3D printer market share
3D Printing Market Size, Growth
The global 3D printing market size was valued at USD 15.10 billion in 2021. The market is projected to grow from USD 18.33 billion in 2022 to USD 83.90 billion by 2029, exhibiting a CAGR of 24.3% during the forecast period. Based on our analysis, the global market exhibited an average growth of 20.2% in 2020 as compared to 2019.
Rapidly increasing digitization, increasing adoption of advanced technologies such as Industry 4.0, smart factories, robotics, machine learning, and others fuel the demand for online 3D printing for simulation purposes. These technologies increase the chances of broader adoption and greater utilization of this technology across industries, including aerospace, automotive, healthcare, among others. For instance,
- Aerospace companies are exploring this 3D printing for manufacturing various hardware parts of their products. For instance, Boeing leverages industrial 3D printing to manufacture the interior parts of its plane, whereas, NASA uses it to build rocket engines and parts of the satellite.
- Automotive industry is expected to show a huge adoption of this technology. Rapid tooling incorporated with additive manufacturing has become the priority of many automotive manufacturers. Customization of the automotive interior is another major application of this technology in the automotive industry.
COVID-19 IMPACT
Supply Chain Disruption and Halts on Production Units Negatively Impact Printing Industry Amid Lockdown
Post outbreak of the COVID-19 crisis, industrial hubs, manufacturing sectors witnessed an immediate supply chain disruption and halts on production. As a result of the fast-spreading pandemic, the overall industrial production across the globe experienced a sharp decline. It was demobilized, reflecting supply chain disruption, and reviving financial market conditions. The crisis forced market players across the globe to reduce their operational expenditure. Fewer operation expenditures restricted the investments of market players in this technology in 2020, impacting the 3D printing market growth.
The temporary closures of the factories in major economies such as China, Southeast Asia, the U.K., Germany, and others have impacted the production plants of the 3D technology industry and operations of suppliers resulting in short-term supply shortages. Manufacturing capacity was observed to be restored to normalized levels by the end of July 2020. The short-term disruptions in supply shortages have resulted in logistics challenges, including delays in delivering services to end-use industries. Such a situation affected the company’s ability to meet the technology demand of the end customers. For instance,
- Stratasys, one of the well-known companies in the market, experienced dip in sales in the early months of COVID-19 pandemic. However, later, the company started rebounding as it picked up new manufacturing contracts.
However, the study conducted by the ‘Society of Manufacturing Engineers’ states that 25% of the manufacturers in the United States plan to change their supply chains in response to the pandemic. The study also found that they prioritize investing in this technology post-COVID-19 out of other technologies such as robotics, 5G, digital security, and artificial intelligence. This shows that the increasing investments of manufacturers in 3D technologies are likely to uplift the growth of the market in the forthcoming years.
LATEST TREND
Request a Free sample to learn more about this report.
Advancement in 3D Hardware and Software is Generating New Revenue Streams for Market Players
Techno-savvy start-ups and established market players are upgrading and developing new technologies. The advancements in hardware have led to faster and reliable 3D printers for production applications. Polymer printers are one of the most used 3D printers.
- According to a 2019 report by Ernst & Young Global Limited, 72% of the enterprises leveraged polymer additive manufacturing systems, whereas the remaining 49% used metal additive manufacturing systems.
The statistics show that developments in polymer additive manufacturing would create new market opportunities for market players.
Fused Filament Fabrication (FFF) and powder bed fusion technologies such as Multi Jet Fusion offered by HP Inc. are expected to be the most preferred industrial 3D technologies by the manufacturers due to their ability of volume manufacturing and high productivity. Similarly, resin-based technologies such as digital light processing (DLP) and Stereolithography (SLA) are more likely to have a growing demand from the dental and consumer goods industry.
Similarly, software developments are gaining pace in the 3D industry driven by the demand to streamline operations. The technology has been extensively used in the manufacturing process, which has surged the need for software that can help manufacturers to increase production volumes and enhance their additive manufacturing processes efficiently.
DRIVING FACTORS
Substantial Investments of Governments and Tech Giants to Foster Market Growth
Many countries across the globe are experiencing massive digital disruptions in advanced manufacturing technologies. The United States is a potential user of 3D technology. In 2018, the United States Department of Defense included this technology as an important capability in their budget. Even tech software giants such as Autodesk, Microsoft, and HP have launched products aimed at additive and 3D printing manufacturing.
