Hp 3d printer materials
HP 3D Printing Materials Portfolio - Expand your capabilities
The content of this site is for information purposes only and it is showing the product configuration for the US market only.
Availability, pricing, product configuration and specifications may differ according to geographical location, local laws and practices.
Please contact us or talk to your local HP 3D Printing representative for further information or for product configurations specific to your local country.
1. Nothing herein should be construed as constituting an additional HP warranty. The only warranties for HP products and services are set forth in the express warranty statements accompanying such products and services and/or in a written agreement between you and HP for such HP products and services. HP believes that the information herein is correct based on the current state of scientific knowledge and as the date of its publication, however, to the maximum extent permitted by law HP EXPRESSLY DISCLAIMS ANY REPRESENTATIONS AND WARRANTIES OF ANY KIND, WHETHER EXPRESS OR IMPLIED, AS TO THE ACCURACY, COMPLETENESS, NON-INFRINGEMENT, MERCHANTABILITY AND/OR FITNESS FOR A PARTICULAR PURPOSE (EVEN IF HP IS AWARE OF SUCH PURPOSE) WITH RESPECT TO ANY INFORMATION PROVIDED. Except to the extent that exclusion is prevented by law, HP shall not be liable for technical or editorial errors or omissions contained herein and the information herein is subject to change without notice. HP shall not be liable for damages or losses of any kind or nature that result from the use of or reliance upon this information. The HP Jet Fusion 3D Materials have not been designed, manufactured or tested by HP for compliance with legal requirements for 3D printed parts and their uses and recipients are responsible for making their own determination as to the suitability of HP Jet Fusion 3D Materials for their purposes and uses, ensure compliance with applicable laws and regulations, and be aware that other safety or performance considerations may arise when using, handling or storing the product.
2. Image courtesy of NACAR
3. HP Jet Fusion 3D Printing Solutions using HP 3D High Reusability PA 11 provide up to 70% powder reusability ratio, producing functional parts batch after batch. For testing, material is aged in real printing conditions and powder is tracked by generations (worst case for reusability). Parts are then made from each generation and tested for mechanical properties and accuracy.
4. HP Jet Fusion 3D Printing Solutions using HP 3D High Reusability PA 12 provide up to 80% powder reusability ratio, producing functional parts batch after batch. For testing, material is aged in real printing conditions and powder is tracked by generations (worst case for reusability). Parts are then made from each generation and tested for mechanical properties and accuracy.
5. Based on internal HP testing, May 2020. HP Jet Fusion 3D Printing Solutions using HP 3D High Reusability PP enabled by BASF provide up to 100% powder reusability ratio, producing functional parts batch after batch. For testing, material is aged in real printing conditions and reclaimed powder is tracked by generations (worst case for reusability). Parts are then made from each subsequent generation and tested for mechanical properties and accuracy showing no degradation of properties up to three generations of use.
6. HP Jet Fusion 3D Printing Solutions using HP 3D High Reusability PA 12 Glass Beads provide up to 70% powder reusability ratio, producing functional parts batch after batch. For testing, material is aged in real printing conditions and powder is tracked by generations (worst case for reusability). Parts are then made from each generation and tested for mechanical properties and accuracy.
7. HP Jet Fusion 3D Printing Solutions using HP 3D High Reusability CB PA 12 provide up to 80% powder reusability ratio, producing functional parts batch after batch. For testing, material is aged in real printing conditions and powder is tracked by generations (worst case for reusability). Parts are then made from each generation and tested for mechanical properties and accuracy.
8. Testing according to ASTM D638, ASTM D256, and ASTM D648 using HDT at different loads with a 3D scanner for dimensional accuracy. Testing monitored using statistical process controls.
9. Supplies price, and maintenance costs recommended by manufacturer. Cost criteria: printing 1.4 full build chambers of parts per day/5 days per week over 1 year of 30 cm3 parts at 10% packing density on Fast print mode using HP 3D High Reusability PA 12 material, and the powder reusability ratio recommended by manufacturer, and printing under certain build conditions and part geometries.
