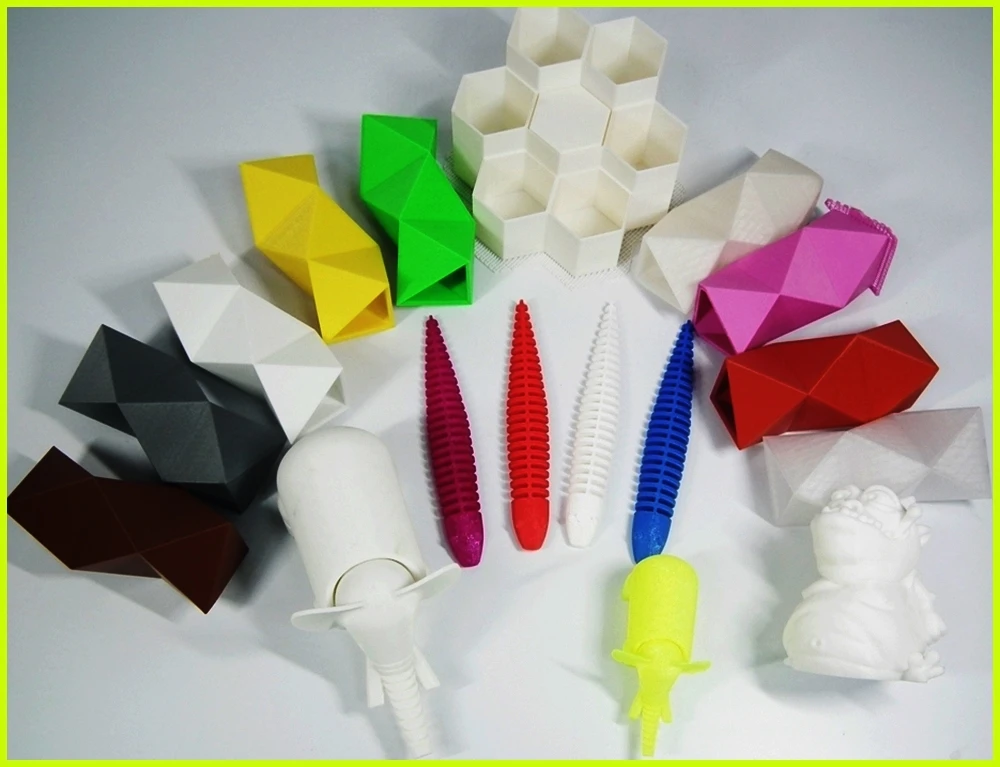
As a reason for the evolution of the world of 3D printing, there are filaments with high resistance to moisture, such as PETG or CPE HG100, copolyesters that can be exposed to water for long periods of time without problems. Among the other filaments we found some with moderate resistance, such as PLA or ABS, and others, especially nylons and PVA, highly prone to moisture absorption, reaching high values in less than a day.
Certain users of 3D printers use conventional methods to remove the moisture from the filament and store it, such as drying the material in a domestic oven and storing the filament in boxes with a closure that is not totally tight. These measures, apart from being dangerous in the case of the domestic furnace, are not totally effective, especially with technical and advanced materials. Here we quote a series of professional recommendations to eliminate moisture and how to store the filaments to prevent absorption:
Filament dryerThe most effective way to eliminate the moisture contained in a material is to use a filament dryer, such as the PrintDry filament dryer, a device capable of breaking the intermolecular bonds between the water and the polymer thanks to its drying temperature (35-70 ºC) and the natural air flow inside it, which drags moisture from the surface of the filament into the air that it surrounds it. The ideal value of moisture in a filament is between 10-13 %.
Both at the beginning of the use of a new coil and after drying a filament, proper storage is essential to maintain the minimum percentage of humidity. In conventional materials (PLA or ABS) and short storage intervals (<2 months) the use of your bag with a grip type closure is sufficient. In case of longer storage times or with technical and advanced materials this measure is not enough. The ideal solution is to use the PrintDry hermetic filament containers with vacuum sealing. They are high-strength plastic containers, where each user can store their filament safely without worrying about whether they pick up moisture. The potential of these containers is in the lid, since in this a vacuum valve is housed, through which and with the help of a manual pump (included with the containers), it is possible to extract the air from the interior of the container, providing storage free of dust and moisture. In this way, the correct condition of the filament can be guaranteed, although several months have passed since the coil was taken out of its original factory seal. The older, it must be taken into account that the relative humidity of the area where the material is stored affects in large quantity, this should be the least possible without harming the health of the user (A good value would be over 40 %).
The life of a filament of quality since its manufacture is 2-3 years, as long as it is in its original seal and vacuum. Once the original bag is opened, the time it takes to lose its mechanical and color properties depends on the type of material and storage. A PLA or ABS stored in the manner mentioned above can retain its properties for more than 1 year, but if it is not, it will resist a tenth of the time. In more delicate materials, such as nylons and PVA, the total loss of your life can be a few days.
It is therefore an evidence that maintaining the filaments with low humidity values (10-13 %) is a key factor to be taken into account at all times, to avoid problems before, during and after a 3D printing.
