What is used in 3d printing
Guide to 3D Printing Materials: Types, Applications, and Properties
3D printing empowers you to prototype and manufacture parts for a wide range of applications quickly and cost-effectively. But choosing the right 3D printing process is just one side of the coin. Ultimately, it'll be largely up to the materials to enable you to create parts with the desired mechanical properties, functional characteristics, or looks.
This comprehensive guide to 3D printing materials showcases the most popular plastic and metal 3D printing materials available, compares their properties, applications, and describes a framework that you can use to choose the right one for your project.
Interactive
Need some help figuring out which 3D printing material you should choose? Our new interactive material wizard helps you make the right material decisions based on your application and the properties you care the most about from our growing library of resins.
Recommend Me a Material
There are dozens of plastic materials available for 3D printing, each with its unique qualities that make it best suited to specific use cases. To simplify the process of finding the material best suited for a given part or product, let’s first look at the main types of plastics and the different 3D printing processes.
There are the two main types of plastics:
-
Thermoplastics are the most commonly used type of plastic. The main feature that sets them apart from thermosets is their ability to go through numerous melt and solidification cycles. Thermoplastics can be heated and formed into the desired shape. The process is reversible, as no chemical bonding takes place, which makes recycling or melting and reusing thermoplastics feasible. A common analogy for thermoplastics is butter, which can be melted, re-solidify, and melted again. With each melting cycle, the properties change slightly.
-
Thermosetting plastics (also referred to as thermosets) remain in a permanent solid state after curing. Polymers in thermosetting materials cross-link during a curing process that is induced by heat, light, or suitable radiation. Thermosetting plastics decompose when heated rather than melting, and will not reform upon cooling. Recycling thermosets or returning the material back into its base ingredients is not possible. A thermosetting material is like cake batter, once baked into a cake, it cannot be melted back into batter again.
The three most established plastic 3D printing processes today are the following:
-
Fused deposition modeling (FDM) 3D printers melt and extrude thermoplastic filaments, which a printer nozzle deposits layer by layer in the build area.
-
Stereolithography (SLA) 3D printers use a laser to cure thermosetting liquid resins into hardened plastic in a process called photopolymerization.
-
Selective laser sintering (SLS) 3D printers use a high-powered laser to fuse small particles of thermoplastic powder.
Video Guide
Having trouble finding the best 3D printing technology for your needs? In this video guide, we compare FDM, SLA, and SLS technologies across popular buying considerations.
Watch the Videos
Fused deposition modeling (FDM), also known as fused filament fabrication (FFF), is the most widely used form of 3D printing at the consumer level, fueled by the emergence of hobbyist 3D printers.
This technique is well-suited for basic proof-of-concept models, as well as quick and low-cost prototyping of simple parts, such as parts that might typically be machined.
Consumer level FDM has the lowest resolution and accuracy when compared to other plastic 3D printing processes and is not the best option for printing complex designs or parts with intricate features. Higher-quality finishes may be obtained through chemical and mechanical polishing processes. Industrial FDM 3D printers use soluble supports to mitigate some of these issues and offer a wider range of engineering thermoplastics or even composites, but they also come at a steep price.
As the melted filament forms each layer, sometimes voids can remain between layers when they don’t adhere fully. This results in anisotropic parts, which is important to consider when you are designing parts meant to bear load or resist pulling.
FDM 3D printing materials are available in a variety of color options. Various experimental plastic filament blends also exist to create parts with wood- or metal-like surfaces.
The most common FDM 3D printing materials are ABS, PLA, and their various blends. More advanced FDM printers can also print with other specialized materials that offer properties like higher heat resistance, impact resistance, chemical resistance, and rigidity.
Material | Features | Applications |
---|---|---|
ABS (acrylonitrile butadiene styrene) | Tough and durable Heat and impact resistant Requires a heated bed to print Requires ventilation | Functional prototypes |
PLA (polylactic acid) | The easiest FDM materials to print Rigid, strong, but brittle Less resistant to heat and chemicals Biodegradable Odorless | Concept models Looks-like prototypes |
PETG (polyethylene terephthalate glycol) | Compatible with lower printing temperatures for faster production Humidity and chemical resistant High transparency Can be food safe | Waterproof applications Snap-fit components |
Nylon | Strong, durable, and lightweight Tough and partially flexible Heat and impact resistant Very complex to print on FDM | Functional prototypes Wear resistant parts |
TPU (thermoplastic polyurethane) | Flexible and stretchable Impact resistant Excellent vibration dampening | Flexible prototypes |
PVA (polyvinyl alcohol) | Soluble support material Dissolves in water | Support material |
HIPS (high impact polystyrene) | Soluble support material most commonly used with ABS Dissolves in chemical limonene | Support material |
Composites (carbon fiber, kevlar, fiberglass) | Rigid, strong, or extremely tough Compatibility limited to some expensive industrial FDM 3D printers | Functional prototypes Jigs, fixtures, and tooling |
Stereolithography was the world’s first 3D printing technology, invented in the 1980s, and is still one of the most popular technologies for professionals.
