3D printer capable of printing metal
Eiger 3D Printing Software | Markforged
Skip to navigation
Eiger™
A leading digital manufacturing software for driving business transformation.
Try It Yourself
Produce parts on-demand and at the point of need with the first connected, secure additive manufacturing platform.
Simulation takes the guesswork out of 3D printing
Try SimulationFrom design to part — easily and quickly
Eiger is an integrated, connected platform designed to take you from CAD to functional part quickly. The browser-based 3D printing software workflows are secure, fast, and intuitive.
Try It Yourself
Print with fibers, composites, and metals
Eiger, our 3D printing software, enables you to slice and print composite parts reinforced with continuous fibers and metals. You can prep parts for printing with a single click, or drill deeply into part settings to optimize your final product.
Interact seamlessly with printers
Eiger software fully integrates with all Markforged 3D printers, enabling you to create builds, print parts, and monitor prints in a seamless workflow.
Customize support placement
Eiger makes it easy to automatically generate supports that are optimized for most parts. Using Support Overrides, you can choose where to place supports to avoid internal channels, small overhangs, or threading or to provide extra support.
Try It Yourself
Validate part strength and optimize print parameters with Simulation
Incorporating 3D printing into tooling and end use applications requires total confidence in part strength. Traditionally, this required lengthy design-print-break testing cycles or costly analysis software. Simulation takes the guesswork out of 3D printing by integrating virtual testing and time/cost optimization into our familiar slice and print workflow.
Store and access parts effortlessly
A secure part library enables you to dynamically manage engineering projects of any size — complete with versioning. Eiger part files are securely stored and can be versioned, edited, and printed anywhere.
Try It Yourself
Manage projects with simple organizational features
Organize and bucket your parts in an intuitive, simple way with folders. Organize parts and projects alphabetically, by create date, or by edit date.
Find the right part every time
Easy-to-use filters sort parts by part name, material, or user — enabling you to quickly find the part you need when you need it.
Drive fleet wide success with real time monitoring
A single place to manage your printer fleet in real time, whether in one spot or worldwide. Benefit from automatic updates while getting analytics, usage data, and live telemetry in a single place.
Try It Yourself
Monitor devices in real time
Eiger empowers you to monitor any connected device in your organization from anywhere in the world. Get real time updates on critical project progress as it happens.
Customer success, built in
Eiger 3D printing software updates automatically push to your organization, unlocking new features and continuously improving printer performance. Support is fully integrated into the software experience and is directly accessible from both part and printer pages.
Eiger Core
Designed to take you and your teams from CAD to strong, functional parts quickly that can be shared and iterated.
Try Eiger
Eiger Fleet
Designed to scale your additive manufacturing operations through centralized control over printers, users, parts, and workflows.
Learn More
Offline Eiger
Designed to take you from CAD to strong, functional parts quickly when Internet access is intermittent or restricted.
Learn More
Learn about online and offline software operations in Eiger Deployment Options and Data Security
Learn the basics of 3D printing software in From Art to Part: A Step-by-Step Guide to 3D Printing
Blacksmith — Trust your parts off your print bed with in-process quality control
Markforged’s revolutionary software Blacksmith enhances part quality and provides both real time and documented part inspection, verifying that the part you printed is the right part for the job.
Learn More
Collaborative and Scalable
Share parts across teams. Kick-off and monitor prints from anywhere on a secure, connected infrastructure.
Day One Productivity
Turnkey for any skill level and feature-rich when you need it. It’s powerful — not complicated.
Constantly Improving
Automatic software updates continually make your hardware and parts better over time. We are always adding new features and enhancing existing ones.
Security built into your workflow
Our software’s security model, world-scale infrastructure, and unique capability to innovate will help keep your organization secure and compliant.
Already a Markforged Customer?
Talk to an expert Request a demo Try the softwareLet’s get started.
Contact Us
Contact Us
- English
Thank you for visiting!
Based on your browser settings it looks like you may prefer to view this page in German, would you like to switch languages?
- Deutsch
Thank you for visiting!
Based on your browser settings it looks like you may prefer to view this page in German, would you like to switch languages?
- Español
Thank you for visiting!
Based on your browser settings it looks like you may prefer to view this page in German, would you like to switch languages?
