3D printed artificial limbs
3D printing prosthetics in 2022: The great revolution
3D Learning Hub
See all categories
Contents:
- Introduction
- Overview of 3D printing in the medical sector
- Why is using 3D printing for prosthetics so interesting?
- They used 3D printing to develop prosthetics
- What is next?
Introduction
Overview of 3D printing in the medical sector
The medical sector benefits from the wide range of advantages offered by Additive Manufacturing. Thanks to the mass-customization opportunities and the flexibility of the manufacturing and design processes, 3D printing becomes a real alternative for this sector. In the future, this manufacturing technology could be used to replace human organ transplants, significantly speed-up surgical procedures, but also produce cheaper and more adaptable versions of required surgical tools. Using technology to rethink and improve the way we produce medical devices leads to great opportunities.
This technology can also improve the lives of those reliant on prosthetic limbs. That is a fact, we can notice a growing interest in adapted orthopedic insoles, orthosis, and prosthetics manufactured using additive manufacturing.
Why is using 3D printing for prosthetics so interesting?
Manufacturing prosthetic is expensive
Thanks to the constant evolution of 3D printing technologies, the medical industry is facing new challenges. In its own way, 3D printing is revolutionizing the field of rehabilitative medicine and tackling a particular issue: prosthetics. According to NGO LIMBS, only 5% of the nearly 40 million amputees in the developing world have access to prosthetic devices or assistance. Many companies such as Unyq are using the advantages of generative design and additive manufacturing to create a brand new approach to prosthetics both in terms of form and functionality. Indeed, some companies are focusing on bringing these advantages to the developing world, to the amputees in environments that lack the medical infrastructure or resources. The goal here is to support the labor-intensive and expensive prospect of traditional prosthetic manufacturing.
Manufacturing adapted and quality devices for amputees is actually a struggle all over the world, as these prosthetics are expensive and most of the time, poorly adapted to the patient’s particularities. New technologies such as this one can also be a major advantage for prosthetists, helping them in the development of customizable prostheses. From the creation of 3D printed prosthetic hands to functional wrists, solutions can be offered with additive manufacturing. Engineers and researchers are opening new possibilities for prosthetics
Advantages of 3D printing prosthetics
- Innovation: Innovate without worrying about the limitations of traditional manufacturing
Thanks to 3D printers, rapid prototyping has never been so easy. Iterate your ideas and projects faster thanks to this technology. Going further than traditional prosthetics manufacturing will enable great future developments.
- Customization: Create adapted prosthetics
The customization part is the most important argument here. Getting adapted devices and prosthetics will benefit the patients and improve their quality of life during a limb loss. Customizable functional prostheses creation is now possible thanks to 3D printers.
- Cost: Why are 3D printed prosthetics cheaper?
Once again, developing such a complex project as prosthetics is expensive with traditional manufacturing techniques. Especially if you want to adapt it to the morphology of the patient, additive manufacturing appears to be the most efficient technique to get low-cost prosthetics. It is becoming a life-changing solution to produce prosthetics in areas where the access to such devices is complicated, or impossible.
No minimum of order, no need to build an expensive mold, you only need a 3D file to print your project. Prosthetics are better, and more efficient while custom-made. However, customization is quite expensive with traditional manufacturing.
