3D photo printers
3d Picture Frame - Custom 3d Printing – 3d Picture Print Online
Claim your 5% site wide off Or free 8X8 canvas offer - Sign Up Now!
The Best Photos for 3D Printing
We want your 3D photos to look great, and the first step is to choose a great 2D photo! Some pictures take better advantage of 3D images – here are a few hints to help you choose photos that will bring eye-popping results
Look For Images That Have A Vertical Orientation
The printing process creates images that are more 3D-enhanced from top To bottom, rather than left to right. A picture of LeBron James running down the court will look good – but a picture of LeBron stretching out to dunk will look great!
Look For Pictures With Depth
3D will look better if the subjects are farther from the background. Outdoor pictures tend to look better for this reason, but indoor pics are fine if the walls are far away from the subjects.
Look For Good Foreground Lighting
When possible, use pictures where the foreground is more brightly lit than the background.
With the front ground more brighter than the background, it gives the right focus to the subject in the front of the photo.
If you have questions about a photo, remember that our experts are standing by to help!
Personalized 3D Pictures
Now you can create a sensational custom 3D picture from any photo! These exquisite 3D personalized picture frames are beautiful and last for fifty years or more. Our custom 3D printing process delivers a crisp 3D image that seems to float in the modern black frame. Personalized 3D pictures are a unique choice for.
- Gifts
- Special Occasions
- Just for Fun!
How about a personalized 3D gift for the person who has everything? Customized 3D picture frames make a remarkable addition to any room or a striking decoration for any office. Use our design tool to create your own 3D picture today!
Stunning 3D Picture Frames Bring Your Photos to Life
Imagine your images etched inside a sleek, high-tech frame in mind-blowing 3D! Your photos appear to be floating in space with the illusion of three dimensions. What a marvelous way to commemorate special occasions memorialize a loved one or event. With sizes up to 24”x24”, these heavy, durable frames look great in any room. 3D picture frames are a truly unique expression for your memories.
Features That Magnify 3D Prints
A certain peculiarities make 3D photos the best choice. Here they are
Custom 3D Photo Printing – Now Available for Your Home
New processes in printing technology mean 3D printing is affordable for any home. Lenticular printing on high-quality 3D PET sheets in a stunning modern frame with your custom image “floating” in jaw-dropping 3D. Edge band protection means these heirloom-quality images are as durable as they are lovely. 3D frames are guaranteed for 50 years of indoor use! Washable and waterproof, your memories are safe – and unforgettable – with our 3D printing technology.
Personalized 3D Photos Make Incredible Gifts
What makes a great gift? Personalized? Enduring? Unique? Customized 3D photos are all those things, and more! These lovely frames make great keepsakes for special occasions, gifts for those hard-to-buy-for relatives. With our durable, heavy construction and a sensational 3D image, your friends, family, and co-workers will enjoy 3D photo frames for years to come. 3D photos look great on the wall, on a desk, or even in a trophy case. Make your next gift a spectacular 3D photo frame!
It Really is 3D! 75-80° Visual Angle
You won’t believe your eyes when you see your photos reproduced in a splendid 24” 3D photo frame! Digital 3D photo frames feature a 75-80° visual angle – you’ll be amazed at how the image retains its 3D look from near and far, or at virtually any angle. Your photos seem to come to life! A modern black frame looks great anywhere. Turn any photo into a spellbinding image you and your guests won’t soon forget.
3D Printing from Any Photo
When you see the miraculous sparkle of custom 3D photo printing, you’ll have only one question: Which photo will I choose for a lustrous 3D look? The best news is that 3D printing is remarkably affordable – you can have an array of stunning 3D photos in your home or office. What photo wouldn’t look better, more alluring, floating in a beautiful black frame in three dimensions? Any photo makes a lovely 3D print!
Digital 3D Printing Brings a New Look to Old Photos
Throw those old photo albums away! You’ve never seen your photos look like this! Your photos just got a new lease on life with digital 3D printing. Your guests will be amazed at the hypnotic power of three dimensions when your images are printed with the latest 3D technology. You’ll adore the way these frames look in your home, and you’ll love how easy they are to clean and maintain. These water-proof frames last for fifty years or more! Bring your old photos into the 21st century – in sparkling 3D!
Your Personal Photos Come to Life in Stunning 3D
Take any photo from nice to spectacular with custom 3D printing. Your images have a new look with a phenomenal 3D sheen and set off by a sleek black frame. 3D photo frames add a modern touch to any room in your home or office and they give new life to photos or art. Ever feel like your wall photos are fading into the woodwork? Give your walls a new spark with 3D photo frames!
Customer Gallery
Need inspiration? Check out these great 3D photo ideas from our customers!
@hellosplendidblog created a kid-friendly gallery wall!
@hellosplendidblog created a kid-friendly gallery wall!
