3D printed shift knob
Weekend Build: 3D Printed and Customized Shift Knob
3D printing custom shift knobs has never been easier thanks to some MatterControl Design Tools. Check out what it takes to make a ready to use shift knob.
Posted on August 2, 2019
by
Alec Richter
For the longest time, I wanted to have a really cool shift knob for my car, and for most of my life, any of the cars I have driven have been automatic and utilize a trigger to disengage and shift gears, which limits my ability to easily swap out the shift knob for something different. I knew manual transmissions would have it easy since usually they’re just screwed onto a threaded shaft. As luck would have it, the car I have now is automatic but doesn’t use a trigger to shift which means I can create whatever knob I want, screw it on, and have that extra bit of flair to my car.
Method 1: One 3D Print, No Hardware
This first method is the easiest to set up, as all it requires is a single extrusion 3D printer and some filament; no hardware at all. To create this one, the first thing I needed to do was create the base shape for the shift knob; it needed to have a base larger than the diameter of the threaded shaft of the shifter and a handle that would fit comfortably in my hand. There are multiple ways you could go about modeling the base piece, but in my case, I wanted to use Fusion360 to get some nice curves to it.
The base used to create the single extrusion knob, modeled in Fusion360.
Once the base was modeled it was time to figure out what design I wanted debossed into it. While I could use the reference canvas tool to bring in a logo, it was actually a lot easier to use MatterControl for this part. I exported the base from Fusion360 and imported it into MatterControl, then started modeling on top of it. A cylinder set to just slightly smaller than the threaded shaft needs to use the Alignment Tool to center it on X and Y and put at the bottom of Z. I want this cylinder to be slightly smaller than the diameter of the shaft so it can tap into the plastic and maintain a good grip on it.
With the Image Converter Design Tool I could turn an image of a flame into an extruded 3D model. Then with the fit-to-bounds I can set some constraints so if I want to go back and change the image, it won’t ruin my settings. some alignment tools, I could center it and extend it into the shift knob. Using the Subtract Tool, I can select the Fit-To-Bounds and subtract it from the main body while maintaining its spacing. Should you have a dual extrusion 3D printer, you can also use Subtract and Replace to have the intersection of the design and the knob be marked as using a different material, so you can dual extrude it.
Image Converter will make it really easy to get back later and swap out this image for something different.
And there we go! A shift knob using a single extrusion 3D printer ready for printing and installing.
Installed and ready to shift into gear.
Method 2: Multiple prints, some hardware
Sourcing the hardware is easy, but determining the threading can be annoying. My first suggestion would be searching online to see what other owners of this car have identified the shifter’s threading, barring that you can also take your shift knob into your local hardware store and see what bolt threads into it properly. In the case of my car, an M8 lock nut was the right fit. Make sure you get a lock nut, otherwise your shift knob will be able to spin too freely.
Much like before, I modeled the base in Fusion360. This base can also be found on Thingiverse as designed by Wills World, but I needed a clean 3D model to embellish with my own designs and to change some of the hole diameters, which is why I remodeled it. Since my personal printer can’t print two materials or colors at once, I couldn’t do a Subtract and Replace like mentioned before; I’d need to do things a little differently. First thing was to create a hole for the nut to sit in, sized just barely larger than the lock nut. It’s better to have this a tight fit and need a vice to press it in rather than loose; a loose nut means your shift knob will have some wiggle to it.
I prefer the appearance of the screws on the face of the knob rather than the simply smooth one.
On the lower half, I made sure the hole was easily larger than the shaft diameter to make sure insertion is easy and on the upper half, this hole will accommodate the shaft as it screws through the nut.
To create the design in this one, I did the same as before: imported the top half of the knob design into MatterControl and used image converter and the align tool to place the design on the face of the knob. Then rather than just subtract the design as I did for the single extrusion method, I can instead use subtract and replace. The difference between the two operations is subtract and replace will subtract a mating chunk from the first part, and then where they were intersecting leave that as a new model, which is perfect for seamless dual extrusion. And now that I have it modeled in MatterControl, I can really get creative. If I want to quickly jump between different images on the knob, all I have to do is change the image and some settings in the image converter and save that as a new version. This way I don’t need to manually retrace a logo every time I want a different one.
A subtracted and replaced design from this shift knob design.
