3D printing electricity cost
How Much Electric Power Does a 3D Printer Use? – 3D Printerly
Besides the cost of the 3D printer itself and the material to actually print out objects, there’s another thing creeps into people’s minds. Just how much electric is this thing using?!
It is a fair question. As fun as it is to 3D print our own objects, we want it to be as cost effective as possible. In this post I’m going to identify just how much power these 3D printers are using up and ways to manage it.
The average 3D printer with a hotend at 205°C and heated bed at 60°C draws an average power of 70 watts. For a 10-hour print, this would use 0.7kWh which is around 9 cents. The electric power your 3D printer uses depends mainly on the size of your printer and the temperature of the heated bed and nozzle.
There’s some more pretty useful information that you’ll want to know in the rest of this article, so keep on reading to get the proper knowledge on electricity with 3D printers.
If you are interested in seeing some of the best tools and accessories for your 3D printers, you can find them easily by clicking here (Amazon).
Determine Power Use by 3D Printer Specifications
Your 3D printer specifications for the power source and maximum/minimum power ratings are the answers you need so you know the limits of power consumption.
As an example, if a printer has a 30A 12V power source, it will have a maximum Watt of 360 (30*12=360), but the printer won’t always run at the upper limit. These maximums will kick in when heating up the necessary parts to start the printing process but will fall much lower as the printing is happening.
A great low-power 3D printer has to be the Ender 3 (Amazon), it’s an all-round popular machine that is perfect for beginners with quality that matches the most premium printers out there. You’ll see from the glowing reviews just how good it is!
Jason King from 3DPrintHQ used the MakerBot Replicator 2 printer and found that the energy costs were only $0. 05 for a 5-hour print. 3D printing only used 50 watts per hour, which is comparable to an HP Laser Jet printer on stand-by, not even while printing or 1 use of your toaster.
Low Relative Cost of Power
When looking at the overall cost of 3D printing, power costs are something that is relatively very low and not something to worry about. Some printers will of course be more efficient than others, but not at such a point that it’s a big determining factor when choosing a printer over another.
Now there are slight differences in how much power a 3D printer is using depending on what the printer is actually doing. When the printer is preheating to the set temperature, if the print bed is relatively large it will use slightly more power than when printing.
The first real use of electric power when a 3D printer is turned on is the heating of the print bed, then comes in the nozzle is heated to the temperature for the specific material. While printing, you will get spikes in the power usage depending on if the heated platform is on to maintain the ideal temperature.
From what I’ve read around, it looks like the average 3D printer consumers as much electric as your standard fridge.
What Affects How Much Power is Used?
Strathprints done a test to compare the power consumption between four different 3D printers and confirmed a few things. The lower the layer thickness of the material, the longer a print will take therefore leading to a higher power consumption overall.
If you can speed up your prints you’ll be using less power overall so check out my post 8 Ways to Speed Up Your 3D Printer Without Losing Quality.
When the heating efficiency of a print bed or hot end is good, it will result in less power being used due to not having to constantly keep the temperatures hot as much.
The video below shows the wide differences in how much electricity a 3D printer will use when incorporating the heated bed.
A good idea to lower how much heating your bed has to do is to use an Ashata Heat Insulator Mat. It has great thermal conductivity and greatly reduces heat and cooling loss of your heated bed.
The MakerBot-Replicator 2X had a baseline of between 40-75 watts to power the controller and motor, but peaked to 180 watts when heat was needed. The hotter the necessary print bed temperature, the more frequent the 3D printer drew power shown by fluctuations in the watt meter used.
The test showed that there is quite a variance between the power consumption of 3D printers. So, it can be concluded that 3D printers don’t consume a similar level of power and it really does depend on many factors.
The set-up parameters of your 3D printer will have a pronounced influence on the overall power consumption. It is important to be familiar with the process of 3D printing so you can print high quality products at lower electricity levels.
If you want to take an extra step, get yourself an enclosure. A great one is the Sovol Warm Enclosure for Ender 3D Printers. It’s pretty pricey, but it will last you years and usually results in better prints.
How Do I Lower Electricity Costs With a 3D Printer?
- Use a smaller 3D printer
- Use 3D printing materials that don’t require a heated bed or high nozzle temperatures (PLA)
- Implement 3D printer settings that make 3D prints quicker
- Change to a larger nozzle so your prints don’t last as long
- Make sure you are 3D printing in a fairly warm environment
When it comes down to lowering power costs with your 3D printer, it boils down to finding ways that speed up your 3D prints and doesn’t require as much heating.
The simple things you can do to speed up prints is to use a bigger nozzle, use less infill, print less often, or printing more things at once rather than doing them separately.
Most of the electricity use comes from the heating elements, so focus on reducing the heat and you’ll be able to save more on power.
This isn’t usually a problem since the associated costs aren’t relatively high. You’re definitely going to be using more money on the filament itself than you ever would with the electricity.
How Much Power Does a 3D Printer Use?
How Much Electric Does an Ender 3 Use?