@hellosplendidblog created a kid-friendly gallery wall!
@hellosplendidblog created a kid-friendly gallery wall!
Love our 3D photo prints?
Need inspiration? Check out these great 3D photo ideas from our customers!
Framed Prints
Stretched Canvas Print
Metal Prints
Wall Displays
3d Printed Photo - Etsy.de
Etsy is no longer supporting older versions of your web browser in order to ensure that user data remains secure. Please update to the latest version.
Take full advantage of our site features by enabling JavaScript.
Find something memorable, join a community doing good.
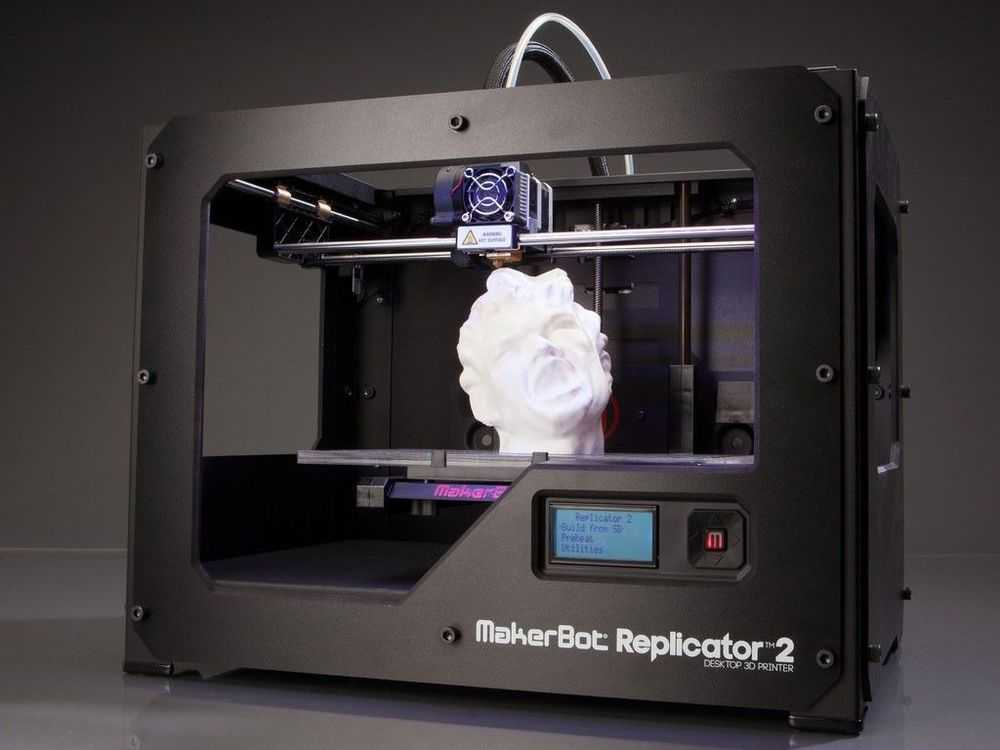
( 1,000+ relevant results, with Ads Sellers looking to grow their business and reach more interested buyers can use Etsy’s advertising platform to promote their items. You’ll see ad results based on factors like relevancy, and the amount sellers pay per click. Learn more. )
3D Printers / Peripherals
Author: Konstantin Afanasiev
Computer technologies are increasingly merging with real life. However, the line between real reality and reality, so to speak, computer or virtual remains. Moving an object from one plane to another is not easy. Of course, if we are talking about text, pictures and other two-dimensional things, then printers and scanners have long made such an exchange a simple and completely ordinary thing. However, in the case of three-dimensional physical objects, everything is much more complicated.
Even technologies that allow you to see a three-dimensional computer model in real volume cannot be called very common (although they are already at the user level both in terms of price and availability). As for the possibility of touching such a model and interacting with it, then so far there is no question of home or amateur use.
And I think that most readers have not even thought about technologies that allow reproducing the model in real material. At best, they heard something out of the corner of their ear. This article will be devoted to such technologies. So to speak, for the general development.
Let's start with the question, why is this needed? Why do you need to take a three-dimensional model of something and make a real object out of it? It turns out there are plenty of uses. The first, and most basic, in the industry - mainly for rapid prototyping - is to see how the model will look in the material. According to a representative of the aerospace company Pratt & Whitney, "the cost of developing a complex product can be greatly reduced if you offer engineers to look at a real part instead of dozens of drawings."
In addition, various tests can be carried out on the finished model even before the final product is ready. What's more, prototypes allow you to perform tests that you can't do on a finished product. For example, Porsche used a transparent plastic model of the 911 GTI transmission to study oil flow during its development. However, the main thing is that such a model can be made very quickly - and in our time of high speeds this is very important. Actually, there is a whole industry of rapid prototyping (Rapid Prototyping - RP), which is precisely engaged in the development and use of volumetric printing technologies for these purposes.