10. Based on internal HP testing, May 2020, with tests for mechanical property retention, dimensional stability, and weight change after 7- and 30-day immersion with acids, bases, organic solvents, and aqueous solutions. Due to the material characteristics, extra tuning is required in part design and printing, compared to other rigid HP 3D Printing materials.
11. Full color parts applicable only with the HP Jet Fusion 580 Color 3D Printer
12. HP Jet Fusion 3D Printing Solutions using HP 3D High Reusability TPA enabled by Evonik provide up to 80% powder reusability ratio, producing functional parts batch after batch. For testing, material is aged in real printing conditions and powder is tracked by generations (worst case for reusability). Parts are then made from each generation and tested for mechanical properties and accuracy.
13. Based on published specifications as of September 2020. HP Jet Fusion 3D Printing Solutions using HP 3D High Reusability TPA enabled by Evonik provide up to 17% lower printed part weight when compared to common powder-based thermoplastic elastomers printed under similar conditions.
14. Image courtesy of OT4
15. Image courtesy of Bowman
16. Image courtesy of Invent Medical
17. Image courtesy of Skorpion Engineering
18. Image courtesy of Extol
19. Image courtesy of Oechsler AG
20. Image courtesy of ETSEIB Motorsport
21. Image courtesy of Rady Children´s Hospital
22. Image courtesy of Addit-ion
23. Image courtesy of Satair
24. Image courtesy of Vestas
25. Image courtesy of Kupol
26. Image courtesy of BASF
27. Image courtesy of Cuni Code
28. Image courtesy of GoProto Inc. Printed with HP 3D High Reusability TPA enabled by Evonik. Post-processed with AMT PostPro chemical vapor smoothing.
29. Data courtesy of HP- Lubrizol
30. Data courtesy of GoProto Inc., Volkswagen & GKN, Heygears, Custom Color, Vital, Addit.ion, Invent Medical, Nacar and Cupra.
A complete guide to 3D printing materials
Whatever you're making with 3D printing, one of the most important questions you'll have to ask yourself as early on as possible, is what material you intend to use. Or you may already have a part in mind with specific specs, mechanical and dimensional requirements, and you are investigating what 3D printing materials would be most suitable. 3D printing allows for a wide range of materials to be used, each of these with subtly different characteristics and capabilities. It's likely that you already know what type of material you would like to print, but it's still helpful to know everything that's available to you. So, let's take a look at the materials available for additive manufacturing.
What are the most common additive manufacturing materials?
In this article, we’ll be covering 3 key categories of material that can be used with 3D printing and additive manufacturing technologies:
- Plastics / Polymers
- Metals
- Ceramics
The type of material you use will depend on the characteristics you want your finished object to have, but also on the type of 3D printing that is available to you. Some of the processes use high temperatures and pressures, which has to be considered when selecting your material or type of process.
Let’s go into a bit more detail on the three broad categories of 3D printing materials.
Back to menu
Plastic materials for 3D printing
Plastics commonly used in 3D printing include ABS and PC. Structural polymers can also be used, in addition to a number of epoxy-based resins and waxes. Mixing polymer powders together can be used to create a whole host of structural and aesthetic materials. Polymers for 3D printing may include ABS (Acrylonitrile butadiene styrene), Polyamide (Nylon), Nylon 12, PC (polycarbonate), Glass-filled nylon (polyamide reinforced with glass beads), PLA (polylactide), epoxy resin, photopolymer resin, and wax.
Back to menu
What are plastic polymers?
A polymer is a long-chain molecule composed of a large number of repeat units, each with an identical structure. Polymers can be classified in different ways according to their properties. For example, the mechanical properties of polymers, such as tensile strength, toughness, and elasticity, depend on hydrogen bonding and intermolecular forces.
Polymers can be classified by molecular force as thermoplastics, elastomers, or thermosets.
Thermoplastics
Thermoplastics are usually semi-crystalline, meaning they’re a combination of crystalline and amorphous regions. The amorphous structure is directly responsible for the elastic properties, while the crystal structure is directly responsible for the mechanical properties of the thermoplastic materials. Polymers with a low to medium stiffness, elongation, and rigidity are considered thermoplastics. They can be melted, reformed, and reused.
