Heat tower 3d printer
How to Use a Temperature Tower for 3D Printing – Clever Creations
Improper nozzle temperatures on your 3D printer can lead to a variety of problems. Oozing and stringing filament on your 3D printed models are some of the most noticeable. Similarly, you might run into your extruder skipping steps randomly when trying out a new filament.
So, how do you figure out the optimal temperature for your 3D printing filaments? The answer is a temperature tower. It is an easy 3D print that can help you accurately figure out the perfect printing temperature for each of your filaments.
Let’s see how you can use a temperature tower to optimize your print settings and get perfect-looking 3D prints.
What is a Temperature Tower?
A temperature tower is a vertical structure that consists of multiple horizontal slabs. Each slab is 3D printed with a different temperature. This way, you can quickly pinpoint the temperature that gives you the best result with a specific filament. You can even use these towers to fine-tune your bridging and retraction settings.
Image: krpavlu via Thingiverse
Temperature towers for PLA and ABSTypically, the temperature decreases in descending order from the bottom to the top. For example, if the bottom slab has a temperature of 240°C, the second slab will have a reading of 235°C, the third will have 230°C, and so on.
That way, if your nozzle stops extruding due to low temperatures, this happens at the top of the temperature tower instead of at the bottom and does not ruin your temp tower.
Why use a temperature tower in 3D printing?
A temp tower lets you evaluate the performance of a particular filament at different printing temperatures. By looking at the final 3D printed temperature tower, it is easy to figure out at which temperature you get optimal results.
Temp towers help eliminate any defects that might be caused by sub-optimal printing temperatures. For example, low printing temperatures are the most common issue behind under extrusion on fused deposition modeling (FDM) 3D printers. On the other hand, if the printing temperature for a specific filament is too high, you will notice a lot of oozing of filament and stringing during the 3D printing process.
Stringing can be a particularly stubborn problem with PETG, which is why we have an entire article on dealing with PETG stringing.
Image: gaaZolee via Thingiverse
Temperature towers test a variety of 3D print featuresIf you plan on selling your 3D prints and making money with your 3D printer, producing high-quality prints without visual defects is a big key to your success.
When should you print a temp tower?
The best time to print a temperature tower is when you change filaments and when you’re altering any crucial components of your 3D printer.
Each filament manufacturer uses a slightly different blend of materials to produce the filaments. PLA filament from manufacturer A may give you optimal results at 190°C, and PLA from manufacturer B might print beautifully at 215°C, despite being the same material.
Even if you have perfectly dialed in your PLA filament print settings and made sure to only use the best PLA filament brands, you can get a completely different result when swapping to a different brand of filament.
At the same time, changing any component of your 3D printer, such as the hot end, cooling fan, cooling fan shroud, or even the heater cartridge directly affects the results with the extruded filament. Printing a temp tower helps you evaluate the effects of these changes on the extruded material and allows you to dial in your temperature and print settings for your filaments.
Image: s1ckopsycho via Reddit
Definitely use a temperature tower when your 3D prints look like thisHow to print a temperature tower?
Temp towers are quick and easy to 3D print. Let’s find out how you can print one for yourself.
1. Get a temperature tower model
There are many free temp towers available for download on Thingiverse and other Thingiverse alternatives. Some are filament-specific temp towers, some are extra quick and easy to 3D print, whereas others have bridging and retractions tests built-in.
Image: Toster256 via Thingiverse
Temperature towers come in a variety of shapes and sizesThere’s no single best temperature towel model, but if we were to choose one for you to start with, it would be the smart compact temperature calibration tower by gaaZolee. There are temp towers with temperature ranges for PLA, PETG, and ABS. Along with finding optimal temperatures, you can test bridging, stringing overhangs, and even curvy shapes with these.
2. Set up slicer settings and generate GCode
Printing the temperature tower without preparing it in the slicer will cause it to 3D print at a constant temperature. Therefore, the basic procedure for preparing the temp tower for 3D printing involves post-processing the GCode file. Let’s take a look at how to set up the gaaZolee’s temperature tower for printing in three different slicers.
Cura
In Cura, once you slice the temp tower, you’ll have to modify the G-code in post-processing.
