What materials can you 3d print with
What Materials Can be 3D Printed?
Using the right material for your 3D printed project can make or break a product. This article covers what materials you can 3d print.
Over the years, 3D printing has become increasingly common. This technology (also known as additive manufacturing) is now readily available — many public libraries and schools offer 3D printing services at no charge, and 3D printing materials can be easily found. From the automotive and aerospace industries to medicine and food safety, supporting material is either soluble and insoluble, and 3D printing processes are everywhere. But what materials can be 3D printed? Let’s take a look at the various options available.
Many 3D printers rely on Fused Deposition Modeling (FDM). This helps product prototypes by layering from the bottom up with heat and thermoplastic filaments. These machines use a variety of materials, both expensive and affordable.
Stereolithography (SLA) is another method of 3D printing, which relies on a UV laser that cures layers in a photo-reactive epoxy resin. It’s more accurate than FDM and is an excellent choice for engineers who need small features or other detailed work.
In Selective Laser Sintering (SLS) 3D printing, a high-power laser fuses tiny polymer powder particles. Though we will not be discussing this 3d printing method, it’s important to emphasize that various materials exist for all types of additive manufacturing.
Back to Basics with Thermoplastics
There are many options to choose from when looking to 3D print something using plastic, which is likely the most common material used. Plastic is utilized for its versatility and can be applied to various projects, offering anything from shiny and matte textures to projects with unique colors. The post-processing step for 3D printed plastics may be more robust. Still, the affordability and potential strength often outweigh the minor downfalls. Items 3D printed with plastic are created layer by layer with thermoplastic filaments, which include plastic made from:
- Polylactic Acid, or PLA: Biodegradable PLA, produced from corn starch and sugar cane, is a favored 3D printing material because it’s more sustainable than most other materials.
It also leads to more robust products overall. PLA is the cheapest material for 3D printing and is used both at home and on larger industrial projects.
- Polyamide. Polyamide is a widespread choice for 3D printing, both at home and industrially, because it is so varied. It’s cheap, includes interlinking and interlocking parts, and can be painted and dyed.
- Polyvinyl Alcohol Plastic or PVA: PVA is used with some frequency because it is low-cost and the material of choice for many in-home printers used more for play. Overall, it lacks strength but is a decent choice for items that aren’t frequently used and for those new to 3D printing.
- Acrylonitrile Butadiene Styrene or ABS: Makers lean towards ABS because it offers strength through filaments shaped like pasta. It’s sometimes referred to as Lego plastic, comes in an array of colors, and is ideal for at-home 3D printing.
3D Printing with Metal
Metal is the second most popular 3D printing material. Commonly used in additive manufacturing, metal adds speed to the 3D printing process while maintaining an aesthetic nice enough for high-quality jewelry and has a strong enough foundation for industrial applications. When used as a 3D printed material, metal is in dust form. Many kinds of metal can be utilized in 3D printing (well beyond those listed here), including:
- Gold: Gold, primarily used for jewelry, is an interesting (but expensive) choice for 3D printing.
- Titanium: Titanium is an ideal metal for fixtures that must be strong and reliable while also maintaining extreme heat resistance.
- Stainless Steel: Stainless steel is a more affordable metal option often utilized to 3D print cookware, utensils, and objects meant to be waterproof.
A Wide Assortment of Materials
Many materials are used for additive manufacturing. While some might be more common than others, they are all worth mentioning. The right material can make or break your product. You owe it to yourself to explore many of them. Here are a few you may not be familiar with:
- Graphite or Graphene: Because they are strong and conduct heat well, graphite and graphene are excellent materials for 3D printing, especially for devices that require flexibility, since it is arguably one of the most flexible 3D printer materials. This 3D printer material is also very lightweight.
- Carbon Fiber: Carbon fiber is a composite material, which acts as a topcoat on plastic materials to make them stronger. Putting carbon fiber over plastic creates a faster and cheaper material than metal but just as strong.