- Français
Thank you for visiting!
Based on your browser settings it looks like you may prefer to view this page in German, would you like to switch languages?
- Italiano
Thank you for visiting!
Based on your browser settings it looks like you may prefer to view this page in German, would you like to switch languages?
- 日本語
Thank you for visiting!
Based on your browser settings it looks like you may prefer to view this page in German, would you like to switch languages?
- 한국어(대한민국)
Thank you for visiting!
Based on your browser settings it looks like you may prefer to view this page in German, would you like to switch languages?
How metal 3D printers work.
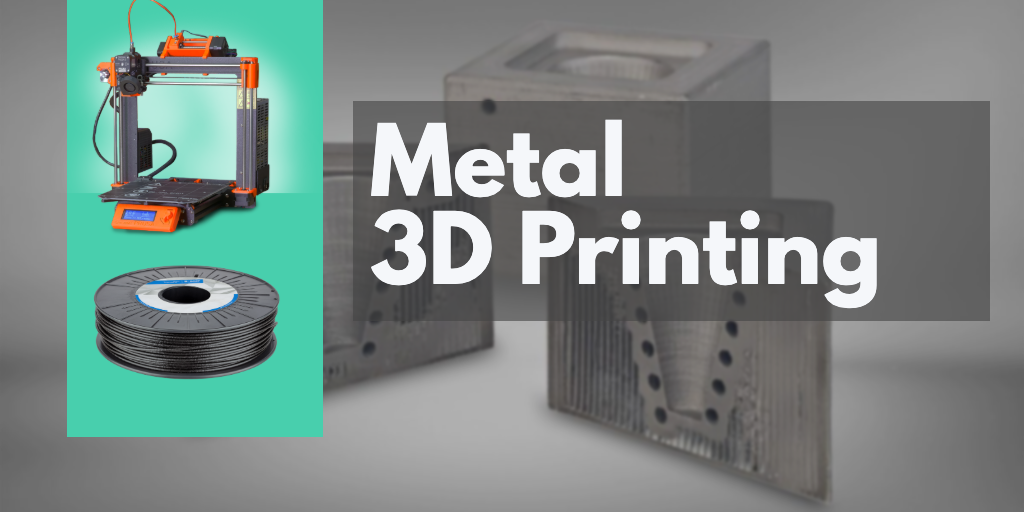
Metal 3D printing. Additive technologies.
SLM or DMLS: what's the difference?
Hello everyone, Friends! 3DTool is with you!
BLT metal 3D printer catalog
Selective laser melting ( SLM ) and direct metal laser sintering ( DMLS ) are two additive manufacturing processes that belong to the family of 3D printing using the powder layer method. The two technologies have much in common: they both use a laser to selectively melt (or melt) metal powder particles, bonding them together and creating a pattern layer by layer. In addition, the materials used in both processes are metals in granular form.
The differences between SLM and DMLS come down to the basics of the particle bonding process: SLM uses metal powders with a single melting point and completely melts the particles, while in DMLS the powder consists of materials with variable melting points.
Specifically:
SLM produces single metal parts while DMLS produces metal alloy parts.
Both SLM and DMLS technologies are used in industry to create final engineering products. In this article, we will use the term "metal 3D printing" to summarize the 2 technologies. We will also describe the main mechanisms of the manufacturing process that are necessary for engineers to understand the advantages and disadvantages of these technologies.
There are other manufacturing processes for producing dense metal parts, such as electron beam melting (EBM) and ultrasonic additive manufacturing (UAM). Their availability and distribution is rather limited, so they will not be presented in this article.
How 3D printing with SLM or DMLS metal works.
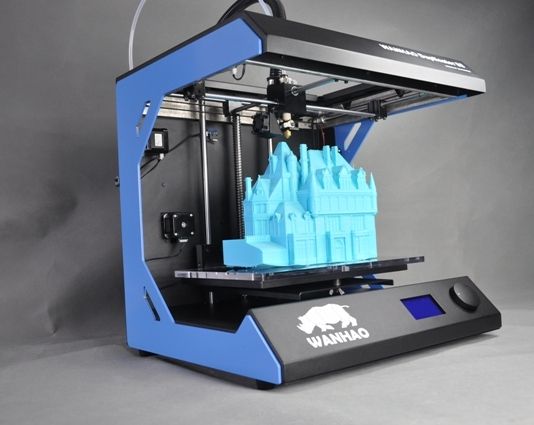
How does metal 3D printing work? The basic manufacturing process for SLM and DMLS is very similar.
