3D printing technology stocks
Top 3D Printing Stocks for Q4 2022
Table of Contents
Table of Contents
-
Best Value 3D Printing Stocks
-
Fastest Growing 3D Printing Stocks
-
3D Printing Stocks With the Best Performance
SSYS is top for value and performance and NNDM is top for growth
By
Noah Bolton
Full Bio
Noah has about a year of freelance writing experience. He's worked on his investing website dealing with topics such as the stock market and financial advice for beginners.
Learn about our editorial policies
Updated October 06, 2022
The 3D printing industry is made up of companies that provide products and services capable of manufacturing a range of products. 3D printing, also known as additive manufacturing, creates physical objects from digital designs. The printing process works by laying down thin layers of material in the form of liquid or powdered plastic, metal, or cement, and then fusing the layers together. Though still too slow for mass production, it is a revolutionary technology that has the potential to disrupt the manufacturing logistics and inventory management industries. The 3D printing industry is comprised of only a handful of companies, including players such as Proto Labs Inc., Faro Technologies Inc., and Desktop Metal Inc.
The industry is so young that it has no meaningful benchmark index. But the performance of these stocks can be compared to the broader market as represented by the Russell 1000 Index. These stocks have not performed well. Stratasys Ltd. (SSYS), the best performing 3D printing stock, has dramatically underperformed the Russell 1000, which has provided a total return of -12.5% over the past 12 months. This market performance number and all statistics in the tables below are as of Sept. 20, 2022.
Here are the top three 3D printing stocks with the best value, fastest sales growth, and the best performance.
These are the 3D printing stocks with the lowest 12-month trailing price-to-sales (P/S) ratio. For companies in early stages of development or industries suffering from major shocks, this metric can be substituted as a rough measure of a business's value. A business with higher sales could eventually produce more profit when it achieves (or returns to) profitability. The price-to-sales ratio shows how much you're paying for the stock for each dollar of sales generated.
Best Value 3D Printing Stocks | |||
---|---|---|---|
Price ($) | Market Cap ($B) | 12-Month Trailing P/S Ratio | |
Stratasys Ltd. (SSYS) | 15.49 | 1.0 | 1.6 |
3D Systems Corp. (DDD) | 9.00 | 1.2 | 2.0 |
Proto Labs Inc. (PRLB) | 37.49 | 1.0 | 2.1 |
Source: YCharts
- Stratasys Ltd.: Stratasys offers 3D printing solutions, such as 3D printers, polymer materials, a software ecosystem, and related parts.
It serves a variety of industries, including aerospace, automotive, consumer products, and healthcare. On Sept. 13, Stratasys completed the merger of its MakerBot subsidiary with Ultimaker, which offers platforms used to make 3-D printers. Ultimaker is backed by NPM Capital. The merged company will keep the Ultimaker name and focus on providing solutions, hardware, software and materials to the industry. NPM Capital will have majority ownership of the new company at 53.5%, and Stratasys will own 46.5%.
- 3D Systems Corp.: 3D Systems provides 3D printing solutions. The company offers a range of hardware, software, and materials designed for additive manufacturing. Its products and services are used in a variety of industries and sectors, including aerospace, automotive, semiconductor, healthcare, and more.
- Proto Labs Inc.: Proto Labs is an e-commerce-based company that provides digital manufacturing services. It offers 3D printing, injection molding, CNC machining, and sheet metal fabrication.
On Aug. 5, Proto Labs announced financial results for Q2 2022, the three-month period ending on June 30, 2022. Net income fell more than 80% to $2.6 million from the prior-year quarter while revenue rose 3.1%.
These are the 3D printing stocks with the highest YOY sales growth for the most recent quarter. Rising sales can help investors identify companies that are able to grow revenue organically or through other means and find growing companies that have not yet reached profitability. In addition, accounting factors that may not reflect the overall strength of the business can significantly influence earnings per share. However, sales growth can also be potentially misleading about the strength of a business, because growing sales on money-losing businesses can be harmful if the company has no plan to reach profitability.
Fastest Growing 3D Printing Stocks | |||
---|---|---|---|
Price ($) | Market Cap ($B) | Revenue Growth (%) | |
Nano Dimension Ltd.![]() | 2.45 | 0.6 | 1,270 |
Desktop Metal Inc. (DM) | 3.07 | 1.0 | 203.9 |
Stratasys Ltd. (SSYS) | 15.49 | 1.0 | 13.3 |
Source: YCharts
- Nano Dimension Ltd.: Nano Dimension is an Israel-based 3D printing company focused on developing equipment and software for 3D-printed electronics. It develops printers for multilayer printed circuit boards and nanotechnology-based inks. The company serves a range of industries, including consumer electronics, healthcare, aerospace, and automotive. On Sept. 1, Nano Dimension released Q2 2022 results. The company's net loss widened sharply to $40.0 million from a loss of $13.6 million in the same quarter a year earlier even as revenue soared more than 13-fold. The larger second-quarter loss was fueled partly by $10.9 million in non-cash adjustments for depreciation and amortization expenses, and share-based payments.