One Ender 3 user who had their 3D printer running for 4 hours only used around 0.5kWh (kilowatt-hour), which consisted of heating up twice (using 280 watts per). When you calculate this on a per hour basis, we can 0.12kWh per hour of using an Ender 3.
People like to know how much power would cost if their Ender 3 was running for a full day, so let’s take a 24-hour period.
24 * 0. 12kWh = 2.88kWh
The average cost of one kilowatt-hour across the US is 12 cents according to NPR, so a full 24 hours of running an Ender 3 would cost $0.35. If you ran your Ender 3 24 hours for the whole month, it would cost you around $11.
The Ender 3 has a 360W power supply (24V DC at 15A.
- Heated Bed – 220W
- 4 Stepper Motors – 16W
- Fans, Mainboard, LCD – 1-2W
After these parts, you should have a spare 60-70 Watts in spare capacity, which allows you to add extra things.
A basic set of 5050 LED lights connected to your 3D printer can be around 20W.
Can You Get Electric Shocks From a 3D Printer?
Now that you know 3D printers don’t actually use that much electricity, you might be wondering whether they are still capable of giving you electric shock. This is a valid question and the answer is pretty simple.
A 3D printer can give you electric shock if you don’t handle it properly, but with proper use, you will be safe from getting an electric shock.
One 3D printer user actually received an electric shock from the power supply, but it was through misuse. After setting up their 3D printer, they used an EU to UK adapter and set the voltage to 230V.
It would have been a better idea to purchase or get the seller to send them a UK plug rather than use an adapter. This could have happened due to poor grounding, because a small current can flow through the connections from the live wire.
Luckily it was just a harmless tingle/shock! You shouldn’t use electronics which are not grounded when they are supposed to be.
How Can I Measure My Actual Electricity Use?
When it comes to electricity use, there really isn’t a perfect measurement we can give you because there are many differences and variables. The best thing you can do to really know how much power you are using is to measure it yourself, rather than us guess for you.
You can purchase a power meter which has an in-built power usage monitor. High-end ones can even calculate the cost of your power usage, so it can easily answer your question.
There are plenty of electricity monitors out there, so I done some research and found one that works very well for most people.
The Poniie PN1500 Portable Electricity Monitor is going to be your best choice. Not only is it officially ‘Amazon’s Choice’ at time of writing, but it is the highest rated out of all the monitors at 4.8/5.
Here’s what’s good about this power monitor:
- Very easy to use, with access to different power parameters
- High-precision current sensor
- Backlight & memory with large digital numbers for easy viewing
- Ability to start detection at just 0.20W so you can monitor almost anything
- 1 full year warranty
You can easily monitor electrical use in real time and it has multiple uses which can allow you to save on future electricity bills. Whether you test other appliances like an old refrigerator or other power-wasting appliances.
Range Of Electricity Use For A 3D Printer
An example of the minimum and maximum levels of power a 3D printer can use is the MakerBot Replicator+, which according to the specs has between 100-240 volts and 0. 43-0.76 amps. To convert this, we simply need to multiply the lower ends and higher ends to get our limits.
100 volts * 0.43 amps = 43 watts
240 volts * 0.76 amps = 182.4 watts
So, the power can range anywhere between 43 and 182.4 watts.
From the watts, we convert this to kilowatts per hour (KwH) by dividing the watts by 1000 then multiplying the number of hours in use. For example, if you had a print that lasted 5 hours the calculation would be:
43 watts/1000 = 0.043 Kw * 5 hours = 0.215 KwH for the lower limit.
182.4 watts/1000 = 0.182 Kw * 5 = 0.912 KwH for the upper limit.
Just as an example, if we take the happy middle for these two power measurements, we’d have 0.56 KWh, costing you only 5-6c in electricity per hour. So now you have a bit of a gauge in just how much electric is used in 3D printing, which isn’t much at all but it can slowly build up over time.
Compared to the actual cost of the 3D printer, the filament materials and other tools and equipment the electric power required for 3D printers is something that you shouldn’t have to worry about.
When we’re talking about sizeable professional printers, then the power costs could be something to take into consideration, but for your standard domestic 3D printer it is very low cost.
If you love great quality 3D prints, you’ll love the AMX3d Pro Grade 3D Printer Tool Kit from Amazon. It is a staple set of 3D printing tools that gives you everything you need to remove, clean & finish your 3D prints.
It gives you the ability to:
- Easily clean your 3D prints – 25-piece kit with 13 knife blades and 3 handles, long tweezers, needle nose pliers, and glue stick.
- Simply remove 3D prints – stop damaging your 3D prints by using one of the 3 specialized removal tools.
- Perfectly finish your 3D prints – the 3-piece, 6-tool precision scraper/pick/knife blade combo can get into small crevices to get a great finish.
- Become a 3D printing pro!
How Much Electricity Does A 3D Printer Use? [EXPLAINED]
If you own or plan to buy a 3D printer, you may be wondering how much electricity does a 3D printer use?