HP Multi Jet Fusion 3D printing technology, for example, uses high-reusability thermoplastic 3D printing materials that have been specifically developed for HP Jet Fusion 3D Printing Solutions.
Elastomers
Elastomers are polymers with a high elastic elongation and a high flexibility against breaking or cracking.
Data courtesy1
Thermosets
Thermosets have a higher resistance to high temperatures than thermoplastics but are more brittle. They can melt and be reshaped once, but the process is irreversible, and they cannot be recycled.
Polymer morphology
Amorphous
Amorphous polymers show a highly disordered polymer chain. As a consequence, they show low shrinkage, have a broad melting point, more elasticity, and present lower resistance to chemicals.
Crystalline
On the contrary, crystalline polymers show a long-range polymer order and chain segments that are considered crystalline. As a consequence, these materials have better mechanical properties, higher shrinkage, and a narrower melting point.
Thermoplastics are usually semi-crystalline – a combination of crystalline and amorphous regions. The amorphous structure is directly responsible for the elastic properties, while the crystal structure is directly responsible for the mechanical properties of the thermoplastic materials.
Back to menu
Metal additive manufacturing (MAM) materials
A number of metal materials can be used in MAM, which includes a range of options suitable for structural and integral component parts. These are mostly in the form of metal powders or wires.
Data courtesy2
Metal materials typically used for 3D printing include:
Stainless steel
The most widely used class of materials known for their corrosion and heat resistance with a good combination of high strength and durability.
Low alloy steel
A widely used class of materials used in applications requiring a balance of hardness with high yield and tensile strengths.
Ni-based superalloys
High tensile materials with excellent durability in a wide range of extreme temperatures requiring excellent corrosion resistance.
Tool steel
Extremely hard class of materials with excellent durability, especially for cutting tool or molding applications.
Cobalt chrome
A biocompatible class of materials exhibiting a good combination of strength, hardness, heat resistance and corrosion resistance.
Copper
High thermal and electrical conductivity material that is easily formed due to its ductility.
Titanium
A lightweight metal with excellent mechanical characteristics. It is strong and highly resistant to heat, oxidation, and acid. Also, it is biocompatible with an excellent strength to weight ratio.
Aluminum
Lightweight, durable, strong, aluminum is also widely used and has good thermal properties.
Back to menu
Ceramic materials for 3D printing
Ceramics are a solid material that comprises inorganic compounds of metal, non-metal, or ionic and covalent bonds. This can cause some confusion as it technically means that many of the 3D printable ceramics sound more like plastics or metals. For example, carbon fiber and silicon are technically ceramics.
Ceramics for 3D printing can be divided into two categories:
Technical ceramics
Most 3D printed ceramics fall into this category as they are regularly created as custom solutions for specific applications. Some well-known technical ceramics are Aluminum Nitride, Zirconia, Silicon Nitride, Silicon Carbide, and Alumina.
Classic ceramics
Made up of natural raw materials, like clay, and include silicon, carbon, and nitrogen. Classic ceramics include stoneware, earthenware, and porcelain.
Back to menu
Want to continue learning?
Footnotes and disclaimers
- Data courtesy of BASF
- Data courtesy of Schneider Electric
Overview of 3D printing materials
What to print: 3D printing materials
17 basic materials used for 3D printing
FDM 3D printers can now be found everywhere - in workshops, apartments, offices, school classrooms and institute auditoriums .
PLA and ABS thermoplastics have actually become the most used materials for 3D printing. But, did you know that there are many unusual materials for 3D printing? Now you can print with wood, metal, carbon fiber and many other materials.
As the name implies, exotic filaments contain special or composite (a mixture of common and special) materials for 3D printing, and are considered the most advanced. They combine plastics such as PLA or ABS with substances such as metals, carbon fibers, wood or phosphorescent dye to produce a material with unique properties.
With such a rich assortment, you can easily create a functional, beautiful, unusual and high-quality thing with the necessary properties. Read our guide to choose exactly the filament - regular or not - that is exactly what you need.
