3D printer mit media lab
Voxel-printing for the digital fabrication of data across scales and domains — MIT Media Lab
Overview ‹ Making Data Matter: Voxel-printing for the digital fabrication of data across scales and domains — MIT Media Lab Find People, Projects, etc.Email:
Password:
We present a multimaterial voxel-printing method enabling the physical visualization of data sets commonly associated with scientific imaging. Leveraging voxel-based control of multimaterial 3D printing, our method enables additive manufacturing of discontinuous data types such as point cloud data, curve and graph data, image-based data, and volumetric data. By converting data sets into dithered material deposition descriptions, through modifications to rasterization processes, we demonstrate that data sets frequently visualized on screen can be converted into physical, materially heterogeneous objects.
Our approach alleviates the need to post-process data sets to boundary representations, preventing alteration of data and loss of information in the produced physicalizations. Therefore, it bridges the gap between digital information representation and physical material composition. We evaluate the visual characteristics and features of our method, assess its relevance and applicability in the production of physical visualizations, and detail the conversion of data sets for multimaterial 3D printing. We conclude wi… View full description
We present a multimaterial voxel-printing method enabling the physical visualization of data sets commonly associated with scientific imaging. Leveraging voxel-based control of multimaterial 3D printing, our method enables additive manufacturing of discontinuous data types such as point cloud data, curve and graph data, image-based data, and volumetric data. By converting data sets into dithered material deposition descriptions, through modifications to rasterization processes, we demonstrate that data sets frequently visualized on screen can be converted into physical, materially heterogeneous objects.
Our approach alleviates the need to post-process data sets to boundary representations, preventing alteration of data and loss of information in the produced physicalizations. Therefore, it bridges the gap between digital information representation and physical material composition. We evaluate the visual characteristics and features of our method, assess its relevance and applicability in the production of physical visualizations, and detail the conversion of data sets for multimaterial 3D printing. We conclude with exemplary 3D printed datasets produced by our method pointing towards potential applications across scales, disciplines, and problem domains.
Research Topics
#design #manufacturing #3d printingCopyright
The Mediated Matter Group
Compilation of a variety of 3D printed physicalizations.
Credit:
The Mediated Matter Group
While physical visualizations and representations of data are as old as prehistoric cave paintings, modern approaches still predominantly rely on the 2D display of 3D data sets on planar computer screens. Scientific visualizations account for a wide range of such virtual information displays, including volumetric rendering of patient data obtained from magnetic resonance imaging (MRI) or point-based rendering of geospatial data obtained from photogrammetry methods. Such visualizations map, process, and represent data and aim to allow a user to gather insights through perception and computer-aided interaction
Although conventional screen-based media visualizations are known to be effective, it has been argued that physical manifestations of data sets can leverage active as well as spatial perception skills, enabling a more comprehensive understanding of presented information in an inherently intuitive manner. Immersive visualization through virtual and augmented reality displays aim to improve the shortcomings of 2D information displays, but currently lack the tangible interaction offered by physical information displays. Advancements in the accessibility and affordability of digital fabrication workflows—such as additive manufacturing—enable a ‘resurrection’ of data in its physical manifestation. Consequently, the representation of data sets in a physical form through digital fabrication has emerged as a research area and practice. More broadly, the manifestation of data as a physical embodiment is often collected under the term data physicalization or physical visualization.
Copyright
The Mediated Matter Group
White matter tractography data physicalization of the human brain, visualizing bundles of axons, which connect different regions of the brain. Photo: The Mediated Matter Group
Credit:
The Mediated Matter Group
Copyright
The Mediated Matter Group
Credit:
The Mediated Matter Group
Furthermore, despite the availability and progression of 3D printing technology, fundamental 3D printing workflows have remained essentially unchanged for the past 30 years. These workflows are limited by the fact that shape specification is directly linked with material specification. This limitation is also reflected in the STL file format, which was introduced three decades ago for the first stereolithographic 3D printers and is still considered the standard file format for additive manufacturing.
The STL file format represents objects through a closed regular surface, which is described by a list of triangles, defined through their vertices. During the 3D printing process each surface is considered a solid object, where space inside the triangle boundary representation is occupied by a single material. Unfortunately, these design and additive manufacturing workflows don’t think ‘beyond the shell’ of objects, despite the fact that commercially available 3D printers can print up to seven materials simultaneously. This means that, in order to 3D print any data set—especially those that are not naturally representable as surfaces—all data first must be converted into a boundary representation. Specifically for scientific data, this conversion process is problematic, as in many cases it introduces computational overhead, alteration of data, and even loss of information.