Similarly, China is making significant efforts to maintain the competitive index of the manufacturing industry in the global market. Chinese manufacturers foresee this technology as both a risk and opportunity for the Chinese manufacturing economy, and hence they tend to invest in the research and development of this technology.
Whereas India is looking forward to this technology as an opportunity to increase its share in global manufacturing competitiveness. The market in India is supported by active government initiatives such as the ‘Make in India’ Initiative.
Korea has established an independent roadmap for research and development of this technology and provides national support to execute it. The government of Korea is introducing tax incentives and accelerating industry regulatory agreements to encourage the adoption of this technology.
The U.K. government has developed an independent 3D technology strategy; however, it is witnessing some uncertainties in the U.K. manufacturing sector due to Brexit. Germany is expected to define new strategies for the technology as Germany has a well-established Industry 4.0 infrastructure.
RESTRAINING FACTORS
High Initial Investments to Restrict Market Growth
High initial investments are observed to be the most significant restraint for adoption of this technology. This investment encompasses investment in hardware, software, materials, certification, additive & manufacturing education, and training for the employees. The capital costs and resources required to set up a 3 dimensional system are quite expensive than traditional printing methods.
However, with the introduction of the industrial Desktop 3D printer, the manufacturers are helping the end-customers cut the high initial costs. Desktop printers are easy to use and handle and also are less expensive than the 3 dimensional system.
SEGMENTATION
By Component Analysis
Wider Adoption of the Software to Make Designs of Objects and Parts to Fuel its Growth Rate
On the basis of component, the market is divided into hardware, software, and services.
Adoption of hardware for manufacturing 3D printed material is maximum and is likely to maintain its dominance during the forecast period. The demand for hardware is increasing as major key players are enhancing their product portfolio and launching new technologies to serve high demand from several industry verticals. Companies are investing in research & development activities, which have a positive impact on the market growth.
The software is expected to grow at a high CAGR during the forecast period. The 3D printing software is widely used in different industry verticals to design the objects and parts to be printed. As manufacturing companies are shifting away from traditional manufacturing methods, the adoption of 3D software has grown to print iterations of different manufacturing parts.
By Technology Analysis
Fused Deposition Modeling (FDM) Technology to be at Forefront
Based on technology, the market has been divided into FDM, SLS, SLA, DMLS/SLM, Polyjet, Multi Jet Fusion, DLP, Binder Jetting, EBM, CLIP/CDLP, SDL, and LOM.
Among these, fused Deposition Modeling (FDM) technology captured the maximum share in 2021. The growth of FDM is mainly due to the ease of operation and advantages associated with the technology. FDM technology is highly used in making durable, strong, and dimensionally stable parts.
Direct Metal Laser Sintering (DMLS/SLM) technology is expected to grow at a high CAGR during the forecast period. The technology promotes the production of high-quality metal components, which makes them suitable for the manufacturing industry since they enable the creation of complex geometries of metals of extremely small sizes.
Selective Laser Sintering (SLS) is expected to show significant growth in coming years. SLS finds a wide variety of vertical applications, including aerospace, defense, automotive, and others. Polyjet, Multi Jet Fusion, DLP, Binder Jetting, EBM, CLIP/CDLP, SDL, LOM technologies are expected to witness a significant rise in adoption in the upcoming years.
By Application Analysis
To know how our report can help streamline your business, Speak to Analyst
Prototyping to Capture Maximum Market Share Due to its Widespread Acceptance Across Various Vertical Industries
This technology has application in prototyping, production, proof of concept, and others.
Due to widespread acceptance of the prototyping process across various vertical industries, the prototyping represented the largest market share in 2021. Prototyping helps businesses to achieve greater precision and produce consistent end products. This technology helps to manufacture 3 dimensional computer-aided design (CAD) models and prototypes.
The production is expected to witness strong growth during the forecast period. While manufacturers are shifting their traditional manufacturing units toward advanced manufacturing processes, the adoption of this technology to produce complex and low-volume parts is expected to grow during the forecast period.
By End User Analysis
Automotive Industry to Lead Market Owing to its Maximum Use in Producing Prototype Equipment
Automotive, aerospace and defense, healthcare, architecture and construction, consumer products, education, and others are some of the end-users of 3D printing.