SLA parts have the highest resolution and accuracy, the clearest details, and the smoothest surface finish of all plastic 3D printing technologies. Resin 3D printing is a great option for highly detailed prototypes requiring tight tolerances and smooth surfaces, such as molds, patterns, and functional parts. SLA parts can also be highly polished and/or painted after printing, resulting in client-ready parts with high-detailed finishes.
Parts printed using SLA 3D printing are generally isotropic—their strength is more or less consistent regardless of orientation because chemical bonds happen between each layer. This results in parts with predictable mechanical performance critical for applications like jigs and fixtures, end-use parts, and functional prototyping.
SLA offers the widest range of material options for plastic 3D printing.
SLA 3D printing is highly versatile, offering resin formulations with a wide range of optical, mechanical, and thermal properties to match those of standard, engineering, and industrial thermoplastics.
Formlabs Materials | Features | Applications |
---|---|---|
Standard Resins | High resolution Smooth, matte surface finish | Concept models Looks-like prototypes |
Clear Resin | The only truly clear material for plastic 3D printing Polishes to near optical transparency | Parts requiring optical transparency Millifluidics |
Draft Resin | One of the fastest materials for 3D printing 4x faster than standard resins, up to 10x faster than FDM | Initial Prototypes Rapid Iterations |
Tough and Durable Resins | Strong, robust, functional, and dynamic materials Can handle compression, stretching, bending, and impacts without breaking Various materials with properties similar to ABS or PE | Housings and enclosures Jigs and fixtures Connectors Wear-and-tear prototypes |
Rigid Resins | Highly filled, strong and stiff materials that resist bending Thermally and chemically resistant Dimensionally stable under load | Jigs, fixtures, and tooling Turbines and fan blades Fluid and airflow components Electrical casings and automotive housings |
Polyurethane Resins | Excellent long-term durability UV, temperature, and humidity stable Flame retardancy, sterilizability, and chemical and abrasion resistance | High performance automotive, aerospace, and machinery components Robust and rugged end-use parts Tough, longer-lasting functional prototypes |
High Temp Resin | High temperature resistance High precision | Hot air, gas, and fluid flow Heat resistant mounts, housings, and fixtures Molds and inserts |
Flexible and Elastic Resins | Flexibility of rubber, TPU, or silicone Can withstand bending, flexing, and compression Holds up to repeated cycles without tearing | Consumer goods prototyping Compliant features for robotics Medical devices and anatomical models Special effects props and models |
Medical and dental resins | A wide range of biocompatible resins for producing medical and dental appliances | Dental and medical appliances, including surgical guides, dentures, and prosthetics |
Jewelry resins | Materials for investment casting and vulcanized rubber molding Easy to cast, with intricate details and strong shape retention | Try-on pieces Masters for reusable molds Custom jewelry |
ESD Resin | ESD-safe material to improve electronics manufacturing workflows | Tooling & fixturing for electronics manufacturing Anti-static prototypes and end-use components Custom trays for component handling and storage |
Ceramic Resin | Stone-like finish Can be fired to create a fully ceramic piece | Engineering research Art and design pieces |
Explore Formlabs SLA Materials
Sample part
See and feel Formlabs quality firsthand. We’ll ship a free sample part to your office.
Request a Free Sample Part
Selective laser sintering (SLS) 3D printing is trusted by engineers and manufacturers across different industries for its ability to produce strong, functional parts. Low cost per part, high productivity, and established materials make the technology ideal for a range of applications from rapid prototyping to small-batch, bridge, or custom manufacturing.
As the unfused powder supports the part during printing, there’s no need for dedicated support structures. This makes SLS ideal for complex geometries, including interior features, undercuts, thin walls, and negative features.
