3D printed electronics box
Benefit from custom electronic enclosures
3D Learning Hub
See all categories
Contents:
- Introduction
- Creating electronic devices with more scalability
- Advantages of 3D printed enclosures
- Developing your own custom electronics enclosures
Introduction
Creating custom electronic devices with more scalability
Creating electronic devices comes with its challenges. How can the creation of electronic enclosures participate in the development of your electronics project and in the growth of your business? Never forget about the advantages of better scalability and adaptability for your electronics enclosures. While creating these electronic devices, you must meet changing market demands with unbeatable lead-times thanks to an optimized and scalable manufacturing process. Making the most of Just-In-Time manufacturing and getting the parts you need when you need them might also be a huge advantage for your business.
Additive manufacturing has a lot of advantages to offer you in the electronics sector. Let’s take the example of the plastic electronics housings. Just on this part, 3D printing has a lot to offer. Implementing additive manufacturing in your process is a solution to speed up your processes and gives the possibility to be more reactive and at the same time, more competitive. But that’s not all! 3D printing is also giving you the opportunity to be more innovative and improve your enclosures designs. This way, you will be able to create plastic PCB enclosures perfecTly adapted to your projects.
Advantages of 3D printed enclosures for engineers and designers
Adaptability
The freedom offered by additive manufacturing has almost no limits. Creating snap fits, interlocking joints, threaded fasteners, and living hinges are all possible when 3D printing enclosures. Adapt your housings with all the functionalities you’ve envisioned for it. 3D printing gives access to a design flexibility injection molding just can’t offer. Indeed, with a mold, you won’t be able to change its design to make modifications to your final parts. If you need to modify your project, then you will need to start from the beginning and re-do the whole process again.
With additive manufacturing, it’s different: you only have to modify your 3D file, it won’t interrupt your manufacturing process at all. More reactivity in your process means you can adapt to your immediate needs without losing time and money. Using 3D files with 3D printing, you don’t have to worry about the lifetime of the enclosure design, your process just become more and more flexible. You will have the opportunity to implement all the changes you will need when you need them.
Moreover, mass-customization is a great benefit of additive manufacturing. You can adapt your file to the needs of your customer. It won’t be more expensive to manufacture several iterations of your enclosure using 3D printing!
Innovation
Additive manufacturing will offer you the opportunity to innovate and develop your projects. While using 3D printing, you can think about what you want to create, and not only what you can create, considering the traditional constraints of manufacturing. Feel free to experiment and innovate using cutting-edge technology such as additive manufacturing.
You can take into account all the functionalities of your part and integrate them directly into your device.
Speed your processes
Speeding your processes will help your business grow. When you create your electronic device, the design and the ergonomy of the enclosure are as important as the features. To fill this important requirement, you can count on the ability of 3D printing to create complex shapes very quickly. 3D printing is the fastest prototyping technology because it allows to create unique prototypes without any mold which means that the price of the part is low.
With 3D printing, the price is not driven by the quantity but by the amount of material used. With several iterations of the same enclosure, 3D printing is a much more reliable and sustainable manufacturing method than traditional ones. Thanks to a 3D printed prototype, it is possible to check the ergonomy, the aspect but also the fit of the internal components or the accessories. With a variety of 3D printing materials, it is also possible to have a look at the final material aspect and to check the assembly.
Additive manufacturing also appears to be the perfect manufacturing method for the production of plastic enclosures. If you need customization or just-in-time manufacturing abilities, then there is no doubt about the benefits of this technology for your business.
Developing your own custom electronics enclosures
What 3D printing material should you choose?
What is the best enclosure material? To develop your project and start creating your 3D design, you will have to choose your material and take into account its design guidelines. If you are using a filament 3D printer, then PLA, PETG, or ABS become options to create your enclosure. But your electronic project might present some requirements and better mechanical properties to create an even more durable 3D printed enclosure.
Plastic electronic enclosures can be developed using additive manufacturing with adapted materials. To create these plastic enclosures, 3D printing materials such as Nylon PA12 or Nylon PA11 will be especially suitable for your project. These are two cost-effective material options that can be used to manufacture your prototypes, small or big series.
How to design enclosures for 3D printing?
It is really helpful to design the component around what you want to enclose before modeling the enclosure. In that way, you can place the components, check that everything fits and it will be easier to determine the clearance for the connectors or the cables afterward. To be sure that your components will fit, we recommend keeping a 0.5 mm clearance between components and 3D printed features.
Access to the component
The first thing to think of when designing an enclosure is what you will put in it and how you will access it. If you do not need to have access to your components, you can design specific fastening components or use adhesives to seal your enclosure permanently.
