3D print zirconium
3D printing and 3D scanning experts crack the Ocean's 8 diamond necklace heist
0Shares
Ocean’s 8, the latest in the line of star-studded line of Hollywood heist movies, recently made its UK debut yesterday with a 3D printer in a starring role.
Sitting on a desktop in the back of the gang’s workshop, a MakerBot Replicator Z18 seamlessly creates a Cartier diamond necklace that convinces an unwitting Anne Hathaway (Daphne Kluger in the film) that it’s the real thing.
Now, where many tech enthusiasts might grimace at the idea of desktop 3D printer achieving such a remarkable feat, I decided to put together my own crack team of 3D experts and prove how exactly, you could 3D print your own diamond necklace.
3D scanning glasses
In the film, Helen Bonham Carter (playing Rose Weil) completes a 3D scan of the original Cartier necklace using a pair of regular-glass spectacles. The data, a blemish-free CAD file, is then wirelessly transmitted to the rest of the team ready to 3D print.
Though Bonham Carter has gone for a more classic Wayfairer style of frame in the film, the 3D scanning glasses did remind me of something…
The Artec Leo 3D scanner at TCT 2017. Photo by Michael PetchThe Leo is a handheld 3D scanner made by Artec3D. According to Andrei Vakulenko, Artec’s Chief Business Development Officer, the solution is simple: “All that is left to do is to reduce our Artec Leo handheld 3D scanner to the size of a pair of glasses and develop a way of sending the file over WiFi at a speed of hundreds of gigabytes per minute,” he explains. “At the moment this takes several hours. But all is coming soon.”
Florian Bommier, application engineer at SHINING 3D, suggests a plan for the design of the glasses; “2 cameras would be on the side of the glasses,” i.e. hidden in the classic pins either side of Wayfarer glasses, “and the projector on the center. ” However he points out, “We would need to change the projector to work with infrared to make the projected pattern invisible to human eye.”
Hang on, what about the shine?
The inherent sparkle of diamonds certainly does pose a steep challenge to our 3D scanner makers. Short of dusting necklace with a fine powder to dull the luster, Bommier also suggests photogrammetry as a suitable approach.
“This process is commonly used in art and for large scans,” Bommier explains, “Google uses this process [to produce] 3D data of cities.”
CAD sculptor and jewelry designer Morgan Morey, winner of the 2017 3D Printing Industry Awards trophy design competition, also backs the idea. Making a CAD model of a diamond necklace according to Morey, “takes a matter of hours and would only need a half decent picture or diagram.”
Official drawing of the original Cartier replicated in Ocean’s 8.
3D printed diamonds
Though detonation nanodiamonds (produced from an explosive mix of TNT and RDX) may have proved to be a 3D printer’s best friend when added to medical implants, achieving an optically clear and shiny stone on an FFF/FDM 3D printer isn’t technically feasible due to the material’s layers, and plasticity.
Morey explains;
“3D printed stones wouldn’t reflect /refract right even if you foil backed the stones.”
The most effective means of replicating diamonds, at least to an untrained eye, is to use cubic zirconia – a fact picked up on by the use of zirconium in the film. Cubic zirconia stones, Morey points out, can be picked up for “pennies” online.
Making the necklace settings
With the CAD data, photos, diagrams and diamonds in place, all that would be left to do at this is to make the settings for the stones. In a process often performed by CAD jewelry makers, the settings would be 3D printed to the exact specifications, cast in a metal, and plated – a job that could take trained technician/jeweler, like Mindy Kaling/Amita in the film, just a few days to complete.
Et voila! Your 3D printed Cartier diamond necklace is complete.
A replica, non 3D printer, diamond necklace as used in Ocean’s 8. Photo via 2018 Warner Bros. Entertainment Inc./CartierFor more 3D printing exclusive news and interview, subscribe to the 3D Printing Industry newsletter, follow us on Twitter, and like us on Facebook.
Search and post 3D Printing Jobs here.