Just like SLA, SLS parts are also generally more isotropic than FDM parts. SLS parts have a slightly rough surface finish due to the powder particles, but almost no visible layer lines.
SLS 3D printing materials are ideal for a range of functional applications, from engineering consumer products to manufacturing and healthcare.
The material selection for SLS is limited compared to FDM and SLA, but the available materials have excellent mechanical characteristics, with strength resembling injection-molded parts. The most common material for selective laser sintering is nylon, a popular engineering thermoplastic with excellent mechanical properties. Nylon is lightweight, strong, and flexible, as well as stable against impact, chemicals, heat, UV light, water, and dirt.
Material | Description | Applications |
---|---|---|
Nylon 12 | Strong, stiff, sturdy, and durable Impact-resistant and can endure repeated wear and tear Resistant to UV, light, heat, moisture, solvents, temperature, and water | Functional prototyping End-use parts Medical devices |
Nylon 11 | Similar properties to Nylon 12, but with a higher elasticity, elongation at break, and impact resistance, but lower stiffness | Functional prototyping End-use parts Medical devices |
TPU | Flexible, elastic, and rubbery Resilient to deformation High UV stability Great shock absorption | Functional prototyping Flexible, rubber-like end-use parts Medical devices |
Nylon composites | Nylon materials reinforced with glass, aluminum, or carbon fiber for added strength and rigidity | Functional prototyping Structural end-use parts |
Explore Formlabs SLS Materials
Sample part
See and feel Formlabs SLS quality firsthand. We’ll ship a free sample part to your office.
Request a Free Sample Part
Different 3D printing materials and processes have their own strengths and weaknesses that define their suitability for different applications. The following table provides a high level summary of some key characteristics and considerations.
FDM | SLA | SLS | |
---|---|---|---|
Pros | Low-cost consumer machines and materials available | Great value High accuracy Smooth surface finish Range of functional materials | Strong functional parts Design freedom No need for support structures |
Cons | Low accuracy Low details Limited design compatibility High cost industrial machines if accuracy and high performance materials are needed | Sensitive to long exposure to UV light | More expensive hardware Limited material options |
Applications | Low-cost rapid prototyping Basic proof-of-concept models Select end-use parts with high-end industrial machines and materials | Functional prototyping Patterns, molds, and tooling Dental applications Jewelry prototyping and casting Models and props | Functional prototyping Short-run, bridge, or custom manufacturing |
Materials | Standard thermoplastics, such as ABS, PLA, and their various blends on consumer level machines.![]() | Varieties of resin (thermosetting plastics). Standard, engineering (ABS-like, PP-like, flexible, heat-resistant), castable, dental, and medical (biocompatible). | Engineering thermoplastics. Nylon 11, Nylon 12, and their composites, thermoplastic elastomers such as TPU. |
Beyond plastics, there are multiple 3D printing processes available for metal 3D printing.
-
Metal FDM
Metal FDM printers work similarly to traditional FDM printers, but use extrude metal rods held together by polymer binders. The finished “green” parts are then sintered in a furnace to remove the binder.
SLM and DMLS printers work similarly to SLS printers, but instead of fusing polymer powders, they fuse metal powder particles together layer by layer using a laser. SLM and DMLS 3D printers can create strong, accurate, and complex metal products, making this process ideal for aerospace, automotive, and medical applications.
-
Titanium is lightweight and has excellent mechanical characteristics. It is strong, hard and highly resistant to heat, oxidation, and acid.
-
Stainless steel has high strength, high ductility, and is resistant to corrosion.
-
Aluminum is a lightweight, durable, strong, and has good thermal properties.
-
Tool steel is a hard, scratch-resistant material that you can use to print end-use tools and other high-strength parts..
- Nickel alloys have high tensile, creep and rupture strength and are heat and corrosion resistant.
Compared to plastic 3D printing technologies, metal 3D printing is substantially more costly and complex, limiting its accessibility to most businesses.
Alternatively, SLA 3D printing is well-suited for casting workflows that produce metal parts at a lower cost, with greater design freedom, and in less time than traditional methods.
Another alternative is electroplating SLA parts, which involves coating a plastic material in a layer of metal via electrolysis. This combines some of the best qualities of metal—strength, electrical conductivity, and resistance to corrosion and abrasion—with the specific properties of the primary (usually plastic) material.
Plastic 3D printing is well-suited to create patterns that can be cast to produce metal parts.