As energy prices soar across the globe, we’re more conscious than ever of our consumption, with many of us looking for ways to reduce our usage to cut costs or at least establish a better understanding of where our money is going.
Considering the hefty price of the machine itself alongside filament and maintenance costs, how much of an impact does a 3D printer’s energy needs have? How do they compare to your average home appliance in terms of energy consumption?
In this guide, we’ll be bringing answers to these very questions and more, with a few surprises along the way that reveal home 3D printing as a fairly energy-efficient pursuit.
Table Of Contents
- How Much Electricity Does a 3D Printer Use?
- How Much Electricity Does a 3D Printer Use Per Hour?
- Are 3D Printers Energy Efficient?
- Factors That Affect 3D Printer’s Energy Consumption
- Printer Size
- Heated Bed
- Hotend/Print Temperature
- Mainboard, Fans, Stepper Motors, and Display
- Print Time
- How to Lower a 3D Printer’s Energy Consumption
- Lower Temperatures
- Print in High Ambient Temperatures or Use an Enclosure
- Shorten Print Times
- Energy-Efficient Components
- How Much Does it Cost to 3D Print?
- How Much Does it Cost to 3D Print in the US
- How Much Does it Cost to 3D Print in the UK
- FAQs
A consumer-grade 3D printer uses roughly anywhere from 50 to 150 Watts of power, equating to between 0. 05 kWh and 0.15 kWh. This represents an average and depending on whether the printing is getting up to temperature, is idle, or is in the middle of a print the power consumption can drop as low as a handful of Watts all the way up to the 3D printer’s rated power/maximum Wattage, for example 400 Watts.
Though these 3D printer power usage figures give us an estimate, they by no means apply to all 3D printers.
Factors like bed temperature, the size of the printer and build volume, print temperature, number of extruders, ambient room temperature, and even the complexity of the print (i.e. stepper motor activity) affect power consumption.
But for the sake of providing a reasonably general sense of the power requirements of a 3D printer, these numbers are what you can expect from typically popular printers like:
- The Ender 3
- Anycubic Kobra
- Voxelab Aquila
- Prusa i3 MK3S+
How Much Electricity Does a 3D Printer Use Per Hour?
Taking our average energy consumption range of 50 to 150 Watts, an average 3D printer uses 0. 05 kWH to 0.15 kWh per hour. Factors like size and temperature can push these figures higher as well as lower. You’d need to run an average machine for between 7 and 20 hours for 3D printing energy consumption to exceed 1 kWh.
Are 3D Printers Energy Efficient?
Yes, 3D printers can be considered energy efficient. On its own, 50 to 150 Watts doesn’t mean much, but when compared to common home appliances we get a better sense of how surprisingly little energy 3D printing requires.
Again, it’s important to stress that this covers a typical, consumer-grade 3D printer.
Considering these wattages for the most common household appliances, we can conclude that a 3D printer’s electricity consumption is equivalent to that of a video game console and high-end TV.
Home Appliance | Energy Consumption (Watts) |
---|---|
Kettle | 1,000-3,000 |
Oven | 2,000-2,400 |
Toaster | 800-1800 |
Microwave | 700-1,400 |
Electric Iron | 1000 |
Vacuum Cleaner | 450-900 |
Desktop PC | 300-600 |
Refrigerator | 100-200 |
Video Game Console | 100-200 |
TV | 25-175 |
60W Light Bulb | 60 |
Chromebook | 45 |
Wi-Fi Router | 4-10 |
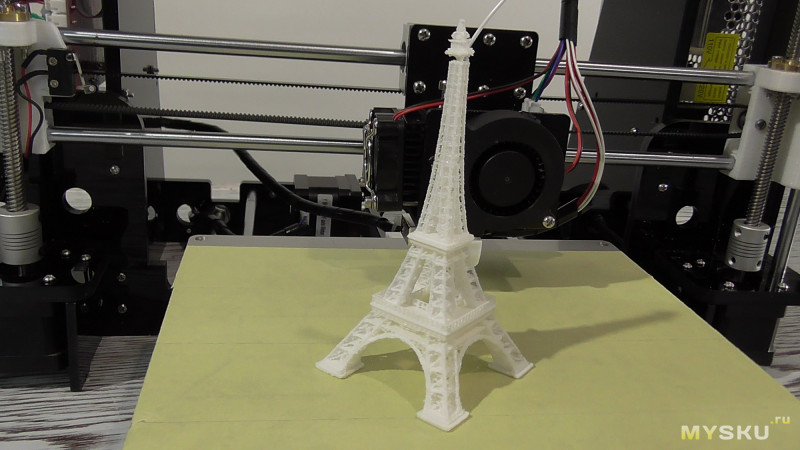
Factors That Affect 3D Printer’s Energy Consumption
Printer Size
The size of the printer itself has no bearing on energy consumption, but extra build volume does have an impact on the printing process, which can make energy consumption rise.
With a larger build volume, a bigger 3D printer will require the stepper motors to have more power to move the print ahead across a larger build volume if it’s used to its full capacity.