They used 3D printing to develop prosthetics
Several 3D printed prosthetics projects have already been developed all around the world. See how 3D printing materials and technologies are helping to create functional artificial limbs. Here are a few examples of 3D printed prosthetics:
3D printed prosthetic arm providing feedbacks
Lorenzo Spreafico is a student at the University of Leeds. He created a prosthetic arm with vibrotactile feedback.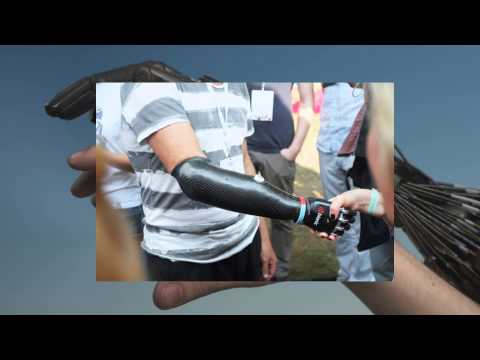
Hand prosthetics
This might not come as a surprise to you, but it is a topic worth mentioning. According to research done by Amputee Coalition, on average there is an amputation done every 30 seconds, and life after such a procedure is hard. But there are people out there using the latest technology innovations to help others. E-nable is a global network of passionate volunteers who help amputees.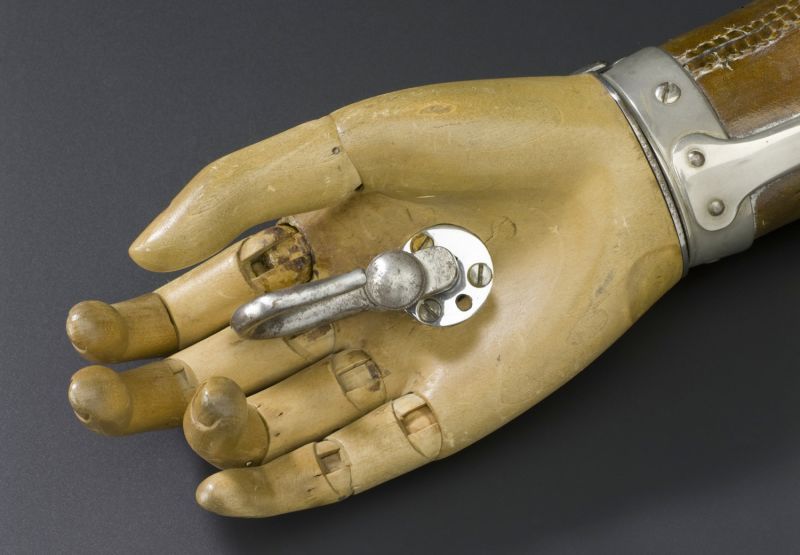
Leg prosthetics
Looking absolutely stunning and even impossible Exo by William Root breaks the boundaries of logic. He brings a new level of the esthetics of prostheses. His prosthetic leg is not only beautiful but also fully functional. First of all the designer improved the time-consuming process of manufacturing a prosthesis. Normally, the amputee had to have a mold done of his limb, then a cast was made, vacuum form, check for fit, assembly, and then adjustments were done.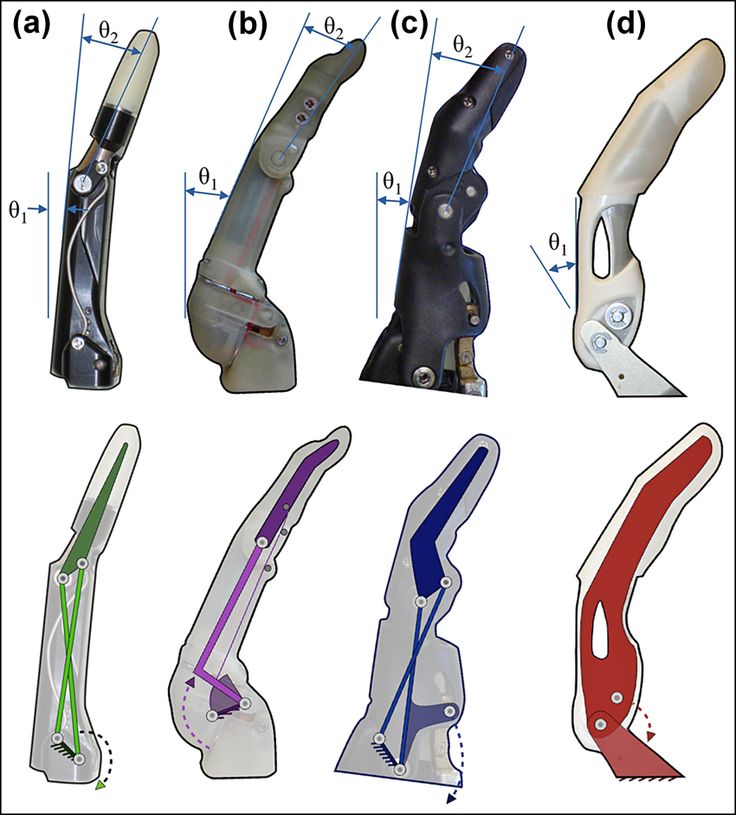
Hero Arm
Hero Arm is a project developed by Open Bionics, who aims to turn disabilities into superpowers with 3D printed bionic arms for children and adults. Using Selective Laser Sintering 3D printing, with Nylon PA12, they develop prosthetics covers inspired by superheroes such as Iron Man, or fictional universes such as Star-Wars or Frozen.Manufacturing prosthetics in remote areas
Guillermo Martínez is the founder of Ayúdame3D, he went from building robots to building prosthetics hands. At first, it was just for fun, and now, Guillermo Martínez helps people in Kenya by developing prosthetic limbs helping amputees living a more normal life.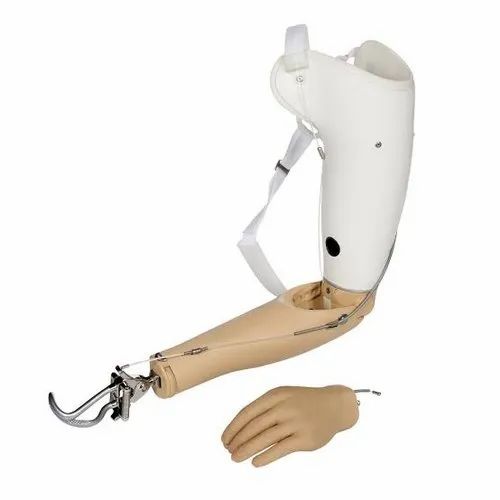