In the menu bar, select Extensions→Post Processing→Modify the Gcode. Then select the “Change at Z” option. This will let you set different temperatures for different heights of the temp tower.
Image: Pranav Gharge
Depending upon the temp tower, you set the trigger height and the temperature for that particular height. For gaaZolee’s PLA temp tower, you’ll have to slice the model at a 0.2 mm layer height with 225°C as the initial temperature (This will be the same in all the slicers mentioned).
Then accounting for the 1.4 mm base and a 10 mm floor height, you’ll set the first trigger at 11.4 mm and the extruder temperature to 220°C. Like this, set the rest of the triggers at 10 mm height intervals and decrease the nozzle temperature by 5°C for each trigger. Slice the model and export the file for 3D printing.
PrusaSlicer
Modifying GCode in PrusaSlicer is slightly easier than Cura. Before slicing the tower in PrusaSlicer, in the Gcode preview, you’ll see a layer height ruler at the right side of the preview window. We’ll use this ruler to navigate and select the various layer heights of the temp tower.
Image: Pranav Gharge
For the first temp change, slide the ruler to 11.4 mm height. Right-click on the ‘+’ symbol and select the ‘Add custom GCode” option. In the pop-up window, type the G-code M104 S220. The ‘M104’ will trigger the temperature change command at the set layer height, and the ‘S220’ part of the G-code will set the temperature to 220°C.
Do this at every height interval of 10 mm. Each time set the temp 5°C less than the previous trigger and reslice the model, and you’re ready to 3D print it.
Simplify3D
Simplify3D makes it slightly easier to set the temperature change. Under the Temperature section, select ‘Primary Extruder Temperature.’ Add setpoints denoting the various layer numbers.
In this case, the first set point for the 1st layer and the temp will be 225°C. The second point will be at layer number 57 (0.2 mm layer height and total 11.4 mm height of the first floor), and the temp will be 220°C.
After that, every other set point will be at successive intervals of 50 layers, i.e., the next setpoints will be at 107, 157, 207, and so on. And each time, the temperature will decrease by 5°C. Once you’ve done this, slice the tower and 3D print it.
How to read the results?
After 3D printing the temp tower, it is crucial to interpret the results. The most basic method is to visually inspect the tower and evaluate which temperature setting gives the best-looking results. Check for defects, retraction issues, bridging results, blobs, stringing, and other visual cues.
Then, to check the layer adhesion, try to separate the layers by hand. This lets you know the temperature at which the layers bond to each other strongly. You’ll notice that layers at lower temperatures do not stick to each other well, as the heat is not enough to melt and bind these layers together.
Filaments from brands such as Overture, Hatchbox, Esun, and especially Prusaments are some of the best materials you can use if you’re struggling to get good quality results due to poor material.
Recommended:
The 10 Best PLA Filaments for 3D Printing
Once you’ve evaluated the results, make sure to document them for future purposes. This allows you to look up the optimal temperature settings the next time you print with the same spool.
Conclusion
Temperature towers are a great way to save yourself time and figure out the best 3D printing temperatures for a particular filament. They take out any guesswork, and you can be confident of the results and expect the best printing quality each time from your favorite material.
Let us know your results and experiences with these temp towers. If you have any additional questions or would like to add something, feel free to comment below.
How To Use A 3D Print Temperature Tower « Fabbaloo
A 3D printed temperature tower [Source: Fabbaloo]
One of the key techniques that should be used by 3D printer operators is the “Temperature Tower”.
It’s an essential tool for using and optimizing print settings for filament-based 3D printers. This technique works only for filament devices, and is of no use for resin printers, for example.
When you receive a spool of filament the manufacturer will often paste a sticker on the side with recommended nozzle temperatures. This is quite a tricky thing to declare by the manufacturer, because in an open materials world they have literally no idea what type of 3D printer it will be used on. The chemistry of the filament needs to be matched to the thermal properties of the specific 3D printer.
Thus the print temperature recommendations are often a range. For example, I’m looking at some handy spools here and they say things like:
-
Print temperature: 255-270C
-
Range can be 220-235C
-
Nozzle temperature 205-225C
-
Print temp: 205-225C
Sometimes you don’t even get that.