The adoption of this technology in the automotive industry is expected to hold a maximum share in 2021. For decades, the automotive industry has been using this technology to produce prototype equipment and small custom products in a short time span. The technology is being widely used for the construction of lightweight components for automobiles and OEMs.
Additive manufacturing has tremendous potential for the aerospace industry, where light, solid, and geometrically complex parts are required — and normally manufactured in limited quantities. Aerospace and defense companies are heavily using this technology to produce lightweight components.
Additive processing in the healthcare industry helps create artificial tissues and muscles that mimic normal human tissues that can be used in substitution operations. These skills are anticipated to lead to vertical acceptance of 3DP in healthcare and the sector's development.
On the other hand, architecture and construction, consumer products, education verticals are anticipated to grow at a significant CAGR during the forecast period.
REGIONAL INSIGHTS
North America 3D Printing Market Size, 2021 (USD Billion)
To get more information on the regional analysis of this market, Request a Free sample
Geographically, the market is divided into five major regions such as North America, South America, Asia Pacific, Europe, and the Middle East & Africa. They are further categorized into countries.
Globally, North America accounted for the maximum share in the global market mainly due to rising expenditure on advanced manufacturing technologies by developed countries such as Canada and the U.S. Also, various government agencies, such as the National Aeronautics and Space Administration (NASA), have identified major R&D investments that can greatly contribute to space applications and create new technologies that drive business expansion.
Europe holds the second-highest market share in the global market. The demand for this technology is high among small and medium-sized industries that require high-speed, reliable, and inexpensive prototypes for manufacturing purposes. The regional market is expected to showcase strong growth in the adoption of this technology in the manufacturing and semiconductors industry.
Asia Pacific is anticipated to grow at the highest CAGR during the forecast period. An increasing interest in the development of a sustainable 3D printing environment has been backed by APAC manufacturers and the implementation of several policies and legislative proposals by governments in the region. Given the massive government funding for the industry, China is possibly the main force behind adopting this technology in Asia.
To know how our report can help streamline your business, Speak to Analyst
The Middle East & Latin America is expected to showcase high growth during the forecast period. The rapid adoption of 3D technology in the region is mainly due to technological advancements and improvements in the manufacturing industry.
KEY INDUSTRY PLAYERS
Companies are Focusing on Partnership and Collaboration Activities for Safer Internet Environment
The prominent players of the market are focusing on offering advanced and innovative solutions catering to the growing needs of industries. These key players are investing in R&D to provide innovative services and materials. They are entering into strategic partnership and collaboration to provide next-generation solutions. These companies are offering consumer-centric solutions to help in boosting business growth. Similarly, the key players are keen on offering a vast range of 3-dimensional materials to grow across every industry application.
February 2022 – Imaginarium partnered with Ultimaker to introduce desktop & industrial 3D printer range in the India market. This partnership would help Ultimaker to expand its business in India, where additive manufacturing is anticipated to reach a point of breakthrough in the coming years.
November 2021 – 3D Systems is planning to enhance additive manufacturing innovation through partnerships and launch of products. The company launched new 3-dimensional printing tools and collaborated with the U.K.-based startup Additive Manufacturing Technologies (AMT) to present novel 3-dimensional printing workflows and improve AM software, which is ideal for automotive components.
List of the Key Companies Profiled:
- 3D Systems Corporation (U.S.)
- The ExOne Company (Germany)
- voxeljet AG (Germany)
- Materialise NV (Belgium)
- Made in Space, Inc.
(U.S.)
- Envisiontec, Inc. (Germany)
- Stratasys Ltd. (U.S.)
- HP, Inc. (U.S.)
- General Electric Company (GE Additive) (U.S.)
- Autodesk Inc. (U.S.)
KEY INDUSTRY DEVELOPMENTS:
- March 2022 – South Africa’s Department of Science and Innovation (DSI) launched a pilot project to build around 25 houses by utilizing 3D printing technology to combat the shortage of housing in the country.
- March 2022 – 3DGence, a European manufacturer, launched a new industrial FFF machine, INDUSTRY F421, which is well-suited with high performance materials. Additionally, the firm has also introduced AS9100, a new high-temperature filament, which is made using polyether ether ketone (PEEK) and certified for use in defense and aerospace sectors.