- Nitinol: This 3D printed material is commonly found in medical technology because it’s highly elastic. As the name suggests, it is a mix of titanium and nickel and can be folded in half while retaining its shape.
- Paper: Although it isn’t useful in applications that require strength, paper is an ideal material for 3D printing, as it gives more life to high-quality prototypes than flat illustrations do.
Paper can be used for 3D printing in great detail, is cheap, and easily accessible for all kinds of projects.
Polymers for High Heat Applications
For high heat applications, there are a few polymers that can be used. These polymers are durable and easy to 3D print with:
- PEEK, or Polyether ether ketone. Part of the PAEK family, PEEK is used in situations that call for an extremely durable material able to withstand high temperatures.
- PEI, or Polyetherimide. PEI is one of the first high-temperature 3D printer materials. It is a more affordable option and is frequently used for aerospace applications, though it isn’t as strong and has less thermal resistance.
- PPSU/PPSF, or Polyphenylsulfone. This high-temperature, high strength material has no melting point, thanks to an amorphous internal structure. It’s also chemically resistant.
The 3D printing process can vary significantly based on your desired outcomes. That said, there’s support material for any project imaginable. Though all require some degree of post-processing, this can vary by material and may be an essential consideration. While this list addresses many, there are endless possibilities that will make a product soar. We hope this blog post has given you a stronger understanding of what materials can be 3D printed.
With digital 3D modeling and design tools, 3D printing is easier than ever before. Autodesk Fusion 360 provides flexible 3D modeling software that encourages creativity and allows for multiple design iterations.
What Materials Are Used in the 3D Printing Process?
The materials used for 3D printing are as diverse as the products that result from the process. As such, 3D printing is flexible enough to allow manufacturers to determine the shape, texture and strength of a product. Best of all, these qualities can be achieved with far fewer steps than what is typically required in traditional means of production. Moreover, these products can be made with various types of 3D printing materials.
In order for a 3D print to be realized in the form of a finished product, a detailed image of the design in question must first be submitted to the printer. The details are rendered in standard triangle language (STL), which conveys the intricacies and dimensions of a given design and allows a computerized 3D printer to see a design from all sides and angles.
Basically, an STL design is the equivalent of multiple flat designs in one computerized file.
The industry for 3D printing is expected to surpass the 10-figure mark in the near future and plastic is set to be the main material to drive this market. As concluded recently in a SmarTech Markets Publishing study, the market for 3D printing is likely to exceed $1.4 billion before 2020. With an ongoing market expansion, the industry has sought new ways to yield plastics, including the use of organic ingredients like soybean oil and corn. Consequently, plastics are set to become the most environmentally friendly option in 3D printing.
Plastic
Out of all the raw materials for 3D printing in use today, plastic is the most common. Plastic is one of the most diverse materials for 3D-printed toys and household fixtures. Products made with this technique include desk utensils, vases and action figures. Available in transparent form as well as bright colors — of which red and lime green are particularly popular — plastic filaments are sold on spools and can have either a matte or shiny texture.
With its firmness, flexibility, smoothness and bright range of color options, the appeal of plastic is easy to understand. As a relatively affordable option, plastic is generally light on the pocketbooks of creators and consumers alike.
Plastic products are generally made with FDM printers, in which thermoplastic filaments are melted and molded into shape, layer by layer. The types of plastic used in this process are usually made from one of the following materials:
- Polyastic acid (PLA): One of the eco-friendliest options for 3D printers, polyastic acid is sourced from natural products like sugar cane and corn starch and is therefore biodegradable.
Available in soft and hard forms, plastics made from polyastic acid are expected to dominate the 3D printing industry in the coming years. Hard PLA is the stronger and therefore more ideal material for a broader range of products.
- Acrylonitrile butadiene styrene (ABS): Valued for its strength and safety, ABS is a popular option for home-based 3D printers. Alternately referred to as “LEGO plastic,” the material consists of pasta-like filaments that give ABS its firmness and flexibility. ABS is available in various colors that make the material suitable for products like stickers and toys. Increasingly popular among craftspeople, ABC is also used to make jewelry and vases.