To have maximum reliability at the time of printing it is vital to have the maximum number of possible controlled variables, and humidity is one of them to ensure maximum robustness in the printing process.
Do you want to receive articles like this in your email?
Subscribe to our monthly newsletter and you will receive every month in your email the latest news and tips on 3D printing.
* By registering you accept our privacy policy.
3D Filament Storage - Top 5 Tips!・Cults
It's no surprise that the quality of 3D printing filament can make a big difference in the quality of your prints. That is why there has been much debate about how best to maintain and store the thread.
However, no one argues about the main enemy of 3D filament - moisture.
There are countless stories on the Internet about manufacturers finding their new threads damaged by moisture in the air. It is important to note that some threads are more sensitive to moisture than others. For example, PLA, PVA carrier material, nylon and ABS are particularly sensitive to moisture in the air.
- 1) Thread breakage: Some threads are more sensitive to moisture in the air because they are made of materials that easily absorb water. For example, PLA plastic is biodegradable and is made from natural resources such as corn or rice. While it's much better for the environment than other plastics, it also means that under the right conditions, it breaks down into carbon dioxide, water, and methane. Humid conditions and ultraviolet radiation accelerate the degradation of the filament, which weakens it and causes inconsistent or poor-quality prints.
On his blog, RepRage talks about an experiment in which scientists tested how long PLA takes to absorb water. They compared the weight of the thread before and after it was immersed in water for 30 days, and it turned out that it absorbed up to 60 ml of water! If you live in the tropics, you may want to store your floss in an airtight place so it doesn't absorb water from the air. Nylon is also highly absorbent and soaks with water as early as 18 hours after exposure to wet conditions.
-
2) Printer jams/nozzles: A side effect of filament absorbing water is that it increases in diameter and weakens the surface of the filament. When you insert it into the printer, it may cause a nozzle jam. Just as rice expands when you boil it in water, so does this filament expand and eventually become unusable because it cannot pass through your printer properly. In extreme cases, it can even mess up your hot end. If you think that the thread has absorbed moisture, it is recommended to measure its diameter.
-
3) Poor quality 3D printing: when water is absorbed into the filament and heated by the 3D printer for extrusion, the water combines with heat to form steam (you will hear a hissing sound when steam is generated).
This results in bubbles as the filament exits the hot end and an uneven print surface.
- 4) Weak thread and breakage: The more water gets on the thread, the higher the risk of thread breakage. While water weakens the filament, the real problem comes when you heat up the wet filament while running it through the hot end of the 3D printer. Studies show that printing with wet material reduces its durability by 33%!
Of course, the degree to which the filament is exposed to moisture depends on the type of filament you are using. PET and ABS are not as sensitive to moisture absorption as nylon or PLA. However, it does not hurt to store all threads in a water-free environment.
There are conflicting opinions about the ideal moisture level for your filament, but 10-15% moisture should be safe. Of course, you don't have to spend tons of money on fancy dehumidifiers and filament protection systems. Many manufacturers have taken to creating their own filament storage kits, such as Stephen Hall and his airtight filament container. Here are some simple and inexpensive tips that we recommend:
- 1) Use desiccants to absorb moisture: The most effective and documented desiccant to keep the filament dry is silica gel. These are small, absorbent gel sachets found in shoe boxes and vitamin bottles. You can buy quartz beads that change color to indicate that the beads have passed a certain amount of water. When the beads change color, you can put them in the oven for 3 hours at 120°C and they will return to their original color and you can use them again. To store the gel, place it in any container with air holes or slots. You can 3D print one or more tinkers by using empty plastic containers and drilling small holes in them.
Rice is also a mild dehydrator and can absorb small amounts of water. If anyone has ever dropped their phone in water, you may have heard of the trick of putting it in a container of rice. It really helps! However, for this purpose, it is not as effective as silica gel in absorbing moisture from the air. If you live in a humid climate, we recommend using silica.
-
2) Use Vacuum Bags: These bags differ from Ziploc bags in that they have a hole through which you can insert a vacuum cleaner tip to suck out all the air. No air = no moisture or other elements that will ruin the quality of your prints! To use the thread, you need to take it out of the bag and close it again. Make it even more effective by adding a few packs of silica gel to your bag!
-
3) Sealed pails or containers: These are an alternative to vacuum bags that can range from pet food containers to large pails available at any hardware store. There are lids with built-in dehydrators, called gamma lids, that you can also get at the hardware store. According to a conversation on the RepRap forum, 5 gallon buckets can hold 4 1kg spools of filament.
-
4) Do not store the thread for more than 12 months: Naturally, the quality of the thread deteriorates over time, no matter what measures you take to protect it from moisture.
It's best not to store too much floss unless you intend to use it within the next year.
-
5) Store in a dry cabinet: There are dry cabinets and dehumidifiers on the market that work, but we recommend drying the simpler solution first. If you have a ton of filaments that you use all the time and want to keep them all in one place, these filaments might be a good option for you.