A large bed requires more power to heat the larger surface evenly and uniformly (more on that below). These factors are generally reflected in larger 3D printers having a higher maximum wattage.
Conversely, a smaller printer with a more modest build volume will require less power to heat to a suitable temperature for printing and the stepper motors won’t have to rely on as much energy to complete a print.
Heated Bed
Heating the bed to suitable temperature sits alongside reaching a print-ready hotend temperature as one of the most energy-intensive processes involved in the 3D printing process.
If you were to measure a printer getting a build plate up to temperature, you would see a significant energy consumption spike, the highest of any part of the printing process.
Once the printer reaches the required temperature, it uses less energy to maintain it, though this can vary depending on ambient temperature. A printer sitting in a cold room at the height of winter requires substantially more power to maintain, for example, a 60°C bed temperature, than on a sunny 30°C summer’s day.
Hotend/Print Temperature
As above, the hotend is arguably the most important component of the 3D printing process, tasked with melting filament ready for deposition by the nozzle.
Heating the hotend to melt filament accounts for a large portion of a 3D printer’s energy budget. Most of this happens when the printer is reaching the right temperature for printing, tailing off to smaller spikes to maintain the temperature.
Different filament types require different temperatures, so the amount of power consumed can vary somewhat whether you’re using PLA, ABS, PETG, or a high-temperature filament such as Nylon.
Much like the heated bed, consumption is also affected by ambient temperatures: the heating element powering the hotend will need to work harder and longer to reach a printing temperature in a colder setting.
Mainboard, Fans, Stepper Motors, and Display
Vital components on a 3D printer, the mainboard, fans, display, and stepper motor require roughly 30-60 Watts between them when in use.
Compared to the heated and hotend which make google up as much as 300 Watts to heat up, these numbers are small, but do factor into the overall power consumption.
Print Time
An obvious one – the longer a printer runs, the more power it consumes. Though beyond the scope of this article, factors like print speed, print size, layer height, support structures, and infill density weigh have a role in determining print times.
How to Lower a 3D Printer’s Energy Consumption
Lower Temperatures
As we know, the most energy-hungry part of the printing process is reaching and maintaining the heated bed and hotend at a temperature that’s suitable for 3D printing. It, therefore, stands to reason that by lowering the temperature will reduce power consumption.
Now, there’s limitations to this which are linked to filament having very specific requirements to not just melt but also adhere properly to the print surface, but it is possible to tweak temperature lower by a few degrees to improve the efficiency of your printer. It’s also worth experimenting with the heated bed turned off, especially with filament like PLA, which technically doesn’t need a heated bed to thrive.
Filament manufacturers provide a recommended temperature range for both the bed and hotend. It’s worth running a test print towards the lower end of the range. If you don’t encounter any temperature-linked issues like warping and bed adhesion problems, then keeping the temperature low is a great way to save on energy consumption.
Lowering temperatures becomes viable when you take into account the following section and adapt your printing environment.
Print in High Ambient Temperatures or Use an Enclosure
As we mentioned above, ambient temperature dictates how hard the heating elements in the bed and hotend have to work to get up temperature. If possible, install and use your 3D printer in a warmer space with a steady, non-fluctuating ambient temperature.
If that isn’t possible, we recommend buying an enclosure. Acting as insulation that protects the printer from outside temperature changes and cool air, an enclosure will maintain a stable thermal environment around your printer, which means the printer won’t need to work quite as hard to maintain the temperature of the heated bed and hotend.
For more on enclosures, including a few thrifty DIY options, check out our dedicated guide. It’s tailored to the Ender 3, but applies to most consumer 3D printers out there.
Shorten Print Times
The less a printer is running and using the power, the lower the energy consumption. As such, reducing and shortening print times is a fantastic way to lower a 3D printer’s energy consumption.
Though print times deserves an article all to itself (fortunately, we’ve got one), here’s a quick breakdown of what settings can reduce print times:
- Layer Height
- Infill Density and Pattern
- Print Speed
- Support Structures
- Rafts/Brims/Skirts
There is a point of diminishing returns here: lower these settings to low and the print suffers, not just in terms of visual quality, but structural integrity.
Worse, the printer may be unable to complete the print with extreme settings, forcing you to pump even more power into the machine for a second or even third printing attempt.
Energy-Efficient Components
It’s also possible to reduce a 3D printer’s energy consumption by upgrading to more energy-efficient components, namely the power supply, fans, mainboard, and, more extreme, swapping for a more energy-efficient modern printer.
That said, you’ll likely have to use the printer for years before you get a return on your investment, so this only really applies for heavy-users sure of using their machine for the foreseeable future.
How Much Does it Cost to 3D Print?
How much it costs to 3D print will vary greatly depending on your country and even region of residence along with the size of the print and how long it takes to print.
While we couldn’t cover every possible permutation for every country, here’s some ballpark figures for the US and UK to give you an idea of the electricity costs involved in running a 3D printer.