REPORT COVERAGE
An Infographic Representation of 3D Printing Market
View Full Infographic
To get information on various segments, share your queries with us
The global 3D printing market research report highlights leading regions across the world to offer a better understanding to the user. Furthermore, the report provides insights into the latest industry growth trends and analyzes technologies that are being deployed at a rapid pace at the global level. It further offers drivers and restraints, helping the reader gain in-depth knowledge about the market.
REPORT SCOPE & SEGMENTATION
ATTRIBUTE | DETAILS |
Study Period | 2018-2029 |
Base Year | 2021 |
Estimated Year | 2022 |
Forecast Period | 2022-2029 |
Historical Period | 2018-2020 |
Unit | Value (USD billion) |
Segmentation | By Component, Technology, Application, End-User, and Region |
By Component |
|
By Technology |
|
By Application |
|
By End-User |
|
By Region |
|
Three Areas Holding Back The $10.
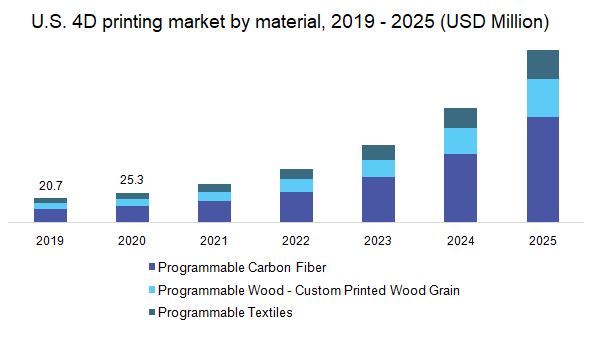
Market research firm SmarTech Analysis recently released its data for the additive manufacturing (AM) industry. It determined that, in 2021, the 3D printing sector reached $10.6 billion in revenue, excluding the revenues associated with hardware maintenance contracts and post-processing equipment. The firm further projects that AM is expected to grow to over $50 billion by 2030.
The 3D printing industry is projected to reach over $50 billion by 2030, according to one market ... [+] research firm.
Image courtesy of SmarTech Analysis.This growth is closely pinned to the trend that large manufacturers will increasingly use the technology for mass production. However, in order for AM to reach wide-scale adoption, it will need to advance significantly in three crucial and interrelated areas: throughput, factory integration, and quality control. Fortunately for the industry, these are all also issues that are being actively addressed.
3D Printing Throughput
Due to its roots as a prototyping technology, 3D printing was never designed with mass production in mind. Instead, its ability to create complex shapes has been limited to one-off parts or small batch manufacturing. For that reason, firms across the 3D printing industry have been working to develop systems that can make many parts as rapidly as possible, a concept known as throughput.
Among the leaders in this regard is HP, which spent years researching the technology before finally unveiling technologies capable of rapid production both in plastics and metals. The 2D printing giant has ported its expertise in inkjet printheads over to 3D printing with a technology called Multi Jet Fusion (MJF). MJF is already being used to produce large batches of polymer parts for everything from eyewear to grocery bots.
Legor Group in Italy is using HP Metal Jet to 3D print functional stainless steel accessories for ... [+] the jewelry and fashion markets.
MORE FROMFORBES ADVISOR
This is just the beginning for the company, which is now rolling out its Metal Jet technology. A form of what is called “metal binder jetting,” Metal Jet deposits a liquid binder onto metal powder, creating a component that must then be sintered in a furnace. Customers as large as Volkswagen are investing in the technology with a plan to mass produce up to 100,000 metal components annually for consumer vehicles.
However, HP isn’t the only company in this quickly evolving space. A widely publicized startup called Desktop Metal is working to speed up metal binder jetting. GE, too, is working on its own version of the technology. Altogether, these companies are ushering in an era in which low-cost metal powders can be used to 3D print large numbers of parts in a single job, potentially changing the cost structure for metal 3D printing altogether.
This means that they will be taking on the established leaders in metal 3D printing, which typically rely on zapping high powered laser beams at expensive metal powders. These companies are working on increasing throughput, as well, by adding up to 12 lasers to their machines.
3D Printing Factories
While a fleet of 3D printers may be capable of manufacturing at volume, that doesn’t mean that they’ll necessarily fit into an existing factory operation. In large part, this is due to the fact that they lack mass production-level software.