- Polyvinyl Alcohol Plastic (PVA): Used in low-end home printers, PVA is a suitable plastic for support materials of the dissolvable variety. Though not suitable for products that require high strength, PVA can be a low-cost option for temporary-use items.
- Polycarbonate (PC): Less frequently used than the aforementioned plastic types, polycarbonate only works in 3D printers that feature nozzle designs and that operate at high temperatures.
Among other things, polycarbonate is used to make low-cost plastic fasteners and molding trays.
Plastic items made in 3D printers come in a variety of shapes and consistencies, from flat and round to grooved and meshed. A quick search of Google images will show a novel range of 3D-printed plastic products such as mesh bracelets, cog wheels and Incredible Hulk action figures. For the home craftsperson, polycarbonate spools can now be purchased in bright colors at most supply stores.
Powders
Today’s more state-of-the-art 3D printers use powdered materials to construct products. Inside the printer, the powder is melted and distributed in layers until the desired thickness, texture and patterns are made. The powders can come from various sources and materials, but the most common are:
- Polyamide (Nylon): With its strength and flexibility, polyamide allows for high levels of detail on a 3D-printed product. The material is especially suited for joining pieces and interlocking parts in a 3D-printed model.
Polyamide is used to print everything from fasteners and handles to toy cars and figures.
- Alumide: Comprised of a mix of polyamide and gray aluminum, alumide powder makes for some of the strongest 3D-printed models. Recognized by its grainy and sandy appearance, the powder is reliable for industrial models and prototypes.
In powder form, materials like steel, copper and other types of metal are easier to transport and mold into desired shapes. As with the various types of plastic used in 3D printing, metal powder must be heated to the point where it can be distributed layer-by-layer to form a completed shape.
Resins
One of the more limiting and therefore less-used materials in 3D printing is resin. Compared to other 3D-applicable materials, resin offers limited flexibility and strength. Made of liquid polymer, resin reaches its end state with exposure to UV light. Resin is generally found in black, white and transparent varieties, but certain printed items have also been produced in orange, red, blue and green.
The material comes in the following three categories:
- High-detail resins: Generally used for small models that require intricate detail. For example, four-inch figurines with complex wardrobe and facial details are often printed with this grade of resin.
- Paintable resin: Sometimes used in smooth-surface 3D prints, resins in this class are noted for their aesthetic appeal. Figurines with rendered facial details, such as fairies, are often made of paintable resin.
- Transparent resin: This is the strongest class of resin and therefore the most suitable for a range of 3D-printed products. Often used for models that must be smother to the touch and transparent in appearance.
Transparent resins of clear and colored varieties are used to make figurines, chess pieces, rings and small household accessories and fixtures.
Metal
The second-most-popular material in the industry of 3D printing is metal, which is used through a process known as direct metal laser sintering or DMLS. This technique has already been embraced by manufacturers of air-travel equipment who have used metal 3D printing to speed up and simplify the construction of component parts.
DMLS printers have also caught on with makers of jewelry products, which can be produced much faster and in larger quantities — all without the long hours of painstakingly detailed work — with 3D printing.
Metal can produce a stronger and arguably more diverse array of everyday items. Jewelers have used steel and copper to produce engraved bracelets on 3D printers. One of the main advantages of this process is that the engraving work is handled by the printer. As such, bracelets can be finished by the box-load in just a few mechanically programmed steps that do not involve the hands-on labor that engraving work once required.
The technology for metal-based 3D printing is also opening doors for machine manufacturers to ultimately use DMLS to produce at speeds and volumes that would be impossible with current assembly equipment. Supporters of these developments believe 3D printing would allow machine-makers to produce metal parts with strength superior to conventional parts that consist of refined metals.
In the meantime, the use of 3D parts is taking flight in the aerospace industry. In what has been the most ambitious push of its kind, GE Aviation plans to print engine injectors at an annual rate of 35,000 units by 2020.