1. ABS
Acrylonitrile butadiene styrene (ABS) used to be the most popular 3D material. This cheap, strong, slightly flexible, lightweight and easily extrudable material is ideal for 3D printing. It's the same plastic that LEGO and bike helmets are made from.
But, unfortunately, ABS has several significant drawbacks, so it fell out of favor. First, it requires a higher temperature, reaching its melting point at 210°C to 250°C.
In addition, its use requires the 3D printer to have a heated platform in order to prevent plastic deformation during cooling.
Another disadvantage of this material is the intense fumes that occur during printing and can be dangerous to people and animals who have difficulty breathing. The 3D printer should be placed in a well-ventilated area, it is harmful to inhale ABS.
High strength, durability, impact resistance
Ideal for moving parts, automotive parts, electronics and toy cases
Flexibility is low, bending strength is low
Soluble in acetone
Must not come into contact with food
General print temperature range is 210°C - 250°C cooling, controlled cooling rate recommended
Heated bed recommended 50°C - 100°C
Moderate printing difficulty, requires fine tuning of nozzle and bed temperatures
2. PLA
Polylactic acid (PLA) polymer has overtaken ABS in popularity and has become the choice of many 3D enthusiasts. It is a biodegradable thermoplastic made from renewable resources. PLA materials are much more environmentally friendly than other plastics.
Another interesting feature of PLA is that it does not emit a strong toxic odor when printed and is much safer for indoor use. Plus, the plastic doesn't shrink as much as it cools, so a heated platform isn't necessary (although it's always welcome).
PLA is harder than ABS, making printed objects slightly more brittle, melting between 180°C and 230°C. between coats
More brittle than ABS
Insoluble
Consult manufacturer for food acceptability
General print temperature range 180°C - 230°C
Low shrinkage on cooling, less warp than ABS
Heated bed optional
Difficulty printing - easy
flexibility that surpasses even ABS. In addition, the print setup is as easy as PLA, there is no smell in the workshop, and polyethylene waste is recyclable.
A good use for PET is phone cases and other products that require flexibility and impact strength or toughness. Polyethylene is used in the manufacture of some body armor, by the way.
Main advantages: high strength, stiff, light and impact resistant
Ideal for mechanical parts: impact resistance, flexibility, durability
Abrasion resistant
Good flexibility: more flexible than PLA or ABS
Insoluble
Contact us for food acceptability manufacturer
General printing temperature range is 220°C - 250°C
Low shrinkage on cooling
Heated bed optional
Moderate printing difficulty, requires fine nozzle temperature adjustment
4. PETT
Polyethylene Co-Trimethylene Terephthalate (PETT) , is a cousin of PET copolymer, sometimes found under the name T-Glase. It is a strong and rigid material whose main characteristics are incredible hardness, transparency and biocompatibility. It has also been approved by the US Food and Drug Administration for use in food containers.
Main advantages: transparent, rigid, light and impact resistant
Ideal for mechanical parts: impact resistance, flexibility, durability
High wear resistance
Good flexibility, more flexible than PLA or ABS
Insoluble
Contact manufacturer
General print temperature range 210°C - 230°C
Low shrinkage on cooling
No heated bed required
Moderate Print Difficulty
5.
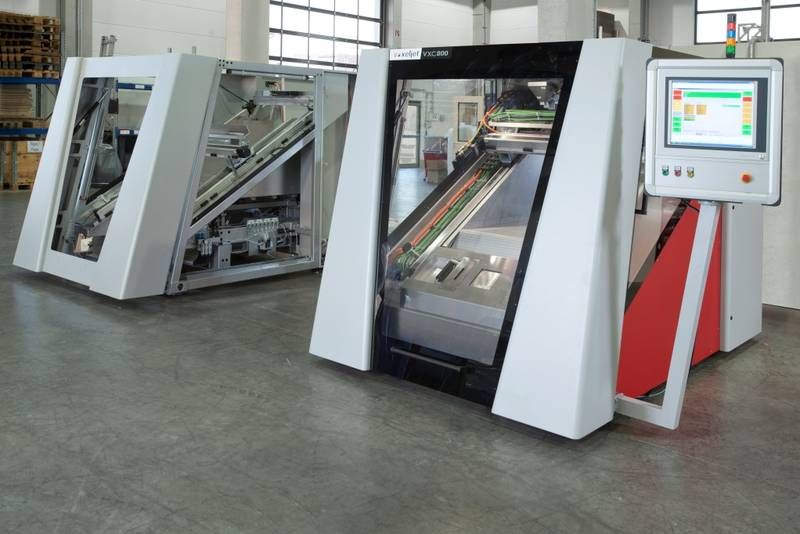
High Impact Polystyrene (HIPS): A material widely used in the food industry for packaging. HIPS filament is biodegradable and bright white, no harmful effects in close contact with people or pets.