However, prototypes are not everything. The next step is rapid production. Already, some RP technologies allow the manufacture of finished items from various materials. This is an ideal solution for small-scale production, since the standard manufacturing process makes it possible to do anything (within reasonable limits, of course) in a relatively short time. Again, some of the 3D printing technologies allow you to quickly produce molds - well, then the production process is already rolled out. True, prices and availability (as well as the choice of materials) still leave much to be desired.
But in the future, who would refuse the opportunity to quickly make some necessary trifle at home, instead of looking for it in stores or ordering a bottle from a familiar locksmith Uncle Vasya. Actually, here you can draw a direct analogy with systems based on FPGA (that is, on programmable logic), which have made a real revolution (although it may be imperceptible for non-specialists) in electronics. FPGA technology allows you to describe electronic circuits on a computer, and then quickly implement everything described in a standard chip. The same fast prototyping, but for electronics. Moreover, if earlier all this was quite expensive and complicated, now, if desired, you can make anything - a microprocessor, DSP, microcontroller - practically at home. Volumetric printing will allow, in the future, to do the same with conventional production. However, it's time to move on from romantic dreams to the harsh truth of life and what 3D printing is now.
Micromachines
The simplest, cheapest and most affordable devices that claim to be a 3D printer actually have almost nothing to do with printers. We are talking about machine tools with program control. However, if you imagined some kind of screw-cutting monster the size of half a room (I immediately recall labor lessons or the Code of Criminal Procedure), then this is in vain. We are talking about very compact desktop machines, which are called desktop CNC machines (CNC means computer numerically controlled, or, in Russian, a machine with numerical control). These devices can be controlled directly from CAD programs and cut, cut and drill models in the material that are developed in these programs. Materials can be almost anything - from plastic or wood to soft metals (bronze, aluminum). For example, the MicroMill 2000 Desktop Machining System from MicroProto, shown in the picture (this is called a CNC milling machine), connects to a computer instead of a printer, can process a volume of 23x14x15 cm and is able to position the tool with an accuracy of hundredths of a millimeter. Machines aluminum and even mild steels. This wonderful thing costs a little less than $ 2,000.
Desktop multifunctional machine, connects instead of a printer
Part model and finished part made on a CNC machine
Another example of such devices is Roland's MDX line of machines. The older models are designed for semi-industrial use and cost, respectively, around $20K. But the MDX-15 machine is estimated at about $ 3,000 and it can already be categorized as amateur and even home equipment. The MDX-15 also allows you to process various materials up to aluminum and bronze, has a working area of 15x10x6 cm and an accuracy of the order of hundredths of a millimeter. It connects to a computer via a serial port. By the way, Roland supplies a special piezoelectric scanning head to its machines, which allows you to do the reverse transformation - translate real objects into computer three-dimensional models.
Roland MDX 20
Machine at work
There are three main types of CNC machines: routers, mills, and lathes. What a lathe is, I think everyone understands that. And what is the difference between router and mill is easiest to understand from the figure. Of the two devices described above, the first is mill, and the second is router. By the way, machines with four degrees of freedom are also produced - to a certain extent combining the capabilities of mill and lathe. All this technique can be used both for the direct manufacture of objects according to three-dimensional models, and for the preparation of molds for casting - this significantly expands the scope. Other possible uses are engraving, fast PCB fabrication (no photomasks or etching), modeling (anyone who has built a model airframe at least once must hate jigsaw sawing for the rest of their lives), and a host of others. Well, you can get more information on desktop CNC machines at www.desktopcnc.com.
What is the difference between CNC-Mill and CNC-Router
Computerized lathe Flashcut
They use several different technologies. Historically, the so-called stereolithography (StereoLithography or SLA) was developed first.

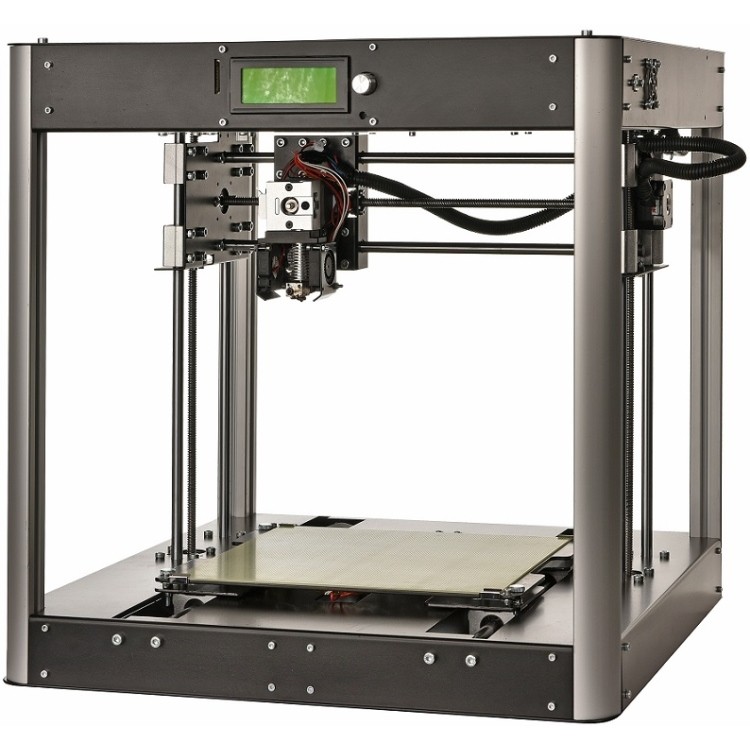
How the SLA machine works
This is what a stereolithography machine looks like from the inside.
