3D printing cincinnati
3D Printing Service for Cincinnati, Ohio
CapabilitiesCustom Online 3D Printing ServiceOhioCincinnati
High Quality Cincinnati, Ohio 3D Printing | 60+ Materials Available
Endless Options
Choose from millions of possible combinations of materials, finishes, tolerances, markings, and certifications for your order.
Easy to Use
Get your parts delivered right to your door without the hassle of sourcing, project management, logistics, or shipping.
Quality Assurance
Our number one job at Xometry is making your custom parts to your specifications.
Your Cincinnati, Ohio 3D Printing Service: 3D Prototypes and Production Parts
A Global Leader in Industrial-Grade 3D Printing
Xometry is an industry-leading 3D printing service. Whether you need prototypes or production parts, we can make them for you in as fast as a day. We are your one-stop-shop for accurate, precise custom 3D printed parts at a low cost. Upload your 3D CAD file to get a quote and lead time within seconds. We use the latest additive manufacturing processes to build affordable functional prototypes & end-use parts in over 60 metals and plastics.
We offer eight high-quality 3D printing processes including selective laser sintering, fused deposition modeling, stereolithography, direct metal laser sintering, polyjet, Carbon DLS, binder jet metal, and HP Multi Jet Fusion. We use commercial and industrial-grade printers such as Stratasys Fortus 900mc and Fortus 450 FDM, EOS Polymer Laser Sintering (SLS) and DMLS, Concept Laser, SLM Solutions, 3D Systems, ExOne, and more.
Xometry's High Quality 3D Printing Services
Selective Laser Sintering (SLS)
Selective Laser Sintering (SLS) is a powerful 3D printing technology that produces highly accurate and durable parts that are capable of being used directly in end-use, low-volume production, or for rapid prototyping.
An additive manufacturing layer technology, SLS involves the use of a high power laser (for example, a carbon dioxide laser) to fuse small particles of plastic powders into a mass that has a desired three-dimensional shape. The laser selectively fuses powdered material by scanning cross-sections generated from a 3-D digital description of the part (for example from a CAD file or scan data) on the surface of a powder bed. After each cross-section is scanned, the powder bed is lowered by one layer thickness, a new layer of material is applied on top, and the process is repeated until the part is completed.
Download the SLS Design Guide.
Stereolithography (SLA)
Stereolithography (SLA) is a robust 3D printing technology that produces extremely accurate and high-resolution parts that are capable of being used directly in end-use, low-volume production, or for rapid prototyping.
SLA is an additive manufacturing process that focuses an ultraviolet (UV) light on a vat of photopolymer resin. It offers higher resolution printing than many other 3D printing technologies, allowing customers to print parts with fine details and surface finishes. SLA 3D printing is a highly-versatile platform for making custom parts in prototype and production settings; often acting as a stand-in for injection-molded plastic parts.
Xometry offers both standard and high-resolution options for fine detail parts, and can also print larger sized parts and products, with some materials offering up to a 58" inch build area. In addition, Xometry's manufacturing partner network allows us to offer a larger variety of materials than other 3D printing companies - we offer a wide range of both Accura and Somos brand materials.
Download the SLA Design Guide.
Fused Deposition Modeling (FDM)
Fused Deposition Modeling (FDM) is a 3D printing technology widely known for its speed, accuracy, and competitive cost. A machine precisely extrudes melted plastic filament to create a part. Parts are very rigid, especially compared to Selective Laser Sintering (SLS), which makes them a great fit for projects with a rigidity requirement. Xometry's FDM solution offers large build volumes up to 24″ x 36″ x 36″, a variety of colors, and a diverse selection of production-grade thermoplastics — from ABS to Polycarbonate to Ultem.
Download the FDM Design Guide.
HP Multi Jet Fusion (HP MJF)
HP Multi Jet Fusion is a new 3D printing technology that produces highly accurate and durable parts that are capable of being used directly in end-use, low-volume production, or for rapid prototyping. Since the process uses well-established 2D printing ink-jetting, it has remarkably fast layer times compared to other powder bed fusion technologies.
Download the HP Multi Jet Fusion Design Guide.
PolyJet 3D (PJ3D)
PolyJet 3D is a 3D printing technology known for its customizable material properties and excellent surface finish. It works by jetting UV curable resin onto a build tray in a process that is somewhat similar to inkjet printing. PolyJet 3D printing offers one of the most advanced industrial 3D printing solutions available, producing parts with incredible precision and speed. It also supports a wide variety of build materials including rigid and rubber-like plastics. Xometry's PolyJet solution has a maximum build envelope of 19. 3 × 15.4 × 7.9 in. (490 × 390 × 200 mm) in a variety of colors and materials.