1. The printing chamber is first filled with an inert gas (such as argon) to minimize the oxidation of the metal powder. It then heats up to the optimum operating temperature.
2. A layer of powder is spread over the platform, a powerful laser makes passes along a predetermined path in the program, fusing the metal particles together and creating the next layer.
3. When the sintering process is completed, the platform moves down 1 layer. Next, another thin layer of metal powder is applied. The process is repeated until the entire model is printed.
When the printing process is completed, the metal powder already has strong bonds in the structure. Unlike the SLS process, parts are attached to the platform via support structures. The support in metal 3D printing is created from the same material as the base part. This condition is necessary to reduce deformations that may occur due to high processing temperatures.
When the 3D printer's chamber cools down to room temperature, excess powder is removed manually, such as with a brush. The parts are then typically heat treated while they are still attached to the platform. This is done to relieve any residual stresses. They can then be further processed. The removal of the part from the platform occurs by means of sawing.
Scheme of operation of a 3D printer for metal.
In SLM and DMLS, almost all process parameters are set by the manufacturer. The layer height used in metal 3D printing varies from 20 to 50 microns and depends on the properties of the metal powder (fluidity, particle size distribution, shape, etc. ).
The basic size of the print area on metal 3D printers is 200 x 150 x 150 mm, but there are also larger sizes of the working area. Printing accuracy is from 50 - 100 microns. As of 2020, metal 3D printers start at $150,000. For example, our company offers 3D metal printers from BLT.
metal 3D printers can be used for small batch production, but the 3D printing capabilities of such systems are more like those of mass production on FDM or SLA machines.
The metal powder in SLM and DMLS is recyclable: typically less than 5% is consumed. After each impression, the unused powder is collected and sieved, and then topped up with fresh material to the level required for the next production.
Waste in metal printing, are supports (support structures, without which it will not be possible to achieve a successful result). With too much support on the manufactured parts, the cost of the entire production will increase accordingly.
Adhesion between coats.
3D metal printing on BLT 3D printers
SLM and DMLS metal parts have almost isotropic mechanical and thermal properties. They are hard and have very little internal porosity (less than 0.2% in 3D printed condition and virtually non-existent after processing).
Metal printed parts have higher strength and hardness and are often more flexible than traditionally made parts. However, such metal becomes “tired” faster.
3D model support structure and part orientation on the work platform.
Support structures are always required when printing with metal, due to the very high processing temperatures. They are usually built using a lattice pattern.
Supports in metal 3D printing perform 3 functions:
• They form the basis for creating the first layer of the part.
• They secure the part to the platform and prevent it from deforming.
• They act as a heat sink, removing heat from the model.
Parts are often oriented at an angle. However, this will increase the amount of support required, the printing time, and ultimately the overall cost.
Deformation can also be minimized with laser sintering templates. This strategy prevents the accumulation of residual stresses in any particular direction and adds a characteristic surface texture to the part.
Since the cost of metal printing is very high, software simulations are often used to predict how a part will behave during processing. These topology optimization algorithms are otherwise used not only to increase mechanical performance and create lightweight parts, but also to minimize the need for supports and the likelihood of part distortion.
Hollow sections and lightweight structures.
An example of printing on a BLT 3D printer
Unlike polymer powder melt processes such as SLS, large hollow sections are not typically used in metal printing as the support would be very difficult to remove, if at all possible.
For internal channels larger than Ø 8 mm, it is recommended to use diamond or teardrop cross-sections instead of round ones, as they do not require support. More detailed recommendations on the design of SLM and DMLS can be found in other articles on this topic.
As an alternative to hollow sections, parts can be made with sheath and cores, which in turn are machined using different laser power and pass speeds, resulting in different material properties. The use of sheath and cores is very useful when making parts with a large solid section, as it greatly reduces printing time and reduces the chance of warping.
The use of a lattice structure is a common strategy in metal 3D printing to reduce part weight. Topology optimization algorithms can also help design organic lightweight shapes.
