3D printed iris diaphragm
STL file Rotating iris diaphragm-2 blades・3D printable model to download・Cults
Sliding Mechanical iris-hexagon cutout
€4.61
Rotating mechanical iris bar style
€4.62
Ravigneaux gear set-planetary gear system
€2.82
butterfly wing
€0.54
Iris mechanism-3 blades
€4.62
Rotating Mechanical Iris_shutter mechanism-gear structure
€4.62
Sliding Iris mechanical-hexagon with center hole
€4.62
1 stage planetary gear set
€2.84
Best 3D printer files of the Gadget category
Rear Lens Cap - NinjaFlex (for Pentax K-Mount)
Free
Batsignal Light Projection
€1. 87
Tape dispenser
Free
Switcherang: Nintendo Switch Joy-Con Grip
Free
Stand Phone For Bike
Free
Ying Yang key holder
€0.83
Xiaomi mijia 360° camera mount for OpenRC F1
Free
Cat - wall hook
€2
Best sellers of the category Gadget
Trx4m Bronco inner fenders
€7.53
Draupnir Spear With multiple Pommels and Ring included | Kratos Spear | By CC3D
€10.31
FLEXI GIRAFFE
€0.93
The Thing - Charger Stand for Airpod and Apple Watch
€14. -25% €10.59 12
Brush rinse cleaner
€2.27
BARABA repeating crossbow pistol with aluminum profile core
€10
App for Cookie Cutters
€3.50
G17- DD17 Rails Frame
€7.50
JEEP WRANGLER PEN HOLDER - 3-IN-1
€1.81
AR-15 LOWER MULTI CAL. REINFORCED STRUCTURE
€8.50
App to create switchable business cards
€3.50
App to turn your photo into 10 types of decoration
€3.50
Program to Create Christmas balls and other lithophany
€3. 50
MECHANICAL CHRISTMAS GIFT BOX
€3.15 -50% €1.57
Bambu AMS Colour 2 Tier Stand (for 2 AMS Units 1 Above 1 Below)
€2.29
Mechanical Spinning Top Dice Box
€3.72
Would you like to support Cults?
You like Cults and you want to help us continue the adventure independently? Please note that we are a small team of 3 people, therefore it is very simple to support us to maintain the activity and create future developments. Here are 4 solutions accessible to all:
ADVERTISING: Disable your AdBlock banner blocker and click on our banner ads.
AFFILIATION: Make your purchases online by clicking on our affiliate links here Amazon.
DONATE: If you want, you can make a donation via PayPal.
WORD OF MOUTH: Invite your friends to come, discover the platform and the magnificent 3D files shared by the community!
▷ iris diaphragm aperture 3d models 【 STLFinder 】
Mechanical Blade Iris Diaphragm Aperture Free low-poly 3D model
cgtrader
Mechanical iris diaphragm Animated model of an iris mechanism with five blades. If You want to print this model in 3D You surely have to take some additional effort. The file is not prepared for 3D printing, yet! Animated NURBS model (with all...
Aperture/Diaphragm
grabcad
Aperture/Diaphragm
iris diaphragm
grabcad
iris diaphragm
iris diaphragm
thingiverse
Developed and printed an iris diaphragm for a dust removal system in the workshop.
Optical Iris Diaphragm
grabcad
Iris Diaphragm, suitable for optical aperture in complect with adapter holder. ...Maximum aperture diameter ~ 10 mm.
iris diaphragm mechanism
pinshape
regards This is an adjustable iris diaphragm mechanism used in many products specially in every camera, it smoothly opens and closes the vent of light and arranges the photo light. It can be used in another product or your creation, it is designed...
Small sized Optical Iris Diaphragm
grabcad
Small sized Iris Diaphragm, suitable for optical aperture in complect with adapter holder. ...Maximum aperture diameter ~ 7 mm.
Spherical iris diaphragm ball sculpture
thingiverse
Ball shaped sculpture consisting of 4 spherical iris diaphragms. It consists of 12 blades connected to a frame consisting of 4 rings. Print Settings Printer: Cubicon Single ...
Iris Diaphragm
grabcad
Component on my shooting glass
Iris diaphragm
grabcad
I just leave it here. ..;-)
Iris Diaphragm
thingiverse
This is a cool mechanism that approximates a center hole with a continuusly variable opening radius. It is in fact an octagon and not a circle but it works quite well! The mechanism itself is purely 2 dimensional and I just designed it for fun one...
diaphragm
grabcad
diaphragm gate
Iris aperture
youmagine
Based off of, but not copying from, several other irising boxes. As printed on an inkjet-binder printer, the assembly fits together and moves quite well with a bit of grease. I left reasonable tolerance on every joint except for the sliding among...
Iris aperture
thingiverse
Based off of, but not copying from, several other irising boxes. As I don't have access to a (FFF) 3D printer, I have not tested it, but the assembly fits together and moves quite well. I left reasonable tolerance on every joint except for the...