The usual use of HIPS in 3D printing is not for making the object itself; the material has curling and adhesion issues, especially if you don't have a heated deck.
Instead, it is very popular for use as a recycled material in dual extrusion, providing structural support for a complex object whose base is printed using a different material.
After printing is complete, HIPS can be dissolved using a colorless liquid hydrocarbon. Acetone, for example. It disappears like magic!
Main application: support structures, e.g. paired with ABS
High strength
Low flexibility, negligible bending strength
Soluble in various solvents
Not considered safe for food contact
General print temperature range: 210°C - 250°C
Cooling shrinkage, controlled cooling rate recommended
Heat platform 50°C - 100 ° C
Moderate complexity, requires fine tuning
6.
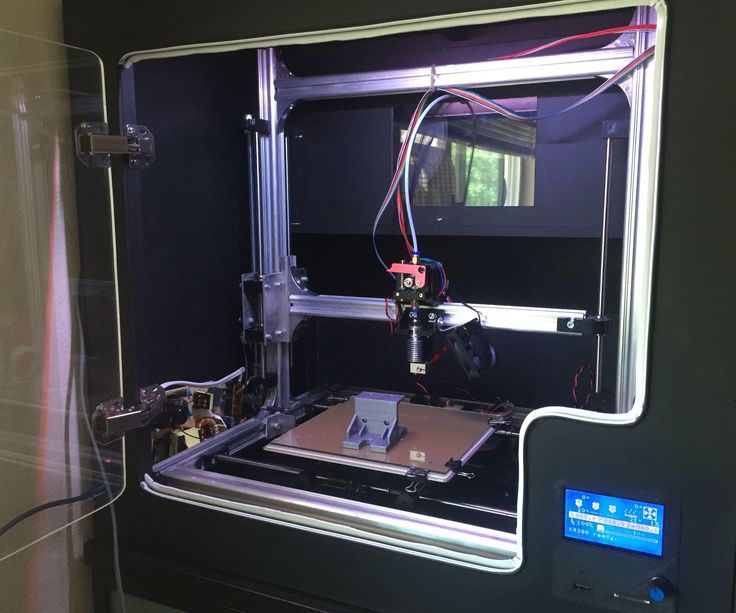
Polyvinyl alcohol (PVA) is typically used as a support when printing complex objects that cannot otherwise be printed. Like HIPS, PVA is an excellent material for dual filament printing.
Based on polyvinyl alcohol, this material is non-toxic and biodegradable and can be dissolved in water.
It can be used on all common desktop FDM 3D printers, but requires a heated bed. It is important to note that you should not exceed the printing temperature.
Primary use: support structures, e.g. paired with PLA
Good strength
Low flexibility
Soluble in water
Contact manufacturer for food compatibility
General printing temperature range is 180°C - 230°C
Some shrinkage during cooling
No heated bed required
Printing difficulty low
used in many industrial applications. It is a cost-effective plastic that is strong, lightweight, flexible and resistant to wear. Significantly less brittle than PLA or ABS.

Nylon can be used to make a variety of products: machine parts, containers, tools, consumer goods and toys. By the way: it can be dyed with fabric dye.