The bottom line here is that basically you have no idea what the optimum temperature will be for a given combination of filament and printer, unless you’ve done some testing.
That’s often the first thing I do when I encounter a foreign spool: perform some test prints within the recommended range to identify which level is best. Sometimes it’s right in the middle, but not very often. Recently I even had one material that would only print outside of the recommended range!
But that’s the exception. Nevertheless, you should always perform a simple experiment with your material to understand exactly how it performs with your specific 3D printer configuration.
I’ve found the best way to do this is through what’s called a “temperature tower”. It is a curious structure that looks somewhat like a small open-air apartment block, with multiple levels.
The idea is to 3D print the entire tower, but vary the temperature on each “floor”. That way you can very easily visually compare the print results between the two temperatures.
How exactly do you configure a 3D print job to do this? Most slicing systems offer a way to change print parameters at specified layers. I can’t get into the details here as it depends on which slicing system you use. It is sometimes a bit tedious, but usually you have to do it once for reasons that will become clear later.
Once configured, the 3D printer will simply adjust temperatures as it encounters the designated layers accordingly.
Normally the highest temperature is to be tested first, so it will be set at the lowest level. Then, as the layers proceed upwards, the temperature will drop, typically by 5C.
Why go from hot to cold? The answer is simple: at some lower temperature the material will cease to flow, and printing will jam. That doesn’t happen at hotter temperatures; the print just gets sloppy.
I’ve encountered this effect several times where a temperature tower print actually fails before it gets to the top. Then you know for sure where the softening temperature is located.
Well-designed filament chemistries will offer a wide range of printable temperatures, so you will sometimes encounter a material that varies very little between temperatures.
More frequently, however, you will see differences in the print quality from layer to layer. Most temperature tower designs offer some basic geometry that you can compare between layers. Look for slumping overhangs, poor bridging, ringing (wobbly echoes near corners), blobs and other print artifacts. If you look closely you will usually see some difference.
Another factor that changes by temperature is the surface quality. Some materials, particularly the “silk” style materials and PETG, offer more or less shine depending on the set temperature.
Pick the temperature that offers the best combination of look and function.
There are plenty of temperature tower 3D models available on public repositories. For example, as of this writing there seem to be over 50 designs on Thingiverse.
But there is a problem. When you examine the printed tower you may see a particular level is optimal, but then you might not recall what temperature was used for that level. Was it 210C or 215C? Sometimes you have to refer back to your slicing profile to figure it out.
But there is an easier way! There are extremely useful temperature tower 3D models that are customizable. These are 3D models that can be generated to have as many levels as you wish — and even label each layer with the temperature! How handy can that be!
One design I’ve tried is the “Customizable Better Temperature Tower” by Thingiverse contributor KM SD.
It may seem tricky to use one of these, but actually it’s quite straightforward. Rather than providing a static 3D model, which cannot be changed, KM SD provides an OpenSCAD script.
OpenSCAD is a free tool to generate 3D shapes from command line — code. Its tagline is “The Programmers Solid 3D CAD Modeller”.
Now, before you freak out, you don’t have to know any software coding before trying this. It’s incredibly simple. First, download a copy of OpenSCAD for your platform. It’s available in Windows, Mac OS and Linux.
View of OpenSCAD code generating a temperature tower [Source: Fabbaloo]
Open OpenSCAD and then open the script from Thingiverse. You’ll see some code on the left, as seen in this image, and a rendering of what it generates on the right.
Now, this is the trickiest part: simply adjust the start and stop temperatures in the code by typing over top of the existing values, which by default are 210-280C. Probably you want different temperatures, so just replace these two numbers:
Only two parameters to change to generate a different temperature tower 3D model [Source: Fabbaloo]
Then hit the render button (“>>”) and you should see and updated tower with your specifications. Hit the “STL” button to download this 3D model and you’re all set to configure your temperature tower 3D print job.
Here’s the best part: once you have a 3D print job configured for a particular temperature range, keep it. Whenever you get a new filament, just print that same job and you’ll get a tower printed with the temperature ranges for inspection.
If you’re not using temperature towers, you should be.