In the case where you want to have access to your components, there are many closing systems you can use:
- Semi-rigid lugs
- Sliding faces
- Screws
- Classic and Living hinges
- Assembly
Lugs, cut-outs and lips, help with the assembly and parts alignment. Moreover, these features are great to strengthen your enclosure if you respect the minimum dimensions of such features. Check the design guidelines of your chosen material for more information. Learn how to connect two parts with 3D printing, in our dedicated article.
The solidity of the 3D printed enclosure
The wall thickness of your enclosure is a major thing to consider. It determines the weight, rigidity, solidity, and possible applications of your enclosure. Even if our machines can print smaller details and walls, we recommend you to respect a minimum wall thickness of 2 mm. This value ensures a structural solidity with a very light weight. Once again, check the design guidelines of your material to adapt this thickness.
Be careful however depending on the length of your enclosure, a 2 mm wall thickness can give a certain flexibility to the walls and can cause some shrinkage.
A fillet is a key feature in 3D printing because hard angles may not be properly 3D printed. Fillets in enclosures are really important both in the inside and the outside.
Fillets avoid sharp angles and reduce the stress
Outside of your enclosure, soften your corners with very small fillets (1 or 2 mm).
Inside your enclosure, the corners can be strengthened with bosses and fillets. A very small radius facilitates 3D printing and reduces the stress concentration on corners.
Bosses with fillets on the inside allow to reduce the stress around a hole
3D printing enclosures: quality and accuracy
If your design contains screw holes or fastener clearance holes, be sure that your material is accurate enough. With our 3D printed plastic, the accuracy is very high but to obtain more precise holes, it is recommended to drill or tap them afterward with machining tools.
Slightly expand the diameter of screw and fastener clearance holes to obtain better results
On the other hand, reduce the diameter of the holes where you want the screw or fastener to bite into the case
To learn more about threading in 3D printing, you can check this article.
In enclosures, small walls and thin features are often added to keep components in place. These features have to respect the minimum thickness of your material but in addition, we suggest adding structure features like gussets or ribs that will give strength to your element and help it to be 3D printed correctly.
Gussets or ribs reduce stress, strengthen thin features and reinforce the case
Finally, remember that you can iterate really fast but it is also possible to go into production with 3D printing for your enclosures. Many of our customers have already tried our online 3D printing service to go into production for their enclosure
Related Topics
- Return to Top
Get the latest 3D printing news delivered right to your inbox
Subscribe to our weekly newsletter to hear about the latest 3D printing technologies, applications, materials, and software.
Premium 3D Printed Electronics Case Supplier
3D printed electronics cases enable us to produce prototypes or final parts in a matter of hours and allow design freedom.
It’s cheaper compared to other traditional manufacturing methods and offers an effective method of confirming form and fit.
In this article, we’ll guide you on how our 3D printing services can help optimize your 3D printed electronics case designs while maintaining premium quality.
What are the Benefits of 3D Printing to Produce Electronic Cases?
In an industry as competitive as electronics, the demand for thinner, smaller enclosures with improved functionality is inevitable.
3D printing technologies can help you in the following ways to get outstanding-quality 3D printed electronics cases:
Faster Time-to-MarketDeveloping highly functional electronic cases and other electronic parts is often challenging and can prolong lead times. 3D printed electronics cases can create efficiencies during the product design stage.
Moreover, it enables a faster turnaround of design iterations. The advanced 3D printing technologies speed up the design validation process and help you gain a competitive advantage by developing your enclosures much faster.
Achieving more flexible manufacturing of electronic cases is possible with 3D printing.
Design Flexibility3D printing helps us manufacture complex shapes and enables design for functionality, meaning that complex structures can be more readily produced.
Customization3D printing offers complete customization of electronic cases and expands its manufacturing capabilities. With thousands of customization options available, you can create personalized 3D printed electronics case.
ScalabilityBy meeting changing market demands with unbeatable lead times thanks to an optimized and scalable 3D printing process, leads to speed up the processes and gives the possibility to be more reactive and at the same time, more competitive.
3D printing allows being more innovative and improves the design of your enclosure. It’s possible to adapt the complex designs and functionalities you’ve envisioned through 3D printing.
It gives access to design flexibility and more reactivity without losing money and time.
Innovation3D printing offers you the opportunity to innovate and develop your projects. Using this cutting-edge technology, you can experiment, innovate, and can take into account all the functionalities of your 3D printed electronics cases and integrate them directly into your parts.
Moreover, it helps your business grow by speeding up your processes.
