3D level scanner for silos
APM 3D - Level - 3D Level Scanner by Echo Process ...
APM 3D - Level - 3D Level Scanner by Echo Process ...- Home breadcrumb
- Companies
- Echo Process Instrumentation, Inc.
- Products
- Model APM 3D - 3D Level Scanner
From Level
0
Share Share with Facebook Share with Tweeter Share with LinkedIn
The 3D Level Scanner - Model S determines the average volume of bulk solids stored in small silos with diameters up to 4 or 5 meters (13 - 16 feet) and height up to 70 meters (230 feet). The 3D Level Scanner - Model M maps the entire surface area of practically any kind of bulk solids stored in large silos, open bins and stockpiles (up to 15 meters / 49 feet in diameter and heights of up to 70 meters / 230 feet), and generates highly accurate measurements of the level and volume of the contents.
The 3D Level Scanner - Model MV maps the entire surface area of practically any kind of bulk solids stored in large silos, open bins and stockpiles(up to 15 meters / 49 feet in diameter and heights of up to 70 meters / 230 feet), and generates highly accurate measures of the level and volume of the contents.
All models incorporate APM's proprietary non-contact dust-penetrating technology enabling it to overcome the challenges of harsh, dusty environments regardless of the type or characteristics of the material being stored. APM software provides a3D representation of the contents- including material build-up and other irregularities that form over time - for display on remote screens to facilitate timely intervention and maintenance.
- Real Level Measurement
- Non-Contact Dust Penetrating
- Patented Self-Cleaning Technology
- Works With Any Dielectric Constant
- LCD Wizard Configuration
- Housing & Antenna: Painted Aluminum die cast
- Ambient, Storage, transport and process temperature: -40...85ºC (-104...185ºF)
- Vessel pressure: 0.2...3 bar (-2.9...43.5 PSI)
- LCD: 4 lines x 20 characters
- Adjustment elements: 4 keys
- Supply Voltage: 18...32 VDC
- Power Consumption: max 1.5W @ 24VDC
- Protection: IP67 according to IEC 60529
- Measuring Range: 70m (230ft)
- Beam Angle: 15 degrees
- Frequency: 4.5 KHz
- Reaction/Setting Time: < 5 s (dependent on the parameter adjustment)
3D Silo Measurement by indurad
iSilo 3D Measurement
Your one-stop-shop for silo inventory
Stop being disconnected from your inventory
1.
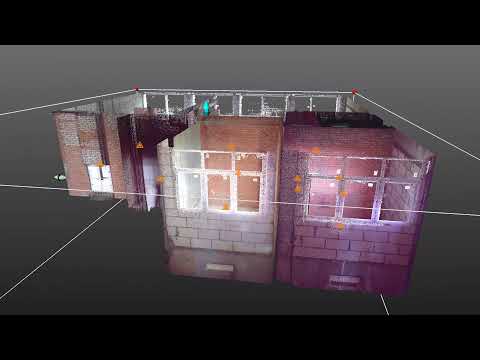
Eliminate delayed or inaccurate inventory informations and make better informed decisions.
2. Buffer zone warning & feeder control
At all times, your PLC and SCADA system has correct detailed inventory information, incl. warnings and alarms.
3. Avoid discharge feed variation
Define individual material zones. Monitor your draw- and feed-points.
4. Material behavior monitoring
You will be surprised how your material behaves in the silo. See & automatically detect ratholes, dump cones, material caking on silo walls, …
5. Trusted Measurement, Reporting and Historical analysis
Play it safe: Receive reliable measurements directly from our tamper-proof solution sent to your business tools. These are generally accepted by auditors as the results are accurate and do not rely on any person taking the measurement.
Get more information
See how easy it is
to get a perfect overview
„Having a digital twin of our silo available in real time allows us to plan the production and shipping process much better. We see if the material starts to stick on the walls and can react. Covering purchases and emergency shutdowns are a thing of the past.
I can‘t tell you how much we save per month“
A.Rachid, Cement Company
EASY TO INSTALL, SIMPLE TO USE, RELIABLE
iSilo 3D starts with robust radar sensors that scan the pile continuously and send the data over Ethernet to our powerful processing unit. The processing unit analyzes the data and sends all outputs directly to your PLC / SCADA systems over the interface of your choice. You can also use a web browser to access a user-friendly interface that provides a real-time, 3D visualization of the material as well as data storage and replay.