With all the new thread types on the market, it's hard to know how to care for each one differently. When in doubt, we recommend storing it in a cool, dry place.
via Pinshape
This page has been translated using machine translation. Suggest the best translation
How to choose the right 3D filament. Company statistics «3Dplast
In plastics, like vikoristovuyutsya in 3D-druk, there is one hot and the most head foe - tsevologіst. Nothing else negatively affects the material itself and the results of your printing.
You will easily know in a number of obscure histories about those that the filament was zipped when taken out of sight. Abo apply not far away sprouts, overruled from such threads.
It is important to note that the working threads are more susceptible to moisture, lower. For example, PLA plastic, PVA trim material, nylon and ABS are especially sensitive to moisture.
Take care of plastic
To figure out how to save plastic, let's talk about why you are responsible for saving your fibers.
1. Thread degradation . Plastics are sensitive to moisture in the air, because the stench is crushed from materials, it is easy to take in water, or it can cause a high level of hygroscopicity, so you speak correctly.
For example, PLA plastic is biodegradable and vibrates from natural resources such as corn or rice. Although it’s better for the most common medium, lower plastics, it also means that, with the singing of the wines, it will decompose into carbon dioxide, water and methane. Vologists mind and ultraviolet improvement speed up the destruction of this material. Of course, you won’t grow up, but if you come to inapplicability, you will surely commemorate yourself for your deaths.
2. Low-emission 3D If the water is spun with a thread, and then the material is heated by a 3D printer for extrusion, the water creates a steam in the heat (before speech, when the steam is folded, you will feel a hissing sound). Naturally, it is necessary to cause the threads to bubbling all over the world, like it comes out of the nozzle and fills the porous and uneven surface.
3. Thread loosening and opening . The more vologists sip in a thread, the greater the ability to grow. The real problem lies in the fact that you heat the thread, passing it through the nozzle of a 3D printer. The results show that the other wet material reduces the moisture content by 33%!
Naturally, I would like to lay down the water in a thread. For example, PET and ABS are less hygroscopic, lower nylon or PLA. But all the same, all your materials need to be stored in a dry environment.
How to save 3D plastic
Now, let's move on to how to save your materials for 3D-friend so that vologists don't get stench.
Make superfluous ideas about the ideal level of moisture for materials, but you should be guilty of at least 10 and 15% moisture. Moreover, it is unlikely that you will be able to showcase your great sums on super-gadgets for saving. It’s better to just follow the deakim, let’s forgive the lads and conquer the koshti, while testing the bagatma in practice.
The most effective and well-proven desiccant for picking up the filament is silica gel.
These are small packets of moisture-wicking gel, as if they were in their big boxes. Once in a while, you can add such gel bags, so that you can change your color, if you get too much water too early and stop effectively lowering the water content again. And then you finish drying them in the oven for the instructions of the cooker and the stench is ready again for operation.
The gel is placed in containers where you can store your 3D plastic. Tse can be like a package on the post, so a box.
The stench is aired in special packages on the Ziploc fasteners, which have an opening in them, which can be used to pick up a pilosos and vismoctate everything. There is no repetition = there are no vologists or other elements that will improve the quality of your virobivs! In order to vindicate your material, you need to vindict it, and at the end, it will re-seal it. As in one package, a sprat of bobbins is saved, and the other will go for a long time, you know that it is necessary to work - vismoktati all the same from the package. By the way, make the package even more effective by adding silica gel packs to the new sprat! You can bring such bags in any everyday supermarket or in stores for more expensive ones, so you can pack your speech on the road in them.
3. Sealed boxes or containers . It's an alternative to vacuum bags, and it can be just as good, from your pet food containers to big buckets, as you might know in any government store. Specially for them, there are covers with the possibility of drying or winding up.
Remember that the quality of the thread is sagging over time, depending on how you come in and receive it, so as to prevent the consumption of water. Better not save too much material for 3D-friends, because you don't plan to beat them for a long time.
So on the market there are special furniture or special outbuildings, which effectively work effectively, but we recommend that you make a more simple solution - the best way to close the wardrobe.
If you have a lot of 3D plastics at once, if you win all the time and if you want to save them in one place, then this wardrobe can be a good option.
0087 . This is at the same time much simpler and more effective solution. There are a lot of such clips on the market, or you can indulge them yourself. On the right, in that, the edge of the thread is ringing to finish the host. And so you save 3D plastic from vacuum bags, the whole edge can easily break through the bag, calling all your efforts to save and fight against water. The clip itself is lying against you in an unacceptable situation.
. Try to change the thread diameter and adjust it with the factory settings. If the wine is larger, then the type of purchase in any case may be varto vіdmovitysya. Abo the maker is disrespectful to put before the brewing of their products. Abo thread scored vologda.
All other signs of a watery thread wilt only at others. We often described in the blog “Now take care of 3D plastic”, but here we add specific visual signs of water material. With each other, the following may appear:
- cracking sounds;
- bad ball joint;
- uneven balls;
- uncharacteristic strings, mikhuri or natikannya;
- fuzzy, porous surface;
- tear filament;
- steam from nozzles;
- The extreme temperature is not enough for the robot.
How to introduce a thread to a vologer
Here we have something to please you. Thread, yak glinted to the Vologda - not a virok. Well, it didn’t lie like that for a month or two, and it didn’t lead to structural deformations of the material.