With this specific design, I really wanted to put some nice finish and polish on this 3D print, so I went ahead and sanded it to smooth it out. I first started with some 120 grit to break down most of the layer lines, and then 220 to clean up the deep scratches of 120. I followed up with 400 and 800, using some water to wet sand for a much smoother surface and finished it all up with a couple coats of gloss clear coat.
Sanding the surface to get a smoother finish.
To attach this knob to the post in my car I sandwiched an M8 lock nut inside the two halves of the printer knob.
Channel locks were used to press in the M8 lock nut.
You can even experiment with different finishes on the knobs depending on the material you print. Since this is going to be in a car, which can easily get hot enough to deform PLA in the right conditions, printing in PETG, ABS, Nylon, or annealed Tough PLA is the right choice. For a more textured feel, a dual NylonG print gives a professional appearance, or ABS that’s been sanded smooth and clear coated can make for a great glossy finish that’s hard to tell was even printed.
A NylonX and NylonG shift knob for better grip and a different texture.
And there we go! With either of these designs saved into MatterControl, I can endlessly change the designs to better fit my friend's and families' personalities and interests. There's definitely some things that can be learned here and there, like trying to print at lower layer heights or a smaller nozzle size to get a cleaner print which would just make for a much better finished product. If you make a shift knob for yourself, I'd love to see it!
Happy shifting!
Article Tags
- 3D Printing
- Firmware
- 3D Design
- MatterControl
- Press Releases
- Small Business
- Automotive
- E3D
- Jewelry Making
- Engineering
- Entertainment Industry
- MatterControl Touch
- ESD Materials
- NylonX
- BCN3D
- Open Source
- Crafty Pen
- Digital Fabrication Anatomy
- How To
- Hardware and Upgrades
- Tips and Tricks
- Weekend Builds
- Top Ten
- Education
- Tech Breakdown
- Women in 3D Printing
- Project Ideas
- Advanced Materials
- Reference
- Pulse Dual Extrusion
- Product Spotlight
- Aerospace
- Jobs
- Military & Government
- Multi-Tool Machines
- Getting Started
- Healthcare
- How To Succeed With Any 3D Printing Material
- Creality3D
- Architecture
- 3D Printer Reviews
- Hacker of the Month
Related Products
View all related products▷ shift knob 3d models 【 STLFinder 】
Shift Knob
grabcad
Shift Knob
shift knob
grabcad
shift knob
shift knob
grabcad
shift knob
Shift knob
grabcad
Model of the popular shift knob from Fanatec.
Shift Knob
grabcad
Shift Knob made for fun M10/12 Thread Pattern
Shift Knob
thingiverse
Shift knob, printed this for my dump truck. ... 3/8-24 thread, prints best upside down.
shift knob
thingiverse
it is a shift knob thats 6.5 inches tall Print Settings Printer Brand: Prusa Printer: Prusa Steel Rafts: Yes Supports: Doesn't Matter Resolution: 100 Infill: 80
Shift Knob
thingiverse
This is a Shift knob with M12x 1. 25 thread on the inside for a Toyota Echo. ...The shift knob fits over the shaft of the shifter very tightly and threads on perfectly to ensure a tight fit and great feel.
Shift Knob
thingiverse
The shift knob is based off of a Mishimoto Weighted Shift Knob. The total height is 3.75 in. and the diameter is 1.4 in. ...It is made to fit an Audi a4 but you can drill the hole to the size you need.
Shift Knob
thingiverse
This is a BIG shift knob, 6cm in diameter (about the girth of a water bottle) and nearly 10cm of height. It taps itself as it threads onto your shift lever and doesn't interfere with the reverse lockout switch.
The top is beveled so it can be...
Shift Knob
thingiverse
I wanted a shift knob for my Forester. I made the knob so that I could glue in a nut inside the knob to hold it into place. This makes the knob pretty universal. ...Ive been using this shape for over a month now and im pretty happy with it.
Shift knob
thingiverse
Designed a custom shift knob for all cars that use a 10x1.5 thread pitch. ...I made the threading slightly bigger (around 10.2mm) but it doesn't hurt to chase the threads with a thread tapper to make sure the knob screws on smoothly
Shift knob
grabcad
This is a universal shift knob. not the best in details but it works. it does not have treads on the inside of both parts which means you can customize it to fit your shifter. ...can be 3D printed as it was made to scale.
