Why use 3d printing
What are the Advantages and Disadvantages of 3D Printing?
3D printing, also known as additive manufacturing, is becoming popular with manufacturers. The demand is growing due to some of the revolutionary benefits that it can provide. Like almost all technologies it has its own drawbacks that need considering.
This page aims to help with the selection process. We will cover each of the advantages and disadvantages of 3D printing.
This production process offers a range of advantages compared to traditional manufacturing methods. These advantages include those related to design, time and cost, amongst others.
1. Flexible Design
3D printing allows for the design and print of more complex designs than traditional manufacturing processes. More traditional processes have design restrictions which no longer apply with the use of 3D printing.
2. Rapid Prototyping
3D printing can manufacture parts within hours, which speeds up the prototyping process. This allows for each stage to complete faster. When compared to machining prototypes, 3D printing is inexpensive and quicker at creating parts as the part can be finished in hours, allowing for each design modification to be completed at a much more efficient rate.
3. Print on Demand
Print on demand is another advantage as it doesn’t need a lot of space to stock inventory, unlike traditional manufacturing processes. This saves space and costs as there is no need to print in bulk unless required.
The 3D design files are all stored in a virtual library as they are printed using a 3D model as either a CAD or STL file, this means they can be located and printed when needed. Edits to designs can be made at very low costs by editing individual files without wastage of out of date inventory and investing in tools.
4. Strong and Lightweight Parts
The main 3D printing material used is plastic, although some metals can also be used for 3D printing. However, plastics offer advantages as they are lighter than their metal equivalents. This is particularly important in industries such as automotive and aerospace where light-weighting is an issue and can deliver greater fuel efficiency.
Also, parts can be created from tailored materials to provide specific properties such as heat resistance, higher strength or water repellency.
5. Fast Design and Production
Depending on a part’s design and complexity, 3D printing can print objects within hours, which is much faster than moulded or machined parts. It is not only the manufacture of the part that can offer time savings through 3D printing but also the design process can be very quick by creating STL or CAD files ready to be printed.
6. Minimising Waste
The production of parts only requires the materials needed for the part itself, with little or no wastage as compared to alternative methods which are cut from large chunks of non-recyclable materials. Not only does the process save on resources but it also reduces the cost of the materials being used.
7. Cost Effective
As a single step manufacturing process, 3D printing saves time and therefore costs associated with using different machines for manufacture. 3D printers can also be set up and left to get on with the job, meaning that there is no need for operators to be present the entire time. As mentioned above, this manufacturing process can also reduce costs on materials as it only uses the amount of material required for the part itself, with little or no wastage. While 3D printing equipment can be expensive to buy, you can even avoid this cost by outsourcing your project to a 3D printing service company.
8. Ease of Access
3D printers are becoming more and more accessible with more local service providers offering outsourcing services for manufacturing work. This saves time and doesn’t require expensive transport costs compared to more traditional manufacturing processes produced abroad in countries such as China.
9. Environmentally Friendly
As this technology reduces the amount of material wastage used this process is inherently environmentally friendly. However, the environmental benefits are extended when you consider factors such as improved fuel efficiency from using lightweight 3D printed parts.
10. Advanced Healthcare
3D printing is being used in the medical sector to help save lives by printing organs for the human body such as livers, kidneys and hearts. Further advances and uses are being developed in the healthcare sector providing some of the biggest advances from using the technology.
Like with almost any other process there are also drawbacks of 3D printing technology which should be considered before opting to use this process.
1. Limited Materials
While 3D Printing can create items in a selection of plastics and metals the available selection of raw materials is not exhaustive. This is due to the fact that not all metals or plastics can be temperature controlled enough to allow 3D printing. In addition, many of these printable materials cannot be recycled and very few are food safe.
2. Restricted Build Size
3D printers currently have small print chambers which restrict the size of parts that can be printed. Anything bigger will need to be printed in separate parts and joined together after production. This can increase costs and time for larger parts due to the printer needing to print more parts before manual labour is used to join the parts together.
3. Post Processing
Although large parts require post-processing, as mentioned above, most 3D printed parts need some form of cleaning up to remove support material from the build and to smooth the surface to achieve the required finish. Post processing methods used include waterjetting, sanding, a chemical soak and rinse, air or heat drying, assembly and others. The amount of post processing required depends on factors including the size of the part being produced, the intended application and the type of 3D printing technology used for production. So, while 3D printing allows for the fast production of parts, the speed of manufacture can be slowed by post processing.