Featured image shows Anna Hathaway (Daphne Kluger) wearing the Cartier diamond necklace in Ocean’s 8. Photo by Barry Wetcher © 2018 Warner Bros. Entertainment Inc.
Tags Andrei Vakulenko artec 3d Cartier Diamonds diamonds are a girl's best friend Florian Bommier jewelry jewelry making Morgan Morey Ocean's 8 shining 3d
Beau Jackson
Korean manufacturer AON Co. Ltd. launches ZIPRO ceramic 3D printer
Who is AON Co. Ltd.?
Based near Seoul in Korea, AON Co., Ltd. is a professional DLP 3D printer manufacturer that has been specializing in the dental industry and its applications for over 10 years.
The company regularly conducts clinical trials at its Research and Development center in order to provide cutting-edge bio-ceramic 3D printers, slurries, and software solutions for the production of artificial teeth.
In 2016, AON Co. started intensively researching and developing an exclusive bio-ceramic liquid material – marketed today under the name INNI-CERA Zirconia slurry – to work with their advanced DLP 3D printers.
Today, AON Co. is launching their new, state-of-the-art ZIPRO Series, replacing the previous INNI lineup.
Meet the brand new AON ZIPRO ceramic 3D printer
AON Co. has built upon its experience with the INNI lineup to provide a brand new series called ZIPRO. Two different versions are available, the ZIPRO Dental and ZIPRO Industrial, to cater to the needs of different types of users.
A few samples of 3D printed zirconia devicesJust as with the INNI series, the Dental version is specifically designed for dental practitioners while the Industrial version suits a broader range of use cases where high-precision ceramic parts are also required.
These top-down DLP 3D printers work with proprietary ZIPROS software that enables professionals to easily upload a file, orient the part, and add automatically generated support structures before slicing and sending the 3D model to the Wi-Fi-enabled ZIPRO printers.
The ZIPRO 3D printer, ZIPROS software, and INNI-CERA materials make for an excellent combinationThe ZIPRO Dental 3D printer is equipped with a Full HD (1920 x 1080p) light projector that precisely controls UV light intensity to print crispy clean layers as thin as 40 micrometers. Its automatic leveling system ensures each layer is uniform before the light is projected onto the slurry.
We must also acknowledge one of the ZIPRO’s most interesting elements: its easy print removal solution. The build plate is punched with a range of small holes in which, after the printing process is complete, a jig can be inserted to easily pop the parts off the plate.
All of the ZIPRO’s features and values are explained in the following presentation video:
INNI-CERA Zirconia slurry
AON Co. developed INNI-CERA Zirconia slurry in-house to provide the highest level of detail and accuracy for the dental industry while respecting international quality standards.
INNI-CERA Zirconia is a Class II material that is KFDA (Korean Food & Drug Safety), CE, ISO, and FDA510(k)-certified.This material is fully biocompatible and offers an optimal flexural strength of up to 1000Mpa, meeting the requirements for extensive or long-span dental restorations.
INNI-CERA Zirconia is also A0/A2-shade-colored to provide a natural-looking base before further staining to match the patient’s natural discoloration. Coloring and staining workflows are offered to help dental labs to get the shades dentists want to have for their patients.
Resin vs Slurry: What’s the difference?
AON Co. emphasizes the fact that their material is a slurry rather than a resin, but what’s the difference between the two?
In 3D printing, the resin is a polymer base in which plastics, metals, or ceramics can be added. Slurry, on the other hand, is a semi-liquid mixture filled with particles of plastics, metals, or ceramics that are suspended in water (no polymer base).
While metal or ceramic-based resins do exist, the term resin is primarily used for polymer and plastic-based stereolithography materials, while the word slurry is more specific to liquid ceramic materials.
A slurry offers a higher concentration of ceramic materials which, furthermore, are uncontaminated by plastics or polymers which aren’t always food-safe or biocompatible.
In addition, parts 3D printed with AON Co.’s INNI-CERA are “green” and must undergo an added sintering step, offering higher strength compared to non-sintered ceramic resin. Generally, sintering parts can cause them to shrink, but AON Co.’s R&D team has worked on providing optimal shrinkage ratios.