Shift Knob
thingiverse
First thing I've ever made. ...It's a 5 speed shift knob that is slightly over 2.25 inches. The thread hole is 3/8 and I left it treadless so you can use it as a self tapping hole to stop threading where you'd like. ...The holt is 40mm deep.
shift knob
thingiverse
This is a shift knob I designed to be made out of bronze, but it was going to be too heavy. The thread is a M12x1.25 metric thread, It should fit all Subaru manual shifter levers.
It has the Counter bore for the reverse lock-out.
...
shift knob
thingiverse
It's a shift knob that fits M10 thread directly due to conicity of the bore. Eventually it'll come lose, i've added some liquid epoxy glue into the hole and attached. It's rock solid and now has some inner thread. I've made it to replace the...
Shift Knob
pinshape
Summary My shift knob in my 2007 Mazda 3 broke, so instead of just buying a new one I created my own simple one. The picture shown does not have the knob screwed on all the way, it does go all the way down to the boot. I was worried about printing...
Gear shift knob. Gear shift knob. (unmarked)
cults3d
Knob for gear shift lever thread M16x2 Gear shift knob thread M16x2 Adapters M8 - M16 https://cults3d.com/en/3d-model/gadget/adaptador-m8-a-m16-rosca-thread-para-pomo-knob M10 - M16...
Shift Knob Sparco
grabcad
Sparco Shift Knob Piuma
Shift knob Mercedes 190
thingiverse
Shift knob Mercedes
Shift knob sequential
thingiverse
SHIFT KNOB SEQUENTIAL
Manual Trans Shift Knob
cults3d
Manual Trans Shift Knob
shift knob mercedes
thingiverse
Shift knob for mercedes
Gear shift knob
thingiverse
Gear shift knob
Gear shift knob
grabcad
Retro style gear shift knob
Shift Knob Test
grabcad
A test shift knob model.
MR2 Spyder Shift Knob
thingiverse
Shift knob for MR2 Spyder
VW T2 Shift Knob
thingiverse
VW T2 1976 Shift Knob
shift knob fiat punto
thingiverse
Custom design shift knob for Fiat Punto.
Polaris Ranger Shift Knob
thingiverse
2013 Polaris Ranger Midsize Shift Knob
STL File BMW E36 Shift Knob Adapter・3D Printer Design Download・Cults
The best files for 3D printers in the Tools category
Filament clip / Universal filament clip
Free
Raspberry Pi Snug Case
Free
Bookmark
Free
1.
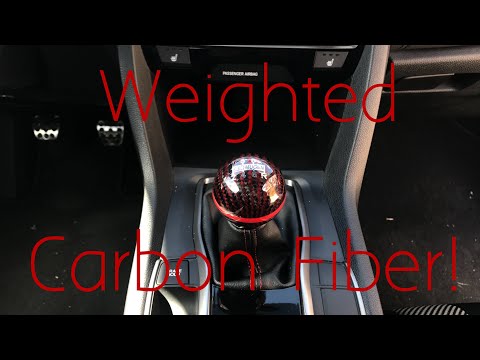
Free
Torture Lattice Cube
Free
Folding Raspberry Pi Case
Free
DSLR Camera FollowSlider V2.0
Free
WoodenMallet cnc
Free
Bestsellers in the Tools category
well designed: Hemera fan duct
2.50 €
Armadillo - flexible wire conduit
1.68 €
telephone ring holder
0,90 €
nine0007 Ender 3 S1 BEST cable guide - vertical €2.50 -25% 1. 88 €
Ender 3 Briss fang Gen2, red lizard, spider, nf crazy, dragonfly, etc.
1.73 €
ARTEMIS -> Shop for Alligator 2 || 6.5" Arrows || Repeating Crossbow
6.25 €
Business card embossing system
3 €
3D printed wave transmission (harmonic drive)
4.99 €
PRECISION CALIPER 3D PRINT DIY
3,13 €
UNIVERSAL BED LEVELING INDICATOR FOR VERY ALL PRINTERS
2.81 €
Bit holder Spartan 4 mm Hex
1,80 €
Ender 3, 3 V2, 3 pro, 3 max, dual 40mm axial fan hot end duct / fang. CR-10, Micro Swiss direct drive and bowden compatible.