Download the PolyJet 3D Design Guide.
Direct Metal Laser Sintering (DMLS)
Direct Metal Laser Sintering (DMLS) is an 3D metal printing technology that builds prototype and production metal parts from a CAD file using a laser to selectively fuse a fine metal powder in either stainless steel or aluminum materials. A DMLS machine is capable of producing highly complex features and all-in-one assemblies using metal materials that would be difficult to achieve with subtractive manufacturing techniques.
Our DMLS metal 3D printing service typically offers build volumes up to 250 x 250 x 325 mm, but we may be able to accommodate larger part volumes upon request in the quote. (See our Manufacturing Standards for more details) A good first step is to find out the cost of the parts you need using DMLS and compare them to other 3D printing processes and CNC machining.
Download the DMLS Design Guide.
Carbon DLS™
Carbon DLS™ uses digital light projection, oxygen-permeable optics, and programmable liquid resins to produce products with end-use durability, resolution and surface finish. This 3D printing technology is called Digital Light Synthesis™, or DLS for short. Another legacy term for the process is Continuous Liquid Interface Production (CLIP). Along with Carbon’s custom liquid resins, DLS unlocks new business opportunities and product designs previously impossible, including mass customization and on-demand inventory of end-use products.
Carbon bridges, and sometimes substitutes, for processes like Urethane Casting and Injection Molding service production, because the materials are urethane-based or epoxy-based, giving excellent mechanical properties. There are even elastomer and silicone resins that outperform most additive manufactured rubber-like materials.
The typical build area is 7.4” x 4.6” x 12.8”. Parts with dimensions exceeding 4” x 4” x 6” will require manual review.
Download the Carbon DLS Design Guide.
Metal Binder Jetting
With binder jetting, an inkjet print head quickly deposits a bonding agent onto a thin layer of powdered particles -- either metal, sand, ceramics or composites. This process is repeated, layer-by-layer, using a map from a digital design file, until the object is complete. Binder jetting is offered through our Digital RFQ Marketplace through Xometry's partnership with ExOne.
Download the Binder Jetting Design Guide.
Locations near Cincinnati, Ohio
Dayton
OhioLexington
KentuckyLouisville
KentuckyIndianapolis
IndianaColumbus
OhioBloomington
IndianaFort Wayne
IndianaWest Lafayette
IndianaTerre Haute
IndianaOwensboro
KentuckyBowling Green
KentuckyToledo
OhioEvansville
IndianaElkhart
IndianaSouth Bend
IndianaCanton
OhioAkron
OhioCleveland
OhioKnoxville
TennesseeAnn Arbor
Michigan
Ready to start making custom 3D printed parts?
3D Printing Service Cincinnati, OH | Instant Quotes Online
Our 3D printing capabilities
We have over 90 3D printing shops in our network and are well known for manufacturing high-quality parts at competitive prices, from rapid prototyping with Fused Deposition Modeling (FDM) to functional end parts made with Selective Laser Sintering (SLS) or Multi Jet Fusion (MJF).
Gallery of 3D printed parts manufactured by Hubs
With over 65,000 customers from every industry, including aerospace, defense, robotics, medical, machinery, automotive and electronics, we have extensive experience meeting a diverse range of 3D printing requirements, from prototyping to production: Visual aids, concept models, injection-molding prototypes, form-fit & function prototypes, tooling and casting patterns, jigs, grips and fixtures, and durable end parts.