3D Radar Sensor
iSDR-P
The indurad Scanning Dynamic Radar - Premium (iSDR-P) is a 3D scanning radar with a field of view of 180˚x120˚ and a Millimeter resolution. The radar sensor covers the entire silo surface, both at low and high silo levels, at distances of up to 40 meters. The main housing parts are milled out of an aluminum block and are eloxated – no compromises are made on durability and longevity. The radar radome is milled out of a special teflon. The housing is IP66 rated / Nema 4x and corrosion resistant. Explosion proof ratings for Zone 20, 21, 22 according to IECEx / ATEX are available for selected sensor models.
The sensor runs on 12-36 volts and is connected via Ethernet to our processing unit (iRPU-F).
Radar Data Processing Unit
iRPU-F
The indurad Radar Processing Unit – Field (iRPU-F) is a compact cabinet which receives data from iSDR sensors via Ethernet and processes all data locally. The cabinet houses a powerful microprocessor, power supply, heater and can be supplied with several interface options (Socket TCP/IP, Ethernet/IP, ProfiNet, OPC, Profibus DP, RS485, RS 422, RS 232, CAN, DeviceNet, Digital I/O, 4..20mA, etc.). Optionally, a Fiber Optic port and remote access via WiFi and/or 4G/5G modem is available. The cabinet is rated IP65 for outdoor use between -20˚C and +50˚C. Optionally available for higher and lower temperatures.
fewer malfunctions, less maintenance
indurad radar sensors outperform ultrasonic, lasers, 1D radar sensors, cameras and human eyes in harsh environmental conditions.
With inventions and innovations, we make a difference.
1D radar sensor often provide little data to deliver an appropriate picture of the stored materials. Besides this, they face issues with multipath propagation in narrow vessels and at steel support beams.
Laser-based solutions are known to deliver accurate results, but often suffer from malfunctions in dusty environments & are naturally maintenance-intensive.
Ultrasonic measurements are frequently distorted by bulk handling particles, drive noise, dust clouds & temperature or pressure fluctuations.
MADE for harsh conditions
It works. Whether hot or cold, snowy or dusty, explosive or corrosive.
indurad sensors have successfully been applied in silos & domes to handle common as well as special commodities.
Ask for case studies
Proven in practice
A&U Wielsbeke
Biomass plant in Belgium.
Peace of Mind
Since we started using iSilo 3D, we no longer have to estimate how full our silos are. We can see it in 3D at any time. This gives us more planning security and peace of mind.
Cement plant
Clinker Silo Greece
At our client site at a cement plant in Greece, knowing the exact fill level 24/7 is key to enable the plant manager to take the right decisions. The clinker silo acts as storage and buffer area between kiln and mill.
Thus, knowing both free capacity and remaining stock is important for a smooth management of upstream and downstream production. With the indurad iSilo solution, the client has this information available at all times. In addition, current dead stock in the silo is finally visible and thus can be taken into account to calculate current available capacity and to take corrective measures like wall cleaning. The indurad radar solution manages to scan where other technologies fail: high temperatures beyond 100°C, dusty environment, and moisture from the material. The sensor requires no regular cleaning or recalibration.
Aluminum Plant
Inventory information & Safety
The customer is an aluminum plant in Iceland. The material (alumina) they receive to feed the operation must be dispatched well in advance as it is delivered by vessels from distant suppliers around the globe.
The alumina is received into a large silo from which material is drawn into the operation. To maximize production, the silo should be close to empty when a ship arrives so that the maximum sized shipment can be received without halting production. To achieve this, precise knowledge of the volume of material in the silos is critical to make the optimal dispatching decisions in a long lead-time environment.
The customer also faced operational challenges when unloading the vessel as there was no information that could be used to adjust the silo’s 17 filling points individually. The material loaded into the silo was sometimes very unevenly distributed. To correct uneven loading, the operators could only slow the loading process to allow the material to slide down to a more even distribution. When the operators were able to see this effect during ship unloading, they were able to adjust different groups of filling points to make the filling more even. This ultimately allowed the customer to reduce unplanned and costly berth times.
Lime Producer
Fast and easy installation
The compact iSilo solution, consisting of a single scanning radar (iSDR-P) and a combined processing and connectivity unit (iRPU-F) provides a complete surface model of the inventory.
Knowing the capacity and deriving the current fill level significantly improves loading and unloading and truck dispatch. The results are significantly reduced cue times and more customer deliveries per day. Especially one factor improves the overall dispatch process, as a loading truck does not have to wait any more until a unloading truck finished his work. So the system now allows simultaneous loading and discharging of the silo.
We are where you need us
Besides our offices, we have a large sales & service partner network – certainly also close to you.