4. Large Volumes
3D printing is a static cost unlike more conventional techniques like injection moulding, where large volumes may be more cost effective to produce. While the initial investment for 3D printing may be lower than other manufacturing methods, once scaled up to produce large volumes for mass production, the cost per unit does not reduce as it would with injection moulding.
5. Part Structure
With 3D printing (also known as Additive Manufacturing) parts are produced layer-by-layer. Although these layers adhere together it also means that they can delaminate under certain stresses or orientations. This problem is more significant when producing items using fused deposition modelling (FDM), while polyjet and multijet parts also tend to be more brittle. In certain cases it may be better to use injection moulding as it creates homogenous parts that will not separate and break.
6. Reduction in Manufacturing Jobs
Another of the disadvantages of 3D technology is the potential reduction in human labour, since most of the production is automated and done by printers. However, many third world countries rely on low skill jobs to keep their economies running, and this technology could put these manufacturing jobs at risk by cutting out the need for production abroad.
7. Design Inaccuracies
Another potential problem with 3D printing is directly related to the type of machine or process used, with some printers having lower tolerances, meaning that final parts may differ from the original design. This can be fixed in post processing, but it must be considered that this will further increase the time and cost of production.
8. Copyright Issues
As 3D printing is becoming more popular and accessible there is a greater possibility for people to create fake and counterfeit products and it will almost be impossible to tell the difference. This has evident issues around copyright as well as for quality control.
Get Further Advice On 3D Printing
Need help with determining whether 3D printing is the right process for you?
Contact our team of world-leading experts with over 20 years of experience in the additive manufacturing field.
Our technology experts help to ensure our customers apply the correct technology process depending on each individual or company requirements:
Related Frequently Asked Questions (FAQs)
10 Advantages of 3D Printing
Are you aware of the many advantages of 3D printing technology? Follow along as we break down our top ten here.
There are 3 main methods used for product development, that is, taking a design from idea to a physical, 3-dimensional prototype of the product.
Subtractive manufacturing is a product development process that continuously cuts away material from a solid block, such as metal. This can be done manually or using CNC (Computer Numeric Controlled) machinery.
Injection molding is a manufacturing process used for producing products in large volumes. As the name suggests, parts are produced by injecting heated material into a mold.
So, what is 3D printing? Additive manufacturing, aka 3D printing, is the process of producing 3-dimensional objects from a computer file, where the part is built by adding material layer-by-layer.
Today, more companies in a variety of industries are embracing the 3D printing process as it presents many significant advantages over the more traditional manufacturing methods of subtractive manufacturing and injection molding.
1. SpeedOne of the biggest advantages of 3D printing technology is Rapid Prototyping. Rapid prototyping is the ability to design, manufacture, and test a customized part in as little time as possible. Also, if needed, the design can be modified without adversely affecting the speed of the manufacturing process.
Before 3D printing industry came to flourish, a prototype would take weeks to manufacture. Every time a change was made, another few weeks of time were added to the process. With shipping times figured in, fully developing a product from start to finish could easily take a year.
With 3D printing techniques, a business can design a part, manufacture it in-house on a professional 3D printer, and test it, all within a few days (and sometimes even less).
For small businesses or even individuals, this difference is significant. The freedom and creativity enabled by 3D printing means that almost anything can be created without the need for warehouses full of expensive machinery. There are no long lead times typically associated with having to outsource complex manufacturing projects. It means freedom from the constraints of minimum orders, that parts and products can be created and customized with ease.
For small production runs and prototyping, 3D printing is the best option as far as speed is concerned.
2. CostFor small production runs and applications, 3D printing is the most cost-effective manufacturing process. Traditional prototyping methods like CNC machining and injection molding require a large number of expensive machines plus they have much higher labor costs as they require experienced machine operators and technicians to run them.
This contrasts with 3D printing process, where only 1 or 2 machines and fewer operators are needed (depending on the system) to manufacture a part. There is far less waste material because the part is built from the ground up, not carved out of a solid block as it is in subtractive manufacturing and usually does not require additional tooling.
Another big advantage of 3D printing is that any given printer can create almost anything that fits within its build volume.
With traditional manufacturing processes, each new part or change in part design, requires a new tool, mold, die, or jig to be manufactured to create the new part.
In 3D printing, the design is fed into slicer software, needed supports added, and then printed with little or no change at all in the physical machinery or equipment.
3D printing allows the creation and manufacture of geometries impossible for traditional methods to produce, either as a single part, or at all. Such geometries include hollow cavities within solid parts and parts within parts.
