3D printer high temperature material
Finding The Best Heat Resistant 3D Printing Filament
Jun 5, 2020
A wide range of innovative and sophisticated heat resistant materials are available for 3D printing. They open the door to new possibilities of manufacturing and design. Here, we help you find which heat resistant 3D printing filament is best for you.
There are several heat resistant 3D printer materials that manufacturers can use for objects that are required to withstand high levels of heat. In this article, we’ve rounded up the best heat resistant 3D printing materials for FFF printing.
1. PET-GA great heat resistant filament is PET-G (polyethylene terephthalate glycol-modified). This 3D printing material is great for beginners because it’s just as easy to print as PLA, but more technically resistant to different stressors such as heat, water, and corrosive chemicals.
For instance, it can withstand operating temperatures of up to 70ºC. It’s commonly used is for end-use parts that need good mechanical and thermal strength. Furthermore, PET-G is employed for its strong water and moisture resistance, making it an ideal material for water-tight materials and waterproof functions.
2. ABSABS (acrylonitrile butadiene styrene) is a commonly used thermoplastic filament that is popular among professional printers due to its stiffness and heat resistance. This 3D printing filament is frequently used for prints that will undergo high-stress applications, like heat or impact.
ABS is a great option for a heat resistant 3D filament, as it can withstand temperatures of up to 100ºC. Besides being heat resistant, it is also water and impact-resistant, even at temperatures as low as -10ºC.
3. PPPP (polypropylene) is well known for its extraordinary chemical resistance, especially against alkali, acids, and organic solvents. But, along with being chemically resistant, it is a heat resistant 3D filament as well.
PP can withstand temperatures of up to 100ºC. Thanks to its smooth, lightweight, and clear appearance, it is often used for food containers, liquid bottles, and other printed parts that come into contact with water or harsh chemicals.
4. PP GF30PP GF30 (polypropylene 30% glass fiber) is similar to its non-glass fiber counterpart, but with an even higher heat resistance of 120ºC plus the added benefit of UV resistance. These two qualities make PPGF30 a great filament option for parts that need to be able to resist a variety of weather conditions.
This 3D printing material is also commonly used in the automotive and aerospace industry thanks to its strong heat and chemical resistance and strength. However, it is still a lightweight 3D printing material. Therefore, it can be used to create prints that are equally strong, rigid, and weather-ready.
PA (polyamide) is another thermoplastic that is suitable for heat resistant 3D printing. Featuring a thermal resistance of up to 120ºC, PA can withstand this high heat for an extended period of time, making it a great option if your print will be subjected to heat.
PA is also semi-flexible due to its semicrystalline structure, meaning this material’s strength goes beyond heat resistance. PA is frequently used to print parts that must be exposed to a variety of environments thanks to its high heat, abrasion, oil, and impact resistance. It used to print a variety of manufacturing materials, like jigs, washers, bearings, handles, and snap-fit joints.
6. The most heat resistant 3D printing filament of all: PAHT CF15PAHT CF15 (high-temperature polyamide carbon fiber reinforced) is a very strong and technically advanced material. Thanks to its 15% carbon fiber, it is both heat and chemical resistant, landing itself as the most heat resistant 3D printing material on this list.
It can withstand continuous temperatures of 150ºC, making it the ideal filament to use if your print will be subjected to high heat for long periods of time. Alongside being heat resistant, PAHT CF15 is also characterized by high stiffness, strength, and printability. This filament is best suited for the most technical printing applications, like moving parts or even metal replacement.
In conclusion, when it comes to finding a 3D printing material that is heat resistant, the options are plentiful. Each heat resistant 3D printing filament comes in many different cost points, skill levels, and strengths. Beyond just being heat resistant, many have additional features that can help narrow down choosing the perfect filament for your print. Should you be interested in learning more, be sure to download our dedicated white paper below, or for a quick fix have a go at our material selector!
The Best Heat Resistant Materials for 3D Printing
One of the many desirable characteristics of 3D printing as a manufacturing technology is its ability to produce fully functional parts for numerous applications across different industries and in various operating conditions. 3D printed parts are often used in high-temperature applications. However, in order to function properly in such environments, they need to be made from heat-resistant materials. This article covers some of the best heat-resistant 3D printing materials for use in high-temperature applications.