With all these materials and 3D printing options available, how can you make the right selection?
Here’s our three-step framework to choose the right 3D printing material for your application.
Plastics used for 3D printing have different chemical, optical, mechanical, and thermal characteristics that determine how the 3D printed parts will perform. As the intended use approaches real-world usage, performance requirements increase accordingly.
Requirement | Description | Recommendation |
---|---|---|
Low performance | For form and fit prototyping, conceptual modeling, and research and development, printed parts only need to meet low technical performance requirements.![]() Example: A form prototype of a soup ladle for ergonomic testing. No functional performance requirements needed besides surface finish. | FDM: PLA SLA: Standard Resins, Clear Resin (transparent part), Draft Resin (fast printing) |
Moderate performance | For validation or pre-production uses, printed parts must behave as closely to final production parts as possible for functional testing but do not have strict lifetime requirements. Example: A housing for electronic components to protect against sudden impact. Performance requirements include ability to absorb impact, housing needs to snap together and hold its shape. | FDM: ABS SLA: Engineering Resins SLS: Nylon 11, Nylon 12, TPU |
High performance | For end-use parts, final 3D printed production parts must stand up to significant wear for a specific time period, whether that’s one day, one week, or several years. Example: Shoe outsoles. | FDM: Composites SLA: Engineering, Medical, Dental, or Jewelry Resins SLS: Nylon 11, Nylon 12, TPU, nylon composites |
Once you’ve identified the performance requirements for your product, the next step is translating them into material requirements—the properties of a material that will satisfy those performance needs. You’ll typically find these metrics on a material’s data sheet.
Requirement | Description | Recommendation |
---|---|---|
Tensile strength | Resistance of a material to breaking under tension. High tensile strength is important for structural, load bearing, mechanical, or statical parts. | FDM: PLA SLA: Clear Resin, Rigid Resins SLS: Nylon 12, nylon composites |
Flexural modulus | Resistance of a material to bending under load.![]() | FDM: PLA (high), ABS (medium) SLA: Rigid Resins (high), Tough and Durable Resins (medium), Flexible and Elastic Resins (low) SLS: nylon composites (high), Nylon 12 (medium) |
Elongation | Resistance of a material to breaking when stretched. Helps you compare flexible materials based on how much they can stretch. Also indicates if a material will deform first, or break suddenly. | FDM: ABS (medium), TPU (high) SLA: Tough and Durable Resins (medium), Polyurethane Resins (medium), Flexible and Elastic Resins (high) SLS: Nylon 12 (medium), Nylon 11 (medium), TPU (high) |
Impact strength | Ability of a material to absorb shock and impact energy without breaking. Indicates toughness and durability, helps you figure out how easily a material will break when dropped on the ground or crashed into another object.![]() | FDM: ABS, Nylon SLA: Tough 2000 Resin, Tough 1500 Resin, Grey Pro Resin, Durable Resin, Polyurethane Resins SLS: Nylon 12, Nylon 11, nylon composites |
Heat deflection temperature | Temperature at which a sample deforms under a specified load. Indicates if a material is suitable for high temperature applications. | SLA: High Temp Resin, Rigid Resins SLS: Nylon 12, Nylon 11, nylon composites |
Hardness (durometer) | Resistance of a material to surface deformation. Helps you identify the right “softness” for soft plastics, like rubber and elastomers for certain applications. | FDM: TPU SLA: Flexible Resin, Elastic Resin SLS: TPU |
Tear strength | Resistance of a material to growth of cuts under tension. Important to assess the durability and the resistance to tearing of soft plastics and flexible materials, such as rubber. | FDM: TPU SLA: Flexible Resin, Elastic Resin, Durable Resin SLS: Nylon 11, TPU |
Creep | Creep is the tendency of a material to deform permanently under the influence of constant stress: tensile, compressive, shear, or flexural.![]() | FDM: ABS SLA: Polyurethane Resins, Rigid Resins SLS: Nylon 12, Nylon 11, nylon composites |
Compression set | Permanent deformation after material has been compressed. Important for soft plastics and elastic applications, tells you if a material will return to its original shape after the load is removed. | FDM: TPU SLA: Flexible Resin, Elastic Resin SLS: TPU |
For even more details on material properties, read our guide to about the most common mechanical and thermal properties.
Once you translate performance requirements to material requirements, you’ll most likely end up with a single material or a smaller group of materials that could be suitable for your application.