Consumables for 3D metal printing.
SLM and DMLS technologies can produce parts from a wide range of metals and metal alloys, including aluminum, stainless steel, titanium, cobalt, chromium and inconel. These materials meet the needs of most industrial applications, from aerospace to medical applications. Precious metals such as gold, platinum, palladium and silver can also be processed, but their use is of a minor nature and is mainly limited to jewelry making.
The cost of metal powder is very high. For example, a kilogram of 316 stainless steel powder costs approximately $350-$450. For this reason, minimizing part volume and the need for supports is key to maintaining optimal manufacturing cost.
The main advantage of metal 3D printing is its compatibility with high-strength materials such as nickel or cobalt-chromium superalloys, which are very difficult to machine with traditional methods. Significant cost and time savings can be achieved by using metal 3D printing to create a near-clean shape part. Subsequently, such a part can be processed to a very high surface quality.
Metal post-processing.
Various post methods. treatments are used to improve the mechanical properties, accuracy and appearance of metal printed products.
Mandatory post-processing steps include the removal of loose powder and support structures, while heat treatment (heat annealing) is typically used to relieve residual stresses and improve the mechanical properties of the part.
CNC machining can be used for critical features (such as holes or threads). Sandblasting, plating, polishing, and micro-machining can improve the surface quality and fatigue strength of a metal printed part.
Advantages and disadvantages of metal 3D printing.
Pros:
1. Metal 3D printing can be used to make complex custom parts, with geometries that traditional manufacturing methods cannot provide.
2. Metal 3D printed parts can be optimized to increase their performance with minimal weight.
3. Metal 3D printed parts have excellent physical properties, metal 3D printers can print a wide range of metals and alloys. Includes difficult-to-machine materials and metal superalloys.
Cons:
1. Manufacturing costs associated with metal 3D printing are high. The cost of consumables is from $ 500 per 1 kg.
2. The size of the working area in metal 3D printers is limited.
Conclusions.
• Metal 3D printing is most suitable for complex, one-piece parts that are difficult or very expensive to manufacture using traditional methods, such as CNC.
• Reducing the need for building supports, will significantly reduce the cost of printing with metal.
• 3D printed metal parts have excellent mechanical properties and can be made from a wide range of engineering materials, including superalloys.
And that's all we have! We hope the article was useful to you.
Catalog of 3D printers for metal BLT
You can purchase metal 3d printers, as well as any other 3d printers and CNC machines, by contacting us:
• By email: Sales@3dtool. ru
• By phone: 8(800)775-86-69
• Or on our website: http://3dtool.ru
Also, don't forget to subscribe to our YouTube channel:
Subscribe to our groups in social networks:
In contact with
how metal printing works on a 3D printer
Contents:
- Metal printing on a 3D printer
- How 3D technologies work
- Two main methods
- Video
Metal printing on a 3D printer (two main technologies)
The introduction of innovative technologies opens up new opportunities in various fields of human activity. A modern 3D printer for printing on metal allows you to print high-precision structural elements that are in demand in the space, engineering, and aviation industries.
How 3D technology works
3D parts are produced using different metal powder melting methods (using a laser). But the basic principle of operation remains unchanged, so any 3D printer prints with metal in several stages, these are:
- filling the build chamber with an inert gas to minimize the oxidation of the starting material;
- heating to the temperature required for the production process.
- distribution of powder over the surface of the build platform;
- 3D scanning of the cross section of the starting material with a laser beam;
- melting and sintering of particles, which makes it possible to obtain a hard layer;
- offset of the platform by the amount of the resulting layer for applying the next one (until the object is formed).
The moment the metal laser 3D printer completes the process, the product is completely covered in powder. Therefore, until the chamber cools down completely (to avoid deformations), the object on the platform is fixed by the support area.
Two main methods
A modern metal 3D printer can use one of the two most common technologies - selective laser beam melting (SLM) or direct laser sintering (DMLS). Among the main differences between the methods, the principle of gluing the component should be mentioned:
- SLM - occurs as a result of complete melting of the powder;
- DMLS - individual particles are sintered (at lower temperatures compared to SLM) without passing into a liquid substance.
Learn more