CAD model is the same, but already made in plastic using SLA technology
A faster version of this technology was originally developed by Cubital Inc. (Now apparently deceased.) It was called Solid Ground Curing or SGC for short. It also used a photopolymer as a working material, but the illumination was carried out with an ultraviolet lamp immediately for the entire working layer. Illumination was carried out through a photomask, which for each layer was printed on glass using a technology reminiscent of laser printing. Processing the entire layer simultaneously instead of pixel-by-pixel scanning with a laser beam just made it possible to achieve a fairly high speed of building an object. Now a system based on a similar principle is offered, for example, by the German company Envisiontec. The device is called Prefactory (very telling name) and is a rapid prototyping system for the end user. The machine occupies only 0.3 square meters of space, so it can be installed even in a small office. Illumination is produced using DLP (Digital Light Processing) technology, similar to those used in computer projection systems. Resolution (for one working layer) is 1280x1024 pixels at a pixel size of 150 or 90 micron. The thickness of the layers varies from 150 to 50 microns.
The Prefactory can make prototypes around 190x152x230mm and print speeds up to 15mm per hour (height). The printer is controlled by a built-in computer running Linux, and communication with the outside world is via Ehternet via a local network. In fact, you can send jobs to the Prefactory just like you would to a regular network printer.
Envisiontec Prefactory Compact 3D Printer
Laser Sintering
An alternative method of three-dimensional printing is called laser sintering (Selective Laser Sintering - SLS). Here, as you might guess, a laser is also used, but the working material is no longer a photopolymer, but a powder of some relatively low-melting plastic. The plastic in the working volume of the SLS-machine is heated almost to the melting point, and so that it does not catch fire and does not begin to oxidize, nitrogen is supplied to the working zone. Then a powerful laser again draws a section of the part on the plastic powder, the plastic is heated above the melting point and sintered. The next layer is poured on top and the procedure is repeated. At the end of the work, the excess powder is simply shaken off the finished model. This process was developed in the late 80s at the University of Texas at Austin and patented in 1989 by university graduate Carl Deckard. The process was then commercialized by DTM Corp. Laser sintering also provides a fairly high quality parts, although their surface is porous. But the models obtained by the SLS method are the most durable and this technology, in principle, can be used for small-scale production. True, the SLS plant is quite complex and expensive, and the production rate is only a few centimeters (height) per hour (plus several hours to heat up and cool down the plant).
This is how the laser sintering machine works
This is how the SLS machine and parts made in it look like
In addition to good manufacturing accuracy and high strength of the "printouts" obtained, SLS has several other important advantages. First, laser sintering makes it possible to produce models with moving parts - for example, working hinges, push buttons, and so on. Secondly, special materials have been developed for the SLS process, allowing the direct production of metal parts. As a powder, steel microparticles are used here, coated on top with a layer of binding plastic. The sintering of the plastic takes place as usual, and then the "printed" part is fired in an oven. In this case, the plastic burns out, and the freed pores are filled with bronze. The result is an object consisting of 60% steel and the remaining 40% bronze. In terms of its mechanical characteristics, it surpasses aluminum and approaches classic stainless steel. In fact, SLS already now allows the production of full-fledged metal objects, and of arbitrary shape. In addition, there is a similar material with a ceramic or glass core - it can be used to make models that are resistant to high temperatures and aggressive chemicals. If only the process itself wasn't so expensive.
..
Laser sintering model and implementation
Lamination
Another laser 3D printing technology is lamination. It was developed by Helysis and sold under the brand name LOM (Laminated Object Manufacturing). Helysis itself ceased to exist in 2000, and several other manufacturers are now developing their equipment based on its technology. The essence of the technology is as follows - thin sheets of working material are loaded into the machine in turn, from which layers of the future model are then cut out by a laser. After cutting, the layers are glued together. Initially, special paper with a layer of adhesive was used as the material. However, thin plastics, ceramics and even metal foils can also be cut in this way.