Design and the ergonomic of your electronic cases are as important as the features and to fill this important requirement, you can count on the ability of 3D printing to create complex shapes quickly.
Can 3D Printing Electronics Plastic Case?
3D printing is an extremely cost-effective way to produce high-resolution, accurate, and extremely strong electronic plastic cases. hybrid material)
Moreover, SLS, SLA, Material Jetting, and MJF are the common 3D printing technologies that offer more accuracy and quality while plastic 3D printed electronics cases.
Can 3D Printing Electronics Metal Case?
SLM and DMLS are two of the most common metal 3D printing technologies.
SLM produces electronic cases from a single metal, while DMLS produces parts from metal alloys.
3D printed electronics cases can produce from the following metals and metal alloys:
- Aluminum alloys
- Stainless steel & tool steel
- Titanium alloys
- Cobalt-Chrome superalloys
- Inconel (Nickel superalloys)
- Precious metals (Gold, Platinum, Palladium, Silver)
These metals cover the needs of most electronic applications. A key strength of metal 3D printing is its compatibility with high-strength materials.
Moreover, significant time and cost savings can be made by using metal 3D printing to create near-net-shape parts and cases that can are later post-processed to a very high surface finish.
What are the Technologies for 3D Printing Electronics Cases?
There’re several 3D printing technologies highly optimized to manufacture high-resolution and accurate electronic cases.
The majority of these technologies feature their benefits and are suitable for a particular kind of printing materials and have their applications.
The following are some benefits you can get from these well-known 3D printing technologies:
Rapid PrototypingFDM is a 3D printing technology that helps prototyping plastics in cost-effective manors. It’s a quick method of printing electronic enclosures.
High TemperatureMaterial Jetting is a high-temperature 3D printing technology that heat resistant plastics to remain stable up to temperatures as high as 80℃ after thermal post.
This section of surface finish is usually governed by the 3D printing time and cost. Different 3D printing technologies offer different surface finish (it also depends on the 3D printing resolution) like Material Jetting and SLA offer fine-detail models with very smooth surfaces. Moreover, some 3D printing materials like SLS nylon results in a satin-like matte finish.
High AccuracySLA, SLS, and Material Jetting are some of the highly accurate 3D printing technologies that are capable of printing high-resolution electronic cases within 0.2 – 0.5 mm.
Transparent3D printing transparent plastics is possible with SLA and material jetting. Transparent electronic cases allow for inspection or verification of internal components and are often applied to applications where fluids are being employed.
Flexible MaterialElectronic cases can be extremely flexible to perform some functions like motion switches through the sealed cases. Rubber-like plastics or SLA flexible resin are perfect flexible materials for 3D printing such flexible electronic cases.
Moreover, electronic cases can be 3D printed from a range of different 3D printing materials like SLS (white), SLA (gray), and FDM (black) with each 3D printing technology having benefits and limitations.
How Do I select the Right 3D Printing Process for My Electronics Cases?
There’re multiple processes and materials available to 3D printed electronics cases.
By materialSelecting a 3D printing process is relatively easy for those who know which material is perfect for their enclosures as only a few technologies can produce parts from the same materials.
By use caseYou must know whether your parts need to be functional or visually appealing that makes choosing a process relatively easy.
The two primary use cases of 3D printed electronics cases are either for functional applications or visual appearance.
For functional applications, thermoplastic polymer cases are suitable while thermosets are best suited for visual appearance.
How Can I Reduce the Cost of My 3D Printed Electronics Case?
The complete cost of your 3D printed electronics cases is associated with the number of:
- Unique parts
- Post-processing requirements
- Material cost
- Individual volume
Moreover, to reduce these costs, you need to understand the impact of these factors on cost.
We reduce the overall cost by reducing the amount of material used by eliminating waste and optimizing our manufacturing processes.
However, reducing the size of your model, eliminating the need for support structures, and hollowing it out can also lead to a lower overall cost.
The most important top is to choose the right 3D printing process and technology for your job.
Metal 3D printing is much more expensive than plastic 3D printing.
Additionally, designing parts correctly can lead to cost-effective 3D printing solutions.
Some 3D printing technologies have their benefits and limitations, which affect the affordability of certain design choices.
Is There any Tooling or Start-Up Costs for 3D Printing Electronics Cases?
When manufacturing your 3D printed electronics cases, the only cost you pay is the unit cost.
There’s no start-up, tooling, or any other hidden costs in our 3D printing services.
In fact, by increasing the number of your 3D printed electronics cases, you can take advantage of the volume price breaks.
Is 3D Printed Electronics Case Cheaper than Injection Molding?