3D printing, in contrast to traditional methods, allows the inclusion of multiple materials into a single object, enabling an array of colors, textures, and mechanical properties to be mixed and matched.
3D printing allows any user, even those with limited CAD experience, to edit designs however they like, creating unique, customized new parts. This also means any given design can be manufactured in a wide range of different materials.
4. Competitive AdvantageBecause of the speed and lower costs of 3D printing, product life cycles are reduced. Businesses can improve and enhance a product allowing them to deliver better products in a shorter amount of time.
3D printing allows the physical demonstration of a new product to customers and investors instead of leaving it to their imaginations, therefore reducing the risk of information being misunderstood or lost during communication.
It also allows for cost-effective market testing, obtaining feedback from potential customers and investors on a tangible product, without the risk of large upfront expenditures for prototyping.
5. Tangible Design and Product TestingAs previously described in competitive advantages, seeing a product on a screen cannot compare with actually touching and feeling a prototype. A physical prototype can be tested and if flaws are found, the CAD file can be modified and a new version printed out by the next day.
What is a 3D printer and why is it needed? / Amperka
Additive technologies have been going to the masses for a long time: institutes and research centers have been closely involved in them since the 80s, and now the moment has come when you can touch high-tech and master 3D printing right at home. You don’t even have to break the bank to do this: the prices of 3D printers have caught up with average smartphones. We understand how it works and what opportunities open up for makers and DIY enthusiasts!
Everything for 3D printing ❯
Why you need a 3D printer
The printer is very useful for do-it-yourself engineers. You no longer have to look for a universal case for the project, and then drill additional holes in it. 30 minutes of design, a few hours of printing - and you already have a case that is perfect for your device. Assembly of 5 shields does not fit anywhere? Forget about such problems.
The printer is sure to help you repair gizmos around the house. Everyone has had a situation in life when a thing had to be thrown away, although only one plastic part was broken in it. With the help of 3D printing, you can easily replace rare plastic parts in appliances that are difficult to find separately.
Until you learn how to model plastic parts yourself, you can simply download them on the Internet. There are many sites with millions of ready-made free models that are freely exchanged by users. We devoted a separate article to the search for models.
Types of 3D printers
There are several main types of 3D printers that differ fundamentally in terms of how they work.
FDM (Fused Deposition Modeling)
FDM printers are the most common type. They work due to a movable print head with a heating element. Plastic is fed into it in the form of a rod, which melts and is squeezed out in liquid form onto the printing table. At the same time, the plastic is blown by a fan and instantly freezes, and the head begins to squeeze out a new layer over the frozen one.
SLA technology (Stereolithography Apparatus)
SLA printers work on the basis of stereolithography: instead of plastic, a special photopolymer resin is used, which cures under the influence of ultraviolet rays. For printing, the resin is filled into a tray, below which there is a display with ultraviolet pixels. A drawing of the lower layer of the model is displayed on it for several seconds. In this case, the resin above the display solidifies in the form of a displayed pattern and then sticks to a special movable table from above. After that, the table with the first layer rises, and the next layer polymerizes in the resin.
SLS (Selective Laser Sintering) Technology
SLS printers use selective laser sintering technology, which uses a special plastic powder. During the printing process, a thin layer of powder is poured, and the printer processes it with a laser so that the layer hardens according to the model. Then the next layer of powder is poured and fused with the previous one - and so on in a circle. At the end, it remains only to clean the finished part from the remnants of the powder, which can then be reused.
Technology comparison
Each type of 3D printer has its advantages and disadvantages.
- SLS printers are large and require expensive raw materials. They are often used in high-tech industries for piece parts.
- SLA printers are much more widespread. The UV display improves accuracy, but working with toxic photopolymer resin at home is difficult.
- FDM printers are the most popular among hobbyists. A plastic rod is much cheaper than a special powder or photopolymer resin. However, to print complex geometry on such a printer, you will have to take care of auxiliary support. And the print speed is on average lower than on other technologies. But FDM printers are the easiest and safest to maintain.
How to prepare a print
The process from the conception of an idea to the production of a finished plastic part is simple - a schoolboy can handle it. We've broken it down in a 3D printing guide using the Flying Bear Ghost 5 printer as an example, but here we'll show you the general principle.
Initial model
First you need to create or download a 3D model of the future part. As a rule, sources are stored in the STL format, which describes the polygonal structure of the model as a set of triangles. But it will not be possible to immediately send such a file to the printer: for successful printing, you first need to break a detailed 3D model into layers that the printer can handle.