Iris Membrane (Diaphragm)
thingiverse
Designed and manufactured using LibreCAD. The size of iris is about 60x60x15
No glue, no nuts, no screws, easy to print, amazing mechanics!
The design is simply assembled - you can see it in the picture.
Six leaves are made straight,...
IRIS-diaphragm door
grabcad
This door is going to be used in an outdoor woodstove.
eye iris diaphragm pendant
pinshape
This pendant can open and close the iris of this eye, with that handle, you can customize this model on your door or anywhere as a sign of observing point. the parts have enough gap to move correctly side by side with each other. it can't be rescale...
eye iris diaphragm pendant
pinshape
This pendant can open and close the iris of this eye, with that handle, you can customize this model on your door or anywhere as a sign of observing point. the parts have enough gap to move correctly side by side with each other. it can't be rescale...
SL4BLSh50A-Laser Cut Square Hole Sliding Iris Diaphragm
grabcad
... ...More: https://twothreed.com or https://www.tanerxun.com/assemble-square-hole-type-sliding-iris-diaphragm/.htmlThis sliding iris diaphragm is similar to a shutter mechanism. The shape is like Chinese ancient copper coins-a circle with a square hole.
Iris Diaphragm - with F360 design
thingiverse
This Iris fully opens/closes by pushing a lever through 47 degrees. It uses 12 leaves that pivot in the base and slide in/out within the slots in the top as the top rotates. Note that rotating the top too far in either direction can damage the...
Iris Diaphragm for Steampunk Goggles
thingiverse
Designed and manufactured using https://iris-calculator.com, this iris mechanism is the perfect enhancement to your Steampunk goggles. Aperture: 7 - 28 mm Blades: 6 Handle: 5 x 12 mm Outside Diameter: 47.5 mm (50.6 mm rim) Height: 12 mm Available...
diaphragm valves
grabcad
diaphragm valves
diaphragm assembly
grabcad
diaphragm assembly
DIAPHRAGM VALVE
grabcad
DIAPHRAGM VALVE 2"
Diaphragm pump
grabcad
Diaphragm pump_RVB2911_Rc112
DIAPHRAGM
grabcad
It is a disk cam mechanism of translation follower. Turn the upper disc cam to open or close the aperture. ...Fixed lower disc has a hexagon slot.
Diaphragm Pump
grabcad
1050 1" Husky Diaphragm Pump
DIAPHRAGM PUMP
grabcad
1" VERSA-MATIC DIAPHRAGM PUMP
Diaphragm Spring
grabcad
Diaphragm Spring model .... ...used in clutch...
diaphragm valve
grabcad
1 inch,1. 5 inch, 2 inch diaphragm valve
Clarity, Accuracy & Tolerances in 3D Printing
Just because your 3D printer says it has "high resolution" does not mean it will produce accurate or sharp prints.
Understanding the meaning of the terms precision, clarity, and tolerance is a prerequisite for achieving quality 3D printing results, regardless of industry. In this article, we will analyze what these terms mean in the context of 3D printing. nine0003
Webinar
Want to learn how to use 3D printing for design? Watch our webinar and learn about the stereolithography (SLA) 3D printing process, different types of materials, and tips from experts on how to optimize your printing process to make it as efficient as possible.
Watch the webinar now
Let's start with some definitions: what is the difference between precision, clarity and tolerance? For each term, we will use a target - a common example for understanding these concepts, helping to visualize them. nine0003
Precision determines how close the measured value is to the true value. In the target example, the true value is the bullseye. The closer you are to the bullseye, the more accurate your throw. In the world of 3D printing, the true value is the dimensions of your CAD model. To what extent does a product made on a 3D printer correspond to a digital model?
Clarity corresponds to measurement reproducibility - how consistent are your hits on the target? Clarity only measures this reproducibility. You can always hit the same spot, but it doesn't have to be the bullseye. In 3D printing, this ultimately leads to reliability. Are you sure that you will get the expected results for each model produced by your printer? nine0003
In engineering terms, "clarity" is used to measure the reproducibility of results. Applied to materials for 3D printing, “clear” can mean the ability to manufacture complex geometries. For example, Formlabs Gray Pro Resin and Rigid Resin resins have a high "green modulus", or modulus of elasticity, that can successfully print thin and intricate details.
What accuracy is required in this case? This is determined by tolerances , which you define. How much wiggle room do you have based on the purpose of the model? What is the allowable variability in the closeness of the measurements to the exact ones? It depends on the specifics of your project. For example, a component with a dynamic mechanical assembly needs tighter tolerances than a conventional plastic housing.
If you're specifying tolerance, you'll probably need precision as well, so let's assume we're measuring bullseye accuracy. Earlier we called the shots in the picture with the target on the right fuzzy. nine0003
But if you have wide tolerances, this may not be a problem. The shots are not as close to each other as they are on the target on the left, but if the acceptable range of sharpness is ±2.5 hoops, then you are not out of range.