- Desktop Metal Inc.: Desktop Metal manufactures 3D printers and related equipment used to build complex parts from metal. It also offers 3D printing software. The company serves a range of industries, including automotive, consumer products, education, and heavy industry. On Aug. 08, the company reported Q2 2022 results. Desktop Metals' net loss increase nearly seven-fold to $297.3 million compared to the same quarter a year earlier even as revenue tripled.
- Stratasys Ltd.: See above for company description.
These are the 3D printing stocks that had the smallest declines in total return over the past 12 months out of the companies we looked at.
3D Printing Stocks With the Best Performance | |||
---|---|---|---|
Price ($) | Market Cap ($B) | 12-Month Trailing Total Return (%) | |
Stratasys Ltd.![]() | 15.49 | 1.0 | -34.5 |
Proto Labs Inc. (PRLB) | 37.49 | 1.0 | -50.6 |
Materialise NV (MTLS) | 10.95 | 0.6 | -53.9 |
Russell 1000 | N/A | N/A | -12.5 |
Source: YCharts
- Stratasys Ltd.: See above for company description.
- Proto Labs Inc.: See above for company description.
- Materialise NV: Materialise is a Belgium-based provider of additive manufacturing software and 3D printing services. It serves a range of industries, including healthcare, aerospace, and automotive. On Sept. 7, Materialise completed its acquisition of Identity3D, which makes products that encrypt, distribute, and track digital parts as they move through supply-chains. The value of the deal was not specified in the announcement.
The comments, opinions, and analyses expressed herein are for informational purposes only and should not be considered individual investment advice or recommendations to invest in any security or to adopt any investment strategy. Though we believe the information provided herein is reliable, we do not warrant its accuracy or completeness. The views and strategies described in our content may not be suitable for all investors. Because market and economic conditions are subject to rapid change, all comments, opinions, and analyses contained within our content are rendered as of the date of the posting and may change without notice. The material is not intended as a complete analysis of every material fact regarding any country, region, market, industry, investment, or strategy.
Article Sources
Investopedia requires writers to use primary sources to support their work. These include white papers, government data, original reporting, and interviews with industry experts. We also reference original research from other reputable publishers where appropriate. You can learn more about the standards we follow in producing accurate, unbiased content in our editorial policy.
YCharts. "Financial Data.
"
Stratasys Ltd. "Stratasys Completes Merger of MakerBot with Ultimaker."
Proto Labs Inc. "Proto Labs Q2 2022 Earnings Release."
Nano Dimension Ltd. "Earnings Press Release for Q2 2022."
Desktop Metals Inc. " Desktop Metals Second Quarter 2022 Earnings."
Materialise NV. "Materialise Acquires Indenity3D."
5 3D Printing Stocks to Consider in 2022
An in-depth look at the leading 3D printing stocks in the U.S stock market this year. Here’s what you need to know.
By Nicholas Rossolillo – Updated Jul 11, 2022 at 2:42PM
Back in the early 2010s, stocks were booming for 3D printing -- also known as additive manufacturing, a computer-controlled process in which three-dimensional objects are made. But the boom was followed by a bust as many pure-play 3D printing companies didn't immediately deliver on lofty expectations.
Rumors of the manufacturing technology's demise are clearly premature. These days, 3D printing is a high-growth niche that is steadily reshaping the manufacturing and industrial sectors. Some estimates point to a doubling in annual revenue from additive manufacturing between 2022 and 2026. Even growth investor Cathie Wood has launched a fund focused on manufacturing tech, The 3D Printing ETF (NYSEMKT:PRNT), via her company ARK Invest.
Here's what you need to know about 3D printing and additive manufacturing stocks for 2022:
Image source: Getty Images.
Investing in 3D printing stocks
The manufacturing of products in all corners of the economy is being revolutionized by 3D printing, from healthcare equipment to metal fabrication to housing construction. It's invading so many sectors that tech giants such as Microsoft (NASDAQ:MSFT), Autodesk (NASDAQ:ADSK), and HP (NYSE:HPQ) have launched products aimed at 3D printing and additive manufacturing. Other engineering and software outfits such as Dassault Systemes (OTC:DASTY), ANSYS (NASDAQ:ANSS), and Trimble (NASDAQ:TRMB) have also gotten involved in 3D printing technology.