The principle of operation of a three-dimensional laminating printer
Inkjet printing
Above, so to speak, three-dimensional laser printing systems have been described. However, inkjet printers are not far behind laser printers in this area. The simplest of the "inkjet" 3D printing processes is the so-called Fused Deposition Modeling (FDM). The idea of FDM is very simple - the dispensing head squeezes drops of heated thermoplastic onto the cooled base platform (almost any industrial thermoplastic can be used as a material). Drops quickly harden and stick together, forming layers of the future object (printing here is also carried out in layers). The FDM process makes it possible to produce quite large ready-to-use parts (up to 600 x 600 x 500 mm) with sufficiently high accuracy (minimum layer thickness 0.12 mm). The fundamentals of this technology were developed 19 more88 Scott Crump. The main manufacturer of FDM equipment is Stratasys.
How the FDM machine works
By the way, NASA is considering FDM technology as a "space factory" candidate. After all, you cannot take an unlimited number of spare parts for all equipment on a space expedition. And it is unlikely that it will be possible to place a full-fledged mechanical workshop on a spaceship. But loading a couple of hundred kilograms of the original plastic and a compact machine that can make any part out of this plastic is easy.
FDM printer at work
Another technology clearly derived from inkjet printing is Objet Geometries' Polyjet. Here the inkjet head is used to print photopolymer plastic. The model, as usual, is printed layer by layer, and the resolution in the layer is 600 x 300 dpi, and the layer thickness can be reduced to as little as 16 microns. Each printed layer is polymerized into a hard plastic under the action of an ultraviolet lamp. In principle, all this is quite similar to SLA, but much faster, more accurate, simpler and more compact. At the same time, the price for Objet printers is at the level of $60K - several times less than for SLA installations. A similar system called InVison is also produced by 3D Systems, so the founding father of stereolithography also does not stand still. The price tag for this machine is about $40K - rapid prototyping systems have clearly become cheaper in recent years.
Objet Eden Rapid Prototyping System 260
And a skull model printed on it
And another "inkjet printing" technology, but using powder materials. It was developed at the famous Massachusetts Institute of Technology, and the Z Corporation became the first and main manufacturer of equipment. Its 3D printers are relatively inexpensive (from $10K to $30K) and are significantly faster than the devices described above. The essence of the technology is as follows - a special inkjet head (by the way, adapted from Hewlett-Packard inkjet printers) sprays an adhesive onto the powder material. Ordinary gypsum or starch is used as a powder. In "splashed" places, the powder sticks together and forms a model. Printing, as in previous cases, goes in layers, and the excess powder is shaken off at the end. However, there is a significant difference - this printer can use an adhesive liquid with the addition of pigment dyes - which means it can print color models. The color printer from Z Corporation has 4 inkjet heads with ink-glue of primary colors, so that the resulting model can reproduce not only the shape, but also the color (that is, the texture) of its virtual prototype. True, plaster models are not very strong, but they can immediately be used as molds for casting. As for the detailing of the "imprint", it is enough to look at the given photographs to appreciate it.
It remains only to shake off the excess powder from the finished print of the model.
Head and parts for it, color 3D printing
Z Corporation serial 3D printer
By the way, ProMetal is developing an interesting variant of the above powder inkjet printing. Its proprietary manufacturing process called the Direct Metal Process works exactly the same way. Only instead of gypsum powder, metal powder is used. Next, the molded product is fired in a furnace, so that the powder either melts itself or binds with a more fusible metal (as in laser sintering of metal powders). Here is another method of direct production using 3D printing.
A part made of metal using ProMetal technology
In general, the prospects for 3D printing are very bright - this technology already saves a lot of time and effort for designers and engineers. And what will happen when it becomes available at the household level. Or, at least, in the form of an inexpensive service. Imagine that you can make any object that you can think of and draw on a computer ... All you have to do is draw a model, determine the material and send an order over the Internet. This is called Distance Manufacturing on Demand. In general, such a technology is simply bound to become mass-produced sooner or later - and then everyone will have their own personal mechanical factory on the table, replacing ordinary production in small things. In the same way that printers have replaced printing houses and typewriting bureaus.
Meanwhile, further developments in this area are in full swing, so you can always expect something new and unexpected. For example, a group of scientists from the University of California at Berkeley is developing a 3D printing technology that would allow both form and content to be created simultaneously. The content here means neither more nor less - electronic stuffing. Let's say the printer prints the plastic case of a mobile phone and prints all the electronics inside at the same time. In principle, there are already ways to print plastic semiconductor devices and the wires connecting them. It remains only to combine them with existing 3D printer technologies and a revolutionary breakthrough in modern production is ready. No, of course, this is not an easy task, but it is quite possible to solve it.