If there are multiple materials that fulfil your basic requirements, you can then look at a wider range of desired characteristics and consider the pros, cons, and trade-offs of the given materials and processes to make the final choice.
Try our interactive material wizard to find materials based on your application and the properties you care the most about from our growing library of materials. Do you have specific questions about 3D printing materials? Contact our experts.
Recommend Me a Material
What Materials Are Used in 3D Printing?
Published Date
Author Jeff Yoders- Plastic is still the most popular material used for 3D printing.
- As the 3D-printing market value increases, the list of what materials can be used also grows.
- Raw materials such as metal, graphite, and carbon fiber are commonly used for 3D printing, though at-home use is mostly limited to PLA for now.
Ice cream. Molecules for medicine. Even human skin. The list of what materials are used in 3D printing grows longer—and much more interesting—by the day. And expanding it is a multibillion-dollar material arms race right now.
A recently released 3D-printing market study found that the worldwide market for 3D-printing products was valued at $12.6 billion in 2020 and was expected to grow to $37.2 billion by 2036. That means a huge increase in the materials those machines use.
What Is The Most Common Material Used for 3D Printing?
Plastic still reigns supreme in the 3D printing. According to a Grand View Research report, the market size for 3D printing plastics globally was valued at $638.7 million in 2020 and was expected to grow to $2.83 billion by 2027.
This material isn’t just your “everyday” plastic. Two types of plastic are most commonly used in 3D printing:
- PLA: Poly Lactic Acid (PLA) is the most popular 3D-printing material.
It’s a biodegradable plastic made from renewables such as cornstarch. Its low melting point makes it easy to use at home.
- ABS: Acrylonitrile butadiene styrene (ABS) is best suited for parts that require strength and flexibility, like car components or household appliances. It’s also known for its low cost.
But it doesn’t stop there in the 3D-printing materials world.
3 Other Materials a 3D Printer Can Use1. Metal
Used for: Ready-to-install parts, finished products, prototypes
If there is a runner-up to plastic, it would be metal. Direct metal laser sintering (DMLS) is the technique and, unlike printing plastics, it can be used to make either a finished industrial product or a prototype. The aviation industry is already an early proponent and consumer of DMLS printing to streamline operations and manufacture ready-to-install parts. There are even already mass-market DMLS printers for creating 3D-printed jewelry.
The growth and popularity of 3D printing metals holds the potential to manufacture and create more effective machine parts that currently cannot be mass-produced onsite. This could lead to better conductors, tensile strength, and other attributes of laboratory metals than “mined-and-refined” metals such as steel and copper.
In the aerospace industry, the materials question is largely answered, and creating volume of parts is the Holy Grail. GE Aviation began printing fuel nozzles for its LEAP jet engine in 2016, ramping up to 30,000 parts in less than three years and printing its 100,000th nozzle in 2021. The LEAP’s successor, the RISE, will also incorporate 3D-printed parts.
An illustration of the molecular structure of graphene. Strong and flexible, graphene is used in 3D printing electronics.2. Graphite and GrapheneUsed for: Electronics, lighting
Australian-listed graphite and nickel miner Kibaran Resources has partnered with 3D-printing company 3D Group to share development costs on a research-and-development venture called 3D Graphtech Industries.
The partnership is pursuing patents to investigate 3D printing graphite and graphene, a pure form of carbon first created in a laboratory in 2004. Graphene conducts electricity better and is stronger, easier to insulate, and lighter than other conductors on the market today. It outperforms even the best conductors several times over. Because it must be created in a lab, it is a good case study for just what kind of mass production of metals additive manufacturing can accomplish.
Materials for research and development are sourced from Kibaran’s Tanzanian mines, where graphite with high crystallinity and a purity of 99.9% carbon has been found. This is incredibly well-suited to the production of graphene.
The semiconductor industry is interested in producing large quantities of graphene, as well. For example, IBM found a way to use it for LED lighting in 2014. The ability to 3D print sheets of material for use in LEDs could seriously cut lighting production costs.