The range of metals that are applicable to the DMLS technique is just as diverse as the various 3D printer plastic types:
- Stainless-steel: Ideal for printing out utensils, cookware and other items that could ultimately come into contact with water.
- Bronze: Can be used to make vases and other fixtures.
- Gold: Ideal for printed rings, earrings, bracelets and necklaces.
- Nickel: Suitable for the printing of coins.
- Aluminum: Ideal for thin metal objects.
- Titanium: The preferred choice for strong, solid fixtures.
In the printing process, metal is utilized in dust form. The metal dust is fired to attain its hardness. This allows printers to bypass casting and make direct use of metal dust in the formation of metal parts. Once the printing has completed, these parts can then be electro-polished and released to the market.
Metal dust is most often used to print prototypes of metal instruments, but it has also been used to produce finished, marketable products such as jewelry. Powderized metal has even been used to make medical devices.
When metal dust is used for 3D printing, the process allows for a reduced number of parts in the finished product. For example, 3D printers have produced rocket injectors that consist of just two parts, whereas a similar device welded in the traditional manner will typically consist of more than 100 individual pieces.
Carbon Fiber
Composites such as carbon fiber are used in 3D printers as a top-coat over plastic materials. The purpose is to make the plastic stronger. The combination of carbon fiber over plastic has been used in the 3D printing industry as a fast, convenient alternative to metal. In the future, 3D carbon fiber printing is expected to replace the much slower process of carbon-fiber layup.
With the use of conductive carbomorph, manufacturers can reduce the number of steps required to assemble electromechanical devices.
Graphite and Graphene
Graphene has become a popular choice for 3D printing because of its strength and conductivity. The material is ideal for device parts that need to be flexible, such as touchscreens. Graphene is also used for solar panels and building parts. Proponents of the graphene option claim it is one of the most flexible of 3D-applicable materials.
The use of graphene in printing received its largest boost through a partnership between the 3D Group and Kibaran Resources, an Australian mining company. The pure carbon, which was first discovered in 2004, has proven to be the most electrically conductive material in laboratory tests. Graphene is light yet strong, which makes it the suitable material for a range of products.
Nitinol
As a common material in medical implants, nitinol is valued in the 3D printing world for its super-elasticity. Made from a mixture of nickel and titanium, nitinol can bend to considerable degrees without breaking. Even if folded in half, the material can be restored to its original shape. As such, nitinol is one of the strongest materials with flexible qualities. For the production of medical products, nitinol allows printers to accomplish things that would otherwise be impossible.
Paper
Designs can be printed on paper with 3D technology to achieve a far more realistic prototype than a flat illustration. When a design is presented for approval, the 3D-printed model allows the presenter to convey the essence of the design with greater detail and accuracy. This makes the presentation far more compelling, as it gives a more vivid sense of the engineering realities should the design be taken to fruition.
Get 3D Plating From Sharretts Plating Company
For more than 90 years, Sharretts Plating Company has offered prompt, affordable, high-quality plating services. Operating from our 70,000-square-foot Pennsylvania production facility, we offer services to customers across North America and abroad. As one of the most globally recognized names in the plating industry, our customizers know they can trust us for plating, metal finishing and other solutions.
With each passing decade, SPC has remained at the forefront of innovation in the world of plating. Now, with 3D printing technology approaching maturity, we are determined to meet the demands of this exciting and revolutionary new form of product creation.
At SPC, our extensive background with plating applications has allowed us to apply these capabilities to 3D-printed parts. In recent years, we have applied surface finishing to 3D parts manufactured by electronics and automotive companies as well as in numerous other industries. Regardless of your industry, we can customize a process that will suit your products.
Ultimately, companies that master this technology are bound to have an edge over their competition. Browse our 3D-print plating page to learn more about the options and contact us today for a free quote.
What material does the 3D printer print with? Plastic for 3d printer.
Layer-by-layer printing of three-dimensional models is made from a variety of materials, be it plastic, concrete or metal, and even hydrogel, chocolate and living cells.