How Much Does it Cost to 3D Print in the US
- Average kWH Price – $0.15
- 3D Printer Electricity Usage – 0.05 to 0.15 kWh
You can expect to pay if you were to run the printer uninterrupted:
- Per Hour – $0.007 and $0.02
- Per Day – $0.17 and $0.48
- Per Year – $62.05 and $175.02
How Much Does it Cost to 3D Print in the UK
- Average kWH Price – £0.28
- 3D Printer Electricity Usage – 0.05 to 0.15 kWh
You can expect to pay if you were to run the printer uninterrupted:
- Per Hour – £0.01 and £0.04
- Per Day – £0.24 and £0.96
- Per Year – £87.60 and £346.75
These figures don’t take into account the standing charge (roughly £0.71 per day currently in the UK).
FAQs
Does 3D Printing Take a Lot of Electricity?
No, 3D printing requires roughly as much power as a video game console or high-end television, though this can vary depending on the specifics of the printer. A 3D printer consumes on average 50 to 150 Watts, which works out as 0.05 kWh and 0.15 kWh. A current generation video game console 5 consumes 0.1 kWh – 0.2 kWh, while a TV requires anywhere from 0.025 kWh to 0.175 kWh.
Do Printers Use a Lot of Electricity?
No, 3D printers use surprisingly less energy than you’d expect given how much heat they require to function. An average 3D printer consumes 50 to 150 Watts on average, which is roughly equivalent to two 60 W light bulbs.
Related posts:
- Are 3D Printers Worth Buying? (Pros & Cons Discussed)
- Best 3 in 1 3D Printers with Laser Engraving & CNC Feature
- Best Large 3D Printers For Every Budget
- Top 3D Printers for Every Price Range
- Sovol SV04 Hands-On Review – Best Low-Cost IDEX 3D Printer?
How to calculate the cost of printing on a 3D printer
For some ideas, 3D printing is the fastest and easiest solution. In some situations, purchasing your own 3D printer can be a good solution, but sometimes it is much more profitable and faster to order the necessary product from a company specializing in 3D printing. Yes, and many owners of a 3D printer are thinking about how to “monetize” their hobby, but how to correctly calculate their costs?
Despite the fact that it is customary to indicate the price per gram of working material, simply multiplying the weight of the model by the cost of 1 gram will be wrong. In addition to the cost of consumables, many more, at first glance, non-obvious costs are added to the price of the product.
Each 3D printing technology uses its own consumables. Let's analyze the most popular and affordable of them.
Available technologies and key differences
Currently, a huge number of 3D devices have appeared, from small desktop ones that fit on the desktop to huge industrial machines. Among the most affordable, 2 technologies can be distinguished - FDM and photopolymer printers (LCD / DLP / SLA).
FDM 3D printing
Today, the most affordable 3D printing technology is FDM. A variety of materials and 3D printers allow FDM to be applied to a wide range of applications.
Schematic operation of FDM printer
A large selection makes it easy to choose a 3D printer for a specific task or find a universal device.
The material for printing is a plastic thread - filament. On the market you can find filament for various tasks, for every “taste” and budget. These can be very inexpensive ABS and PLA plastics or specific ones - conductive, burnable, etc.
Pros:
Cons:
Despite the fact that FDM allows you to print a wide range of plastics with different properties, the technology has some limitations. For example, it is impossible to obtain a perfectly smooth surface, to produce miniature and very thin elements, or to produce parts with very complex internal geometry with high accuracy.
Photopolymer printing
Photopolymer printers can work on one of 3 technologies - SLA, DLP or LCD. These devices will come to the rescue if you need to make a small but very detailed model with many small details.
How photopolymer printers work
As a consumable material, a photopolymer resin hardened by UV radiation is used. Now there is a wide variety of photopolymer resins for every taste. From particularly strong and precise engineering or jewelry resins to soft flexes.
Pros:
-
High print precision
-
Good surface quality
-
A wide variety of printers and consumables
Minuses:
Photopolymer printers have shown themselves well in a variety of industries that require a perfectly smooth surface and high accuracy. They are used in dentistry, the jewelry industry, for making miniature master models for casting, and much more.
Industrial printers
These are already industrial machines, which require a separate room and sometimes certain requirements for ventilation, etc. In this article, we will not analyze these devices in detail, but briefly consider the most popular technologies.
FDM
In addition to desktop devices using FDM technology, industrial printers that work on the same principle are common.
This category includes devices with a large print area (from 30x30x30 cm and more). For example, Raise Pro2 with a print area of 30x30x30 cm.
Raise Pro2
Or machines designed for printing with refractory materials (eg PEEK). Such 3D printers usually have an active thermal chamber, and the extruder can be heated above 400 degrees.
CreatBot F160-PEEK designed to work with refractory plastics
Photopolymer printers
Industrial photopolymer devices usually have a much larger working area, compared to their "home" brothers. In addition, many processes have been optimized and automated for faster operation. On such printers, you can quickly and accurately produce a small batch of models, a large prototype or a master model.