Copyright
The Mediated Matter Group
Credit:
The Mediated Matter Group
In our paper, and in contrast to the methods described above, we present an approach to physical data visualizationthrough voxel printing using multimaterial 3D printing to improve the current data physicalization workflows.
Multimaterial 3D printing with photopolymeric materials enables the simultaneous use of several different materials, and by utilizing dedicated cyan, magenta, yellow, black, white, and transparent resins, full-color models with variable transparency can be created. The ability to create objects with and inside transparent material enables the physical visualization of compact n-manifolds such as unconnected point cloud data, lines and curves, open surfaces, and volumetric data.
Multimaterial 3D printers operate by depositing droplets of several UV-curable resins in a layer-by-layer inkjet-like printing process to construct high-resolution 3D objects. High levels of spatial control in manufacturing can be achieved by generating a set of layers in a raster file format at the native resolution of the printer, where each pixel defines the material identity of a droplet and its placement in 3D space. The set of layers can be combined into a voxel matrix. A printer can then process these droplet deposition descriptions given as a voxel matrix to digitally fabricate heterogeneous and continuously varying material composites. This approach is often described as bitmap-based printing or voxel printing .
Copyright
The Mediated Matter Group
3D printed data visualization of a point cloud representing a statue from the Tampak Siring Temple in Bali . Photo: The Mediated Matter Group
Credit:
The Mediated Matter Group
Copyright
The Mediated Matter Group
Credit:
The Mediated Matter Group
Commercially available multimaterial 3D printers can have a build envelope of 500 mm by 400 mm by 200 mm with a droplet deposition resolution of 600dpi and 300dpi, respectively, and a layer separation of down to 12μm, which results in 929 billion individually addressable material droplet positions, or voxels, through the approach described above. This high-resolution build space enables two key characteristics relevant for physical visualization:
- Volumetric color and opacity gradients, achieved by varying the spatial density of droplets of different materials.
- Preservation of detail, achieved through a clear enclosure volume, which allows the digital fabrication of highly detailed structures with fine features.
While multimaterial 3D printing is used in the sophisticated design processes of advanced products with complex geometries, it has only recently been used for the generation of data sculptures containing data-informed patterns.
Copyright
The Mediated Matter Group
3D Printed visualization of Biopsy from a mouse hippocampus, observed via confocal expansion microscopy. Photo: The Mediated Matter Group
Credit:
The Mediated Matter Group
Copyright
The Mediated Matter Group
Credit:
The Mediated Matter Group
Copyright
The Mediated Matter Group
In vitro reconstructed living human lung tissue on a microfluidic device, observed through confocal microscopy. Photo: The Mediated Matter Group
Credit:
The Mediated Matter Group
Copyright
The Mediated Matter Group
Credit:
The Mediated Matter Group
Our approach to physical data visualization through voxel printing using multimaterial 3D printing presented herein enables direct digital manufacturing of numerous data sets commonly found in scientific visualizations through rasterization, without the need to create intermediate representations for 3D printing. As a result, the method and its various applications point towards the elimination of the digital/physical divide, bridging digital on-screen data and their physical manifestations.