Key benefits: high strength, durability and flexibility
Ideal for mechanical components, structural parts, gears and bearings, withstands dynamic loads
High strength
High flexibility
Insoluble
Consult manufacturer for food compatibility
General printing temperature range is 220°C - 260°C
Some shrinkage during cooling
Platform heating to 50°C - 100°C recommended
Printing difficulty is moderate
8. Wood
create objects with the tactile feel of wood. There are many wood filaments on the market today, each with its own mixture of plastic and wood fibers. But keep in mind, they have drawbacks in terms of flexibility and strength.
Key Benefits: Look and feel
Ideal for home decor
Durability dependent on print geometry
Good flexibility
Insoluble
Should not come into contact with food
General print temperature range 195°C - 220°C
Some shrinkage during cooling
No heating required
Moderate print difficulty
9.
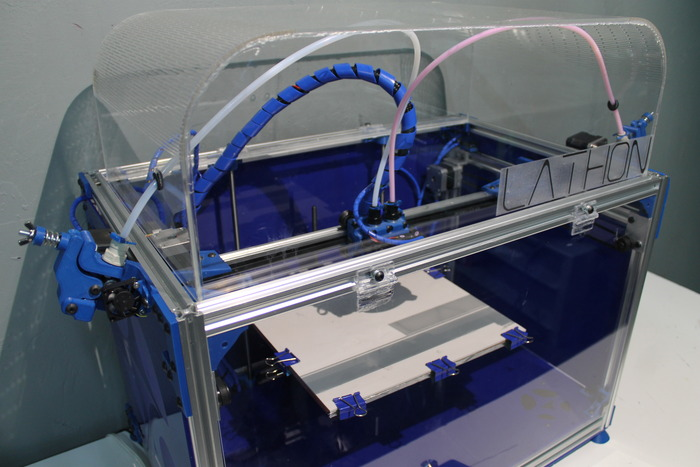
If you are working on architecture or landscaping, this is a good option. Filament Sandstone contains chalk powder with PLA to reproduce the color and texture of the stone. By changing the extrusion temperature during 3D printing, it is able to create a smooth or rough surface.
Key benefits: appearance
Ideal for building layouts and landscaping
Low strength, no flexibility, crumble
Insoluble
Must not come into contact with food
General print temperature range: 165°C - 210°C
No shrinkage during cooling time
No platform heating required
Printing difficulty moderate
10. Metal+PLA
It's basically PLA mixed with metal powder. Metal+PLA 3D printed objects will look and feel as if they were made from bronze, brass, or copper, and can be polished and artificially aged like those metals. This material is several times denser than standard PLA, so it feels more like metal than plastic.
Unique appearance
Ideal for jewelry, statues, home equipment, artifact replicas
High strength
Low flexibility, depends on design
Insoluble
Food grade
Printing temperature range: 195°C - 220°C
Shrinks little when cooled
No platform heating required
Printing complexity is high, fine adjustment of extruder nozzle temperature is required
11. Magnetic PLA
Is metal 3D printing too boring for you? Okay, then what about magnetic metal? PLA with iron powder for a grainy finish and magnetic metal properties. The bonus is that you can make this PLA stick to magnets, a mechanical property that could come in handy for your next project.
Main advantages: magnetic properties
Ideal for decorating the refrigerator and creating moving parts
High strength
Low flexibility, depends on design
Not soluble
Should not come into contact with food
Printing temperature range is 195°C - 220°C
Shrinks slightly when cooled
No bed heating required
High printing complexity, exact exit temperature required
12.
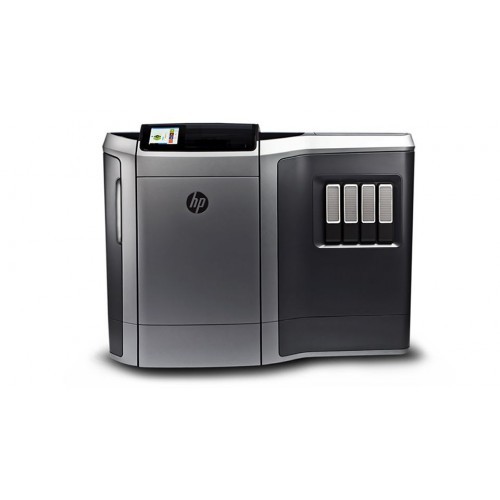
Conductive filament opens up a whole new realm of engineering possibilities for your next 3D printing project. From a material with the addition of conductive carbon particles, you can print 3D electronic circuits for simple elements such as LEDs and sensors.