Millie: the first-ever dog with a 3D printed prosthetic leg in Australia
People are not the only ones whose lives changed thanks to Additive Manufacturing. We already talked about a few animals such as a penguin and a duck with a prosthesis, now it’s time for Millie, the greyhound from Australia. She’s a rescue dog, which was kicked out because of a bad paw. Unfortunately, professional prosthetics cost 10 000$ and they are not as personalized. The owners turned to Autodesk, a leader in 3D modeling and CAD software. With Fusion 360 they designed a new, ideally-fitting prosthesis and then 3D printed it.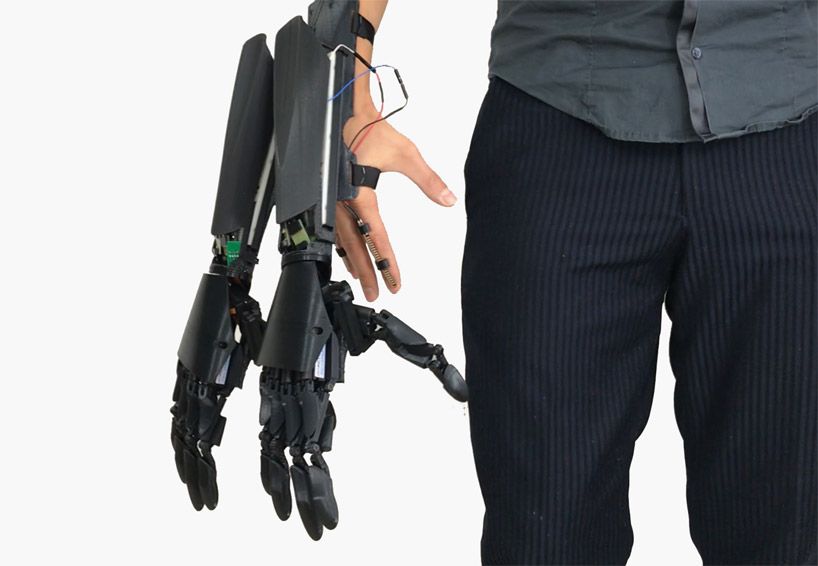
What is next?
The future of 3D printed prosthetics
It is definitely bright! As you’ve seen in this article, the presented examples show how beneficial Additive Manufacturing is to the medical industry. 3D printing prosthetics are cheaper by thousands of dollars. They are also much more comfortable, fitting exactly the limb, not causing pain to the user, and they are highly customized. This level of personalization has never been achievable before.
Do you have a prosthetics manufacturing project?
Using an online service bureau such as Sculpteo, there is no minimum order quantity, from a single object to 10 000+ parts, you can 3D print the exact amount of parts you need. With 10+ years of expertise in additive manufacturing for production and prototyping, Sculpteo is also offering rigorous quality control. With our online 3D printing service, you get professional 3D printing at your fingertips with +75 materials and finishes to develop your most ambitious projects, such as prosthetics. We’ll take care of the rest in our industrial ISO 9001 factory.
Upload your 3D file and get your free instant quote!
Any question? Feel free to contact us to discuss your project, our 3D printing expert are here to help you develop your project.
Related Topics
- Return to Top
Get the latest 3D printing news delivered right to your inbox
Subscribe to our weekly newsletter to hear about the latest 3D printing technologies, applications, materials, and software.