1.56 €
PET-Machine, make your own plastic bottle filament at home! nine0008
15 €
ENDER 3 S1/S1 PRO COIL HOLDER AND DEPORTED COIL
€2.13 -twenty% 1.71 €
Phone holder
2.44 €
Ender 3 S1 pro fan duct 5015 4020
1,30 €
nine0002Do you want to support Cults?
Do you like Cults and want to help us continue our journey on our own ? Please note that we are a small team of 3 people, so supporting us in maintaining the activities of and creating future developments of is very simple. Here are 4 solutions available to everyone:
-
ADVERTISING: Disable the AdBlock banner blocker and click on our banner ads. nine0006
-
AFFILIATION: Shop online with our affiliate links here Amazon.
-
DONATIONS: If you want, you can donate via PayPal here.
-
* INVITE FRIENDS: * Invite your friends, discover the platform and great 3D files shared by the community!
Additive technologies at the service of the automotive industry: application of 3D printing
You can't buy a fully 3D printed car at a car dealership yet, but additive technologies have been used in car design for years. Every year, especially in recent years, 3D printing is taking an increasingly important place at all stages of production. This is evidenced by the rapid growth of the 3D printing market share in automotive manufacturing, which is projected to reach $2. 5 billion by 2023. For example, luxury car companies including Bentley, Porsche, BMW and Ferrari are using 3D printing to create custom car interior parts. GM, Volvo, Ford are using 3D printing to produce tooling to save money, improve design and reduce delivery times. 3D printing constantly has new opportunities, it becomes more and more accessible. If the first 3D printers cost about $20,000, now you can find 3D equipment for $100. Now companies can, with the help of additive technologies, produce the necessary components directly at their own enterprises and not depend on suppliers. nine0006
Source 3dprinting.com
New materials on 3D printers can print high-precision, functional final parts. Additive technologies facilitate the production of custom products and increase productivity. But this is only the beginning of the journey. Here are five key ways 3D printing is driving innovation in the automotive industry, from car design to production. Plus one bonus.
1. Changing the Prototyping Process
Prototyping was the beginning of 3D printers in the automotive industry. 3D printed prototypes took much less time than traditional methods required.
Using Raise3D 3D printers and ideaMaker software, Crazy Grandpa Garage was able to automate the process of creating custom car parts. Production costs have been reduced by 50%, design reliability has improved significantly, and lead time has been reduced by 83%. The parts now come out very well fitted to the car. nine0006
Source: facebook.com
Using 3D printing, car designers can quickly create prototypes of individual parts or assemblies, from interior parts to dashboards, or even full-size car models. Thanks to 3D prototyping, the initial idea quickly turns into a physical embodiment of the concept - a conceptual model. The concept can then be developed into full-featured, high-fidelity prototypes, and after several validation steps, mass production begins. For the automotive industry, getting through these steps quickly is vital, and the entire downtime of an automobile production line in just an hour is very costly for the company. nine0006
For example, the assembly plant of American car manufacturer General Motors claims that the purchase of a 3D printer in 2016 saved more than $300,000.
Using Laser Stereolithography (SLA) in their facility, Ringbrothers designers and engineers are independent of third parties. The cost is reduced, the development time is reduced. Source: formlabs.com
Hose for BMW M4 by Eventuri, Source: ultimaker.com
Traditional prototyping was time consuming and costly, in part because the product went through more iterations. With 3D printing, you can create high-quality prototypes in one day and at a much lower cost. More examples.
The Ford Fiesta ST with 3D printed parts, ext. SEMA 2016, ultimaker.com
For example, General Motors has partnered with Autodesk to produce low-cost, lightweight automotive parts using 3D printers. Tools, fixtures and fittings can now be produced at a fraction of the cost, according to Autodesk. For example, a 3D printed tool used to align engine and transmission ID numbers costs less than $3 at General Motors. A traditionally produced instrument will cost $3,000. In addition, downtime due to faulty tools can be significantly reduced as new tools are produced in-house. nine0006
2. Creating custom and complex parts
Daihatsu, the oldest car manufacturer in Japan, launched a project in 2016 to customize its Copen model.
Source: 3dprint.com
In partnership with Stratasys, Daihatsu customers can design and order custom 3D printed panels for their front and rear bumpers, with a choice of over 15 basic patterns in 10 different colors. nine0006
Source: 3dprint.com
In Europe, the BMW MINI brand also uses 3D printing to create personalized car parts. Since the beginning of 2018, MINI customers have been able to personalize various trim elements such as the instrument panel, LED treadplates and illuminated bumpers, as well as choose from different colors and textures. These parts are then 3D printed using a range of technologies from DLS Carbon to SLS.