HP PA 12 - Dyed Black
Customer | True North Design |
Purpose | Structural and vacuum EOAT components |
Process | SLS / MJF |
Unit price | $69.23 / $34.33 |
Industry | Automotive |
Prototyping PLA
Customer | Allision Conner |
Purpose | End caps and cable strain relief for sheet metal enclosure |
Process | FDM |
Unit price | $7.![]() |
Industry | Industrial Automation |
HP PA 12
Customer | US Hammer |
Description | A part for gasoline engine powered jackhammers |
Process | MJF |
Unit price | $22.18 |
Industry | Construction |
Markforged Onyx - Black
Customer | Autocom Manufacturing |
Purpose | A production part for 3D printed lathe gantry gripper fingers |
Process | FDM |
Unit price | $48.86 |
Industry | Automotive |
PC Stratasys - white
Customer | Terumo medical corporation |
Purpose | Prototyping parts used for a disposable electrical device |
Process | FDM |
Unit price | $55.![]() |
Industry | Medical |
Formlabs Clear Resin
Customer | Aversan Inc |
Purpose | A prototyping part of an injection molded component for an automated door mechanism |
Process | SLA |
Unit price | $29.83 |
Industry | Aerospace |
HP PA 12 - Dyed Black
Customer | True North Design |
Purpose | Structural and vacuum EOAT components |
Process | SLS / MJF |
Unit price | $69.23 / $34.33 |
Industry | Automotive |
Prototyping PLA
Customer | Allision Conner |
Purpose | End caps and cable strain relief for sheet metal enclosure |
Process | FDM |
Unit price | $7.![]() |
Industry | Industrial Automation |
HP PA 12
Customer | US Hammer |
Description | A part for gasoline engine powered jackhammers |
Process | MJF |
Unit price | $22.18 |
Industry | Construction |
Markforged Onyx - Black
Customer | Autocom Manufacturing |
Purpose | A production part for 3D printed lathe gantry gripper fingers |
Process | FDM |
Unit price | $48.86 |
Industry | Automotive |
PC Stratasys - white
Customer | Terumo medical corporation |
Purpose | Prototyping parts used for a disposable electrical device |
Process | FDM |
Unit price | $55.![]() |
Industry | Medical |
Formlabs Clear Resin
Customer | Aversan Inc |
Purpose | A prototyping part of an injection molded component for an automated door mechanism |
Process | SLA |
Unit price | $29.83 |
Industry | Aerospace |
HP PA 12 - Dyed Black
Customer | True North Design |
Purpose | Structural and vacuum EOAT components |
Process | SLS / MJF |
Unit price | $69.23 / $34.33 |
Industry | Automotive |
Prototyping PLA
Customer | Allision Conner |
Purpose | End caps and cable strain relief for sheet metal enclosure |
Process | FDM |
Unit price | $7.![]() |
Industry | Industrial Automation |
HP PA 12
Customer | US Hammer |
Description | A part for gasoline engine powered jackhammers |
Process | MJF |
Unit price | $22.18 |
Industry | Construction |
Markforged Onyx - Black
Customer | Autocom Manufacturing |
Purpose | A production part for 3D printed lathe gantry gripper fingers |
Process | FDM |
Unit price | $48.86 |
Industry | Automotive |
PC Stratasys - white
Customer | Terumo medical corporation |
Purpose | Prototyping parts used for a disposable electrical device |
Process | FDM |
Unit price | $55.![]() |
Industry | Medical |
Formlabs Clear Resin
Customer | Aversan Inc |
Purpose | A prototyping part of an injection molded component for an automated door mechanism |
Process | SLA |
Unit price | $29.83 |
Industry | Aerospace |
HP PA 12 - Dyed Black
Customer | True North Design |
Purpose | Structural and vacuum EOAT components |
Process | SLS / MJF |
Unit price | $69.23 / $34.33 |
Industry | Automotive |
Prototyping PLA
Customer | Allision Conner |
Purpose | End caps and cable strain relief for sheet metal enclosure |
Process | FDM |
Unit price | $7.![]() |
Industry | Industrial Automation |
HP PA 12
Customer | US Hammer |
Description | A part for gasoline engine powered jackhammers |
Process | MJF |
Unit price | $22.18 |
Industry | Construction |
Markforged Onyx - Black
Customer | Autocom Manufacturing |
Purpose | A production part for 3D printed lathe gantry gripper fingers |
Process | FDM |
Unit price | $48.86 |
Industry | Automotive |
PC Stratasys - white
Customer | Terumo medical corporation |
Purpose | Prototyping parts used for a disposable electrical device |
Process | FDM |
Unit price | $55.![]() |