3D-printed prosthetic limbs: the next revolution in medicine | 3D printing
John Nhial was barely a teenager when he was grabbed by a Sudanese guerrilla army and forced to become a child soldier. He spent four years fighting, blasting away on guns almost too heavy to hold, until one day the inevitable happened: he was seriously injured, treading on a landmine while he was on morning patrol.
“I stepped on it and it exploded,” he recalled. “It threw me up and down again – and then I tried to look for my leg and found that there was no foot.”
His comrades carried him back to base camp, but there was hardly any medical care available. It took 25 days before he received proper treatment, during which time he developed tetanus down one side of his body. Finally, Nhial (not his real name) was put on a flight to the Kenyan border, his life only saved when he was handed over to a Red Cross team.
Now, a decade later, he lives in a Juba refugee camp, having suffered further troubles in the conflict that has engulfed the struggling new nation of South Sudan. He plays wheelchair basketball for his country, although he relies on a prosthetic lower leg to struggle around the muddy, sprawling camp. Reaching the most basic services often entails long walks and it can be difficult to get to training. But at least his hands are free to carry things such as food and water, unlike those on crutches.
Such stories of lives devastated by conflict or disease are all too common in developing countries. Lack of an arm or leg can be tough anywhere, but for people in poorer parts of the world it is especially challenging. Some are victims of conflict, while others may have been born with congenital conditions. Many more are injured on roads, with the casualty toll soaring in poorer nations. In Kenya, half the patients on surgical wards have road injuries. The World Health Organization estimates there are about 30 million people like Nhial who require prosthetic limbs, braces or other mobility devices, yet less than 20% have them.
Prosthetics can involve a lot of work and expertise to produce and fit and the WHO says there is currently a shortage of 40,000 trained prosthetists in poorer countries. There is also the time and financial cost to patients, who may have to travel long distances for treatment that can take five days – to assess their need, produce a prosthesis and fit it to the residual limb. The result is that braces and artificial limbs are among the most desperately needed medical devices. However, technology may be hurtling to the rescue – in the shape of 3D printing.
Slowly but surely, 3D printing, also known as additive manufacturing, has been revolutionising aspects of medicine since the start of the century, just as it has had an impact on so many other industries, from cars to clothing. Perhaps this is not surprising, given that its key benefit is to enable the rapid and cost-efficient creation of bespoke products. There are few commercial products that need to suit a wider variety of shapes and sizes than medical devices made for human beings.
Experts have developed 3D-printed skin for burn victims, airway splints for infants, facial reconstruction parts for cancer patients, orthopaedic implants for pensioners. The fast-developing technology has churned out more than 60m customised hearing-aid shells and ear moulds, while it is daily producing thousands of dental crowns and bridges from digital scans of teeth, replacing the traditional wax modelling methods used for centuries.
Jaw surgery and knee replacement operations are also routinely carried out using surgical guides printed on the machines. So it is no surprise that the technology has begun to stir interest in the field of prosthetics, even if sometimes by accident. Ivan Owen is an American artist who likes to make “weird, nerdy gadgets” for use in puppetry and budget horror movies. In 2011, he created a simple metal mechanical hand for a steampunk convention, the spiky fingers operated by loops pulled through his own.
He posted a video that was seen by a carpenter in South Africa who had just lost four fingers in a circular-saw accident. They began discussing plans for a prototype prosthetic hand and that came to the attention of the mother of a five-year-old boy, called Liam, who had been born without fingers on his right hand.
She wanted a tiny version of their hand, but Owen realised the child would rapidly grow out of anything they made, so he looked at the idea of using 3D printing. “If we could develop a design that was printable, it would be possible to rescale and reprint the design as Liam grew, essentially making it possible for his device to grow with him,” he said.
So the artist persuaded a printer manufacturer to donate two machines and developed what has been claimed to be the first 3D-printed mechanical hand. Crucially, rather than patent this work, Owen published the files as open source for anybody to access, allowing others to collaborate on, use and improve the designs.
This has grown into Enabling the Future, a network with 7,000 members in dozens of countries and access to 2,000 printers, who help make arms and hands for those in need. One school student in California even printed a new hand for a local teacher.
Often they are aimed at children, since many dislike the weight, look and hassle of modern prosthetics, which can involve inserting the arm into a silicone sleeve and using straps across the back to hold the device in place.