Source: formlabs.com
Volkswagen Motorsport’s I.D. R Pikes Peak is designed with over 2000 3D printed test parts.
Source amfg.ai
The use of 3D printers makes it possible to experiment in the development of non-standard designs, reduces the cost of their production. Long production processes for custom-made products are becoming much shorter.
Ringbrothers uses 3D printing to create customized end pieces such as ventilation grilles. Source: formlabs.com
Large companies combine 3D printing technologies and traditional production methods. Volkswagen has recreated its iconic 1962 Microbus by replacing the petrol engine with a 120 hp electric one. The Type 20 concept electric minivan has received many improvements using 3D printed parts. These improvements include cast aluminum wheels. Even the wheel hubcaps, while looking like stamped steel, are actually printed on a Formlabs SLA 3D printer, then electroplated and polished. nine0006
Source: formlabs.com
SLA specifications of the Formlabs Form 2 3D printer
Source top3dshop.ru
The Bentley Speed 6 is another example. Bentley has used cutting-edge metal 3D printer technology to produce a grille, side vents, door handles and exhaust pipes much more complex than those used on current production models.
Bentley used metal 3D printing to create intricate micron precision parts. Source: formlabs.com
3D printing has also made it possible to create parts that could not be made in any other way.
Bugatti's monobloc brake caliper is a prime example. For some components, Bugatti would have preferred titanium due to its high performance, but processing this metal with traditional methods is expensive and difficult. 3D printing has allowed Bugatti to produce a titanium alloy brake caliper. Due to the thin walls, the caliper turned out to be very light - almost two times lighter than forged aluminum. At the same time, the strength of the 3D-printed monoblock is superior to that of aluminum. The 3D printed titanium monoblock has a tensile strength of 1250 N/mm2. This means that a force of just over 125 kg will be applied per square millimeter of this titanium alloy without tearing the material. The new titanium caliper is 41 cm long, 21 cm wide and 13.6 cm high and weighs only 2.9kg compared to currently used aluminum, which weighs 4.9 kg.
The Bugatti Brake Monobloc is the industry's largest functional 3D printed titanium vehicle component. Source: formlabs.com
3. Tool and tool making
Various tools help to facilitate and speed up production and assembly processes, and increase the safety of workers. Automotive factories and component suppliers use a large number of non-standard tooling that is specifically designed and optimized for end use. As a result, a lot of non-standard equipment and tools are made, which increases production costs. nine0006
This 3D protective wheel disc was purchased for 800 euros but can now be printed for just 21 euros. Tool development time has been reduced from 56 to 10 days.
Source: ultimaker.com
Outsourcing the production of custom tools and fixtures to service providers who machine parts from solid metal or plastic stock can delay production by weeks.
For example, the development and prototype of a commutator motor using traditional manufacturing methods can take up to four months and cost about half a million dollars. Thanks to 3D printing, Ford was able to develop several variants in just 4 days and 99.4% cheaper - only $3,000.
Additive technologies allow you to complete the task in a few hours and significantly reduce costs compared to ordering from a third-party enterprise. Since increasing the complexity of a 3D printed model does not incur additional costs, products can be better optimized for their application. New elastic materials for 3D printing in many cases allow you to print plastic parts instead of metal or create prototypes on a 3D printer to test the tool before using it in production
Gradually, the production of 3D printed accessories and tools is becoming one of the largest applications of additive technologies.
Pankl Racing Systems uses 3D printed fixtures to attach workpieces to a conveyor belt. Source: formlabs.com
For example, Pankl Racing Systems uses multiple Formlabs SLA 3D printers to make critical manufacturing tools. The multi-stage production of parts for transmissions on automatic lathes requires a series of fixtures and tools designed for each specific part. nine0006
With the help of 3D printing, Pankl's engineers have reduced the production time for the aids by 90%, from 2-3 weeks to around 20 hours. Costs were also reduced by 80-90%, saving $150,000.
The shift to 3D printing has enabled Volkswagen Autoeuropa to cut tooling development costs by 91% and cut tooling times by 95%.