As a rule, achieving and maintaining tighter tolerances entails higher production and quality control costs.
White Paper
Tolerance and fit are important concepts that engineers use to optimize mechanical functionality and manufacturing cost. Use this white paper when designing 3D printed workpieces or as a starting point when designing a fit between parts printed with Formlabs Tough Resin or Durable Resin. nine0003
Download white paper
There are many factors to consider when thinking about precision and clarity in 3D printing, but it's also important to get your needs right.
For example, a sharp but inaccurate 3D printer may be optimal for some applications. An inexpensive Fused Deposition Modeling (FDM) machine will produce less accurate parts, but for a teacher teaching students 3D printing for the first time, the exact fit of the student's CAD model doesn't matter as much. nine0003
But if the printer performs to specifications and delivers the quality expected of it within the tolerances the user is accustomed to, this may be sufficient for successful operation.
Check out our detailed guide comparing FDM vs. SLA 3D printers to see how they differ in terms of print quality, materials, application, workflow, speed, cost, and more.
There are four main factors that affect the accuracy and clarity of a 3D printer:
3D printing is a type of additive manufacturing where models are made layer by layer. Violations can potentially occur in every layer. The layering process affects the level of clarity (or reproducibility) of each layer's accuracy. For example, when printing on an FDM printer, layers are formed using a nozzle, which cannot provide the same accuracy for obtaining complex parts as other 3D printing technologies. nine0003
Because layers are extruded, FDM models often show layer lines and inaccuracies around complex features. (Left is an FDM printed part, right is a SLA printed part.)
In stereolithography (SLA) 3D printing, each layer is formed by curing a liquid polymer with a high-precision laser, resulting in more detailed models and achieve high quality on a consistent basis. nine0003
Selective Laser Sintering (SLS) also uses a laser to accurately convert nylon powder into lightweight, durable parts.
The specifications of a 3D printer alone do not give an idea of the accuracy of the models produced. One of the common misconceptions about the accuracy of various 3D printing technologies is describing XY resolution as dimensional accuracy.
For digital light processing (DLP) printers, the XY resolution corresponds to the projected pixel size. Many 3D printer systems use this projected pixel size, or XY resolution, as a general measure of accuracy, such as stating that with a projected pixel size of 75 µm, the accuracy of the device is ±75 µm. nine0003
Check out our guide to SLA and DLP 3D printing, where we talk about the features of the two processes and how they differ.
But this data does not affect the accuracy of the printed model. There are many other sources of error that affect accuracy, from components and calibration to materials and post-processing. We will consider the last two factors in more detail.
The best way to evaluate a 3D printer is to study the models printed on it. nine0006
Accuracy may also vary depending on the media you are printing on and the mechanical properties of those media, which can also affect the likelihood of model warping.
Formlabs Rigid Resin has a high "green modulus", or modulus of elasticity before final polymerization, which allows you to print very thin models with high definition and reliability.
But, again, it all depends on your goals. For example, in dentistry, the accuracy of 3D printed models is critical. But if you're printing a concept model, chances are you just want to get a general idea of the physical product, and accuracy won't be that important. nine0003
Margins, mold surfaces, and contact surfaces printed with Formlabs Model Resin are accurate to within ±35 µm of the digital model at over 80% of surface points when printed at 25 µm settings. The overall accuracy across the entire arc is within ±100 µm on 80% of surfaces when printed with settings of 25 or 50 µm.
3D printed models often need to be cured, which in turn often leads to shrinkage. This is normal for any part made using SLA or DLP 3D printing. Depending on the printer, this phenomenon may need to be considered in the design. PreForm, Formlabs' free file preparation software, automatically compensates for this shrinkage, ensuring that the final cured models are the same dimensions as the original CAD model. nine0003
How does the final polymerization work? Learn more about the theory behind the process and see efficient ways to successfully finish curing models made with stereolithographic 3D printers.
Producing quality models on a 3D printer requires attention not only to the printer itself, but to the entire production process.
The final result may be affected by the print preparation software, post-processing materials and tools used. In general, integrated systems designed to work together produce more reliable results. nine0003
Unlike machining, where parts are progressively improved to tighter tolerances, 3D printing has only one automated manufacturing step. While complex coating adds cost to processes such as CNC milling, creating complex features with 3D printing is essentially free, although the tolerances of a 3D printed model cannot be automatically improved beyond the capabilities of the printer. without resorting to subtractive methods. nine0003
3D printing is a great option if you have rough, complex features such as undercuts and complex surfaces, and don't necessarily need surface accuracy better than ±0.125mm (standard machining). Tolerances beyond standard machining must be achieved using subtractive methods, either through manual or machine processing, for both 3D printed and CNC models. nine0003
SLA has the highest tolerance compared to other commercial 3D printing technologies. The tolerances for stereolithographic 3D printing are somewhere between standard and precision machining.