Here are five key players to consider for 2022 that are a more focused bet on 3D printing:
Company | Market Cap | Description |
---|---|---|
Desktop Metal (NYSE:DM) | $1.3 billion | Recent IPO that focuses on metal fabrication technology. |
Stratasys (NASDAQ:SSYS) | $1.5 billion | One of the original 3D printing pioneers, with a wide array of printers and supporting design software. |
Xometry (NASDAQ:XMTR) | $1.9 billion | A manufacturing marketplace, including access to on-demand 3D printing services.![]() |
3D Systems (NYSE:DDD) | $1.9 billion | Another original 3D printing pioneer and the largest pure-play stock on 3D printing technology. |
PTC (NASDAQ:PTC) | $11.7 billion | A manufacturing technology provider with a suite of software and related services for industrial businesses. |
1. Desktop Metal
This company is a recent entry into the 3D printing space after going public via a SPAC at the end of 2020. The stock has been a terrible market underperformer since then, losing three-quarters of its value as of spring 2022. However, Desktop Metal could still be a promising investment for the long term.
As its name implies, Desktop Metal develops 3D printing hardware and accompanying design software for metal and carbon fiber parts. The company's smaller systems can handle prototyping and one-off parts, and larger printers are production grade-designed for manufacturing facilities. Desktop Metal serves companies operating in automotive, consumer goods, and heavy industrial equipment businesses.
Despite a tenuous start as a public company, Desktop Metal was actually increasing revenue at a torrid triple-digit pace in 2021. Gross profit margins are thin, and the company generated a steep net loss, but that should improve over time as the business scales its operation. Desktop Metal also has several hundred million dollars in cash and investments to fund its expansion. It used some of these funds to acquire additive manufacturing peer ExOne at the end of 2021.
2. Stratasys
Stratasys was part of the early 2010s 3D printing stock boom and bust, but its business has endured. Sales took a dip early in the COVID-19 pandemic but are rebounding as the Israel-based company picks up new manufacturing contracts.
Stratasys serves a diverse set of customers, including aerospace and automotive parts manufacturers, medical and dental companies, and makers of basic consumer products. In addition to a wide array of 3D printer models, Stratasys develops software to help users accelerate the time between design and final printing.
It isn't the highest-growth name on this list, but Stratasys is profitable (on a free cash flow basis) and has more than $500 million in cash and investments on its balance sheet, as well as no debt. Management thinks its payoff from years of research and development into additive manufacturing will accelerate in 2022.
3. Xometry
This is another newcomer to public markets. Xometry completed its initial public offering (IPO) over the summer of 2021, raising almost $350 million in cash in the process. As is often the case with new IPOs, the stock has underperformed since then. It has lost over half of its value from the time it started trading on public markets, but the business itself is rapidly growing.
Xometry is a marketplace for on-demand manufacturing of prototyping and mass production. It has a network of more than 5,000 suppliers that companies can call on to meet their fabrication needs. Among the suppliers on the Xometry platform are 3D printing companies, injection molding, and automated machining. The company reported having more than 28,000 active buyers utilizing its platform at the end of 2021.
Although it isn't profitable yet, Xometry's unique approach to the 3D printing and additive manufacturing industry is growing fast. Like other names on this list, it has a sizable war chest of cash and short-term investments that it can spend on research and marketing as it tries to attract more suppliers and buyers to its marketplace.
4. 3D Systems
3D Systems was another early player in the 3D printing industry, and while it suffered through the boom-and-bust period of the early 2010s, its business has held steady for much of the past decade. After a brief dip during the early days of the pandemic, 3D Systems is back in growth mode.
The company develops printers and design software for all sorts of materials and industries (medical device makers, dental labs, semiconductor designers, aerospace, and automotive manufacturers). It claims leadership among independent 3D printing companies (as measured by sales). As the 3D printing industry expands in the coming years, 3D Systems thinks it will be able to attract lots of new business with its extensive experience and global reach.
As an established tech outfit in the manufacturing sector, 3D Systems offers investors the prospect of more stable growth, along with profitability. It also has a large net cash position from which it can consolidate its lead in 3D printers and software technology.
5. PTC
By far the largest company on this list, PTC is a longtime technology partner of manufacturing and industrial enterprises. Fast approaching $2 billion in annualized sales and highly profitable, PTC has all the tools needed to digitally transform industrial businesses.