Best heat-resistant 3D materials
Acrylonitrile Butadiene Styrene (ABS)
ABS is capable of withstanding temperatures of up to 100°C. Its heat deflection temperature is between 88-89°C and its melting point of about 200°C. ABS is also known for its toughness and resistance to impact. These allow for the printing of parts to be subjected to high-stress applications. It has a glass transition temperature of about 105°C and is highly resistant to aqueous, phosphorus and hydrochloric acids.
- Technology: Fused Deposition Modeling (FDM)
- Key Features: Chemical resistance, impact resistance
- Common applications: Drain/waste pipes, inhalers, housing for electrical components
ULTEM 1010
ULTEM 1010 has the highest heat resistance, chemical resistance and tensile strength compared to other FDM thermoplastics. It is available in transparent, opaque and glass-filled grades. This material has broad application in custom tools for metal or plastic parts fabrication, medical tools and temperature resistant dies.
It is a high-performance polyetherimide thermoplastic with a melting point of 340°C and a glass transition temperature of 216°C. ULTEM 1010 has the lowest coefficient of thermal expansion. It has food-contact and biocompatibility certifications, which makes it ideal for applications in the food industry.
- Technology: Fused Deposition Modeling (FDM)
- Key features: Excellent heat resistance, tensile strength, low coefficient of thermal expansion
- Common applications: Medical tools, temperature resistant dies
CE 221 (Cyanate Ester)
This material is known for its high-temperature resistance and rigidity. Due to its high heat-deflection temperature, it can be safely applied in applications with high thermal requirements.
The CE 221 resin has long-term thermal stability with a glass transition temperature of about 225°C and a heat deflection temperature of 231°C. This material is capable of withstanding high pressure and giving a highly precise surface finish.
- Technologies: Carbon DLS
- Key Features: Thermal stability, rigid, high pressure resistance
- Common applications: Industrial products, electronic assembly components, fluid manifolds
ULTEM 9085
This has a high strength–to–weight ratio, high impact strength with good heat resistance. ULTEM 9085 is highly flame retardant. It is used in the production of prototypes as well as tools in the aerospace and automotive industries. This has a glass transition temperature of 186°C and a heat deflection temperature of 153°C.
ULTEM 9085, with its superior mechanical strength and lightweight, is suitable for the production of end-use components.
- Technology: Fused Deposition Modeling (FDM)
- Key Features: Flame retardant, impact resistance
- Common applications: Jigs, fixtures, composite moulds
Polycarbonate (PC)
This material has a crystalline melting point of about 230°C – 260°C and a glass transition temperature of 147°C. Polycarbonate is a tough and amorphous material with high impact strength, stability and good electrical properties. It has a wider temperature range of usage with a heat deflection temperature of 140°C. It is widely used for the production of safety helmets, lenses for car headlamps and bulletproof glasses.
- Technology: Fused Deposition Modeling (FDM)
- Key Features: Translucence, pliability
- Common applications: Plastic lenses in eyewear, protective gear, automotive components
PEEK
It has excellent resistance to harsh chemicals with high mechanical strength and dimensional stability. Its melting temperature is at 343°C and it has a glass transition temperature of 143°C. PEEK has the ability to retain its stiffness at elevated temperatures and can be applied for continuous use at temperatures up to 170°C. It is used in aerospace, oil and gas and semiconductor production.
- Technology: Fused Deposition Modeling (FDM)
- Key Features: Chemical resistance, good stiffness, resistance to steam and water
- Common applications: Semiconductor components, valve and pump components, food processing machinery
PC – Like Heat Resist Translucent / Accura 48
This is a high-temperature resistant material that is best suited for parts that require high strength and stiffness. It is widely used for the manufacturing of prototypes of electronic and lighting components. It provides enhanced feature details.
At 0.46MPa test pressure, PC-Like Heat Resist Translucent has a heat deflection temperature that ranges from 70 – 85°C. This heat deflection can be enhanced to about 135°C with a thermal post-cure.
- Technology: Stereolithography (SLA)
- Key Features: Temperature resistance, high strength, stiffness
- Common applications: Electronic and lighting components
Aluminuum AlSi10Mg
Aluminium AlSi10Mg has excellent strength at elevated temperatures (about 200°C). It has good resistance to corrosion and can be easily polished. It has good workability and good heat crack resistance with a melting point of 670°C. The fatigue strength is excellent at 110N/mm2.