Europe / Headquarter ADDRESS
Belvedereallee 5
52070 Aachen
Germany
CONTACT
Johannes Hornung
Phone: +49 241 538070-90
Email: [email protected]
REGIONS
Germany, Europe, China, India, Middle East, Northern Africa
ADDRESS
Clemente Fabres 1061
Santiago de Chile
Chile
CONTACT
Marcel Giardiná
Phone: +56 9 6630 5037
Email: latinamerica@indurad. com
REGIONS
Chile, Peru, Argentina, Colombia, Mexico
ADDRESS
1200 McGill College Ave. Suite 1100
Montreal, QC, h4B 4G7
Canada
CONTACT
Nicholas Himmelmann
Phone: +1-514-789-9152
Email: [email protected]
REGIONS
Canada, USA
ADDRESS
Suite 3, Level 2
123 Adelaide Terrace
East Perth, WA, 6004
Australia
CONTACT
Fides Pascher
Phone: +61-8-62252512
Email: [email protected]
REGIONS
Australia, Oceania, Southeast Asia
ADDRESS
173 Oxford Road
Floor 2 Suite 135
Rosebank 2196
South Africa
CONTACT
Nicolas Morgan
Email: southafrica@indurad. com
REGIONS
Sub-Saharan Africa
ADDRESS
Rua dos Libaneses, 04
13.271-441 Valinhos SP
Brasil
CONTACT
Vladimir Scarlassara
Phone: +55-19-997750608
Email: [email protected]
REGIONS
Brazil
We’d like to help you
Please provide more information.
Company Name Email* Job title PhoneMy silo details are:
Plant name Diameter (meter) Height (m) Type / Commidity *requiredelevators need non-contact wave 3-D scanners — Elevatorist.

- TOPIC OF THE DAY:
- Agrobusiness of Ukraine pid hour of war
Roman Lukashenko
Spring 22, 2016, 10:34 am
Many elevators need to quickly and accurately determine the amount of grain in the silo. Unfortunately, this is not always possible. With this material, I want to attract the attention of domestic manufacturers. Perhaps someone can help solve our problem. I will explain in detail what is at stake. nine0009
Today 99% of silos in Ukraine are equipped with grain level sensors. These are mainly rotary type sensors that are mounted on one vertical axis. A lower level sensor is installed at the bottom, and an upper level sensor, respectively, at the top. These devices allow the operator to understand the degree of loading of the silo. But they are more suitable for elevators that are focused on long-term storage. There they calmly load the silo, use the upper level sensor to determine that it is already full, and fill the next container. Then, just as calmly, if necessary, everyone is unloaded. nine0009
If the elevator is faced with the task of making as many turns as possible, every day there is prompt loading and unloading, and there are also problems with logistics - there are no wagons and shipments, and the elevator works, as they say, "on suction" - then you have to very quickly look for opportunities to load each silo to the maximum. At the same time, you need to know exactly how much grain is left in the silo, and how much more can be added there.
How is the amount of grain in a silo most often determined today? There are two ways. A person goes upstairs and either looks through the hatch into the silo, or knocks on the wall of the silo with his hand - he determines by the sound: there is emptiness there or there is grain there. Then approximate calculations are made. Those who work at the elevator for a long time know how many tons of grain fit in one "ring" of the silo. And this procedure is carried out every day, sometimes several times. nine0009
It happens that workers make mistakes - dust has accumulated somewhere, a man knocked - it seems empty, but it turns out that there is grain. Or vice versa - it seemed like a full silo, but the grain came off unevenly, and there is free space. Imagine if 10 or more silos are checked... The same situations happen during grain inventory.
What is the best option? To date, there are interesting technologies - 3-D scanners. They are more common in construction, food and processing industries, where there is a need for operational accounting and control of the level of inventories and products. Non-contact 3-D scanners are installed in containers, which scan the surface at regular intervals. Through the controller, they visualize it, and the operator on the computer in 3D format has a picture of the surface of the substance in the tank, with all the irregularities and unprecedented accuracy. nine0009
Such sensors would also help in emergency situations. For example, if the grain hangs on one side and is unloaded unevenly, then there is a danger of the silo falling. Information obtained using 3-D scanners could have prevented an accident.
In a word, the benefits of such devices are very great. But there is one thing - the high cost of this equipment. For example, the cost of a set of scanners and controllers for an elevator with 10 silos is more than 200,000 euros.