Learn more about AON Co. Ltd.’s INNI-CERA slurry.
Clinical trial for trueness evaluation of the internal and marginal fit of Zirconia crown produced by 3D printer at Korea University
AON Co. conducted a study to answer the following question: Can modern additive manufacturing methods replace traditional dental milling techniques?
To do so, their team first analyzed to what extent the trueness* of internal and marginal-fit Zirconia crowns differ when produced via additive and subtractive manufacturing methods, namely:
- CNC milling
- DLP 3D printing
- Laser SLA 3D printing
Trueness: According to ISO, “Trueness” refers to “the closeness of agreement between the arithmetic mean of a large number of test results and the true or accepted value. ”
The R&D team first set an abutment – the interfacing element between the implant (sort of screw that goes into the gum) and the visible crown – for the patient’s right maxillary first molar.
Then, they 3D scanned the abutment and, after cleaning up the 3D data with special software, AON Co.’s researchers were able to design a crown coping (the inner core of a crown) to perfectly fit the abutment.
Once the 3D model of the coping was ready, the team was able to produce it both with additive manufacturing and subtractive manufacturing.
Their manufacturing tools were the following:
- Datron Dynamics’ DATRON D5 dental milling machine
- AON Co’s ZIPRO Dental bio-ceramic DLP 3D printer with INNI-CERA Zirconia slurry
- A 3D CERAM CERAMAKER 900 laser SLA ceramic 3D printer
Once the coping was produced in three copies, one from each machine mentioned above, the team proceeded to 3D scan each copy. The resulting 3D data could then be evaluated by comparing the inner side, outer side, and margin to one another:
External surface | Internal surface | Margin | |
---|---|---|---|
Datron Dynamics | 18.![]() | 17.73±0.6μm | 16.56±1.6μm |
AON Co. Ltd. | 27.26±1.86μm | 26.73±2.73μm | 38.4±1.66μm |
3D CERAM | 40.26±4.06μm | 72.13±0.46μm | 60.26±5.8μm |
While CNC milling unsurprisingly produced the most accurate coping, the tolerances achieved by both additive methods are clinically acceptable, confirming the relevance of AM ceramic systems for such dental applications.
Clinical cases of 3D-printed crowns for patients
3D-printed crown #17
- Date: October 2021
- Dental clinic: Seoul Leaders Dental Clinic(located in Bundang)
- Patient: Song (born in 1964, male)
- # of tooth and color: #17 / A2
- Fabrication method and material: AON’s 3D Printer (ZIPRO)/ Liquid Zirconia Slurry(INNI-CERA)
- Result and feedback
- Patient: no feeling of irritation and resembles natural teeth
- Dental Clinic: excellent strength and good coloring, translucency as required
3D-printed crown #12
- Date: December 2020
- Dental clinic: Seoul Goldplant Dental Clinic(located in Seoul)
- Patient: Kim (born in 1972, male)
- # of tooth and color: #12 / A3.
5
- Fabrication method and material: AON’s 3D Printer (ZIPRO) + PFZ / Liquid Zirconia Slurry(INNI-CERA)
- Result and feedback
- Patient: no feeling of irritation and resembles natural teeth
- Dental Clinic: excellent strength and good coloring, translucency as required
3D-printed crown #37
- Date: July 2022
- Country and city: Australia, Sydney
- Dental clinic: Parramatta Dental Studio(Dr. Andrew Ip)
- Patient: A (born in 1975, male)
- # of tooth and color: #37 / A0 with A3 coloring and staining
- Fabrication method and material: AON’s 3D Printer(ZIPRO-D) / Liquid Zirconia Slurry(INNI-CERA)
- Result and feedback
- Patient: no feeling of irritation and resembles natural teeth
- Dental Clinic: excellent strength and good coloring, translucency as required
Zirconia Dental Membrane
- Zirconia Dental Membrane Implant Project with ZIPRO 3D Printer and INNI-CERA
- Performed by Hong Kong Dentist, Dr.