Prismlab Large Area Industrial Resin Printer Family
3DP
3DP - Three-Dimensional Printing (translated as three-dimensional printing) is a logical continuation of conventional two-dimensional printers. Printing is done using nozzles that selectively apply a binder to the material (usually gypsum). A dye can be added to the binder and the model will be colored.
Colored plaster model
Since the plaster model is fragile, a similar principle is used for printing with metals. Only the finished product needs to be treated in an oven to remove the binder and improve strength. But despite the processing, such metal prints will still be inferior in strength to cast products.
MJM
This is a proprietary technology of 3D Systems. MJM is a mix of FDM, 3DP and sometimes SLA (depending on material chosen). Printing is done using a variety of small nozzles (from 96 to 488) located on the head of the machine. The accuracy and quality of the surface of models made in this way is in no way inferior to photopolymer printers.
Models made with MJM technology
Such devices can work with photopolymer resins, wax or thermoplastics. You can combine several materials at once - for example, for complex models, you can use wax as a support.
SLM
SLM is the layer-by-layer sintering of metal powder using a powerful laser. There are several similar technologies - SHS/SLS. The principle of operation is the same, only a thermal print head is used instead of a laser beam.
SLM Turbine
As a material for printing, you can use powders of various metals - gold, stainless steel, aluminum, various alloys, etc.
During printing, the working chamber is filled with an inert gas to prevent oxidation of metals. This allows printing even with titanium powder.
Models made by this method are in no way inferior, and sometimes even superior, to cast products. SLM allows you to produce models with complex internal geometry that cannot be produced by another method (casting or milling).
Cost of 3D printing
The cost of a model usually consists of several factors.
-
Equipment depreciation. The printer, like any machine, requires maintenance and periodic replacement of some parts. During operation, belts gradually stretch, bushings or linear bearings wear out. For example, when bushings or linear bearings are worn; shafts may wear out and need to be replaced.
Cost of materials
The main cost item for a 3D printer is, of course, the printed material.;
FDM (plastic filament)
Since FDM technology is by far the most common, the choice of filaments is very diverse.
-
Engineering plastics are usually nylon with various fillers added to improve the physical characteristics of the finished model. Special cost. plastics starts from 2000r per coil and above. It all depends on the manufacturer and filler (carbon fiber, fiberglass, etc.).
-
Decorative plastics are used to imitate various materials. Plastic can simply be unusually colored (luminous, transparent plastics) or a special filler is added to it (plastics with metal powder). The cost of decorative plastics starts from 1500 rubles per coil and more, depending on the filler.
A big advantage of FDM is the diverse choice of materials to work with. This allows, having one printer, to produce almost any product - from a child's toy to a complex engineering prototype.
Photopolymers (resin)
Photopolymer resin printing technology is becoming more and more accessible. There are many different resins.
-
The cost of ordinary colored resin starts from 2500 rubles per 0.5 kg (volume +/- 0.5 l). You can find a smaller volume of resin (250 gr) on sale. You can buy several different resins in small containers and find out in practice which one is best for a particular model.
-
Engineering resins are resins with increased strength. They can be used not only for printing decorative items, but also for making functional prototypes and models. The cost for 0.5 kg starts from 5900r and above.
-
Special resins - burnable, dental, soft flexes, etc. Depending on the resin, the price for 0.5 kg can start from 4800 rubles and more. It all depends on the characteristics of the resin.
Photopolymer resins have not yet reached such a variety as FDM filaments, but they are surely catching up. Although due to the fact that a liter of resin costs significantly more than a spool of filament, the cost of the product is much higher.
Print examples
FDM
Mag Pull (quick release loop) for G3 magazines.
The model was downloaded for free from an open source (the file can be downloaded here). Printing with engineering carbon-filled plastic (price per spool from 4700 rubles). The weight of the model with support is about 25 grams. Post-processing was not needed. The cost of the finished model is 250 rubles.
Plastic fastener
The file was downloaded from an open source (can be downloaded here). Plastic - carbon-filled nylon (price per coil from 4700r). The weight of the finished product is about 20 grams. Print without post-processing. The total cost is 200 rubles.
Model watch
The model is modeled to order (the cost of modeling is from 1000 rubles). The product is printed on an industrial printer using soluble support. Print without post-processing. The cost of the finished product - from 700 rubles per piece (depends on the number of required products).
Traction prosthesis
The model is taken from an open source (you can download the modified version of the prosthesis here). The weight of the used material is about 600 gr, printed with ABS plastic (the cost of the coil is from 800 r). After printing, post-processing and assembly took place. The total cost of the product - from 3000 r (depends on the print material, support material, filling, etc.).
Pedal layout
Production of a 3D model according to the drawing (from 1000 r). The weight of the finished model is about 200 gr. The product was printed with engineering carbon-filled plastic (the cost of the coil is from 4700 r). Post-processing was not needed. The cost of the finished product is about 3000 rubles.