Industry | Medical |
Formlabs Clear Resin
Customer | Aversan Inc |
Purpose | A prototyping part of an injection molded component for an automated door mechanism |
Process | SLA |
Unit price | $29.83 |
Industry | Aerospace |
HP PA 12 - Dyed Black
Customer | True North Design |
Purpose | Structural and vacuum EOAT components |
Process | SLS / MJF |
Unit price | $69.23 / $34.33 |
Industry | Automotive |
Prototyping PLA
Customer | Allision Conner |
Purpose | End caps and cable strain relief for sheet metal enclosure |
Process | FDM |
Unit price | $7.![]() |
Industry | Industrial Automation |
HP PA 12
Customer | US Hammer |
Description | A part for gasoline engine powered jackhammers |
Process | MJF |
Unit price | $22.18 |
Industry | Construction |
Markforged Onyx - Black
Customer | Autocom Manufacturing |
Purpose | A production part for 3D printed lathe gantry gripper fingers |
Process | FDM |
Unit price | $48.86 |
Industry | Automotive |
PC Stratasys - white
Customer | Terumo medical corporation |
Purpose | Prototyping parts used for a disposable electrical device |
Process | FDM |
Unit price | $55.![]() |
Industry | Medical |
Formlabs Clear Resin
Customer | Aversan Inc |
Purpose | A prototyping part of an injection molded component for an automated door mechanism |
Process | SLA |
Unit price | $29.83 |
Industry | Aerospace |
HP PA 12 - Dyed Black
Customer | True North Design |
Purpose | Structural and vacuum EOAT components |
Process | SLS / MJF |
Unit price | $69.23 / $34.33 |
Industry | Automotive |
Prototyping PLA
Customer | Allision Conner |
Purpose | End caps and cable strain relief for sheet metal enclosure |
Process | FDM |
Unit price | $7.![]() |
Industry | Industrial Automation |
HP PA 12
Customer | US Hammer |
Description | A part for gasoline engine powered jackhammers |
Process | MJF |
Unit price | $22.18 |
Industry | Construction |
Markforged Onyx - Black
Customer | Autocom Manufacturing |
Purpose | A production part for 3D printed lathe gantry gripper fingers |
Process | FDM |
Unit price | $48.86 |
Industry | Automotive |
PC Stratasys - white
Customer | Terumo medical corporation |
Purpose | Prototyping parts used for a disposable electrical device |
Process | FDM |
Unit price | $55.![]() |
Industry | Medical |
Formlabs Clear Resin
Customer | Aversan Inc |
Purpose | A prototyping part of an injection molded component for an automated door mechanism |
Process | SLA |
Unit price | $29.83 |
Industry | Aerospace |
HP PA 12 - Dyed Black
Customer | True North Design |
Purpose | Structural and vacuum EOAT components |
Process | SLS / MJF |
Unit price | $69.23 / $34.33 |
Industry | Automotive |
Prototyping PLA
Customer | Allision Conner |
Purpose | End caps and cable strain relief for sheet metal enclosure |
Process | FDM |
Unit price | $7.![]() |
Industry | Industrial Automation |
HP PA 12
Customer | US Hammer |
Description | A part for gasoline engine powered jackhammers |
Process | MJF |
Unit price | $22.18 |
Industry | Construction |
Markforged Onyx - Black
Customer | Autocom Manufacturing |
Purpose | A production part for 3D printed lathe gantry gripper fingers |
Process | FDM |
Unit price | $48.86 |
Industry | Automotive |
PC Stratasys - white
Customer | Terumo medical corporation |
Purpose | Prototyping parts used for a disposable electrical device |
Process | FDM |
Unit price | $55.![]() |
Industry | Medical |
Formlabs Clear Resin
Customer | Aversan Inc |
Purpose | A prototyping part of an injection molded component for an automated door mechanism |
Process | SLA |
Unit price | $29.83 |
Industry | Aerospace |
HP PA 12 - Dyed Black
Customer | True North Design |
Purpose | Structural and vacuum EOAT components |
Process | SLS / MJF |
Unit price | $69.23 / $34.33 |
Industry | Automotive |
Prototyping PLA
Customer | Allision Conner |
Purpose | End caps and cable strain relief for sheet metal enclosure |
Process | FDM |
Unit price | $7.![]() |
Industry | Industrial Automation |
HP PA 12
Customer | US Hammer |
Description | A part for gasoline engine powered jackhammers |
Process | MJF |
Unit price | $22.18 |
Industry | Construction |
Markforged Onyx - Black
Customer | Autocom Manufacturing |
Purpose | A production part for 3D printed lathe gantry gripper fingers |
Process | FDM |