It would be good if there were domestic manufacturers who could develop their own, cheaper, sensor. This product would be in great demand. Only we, practitioners, have a few basic requirements for the sensor: it must be moisture-, explosion- and dust-proof and work in conditions of heavy dustiness. nine0009
Our company is ready to test this development and then purchase sensors for all its elevators.
Roman Lukashenko
Related materials
Variant Agro Stroy successfully tested a silo with a diameter of 32 m for snowfall
Installation of operational silos
is being completed at the Voznesensky branch of NIBULONIn Ukraine, there is no method for storing grain in metal silos - expert
More
Editor's Choice
How to choose a grain drying complex: manual
nine0008 Generator for the elevator - how to get rid of that on what to return respectWhy do dryers burn and what work at the same time burn
How to save grain at the elevators in the minds of turning on the electricity
The heat generators of the NEW ELEVATOR help to save money on dry grain
nine0008 Artem Rempen: Logistics "gray" the entire Ukrainian grain market 90,000 LinkedIn 90,001 90,062 (Korean)Italiano (Italian)简体中文 (Chinese (Simplified))Nederlands (Dutch)日本語 (Japanese)Norsk (Norwegian)Polski (Polish)Português (Portuguese)Română (Romanian)Russian (Russian)Svenska (Swedish)Tagalog ( Tagalog)ภาษาไทย (Thai)Türkçe (Turkish)العربية (Arabic)
Urbء المحاولة مورة خرى للصص اليا# أو الال لـship imesز المς nderد مmy المومات
Omlouváme se, nemůžeme najít stránku, kterou hledate.

Vi kan desværre ikke finde den side, du leder efter. Gå tilbage til den forrige side, eller besøg Hjælp for at få flere oplysninger
Gåtil dit feed
Die gewünschte Seite konnte leider nicht gefunden werden. Versuchen Sie, zur vorherigen Seite zurückzukehren, or besuchen Sie unseren Hilfebereich, um mehr zu erfahren.
Zu Ihrem Feed
Uh oh, we can't seem to find the page you're looking for. Try going back to the previous page or see our Help Center for more information
Go to your feednine0065 Vaya, parece que no podemos encontrar la pagina que buscas. Intenta volver a la página anterior o visita nuestro Centro de ayuda para más información. Ir a tu feed
Nous ne trouvons pas la page que vous recherchez.
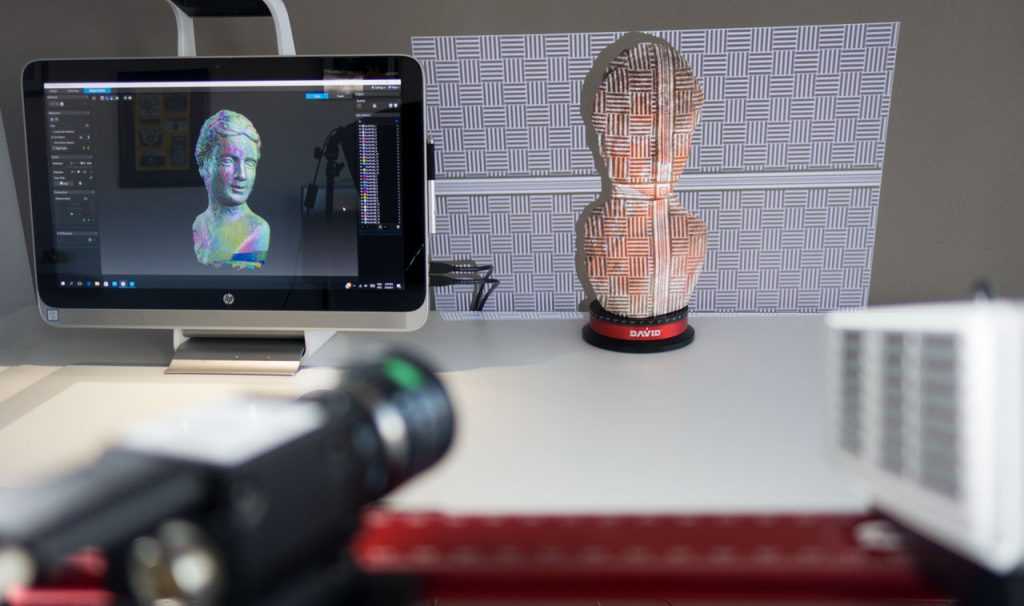
Maaf, sepertinya kami tidak dapat menemukan halaman yang Anda cari. Coba kembali ke halaman sebelumnya atau lihat Pusat Bantuan kami untuk informasi lebih lanjut
Buka feed Anda
Non abbiamo trovato la pagina che stai cercando. Prova a tornare alla pagina precedente o visita il nostro Centro assistenza per saperne di più.