In general, more malleable stereolithography materials will have a wider tolerance zone than more rigid materials. Designing subassembly parts for tolerance and fit reduces post-processing time and simplifies assembly, as well as reduces material costs per iteration. nine0003
There are many other factors to consider when evaluating 3D printers. Should your models be isotropic? What mechanical properties should your models (and, accordingly, the materials from which they are made) have? The best place to start is to get familiar with the physical models printed on a 3D printer. Order a free material sample from Formlabs of your choice and see for yourself the quality of your stereolithography print.
Request a sample 3D model
Post-processing of 3D printed parts (PLA, ABS, SBS, PETG)
Table of Contents
- Remove Supports
- Removing Soluble Supports
- Sanding
- Cold welding
- Filling voids
- Polishing
- Priming and painting
- Steam smoothing
- Epoxy coating
- Metallization
Introduction
FDM technology is best suited for rapid, low-budget prototyping. Layer lines are usually visible in FDM prints, so post-processing is essential if a smooth surface is to be achieved. Some post-processing techniques can also make a print more durable by changing the degree of its elastic properties, density, structural and textural features.
In this article, we will discuss the most common post-processing techniques in FDM. nine0003
Post-processed FDM prints (left to right): cold welded, void filled, raw, sanded, polished, painted and epoxy coated. Photo 3dhubs.com
Removing Supports
Removing supports is usually the first step in post-processing for any 3D printing technology that uses them. In general, props can be divided into two categories: standard and soluble. Unlike other post-processing methods discussed in this article, the removal of props is mandatory and does not result in improved surface quality. nine0003
Initial printout with props, poor prop removal, good prop removal. photo 3dhubs.com
Removal of standard props
Tools
- Wire cutters, needle nose pliers, tongs
- Toothbrush, brush
Finishing | ★ ☆ ☆ ☆ ☆ |
Approvals | ★ ★ ☆ ☆ ☆ |
Speed | ★ ★ ★ ★ ☆ |
Suitable for | all thermoplastics FDM |
Process
Normally the backups come off the printout without problems, and hard to reach places (such as holes or cavities) can be cleaned of the backup material with an old toothbrush. Proper placement of support structures and correct print orientation can significantly reduce the negative impact of supports on how the final printout will look. nine0003
Pluses
- Does not change the overall geometry of the part.
- The process is very fast.
Cons
- Does not remove layer lines, scratches or other surface defects.
- If excess material or marks remain from the support structure, print accuracy and appearance suffer.
Soluble Support Removal
Instrumentation
- Solvent resistant container
- Thinner
- Ultrasonic cleaner (optional)
Finishing | ★ ★ ★ ☆ ☆ |
Approvals | ★ ★ ☆ ☆ ☆ |
Speed | ★ ★ ★ ★ ☆ |
Suitable for | all thermoplastics FDM |
Process
Soluble support standard materials are removed from the printout by immersing it in a reservoir of the appropriate solvent. Supports are usually printed:
- HIPS (usually with ABS)
- PVA (usually with PLA)
A glass container like a preservation jar is fine. Any non-porous vessel is suitable for water treatment. To quickly remove props from HIPS/ABS printouts, you will need a solution of equal parts D-limonene and isopropyl alcohol. Many other support structure materials such as PVA (with PLA) dissolve in normal water.
Pro Tricks
Shorten the solution time by using an ultrasonic cleaner and changing the solvent as it becomes saturated. A warm (not hot) solution works faster - heating is useful if there is no cleaner. nine0003
Pluses
- Complex geometry is allowed for which the standard method of removing props is not possible.
- Smooth surface at the support points.
Cons
- Improper dissolution of the supports can cause discoloration and skewed printouts.
- Does not remove layer lines, scratches or other surface imperfections.
- May cause small holes or holes if soluble material seeps into the object during printing. nine0130
Scrap with a skin
SHIP SHIC ABS ABS ABS PROBECTION
Instrumentation
- FORESTIONAL PREASE with grain
on 150, 220, 400, 600, 1000 and 200 9013ANDS - Cleaning cloth
- Toothbrush
- Soap
- Face mask
Finishing | nine0002 ★ ★ ★ ★ ☆ |
Approvals | ★ ★ ★ ☆ ☆ |
Speed | ★ ★ ☆ ☆ ☆ |
Suitable for | all thermoplastics FDM |
Process
Once the props have been removed or dissolved, sanding can be done to smooth the part and remove any obvious defects such as blots or prop marks. Which sandpaper to start with depends on the thickness of the layer and the quality of the print: for layers of 200 microns or less, or for prints without blotches, you can start with sandpaper at P150. If there are blobs visible to the naked eye, or the object is printed with a layer thickness of 300 microns or more, stripping should begin with P100. nine0003
The process can be continued up to P2000 grit (one approach is to go to 220, then 400, 600, 1000 and finally 2000). Wet sanding is recommended from the very beginning to the very end - this will avoid excessive friction, which can lead to an increase in temperature and damage the object, as well as contaminate the sandpaper itself. Between sanding, the printout should be cleaned with a toothbrush and washed with soapy water, then wiped with a cloth to remove dust and prevent it from sticking together. Even P5000 can be sanded to achieve a smooth, shiny FDM part. nine0003
Pro Tricks
Always sand in small circular motions - evenly over the entire surface of the part. It may be tempting to sand perpendicular to the layers, or even parallel, but this can lead to gouges. If the part is discolored or has a lot of scratches after sanding, it can be heated a little to soften the surface and allow some defects to smooth out.