These body-powered hands cost thousands of pounds, yet must be replaced every couple of years as a child grows. The 3D-printed versions cost about £40, come in any colour and look like a cheery toy, so are often more appealing despite being less sophisticated.
Jorge Zuniga, a research scientist in the biomechanics research department at the University of Nebraska in Omaha, heard about this project on his car radio. He was only half-listening, but on arriving home he started playing baseball with his four-year-old son and observed how important the grabbing of an object was to his child’s development.
A Cyborg Beast prosthetic hand.He spent the next month carefully building a prosthetic model that mimicked the human hand, only for his work to be dismissed instantly by his son. “He told me children wanted a hand that looked like a robot.”
From this conversation and the open-source designs emerged Cyborg Beast, a project heavily backed by Zuniga’s department to develop futuristic-looking, low-cost prosthetic hands. “You can do anything with 3D printing,” said Zuniga, who now leads a seven-strong team. “We believe it will revolutionise the prosthetics field. It will lower the costs worldwide and gives engineers, patients and doctors the chance to modify prosthetic hands as they want. And they can be any colour.”
When I told Zuniga, slightly hesitantly, that his design looked like a toy, he was delighted. “That’s great – we want children to see it as a toy,” he said. “This is a transitional device. Many children do not like prosthetics, however good they are these days, because they might have a hook for a hand and they need help to put the harness on, which children dislike. So this is to bridge the gap, helping them get used to the idea as they grow up.”
“We have even had a child missing a shoulder. So we developed a device that weighs the same as the missing arm. This meant he not only got a new arm that helped daily life but it also improved his posture and balance, therefore was much better for his spine. This sort of thing can be done much easier with 3D technology.”
It is remarkable that people who do not even own a printer can obtain a functional child’s hand for the price of a theatre ticket within 24 hours. Zuniga says at least 500 Cyborg Beasts are in use worldwide and the design has been downloaded more than 48,000 times. He has taken it to his native Chile, where he runs a paediatric orthopaedic 3D-printing laboratory, and has had recent requests for the plans from Nigeria.
“My concern at this stage is that some of the materials can melt in higher temperatures. It is not working well there yet, but this sort of prosthetic has huge potential to be used with better materials in the developing world. We are still in the infancy stage at this moment.”
Another scheme experimenting with this technology is Project Daniel in the Nuba mountains of Sudan, where in the middle of the ongoing civil war an American physician, Tom Catena, has been working as the only permanent doctor for half-a-million people around his Mother of Mercy hospital. Fuelled by his religious faith, for almost a decade this brave medic has ignored bombings, a lack of electricity and water shortages to do everything from delivering babies to amputating limbs.
“It’s demoralising for us to amputate an arm knowing that there is no good solution,” Catena told me by email. “We have many arm amputees – both above and below the elbow as a result of the war here and general lack of medical care. This in an agricultural society, where nearly everyone is a subsistence farmer. If one is missing an arm, he is not very functional in this society.They become totally dependent on the family and have a difficult time getting married [which is also very important in this society].”
The idea of using 3D printing to help arose when Mick Ebeling, an American film producer and philanthropist, learned about the Mother of Mercy hospital at the same time as he was hearing about the emerging work on low-cost prosthetic hands. Searching for information on Catena, Ebeling read about one of his patients: Daniel Omar, a 12-year-old boy who had wrapped his arms around a tree to protect himself during an aerial attack. His face and body were protected when a bomb exploded nearby, but both the boy’s arms were blown off.
You can’t just smash in these new technologies, but if we get this right the growth could be exponentialMatt Ratto, Nia Technologies
Ebeling travelled out to the Nuba mountains with 3D printers and, working with hospital staff, fitted about a dozen people with new arms. “Unfortunately, as time went on, none of the amputees was using the prostheses as they felt they were too cumbersome,” said Catena. The doctor concluded: “The 3D model was good, fairly easy to make and inexpensive… although it hasn’t worked out so well here. Perhaps with some tweaking, the 3D printers can be of great use for arm amputees.”
Yet for all the agonies and difficulties associated with arm loss, the bigger problem in poorer countries is when lower limb disability leads to a loss of mobility. Wheelchairs are expensive and can be difficult to use when roads are potholed, streets are muddy and pavements are nonexistent. Without a prosthetic limb, people struggle to fetch water, prepare food and, above all, to work. This throws them back on their families and communities, intensifying any hardship and poverty.