View more
people, updates
{{#each images}}
{{/each}}
Previous Nextof
{{#each images}}
{{ title }}
{{{ caption }}}
{{/each}}
Leveraging a 3D printer “defect” to create a new quasi-textile — MIT Media Lab
Leveraging a 3D printer “defect” to create a new quasi-textile — MIT Media Lab Find People, Projects, etc.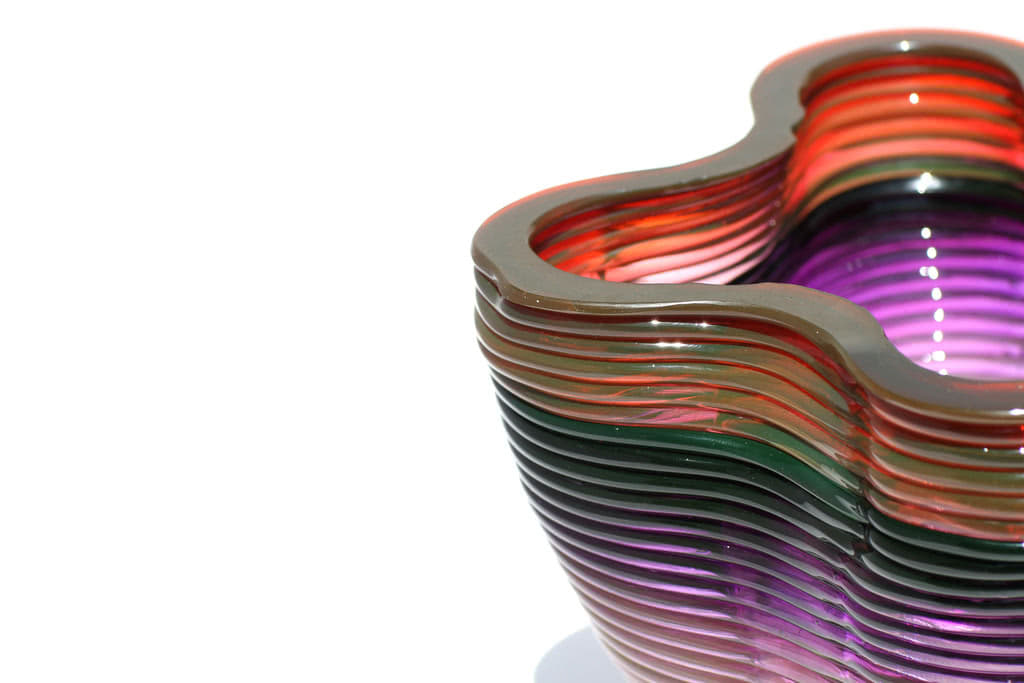
Email:
Password:
via MIT News
Oct. 26, 2020
Topics
- #3d printing
- #materials
- #fabrication
- #covid19
People
-
Jack Forman
Research Assistant
Projects
- DefeXtiles: 3D printing quasi-woven textiles via underextrusion
Groups
ByBecky Ham | MIT Media Lab
Sometimes 3D printers mess up. They extrude too much material, or too little, or deposit material in the wrong spot. But what if this bug could be turned into a (fashionable) feature?
Introducing DefeXtiles, a tulle-like textile that MIT Media Lab graduate student Jack Forman developed by controlling a common 3D printing defect — the under-extrusion of polymer filament.
Forman used a standard, inexpensive 3D printer to produce sheets and complex 3D geometries with a woven-like structure based on the “glob-stretch” pattern produced by under-extrusion. Forman has printed these flexible and thin sheets into an interactive lampshade, full-sized skirts, a roll of fabric long enough to stretch across a baseball diamond, and intricately patterned lace, among other items.
Read on MIT News
Related ContentPublication Research
DefeXtiles: 3D Printing Quasi-Woven Textiles Via Under-Extrusion
Jack Forman, Mustafa Doga Dogan, Hamilton Forsythe, and Hiroshi Ishii. 2020. DefeXtiles: 3D Printing Quasi-Woven Fabric via Under-Extrusion. In Proceedings of the 33rd Annual ACM Symposium on User Interface Software and Technology (UIST '20). Association for Computing Machinery, New York, NY, USA, 1222–1233. DOI:https://doi.org/10.1145/3379337.3415876
Proceedings, Oct. 2020
in Tangible Media
Post Research
Jack Forman receives the 2021 MIT RISE LBGTQ+ Pride Award
The RISE LBGTQ+ Pride Award recognizes staff and students who have made significant contributions to creating an inclusive community.
May 10, 2021
in Tangible Media
Post Research
Media Lab researchers honored in 2021 A'Design Awards
Congratulations to the winners of this year's A'Design Awards, including Media Lab researchers Jack Forman, Ali Shtarbanov, and Hila Mor!
May 14, 2021
in Tangible Media · Responsive Environments
Post Research
The Media Lab at the 2021 Core77 Design Awards
Congratulations to the winners of the 2021 Core77 Design Awards!