Now, a handful of startups have emerged to take on the challenge of developing AM-specific software for manufacturing execution systems (MES). These tools make it possible to both manage a fleet of 3D printers and connect them to a company’s existing production software. They typically aid in the entire order-to-fabrication workflow. This means order quoting and tracking, print file preparation, print job monitoring and data collection, printer fleet queuing, quality control, and shipping.
MES software necessarily connects to a business’s existing software tools. This includes product lifecycle management (PLM), enterprise resource planning (ERP), and general IT software. While PLM might include a company’s preferred 3D modeling software, ERP will be made up of everything from payroll programs to tools for tracking overall finances.
MES platforms are now working to take all of the software that a manufacturer might already be working with and inserting 3D printing into the mix. However, they’re not just limiting themselves to AM. Many MES developers are looking to connect with other production equipment, such as CNC machines. Then, with the help of machine learning, the entire workflow can be improved automatically as data from each order and each machine job feeds back into the work cycle. Artificial intelligence is significantly adding to the capabilities of MES software.
3D Printing Quality Control
Perhaps the biggest obstacle to widespread AM adoption is quality control. This is because, with additive, each part is distinct. Every point on the build platform may be slightly different and even the slightest variation in a printing parameter may change the microstructure of the printed object.
In turn, an object printed at one angle will not be the same as one printed at another. And, because parts are built up layer by layer, it is difficult to validate the internal geometries of an item once printing is complete. As a result, the only true way to assure the quality of a printed object is with a CT scan, typically a cost-prohibitive method for inspecting multitudes of parts.
Fortunately, not only are newer CT scanning systems with lower price tags coming onto the market, but there are other tools that are being used to ensure the quality of printed parts. Among them is computer simulation. Companies like ANSYS have developed software that can anticipate any defects that occur during the printing process and compensate for them. Hexagon is taking this one step further by predicting issues at the microscopic level.
Meanwhile, firms like Sigma Labs and Additive Assurance have created hardware to monitor the build chambers of metal 3D printers to detect errors. Increasingly, these tools will enable active feedback so that the machines can quickly correct issues during the print process. When connected with MES software and 3D printing simulation, the equipment can learn from past errors and address them before they even happen in the future.
Altogether, these areas are advancing at incredible rates, in large part because manufacturers see the value in being able to produce objects from digital files on demand. As companies as large as Ford, GE, and Siemens look to 3D printing to produce quality end parts, they are driving the entire additive market to bend to their needs. To reach a whopping $50 billion by the end of the decade, the 3D printing industry has to be capable of making millions of parts for those customers.
Overview of the 3D printing market in 2020
Analytics and business
Experts recommend
Author: Andrey Kombarov
Author: Andrey Kombarov
Additive Manufacturing Trends | Application of 3D printing | A look at additive technologies | Business Strategies for 3D Printing | Overview of the 3D printing industry over the past 6 years | Key Findings
The future of additive manufacturing starts with understanding the goals and expectations of 3D printing users around the world. This was the reason for the launch of an ambitious research project by the French company Sculpteo - the annual State of 3D Printing report. Today it is one of the most authoritative and comprehensive sources of information about the real situation and prospects of the industry.
This year, 1,600 respondents from 71 countries took part in the Sculpteo survey. According to the report, a growing number of companies are realizing the possibilities of additive manufacturing, increasing investments and demonstrating undeniable confidence in the future of professional use of 3D printing.
This material offers a complete overview of the world of additive manufacturing and will help you develop the right business strategy.
In the blog , the State of the 3D Printing Market 2020 is published in abbreviated form. You can download the full version for free in our virtual library:
Additive Manufacturing Trends
Materials
- New and available materials.
- Improving the quality and stability of budget additive technologies.
- Improving post-processing technologies to obtain parts with the highest quality surface.
- 3D printing from multiple materials at once.
Environmental sustainability
- Biodegradable materials and materials of biological origin.
- Manufactured on demand and on site to reduce transport and environmental costs.
- Application of 3D printing to meet the challenges of renewable energy and energy efficiency.
Technology Development
- Improved usability of software and printers
- Mass Production: Printing and 3D Scanning Speed
- Generative design
Availability
- Reducing the cost of 3D printers and materials (metals, photopolymers).
- Low post-processing costs.