Photopolymer printers
Model jaws for crowns
Files for printing were obtained using a 3D scanner and finalized in a 3D editor (the cost of scanning is from 3000 r, the cost of manual revision is from 1000 r). Printing on an industrial photopolymer printer. Post-processing is not needed. The cost of the finished product is from 80 r per gram.
Burnout resin rings
The model is made to order. Printing on a desktop SLA printer with a burnable polymer. Post-processing is not needed. The cost of the finished product is 200 rubles per product.
Miniatures
The models were bought on the myminifactory website (the cost of the model is from $2). Made with a desktop DLP printer. Post-processing was not required. The cost of the finished figurine is from 70 r per gram.
Custom 3D printing
Many owners of 3D printers are thinking about monetizing their hobby. But you should understand that the price of 3D printing “for yourself” and the price of commercial printing are very different.
When starting to print to order, it is better to have several printers working on different technologies.
![]()
Cost of commercial 3D printing
In addition to the cost of the model, to the commercial production of products, you can add:
-
Modeling. Often the client needs not only to make a part, but to pre-model it. It can be a simple cogwheel that doesn't take long to model, or it can be a complex sculpture that takes more time to model than it does to make.
-
Model post-processing. This can be simply the removal of supports, with cleaning of the place of their contact with the product, or a complete processing cycle (puttying, surface grinding, painting, etc.).
It should be borne in mind that it is not always possible to print the model the first time. Sometimes it may take several attempts. And these are additional costs.
What is unprofitable to print
Despite the wide possibilities of 3D printing, there are models that are unprofitable to make on a 3D printer. For such models, it is better to use other manufacturing methods.
Commercial print examples
Jewelry for further casting
Manufacture of promotional items and souvenirs
Piece miniatures or master model for further casting
3D printed model
Profitable to print on a 3D printer:
-
If the item is only sold as an assembly. For example, a small gear broke in the mechanism, but the mechanism is sold only “assembly”. It is much cheaper to make the desired gear on a 3D printer than to buy the entire mechanism.
-
A small batch of parts. Small batches, especially models with complex geometry, are more profitable to produce on a 3D printer than by casting or other methods.
Totals
If you need several models or a small project, sometimes it will be more expedient to outsource manufacturing. After all, in addition to buying equipment and materials, you will have to understand the nuances of the settings and the characteristics of various materials.
Buying a 3D printer for commercial use is justified if you can fully load it with work or then it can be used for other purposes.
To print to order, you need to have several printers working on different technologies. It is better to get several devices with a smaller print area than to buy just one printer, albeit with a large working area.
How much electricity does a 3D printer use?
Author Kirill Sokolov Reading 8 min. 292 views Posted by
While 3D printing is certainly a fun hobby, there's no doubt that it can also get quite expensive. Apart from the cost of the printer and filaments, you could easily spend a few hundred dollars just to get started. Another recurring cost that we should not ignore is the cost of electricity consumed by a 3D printer.
Whether you're 3D printing for fun or business, the money you spend on electricity is what you need. keep in mind. How much electricity does a 3D printer use and what can you do to reduce your energy bills?
Table of Contents
- Step One: Check Your Printer's Power Rating
- What Factors Affect How Much Power 3D Printing Uses?
- Hot end heating
- Heating of the printed platform
- Heating losses
- Step engines
- Control board
- Comparison of energy consumption of various models of 3D printers
- Tips for reducing the costs of 3D printer
- 1. Use the Printer with the Corps
- 2. Rede printing
- 3. Print with high temperature fibers only when necessary
- Closing thoughts
Step One: Check Your Printer's Power Rating
Like any electrical device, your 3D printer must be rated. For example, a 3D printer that requires 30A 12V consumes up to 360W of power (power = current x voltage). This is a very high figure, but only because it is the maximum power that this particular 3D printer can draw.
There can be a very significant difference in power consumption if you print at high temperatures. , high speed settings or heated beds. However, between different models, you can expect printers with larger platforms to use more power, as well as printers that can print at higher temperatures.
What factors affect how much energy 3D printing consumes?
If you're interested in the exact amount of power your 3D printer requires, then the best way is to use a power consumption monitoring tool. These tools act as an interface between your 3D printer and an electrical outlet, giving you an accurate measurement of the volts, amps, and power your 3D printer draws. A good example is Kill A Watt Electricity Usage Monitor by P3.
It would be impossible to isolate any particular part of the 3D printing process and test how it affects the power consumption of the printer. Instead, we can sum up these factors and infer how much electricity they consume.
Heating at the hot end
One of the most energy intensive drain parts of a 3D printer is the hot end, specifically the part of the nozzle that melts the filament. How much energy this process consumes depends on the temperature you set as well as the type of filament you are working with. If you're working with a lot of high temperature fibers like nylon or ABS, then you're probably using a lot of electricity for just that part.
Print bed heating
The print bed temperature depends on the nozzle temperature. This is a measure that improves adhesion to the layer and prevents warping, which is one of the constant problems when working with high temperature fibers.