Its characteristics allow for complex geometries to be printed and are widely applied in parts for vehicles, machines and aircraft. It has a tensile strength of 450 MPa at room temperature.
- Technology: Direct Metal Laser Sintering (DMLS)
- Key Features: Light weight, stress resistance
- Common applications: Motors, engines
Stainless Steel 316L / 1.
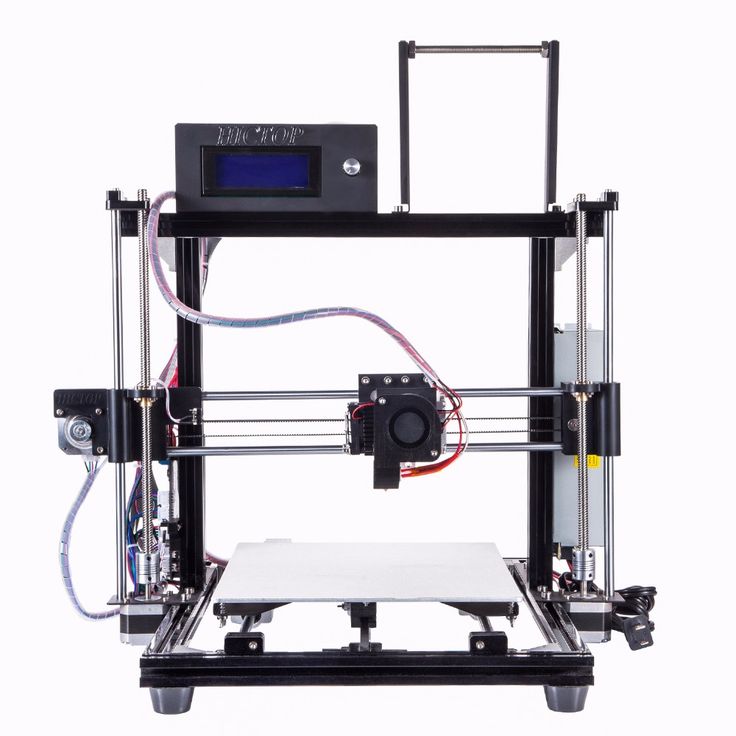
Stainless steel 316L can be used in continuous service in temperatures of up to 550°C. This material has low carbon content and is chromium-nickel-molybdenum stainless steel with a melting point of 1400°C. It has excellent corrosion resistance and stability against chlorine-based media and non-oxidizing acids. Its corrosion resistance and ductility make it ideal for applications in several industries such as aerospace, medical and automobile.
- Technology: Direct Metal Laser Sintering (DMLS)
- Key Features: Corrosion resistance, ductility
- Common applications: Laboratory equipment, heat exchangers, nuts and bolts
Inconel 718 (Nickel-Chromium superalloy)
Inconel 718 is a nickel-chromium based high-strength superalloy. It is resistant to corrosion, extreme pressure and elevated temperatures of up to 700°C. This material melts at about 1400°C. It has a tensile strength of 1035 MPa. However, it is brittle and has good machinability with a hard cutting tool. It is widely applied in manufacturing, military equipment and the aerospace industry.