June 21, 2021
in Tangible Media · Media Lab Spinoffs
{{#each images}}
{{/each}}
Previous Nextof
{{#each images}}
{{ title }}
{{{ caption }}}
{{/each}}
Skoltech Additive Technologies Laboratory: more than 3D printing
A new additive manufacturing laboratory was opened at the Skolkovo Institute of Science and Technology. In terms of a set of unique equipment (including the country's largest 3D printer Insstek MX 1000) and the scale of tasks, the laboratory has no equal in Russia.
The new laboratory, headed by Professor Iskander Akhatov, director of the Skoltech Center for Engineering, Manufacturing Technologies and Materials, is a large-scale international project, which also involves the Swiss technology company Oerlikon through its Munich division specializing in 3D printing, as well as one of best universities in Germany, Munich University of Technology.
Russia's largest 3D printer Insstek MX 1000. Photo: Sk.ru
Skoltech Rector Alexander Kuleshov, speaking at the opening of the laboratory, recalled its background. It all started a year ago, when academician Kuleshov met with the president of the Technical University of Munich and with the chairman of the board of directors of Oerlikon, Michael Suess. “We signed a non-committal cooperation agreement,” he recalls. - The document did not oblige us to anything, because Skoltech had nothing to offer then. But each of the partners had their own trump cards. We had an excellent team in the field of mathematical modeling; Oerlikon, one of the world leaders in the production of new materials and technologies for these materials, is interested in developing 3D printing technologies. Plus the Technical University of Munich, the best university in Germany with gigantic authority - primarily in the field of mechanics, mechanical engineering, engineering. The result was a very successful triumvirate. Within a year, we were completely ready for cooperation.”
Skoltech Rector Alexander Kuleshov: “Over a year, we were completely ready for cooperation.” Photo: Sk.ru
Michael Suess called the opening of the laboratory at Skoltech "a new milestone", explaining that this is only the first step in the development of a trilateral partnership. In late autumn or early summer, Oerlikon will enter the laboratory with its equipment and technology. As noted in this regard, Prof. Iskander Akhatov, by this time the laboratory, along with the entire Skoltech, will move to a new university campus.
“Humanity is facing a choice of a new way of production”
However, according to Michael Suess, the joint operation of the latest 3D printers and the performance of research with their help is only one part of the cooperation: “The second and, perhaps, the most important part , lies in the fact that we are all learning new additive technologies and mastering them together. Because for the first time in the past few centuries, humanity is faced with the choice of a new mode of production. This is a giant challenge. And success in this direction is not yet guaranteed. One thing is clear: if we try to achieve a result alone, then we will definitely fail. This new type of production becomes possible only thanks to the ongoing digitalization of the economy, the growing power of computers that allow creating complex mathematical models. And this is the strength of Skoltech, where a brilliant team of mathematicians has gathered under the leadership of Academician Kuleshov. Cooperation with Skoltech is of a substantive nature, because we are going to implement specific projects together.”
Oerlikon Chairman Michael Suess. Photo: Sk.ru
The head of the laboratory of additive technologies, Professor Akhatov, also believes that, as he puts it, “the strength of Skoltech is not in the equipment, but in the fact that a large team of mathematicians has gathered here who are engaged in mathematical modeling.” The fact that the new laboratory will be one of several that are part of the Skoltech Center for Design, Manufacturing Technologies and Materials will make it possible to comprehensively study the three-dimensional structure of materials, and, consequently, to predict their physical properties. Work in this area will, in particular, be carried out within the framework of pilot projects in cooperation with the Munich University of Technology.
Prof. Iskander Akhatov, head of the new laboratory: "Ahead is an extremely difficult process. " Photo: Sk.ru
“Skoltech absolutely needed to open such a laboratory,” Alexander Fertman, director of the Skolkovo Department of Science and Education, told Sk.ru. - The direction of additive technologies in itself is so important for the development of the digital economy, because it is it that ensures a quick transition from digital to free forms, to details that are not limited by the capabilities of machine tools. The partnership with Oerlikon will be an important step for us in implementing additive technologies and projects based on them not only in Russia, but also in the international market.”
A laboratory employee demonstrates a part printed on a Ceram Ceramaker 900 ceramic 3D printer. Photo: Sk.ru
Three 3D printers were purchased for the laboratory that opened today: Trumpf TruPrint 1000 with metal printing; Ceram Ceramaker 900 with ceramic printing and Insstek MX 1000, which is designed to work with large parts in steel, copper, aluminum, titanium and nickel, is an industrial high-speed printing.