For 3D printing, the use of ABS plastic is most optimal. Acrylonitrile butadiene styrene (official name ABC plastic ) is valued for the absence of foreign smell, toxicity, in addition, it is impact resistant, flexible and elastic. The material begins to melt from 240 to 248 degrees Celsius. Plastic goes on sale in a powdered state, or in the form of bobbins with plastic threads wound around them. Despite the fact that plastic does not tolerate direct sunlight, models made from it are famous for their durability. Plastic for a 3D printer can be bought in our online store.
Unlike ABC plastic, which models are opaque, acrylic is used to create transparent objects. But acrylic is more capricious in the process of use: the melting point of acrylic is reached later, which means that it will take more time and energy to heat up, and at the same time it quickly cools and hardens. The very process of manufacturing the product is laborious, since heated acrylic contains a lot of air bubbles that can distort the finished product.
Concrete applied for 3D printing , improved, and has a formula that differs from the formula of conventional cement by 5%. The “printing” of a residential building with an area of 230 m2 on a 3D printer will take no more than 20 hours, during which it carefully “lays out” building blocks and structures from concrete.
The use of hydrogel for 3D printing was successfully tested by scientists from the University of Illinois, who used a 3D printer to print miniature (5-10 mm) biorobots. Living cells isolated from the tissue of the heart muscle were placed on them, which, spreading through the hydrogel, set the biorobot in motion. The speed of such a biorobot is 236 µm/s. As planned by scientists, in the future, with the help of such biorobots, tumors and toxins in the body will be detected and neutralized, and they will also be used to deliver medications to diseased human organs.
There are 3D printers that use ordinary office paper as a material. Pre-cut layers of paper are applied one on top of the other and attached with glue. Paper models are cheap enough that they are accessible to users, but at the same time, paper models are not durable and not aesthetically pleasing. Models created in this way are ideal for prototyping in computer projects.
Gypsum used for 3D printing is a fragile, short-lived material, but at the same time it has a low cost. Therefore, models made of plaster are mainly suitable for presentations, perfectly conveying the shape, structure and size of the original product. The resistance of gypsum to heat treatment makes it possible to use it in the foundry as samples for casting.
Fans of natural wood and products made from it will also enjoy 3D printing, as there is a specially designed “wood” fiber that contains wood and a polymer, and its properties are similar to polyactide (PLA). Outwardly looking like natural wooden models with the smell of fresh wood, they are quite strong and durable. Currently, the material can only be used in the RepRap self-replicating printers.
3D printing with ice is perhaps the most exotic way of making small figures today. The temperature at which the figures are printed is quite low and is -22 degrees Celsius, and the printing material is water and methyl alcohol heated to 20 degrees Celsius.
The pleasant soft sheen and high strength of the metal are far ahead in quality of any plastic used in 3D printing, therefore light and precious metal powders are successfully used in this area. Copper, aluminum and its alloys, gold and silver in powder form are used for printing, adding fiberglass and ceramic inclusions to them.
Nylon printed parts are similar in many ways to ABS plastic parts, but are softer and more practical. Nylon manufacturing technology is more capricious, in particular, it has a longer curing period, the printing temperature reaches 320 degrees Celsius, and it is more toxic.
The 3D printers of the near future will print shaped chocolate molds, which should be in great demand in restaurants and pastry shops.
It is also impossible not to mention polycaprolactone, the most popular consumable for 3D printing. This material is so valued for its excellent physical properties and the possibility of being used in various printing technologies.
Of the plastic materials for printing, it is also worth highlighting polycarbonate (hard plastic), polylactide material obtained from biomass, sugar beet or corn silage, polypropylene, polyphenylsulfone, which came from the aviation industry, and an unsurpassed leader in the field of 3D printing, used in any of its areas - polyethylene low pressure.
Among other things, there are also printers that carry out 3D printing with mixtures of clay, lime powder, food, cells from living organic matter. And what exotic materials will be printed 3D printers in the future, one can only guess.