- Technology: Direct Metal Laser Sintering (DMLS)
- Key Features: Corrosion resistance, brittle, mechanical strength
- Common applications: Gas turbine engine parts, compressor casings, die holders
Properties of heat-resistant 3D materials
The following table compares the melting point and glass-transition temperature of the 10 best heat-resistant materials for 3D printing:
Material | Melting point | Glass transition temperature | Tensile strength |
ABS | 200°C | 105°C | 42.5 – 44.8 MPa |
ULTEM 1010 | 340°C | 216°C | 105 MPa |
CE 221 | – | 225°C | 92 MPa |
ULTEM 9085 | – | 186°C | 71.![]() |
PC | 230 – 260°C | 147°C | 60 MPa |
PEEK | 343°C | 143°C | 110 MPa |
Aluminium AlSi10Mg | 670°C | – | 450 MPa |
Stainless Steel 316L | 1,400°C | – | 520 – 690 MPa |
Inconel 718 | 1,370 – 1,430°C | – | 965 MPa |
PC – Like Heat Resist Translucent / Accura 48 | Heat deflection temperature at 0. 46 MPa after thermal post-curing: 170 – 250°C | Glass transition temperature UV and thermal post cure: 122°C | 50 MPa |
Heat-resistant 3D printing materials cost comparison
Let’s have a cost comparison of the three resins from Xometry’s quote engine for the CAD model:
Material | 3D printing technology | Cost per one unit | Unit cost per 10 pieces | Unit cost per 100 pieces |
ABS | FDM | € 9.![]() | € 6.34 | € 2.57 |
ULTEM 1010 | FDM | € 50.03 | € 35.80 | € 34.61 |
CE 221 | Carbon DLS | € 645.21 | € 171.58 | Price on demand |
ULTEM 9085 | FDM | € 53.20 | € 23.83 | € 13.66 |
PC | FDM | € 34.45 | € 25.89 | € 25.03 |
PEEK | FDM | € 88.42 | € 64.65 | € 47.12 |
PC – Like Heat Resist Translucent | SLA | € 72.87 | € 21.64 | € 18.03 |
Aluminium AlSi10Mg | DMLS | € 174.76 | € 89.19 | € 87.80 |
Stainless Steel 316L | DMLS | € 387.12 | € 294.83 | Price on request |
Inconel 718 | DMLS | € 487.77 | € 333.![]() | Price on request |
Conclusion
Xometry Europe offers fast, reliable, and highly accurate 3D printing online services with these technologies and heat-resistant materials. Through our Instant Quoting Engine and our network of over 2,000 manufactures, we ensure that you experience a seamless part production process, from quoting to doorstep delivery.
Overview of high-temperature FDM plastics for industrial 3D printing
The scope of application of additive technologies is wide: on one extreme - desktop printers "only PLA", for decorative applications, on the other - installations for direct printing with metals, between them - equipment and materials in assortment. To understand what materials are needed to obtain a strong and lightweight part, we are moving from personal printing to industrial printing. PLA, ABS, SBS are consumables that are familiar to all printers. PETG, nylon, polycarbonate - rather exotic. But these are far from the most serious materials.
Where are superplastics needed?
Plastics with outstanding properties are very useful in space. No, it’s not yet possible to print a rocket engine out of plastic, the heat resistance is not even close to the same, but it is ideal for various parts around. An example is Stratasys and the "climate control" of Atlas V rockets. 16 printed parts instead of 140 metal parts - faster, lighter, cheaper. And this is not a theoretical project, it has already flown into space.
Another example is aviation. The flight altitude is lower, but the application is more massive. Here, too, there is a reason to reduce the mass of parts, switch to plastic where possible. It is used in the aircraft industry and direct metal printing, when it comes to engine components or fuselage frame parts, but less loaded structural elements, such as cabin ventilation and interior elements, are best made from plastic. This direction is being developed, for example, by Airbus.
We are descending from heaven to earth: here the mass is no longer so critical, other properties of engineering plastics are interesting. Resistance to aggressive chemicals and elevated temperatures, the ability to create structures inaccessible to classical methods. At the same time - a lower price, in comparison with metal printing. Printed products are used in medicine, oil and gas industry, chemical industry. As an example, a mixing block with a complex channel structure, made for illustration in a section.
Difference from conventional plastics
Why not launch PLA into space and make aircraft cabin air vents out of ABS? A number of requirements are applied to engineering plastics related to resistance to high and low temperatures, fire resistance, mechanical strength. Usually all at once. So, it is undesirable to launch PLA “floating” when interacting with the environment or perfectly burning ABS into the sky. Now - to what, in fact, plastics are used in industrial printing using FDM / FFF technology.
Polycarbonate filaments
Polycarbonate is a common industrial plastic with high impact resistance and transparency, also produced for the needs of FDM printing. The material holds temperature better than ABS, is resistant to acids, but is sensitive to UV radiation and is destroyed by oil products.
Clear polycarbonate, PC
The operating temperature limit for polycarbonate products is 130°C. Polycarbonate is biologically inert, products made from it can withstand sterilization, which makes it possible to print packaging and auxiliary equipment for medicine.
- Stratasys PC, PC-ISO for Fortus printers. The first is general purpose, the second is certified for biocompatibility, for medical use.