Unit price | $48.86 |
Industry | Automotive |
PC Stratasys - white
Customer | Terumo medical corporation |
Purpose | Prototyping parts used for a disposable electrical device |
Process | FDM |
Unit price | $55.![]() |
Industry | Medical |
Formlabs Clear Resin
Customer | Aversan Inc |
Purpose | A prototyping part of an injection molded component for an automated door mechanism |
Process | SLA |
Unit price | $29.83 |
Industry | Aerospace |
HP PA 12 - Dyed Black
Customer | True North Design |
Purpose | Structural and vacuum EOAT components |
Process | SLS / MJF |
Unit price | $69.23 / $34.33 |
Industry | Automotive |
Prototyping PLA
Customer | Allision Conner |
Purpose | End caps and cable strain relief for sheet metal enclosure |
Process | FDM |
Unit price | $7.![]() |
Industry | Industrial Automation |
HP PA 12
Customer | US Hammer |
Description | A part for gasoline engine powered jackhammers |
Process | MJF |
Unit price | $22.18 |
Industry | Construction |
Markforged Onyx - Black
Customer | Autocom Manufacturing |
Purpose | A production part for 3D printed lathe gantry gripper fingers |
Process | FDM |
Unit price | $48.86 |
Industry | Automotive |
PC Stratasys - white
Customer | Terumo medical corporation |
Purpose | Prototyping parts used for a disposable electrical device |
Process | FDM |
Unit price | $55.![]() |
Industry | Medical |
Formlabs Clear Resin
Customer | Aversan Inc |
Purpose | A prototyping part of an injection molded component for an automated door mechanism |
Process | SLA |
Unit price | $29.83 |
Industry | Aerospace |
HP PA 12 - Dyed Black
Customer | True North Design |
Purpose | Structural and vacuum EOAT components |
Process | SLS / MJF |
Unit price | $69.23 / $34.33 |
Industry | Automotive |
Prototyping PLA
Customer | Allision Conner |
Purpose | End caps and cable strain relief for sheet metal enclosure |
Process | FDM |
Unit price | $7.![]() |
Industry | Industrial Automation |
HP PA 12
Customer | US Hammer |
Description | A part for gasoline engine powered jackhammers |
Process | MJF |
Unit price | $22.18 |
Industry | Construction |
Markforged Onyx - Black
Customer | Autocom Manufacturing |
Purpose | A production part for 3D printed lathe gantry gripper fingers |
Process | FDM |
Unit price | $48.86 |
Industry | Automotive |
PC Stratasys - white
Customer | Terumo medical corporation |
Purpose | Prototyping parts used for a disposable electrical device |
Process | FDM |
Unit price | $55.![]() |
Industry | Medical |
Formlabs Clear Resin
Customer | Aversan Inc |
Purpose | A prototyping part of an injection molded component for an automated door mechanism |
Process | SLA |
Unit price | $29.83 |
Industry | Aerospace |
Instant, online 3D printing quotes
-
Upload a CAD to start (STEP, STP, IGES, IGS, SLDPRT, 3DM, SAT, STL, OBJ or X_T)
-
Price updates in real-time as you change materials, lead time, etc..
-
No hidden costs. Our instant quotes are not just indications, but the actual price, and include shipping and customs up front.
Learn about how our quoting algorithm works
Our ordering process
Receive instant quote
Upload your CAD to our online quoting platform
Confirm specs
Configure your part specifications and select a lead time that suits your schedule
Production
We select the best manufacturer for your order, and production begins immediately
Quality control
We take full responsibility for making sure your parts are manufactured according to our standards
Delivery
Our 3D printing service has been rated 4.9/5
Over 205 customers are satisfied with our 3D printing service.
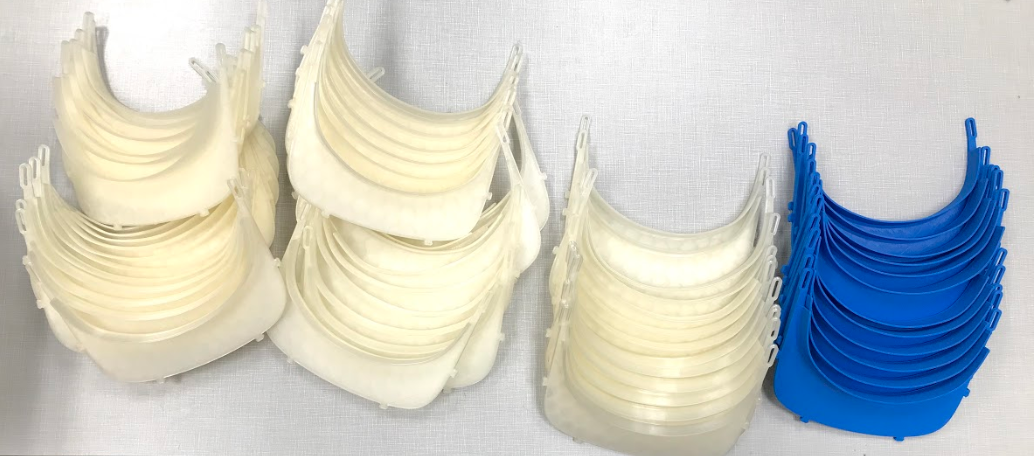
“Very quick turnaround, notified me of a part that would be problematic to print and had me update the sketch before printing”
“Good quality print, tiny bit of stringing on one side but causes zero issues. ”
“I'm very happy with the results. Will use this service again! ”
“I hate repeating myself but I have to say that EVERY print I get is top notch!”
“Shipping method and timeline worked out fine”
“OUTSTANDING!!! My new "go to" source for 3D printing. Thank you so much, and I look forward to working with you in the future. ”
“Got here faster than expected and split my two orders so I didn't have to pay extra shipping. Print quality was excellent as usual.”