3D printing materials | A wide variety of materials
Materials for 3D printing! To date, the main materials for printing on a 3D printer are PLA and ABS plastic. Both materials have long established themselves on the market and are used for printing on a 3D printer using layer-by-layer material build-up technology.
ABS (ABS) plastic is a plastic formed during the polymerization of substances such as acrylonitrile (A) with butadiene (B) and styrene (S).
PLA plastic, or as it is also called biodegradable plastic, is an aliphatic polyester with a monomer in the form of lactic acid. The materials for the production of such plastic are rapidly renewable resources - corn or sugar cane, that is, starch or cellulose.
PVA plastic. The well-known PVA glue is transferred from a dry state to a liquid of the desired consistency, then melted using special equipment and formed into PVA threads or special granules that are used for 3D printing.
An even newer material, Nylon, is resistant to a wide range of chemicals and solvents. The materials discussed above are known to everyone who is associated with the 3D technology market.
These are the most commonly used materials. But manufacturers have stepped far ahead, and are already using a wide variety of materials for printing on a 3D printer, for example, clay, resin, seaweed, and more. etc.
Here is a list of the most unexpected and creative materials for 3D printing:
White Resin from Formlabs:
3D Printing Materials
3D printing equipment manufacturer Formlabs introduces a new material - White Resin. The company has recently launched two new 3D printing materials, Clear Resin and Gray Resin. The main feature of the White Resin material is the striking white and opaque color of the material, as well as the exceptional smoothness of the surface of the printed object. In addition, this material is ideal for subsequent staining.
Titanium Powder for 3D Printing Auto Parts:
British metalworking company Metalysis has released a new cheap titanium powder that is suitable for 3D printing of auto parts and parts. Until now, the most popular materials for 3D printing have been plastics, due to the high cost of producing titanium powders. But recently, Metalysis has found a new, low-cost way to produce titanium powder, which could become the most sought after in the manufacture of equipment and machinery in the aerospace, defense and automotive industries.
For the production of titanium powder, Metalysis uses rutile, which is electrolyzed directly into titanium powder. This method of obtaining a powder makes it possible to change, if necessary, the size of the powder granules, its purity, morphology and the proportion of the content of alloying elements in the composition.
Metal plastic for ColorFabb 3D printer:
Materials for 3D printing
BronzeFill and CopperFill are two new filaments from the premium Dutch manufacturer colorFabb. Their key feature is the addition of bronze and copper powder to the plastic, which gives the filament additional rigidity, as well as a pleasant metallic sheen and smoothness. To the touch, the model obtained as a result of printing will very much resemble a metal one.
Bronzefill and CopperFill can be polished to a beautiful metallic sheen just like any other hard bronze and copper items. After polishing, the visible streaks that remain after printing disappear, and the bronze or copper item begins to shine.
Bronze and copper plastic for 3d printing is ideal for prototyping metal products and obtaining very durable models in industry, architecture, design and other fields.
One of the most amazing materials is graphene:
3D Printing Materials
A 3D printable material with incredible potential for applications in various fields (molecular programming, solar energy, etc. ), it can change the lives of many people. In this regard, the Canadian research company Lomiko Metals Inc. announced the opening of a new special laboratory Graphene 3D Labs Inc., which will focus on the development of high-performance materials based on graphene. Information about the material: graphite or graphene is entirely composed of carbon atoms, but 1 mm of graphite contains about 3 million layers of graphene. Graphite has a three-dimensional crystal structure, while graphene is a two-dimensional crystal 1 atom thick.
3D Printer Wood Filament:
3D Printing Materials
Dutch 3D printing material company colorFabb has launched WoodFill wood filament. Wooden threads WoodFill are available in two types - Fine (Delicate) and Coarse (Rough). The main difference between these threads is the quality of processing of wood fibers. WoodFill Fine uses finely ground wood particles, WoodFill Coarse threads are thicker - based on coarsely ground wood particles. Wooden threads allow you to print beautiful and original vases, decorative elements and interior items. Finished objects are highly durable and produced in a short time. WoodFill filaments are made up of 30% pine wood fibers and 70% PLA plastic.