Pros
- An exceptionally smooth surface is obtained.
- Further post-processing (painting, polishing, smoothing and epoxy coating) is greatly facilitated.
Cons
- Not recommended for double or single shell parts as sanding may damage the printout.
- The process is difficult in the case of sophisticated surfaces and the presence of small details in the object.
- Grinding too aggressively and removing too much material can affect the appearance of the part. nine0130 Acetone for ABS. Dichloromethane for PLA, ABS
- Foam applicator
Finishing | ★ ★ ☆ ☆ ☆ |
Approvals | ★ ★ ☆ ☆ ☆ |
Speed | ★ ★ ★ ★ ★ |
Suitable for | all thermoplastics FDM |
Process
If the size of the object exceeds the capacity of the printer, the object is printed in parts and then assembled. In the case of PLA and some other materials, assembly can be done with Dichloromethane or a suitable adhesive (the choice of adhesive depends on the plastic). In the case of ABS, it is possible to "weld" with acetone. The mating surfaces should be slightly moistened with acetone and squeezed tightly or clamped and held until most of the acetone has evaporated. So the parts will be held together by chemical bonds. nine0003
Pro Tricks
Increasing the surface area of the acetone contact increases bond strength. Tongue-and-groove to help.
Pros
- Acetone does not change surface color as much as most adhesives.
- After drying, the compound acquires the properties of ABS, which makes further processing easier and more uniform.
Cons
- The bonding of ABS parts by cold acetone "welding" is not as strong as if the part were printed as a whole.
- Excessive use of acetone can dissolve the part and affect final appearance and tolerances.
Void Filler
Black ABS Print, Filled and Sanded
Tool Kit
- Epoxy (for small voids only)
- Automotive body filler (large voids and joints)
- ABS filament and acetone (only for small voids in ABS printouts)
Finishing | ★ ★ ☆ ☆ ☆ |
Approvals | ★ ★ ★ ☆ ☆ |
nine0002 Speed | ★ ★ ★ ☆ ☆ |
Suitable for | all thermoplastics FDM |
Process
Unusual voids may come out after the part has been ground or the soluble props have been dissolved. These voids are formed during printing when the layers are incomplete due to any restrictions on the trajectory of the print head, which is often inevitable. Small gaps and voids can be easily filled with epoxy and no additional treatment is required in this case. Larger gaps or voids left by assembling a multi-part object can be filled with automotive bodywork filler, but the printout will then need to be re-sanded. Putty works great, is easy to process with sandpaper and can be painted. Moreover, the parts connected by such a filler, or voids filled with it, turn out to be stronger than the original plastic. nine0003
Slots in ABS printouts can also be filled with ABS thinned with acetone, which reacts chemically with the ABS object and seeps into existing voids. It is recommended to make such a putty from 1 part ABS and 2 parts acetone, then it will not spoil the surface if used correctly.
Dichloromethane works on all plastics: ABS, PLA, HIPS, SBS, etc.
Epoxy is also useful if you want to make your 3D printed part more durable
Pros
- Epoxy filler is easy to sand and prime, resulting in an excellent surface for painting.
- ABS solution of the same filament will give the same color so nothing will be visible on the surface.
Cons
- Auto body filler or other polyester epoxy adhesive is opaque when dry and will leave discolored areas on the printout. nine0130
- Additional processing required to achieve a uniform surface.
- Grinding too aggressively and removing too much material can affect the appearance of the part.
Polished
PLA model, polished. Photo rigid.ink
Tools
- Plastic polishing compound
- Sandpaper for P2000
- Cleaning cloth
- Toothbrush
- Polishing pad or microfiber cloth
Finishing | ★ ★ ★ ★ ★ |
Approvals | ★ ★ ★ ☆ ☆ |
Speed nine0190 | ★ ★ ☆ ☆ ☆ |
Suitable for | all thermoplastics FDM |
Process
Once the part has been cleaned, a plastic polish can be applied to the part to give a standard ABS or PLA object a mirror finish. After the part has been sanded for 2000, it is necessary to remove dust from the printout with a cloth and rinse the printout under warm water using a toothbrush. When the object is completely dry, buff it on a buffing pad or microfiber cloth, adding a polishing compound as you go, such as polishing jewelry. They are designed specifically for plastics and synthetics and give a long-lasting shine. Other plastic polishes, such as those used to polish car headlights, also work well, but some of them contain chemicals that can damage the printout. nine0003
Pro Tricks
To polish small parts, place the polishing wheel on your Dremel (or other rotary tool such as a power drill). For larger and stronger parts, you can use a grinder, just make sure that the part does not stay in one place for too long, otherwise the plastic may melt from friction.