“Another fine job. Perfectly printed and delivered quickly. Thank you. ”
“Great quality prints and quick to respond for any questions throughout the process.”
“First time user. Great experience. Will return!”
“Very good prints with fast turn-around time. Highly recommended!”
“Everything about this experience was great! The quality of the print was perfect and the time was right on the money. ”
“Excellent service! Ordered on May 31 and delivered via mail just a couple days later. Party looks good and material looks sturdy. This was my first time ordering a print and if given the opportunity I would use this printer again”
“great service, and communication! thank you”
“Excellent experience. Even printed an extra piece for me beyond the ones requested.”
“OMG the print is uber amazing. looks perfect. thanks again for everything”
“Print arrived in fantastic shape. Thank you!”
“Great print, parts fit together very well and look nice. Thanks!”
“Great communication to make sure my order was placed with the correct specs.”
“Everything came back perfect! Great experience!”
“Had a fairly large print - turned out great!”
“Part was of good quality and received it in a timely manner. ”
“Prompt and friendly communication. Prints arrived as expected and ahead of schedule”
“Very good communication, extremely fast turnaround.”
“I was very happy with the parts, These were Prototypes and we found a dimension problem with our print because the parts were exactly what we ordered. This was a perfect prototype run, Proof of concept verified and part file was tested out.”
Show more reviews
Show less reviews
Teams build better parts
Create your Hubs team and start collaborating
Read more
The Hubs Standard - consistent quality, every time
Hubs takes the stress out of manufacturing by guaranteeing the quality and consistency of every part. Each order is dimensionally and visually inspected to make sure it meets the Hubs Standard.
3D printing materials
We can generate instant 3D printing quotes for 25+ plastics. For metal 3D-printed parts, you can request a quote from our parent company, Protolabs.
Available materials
SLS
PA 12 Glass filled PA 12
Desktop FDM
Prototyping PETG Prototyping ASA Prototyping TPU Prototyping ABS Prototyping PLA
Desktop SLA
Formlabs Standard Resin Formlabs Clear Resin Formlabs Tough Resin 2000 Formlabs Rigid Resin 4000 Formlabs Grey Pro Resin Formlabs Flexible Resin 80A Formlabs High Temp Resin Formlabs Durable Resin
MJF
HP PA 12 Glass filled HP PA 12
Industrial FDM
Markforged Onyx ABSplus Stratasys ULTEM 9085 Stratasys Stratasys ASA ABS M30 Stratasys ULTEM 1010 Stratasys
Industrial SLA
Accura 25 (PP-like) Accura ClearVue Accura Xtreme White 200 (ABS-like)
3D printing locations near Cincinnati, OH
Cincinnati, OH Hamilton, OH Middletown, OH
Columbus, IN Louisville, KY Kettering, OH
Lexington, KY Dayton, OH Greenwood, IN
Muncie, IN
The 3D Printing Handbook
No one understands 3D printing like us - our founders literally wrote the book. Click here to download the sample chapters.
Buy the book from Amazon
FAQ's
How much does your 3D printing service cost?
The cost of your 3D printed parts depends on factors such as part volume, part complexity, choice of material, which 3D printing technology is used, and if any post processing is required. For more details on these cost factors, see our article on the cost of 3d printing. To check the cost of your 3D printed part, simply upload a CAD (.STL) file and select your material and 3D printing technology to receive a quote within seconds.
How do you guarantee the quality of my prints?
Your parts are made by experienced 3D printing shops within our network. All facilities are regularly audited to ensure they consistently meet the Hubs quality standard. We include a standardized inspection report with every order and offer a First Article Inspection service on orders of 100+ units.
We have partners in our network with the following certifications, available on request: ISO9001, ISO13485 and AS9100.
Follow this link to read more about our quality assurance measures.
How do I select the right 3D printing process for my prints?
You can select the right 3D printing process by examining which materials suit your need and what your use case is.
By material: if you already know which material you would like to use, selecting a 3D printing process is relatively easy, as many materials are technology specific.
By use case: once you know whether you need a functional or visual part, choosing a process is easy.
For more help, read our guide to selecting the right 3D printing process. Find out more about Fused Deposition Modeling (FDM), Selective Laser Sintering (SLS), Multi Jet Fusion (MJF) and Stereolithography (SLA).
How can I reduce the cost of my 3D prints?
In order to reduce the cost of your 3D prints you need to understand the impact certain factors have on cost. The main cost influencing factors are the material type, individual part volume, printing technology and post-processing requirements.