Vai al tuo feed
申し訳 あり ませ ん お 探し の ページ 見つかり ませ ん。 前 の に 戻る か 、 ヘルプセンター 詳細 を ご 確認 ください
원하시는 이전 페이지로 돌아가거나 고객센터에서 자세히 알아보세요.
홈으로 가기nine0065 Harap maaf, kami tidak dapat menemui laman yang ingin anda cari. Cuba kembali ke laman sebelumnya atau lihat Pusat Bantuan kami untuk maklumat lanjut Pergi ke suapan
De pagina waar u naar op zoek bent, kan niet worden gevonden.
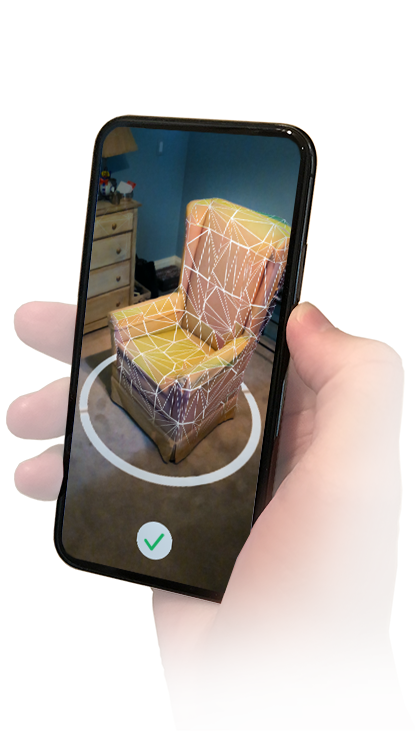
Vi finner ikke siden du leter etter. Gå tilbake til forrige side eller besøk vår brukerstøtte for mer informasjon
Gåtil din feed
Nie możemy znaleźć strony, której szukasz. Spróbuj wrócić do poprzedniej strony lub nasze Centrum pomocy, aby uzyskać więcej informacji
Przejdź do swojego kanalu
A página que você está procurando não foi encontrada. Volte para a página anterior ou visite nossa Central de Ajuda para mais informações
Voltar para seu feed
Ne pare rău, nu găsim pagina pe care o căutatţi. Reveniţi la pagina anterioară sau consultaţi Centrul nostru de asistenţă pentru mai multe informaţii
Accesati fluxul dvs.
The page you are looking for cannot be found.
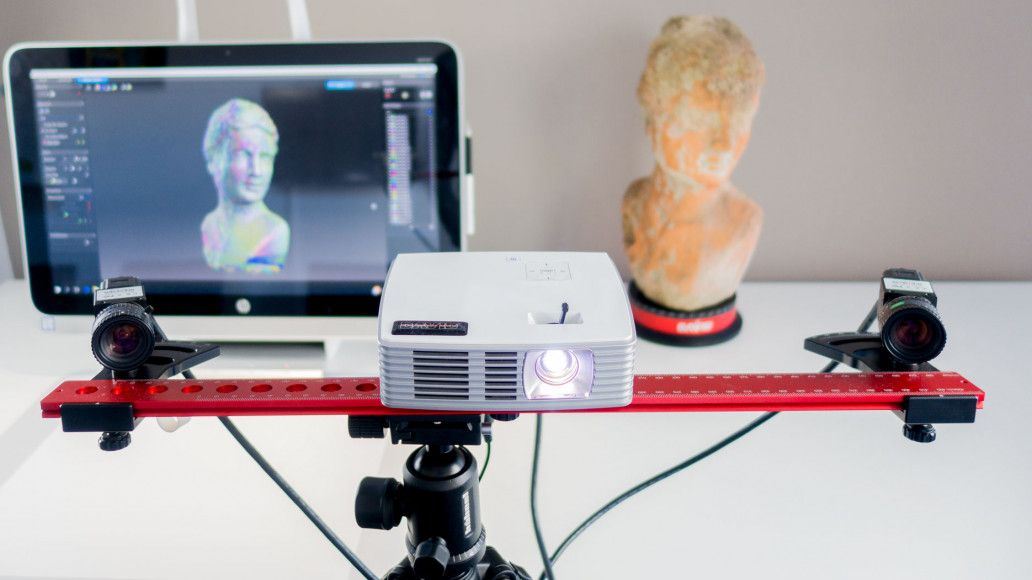