Besides 3D printing computer-aided design software (ANSYS is a peer and software partner that also operates in this space), PTC specializes in augmented reality, industrial IoT (Internet of Things), and product life-cycle management software. Most of its revenue is subscription-based (including its Creo software that enables 3D printing), making for a stable and steadily growing business model that generates ample cash flow. PTC puts spare cash to work developing new products for its partners and makes bolt-on acquisitions of other software companies that enhance its overall portfolio.
As a larger company, PTC won't be the fastest-growing stock in the additive manufacturing and 3D printing space. However, the company has established itself as a leader in industrial technology and should be a primary beneficiary as the production of manufactured goods gets more efficient.
The future of 3D printing
Manufacturing technology is making inroads throughout the global economy by reducing the cost of production and localizing and speeding up the time it takes to deliver customer orders. This is far from mere hype. Nevertheless, as is the case with all technology investments, progress won't go straight up. Expect twists and turns in these stocks as they develop new methods to design and make products.
If you decide to invest, do so in a measured way. Maintain a diversified portfolio, be wary of stocks benefiting from investor over-optimism, and always leave spare cash to invest more when there are inevitable dips. Given enough time -- years and decades -- investing in 3D printing could eventually provide a big payoff.
Related communication stocks topics
Investing in 5G Stocks
As the 5G technology rollout continues, these companies look like winners.
Investing in Top Telecommunications Stocks
Our world is increasingly interconnected, and these companies make it happen.
Investing in Communication Stocks
Communications has a broad definition. These companies are the leaders in the space.
Investing in Top Consumer Discretionary Stocks
When people have a little extra cash, they indulge in offerings from these companies.
Nicholas Rossolillo has positions in Autodesk and PTC. The Motley Fool has positions in and recommends Autodesk, HP, and Microsoft. The Motley Fool recommends 3D Systems, ANSYS, Dassault Systemes, PTC, and Trimble Inc. The Motley Fool has a disclosure policy.
Motley Fool Investing Philosophy
- #1 Buy 25+ Companies
- #2 Hold Stocks for 5+ Years
- #3 Add New Savings Regularly
- #4 Hold Through Market Volatility
- #5 Let Winners Run
- #6 Target Long-Term Returns
Why do we invest this way? Learn More
Related Articles
This Software Stock Crushed the Nasdaq by 31% in 2022: Here's Why It Has Room to Run
Got $2,000? Here Are 3 Smart Stocks to Buy Now
Best ETFs to Buy
Best Bonds to Invest in
Down Over 25% in 2022, This FAANG Stock Is a No-Brainer Investment
1 Green Flag for Microsoft Stock in 2022 and 1 Red Flag
What Is Liquidity?
Premium Investing Services
Invest better with The Motley Fool. Get stock recommendations, portfolio guidance, and more from The Motley Fool's premium services.
View Premium Services
Selective Laser Sintering (SLS) 3D Printing Guide
Selective Laser Sintering (SLS) 3D printing is a technology trusted by engineers and manufacturers across industries to create durable and functional models.
In this detailed guide, we'll explain selective laser sintering technology, the different systems and materials on the market, the workflow and different applications of SLS printers, and when to choose 3D printing with this technology over others. additive and traditional manufacturing methods.
White paper
Looking for a 3D printer to create durable, functional models? Download our white paper to learn how selective laser sintering (SLS) technology works and why it is popular in 3D printing for functional prototypes and end-use products.
Download white paper
Selective laser sintering (SLS) is an additive manufacturing technology that uses a powerful laser to sinter fine polymer powder particles into a solid structure based on a 3D model.
SLS 3D printing has been popular with engineers and manufacturers for decades. With its low model cost, high productivity, and common materials, this technology is well suited for a wide range of applications, from rapid prototyping to low-volume production, limited trial runs, or custom-made products.
Recent advances in technology, materials and software have opened up the possibility of SLS printing to a wider range of companies. Previously, such tools were used only in a few high-tech industries.
Introducing the Fuse 1 high performance SLS 3D printer, finally available.
Webinar
Watch our product demo to learn about Fuse 1 and SLS 3D printing from Formlabs.
Watch webinar
Schematic representation of the selective laser sintering process. The SLS method uses a powerful laser to sinter small particles of polymer powder into a solid structure based on a 3D model.