Mostly, 3D printing can be more cost-effective than using injection molding for your electronic enclosures.
The part cost of a 3D printed electronics case is more economical due to no tooling or start-up cost for low to mid-volume parts production.
Our customers make savings on quantities up to tens of thousands of parts as there’re also no restrictions to design alterations through the production process.
Does DEK Offer Custom 3D Printed Electronics Cases?
The demands of customers’ need for custom 3D printed electronics cases are increasing and manufacturers are facing pressure from various requirements and market demands.
At DEK, we understand our customer needs and produce these custom enclosures tailored to your design, functional, and material requirements.
We make 3D printing less time-intensive and cost-effective with rapid availability.
DEK offers three types of 3D printing customizations:
- Transparent customization: It involves user-defined patterns and preferences to create electronic cases by monitoring customers’ consumption patterns.
- Cosmic customization: It involves customizing the design of a standard type of electronic case without changing its functionality or features.
- Adaptive customization: It involves modification or reconfiguration of a standard electronic case based on your needs without direct interaction with the manufacturer.
We can give you design freedom so you can later modify or configure your electronic cases according to your applications.
You can expect electronic cases made through mass customization to be delivered quickly and in a cost-effective manner while working with us.
How You Guarantee the Quality of My 3D Prints?
We take quality seriously as we focus on the complete satisfaction of our customers.
We have a highly-skilled staff of engineers to control our advanced 3D printers to ensure we continue to deliver the highest quality parts to our customers.
With each order, we include a comprehensive and standardized inspection report to ensure quality metrics are being met.
Is There any Minimum Order Quantity for 3D Printed Electronics Enclosures?
One of the primary reasons to choose 3D printed electronics cases is no minimum quantity.
It’s suitable to produce both a single prototype and a high-volume production.
You can start with just one 3D printed electronics case. Moreover, the final production run will be exact to the prototype as prototypes are produced on the same 3D printing machines.
Why Choose DEK?
Our 3D printing services consist of seven 3D printing technologies and many materials to transform your 3D files into plastic, metal, and elastomeric electronic cases.
We have an unmatched capacity that reliably delivers 3d printed electronics cases within days.
In addition to a broad material selection, we offer several post-processes options to improve cosmetics or enhance mechanical properties.
The following are some reasons why we are the best in 3D printing:
- Consultative quoting
- Precision and repeatability
- Unmatched scale
- Wide material selection
Our industry-leading tolerances and surface finish quality stem from a dedicated process engineering and quality team for each 3D printing technology.
STL file DIY 3D printed electronics box / medical box / SMD box・3D printing design to download3D・Cults
Attachment for 18650 batteries (double-row/double-sided) - Li-ion welding
0. 56 €
775 DC motor pulley 4 different sizes
0.52 €
18650 Lithium Ion Battery Holder and Cell Balancer x 8
0.57 €
18650 LITHIUM ION DOUBLE ROW BATTERY FIXTURE FOR STRIP WELDING (10x2)
0,59 €
18650 LITHIUM ION SINGLE ROW BATTERY FIXTURE FOR STRIP WELDING (8x1)
0,52 €
18650 LITHIUM ION DOUBLE ROW BATTERY FIXTURE FOR STRIP WELDING (9x2)
0,58 €
nine0003 18650 LITHIUM ION DOUBLE ROW BATTERY FIXTURE FOR STRIP WELDING (7x2)0,57 €
18650 LITHIUM ION DOUBLE ROW BATTERY FIXTURE FOR STRIP WELDING (4x2)
0,54 €
Best 3D Printer Files in Home Category
The Spiral - Desk Clock
Free
nine0003 Magnetic pen1 €
Garden Bed Screen
Free
Lampshade
Free
FruitSkewer 🍉🥝
1. 32 €
Sponge and towel holder
0.85 €
Steampunk Shelf Bracket
Free
Tassimo - Capsule holder
Free
Bestsellers in the Home category
Samurai incense holder
2.40 €
Venus and Aphrodite
3.60 €
Wall shelf "Mushroom Amanita"
2.40 €
Wallet card holder (universal package)
1.28 €
Pencil with dinosaur gluttony
1,55 €
Waste bin with hinged lid
3.20 €
Quick Print Gift/Storage Boxes - Ultimate Collection (Vase Mode)
€5. -25% 4.26 € 68
Bordeaux, Octopus
2.36 €
Prepaid Gift Card Holder v2.0
1.92 €
Wall shelf "Oyster mushroom"
2,40 €
nine0003 Notepad2.60 €
Articulated Christmas tree in lingerie
2.36 €
Crystal corner decor - printing on site
1.54 €
Modular storage box system with quick print
5.68 €
Another quick-change toilet roll holder
1 €
Secret tray for bowls of ramen noodles
2. 66 €
Do you want to support Cults?