Once these have been decided, an easy way to further cut costs is to reduce the amount of material used. This can be done by decreasing the size of your model, hollowing it out, and eliminating the need for support structures.
To learn more, read our full guide on how to reduce the cost of 3D printing.
Where can I learn more about 3D printing?
Our knowledge base is full of in-depth design guidelines, explanations on process and surface finishes, and information on how to create and use CAD files. Our 3D printing content has been written by an expert team of engineers and technicians over the years.
See our complete engineering guide to 3D printing for a full breakdown of the different 3D printing technologies and materials. If you want even more 3D printing, then check out our acclaimed 3D printing handbook here.
We have an extensive range of online resources developed to help engineers improve their capabilities.
Introductory guides
Design guides
Material guides
Applications
CAD & file preparation
Post processing & finishing
Our other manufacturing capabilities
CNC machining
CNC machining
Milling (3-, 4- & full 5-axis), turning and post-processing
-
50+ metals and plastics & 10 surface finishes
-
Tolerances down to ±.0008” (0.020 mm)
-
Lead times from 5 business days
See our CNC machining services
Put your 3D printed parts into production today
Get an instant 3D printing quote
Cincinnati Incorporated offers NV Pro 3D Printer under its own brand
News
Cincinnati Incorporated is known in maker circles for the huge BAAM 3D printers used in Local Motors' printed cars, but now the company is adding a small rapid prototyping machine to its range.
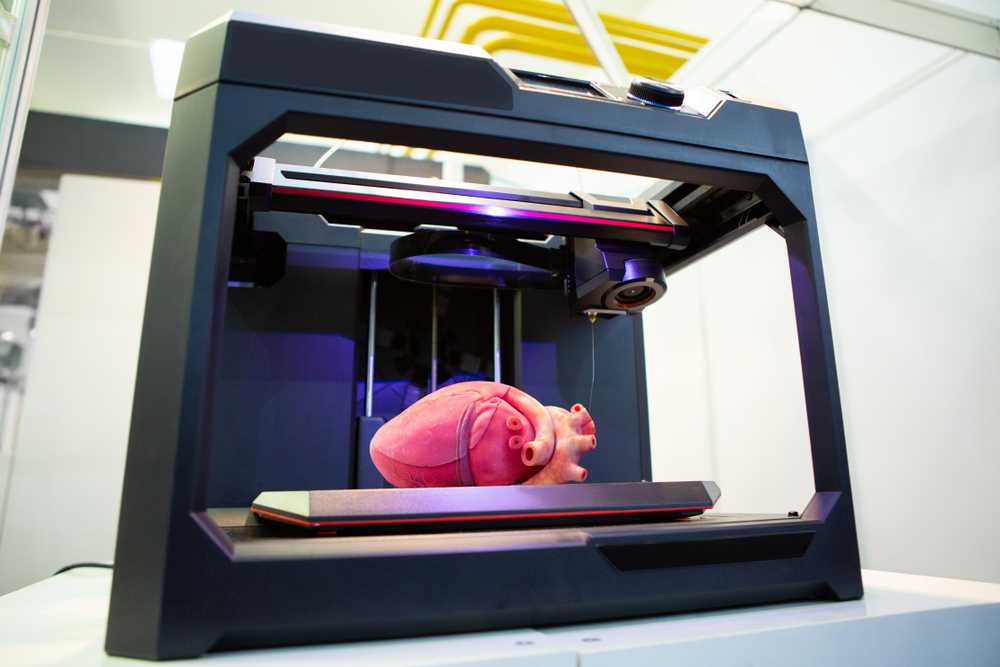
BAAM is similar in principle to desktop FDM printers, although there are some differences. Firstly, these are huge dimensions that allow printing products up to 6x2.3x1.9 m in size. Secondly, the screw feed of granular plastic to the hot end. The installation is designed for high speed, so quality has to be sacrificed, but finished parts can always be processed. BAAM has proven itself in action, but one problem remains: what if an unnoticed mistake crept into the design? Is there a printer who has never cringed at the sight of a failed model? Now imagine a defective boot or a six-meter-long whistle.
The solution suggests itself: first we print a small prototype, and if it passes the inspection and feel test, we print a full-scale part. To make things easier, Cincinnati Incorporated decided to rush in the opposite direction and replenish the line with the SAAM 3D printer - the little brother of BAAM. "SAAM" stands for "Small Area Additive Manufacturing" or "Small Format Additive Manufacturing".
“Additive manufacturing has opened up new possibilities for designers and engineers. SAAM will help all these creatives explore the limits of design thought through rapid prototyping and test their designs before going into full scale production with BAAM's much larger 3D printers. Simply put, SAAM is designed for relatively cheap previews,” explains Cary Chen, president and CEO of Cincinnati Incorporated.