Pros
- The part is polished without solvents that can warp it or change its tolerances.
nine0130
- When properly ground and polished, a mirror-smooth surface is obtained, very similar to cast.
- Polishing and deburring plastics is extremely economical, making this a very cost-effective method of achieving a quality finish.
Cons
- If you want to achieve a mirror-smooth surface, the part must be carefully ground before polishing, which may affect tolerances.
- After polishing, the primer or paint no longer sticks.
Primer and paint
Gray PLA FDM print spray painted black. 3dhubs.com
Tools
- Cleaning cloth
- Toothbrush
- 150, 220, 400 and 600 grit sandpaper
- Aerosol Primer for Plastics
- Finish paint
- Polishing sticks
- Polishing paper
- Masking tape (only if multiple colors are expected)
- Nitrile gloves and matching face mask
Finishing | ★ ★ ★ ★ ★ |
Approvals | ★ ★ ★ ☆ ☆ |
Speed | ★ ☆ ☆ ☆ ☆ |
Suitable for | all thermoplastics FDM |
Process
After the printout has been properly sanded (it is enough to reach P600 when painting), it can be primed. Aerosol plastic primer should be applied in two coats. This primer is intended for subsequent painting of models, provides an even coating and at the same time thin enough not to hide small elements. Thick primer, which is sold in hardware stores, can clump, and then you have to seriously work with sandpaper. Apply the first spray coat with short pressures from a distance of 15-20 cm from the object, trying to do it evenly. Let the primer dry and smooth out the unevenness with 600 grit sandpaper. Apply a second coat of spray with light, quick pressures, also very gently and evenly. nine0003
When the priming is completed, you can start painting. You can paint with artistic acrylic paints and brushes, but a spray gun will provide a smoother surface. Hardware store spray paints are thick and viscous and difficult to control, so use paints that are designed specifically for modeling. The primed surface must be sanded and polished (sanding and polishing sticks, which are used in nail salons, can be purchased online, they are great for our task), and then wiped with a cloth. The paint should be applied to the model in very thin layers, the first layers should be transparent. When the paint finish becomes opaque (usually 2-4 coats), let the model rest for 30 minutes to allow the paint to dry completely. Carefully polish the paint layer with manicure sticks, repeat the procedure for each of the colors (between each applied paint). nine0003
Separate parts of the model can be covered with masking tape so that the colors, if there are several, do not mix. When painting is complete, remove the masking tape and polish the object with polishing paper. Polishing paper, such as 3M or Zona, comes in a variety of grits and is a relatively new product. It is sold in packs in various online stores, and after processing with this paper, the ink layer or topcoat will literally shine - and nothing else can achieve this effect. Apply 1-2 coats of top coat to protect the paint and let it dry completely. The top coat is selected in accordance with the recommendations of the paint manufacturer. If the topcoat and paint are incompatible, it can render your entire painting job meaningless, so compatibility is very important here. nine0003
Pro Tips
Don't shake the can when spraying! It is important not to mix the pigment or primer with the propellant (propellant gas), which will cause bubbles to form in the spray. Instead, the can must be rotated for 2-3 minutes so that the mixing ball rolls like a pearl, and does not strum.
Pros
- Excellent result, if you take into account all the nuances of the process and practice. nine0129 You can do anything with the final look of the object, no matter what material it is printed on.
Cons
- Primer and paint increase the volume of the model, which affects tolerances and can be a problem when it comes to a part of a larger object.
- A high quality spray paint or spray gun increases costs.
Vapor smoothed
Vapor smoothed black ABS printed hemisphere
Tools
- Cleaning cloth
- Solvent resistant sealed container
- Thinner
- Paper towels
- Aluminum foil (or other solvent resistant material)
- Face mask and chemical resistant gloves
Finishing | nine0002 ★ ★ ★ ★ ☆ |
Approvals | ★ ★ ☆ ☆ ☆ |
Speed | ★ ★ ★ ☆ ☆ |
Suitable for | all thermoplastics FDM |
Process
Line the bottom of the container with paper towels, if possible along the sides. It is critical that the vapors cannot damage the container and that the container itself is sealed. It is recommended to use a glass or metal container. Apply enough thinner to the paper towels so that they are wet but not soaked - this will also help them adhere better to the walls. Acetone is famous for its ability to smooth out ABS. PLA can be smoothed with a variety of other solvents (dichloromethane works well), but this plastic tends to be much harder to smooth than ABS. When working with any solvents, please follow the safety precautions for handling chemicals and always take appropriate precautions. Place a small "raft" of aluminum foil or other solvent-resistant material in the center of the paper towel-lined container. Place the printout on the "raft" (either side of your choice) and close the lid of the container. Steam polishing can take varying amounts of time, so check your printout periodically. To increase the speed of polishing, the container can be heated, but this must be done carefully so as not to cause an explosion.