One group that has spent almost three decades trying to tackle these issues is Exceed, a British charity set up by diplomats and academics at the request of Cambodia’s government to help thousands of landmine survivors. It works in five Asian countries, training people at schools of prosthetics and orthotics. In Cambodia, there are almost 9,000 landmine survivors in need of artificial limbs, although these days traffic accidents are a more likely cause of disability, while children also need braces for a range of common conditions such as spina bifida, cerebral palsy and polio.
“If you wear a prosthesis, you are disabled for about 10 minutes in the morning while you have a shower, then you put your leg on and go to work. If you do not have one, then your hands are out of use with crutches so you can’t even take drinks to the table,” said Carson Harte, a prosthetist and the chief executive of Exceed. “Without a prosthesis, there are no expectations. You just go back and rely on the goodwill of your family.”
It is not really a lack of money that denies people these devices, since simplified forms cost little and generic Chinese models are improving fast. The components can cost just £30. The big hurdle is the lack of trained technicians to fit the artificial limbs. In the Philippines, there are estimated to be 2 million people needing prosthetics or orthotics. However, there are only nine fully trained experts, each able to treat 400 patients a year, at most, although more are being trained on a new four-year course.
Orthopaedic technician Moses Kaweesa assembles a 3D-printed artificial leg at CoRSU hospital in Uganda. Photograph: Isaac Kasamani/AFP/Getty ImagesTraditionally, a prosthetist would wrap a stump with plaster of Paris bandages to make a reverse mould and let it dry, then fill it with more plaster that must harden. From this, a socket can be forged that fits, with more modifications for precision, to the bone on the stump. Great care must be taken to avoid nerves and tender areas that are not tolerant of pressure.
The key for the technician is to understand the pathology of a stump, which differs for each person. This is a cumbersome process that can take a week, especially with physical therapy for new patients that lasts three days. It can also be messy work, mixing up and moulding the plaster, while a prosthetist visiting a rural area must transport 20-kilo packs of plaster. With a 3D scanner, a digital image can be made in half an hour and sent by email.
Exceed has begun a seven-month trial of 3D-printed devices in Cambodia with Nia Technologies, an innovative Canadian not-for-profit organisation. “This technology has the potential to increase the productivity of every technician,” said Harte. “It is not about printing off legs, nor does it replace the skills of a well-trained professional, but it has potential to produce a better, faster, more easily repeatable way of doing one key part of the chain. There are no magic bullets, but this may be an important incremental change.”
Nia is also trialling its 3D PrintAbility technology in Tanzania and Uganda, where there are only 12 prosthetists to serve a population of about 40 million people; at the time of writing, all six state clinics have run out of materials. Doctors there often deal with children who have lost limbs after falling into open cooking fires, while other youngsters need braces after suffering post-injection paralysis caused by badly administered jabs that damage nerves.
In Uganda, its team is working with CoRSU hospital in Kisubi, a specialist rehabilitation centre for children with disabilities. Orthopaedic technician Moses Kaweesa said they found the technology lighter and faster to use, as well as easier for people in remote rural areas. “It used to take five days to have a limb manufactured, with lots of hanging around for the patient. Now, it is barely two days, so they spend much less time in the hospital. There is also less waste of material, so for a country like ours this can help so much by cutting down the costs.”
The first person to test out a 3D-printed mobility device at the hospital was a four-year-old girl who until then had dragged herself across floors and had to be carried around by her family. “When she was born, her right leg was missing the foot,” said her older brother. “It was very difficult for her to walk, to play with other children. She can be lonely. But when she was given a leg she was able to run with others, play with others.”
Matt Ratto, Nia’s chief science officer, who led the project’s development, admitted that it was only when he saw the serious-looking child in her red dress start to walk that he realised his technology actually worked. But, like Harte, he urges caution. “We are surrounded by the hype of 3D printing with crazy, ridiculous claims being made,” he said. “We must be cautious. A lot of these technologies fail not for engineering reasons but because they are not designed for the developing world. You can’t just smash in these new technologies.”
Ratto’s aim is to use the technology to fit 8,000 people with 3D-printed mobility devices within five years, across some 20 sites in poorer countries. “If we get this right the growth could be exponential. If we iron out the kinks, and work out the best way to help clinicians, I think we will see something of a hockey stick curve on the graph. But we must not get it wrong, move too fast nor over-hype the potential.”