Ten models for 3D printer calibration.
top sellers
-
Bearing 604UU U604ZZ
U-bearing U604ZZ 604UU 4*13*4
35.00 UAH
-
Thermal mat for 3D printing 200 x 200 mm
3D printing thermal pad
150.00 UAH
-
Buy epo3d+ 3D printer
Epo3d+ Ukrainian FDM 3D printer on HIWIN rails. Thanks to reliable...
UAH 35,000.00
-
ABS granules
ABS granules for extrusion
400.
00 UAH
-
PLA
PLA environmental plastic from Plexiwire. 100% advance payment....
UAH 375.00
-
Buy ABS plastic (ABS)
ABS plastic from Plexiwire. 100% prepayment. Free shipping...
UAH 220.00
-
Mini motor reducer 12v 100 rpm
high torque mini electric motor. Its size...
150.00 UAH
-
Nozzle for 3D printer 1.
75 mm, for E3D and MK8 hotends
3D printer nozzle 1.75 mm 0.2/0.3/0.4/0.5
35.00 UAH
-
PETG plastic for 3D printer
PETG plastic from Plexiwire. 100% prepayment. Free...
UAH 360.00
-
SHF-20 shaft support
SHF-20 shaft support is used for CNC
60.00 UAH
-
A4988 stepper motor driver
35.00 UAH
-
Buy epo3d 3D printer
Ukrainian epo3d 3D printer built on the basis of modern kinematics.
..
UAH 18,000.00
All best sellers
Information
Ten models for 3D printer calibration.
After reading the all3dp.com article "3D Printer Test Print - Top 10 Models to Test Your 3D Printer", the epo3d team decided to test all the models and print them for you.
1. 3D Benchy
3D Benchy is the flagship of all 3D printer tests. This boat model checks everything from protrusions to extrusion. If you want to put your 3D printer to the test, the benchmark will help you determine the settings for the ideal job. Nearly 3000 Thingiverse users have submitted their samples, Benchy has been printed with hundreds of machines and materials.
Printed with plastic:PLA.
https://www.thingiverse.com/thing:763622
https://www.thingiverse.com/thing:763622
All-in-one 3D printer test - the name says it all! Canopies, bridges, string, extrusion, temperature, belt tension - this model tests everything.

Printed with ABS plastic.
https://www.thingiverse.com/thing:2656594/makes
3. Calibration cube 20 mm XYZ
This cube is a simple, fast and easy model for testing. Its main purpose is to help dial in the dimension of a 3D printer by customizing its steps in millimeters. But also temperature, extrusion and vibration can be tested. On Thingiverse, it has been printed with countless machines and materials.
Printed with ABS plastic.
https://www.thingiverse.com/thing:1278865
, extrusion and vibration within an hour! Designed for initial calibration, this cat will set up your 3D printer in no time. Over 250 users have posted their examples.
Plastic printed: Elastan D160.
https://www.thingiverse.com/thing:1545913
5. MatterHackers Mascot Phil A. Ment
Phil A. Ment is an adorable MatterHackers mascot for manufacturers. According to the company's description, "Phil has several features specifically designed for the 3D printer. Its features include fine insert details, small relief details, ridges, vertical and horizontal cylinders, fillets, chamfers, bridges, and even a domed helmet." 84 drawings were published on Thingiverse. PhilA, his record size is 5.1397 mm!
Printed with plastic: CoPet.
https://www.thingiverse.com/thing:2557603
plastic.
Plastic printed: Nylon.
7. New test from Autodesk
Andreas Bastian has developed a test procedure to help 3D printer manufacturers better calibrate their machines and demonstrate the capabilities of printers to Kickstarter supporters. A single consolidated STL file verifies the precision, resolution, and size alignment of the printer. For example, poor performance of the "bridge" function shown below will result in a loose and stiff print. A well-tuned printer will do the horizontal function with fewer problems.
printed with plastic: PLA
https://github.com/kickstarter/kickstarter-autodesk-3d
8. Polyperal Tower
,0008 tutes Polypearl, Crown, Crown, Crown, Crown, Crown and much more, described as a torture tower with a twist, it will help you calibrate your 3D printer settings.Printed with plastic: ABS.
https://www.thingiverse.com/thing:2064029
9. Ultra-fast and economical screening test
Provides an ultra-fast way to check the temperature, cooling and retraction of your 3D printer. Weighs about 0.23g, and can immediately remove the so-called "strings"!