3.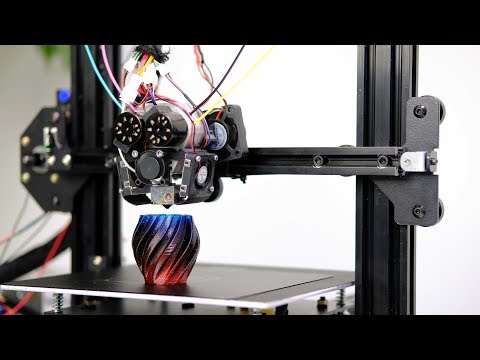
Used for: Bearings, parts, electrical cable installation
Related to graphite, carbon fiber (which undergoes an oxidation process that stretches the polymer) can be added to the more traditional plastic to create a composite that can be as strong as steel but less intensive to use than aluminum, says Markforged. The company’s large-format 3D printers are designed to print stronger parts more quickly and at significantly lower costs.
Meanwhile, startup Impossible Objects has also been exploring carbon fiber, as well as glass, Kevlar, and fiberglass. The company’s printer can also work with PEEK (polyether ether ketone) thermoplastic polymers, which are typically used for bearings, piston parts, and electrical cable installation.
New 3D Printing Materials
The 3D-printing industry is experimenting with a wide variety of innovative, novel approaches such a bio-based resins made from corn and soybean oil, powders, nitinol, and even paper.
As the list of materials grows, what does this mean for the actual hardware? Right now, on the consumer level, plastic is about as good as it gets. For example, the $1,399 Dremel 3D40 Flex is limited to PLA.
Today, several printers are focused entirely on DMLS, including the 3DSystems DMP Flex 350 and several models from Stratasys, but these currently cost upward of $100,000 each because DMLS printers burn much hotter than their plastic counterparts, as the powders and metals they create have higher melting points. Stronger housings and more powerful industrial smelting tools increase their costs significantly.
Although many 3D-printer manufacturers are offering metal 3D-printing services, it will be some time before the economies of scale that helped bring down the cost of plastic 3D printing affect the DMLS market. And 3D-printing systems with graphite/carbon fiber are just now starting to gain traction in the marketplace.
The diversity of applications that industries are exploring for 3D printing makes for an exciting but tumultuous time. From jet parts to lighting to rapid prototyping, the new (and “old”) 3D printing materials will deliver even more opportunities for how and what industries print.
This article has been updated. It was originally published in November 2014.
About the Author
Jeff Yoders has covered IT, CAD, and BIM for Building Design + Construction, Structural Engineer, and CE News magazines. He has won six American Society of Business Publications Editors awards and was part of the reporting team for the 2012 Jesse H. Neal Award for best subject-related series of stories.
Follow on Twitter Content by Jeff Yoders
what a 3D printer can do
3D printing possibilities
Unfortunately, the current level of awareness in 3D technologies leaves much to be desired. It happens that even with a basic knowledge of 3D printers, the actual application of 3D printing remains incomprehensible to a number of users. To avoid such situations, we have prepared this article and will consider in detail all the possibilities of 3D printing.
3D printing application
When it comes to 3D printing applications, it is worth considering not only the existing possibilities, but also the prospects. Already today, the application of 3D printing technology is extremely extensive and does not stop expanding. Of course, in the future we expect a large-scale distribution of additive techniques, but the practical application of 3D printing is available to everyone today. We will not delve into narrowly specific aspects of technology, such as 3D food printing, or bioprinting. Instead, let's talk about how 3D printing technology can be used by ordinary users with desktop 3D printers. nine0005
1. Prototyping
The best way to use 3D printing is for its intended purpose. Rapid prototyping is not only the second name of the technique, but also the original goal of its development. Creating prototypes using 3D printing significantly reduces production time and costs. And thanks to the possibilities of 3D modeling, the range of designed parts is practically unlimited. Prototyping allows you to visually assess the possible shortcomings of the product at the design stage and make significant changes to the design of the part even before its final approval. nine0005
2. Small-scale production
For small-scale production, 3D printing is a godsend. The properties of many materials allow the production of finished components at minimal cost. Compared to traditional production methods, small-scale production using 3D printing is very profitable from a financial point of view. The manufacture of molds, for example, is a lengthy and costly process. At the same time, injection molding itself takes a lot of time. On a 3D printer, you can print a batch of the necessary products in a matter of hours. This application of 3D printing is extremely relevant for frequent orders for small batches of parts. nine0005
3. Repair and restoration
Another application of 3D printing is the repair and restoration of damaged parts. For these purposes, 3D printing is ideal. You can carry out such a procedure both independently, with the appropriate skills and equipment, and in specialized 3D printing services, such as 3DDevice. First, a correct 3D model is built on the basis of the damaged product. 3D scanning can also be used to simplify design. Next, the finished model is sent to print and reproduced on a 3D printer in the required number of copies. Repair and restoration of damaged parts using 3D printing is fast, and the presence of a digital model of the component allows you to reprint it at any time. nine0005
4. Production of functional models and finished components
One of the industrial applications of 3D printing is the production of functional models and finished components. Making products on a 3D printer from a transparent material allows you to see the work of a functional part “from the inside”, which is very useful when developing various engineering samples. In addition, a wide range of different materials for 3D printing turns it into a full-fledged production tool. Industrial 3D printers are gradually becoming a part of every industry, allowing the production of durable metal components. nine0005
Other questions and answers about 3D printers and 3D printing:
- Opportunities What is the future of 3D printing?