Or, for example, the developments of the University of Missouri, which allow using an inkjet printer to print original blanks of biological organs. In this case, clumps of cells of a given type are used as ink. Instead of "paper" there is a special bio-gel that fixes the position of cell clumps in space. The printing is done in several layers, so that the result is a three-dimensional construction of cells, which, in principle, can imitate any organ (after the cells grow, the gel dissolves, so that hollow structures can be obtained). Of course, printing a full-fledged organ for transplantation seems too difficult for now, but work is underway.
Cellular ink printing system
For those who are interested in this topic, I can give some useful links. First, at this address is a collection of links to equipment manufacturers, technology developers and researchers. Moreover, the links are broken down by materials and production methods, so that a fairly clear picture of the state of affairs in this area immediately emerges. Secondly, at www.rpm-novation.com there is quite a good site dedicated to rapid prototyping technologies in Russian. And here you can find a good table with the characteristics of existing equipment.
And finally, a bit of high art combined with exact science. Look at the photo - in front of you is a model (or, rather, a map) of our metagalaxy. This glass rectangle 7x7x10 centimeters in size depicts a piece of space 100x100x100 megaparsec. Everything is done in full accordance with the exact astronomical data. And the picture itself is burned into the glass with a laser. Also, in general, a kind of 3D printer. Made this wonderful thing by the artist Bathsheba Grossman. See more of her work at www.bathsheba.com.
Space in the thickness of the crystal, laser printing… on glass
3D printers in construction: prospects for application
At first glance, 3D printing structures seem to be some kind of half-finished building shell. But upon closer examination, you will not find even a brick. Layers of material seem to build up one on top of the other - this is how a complex structure is created. It's a futuristic 3D printing world where robotic arms automatically layer and compress layers of concrete or plastic or any other material into a foundation and build the structure.
This method of construction is quite niche today - only a few prototypes of 3D houses and offices have been printed in the world. However, this technology represents an exciting and potentially powerful solution to building change.
What is 3D printing in construction, what is the potential, and will we be working on 3D printed projects in the near future?
- What is 3d printing in construction?
- 3D printers in construction: how is it done?
- 5 examples of innovation
- How can 3d printed projects help construction companies?
- 3D printing distribution
- 3D printing in civil engineering
- Wiki House technology - an open source project for 3D printing: what is behind the concept
- Reverse side of the coin
- How can 3D printing be integrated into construction
- About PlanRadar
3D printing in construction - what kind of technology?
3D printing for construction uses both a 3D printer, which has a robotic "crane-arm" that builds structures right on the construction site, and the creation of certain elements by printers at the factory, which are already assembled into a structure on site.
The concept of 3D printing is not new: it first appeared in the 80s. But it's only in the last decade that this technology has been improved enough (and the cost significantly reduced) to become a real mainstream.
3D printers are not much different from conventional inkjet office printers. The software tells the printer about the dimensions of the final product. And then the printer starts to output the material to the platform according to the plan. 3D printers often use liquid metals, plastics, cement, and variations of various materials that, when cooled and dried, form a structure.
In a 3D construction printer, the CAD or BIM programs tell the device what to print, and the machine starts layering the material according to the design plan.
3D printers in construction: how do they work?
3D printing concept - The printer extrudes a defined liquid mixture in layers, layer by layer, creating a design based on a 3D model. The prepared mix of concrete, filler, plasticizer and other components is loaded into the hopper of the device and fed to the print head. The mixture is applied to the surface of the site or to the previous printed layers. This is how most 3D printers work. Among them, there are three types of devices for 3D printing:
Robotic printer
Read also: New technologies in construction 2021
5 innovative examples of 3D printing
To date, only a few 3D printing projects have been implemented in the construction industry. Here are five of the most impressive and promising projects:
Dubai City Hall Office Building, UAE
1. Dubai City Hall Office Building, UAE
3D printed building. The office block built in the UAE is 9,5 meter high building with an area of 640 m2.
An Apis Cor 3D printer moved around an open-air construction site with a crane and erected various parts of the structure.
2. Office of the Future, UAE
Office of the Future, UAE
Another impressive 3D printed building in the UAE, the Office of the Future is a unique, fairly large structure that currently houses a temporary headquarters organization Dubai Future Foundation.
For this building, the elements were not created on site and were printed in 17 days, while the building itself was assembled in 48 hours.
3. WinSun 3D Printer Homes, China
WinSun 3D Printer Homes, China
WinSun 3D Printing Company in China has also used factory-built 3D printers to build residential buildings. The company has created several house projects, including a small multi-storey building. All construction details can be printed quickly and cheaply and then quickly assembled on the construction site.
The company calculated that it could cost as little as $161,000 to build and print their five-story building.
4. 3D printed number plate in Lewis Grand Hotel, Philippines
3D printed number plate in Lewis Grand Hotel, Philippines
When planning a trip to the Philippines, consider staying at the Lewis Grand Hotel in Angeles City , Pampanga, where visitors will be greeted with the world's first 3D printed hotel suite. The hotel room was designed by Lewis Jakich, hotel owner and materials engineer, in collaboration with 3D printing specialist Anthony Rudenko. They created a massive 3D printer that prints sand and concrete based on volcanic ash. The room was printed in 100 hours.