Printed with plastic: PETG.
https://www.thingiverse.com/thing:2219103
10. Table Calibration Object (Parametric)
Lowering the table is often the most difficult part of printer calibration. This model will help you understand how to improve the first layer for better prints.
https://www.thingiverse.com/thing:34558
(There is a solution) How to use the heat tower?
When you cut the STL of a thermal tower, you need to tell the cutter that you need a different temperature at a certain level , and maintain this new temperature until another change is requested.
I usually do this with using the Ulltimaker Cura post-processing script, but you can easily do this by yourself by manually modifying the G-code file .
To make it work in Ultimaker Cura, you need:
Extensions -> Postprocessing ->> Edit G-code>>
, Add scenario
and select Change
, trigger
) with which you can change parameters either at a specific height
or at a
specific layer number.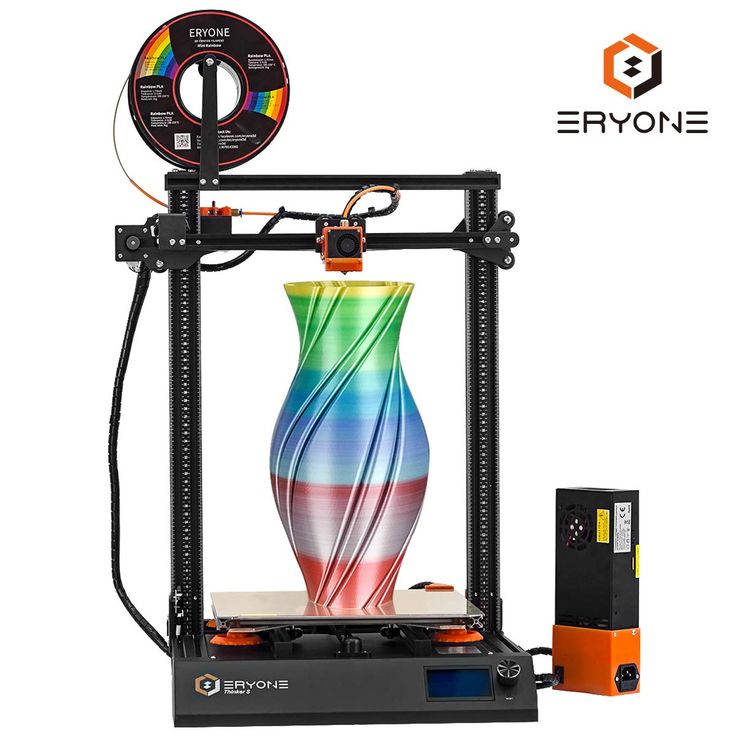
Change altitude
, Change extruder temperature 1
(make sure the behavior of the
box is set to keep the value
so that it will keep this value until you specify otherwise, otherwise it only affects one layer) , ,
until you specify all temperatures for all levels If you look at the generated G-code file (the snippet below is taken from the Ultimaker 3 G-code screen) you will see that after processing the script, additional lines will be added to the G-code file. For example. the following snippet shows 2 temperature changes, one for 5mm (extruder 1 @ 250°C) and another for 10mm (extruder 1 @ 245°C):
... ;LAYER:48 G0 X93.4 Y132.161 Z5 ;ChangeAtZ V5.1.1: executed at 5.00 mm M117 Printing... [email protected] 5.0 M104 S250.000000 T0 ... ... ;LAYER:98 G0 X93.4 Y132.35 Z10 ;ChangeAtZ V5.1.1: executed at 10.00 mm M117 Printing... [email protected] 10.0 M104 S245.000000 T0 ...
The bottom line is that the extruder must be instructed to heat up or cool down to a new temperature. This is also something you could manually insert yourself by adding the codes M104 SXXX.000000 T0
at certain levels, where XXX
is the extruder temperature required for that level.
This basically describes how to print heat tower calibration prints, rather than choosing the settings (such as extruder temperature) to be used for your prints. Once you've created your print file, you're ready to print the tower and monitor print quality.