Do you like Cults and want to help us continue our journey on our own ? Please note that we are a small team of 3 people, so it is very easy to support us in maintaining activities and creating future developments. Here are 4 solutions available to everyone:
-
AD: Disable the AdBlock banner blocker and click on our banner ads.
-
AFFILIATION: Shop online with our affiliate links here Amazon.
-
DONATIONS: If you want, you can donate via PayPal here.
-
* INVITE FRIENDS: * Invite your friends, discover the platform and great 3D files shared by the community! nine0006
Gone・Cults
Unfortunately, the job you are looking for has disappeared...
But don't panic!
Yes, this work is no more, it's sad. .. but you can always check the profile of the author Mr_Armageddon, who made this model, or even send him a direct message.
Otherwise, at Cults, we always have something to please your 3D printer. For example, look at these little hooligans:
01 nine0003 Deadpool Kirby
Free
02Century buggy rally car - print on site
1.79 €
03Train station for wooden railway BRIO
1.08 €
04Pennywise Mask | It
7.45 €
05 nine0003 Emergence Vase €4.01 -thirty% 2. 80 €
MAMMUT, articulated, flexible
3.22 €
07Rattlesnake articulated toy, imprinted body, snap head, cute flexi
3,72 €
08 nine0003 Fokker DR1 3D printed RC aircraft18.15 €
09Key ring for weapons
1 €
10Totor Viking
6 €
elevenMini Tetris GameBoy - retro console and container
4.71 €
12 nine0003 Card Fountain3.63 €
13Snap Fit Mini Crossbow V3 (easy to assemble version)
Free
fourteenBirdhouse
Free
15The Shining - The Torrance Family Retro Style Action Figure Kenner Reaction 3.
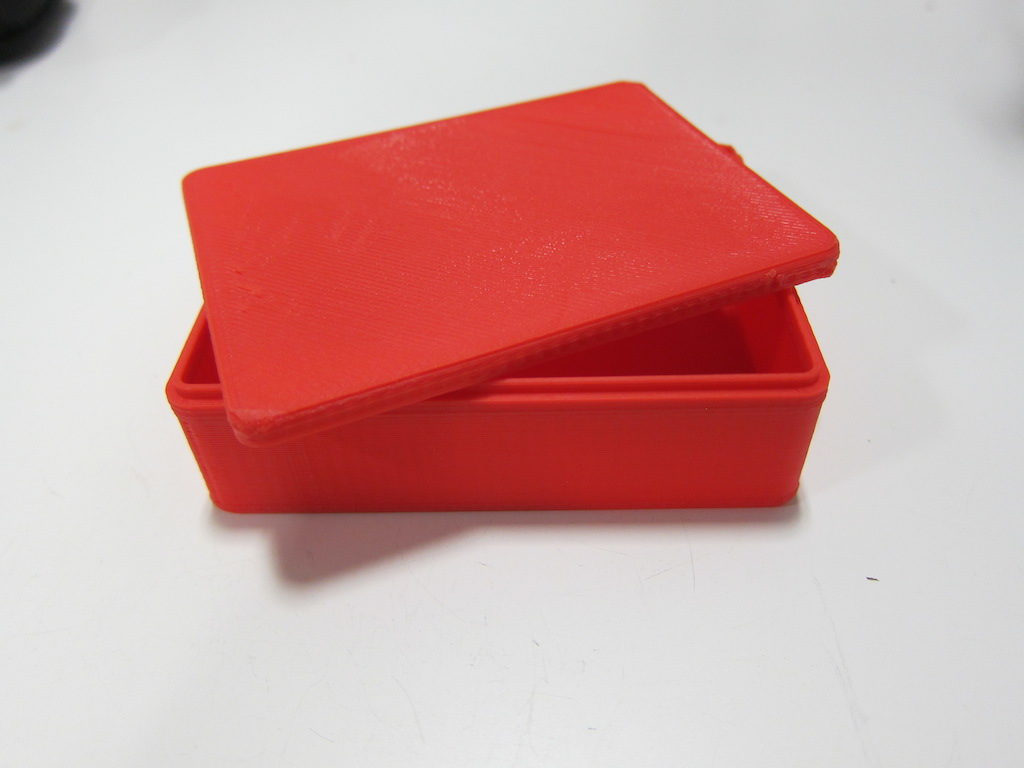