Pair this filament with standard PLA and you can make a PCB directly on your 3D printer platform.
Low voltage electronics printing
Ideal for LEDs, sensors, circuits and low voltage Arduino projects
Low strength
May break from repeated bending
Insoluble
Should not come into contact with food
Printing temperature range is 215°C - 230°C
Low shrinkage
Platform heating not required
Print complexity is low, very similar to standard PLA
13. Heat sensitive PLA
Remember those T-shirts from the eighties that change color with body temperature? It's the same concept. The thermosensitive filament will change color depending on the change in temperature. There are several color combinations available, from different manufacturers, each with several different properties. Some of them also react to light!
Changes color at certain temperatures
Ideal for toys, souvenirs, artwork
Good durability
Medium flexibility
Insoluble
Food-safe
General print temperature 215°C
Low shrinkage on cooling
No heated bed required
Printing Difficulty: Easy, very similar to standard PLA
14. Carbon PLA
PLA with a small amount of carbon fiber gives incredible rigidity, structure and great layer adhesion. But these additional advantages are offset by disadvantages: this filament is abrasive and increases extruder wear by several times. After printing with only 500 grams of such a filament, for example, an increase in the diameter of the brass nozzle will be noticeable.
Ideally, the printer nozzle should be coated with tungsten carbide. Otherwise, be prepared to replace nozzles after extended use!
High structural strength, layer adhesion and stiffness
Ideal for mechanical parts, containments and housings
High strength
Low flexibility, brittle
Insoluble
Never use this filament with food.
Printing temperature range 195°C - 220°C
Very little shrinkage during cooling
No heated bed required
Moderate print difficulty, high extruder wear.
15. Flexible TPE
Thermoplastic elastomer will help make objects that stretch well, ABS or PLA would not survive under such loads. It is difficult to work with - the material tends to fly out of the extruder in all directions except the nozzle!
Extremely flexible
Ideal for toys, souvenirs, unusual items
High strength
High flexibility
Insoluble
Should not come into contact with food
Printing temperature is 225°C - 235°C
Low shrinkage on cooling
No heated bed required
High printing complexity, fine temperature and feed rate adjustment required
16.
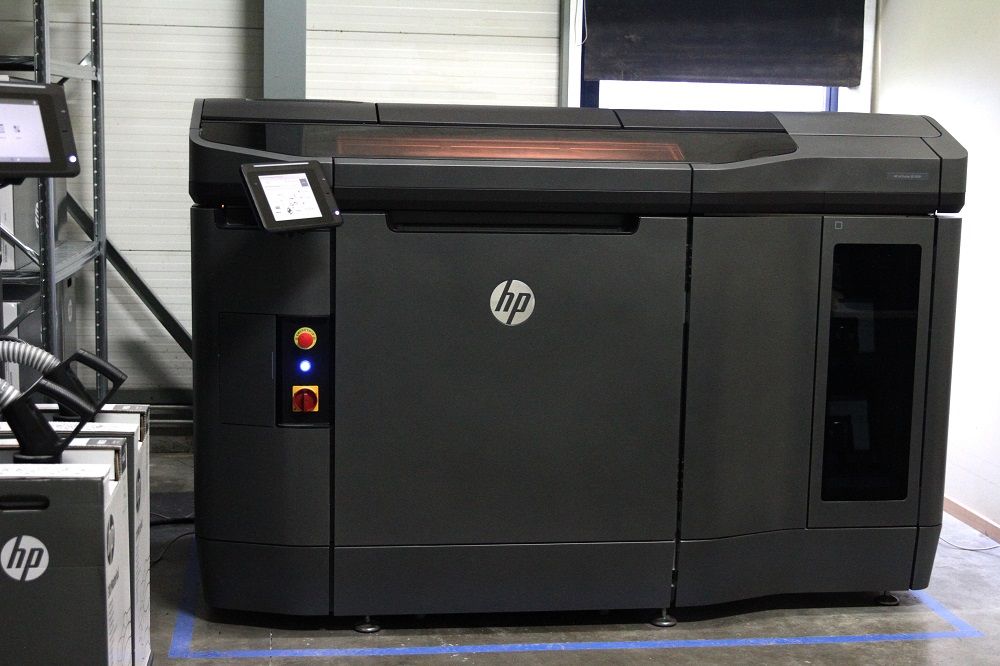
The characteristics are quite obvious: it accumulates light and glows in the dark. A good choice for Halloween projects or for extra functionality in low light conditions.