4. Solving problems with spare parts
Spare parts have always been a problem for the automotive industry. The demand for them is either there or not, so the production of spare parts is not economically viable, and the storage of pre-fabricated replacement components is also costly. But if there are no repair parts available, difficulties arise and the main product becomes less valuable. nine0006
3D printing could solve the problem of parts in the automotive industry in many ways. The main factors are printed materials, which can match the characteristics of traditional materials used in parts and be cost-effective. There are prerequisites for this.
Using computer-aided design, drawings of all parts can be stored digitally, so there is no need to store the parts themselves. The parts needed by the client can be printed on a 3D printer right in the workshop. nine0006
Even obsolete parts whose drawings have not survived can in principle be recreated by making a 3D scan of existing parts of this type and applying reverse engineering (reverse engineering). You can read more about this in our blog. Old projects can take on new life. There are many lovers of vintage cars, with the help of 3D printing it would be possible to create parts for them.
Ringbrother 3D printed the Cadillac emblem for a custom built old car. Source: formlabs.com
5. Production of standard parts
As 3D printers and materials for 3D printing become more affordable, a gradual transition to the production of mass-produced automotive parts using additive technologies is possible.
3D printing makes it possible to combine components into a whole. Let's say there is a mechanism assembled from six or seven car parts that can be combined into one printed part. It will save time and assembly costs. With 3D printing, it is also possible to reduce the weight of the combined assembly, as a result, the car will use fuel more efficiently. nine0006
3D Systems has developed an advanced exhaust pipe for a sport bike. In the image below, you will see 20 sheet metal and hydroformed parts needed to assemble the original exhaust pipe. On the right is a monolithic exhaust pipe that does not require assembly, made using metal 3D printing.
Source designnews.com
The 3D printed tube was produced using Grade23 titanium in just 23 hours, compared to three weeks for traditional production. Design development time reduced from 6 weeks to 6 days. Additive manufacturing also eliminates the need for tooling, fixtures, multiple welding and multiple inspections. nine0006
Geometry optimization has reduced the amount of material needed for maximum productivity. All elements of the original exhaust pipe are incorporated into the new design and, when printed with a typical wall thickness of 0.5mm, the 3D printed exhaust pipe is about 25% lighter than the original one.
A wide range of 3D printing materials is beginning to meet the requirements of various vehicle components. Since additive methods reduce costs compared to traditional methods (such as molding and injection molding), it makes a lot of sense from a manufacturing and financial point of view to further introduce 3D printing into the production of basic parts. nine0006
Volkswagen, one of the world's largest and most innovative car manufacturers, is using an HP Metal Jet 3D printer to produce high-performance functional parts with special design requirements, such as shift knobs and mirror mounts. Volkswagen's long-term plans to work with HP include accelerating the production of mass-customized parts such as key rings and exterior nameplates.
+1. 3D Printed Cars
Although complete 3D printed cars have not hit the market yet, some interesting designs and concepts can be seen as a possible direction for the automotive industry.
Light Cocoon. German engineering firm EDAG was clearly inspired by nature to create the 3D printed supporting structure of the Light Cocoon concept car. The frame resembles the veins of a tree leaf or its branch. Despite the fact that the design of the EDAG took less material than a conventional frame, all the strength requirements for structurally significant components are met. Outside, the case is covered with a lightweight and durable waterproof fabric. nine0006
The cover protects the EDAG Light Cocoon from the weather and gives the car a unique personality. Source: formlabs.com
Blade. Blade ("Blade") announced as "the world's first 3D-printed supercar. " It meets supercar standards but is made from inexpensive materials: carbon fiber tubes and aluminum rods, combined with 3D printed metal parts. Blade turned out to be very light and does not take long to assemble.
The world's first 3D printed Blade supercar. Source: formlabs.com
Strati. The American company Local Motors 3D printed and assembled the Strati electric car right at the exhibition stand, in just 44 hours. Most of the components were printed - the body, seats, interior parts. A car is made up of less than 50 assemblies, far fewer than the thousands of parts that go into a traditional car. The company intends to reduce the print time to 10 hours.
Local Motors Strati has less than 50 individual parts*. Source: formlabs.com
LSEV. Developed by the Italian company XEV, the LSEV could be the first in the 3D printed electric vehicle market when it goes on sale. The 3D printed chassis, seats, windshield and all visible parts of the LSEV.