5. Two-story mansion in Beckum, Germany
Two-story mansion in Beckum, Germany
The first 3D-printed residential building with an area of about 80 square meters - the brainchild of the German construction company PERI GmbH and the architectural design bureau MENSE-KORTE ingenieure + architecture. A BOD2 3D printer was used to print one square meter of double wall cladding in 5 minutes. The building is a structure with three-layer hollow walls filled with insulating mass. Installation of hollow pipes and connections during printing was carried out manually.
3D printing in construction seems really impressive, but what are the real benefits of such technology?
How can 3D printed designs be useful for construction companies?
Proponents of 3D printing houses and commercial offices point to several advantages of this construction method:
- Waste-free construction
In the UK, almost a third of the waste comes from the construction industry. According to the Transparency Market Research Group, the construction industry worldwide will produce 2.2 billion tons of construction waste by 2025. And although most of the waste is related to the demolition of buildings, the construction sites themselves produce a lot of waste.
Conversely, 3D printing can reduce waste to almost zero. A 3D printer uses a well-defined amount of material that is required to print a design - no more, no less. This can be a big savings.
- Reduced energy consumption
3D printing in construction encourages the use of locally available materials and natural ingredients. This practice can reduce energy costs in transportation, construction and manufacturing, as most local materials require less energy to process or install. If traditional materials with toxic chemical impurities are replaced with natural ones, then the toxicity of the entire construction can be reduced. In addition, local materials are often better suited to local climates and can reduce a building's heating or cooling load, which also reduces construction costs.
- Save time and money
As with AI in construction, a 3D printer can run 24 hours a day, 7 days a week. This means construction projects have the potential to be completed much faster and a number of low-skilled labor costs can be avoided. What's more, 3D printing eliminates the need for temporary structures, such as formwork and scaffolding, that are commonly used in traditional construction. Studies of 3D printed concrete structures have shown a significant reduction in formwork requirements, reducing costs by 35-60%.
- Can realize unusual design shapes
One of the most attractive characteristics of 3D printers is their ability to create complex and unusual design designs, including a single, unique one. Since the job of a 3D printer is to layer the material, they can be programmed into absolutely any unusual shape that would be much more difficult to create with traditional techniques.
- Minimize human error and improve safety
The published injury statistics at the workplace by the American agency BLS in 2020 indicates that construction is one of the most traumatic areas and a high incidence of diseases. Every day, about 5333 workers die on the construction site. And with the advent of 3D printing, the number of work injuries and fatalities will obviously decrease, as it makes construction more programmable and automated. Robotic construction requires standardized, accurate and complete digital building information, making this technology more accurate and efficient, with minimal rework due to human error or any information inconsistencies. The usual problems with materials and components that need to be stored somewhere, protected from damage - are leveled out, as well as problems with installation and work in progress due to damage - 3D elements are created as you build, they do not need to be moved and stored.
- Exploring new markets
The use of a 3D printer also allows construction companies to enter new market sectors that were previously inaccessible to them. And for start-up companies, having a 3D printer will be a competitive advantage. What's more, 3D printing is a brilliant way to elevate or improve the reputation of a construction company's brand among those who believe that concrete production has an impact on the planet's environment.
Distribution of structural 3D printing
3D printing for structural reinforcement, small scale components and structural steel could revolutionize design, construction and space exploration. In addition, the European Space Agency (ESA) believes that using 3D printed metals to create high-quality complex shapes can significantly reduce their cost, and they will become very common.
ESA has developed a project with the European Commission to improve the printing of metal components that can be used in space. In total, 28 European partners have united for the joint project AMAZE (Additive Manufacturing Aiming Towards Zero - layer-by-layer 3D printing for zero waste from production and efficient production of high-tech metal products).
Almost everything can be designed on a computer, so AMAZE plans to install a 3D printer on board the spacecraft, and as soon as an astronaut needs any part, a tool, he can simply print it.
Structural 3D printing
Civil engineering 3D printing
Civil engineering 3D printing has been gaining popularity over the past decade, as has the aerospace and biomedical industries. This revolutionary manufacturing technique is based on its unique ability to create any geometric shape without any formal restrictions, minimizing waste but increasing productivity and results. The construction industry's push towards automation has recently reached important milestones, including the creation of the first structures using robotic "arms" and 3D printing technology.
The use of 3D printing in the creation of structural elements from polymer materials, concrete and metals is becoming more common.
These civil engineering technicians can create freeform and innovative architectural designs using CAD-integrated software.
However, despite considerable research in the aerospace and bioengineering industries to evaluate and analyze this mechanism, there is still a lack of understanding of its use, the impact of 3D printed materials in civil structures, both in terms of material properties and structural response.