Brian Chan
- Summary: Zirconia dental membranes have been fabricated with CadCam milling machine, but switched to 3D-print, and printed it with AON’s 3D printer and liquid Zirconia slurry
- Surgery date: March 31, 2022
- Result and feedback
- Easy and quick fabricating the membrane,
- Successful surgery and satisfactory feedback from the patient
What to expect from AON Co. later this year?
AON Co. is developing ZIRWASH aimed to automatically clean up the 3D-printed crowns with IPA liquid, coloring and staining workflows which will help dental labs being jumboized to quickly fabricate strong and beautiful crowns.
The company is also reportedly working on a new, highly translucent slurry to widen the possibilities for dental practitioners, which will be able to stain their devices from scratch and provide an even more personalized coloration for their patients.
New from BEGO - Varseo 3D printer! | Megastom
home
News
Milling center equipped with Varseo BEGO 3D printer with improved design and intuitive interface
07/18/2017
DEAR COLLEAGUES AND PARTNERS
WE INVITE YOU TO COOPERATION!
The German Dental Center CAD / CAM GERMAN LAB is equipped with exclusive automatic equipment for the manufacture of precision individual titanium abutments and anatomical crowns from zirconium dioxide with a gap of 10 microns in just 3 working days!
We mill structures and crowns for leading implantation systems: Nobel Replace, Straumann Bonelevel, AstraTech, XiVE and BEGO SEMADOS.
The innovative equipment of the laboratory included a new generation Varseo 3D printer from the German company BEGO with an improved design and an intuitive interface.
The 3D printer is aimed at large full-cycle dental laboratories and is designed to manufacture a wide range of products.
ADVANTAGES
• The specialized module "Open STL file" is designed for all types of dental software.
• Varseo 3D printer's wide range of capabilities allows you to work with a variety of materials.
• DLP technology increases print speed compared to previous laser 3D printing technologies.
• Convenient display for quick access to the necessary functions.
• Simultaneous 3D printing of multiple objects.
A three-dimensional object is created by successively applying two-dimensional layers.
Produced on Varseo BEGO 3D printer:
- partial and complete dental models,
- individual spoons,
- splints or guards,
- orthotics,
- high-precision surgical templates with guide sleeves for the BEGO SEMADOS implant system.
German Dental Center CAD/CAM GERMAN LAB - We make sure that you receive the highest quality dental products.
Director of the GERMAN DENTAL TECHNICAL CENTER CAD/CAMGERMAN LAB, Dentist
Sadovsky Mikhail Andreevich
Order dental products by phone:
+7 (495) 150-32-32
EVENTS
New in section
11.06.2020 - 25.06.2020
Webinar "Guided Surgery with BE GO"0013
04.04.2020
The webinar
16.03.2020
in February and March 2020 took place with the BEGO SEMADOS
23.2020 9000 9000
22 on January 22, on January 22, on January 22, on January 22, on January 22, on January 22, on January 22, on January 22, on January 22, on January 22. BEGO Semados
Mon-Fri
Sat-Sun 09:00-18:00
day off
Everything you need to know about 3D printing in dentistry.