-
Print: A thin layer of powder is applied to the top of the platform inside the working chamber. The printer preheats the powder to just below the melting point of the feedstock. This allows the laser to more easily raise the temperature of certain areas of the powder bed and monitor the solidification of the model. The laser scans the cross section of the 3D model, heating the powder to the material's melting temperature or just below. Particles are mechanically joined together to form a single solid object. The unsprayed powder supports the model during printing and eliminates the need for special support structures. The platform is then lowered into the working chamber one layer, typically 50-200 µm thick, and the process is repeated for each layer until the models are complete.
-
Cooling down: after printing and before post-processing, the build chamber should cool down a little in the printer body and then outside the body to ensure optimal mechanical properties of the models and avoid their deformation.
-
Postprocessing: finished models must be removed from the working chamber, separated from each other and cleaned of excess powder. The powder can be recycled and printed models can be blasted or tumbled.
To learn more about the workflow, see the SLS 3D Printing Workflow section below.
SLS models have a slightly grainy surface, but the layer lines are almost invisible. To achieve a smooth surface, SLS models are recommended to be blasted or tumbled. This sample was printed on a Fuse 1 industrial 3D printer with SLS technology for workshops from Formlabs.
The green powder supports the model during printing and eliminates the need for special support structures. This makes SLS ideal for complex geometries, including internal features, undercuts, thin walls, and negative draft features.
Models created using SLS 3D printing have excellent mechanical properties: their strength is comparable to that of injection molded models.
Compare Selective Laser Sintering (SLS) 3D printing with other common plastic modeling technologies: Fused Deposition Modeling (FDM) and Stereolithography (SLA).
Selective Laser Sintering (SLS) is one of the first additive manufacturing technologies developed in the mid-1980s by Dr. Carl Deckard and Dr. Joe Beeman at the University of Texas at Austin. Since then, the method has been adapted to work with a variety of materials, including plastics, metals, glass, ceramics, and various powdered composite materials. Today, all of these technologies are classified as wafer synthesis, additive manufacturing processes that selectively sinter regions of a powder layer under the influence of thermal energy.
The two most common substrate synthesis systems currently available are a plastic based method commonly referred to as Selective Laser Sintering (SLS) and a metal based method known as Direct Metal Laser Sintering (DMLS) or Selective Laser Melting (SLM). ). Until recently, both systems were very expensive and complex, which limited their use to the production of small batches of expensive models or custom-made products, such as aerospace components or medical devices.
Innovation in this area will make plastic-based SLS as affordable as other 3D printing technologies such as stereolithography (SLA) and Fused Deposition Modeling (FDM) and become widely available in affordable, compact systems.
All selective laser sintering 3D printers use the process described in the previous section. Basically, such printers differ in the type of laser, the volume of printing and the complexity of the system. Different solutions are used for temperature control, powder dosing and layering in different devices.
Selective laser sintering technology requires high precision and strict control during the printing process. The temperature of the powder and (incomplete) models must be controlled within 2°C during the three stages of production: preheating, sintering and storage before extraction, in order to minimize warping, stress and thermal deformation.
For decades, selective laser sintering has been one of the most popular professional 3D printing technologies, but due to its complexity, strict requirements and high price, only service bureaus and large enterprises could use it.
Conventional industrial SLS 3D printing systems have one or more powerful lasers. An inert atmosphere (nitrogen or other gases) is needed to prevent the powder from oxidizing and breaking down during the printing process, which requires specialized air handling equipment.
These installations also require special heating, ventilation and air conditioning (HVAC) systems and industrial power supplies. In addition, even the smallest industrial installations occupy an area of at least 10 square meters. m.
Due to the high initial cost of approximately $100,000 (and much more for complete solutions), traditional industrial systems with SLS technology were out of reach for many enterprises.
As with other 3D printing technologies such as Fused Deposition Modeling (FDM) and Stereolithography (SLA), more affordable, compact systems with SLS technology have recently begun to appear on the market. However, these solutions had significant drawbacks. These include low quality models and complex manual workflows due to a lack of post-processing solutions. This severely limited their use in industrial production.
The Formlabs Fuse 1 printer is in a new category with these deficiencies fixed . It is the first industrial SLS 3D printer for the workshop, delivering high quality, compact size, streamlined workflow, and cost far less than traditional industrial systems of the same type.
The Fuse 1 printer does not require any special infrastructure and will easily fit into your workplace.
The Fuse 1 uses a single laser and has a smaller working chamber that requires less heat. The powder is exposed to elevated temperatures for a shorter period of time, so there is no need for inert gases and specialized ventilation equipment. Thanks to its lower power consumption, it can run on a standard AC power supply without requiring special infrastructure.
The Fuse 1 features patent pending Surface Armor technology. This creates a semi-baked shell that heats evenly around the models as they are printed. This results in excellent surface quality, stable mechanical properties, high reliability and a high material renewal rate.