- Intamsys PC;
- Esun ePC;
- SEM PC;
- PrintProduct PC;
ABS/PC
Polycarbonate/ABS alloy combines the sanding and painting capabilities of ABS with higher impact resistance and operating temperature. Retains strength at low temperatures down to -50 °C. Unlike pure PC, it is better applicable in cases where it is necessary to eliminate the layered structure of the part by grinding or sandblasting. Application: production of housings and elements of controls for piece and small-scale production, replacement of mass-produced plastic parts in equipment, parts for which have ceased to be produced.
- Stratasys PC/ABS;
- Roboze PC-ABS;
- SEM ABS/PC;
- BestFilament ABS/PC.
Polyamide based filaments
Polyamides are used in the manufacture of synthetic fibers, a popular material for laser selective sintering (SLS) printing. For printing using FDM / FFF technology, polyamide-6 (kapron), polyamide-66 (nylon) and polyamide-12 are mainly used. Common features of polyamide-based filaments include chemical inertness and anti-friction properties. Polyamide-12 is more flexible and resilient than PA6 and PA66. Operating temperature approx. 100 °C, some modifications up to 120.
First of all, gears are printed from polyamide. The best material for this purpose, which can be worked with on a regular 3D printer with a closed chamber. Abrasion resistance allows you to make rods, cams, sliding bushings. In the line of many manufacturers there are composite filaments based on polyamide, with even greater mechanical strength.
- Stratasys Nylon 6, Nylon 12, Nylon 12CF. The latter is filled with carbon fiber.
- Intamsys Nylon, PA6.
- Taulman Nylon 618, Nylon 645 - based on PA66 and PA6, respectively. Nylon 680 is approved for use in the food industry. Alloy 910 is a low shrinkage polyamide alloy.
- PrintProduct Nylon, Nylon Mod, Nylon Strong;
- REC Friction;
- BestFilament BFNylon.
Moving on to the fun part
You can work with polycarbonate or polyamide on a regular 3D printer. With the filaments described below, it is more difficult, they require other extruders and maintaining the temperature in the working chamber, that is, you need special equipment for printing with high-temperature plastics. There are exceptions - for example, NASA, for the sake of experiment, upgraded the Lulzbot TAZ popular in the USA to work with high-temperature filaments.
Polyetheretherketone, PEEK
Working temperature of PEEK products reaches 250 °C, short-term heating up to 300 is possible - indicators for reinforced filaments. PEEK has two disadvantages: high price and moderate impact resistance. The rest is pluses. The plastic is self-extinguishing, heat-resistant, chemically inert. Medical equipment and implants are produced from PEEK, abrasion resistance makes it possible to print parts of mechanisms from it.
- Intamsys PEEK;
- Apium PEEK;
- Roboze PEEK, Carbon PEEK. The second is reinforced with carbon fiber.
Polyetherimide, PEI
aka Ultem. A family of plastics developed by SABIC. The characteristics of PEI are more modest than those of PEEK, but the cost is noticeably lower. Ultem 1010 and 9085 are Stratasys' primary materials for printing functional parts. PEI is in demand in the aerospace industry - the mass is much less compared to aluminum alloys. Operating temperatures of products, depending on the modification of the material, reach 217 ° C according to the manufacturer and 213 - according to the results of tests by Stratasys.
The advantages of PEI are the same as those of PEEK - chemical and temperature resistance, mechanical strength. It is this material that Stratasys is promoting as a partial replacement for metal in the aerospace industry, for drones, the manufacture of tooling for molding, the rapid printing of functional parts in pilot production.
The Atlas V rocket cooling system components and Airbus plastic parts shown as an example at the beginning of the review are made of Ultem 9085.
- Stratasys Ultem 1010 and 9085, for Fortus 450mc and 900mc printers.
- Intamsys Ultem 1010 and 9085;
- Roboze Ultem AM9085F;
- Apium PEI 9085.
Polyphenylsulfone, PPSF/PPSU
Another material that combines temperature resistance, mechanical strength and chemical resistance in its properties. Stratasys PPSF is certified for aerospace and medical applications. Positioned as a raw material for the production of auxiliary medical devices, it can be sterilized in steam autoclaves. It is used in the production of parts for laboratory installations in the chemical industry.
- Stratasys PPSF;
- 3DXTech Firewire PPSU.
Polysulfone, PSU
Less common than PPSU, similar physical characteristics, chemically inert, self-extinguishing. 175°C operating temperature, up to 33% cheaper than PPSU.
- 3DXTech Firewire PSU
Filament performance comparison
* Baked for 2 hours at 140°C.