- Finance How to choose the right 3D printer?
5. Household items
Need an office organizer? Or a knife holder? Any household items can be printed on a 3D printer. The advantage of this application of 3D printing is that there are no restrictions when developing 3D models. That is, if you want to show imagination and create something original - all the cards are in your hands. Thanks to 3D printing, your home can be decorated and made more functional easily and inexpensively. nine0005
6. Toys and souvenirs
Having a 3D printer makes it very easy to make a child happy – just make cute 3D toys. There are already some pretty interesting projects of collective 3D printed games, and in the future this list will only expand. This application of 3D printing will please not only children, but also enthusiastic collectors, because on a 3D printer you can print figures of any characters and attributes of computer games and films. And color 3D printing will make it possible to produce exclusive full-color souvenirs - miniature figurines of real people. To do this, a digital model of a person is formed on the basis of 3D scanning data. In this case, all textures and color data are preserved. Everyone will definitely like such a gift, because getting a tiny copy of yourself is so unusual. nine0005
7. Design products
For creative people, there is another use for 3D printing. 3D technology in general is a unique opportunity to show your talent in the most unusual way. Artists, sculptors, fashion designers and designers from all over the world use 3D printing to create exclusive pieces of art that would be impossible to produce with standard methods. Such designer pieces impress with their beauty and originality, often fusing digital and traditional art. In addition, 3D printing techniques for clothing and footwear are being actively developed. Some models have even gone on sale, but it's too early to talk about mass production. nine0005
8. Capabilities of a 3D printer
We have listed the main capabilities of a 3D printer, but they do not end there. 3D printing finds application in a wide variety of industries. With its help, electronics, various components, food and even living tissues are printed. Of course, this list will be replenished in the future, but already now it impresses with its scale. We hope that we were able to provide information about the existing application of 3D printing in an accessible way. If you have additional questions that we have not covered, write to us by e-mail and we, if necessary, will add your questions! Best regards, 3DDevice team. nine0005
In addition, our company provides 3D printing, 3D scanning and 3D modeling services of any complexity at the best prices on the Ukrainian market. The 3DDevice online store offers a wide range of products (3D printers, 3D scanners) and consumables (plastics and resins). For any questions please email us or call one of these numbers. We look forward to collaborating!
Back to home page
Application of 3D printing technologies in various fields and industries
Application of 3D printing
3D printing is no longer a novelty, not something cosmic and top-secret, but a technology that is quite applicable in real human life, which is actively developing more and more new areas (applications). Already now there are areas of application of 3D printing, in which it has firmly established itself and is not going to lose ground. First of all, the following should be noted:
- medicine and dentistry;
- education;
- jewelry production; nine0032
- small-scale production, including souvenirs;
- architecture and construction;
- design and fashion;
- art and museum work;
- functional sample testing and more.
3D printing in medicine and dentistry
3D printers in medicine and dentistry can solve a wide range of tasks. First of all, prosthetics should be noted, since conventional 3D printers make it possible to create not only banal prostheses, but also entire exoskeletons that can significantly improve the quality of life of many people. Also, 3D printing with biocompatible materials is used to create high-precision implants, for example, in maxillofacial surgery. nine0087 In the field of orthopedics, unique insoles and shoes can be made using a 3D printer.
3D printing is indispensable for planning operations, so you can print an organ or affected area with the highest detail based on MRI or CT data. In this way, you can reduce the time of the operation and eliminate errors.
Dentistry uses 3D printing to make high-precision casts, prostheses of teeth of varying degrees of complexity, as well as mouthguards for bite correction.