Glow in the dark.
Ideal for toys, souvenirs, etc.
Good strength
Medium flexibility
Insoluble
Should not come into contact with food
General print temperature is 215°C
Low shrinkage on cooling
No heated bed required
Easy to print, very similar to standard PLA
17. Amphora
9003Amphora is Eastman Chemical Company's next generation filament, chemically formulated as Copolyester. This is a brand new polymer specifically designed for 3D printing unlike any other thermoplastic. The difference is not great, but significant. Key Benefits: Virtually odorless during printing, durable, higher melting point than PLA, and better adhesion for improved surface finish. It is also approved by the US FDA for food contact.
Currently sold as "NGEN" by ColorFabb and "N-Vent" by Taulamn. It is new to the market, but the first impression is very positive.
Main advantages: high strength, rigid, light, flexible and impact resistant
High strength
Good flexibility, more flexible than PLA or ABS
Insoluble
Printing temperature range is 220°C - 250°C
Low shrinkage on cooling
Heated bed not required
Printing difficulty is moderate, requires temperature fine tuning
Source: Ink-Market.ru.
HP started shipping Jet Fusion 3D 4200 Printer 3D printers « 3D « Knowledge base MnogoChernil.ru
HP started shipping its Jet Fusion 3D 4200 Printer 3D printers to customers. The first to receive the devices are the company's partners who supported the development of the novelty - Jabil, Materialise and Shapeways.
Jet Fusion 4200 operates on the basis of “HP Multi Jet Fusion technology”, which is a modified SLS (Selective Laser Sintering): layers of special powder are poured layer by layer, the desired areas of the layer are selectively sintered under special lighting. Powder from unused areas can sometimes be reused. HP claims that its devices are more reliable, print faster (advantage up to x10) and better, and the infrastructure being created in the form of professional software and the market for materials will make their use as convenient as possible.
The printing process is as follows: the model file and powder are loaded into the Processing Station, which prepares the printing process in the ”Build Unit”. Next, the Build Unit is removed from the station and installed in the printer itself, and printing starts.
Main specifications of the Jet Fusion 3D 4200 Printer (without Processing Station):
- Maximum part size: 406 x 305x 406 mm
- Layer height: 0.07 to 0.12 mm
- Unit size: 2178 x 1238 x 1448 mm @ 730 kg (unpackaged)
- Features: 380 volt power supply, 2 terabyte HDD, Ethernet interface
Processing Station weighs from 450 kg and measures from 1926 x 1245 x 2400 mm to 3121 x 1571 x 2400 mm (with rapid cooling system installed).
Read more about HP Jet Fusion 3D printers here.
The Jet Fusion 4200 is currently printing with HP's proprietary 3D High Reusability PA12 resin (with the ability to reuse “excess” powder). The device will also support materials from alternative manufacturers (the concept of Open Platform). For example, Evonik recently announced the release of its plastic. Printing materials will also be supplied by BASF, Arkema and Lehmann and Voss.
Ramon Pastor, Vice President of HP, commented: “6 months ago we released information about our Jet Fusion 3D and a list of forward-thinking companies looking to join HP on the industrial revolution. We hope that this cooperation will lead to a joint development, as a result of which we will achieve unparalleled quality and print economy.”
Also soon, HP plans to release a more budget solution with speed and layer height limitation HP Jet Fusion 3D 3200 with a price of 130 thousand dollars. With Processing Station - $155,000.