- Sharing projects and tools.
iQB Technologies experts recommend articles:
3D printing as a full-fledged manufacturing technology in the context of the COVID-19 pandemic
2020 results and forecasts: the 3D printing market will grow by 25% annually
Application of 3D printing
The possibilities of 3D printing are growing every day, and with them the scope of its application is expanding. Gradually, companies begin to feel more confident in relation to 3D technologies. 68% of respondents are looking to use additive manufacturing to solve more problems, and 44% of are going to introduce new 3D printing technologies. Most professionals outsource SLS and Jet Fusion printing, as well as metal 3D printing, so they do not need to maintain their own equipment, and this will encourage them to test new technologies.
So what are the most popular 3D printing and post-processing technologies? Let's find out!
We emphasize once again that production volumes using 3D printing continue to grow. We are seeing this growth in research and development and education, which is in line with the increased demand for new materials and technologies in the market.
Click image to enlarge
The use of photopolymers is increasing through both internal and external services, while for metal 3D printing, most users outsource.
Design, testing and prototyping remain the main tasks solved with the help of 3D printing.
Stability and quality control remain a major concern for users seeking to scale up the use of 3D printing.
Most users use SLS, Jet Fusion and metal 3D printing technologies through outsourcing without purchasing equipment.
3D printing users are interested in exploring new applications, technologies and materials.
Typically, 3D printing is used in conjunction with traditional manufacturing methods such as laser cutting, CNC machining, and injection molding.
A look at additive technologies
What do respondents think about 3D printing technologies? In this section, we will look at the main benefits of 3D printing for users and their companies. How exactly does it optimize production processes?
66% of respondents use 3D printing to create parts with complex geometries. Survey participants cite the reduction in iterations, lead times and costs as the most important benefits of this technology.
In this section, we will also look at the future of the additive industry and the factors driving its growth and business adoption. What needs to be done to accelerate the adoption of 3D technologies? Now we'll find out.
As technology and materials become more accessible, the cost savings of 3D printing become clear to more and more users. Many also cite time savings due to reduced iterations and lead times as a benefit.
Set-up costs and lack of knowledge are seen as the main limiting factors for the adoption of 3D printing.
The role of 3D printing in business and manufacturing continues to grow.
New materials and reliable technologies are in demand for more than 55% industries.
Business Strategies for 3D Printing
Additive manufacturing is a huge competitive advantage. With some significant benefits of 3D printing, such as reduced lead times and speed of innovation, the vast majority of respondents view 3D printing as a significant improvement for their business.
As for money, investment in additive technologies is growing every year. Most of these users will increase their investments in 2020! It can also be seen that the vast majority of those surveyed have been using 3D printing for several years and plan to invest more in this technology in the near future. The business world believes in the promise of additive manufacturing.
Let's watch how 3D printing becomes a real asset for companies, helping them develop their business strategy!
63% of see a significant or dramatic impact on sales. Reduced lead times and speed of innovation are the most important success metrics for 3D printing.
Nearly 60% of consider 3D printing one of their strengths compared to the competition.
65% of companies plan to increase their investment in 3D printing in 2020.
The integration of 3D printing into manufacturing processes continues to increase: 74% of actively use 3D printing in their companies.
Overview of the 3D printing industry over the past 6 years
The Sculpteo report offers a look at the analysis of the state of the 3D printing industry for each year since 2015. How has the use of 3D printing evolved over the period 2015-2020? Let's look at the answers of the latest polls.
Large-scale production using 3D printing continues to spread, becoming as commonplace as prototyping and testing.
Accelerating development and offering customized products and limited editions remains a major challenge for companies using 3D printing.
The market share of photopolymers continues to increase, showing significant growth over the past two years.
Key Findings
1. Lack of stability is the Achilles' heel of 3D printing
In order for additive technologies to become an integral part of any production, it is necessary to develop equipment and materials that ensure high stability.
- 51% claims to use 3D printing mostly for quality control purposes.
- 62% of believe the 3D printing industry needs more robust technology to grow.
2. 3D printing is gaining ground in certain industries
Many industries are beginning to increase their use of 3D printing as its role in their manufacturing processes becomes more significant. Users are constantly deepening their knowledge and experience in the application of additive technologies.
- 80% of have been using 3D printing in their companies for over 2 years.
- 33% expect up to 50% increase in investment this year, which is a more conservative estimate than in previous years.
3. 3D printing may not be profitable
For wider use of additive technologies, the cost of manufactured parts must be reduced - this will attract more industries and sectors.