There are two factors to consider when evaluating the energy consumption of a heater. bed – temperature setting and bed size. The temperature also depends on the type of filament you are printing with. The size of the bed depends on your 3D printer. The larger the bed, the more energy will be required to maintain the set temperature.
Heat loss
3D printer components can reach temperatures above 200°C. They must also remain at this temperature, so any heat loss to the environment must be compensated by the heating element. This is another issue for high temperature 3D printing as a hotter nozzle and print bed will inevitably have higher heat loss. If there is a way to minimize heat loss, you can save a lot on your energy costs.
Stepper Motors
There are two important sets of stepper motors in a single 3D printer: those that drive the extruder gears and those that drive the movement of the nozzle. While these motors are very small and draw little power, they also need to be constantly running for the hours needed to complete a single 3D printing project.
Control Board
The control board or "brain" of a 3D printer consists of several electrical components that help control the printer's temperature, nozzle placement, extruder gears, and various other trivial tasks. Despite the importance of this feature, the control board does not actually consume much power.
The conclusion we can draw from this little exercise is that most of the energy consumed by a 3D printer goes towards heating the nozzle and the print bed. While not surprising, this fact also gives us insight into how we can reduce the power consumption of our 3D printing projects.
Comparison of power consumption of various 3D printer models
Since it is impossible to determine the exact power consumption of a 3D printer without specifying the model, we will look at how much power consumption of various 3D printer models and how this affects costs.
Let's start with the Monoprice Mini Delta, a very small and inexpensive Delta type device. A 3D printer that has proven to be quite popular among beginners. Among its distinguishing features are a small build platform and a print head driven by three stepper motors. The Monoprice Mini Delta reportedly only consumes up to 45W during bed and nozzle preheating. Power consumption during printing increases slightly to 60W, probably due to the action of the stepper motors.
To provide contrast, let's look at the power consumption of Flashforge Creator Pro. This is a much more expensive 3D printer with a larger print bed, a rigid metal frame, and a built-in housing. Preheating the large print bed required a staggering 300W of power, while the nozzle required slightly less than 280W. The case proved to be very useful in reducing heat loss and stabilizing the printer's power to 250W during printing.
The two 3D printers we referenced here give us a useful range of how much power models of varying complexity can consume, from 60W to 250W when printed. In terms of kWh, this range corresponds to 0.07–0.24 kWh.
This also allows us to compare the power consumption of 3D printers with other devices we have in the house. For example, a typical desktop computer consumes about 1.05 kWh, which is more than four times the power consumption of Flashforge Creator Pro.
Based on electricity tariff data from April 2020, the average US consumer pays 13.31 cents per kWh. This means that you will pay approximately 3.2 cents for every hour you use Flashforge Creator Pro. The numbers for the Monoprice Mini Delta are even more pleasantly surprising - you pay less than 1 cent for every hour of use.
These numbers are likely to come as a relief to 3D printing enthusiasts, especially those who leave their printers running for hours on end. While this isn't an excuse for wasting electricity, it's still nice to know that you haven't been hit hard on your running costs just because you got into 3D printing.
Cost Saving Tips 3D Printer Power Consumption
Although you've come to terms with the fact that you're unlikely to add a huge amount to your energy bill just because you use a 3D printer, many of you probably we still appreciate any advice on how to reduce power consumption.
1. Use the Printer with the
Enclosure According to our analysis of Flashforge Creator Pro, having a build platen enclosure can significantly reduce the power consumption of the 3D printer during the printing process. This becomes even more pronounced if you are printing with a filament that requires high temperatures for both the nozzle and the print bed. If you're using an inexpensive printer without a built-in case, you can simply make your own using a couple of plastic sheets and wood frames. There are many tutorials on the internet for DIY 3D printer cases.
2. Reduce Print Time
Time is a factor we haven't really talked about yet, but it's certainly one of the most important when determining how much power a 3D printer consumes. If you can reduce the print time of your project, you can significantly reduce your energy costs.
There are several ways to achieve this goal, but there are two that are particularly effective: increasing print speed and printing with thicker layers. Obviously, this is not advice that can be taken in a vacuum. When making these adjustments, you need to consider other factors such as print temperature, filament type, and the quality level of the finished product. .
3. Print with high temperature fibers only when necessary
Experimenting with different types of fiber materials is a natural part of 3D printing, but using those that require very high print temperatures can be quite expensive in the long run. . This requires not only more heat in the nozzle, but also a hotter print bed. The difference between 30 and 40°C may not seem like much, but every little thing counts – at least depending on which point of view you take.
Your 3D printer is unnecessary, then you can stick with low temperature fibers like PLA if you're printing just for fun. PLA not only saves energy but is also a more environmentally friendly choice due to its biodegradable nature.
Closing Thoughts
Consider how much power each of our electrical devices we consume on a regular basis is only part of being a responsible consumer. The same principle applies to 3D printers. As 3D printing is quickly becoming a hobby for more and more people, now is the perfect time to be more aware of how much power 3D printers use.