nine0003
When removing the printout from the container, try not to touch it in any way, leave it on the “raft”, take them out together. In all those places where the printout has come into contact with something, there will be defects, since the outer layer will be under-dissolved. Before working with it, let the printout completely “breathe” so that all solvent vapors have evaporated.
Many aerosols and/or solvent sprays are flammable or explosive and their vapors can be harmful to humans. Be extremely careful when heating solvents, always handle them and store them in a well ventilated area. nine0006
Pros
- Many small blotches and a lot of layer lines are smoothed out without additional processing.
- The printout surface becomes exceptionally smooth.
- The procedure is very fast and can be performed using commonly available materials.
Cons
- Doesn't "heal" gaps, doesn't completely hide layer lines.
- During the smoothing process, the outer layer of the printout dissolves, which greatly affects the tolerances. nine0130
- Negatively affects the strength of the printout due to changes in the properties of its material.
Immersion
PLA model immersed in dichloromethane. Photo 3dpt.ru
Tools
- Solvent resistant container
- Thinner
- Eye hook or cog
- Heavy wire for sculpture or landscaping
- Dryer or drying frame
- Face mask and chemical resistant gloves
Finishing | ★ ★ ★ ★ ☆ |
Approvals | ★ ☆ ☆ ☆ ☆ |
Speed | nine0002 ★ ★ ★ ★ ☆ |
Suitable for | all thermoplastics FDM |
Process
Make sure the container you are using is wide and deep enough to completely submerge the printout in the solution. Fill the container with the appropriate amount of solvent - be careful not to splash. As with vapor smoothing, ABS dip smoothing can be done with acetone, which is easy to find in the store, and for PLA, dichloromethane can also work well with ABS, HIPS, SBS, PETG, and many other materials. PLA is quite resistant to solvent smoothing, so it may take several passes to achieve the desired result. Prepare the printout for dipping by screwing a hook or eye screw into it in an inconspicuous place. Pass the wire through the eyelet or wrap the wire around the screw so that the printout can be immersed in the solvent. If the wire is too thin, it will not be able to withstand the buoyant force on the printout, and it will be difficult to sink the object. nine0003
Once the printout is ready, use a wire to completely immerse it in the solvent for a few seconds. Remove the printout and hang it by the wire in a dryer or on a drying frame to allow the solvent to completely evaporate from the surface. After ejection, the printout can be gently shaken to facilitate the drying process and ensure that no solvent has accumulated in the depressions.
Pro Tricks
If an opaque whitish coating appears on the printout after drying, this can be corrected by holding the object over a solvent bath for a while so that its vapor slightly dissolves the surface. This restores the original color of the printout and achieves a shiny outer layer. nine0003
Pros
- The surface of the print is smoothed much faster than steam polishing.
- Significantly less fumes are generated than other solvent polishing methods, so this method is less hazardous.
Cons
- The surface is smoothed very aggressively, so you can forget about tolerances.
- Immersion for too long can result in complete deformation of the object and a significant change in material properties. nine0130
Epoxy
Black ABS print, half epoxy coated, half uncoated
Tools
- two part epoxy
- Foam applicator
- Mixing container
- Sandpaper P1000 or finer
Finishing nine0190 | ★ ★ ★ ★ ☆ |
Approvals | ★ ☆ ☆ ☆ ☆ |
Speed | ★ ★ ★ ★ ☆ |
Suitable for | all thermoplastics FDM |
Process
After the printout has been cleaned (preliminary cleaning gives the best end result), wipe it thoroughly with a cloth. Mix the resin and hardener in the proportion indicated in the instructions, accurately measuring all volumes. The curing process of epoxy resin is exothermic, so glass containers and containers made of materials with a low melting point should be avoided. It is recommended to use containers that are specifically designed for mixing epoxy resins. Incorrect ratio of resin and hardener can result in longer curing time or no curing at all and result in a permanently sticky substance. Mix the resin and thinner as directed in the instructions - carefully, in smooth movements to minimize the amount of air bubbles remaining inside the mixture. Very little epoxy is needed, and most of these resins only work for 10-15 minutes, so plan accordingly. nine0003
Apply the first coat of epoxy with a sponge applicator, being careful not to build up in crevices and small parts. When the printout is sufficiently coated, allow the resin to fully cure - as described in the instructions that came with it. One coat may be sufficient, but for optimum results it is best to lightly sand the printout with fine sandpaper (on P1000 and above) to eliminate any imperfections. Wipe off the dust with a cloth and, in the same way as before, apply a second layer of epoxy. nine0003
Pros
- A very thin coat of epoxy won't affect tolerance too much (unless the printout has been sanded excessively hard first).