In addition to providing a compact, self-sustaining ecosystem and complete powder handling capability, Fuse 1 is complemented by the Fuse Sift Station, a stand-alone stand-alone device for model retrieval, recovery, storage and powder mixing.
Overall, the Fuse 1 industrial 3D printer with SLS for workshops has slightly less print volume than traditional entry-level SLS systems, but is smaller, easier to work with and less expensive.
Fuse 1 Industrial SLS Workshop Printer | Traditional Industrial SLS 3D Printers | 5 Cost | from 18,500 US dollars | 100 000 - 500,000 US dollars and more than | ||||
---|---|---|---|---|---|---|---|---|
Press volume | to 165 x 165 x 300 mm | 9010 x 550 x 750 mm 7509 Benefits | Availability High quality models High performance Simplified workflow Compact dimensions Low maintenance | High print volume High quality models High performance Many material options | ||||
Disadvantages | Less print volume Limited material options | Expensive equipment Big sizes Infrastructure Requirements Large amount of maintenance Special Operator Required |
The most common selective laser sintering (SLS) material is nylon. It is a high performance engineering thermoplastic for both functional prototyping and end-use fabrication. Nylon is ideal for the production of complex knots and strong models with high environmental resistance.
3D printed SLS nylon for strength, rigidity and durability. The final models are impact-resistant and highly wear-resistant. Nylon is resistant to UV, light, heat, moisture, solvents, temperature and water. Nylon models printed on a 3D printer are also biocompatible and do not cause allergic reactions. This means that they can be worn and used safely in many situations.
Nylon is ideal for a range of functional applications, from consumer product design to healthcare applications.
Nylon is a synthetic thermoplastic polymer from the polyamide family. It is available in several versions, each designed to print different products. Nylon 12 Powder has a wide range of applications and is a general purpose, general purpose SLS 3D printing powder. Nylon 12 GF Powder is a composite material with a high fiber content, increased stiffness and heat resistance for difficult industrial conditions. Nylon 11 Powder helps fill a gap in prototyping and end-use applications where increased ductility, impact resistance and the ability to withstand wear without brittle fracture are required.
- Impact proof prototypes, fixtures and fittings
- Thin-walled pipes and bodies
- Rivets, fasteners and latches
- Orthopedic products and prostheses*
- High Performance Prototyping
- Small batch production
- One-piece clamping and holding fixtures and tooling
- Conventional SLS models
- Heavy duty clamping and fastening fixtures and spare parts
- Continuous models
- Thread and sockets
- High temperature models
* Material properties may vary depending on model design and manufacturing method. It is the manufacturer's responsibility to confirm the suitability of printed models for their intended use.
109 40%
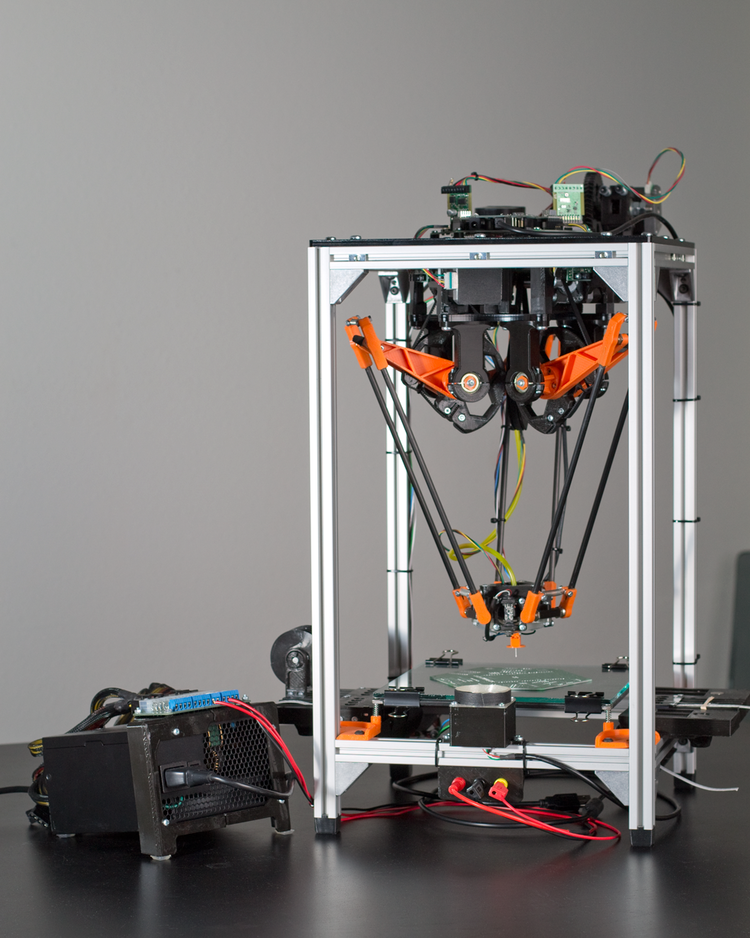
Nylon 12 Powder and Nylon 11 Powder are one-component powders, but some SLS 3D printers can also use two-component powders, such as coated powders or powder blends.