“Skoltech absolutely needed to open such a laboratory. In itself, the direction of additive technologies is so important for the development of the digital economy, because it is it that provides a quick transition from digital to free forms, to details that are not limited by the capabilities of machine tools”
“Unlike many other centers where additive systems are idle for months, Skoltech managed to launch all three machines in three to four months. We already have pilot samples, we are already negotiating orders with large and medium-sized enterprises. So far, these orders are not too scientific - rather, technological. I think that the next most important step will be the creation of a strategy for the laboratory of additive technologies and the division of attention between applied tasks and fundamental research, of which there are still many in additive technologies. I hope that the Skoltech team, with the support of both the Skolkovo Foundation and our startups, will be able to become one of the main centers of competence in the field of additive technologies in Russia. ”
Director of the Skolkovo Science and Education Department Alexander Fertman: “I hope that the Skoltech team, with the support of the Skolkovo Foundation and our startups, will be able to become one of the main centers of competence in the field of additive technologies in Russia.”
The management of Skoltech has a sober view of the work ahead. Academician Alexander Kuleshov, who, according to him, finds time every day to visit the new laboratory, said that, in addition to many discoveries and great interest, there are also disappointments. “It's not enough to buy a 3D printer and assume that everything else will magically fix itself. As always, the devil is in the details, and there are a lot of these details. Be that as it may, these technologies have a perspective, and we understand this very well. In the near future, the industry will do without standard machines,” said the rector of Skoltech.
Photo: Sk.ru.
The head of the laboratory, Iskander Akhatov, preceded his acquaintance with it with a quote from Pushkin about "experience, the son of mistakes is difficult. " In addition to the experience gained by the inevitable mistakes in such a new business, genius and chance, about which the poet wrote, will also be required.
As the head of the laboratory of additive technologies said: "This is an extremely difficult process."
3D printing of teeth and other products
Home
Dental laboratory Top 3D Shop
Top 3D Shop Dental Laboratory
Top 3D Shop Laboratory manufactures a full range of dental products using additive and classical methods, using materials and equipment from leading manufacturers: crowns and implants, bridges and caps, abutments, inlays, frameworks and bars , byugels, veneers, caps, surgical templates, models.
Designs:
Abutments
We accept STL files from any intraoral scanners:
- iTero
- Sirona
- ZM
- Zshape
- MHT
- Planmeca
Workpiece materials:
- Wax
- Titanium
- Ceramic
- Cobalt Chrome
- Zirconia
- Polyetheretherketone
- Polymethyl methacrylate
- Composites and specialty materials from leading manufacturers
Implant systems:
- ABDental
- Adin
- AlphaBio
- Ankylos
- Antogyr
- Astra
- Bego Semados
- BioHorizons
- Biomet 3i
- Biotech
- Conmet
- CSM
- C-Tech
- Dio
- Impla Conical
- ImplaSchutz
- Implantium
- Impro
- LIKO-M
- Medentix
- Megagen
- Mis
- NeoBiotech
- NIKO
- Nobile Active
- Nobel Branemark
- Nobel Conical Connection
- Nobel_Replace
- Osstem
- OT Medical
- Radix
- Renova
- Sic
- Sin
- Sky Bredent
- TBR
- Xive
- Zimmer
3D dentistry is new in the world of prosthetic technologies
A prosthesis on a 3D printer is no longer a fantasy, but a completely familiar and ordinary solution to many issues related to prosthetics. Now, many modern advances are used in dental clinics, thanks to which it is possible to solve problems as simply as possible and much cheaper than it was before. Unfortunately, not everyone has access to 3D dentistry, since such equipment requires additional costs and the ability to work with special equipment. But our services can be considered a way out of the situation, because we represent the whole range of work that a dental laboratory can perform. Our only difference is the 3D technologies used, thanks to which it is possible to print almost any products and designs.
The production of abutments, crowns or bridges can be quite time consuming using classical methods. The manufacture of dentures and other products in a modern laboratory equipped with appropriate equipment is a completely different direction, which allows you to reduce the cost of the process as much as possible, but not reduce the quality of the products obtained. Even artificial gums, thanks to printing in a private clinic, are not a problem - all activities in our dental laboratory are carried out quickly and professionally.