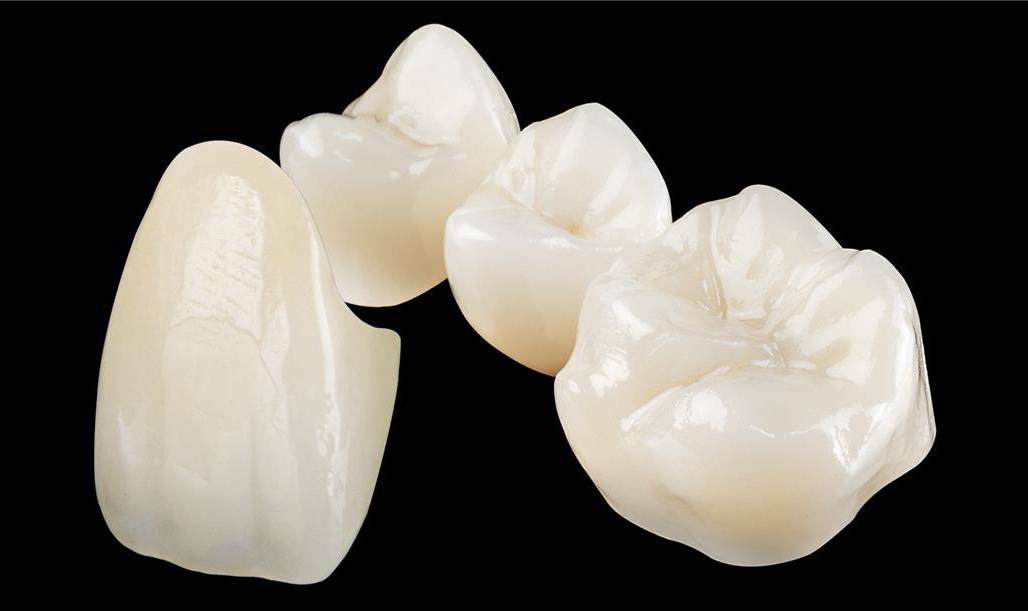
10/16/2017
3D printing is replacing cad cam milling. New digital technology makes it possible to perform more complex tasks that were previously beyond the power of dental technicians. We will tell you more about the advantages of 3D printing before milling, how to choose a 3D printer and which models you should pay attention to in this review.
Advantages of 3D printing over milling
- No waste. One of the main disadvantages of cad cam technology is the large amount of waste. In fact, expensive materials are simply sent to the trash can. 3D printing does not have this drawback: the printer consumes exactly the amount of material needed to produce a specific design.
- Product accuracy. Milling has many limitations related to the features of the tools used, the skill of the technician and the technologies used. At the same time, difficulties in milling, as a rule, arise when processing undercuts and complex structural elements.
3D printing is much more perfect in this regard: almost any dental design can be printed on a printer.
- Operating speed. Milling does not allow to produce several designs at once. With the help of a 3D printer, you can put as many parts into work as you like.
Tips for choosing a 3D printer
The first rule to learn is that universal 3D printers have not yet been invented. That is why, when choosing, it is very important to determine what tasks are to be performed on this equipment.
At the moment, there are two key methods of 3D printing in dental practice. First, we are talking about the polymerization of a photopolymer. The essence of this method is dot layer by layer (SLA), layer by layer (DLP) or inkjet printing. Secondly, laser sintering technology is used, which is performed using a laser installation by step-by-step sintering of the powder. This method can be applied to the production of titanium, cobalt-chromium or plastic products.
The new methods include the polymerization of structures in a continuous mode. In this case, not individual layers are subjected to polymerization, but the entire product. Initially, only one material was used with this technology - plastic with a photoinitiator. To date, the range of materials has increased significantly: from composites for temporary products to zirconium dioxide, which until then had only been milled. In addition, 3D printing allows the use of biocompatible materials - for example, from NextDent, which are used to produce temporary crowns, removable dentures and other dental products.
3D printer affordable
We have to admit that 3D printing has ceased to be something fabulously expensive. 3D equipment is becoming available to almost every clinic, and the cost of portable equipment starts from 3.5 thousand euros, and even primary printers can print designs of varying complexity.
If we talk about specific models, then among the entire range we can note the Form2 model manufactured by Formlabs (USA). The cost of this equipment is quite reasonable, and the functionality is really great. Such equipment easily prints clasp, frames, templates, various models, prostheses, splints, caps, crowns - in a word, a huge range of dental structures.
The advantages of the Form2 3D printer also include a wide working surface (145 x 145 x 175), which allows you to print several products at the same time. It is also important that this printer is characterized by high precision printing along the Z axis, and the well-proven SLA technology is used as a printing method.
As for spending on consumables, on average, one liter costs 225 euros. This material is enough for a huge number of products - the benefits are obvious.
Modern models of 3D printers for sale
Currently, the range of printers has become huge. There are advanced models such as Objet Dental Prime on the market, which are distinguished by unsurpassed product accuracy - up to 100 microns.