Nylon 12 GF Powder is a composite material with a high fiberglass content, while other nylon composites with aluminide, carbon or glass are designed to increase the strength, stiffness or flexibility of models. In such two-component powders, only the component with the lower glass transition point is sintered, which binds both components.
SLS 3D printing accelerates innovation and helps businesses in a wide range of industries such as engineering, manufacturing and healthcare.
Manage the entire product development process, from iteration of first concept design to production of ready-to-use products:
- Rapid Prototyping
- Product mockups for user feedback
- Functional Prototyping
- Functional testing of products under severe conditions (e.
g. piping, brackets)
Manage your supply chain and respond quickly to changing needs:
- End-Use Manufacturing
- Small batch production
- Mass production of new customized consumer products
- Spare parts manufacturing, supply chain sustainability
- Durable, durable clamping and fastening devices (e.g. clamps and clamps) and accessories
- Custom manufacture of automotive, motorcycle and marine equipment parts, and restock military items on demand
Self-manufacturing of ready-to-use medical devices, taking into account the individual characteristics of patients:
- Medical device prototyping
- Prostheses and orthotics (e.g. prosthetic limbs and orthoses)
- Surgical models and instruments
- End use products (nylon 12 biocompatible and sterilizable*)
* Material properties may vary depending on model design and production method. It is the manufacturer's responsibility to confirm the suitability of printed models for their intended use.
Use any CAD software or 3D scan data to design the model and export it to a 3D printable format (STL or OBJ) file. All printers with SLS technology use software that allows you to adjust settings, position models, estimate print times, and layer your digital model. Once set up, the model preparation software sends commands to the printer via a wireless or cable connection.
The Fuse 1 uses PreForm print preparation software (free to download). It allows you to easily duplicate and place multiple models on a 3D grid to maximize your print volume. PreForm automatically suggests the optimal orientation and position of models with the ability to make manual changes.
The workflow for preparing the printer varies from system to system. Most traditional SLS systems require extensive training, tools, and physical actions to prepare and maintain them.
Fuse 1 redefines the SLS workflow, making it simple and efficient, as well as providing trouble-free printing and complete powder handling thanks to modular components.
The Fuse 1 can be easily loaded with powder using a special cartridge.
The Fuse 1 uses a detachable build chamber so you can start a new print while the previous build chamber is still cooling.
Once all pre-checks have been completed, the machine is ready to print. Depending on the size and complexity of the 3D models, as well as their density, printing using SLS technology can take from several hours to several days.
When printing is complete, the build chamber in the housing should cool down a bit before proceeding with the next step. To start the next print, you can remove the build chamber and insert a new one. Before post-processing, the working chamber must cool down to ensure optimal mechanical properties of the models and avoid their deformation. This can take up to half of the total print time.
Fuse 1 is equipped with a touch screen that allows you to see in real time how each new layer is formed during the printing process. This camera image can also be transferred to a computer using PreForm to monitor the print without leaving the workplace.
Compared to other 3D printing processes, post-processing of SLS-printed models requires a minimum of time and labor. With no supporting structures, it is easy to scale and provides consistent results across batches of models.
After printing is completed, remove the finished models from the build chamber, separate them and clean them of excess powder. As a rule, this is done manually at the cleaning station using compressed air or a jet apparatus.
The excess powder left after the creation of the model is filtered to remove large particles from it. After that, it can be recycled. Under the influence of high temperature, the properties of green powder deteriorate slightly, so for subsequent printing it must be mixed with new material. Due to the possibility of reusing materials, SLS technology produces a minimum amount of waste.
SLS technology typically uses separate devices for powder recovery, storage and mixing. The Fuse 1 workflow uses a single Fuse Sift to retrieve patterns and greens, store, dispense, and mix material streams.
Fuse Sift completes the Fuse 1 SLS print workflow. This system is used for safe and efficient model retrieval and powder recycling.
Fuse Sift automatically doses and mixes used and new powder, reducing waste and controlling powder delivery.