** Apium PEEK 450 natural, no similar impact test results available. Temperature resistance is specified for unfilled PEEK.
Data shown for Stratasys filaments, excluding PEEK. If a range of values is indicated, then the tests were carried out along and across the layers of the part.
About Composite Filaments
Most FDM materials have composite versions. If we talk about PLA, then metal or wood powders are added to it to change the aesthetic properties. Engineering filaments are reinforced with carbon fiber to increase the rigidity of the part. The influence of such additives on the properties of plastic depends not only on their quantity, but also on the size of the fibers. If a fine powder can be considered a decorative additive, then the fibers already significantly change the characteristics of the plastic. By itself, the word Carbon in the name of the material does not yet mean outstanding properties, you need to look at the test results. For example: Stratasys Nylon12CF has almost twice the tensile strength, when tested along the layers, than Nylon12.
An exotic variant of Markforged's implementation of continuous reinforcement. The company offers a reinforcing filament for co-FDM printing with other plastics.
Other specific properties
Engineering plastics are not only high temperature resistance and mechanical strength. For housings or boxes for storing electronic devices, and in environments where flammable volatile liquids are used, materials with antistatic properties are required. In the Stratasys line, this is, for example, ABS-ESD7.
- Stratasys ABS-ESD7;
- Roboze ABS-ESD.
Conventional ABS is not UV resistant, limiting its outdoor use without a protective coating. As an alternative, ASA is offered, which has characteristics similar to ABS, except for the UV resistance.
- REC Eternal;
- SEM ASA;
- BestFilament ASA.
Original alternative
Plastic can replace metal in many areas, as it surpasses it in lightness, thermal and electrical insulation, resistance to reagents. But printouts from the best FDM filaments do not reach the physical indicators of metal products.
Chemical giant BASF offers Ultrafuse 316LX FDM filament with 80% stainless steel by weight. The part is printed on an FDM printer and then placed in an oven where the binder plastic is burned off and the metal is sintered. The part obtained in this way is much cheaper than the one made by direct metal printing. With an FDM printer and a suitable oven, no new equipment is needed at all.
Note that Virtual Foundry offers a similar solution - its Filamet, with bronze or copper powder, is baked in a similar way. The choice of metal hints at decorative rather than engineering applications.
AIM3D has its own implementation of this principle - the ExAM 255 printer does not work with filament, but with granules. This allows the use of raw materials for FDM printing, which are usually used in MIM installations, Metal Injection Molding. For sintering the part, the company offers an ExSO 9 furnace0. It is also possible to print with plastic granules, which is usually cheaper than using traditional filament.
Special machinery for engineering plastics
To recap. In a nutshell: the considered consumables differ from the usual materials in high printing temperature, which requires the use of special equipment, and serious heat resistance and mechanical strength of the manufactured parts. To work with such filaments, 3D printers with an extruder operating temperature of 350 °C and a heat-stabilized working chamber are required. Top 3D Shop specialists will help you with the selection of an industrial 3D printer and plastics for solving the most interesting tasks.
Want more exciting news from the world of 3D technology?
Follow us on social. networks:
Vk
Youtube
Top 3D Shop - Your expert in the 3D technology market
consumer grade 3D printers.

Polyethylene terephthalate (PETG) is usually the next step. It is not much harder to work with compared to PLA, while it is more reliable and can withstand higher temperatures. In general, it is better suited for creating mechanically loaded parts. But if you need to make even stronger and more heat resistant parts, you can switch to acrylonitrile butadiene styrene (ABS), polycarbonate (PC) or nylon. And this is where the problems begin. These materials are extruded at temperatures over 250°C and closed chambers are recommended for best results. These printers are at the top of the budget range that hobbyists are willing to work with.
Industrial 3D printers like this one, the Apium P220, start at around $30,000. (PAEK, PEEK, PEKK). Components made from these plastics are suitable for aerospace applications as they can replace metal while remaining much lighter.
These plastics need to be extruded at temperatures in the order of 400°C and require a hermetically sealed chamber that is constantly above 100°C. The cheapest printers of this kind cost tens of thousands of dollars, and some models even cost six figures.
Naturally, not so long ago, the same could be said about all 3D printers. Once used only by well-equipped research labs, these machines now sit on the workbenches of hackers and hobbyists the world over. It is difficult to predict whether the same price-cutting race will start for high-temperature 3D printers, but the first steps to democratize the technology have already been made.