Slicing
The program for cutting models (slicer) will require you to enter the model of your printer and set the print settings: layer thickness, percentage of internal filling of the part, auxiliary supports and the like. Based on this data, the slicer will automatically prepare a special code for the printer - G-Code, which describes how to move the print head, to what temperature it should be heated, and at what speed to extrude plastic in order to get the desired model layer by layer. Then it remains to load this code into a 3D printer and be patient until the end of printing.
The whole process of model preparation is clearly illustrated by the program and provided with intuitive tips for novice users. In general, slicing is not as scary as it is painted!
Finishing
After the model is ready, it can be further processed with sandpaper or a chemical solution. This will smooth out the unevenness between the layers, and the part will look just like the factory. There are a lot of life hacks on the Internet that will help minimize the flaws of the model and give it an improved look.
Printing consumables
The properties of the printed item largely depend on the raw material. As we said before, FDM 3D printers use plastic filament as a consumable, and you have a lot of room to experiment with different types of plastic.
- PLA is highly extrudable and allows complex shapes to be printed at relatively low head operating temperatures of 190°C.
The biodegradability of PLA plays into the hands of the environment, but at the same time, things from it are not very durable.
- PETG plastic is stronger than PLA, but also well suited for printers with temperatures around 200 °C. Varieties of PET plastic are well known to you from bags and plastic soda bottles.
- ABS plastic is more durable than other types. However, your printer will need an elevated extrusion temperature of around 250°C and a heated bed up to 120°C to print quality ABS plastic, so not every model aims to support it.
- HIPS plastic is close in temperature properties to ABS, but has low caking with it and is easily removed with an organic solvent. Because of this, HIPS plastic is often used for printing composite models and supports for ABS models.
- Wood plastic is produced with the addition of wood dust. Finished models from it imitate wood not only in their appearance, but also in smell.
Plastic spools are everywhere - you can easily choose the right consumables and combine different properties and colors of parts when printing.
In conclusion
Home 3D printing is easier than you think. With a 3D printer at hand, you can create any plastic parts you can think of: cases, mock-ups, figurines, and more. Do not forget that you have at your disposal a huge library of models that are shared on the Internet. Broken vacuum cleaner nozzle or window opening limiter? No problem! Having your own 3D printer, you just need to take the finished model from the Internet, run it through the slicer program in a couple of clicks and send it to print.
Useful Links
- Where to Download Free 3D Models of
- Flying Bear Ghost 5 3D Printing Manual
- Creality Ender-3 V2 3D Printing Manual
10 Benefits of a 3D Printer: Save Time and Money
Until recently, 3D printing was viewed as something completely new. The technology was underdeveloped, the hardware was too expensive for widespread use. But only a few years have passed, and the situation has changed radically. Not only did more and more 3D printers begin to appear in stores, but also some enthusiasts began to assemble this equipment themselves.
1. Cost-Effective
While large-scale projects with thousands of 3D printed parts are not cheap, they are still much more cost effective than other technologies. Many manufacturers use 3D printing for small runs or for prototyping. Plastic can also be used for injection molding, but casting small batches can require expensive equipment. But even in this case, manufacturers can produce cast 3D parts several times cheaper than using aluminum.
Prototype parts printed on Prusa i3 Bizon 3D printer, layer height 0.1mm, PLA material
Compared to traditional production methods, the entire process can take weeks or days, and most products are printed in hours. Some manufacturers have even begun to make parts to order, which has also allowed them to optimize their warehouse capacity and resource management scheme, making them more flexible.