After the powder has been sieved, the 3D models printed using selective laser sintering technology are ready for use. However, there are a few more post-processing steps you can perform on these models.
By default, the surface of 3D models created using SLS technology remains grainy. To achieve a smooth surface, Formlabs recommends blasting or tumbling models made using this method. Models can be spray painted, lacquered, electroplated or otherwise to achieve the desired color, surface quality and properties such as water resistance (special coating) and electrical conductivity (electrolytic coating). Models created with SLS Formlabs are dark in color and therefore not well suited for staining.
Immersion printed SLS model from Partial Hand Solutions.
SLS models can be electroplated for a metal-like surface.
Selective laser sintering is preferred by engineers and manufacturers for its wide design options, high productivity, low model cost and proven end use materials.
Most additive manufacturing processes such as stereolithography (SLA) and Fused Deposition Modeling (FDM) require specialized support structures to fabricate overhang structures.
Selective laser sintering does not require support structures because the unsintered powder surrounds the model during printing. SLS printing makes it easy to create overhangs, intricate geometries, interconnecting parts, internal channels and other intricate details.
Intricately patterned arm splint for weight reduction.
Engineers typically design models in terms of the capabilities of the final manufacturing process, also known as design-for-technology (DFM). When additive manufacturing is only used for prototyping, it comes down to creating models and designs that can be replicated in the manufacturing process using traditional tools.
Selective laser sintering is emerging as a viable rapid production method and its application area continues to expand, so it can open up new possibilities in design and construction. 3D printers with SLS technology can create complex geometries that are impossible or incredibly expensive to manufacture using traditional processes. SLS technology also allows design professionals to combine complex assemblies into a single model that would normally require multiple models to be created. This helps avoid the problem of loose connections and saves assembly time.
Selective laser sintering can unleash the potential of generative design, as it allows the creation of lightweight models that use complex lattice structures that cannot be fabricated by traditional methods.
Selective laser sintering is the fastest additive manufacturing technology for making functional, durable prototypes and end-use products. Lasers used for powder sintering have much faster scanning speeds and are more accurate than the layering methods used in other processes such as Industrial Fused Deposition Modeling (FDM).
To maximize the available print volume in each printer, multiple models can be placed side by side. Operators can use the software to optimize print volume and maximize productivity by leaving only minimal clearance between models.
SLS technology allows operators to fill the build chamber with as many models as possible, as it allows them to be printed without supporting structures, saving time in post-processing.
SLS 3D printing requires the right materials for functionality and versatility. Nylon and its composites are proven, high quality thermoplastic materials. Laser-sintered nylon models have close to 100% density and mechanical properties that are comparable to products made using traditional manufacturing methods such as injection molding.
Screwdriver printed in Nylon 12 Powder. After a simple post-processing, nylon models have a smooth, professional quality surface.
SLS Printable Nylon is an excellent replacement for conventional injection molded plastics. The latches and other mechanical connections produced from it are superior to products created using any other additive manufacturing technology. It is ideal for making functional plastic parts that will work and not break down over time like products created through other additive manufacturing methods.
When calculating the cost of one model, it is usually necessary to take into account the cost of ownership of equipment, material costs and labor costs:
-
Equipment cost of ownership: The more models a printer can produce over its lifetime, the lower the cost per model. Therefore, higher performance results in a lower cost of ownership per model. With high laser scanning speeds, the ability to produce multiple models at once to maximize the working volume, and a simple post-processing process, SLS 3D printing guarantees the highest productivity of any additive manufacturing method.
-
Material: Most 3D printing technologies use proprietary materials, while nylon is a common thermoplastic that is produced in large quantities for industrial applications.
This makes it one of the most inexpensive raw materials for additive manufacturing. SLS 3D printing requires no support structures and allows you to print with recycled powder with minimal waste.
-
Labor: Labor is a disadvantage of many 3D printing solutions. Work processes in most technologies are quite laborious and difficult to automate, which can significantly affect the cost of one model. Easy post-processing with SLS printing reduces manual labor and allows for easy scalability.
A 3D printer with SLS technology is a significant investment initially, but this investment often pays off even faster than buying smaller devices. SLS for workshop technology significantly reduces initial acquisition costs and also reduces model costs in most applications.
If 3D printing is rarely used in your business, it is recommended to use the services of third-party service bureaus. But in this case, the cash costs will be higher and you will have to wait longer for the order to be completed. One of the main advantages of 3D printing is its speed compared to traditional production methods. But this advantage loses its value when it takes up to several weeks for a third-party company to deliver a model.
REEKON Tools