- More than 50% of outsource SLS, Jet Fusion, SLM/DMLS and Binder Jetting to offset equipment and service costs.
- 59% indicate that the cost of organizing production is a limiting factor for the adoption of 3D printing.
4. Changing Perceptions: From Prototyping to Full Manufacturing Technology
Despite the increasing use of 3D printing in manufacturing, its benefits are so far only apparent for prototyping and small-scale production. Businesses need to be shown the real benefits of 3D printing for industrial production.
- 60% report a significant reduction in part cost when using 3D printing.
- 52% of use 3D printing for manufacturing, while 68% of use 3D printing for prototyping.
This article is an abridged version of the Sculpteo report. The full version is available at link .
© 2020 Sculpteo. The material was translated by iQB Technologies exclusively for the 3D experts' blog blog.iqb.ru.
Download material
Article published on 08/20/2020, updated on 06/11/2021
3D Printing Market Research: 6 Important Trends
Time is the most valuable commodity today. High competition and the emergence of new business models require accelerated development cycles to quickly and flexibly implement innovative ideas. With new, more efficient equipment, high productivity, and a wide choice of materials, 3D printing technology saves time and money in the development and production of parts.
3D printing was originally designed to completely change the principles of production. The technology has a number of strategic advantages, such as design flexibility, reduced time to market, mass customization, distributed manufacturing, and many others. Despite some difficulties, 3D printing continues to show undeniable advantages.
Over the past few years, Jabil, a global manufacturing services company, has sponsored three 3D printing trend studies to help guide additive manufacturing and assess current realities. The 2021 survey surveyed more than 300 people responsible for making 3D printing decisions in manufacturing companies. The report allows you to get acquainted with the experience and opinion of professionals working "at the forefront". Respondents work in a wide range of industries, including electronics, plastics and packaging, industrial engineering, automotive, healthcare, and many others, giving us a comprehensive understanding of the 3D printing market and how additive technologies are being used.
1. The field of 3D printing is rapidly expanding
Thirty years is a very short time when it comes to traditional production methods. Additive technologies are revolutionizing a wide variety of industries.
The results of the last two surveys contrast sharply with the information that was obtained during the first survey in 2017. Even in the past two years, the adoption of 3D printing has increased significantly. The rise in popularity and expansion of the scope of additive manufacturing is clearly seen in the present study.
In 2017, the most popular answer to the question “what is 3D printing used for in your company?” was the answer "for rapid prototyping". Seven out of ten respondents confirmed the use of 3D printing for this purpose. The remaining answer options lag far behind the first: only three out of ten respondents chose the second option (tooling production). Since then, the scope of 3D printing has expanded significantly.
R&D has become the most popular area for 3D printing, ahead of prototyping. At the same time, there is a sharp increase in application scenarios in other areas. Since 2017, the proportion of companies using additive manufacturing to manufacture parts and tooling has doubled, and the use of these methods for mass production of parts has tripled.
Nearly 100% of study participants reported that they use 3D printing to produce functional or final parts. Undoubtedly, the scale of their production varies. Nearly 80% of respondents report using additive manufacturing to make at least 25-50% of functional parts.
Improvements in 3D printers allow companies to experiment with additive technologies in areas where they were previously unavailable. As the price of 3D printers declines and their productivity rises, the technology will become more accessible and will change the manufacturing industry as a whole.
2. The growth of additive manufacturing: forecasts are more optimistic than ever
Prospects for the development of 3D printing are extremely positive. Market participants are confident in a significant increase in the popularity of technology in the future. 97% of respondents believe that the adoption of 3D printing in their companies will grow in the next five years.
Most of the study participants believe that the use of 3D printers in their organizations will at least double over this period of time. Nearly half of respondents expect usage to double, and 4 out of 10 expect much more significant increases (5x or more). In addition to the growing popularity of additive technologies, a significant role in expanding their use, as already mentioned, will be played by their availability.
Companies in general plan to increase their additive capacity, but the highest expectations are in mass production of parts and goods. Slightly more than 80% of respondents expect that the use of additive technologies for mass production of products in their organizations will grow at least twice over the next five years.
H. 3D printing brings many benefits to companies
During the first study, many of the benefits were perceived as "intangible" concepts. However, over the past few years, use cases have increased, concepts have become reality, and two years later, respondents are even more inspired by the benefits of additive technologies. We have identified three main benefits of additive manufacturing according to reviews.