Engineering difficulties
Simply put, a machine that supports these so-called. "engineering plastics", you need to be a hybrid of a 3D printer and a stove. This, of course, is the main problem. The printer itself - of the type and quality we are accustomed to seeing on our desks - will not survive in such conditions. In order for a consumer printer to produce PEI and PEEK plastic parts, it needs to be seriously redesigned. This is exactly what NASA did with the LulzBot TAZ 4 in 2016.
LulzBot TAZ 4 redesigned to support high temperature printing
The first step was to construct an insulated housing to fit the TAZ 4 and install a set of 35W infrared lamps for heating. Under such conditions, the printer's electronics would naturally overheat - so it had to be taken outside.
Stepper motors would also overheat. But instead of taking them out, the team at the Langley Research Center decided to build cooling shrouds on each of the motors through which the compressed air must circulate.
Like many desktop 3D printers, the TAZ 4 uses several printed components. Since they are ABS, they would quickly break down in a chamber designed to support PEEK. They were printed from PC, but even this material was not resistant enough for permanent use. In classic RepRap tradition, the team printed the last, third set of components on their most modified printer, in PEI plastic, commercially named Ultem.
Surprisingly, the team had no trouble changing the printer's nozzle to one that could extrude plastic at 400°C. The popular E3D-v6 extruder costs less than $100 and has been shown to be able to maintain this temperature. True, the team had to replace the thermistor with a better one, as well as edit the Marlin firmware so that it allowed it to reach high temperatures. For conventional printers, too high a temperature should cause an emergency shutdown.
Printing results from Ultem 1010 plastic on a remanufactured LulzBot TAZ 4.
In the end, the NASA report indicated that the redesign of the LulzBot TAZ 4 was a complete success. They noted that an attempt to print PEI with infrared lamps turned off ended in failure - delamination and distortion of the model, which was to be expected. They did not specify the cost of the conversion, but given that at that time the TAZ 4 cost $2200, the entire project could cost 10 times cheaper than similar commercial proposals.
Starting from zero
A NASA experiment has shown that an existing desktop 3D printer can be converted to print with high-temperature engineering plastics, and quite inexpensively. But hardly anyone believes that this approach is the ideal solution. There are too many repetitive operations involved here, and NASA engineers had to abandon some of the decisions made by the LulzBot developers. Still, the experiment provided a valuable baseline for other projects built from scratch.
In September 2020, a team from Michigan Technological University demonstrated the Cerberus, an open-source, high-temperature 3D printer capable of creating objects from PEI and PEKK that costs as little as $1,000 to build. Without trying to adapt existing designs, the team started development from scratch, aiming for high temperature printing. All electronics are housed separately from the sealed chamber, which uses a kilowatt heating element to quickly raise the temperature in the chamber to operating temperature.
All stepper motors are also outside the chamber. Because of this, the kinematics become more complex than in desktop 3D printers, but Cerberus no longer requires a special motor cooling system.
Building a Cerberus is quite affordable for the aspiring hobbyist. It has a simplified circuit, ready-made control electronics based on the Arduino Mega 2560 and RAMPS 1.4, and the same E3D-v6 extruder as the TAZ 4. In addition, the team posted clear and detailed instructions for assembling the printer - this is not in the NASA report. meet.
Expanding possibilities
Whether it's NASA's redesign of the TAZ 4, or the new Cerberus-type circuits, it's clear that the technical capabilities of PEI and PEEK printing in the home workshop are already available for those who really need them. So far, it's not as easy as buying a $200 3D printer on Amazon, but if there is demand, cheaper machines based on the same principles will appear on the market. The situation is not much different from the current wave of affordable laser cutters hitting the markets in the past few years.
Fans all over the world print PPE
Is there a demand for such machines? A year ago, the answer might have been different from today. But in the fight against the coronavirus pandemic, there is a new demand for the rapid production of personal protective equipment (PPE) that no one could have foreseen.
print PPE that can be sterilized at high temperatures. The team believes that masks printed from PEKK can be reused rather than thrown away.
Components that can be printed and re-sterilized will obviously have other potential medical applications. A portable, low-cost machine capable of producing such components has the potential to save lives in places on the planet where supplies and equipment cannot be quickly accessed.