Interestingly, the company has nothing to do with the development of SAAM. The design belongs to startup New Valence Robotics (NVBOTS), which first demonstrated the NV Pro (aka "SAAM") system last year. At its core, this is an ordinary FDM printer, but with one unusual ability: the function of automatically separating finished models from the desktop after printing is completed. The printed parts are dumped into a special compartment, after which the production cycle is restarted, eliminating the need for operators to monitor the operation of the machine. The full potential of such a mini-factory can be unlocked with NVCloud cloud software, allowing multiple users to work remotely on a single machine.
According to the NVBOTS website, about fifty NV Pro 3D printers have been sold to date, but adapting the device under the Cincinnati Incorporated brand should help with marketing and make life easier for companies that have adopted BAAM. As for NVBOTS, the startup plans a 3D printer that prints with metal wire using MAD (Metal Additive Deposition) technology. According to the developers, the design of the metal 3D printer will be based on the NV Pro. The technology will allow working with several materials within a single cycle, including stainless steel, titanium, nickel, copper, aluminum, silver, palladium, etc. The print speed should exceed that of sintering plants (SLS) by about ten times. Details have not yet been disclosed, but the investment of $ 2 million gives solidity to the project. Additional information on the NV Pro / SAAM 3D printer is available at this link.
Retrieved Do you have any interesting news? Share your developments with us, and we will tell the whole world about them! We are waiting for your ideas at [email protected].
Follow the author
Follow
Don't want
4
More interesting articles
7
Subscribe to the author
Subscribe
Don't want
New intervertebral cages from the Russian company Pozvonoq, used to solve the problems of stabilization...
Read more
four
Subscribe to the author
Subscribe
Don't want
Specialists of the department "Foundry and High-Efficiency Technologies" of the Samara State Technical. ..
Read more
82
Subscribe to the author
Subscribe
Don't want
Collaboration 3D
We are pleased to present you our joint development with Speci... 9Ol000 Area Additive Manufacturing has produced what is possibly the largest composite 3D printed part in the world using recycled granular composite materials.
The part in the illustration above is a formwork component, apparently not yet post-processed. Such formwork is used in the production of concrete panels with window openings for New York high-rise buildings. It took only about seven hours to 3D print a 180-kilogram part over three meters long, which indicates the high productivity of BAAM 3D printers, developed with the participation of the Oak Ridge National Laboratory (ORNL).
BAAM additive systems are constantly being improved in terms of performance and compatibility with different materials. Early versions implemented 3D printing with granular polymers and composites through a screw extruder. As a rule, expendable material is carbon-filled ABS plastic. The most well-known example of the application of such equipment is the additive production of bodies at the facilities of the automotive company Local Motors.
In this experiment, a new version of BAAM was used, capable of printing with two materials at the same time due to the rocking mechanism for switching between two hoppers. The developers point out the importance of this point, since such a design is cheaper than a full-fledged two-extruder system and makes it possible to upgrade existing systems to a new level without significant alterations.
“The feed system switches from one material to another on the fly during 3D printing by shifting the hopper connections from side to side above the extruder. Also connected to the system is equipment for mixing consumables installed outside the 3D printer, which makes it possible to obtain granules with different proportions of materials and fillers, ”says Alex Ristenberg, product manager at Cincinnati Incorporated.
Formwork materials were a mixture of primary and secondary granules of carbon-filled ABS, plus syntactic foam based on the same acrylonitrile butadiene styrene. The experiment served two purposes: to demonstrate large-format 3D printing in two with programmable mechanical properties of individual sections through the use of two or more materials and the possibility of using recycled materials with the resulting production savings and increased environmental friendliness. As an example, in the case of the same formwork or molding equipment, you can save money by printing work surfaces with expensive structural materials, and filling and supporting structures with cheaper polymers.
“Research shows that by using multiple materials in the structure of a product, new mechanical properties and multifunctionality can be achieved, for example, lightweight products with customized mechanical properties, soft and hard areas within a product, structures with increased impact resistance” , explains ORNL materials scientist Vidya Kishore.
Do you have interesting news? Share your developments with us, and we will tell the whole world about them! We are waiting for your ideas at [email protected].
composite ORNL BAAM
Follow author
Follow
Don't want
7
More interesting articles
5
Subscribe to the author
Subscribe
Don't want
The Russian company REC has released a PLA Stone filament for 3D printing of decorative products. New compo...
Read more
four
Subscribe to the author
Subscribe
Don't want
Scientists at Khalifa University in Abu Dhabi have achieved interesting results in experiments to make.