Perhaps the rise in popularity of 3D printing is not a coincidence, but is due to increased demand for additive manufacturing during the COVID-19 crisis. As the pandemic spread, companies with 3D printers began to produce personal protective equipment such as respirators and masks that suddenly became scarce. When developing new diagnostic equipment and analysis kits, the use of 3D printing has accelerated the process of prototyping and design.
Respondents chose faster manufacturing of parts as the main benefit of additive manufacturing. Jabil saw this first hand: indeed, the desire to eliminate the labor-intensive iterative process was the driving force behind the introduction of additive manufacturing into the Auburn Hills facility. Not only did it speed up workflows, but it also helped reduce costs by being able to immediately recreate the exact geometry (no need to cut off excess material). In fact, savings amounted to 30-40% on tooling and 80% on lead times.
“With the power of 3D printing, every aspect of manufacturing has been greatly improved,” said John Wahl VI, Tooling Engineer at Jabil's Auburn Hills facility. “The first aspect is time, the second is a more creative approach, the third is costs, the fourth is materials.”
According to the distribution by job level, senior managers are more optimistic about the benefits of 3D printing than department heads. Since it is the leaders who shape the vision (and plan the budget) for the future of the company, everything points to the further spread of 3D printing.
4. 3D printing materials become more affordable
Compared to 2019, companies are using many more types of 3D printing materials. Despite the fact that plastics/polymers are still leading the way, other materials are not losing ground and are catching up. This confirms our conclusion that the scope of 3D printing is expanding.
When it comes to primary material, the difference between plastic and metal in 3D printing is not as big as you might think. More than a third of respondents answered that they use plastic and metal equally, and those who choose only plastics are only 10% more.
Certainly some problems must be overcome in order to use some materials. More than half of the respondents (twice as many as in 2019) said that it takes too long to develop the necessary materials. Slightly more survey participants said that some materials are too expensive for large-scale use, and are not available or certified.
However, as these problems are overcome, interest in different materials increases. When you look at what materials companies actually use and what they would like to use, plastic still comes out on top. At the same time, the desire to use almost all materials exceeds the current use. It is noteworthy that the interest in printing with glass exceeds the actual use by 20%, ceramics - by 14%, metal - by 10%. It will be interesting to see the changes in the use of materials in the next two years.
5. Additive manufacturing is still a source of problems
Despite the optimistic view of the development of additive manufacturing, companies still have to solve a number of problems associated with 3D printing. In 2019, half of respondents cited material costs as a problem, but this year only about two-fifths did so. All problems are located approximately on the same level: most of them fluctuate around 40%.
However, many of the current problems are related to costs, since 95% of respondents reported financial barriers to adopting additive manufacturing. Obtaining appropriate qualifications and certifications is the main challenge, followed by capital expenditures associated with equipment and the need for in-house specialists.
In 2021, pre- and post-processing costs have become a major concern. Companies are using more and more pre- and post-processing methods. In 2019, just over half of respondents reported using mechanical finishing, now it is almost three-quarters, with no polishing being the most common option. Given that the use of all processing methods has increased significantly, it is possible that companies are experiencing growth difficulties. If these problems continue to be given priority attention, they can be overcome.
6. Training of specialists is a priority
Now about three-quarters of the respondents are engaged in additive manufacturing on their own. Given that half of the time they chose “lack of in-house talent” as their problem, it can be assumed that companies are prioritizing educating their employees about additive manufacturing or attracting professionals with experience and knowledge in the field of 3D printing.
This does not mean that organizations are opposed to outsourcing additive manufacturing: in fact, almost 100% of respondents said they were considering this option. When looking at potential suppliers, companies take into account a variety of criteria. Design capability is key, and scalability, pricing, and experience continue the list.
We are seeing significant growth in 3D printing in some areas. In others, this growth is still small. Four years ago, companies used 3D printers primarily for fast, low-cost prototyping: Few businesses relied on additive manufacturing for full-scale production. However, in just four years, as the problems with materials for additive manufacturing were solved and the scope of its use increased, the situation has changed. We have seen how 3D printing has literally taken over many manufacturing industries, which is reflected in the growth of market performance. Slowly but surely, the adoption of additive manufacturing continues. Digital manufacturing is the future.