Imperial College London
Read also: Best Building Apps in 2021
WIKI HOUSE - 3D printing in construction: what is the concept behind
Wiki House is an innovative project created by a small group of architects in London in 2011 . It offers an open source digital house design system that allows users to create, upload and share designs and print their own houses.
The kit does not require any special knowledge and training and can be created in 1 day. Elements are digitally cut from ordinary sheet material, like plywood, using a CNC machine. And it's much faster, less costly, and doesn't require the involvement of experts, as in conventional traditional construction.
A standard two bedroom house can be built for less than £50,000 and additional components such as cladding, insulation, windows and more can be added to the main frame of the structure. The first house that was built on the basis of the open source Wiki House technology was a two-story building. The 3D printed house was presented at the London Design Festival in 2014.
The Wiki House movement was spearheaded by Alastair Parvin, whose TED presentation "Architecture for People, Built by People" talked about the promise of 3D printing in construction. The creator of this project believes that Wiki House can help solve the housing problem, especially in emergency situations such as earthquakes (there is already evidence that 3D-printed houses can withstand shocks up to magnitude 8).
In the future, this could become a real alternative to low-cost houses, while allowing the customer to control the design of the project.
3D building built using Wiki House
Will 3D printing be the sustainable future of building?
3D printing has the potential to revolutionize the supply chain and structure through a new method of design and manufacturing. According to the study, 3D printing can help the construction industry become more economical, more efficient and greener.
Saxon University of Applied Sciences scientists Ivo Kotman and Neils Faber claim that 3D printing technology will be a "game changer". They explored the possibilities of 3D printing concrete, and their conclusions are:
- 3D printing shortens the supply chain and the overall design process. 3D printing right on the job site eliminates time-consuming steps in the design process. The architects, engineers, contractors, clients, and executives who normally have to be actively involved in a project are no longer needed in 3D printing. Since all tasks can be combined in one figure of the architect, who uses the modeling method and reproduces the exact holistic designs.
- Pipe fitting and electrical wiring become easier and more efficient. Heating systems, insulation, plumbing and electricity all require the laborious on-site installation of conventional construction.
However, in 3D printing, some of these features can be incorporated into the 3D printing process. Cavity wall printing is less resource intensive, improves insulation, and allows the use of 3D-printed hot or cold water channels. Moreover, the need for on-site installation is eliminated, which directly affects the reduction of waste.
- The best logistics. 3D printing eliminates 3 logistics and shipping issues. Firstly, a lot of materials and elements often deteriorate upon delivery, and if everything is printed on site, then damage is minimized
Secondly, in order to withstand transportation, the parts must be with increased technical characteristics, which by default increases the cost of them, and therefore the entire project. 3D printing right on the construction site will help to avoid such additional costs.
- Creation of individual house designs available to the general market.
Usually, building a house with the involvement of an architect is an expensive pleasure for most consumers. But with concrete 3D printing, you don't have to worry about the chosen shape, it won't cost more. In fact, this means that in the future more people will be able to buy houses of their own design according to their individual needs
Reverse side of the coin
While 3D printing is definitely attractive, it's still important to look at it impartially, removing some of the promotional stimulus. Skeptics note several disadvantages of this technology.
- Research and development costs
Most construction companies operate with relatively low profitability. To start using 3D printing everywhere, significant investments will be required.
- Will consumers see this as a marketing ploy?
3D printed houses, offices, shops and other infrastructure are often impressive. But do most people really want to live or work in one? For most people, brick houses are much more familiar and attractive. Other technologies such as prefabricated houses also seemed like an attractive technology of the future for some time, but have not been widely adopted, despite the fact that in many cases they were cheaper than traditional ones.
- Difficulty integrating with other components
3D printers can create unique and interesting designs. However, if you need a building that will use different materials or different elements that will not be suitable for 3D printing, then it will be a challenge to include a 3D printer for the building process.
- Skilled labor shortage
With the current problem of a shortage of skilled labor in the construction sector in general, 3D printing will require an even larger set of specialized knowledge and skills, which will have to be selected from an already small niche of candidates. So finding specialists to work in 3D printing for construction may be another difficult task in the future.
- Construction quality control
Weather conditions can slow down the traditional building process, but things are even worse for 3D printing. The environmental factor for commercial construction may reduce the demand for 3D printing. What's more, quality control can be a much more serious task, requiring constant monitoring of the process by real people at the construction site.
- No standards and regulations
Despite the regular mention of 3D printing in the media, it still has not had a significant impact on the construction sector. There is an obvious liability issue when using these printers, even more so than human liability when doing some construction work. And quite a few other ambiguities regarding this technology. So until norms and standards are established, as well as rules in this area, 3D printing is unlikely to become mainstream in the construction industry.