This article first appeared on Mosaic and is republished here under a Creative Commons licence
A 3D printed leg costs $100. The prosthesis is always individual, it must take into account the personal characteristics and needs of the consumer, be durable, serving the owner for a number of years, and at the same time relatively light and comfortable. All these requirements are not easy to meet, and the manufacture of a prosthesis is delayed for weeks, or even months, and is quite expensive even in the developed countries of the world.
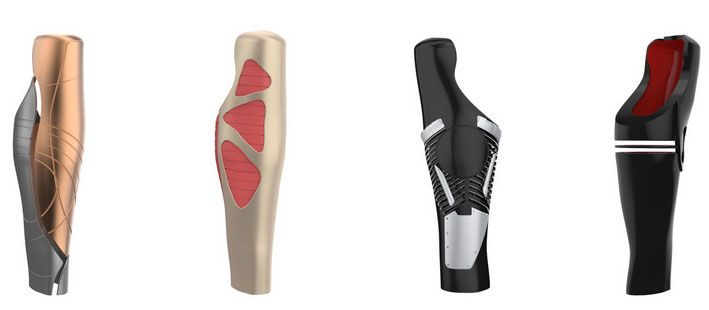
The situation is more complicated for children: firstly, they grow up, and secondly, they break things more often than adults, which means that dentures have to be replaced regularly, and this becomes a difficult financial burden for the family or insurance authorities if the replacement of the denture is covered insurance.
Apparently, the future is not far away when many of these difficulties will be left behind.
Bioengineers from the Japanese company SHC Design have developed a system for 3D printing medical leg prostheses at home. One of the first patients to receive such a prosthesis was 41-year-old Fuminori Ando, who lost his leg below the knee shortly after birth. nine0003
Photo courtesy of wsj.com
He received an artificial leg made of soft and light polymer material, outwardly almost exactly copying the real one, reproducing the natural curve of the heel, and even the distance between the toes. This is important for Ando: he has long dreamed of wearing sandals to match his Japanese-style summer suit.
And one more important advantage: now a man can go to the pool and swim with a beautiful and comfortable artificial leg.
Once he gave up swimming because of the weight and unaesthetic appearance of the old prosthesis. nine0003
A high-quality, custom-made prosthesis costs about $4,200 in Japan. SHC Design senior Yutaka Tokushima predicts the price of a new prosthesis printed on their company's 3D printer to be around $100.
Photo courtesy of wsj.com
This was made possible not only by their development, but also by the creation of a new material - elastic polymer - rubber manufacturer JSR, who joined forces with SHC Design.
So, first, the patient's healthy leg is scanned, then, using a computer program, a template of a symmetrical prosthesis is created that takes into account the parameters of the shoe at the request of the patient, the feeder supplies the material for printing, and after a while, a soft but strong prosthesis is ready. Its low cost will allow the patient to have several spare prostheses for different shoes and different activities.
However, SHC Design is not only going to meet the needs of patients who care about greater comfort and aesthetics. In a poor country like the Philippines, where their 3D printer is currently being tested, nearly 350,000 people need a prosthetic leg and 90% cannot get it because of the high price and lack of specialists.
“I would like to deliver my product to those who are really in need,” says SHC Design CEO Tsuneo Masuda, who founded the company after 26 years of medical device manufacturing experience. The company received subsidies from the Japanese government to develop a system for printing prostheses.
Senior developer Yutaka Tokushima believes that the company will start selling its 3D printers bundled with software in Japan and the Philippines as early as April next year. They will cost $ 2,000, but the scanner will need to be purchased separately from another provider. nine0003
Major prosthesis manufacturers are also interested in 3D printing. Its elements are used by the German company Ottobock, which prints coatings for prostheses that make it possible to hide its mechanical parts from the eye. The Icelandic company Ossur uses 3D printing to create prototypes and some parts of the microprocessor-controlled knee.
Photo from dailycaller.com
The use of a 3D printer is productive not only for printing lower extremities. The Massachusetts Institute of Technology has developed a computer-aided design for a prosthetic hand that can be printed for as little as $50 for the Enable Foundation. nine0003
Bioengineers predict the rapid development of prosthetics using 3D printing. Over time, printing artificial limbs will become as commonplace as printing a document today.
Even a child can print a hand for special needs, such as an extendable one, to effortlessly reach the floor and pick up a dropped object.