- A protective shell forms around the object.
Cons
- The layer lines will remain visible, they will only be covered by a smooth shell.
- If too much epoxy is used, it can flood parts and edges, and the surface can appear greasy. nine0130
Metallization
FDM printed structural element nickel plated with Repliform RepliKote technology
Tools (for home use)
- Sacrificial anode. The anode material must match the metal of the solution: for example, if copper sulfate is used in the solution (with water it is copper sulfate), then the anode must also be copper. Any object made of the appropriate metal will do (for example, copper wire for copper plating), or you can buy special strips of metal for galvanization.
- Conductive paint or acetone with graphite. Electroplating requires the surface of the printout to be electrically conductive, and this can be achieved with a conductive paint or a solution of equal parts graphite and acetone. Conductive paint will work with any material, but acetone with graphite will only work with ABS. nine0130
- Power rectifier. A simple battery can be used as this element, only it will not be as efficient and will not give a fast enough result than the rectifier itself (household current).
The rectifier is safer in the sense that it can simply be turned off and thus cut off the current during the galvanization process.
- Conductive screw or eye hook
- Non-conductive container
- Contacts nine0129 Non-conductive gloves and goggles. Electroplating solutions are acidic and can cause injury if splashed into the eyes, so wearing goggles is very important. Solutions also irritate the skin and conduct electricity, so insulating gloves are needed.
- A galvanizing solution can be obtained by mixing a metal salt, acid and water, but if the proportions are inaccurate and the substances are of insufficient quality, one cannot count on a professional result.
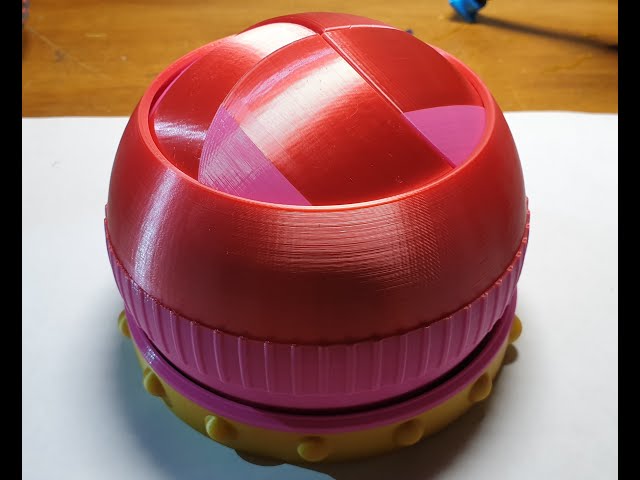
Finishing | ★ ★ ★ ★ ☆ |
Approvals nine0190 | ★ ★ ★ ☆ ☆ |
Speed | ★ ★ ★ ★ ☆ |
Suitable for | all thermoplastics FDM |
Process
Electroplating can be carried out at home or in a professional workshop. To do everything right, you need to be well versed in the materials, in what is actually happening - and at home these opportunities are usually limited. In order to achieve excellent surface quality and to have more plating options, including chrome plating, it is best to use the services of professional workshops. The copper galvanization process will be described below as an example. nine0003
At home, you can galvanize with copper or nickel, and this coating will then serve as the basis for galvanizing with other metals. It is critically important that the printout surface be as smooth as possible before it is galvanized. Any bumps and lines in the layers will be enhanced as a result of the process. Prepare the sanded and cleaned object for plating by coating the plastic with a thin coat of high quality conductive paint, or with a graphite and acetone solution for ABS printouts. Allow the conductive coating to dry completely, sand if necessary to ensure a smooth surface. At this stage, it is extremely important not to touch the printout with bare hands or to wear gloves, because sweat marks on the object will certainly affect the quality of the galvanization. nine0003
Insert a screw or eyelet in an inconspicuous place on the printout and connect it to the negative terminal of the rectifier. This will be the cathode. Connect the copper anode to the positive contact of the rectifier. Fill the container with enough copper plating solution so that the printout is completely covered with it. Immerse the anode in the container and turn on the power. After the rectifier is turned on, immerse the printout in the container, making sure that it does not touch the anode anywhere. nine0005 Beware! When the object is already in the bath, the galvanization system is active, and contact with the solution, cathode or anode can be traumatic. Set the voltage on the rectifier to 1-3 Volts, and the process will go to full metallization. To speed things up, the voltage can be increased, but not more than 5 volts. When enough metal has deposited on the printout, simply turn off the power and dry the object with microfiber towels. When it's dry, varnish the object to protect it from corrosion.