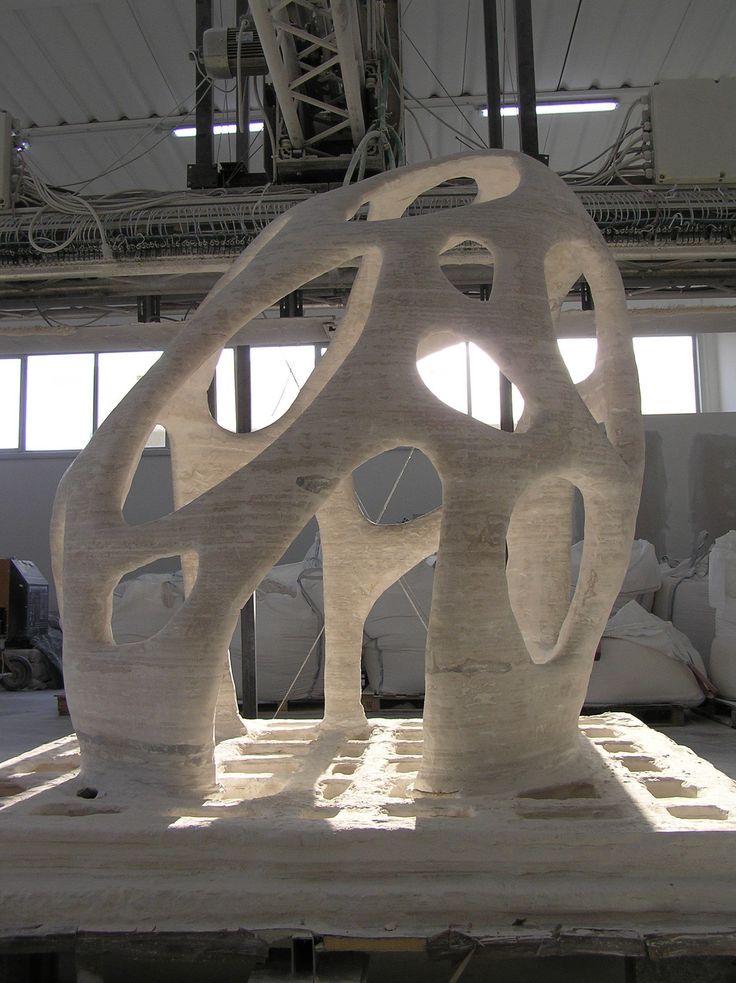
Miniature parts printed by Wanhao Duplicator 7 photopolymer 3D printer, layer height 0.5mm, photopolymer resin material
It not only affects the reputation of the company in its industry, insufficient technical control can lead to injury to employees and customers. Since 3D printing uses a completely different production method than most machine tool operations, the process has significantly fewer weaknesses and flaws overall.
Model printed on Picaso Designer X PRO 3D printer, 0.2 mm layer, ABS materials, HIPS
4. Less waste
The press is gaining more and more support in the form of supporters of the "green" movement. Because 3D printing produces significantly less waste than traditional processing, the technology is more environmentally friendly while reducing costs. 3D printing has even made its way into the textile industry, allowing clothing and prototypes to be printed.
Hercules Strong 3D Printed Yacht Steering Parts. Details printed in 15 hours with a 0.5 mm nozzle and a layer height of 0.3 mm at a speed of 60 mm/s.
5. Greater customization
3D printed products are also highly customizable. Parts can be printed not only with light plastic, some next-generation models may also have a metal coating. As a result, objects are not only aesthetic, but also functional. In addition, they can acquire thermal and chemical resistance. The existing metallization method can also be used for plastic.
Functional parts printed on Hercules. Material ABS, nozzle diameter 0.5 mm, layer height 150 µm, filling 100%. The model consists of 3 parts: the body and 2 halves of the latch, after printing and processing, the parts were glued together with acetone.
6. Customer Availability
If some craftsmen set up small machine shops, for example, in garages, then most of us cannot afford such a luxury. 3D printing allows you to bring a significant part of the manufacturing process directly into the home, made possible by the availability of user-grade 3D technology. While it turns out to be quite expensive for one-off projects, the price of 3D printers and consumables is dropping rapidly.
Technical wing caps in REC RUBBER or REC FLEX. The models are printed on a Prusa i3 Steel 3D printer.
7. High complexity
In most cases, when it comes to complex parts and elements, the manufacturing process imposes certain limitations. Techniques used in casting and finishing objects may not be subtle enough for sophisticated design details. 3D manufacturing processes make it possible to realize almost any design solution, regardless of its complexity, and in a reasonable time. This not only eliminates the extra assembly steps required by traditional methods, but also provides more freedom to create future-proof designs.
Zenit 3D printer print large parts from engine mockup
8. Fewer risks
While there are inherent risks associated with these new technologies, in terms of day-to-day business, 3D printing risks are significantly lower than with traditional manufacturing methods. Not only is 3D printing much cheaper when it comes to testing a new design or product, the printed prototypes themselves can stir up investor and customer interest and get them to decide whether to proceed with mass production of a product, whether it is worth the time and effort required.
Wanhao Duplicator i3 3D Printer Miniature Printing
9. Variety of materials
The materials used in today's 3D printers are much more diverse than most raw materials in traditional production methods.