The development of new technologies for scanning and modeling body parts, created by companies such as Body Labs (New York), is of great importance in this matter. nine0003
And when 3D printing combines with propulsion systems, integrated sensors and sophisticated algorithms to easily control the prosthesis, artificial limbs will look little different from real ones.
Sources
1
Bird's beak printed in USA using biocompatible resin
Scientists from the University of South Florida (USA) and Formlabs performed a successful operation to replace part of a diseased beak of a rare bird. Doctors operated on a hornbill that lives in the Tampa City Zoo, Florida. The animal suffered from skin cancer, which is fatal to this type of bird; as a result of cancer, the part of the beak that covers the nasal sinuses was damaged. Specialists scanned the skull of the animal, made a prosthesis based on a special resin and installed it in place. nine0067 According to doctors, after the operation, the bird recovered quickly, the surgical intervention did not affect her appetite and habits. After some time, the protective mask printed on a 3D printer acquired the color of a beak, which became possible due to the secretions of special glands produced by the body of hornbills. The inventors of a medical 3D printer and a biocompatible resin said that in the future it is possible to use prostheses and artificial organs created individually for each patient with a specific disease. nine0003
3D printed hornbill implant
Photo: ZooTampa at Lowry Park
2
3D printing solves the problem of creating high-quality and affordable prostheses
Experts estimate that hundreds of thousands of people lose limbs and become waiting for a prosthesis. Mass-market prostheses are only available in a few sizes, so wearers have to adapt to the features of the medical equipment. In addition, they are short-lived and expensive to manufacture. 3D printing allows you to create an almost perfect prosthesis according to individual drawings. In this case, he can successfully replace the lost arm or leg. nine0067 Also, prosthetic services are usually available to patients in the developed world with good health insurance. Formlabs experts note that the problem lies in the lack of manufacturing processes that allow the production of non-standard parts at an affordable price. 3D printing could make prosthetics more affordable. For example, the non-profit initiative e-NABLE offers free blueprints, mockups, and open source programs to create medical devices using printers. In this case, the cost of one custom-made prosthesis can be only about $50. nine0003
3
Medical 3D printing requires a special resin that is compatible with living organisms
Modern 3D printers print blanks based on photopolymer resin, a special liquid substance that hardens when exposed to light. In medical printing, everything is much more serious, since it is believed that a person will be in direct contact with an object created using a 3D printer for quite a long time. Scientists explain that printed prostheses must have an ideal shape, taking into account the structural features of the body, and also consist of safe materials that will not cause an allergic reaction or rejection. nine0067 “The importance of 3D printing in healthcare cannot be overestimated,” says Gaurav Manchanda, director of medical market development at Formlabs. For example, medical "live" resin essentially resembles the material for printing conventional 3D blanks, but differs in detail from them. Firstly, it allows you to print more accurate objects - about a hundred microns in size. Secondly, it is designed for prolonged contact with the skin or mucous membranes. Thirdly, the resin can be given absolutely any shade, which is especially important in dentistry. For example, Formlabs has BioMed Clear Resin, which has a high degree of transparency, which may be required to produce parts that show internal anatomy. nine0003
4
3D printing will eliminate organ transplants
When organ transplants are needed, patients may face the same problem as when creating a prosthesis: the supply of suitable biomaterials is extremely limited, and the cost of transplantation is very high. In addition, the body may not accept a new organ, in which case the efforts to find a donor and prepare the patient for surgery will go down the drain. Theoretical medicine proposes to create the necessary organs on order, literally printing them on the basis of the patient's biomaterial. nine0067 Experts describe the use of bio-ink, a special material and a kind of raw material for medical 3D printers. Bio-ink is created using tissue engineering techniques based on samples received from the patient. Doctors take a part of the patient's tissue and place it in a bioreactor, where, with the help of nutrients, the material acquires the mechanical and biological properties of organic tissue. Bioengineers can direct cell growth in such a way that the desired tissue or organ type is obtained as a result. The probability that the resulting organ will take root in the patient's body is extremely high. Also, scientists from around the world offer to grow organs in the body of animals. According to Genotek CEO Valery Ilyinsky, such technologies will become a reality in five to ten years. However, the production of individual kidneys, liver or heart based on the patient's biomaterial still seems to be a more reliable way to replace a damaged organ - due to the maximum compatibility of the printed organ and the patient's body.