Seaweed 3D Printer Filament:
3D Printing Materials
Le Fabshop is the first company in the world to introduce SWF filaments - "green" filaments based on seaweed.
New materials from Proto-Pasta:
Recently, scientist Aaron Crum and mechanical engineer Dustin Crum launched the Proto-Pasta project, which developed three new materials for use in a desktop 3D printer: Carbon Fiber Reinforced PLA ( PLA reinforced with carbon fiber), High Temperature PLA (high temperature PLA) and Polycarbonate-ABS (ABS with polycarbonate alloy). Compared to all known types of plastic - ABS and PLA, the presented materials have improved performance characteristics and are affordable. Carbon Fiber Reinforced PLA is more resistant to high temperatures than regular PLA. Polycarbonate-ABS (PC-ABS) is characterized by high elasticity and bending strength.
Rubber material for stereolithography:
Materials for 3D printing
This is a rubber based material ideal for stereolithography printing, the new material has a wide color gamut, allows you to print objects in high resolution, odorless, easy to peel, available from price.
3D printing material based on silk:
3D printing materials
Another 3D printing material was created from raw silk. The raw silk has been sourced from sustainable sources and treated with epoxy. The silk-based material is flexible and highly durable, thin and light, ideal for 3D printing applications.
Polished and Raw Brass for 3D Printing:
3D Printing Materials
Shapeways has introduced two new materials to the world at once - Polished Brass and Raw Brass. Polished Brass is a material with a smooth, glossy bright yellow surface. Products printed with its help, then covered with 22 carat gold, are almost indistinguishable from real gold jewelry. Raw Brass is ideal for 3D printing antique or antique-style objects, and is also useful for jewelry prototyping and functional parts.
Shapeways Soft Plastic:
3D Printing Materials
Shapeways has developed a new soft plastic, Elasto Plastics, for use in summer footwear. Elasto Plastics has a milky white color, the material is very flexible, has an uneven grainy surface and is quite strong.
In our online store ac5ffgxkeg.lceqo.ccwc.finefive.ru there is an excellent analogue of Elasto Plastics - this is a unique flexible plastic from a Ukrainian manufacturer - PLASTAN 9 plastic0003
The second analogue - FlexibelPolyEster (FPE) - is a rubber-like elastic plastic thread designed specifically for printing on a 3D printer
Transparent resin for a 3D printer:
Materials for 3D printing stereolithography, according to the technology of layering transparent resin and strengthening the layers with a special laser.
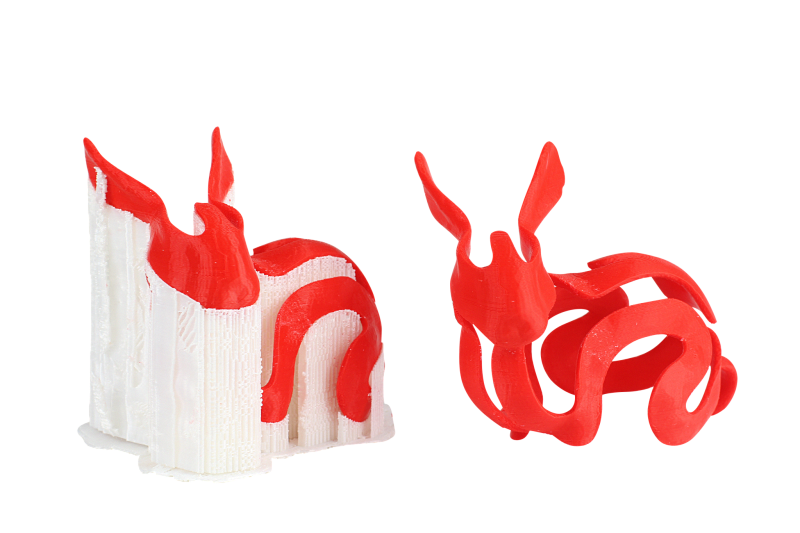