3D printing in architecture and construction
In the field of architecture and construction, 3D printing is most in demand in the field of creating models of future structures. For this purpose, full-color plaster printing is used. As a result, a ready-made highly detailed layout can be obtained literally in hours, and not months, as it was before.
3D printing is also used to create small architectural forms, both from plaster and plastic.
Fashion, art, design…
3D printing with flexible polymers is actively used in the field of creative clothing and footwear. The technology allows you to implement a project of any complexity, and is already highly appreciated by fashionistas, stylists and just creative people. nine0087 Creating design objects using 3D printing is a new word in interior and fashion design. The most original and unusual idea can be implemented in the shortest possible time (application). At the same time, not only clothes are printed, but also figurines, original lamps and even furniture. Particularly stands out the possibility of creating original jewelry, jewelry and accessories.
Application of 3D printing in the jewelry industry
3D printing in the jewelry industry is no less in demand. Firstly, with the help of 3D printing, you can create original prototypes, burn-out samples. Secondly, there are 3D printers capable of printing jewelry alloys, which allows you to create original precious jewelry through 3D printing. Many jewelry stores offer the development of individual jewelry and use 3D printing to create them. nine0005
Functional testing and small-scale production
For sample testing and small-scale production (from 1 unit of goods, including exclusive), it is not advisable to use expensive casting technologies, which also take a lot of time. 3D printing allows you to get an object with the necessary characteristics in the shortest possible time and carry out all the functionality tests.
If you need 3D printing, you don't have to buy an expensive 3D printer. Printing services are available. We offer you a wide range of materials and printing technologies. Competent employees are ready to choose the best printing option that will 100% meet all your requirements. To order 3D printing, you must provide a file with a digital model in STL format. nine0005
Application of 3D scanning
Simple scanning of two-dimensional objects made a splash when it appeared. What are the prospects for 3D scanning? Now a huge number of spheres of human activity uses the possibilities of 3D scanning. It is most in demand in the following areas:
- medicine and dentistry;
- reverse engineering and industrial production;
- design;
- architecture, restoration; nine0032
- museum work and art;
- archeology;
- automotive and tuning;
- production of souvenirs and much more.
The range of possibilities for using 3D scanning is vast and much wider than it can be described.
3D scanning in medicine and dentistry
The medical field is an area that actively uses almost all innovative technologies. With the help of 3D scanning, you can achieve the highest quality solutions in the field of maxillofacial surgery. 3D scanning allows you to make prosthetics as accurate as possible. 3D scanners are also used in the manufacture of ear prostheses and inserts that maximally repeat the individual anatomy of the patient's ear. nine0087 In dentistry, 3D scanning creates an exact digital copy of the future prosthesis and the patient's oral cavity.
3D scanning of the human foot allows for high-precision modeling in orthopedics for the manufacture of shoes that are ideal in design and shape.
3D scanning in industrial production and reverse engineering
3D scanning allows you to get an exact digital copy of the part for its subsequent modernization, modification or refinement. This approach is called reverse engineering. nine0087 Applicable 3D scanning in the field of industrial production, allowing for better and more advanced 3D modeling of a wide variety of objects.
Design, art, museums and archeology
3D scanning of art objects allows you to create inexpensive replicas. In the field of design of various objects, 3D scanning allows them to be unique by adding various creative elements.
Through 3D scanning, you can create virtual museums and archives that will store exact copies of art and history. You can work with digital copies without fear of damaging the original. Therefore, 3D scanning is actively used in archeology. The use of 3D scanning is also very promising in the field of restoration of various objects. nine0087 It is simply impossible to enumerate all the possibilities of using 3D scanners. And if you need to take advantage of these opportunities, then it is not at all necessary to buy an expensive 3D scanner. You can order 3D scanning in our company. Professional engineers will quickly and efficiently carry out all the work, providing you with the necessary material.
Application of 3D modeling
3D modeling is work in a special software environment that allows you to create a digital three-dimensional, three-dimensional prototype of an object. The main purpose of 3D modeling is the creation of new objects, products, products. nine0087 The range of application of 3D modeling and 3D visualization is very wide:
- medicine and dentistry;
- industrial production;
- science and education
- architecture;
- graphics, animation, games and videos;
- design;
- advertising and marketing;
- jewelry sphere, etc.
A variety of software products are used for work, depending on the task and goals. Among the main ones: Autodesk 3d Max, Blender, Zbrush, Compass (CAD), AutoCAD, SolidWorks and many others. nine0005
3D modeling and visualization in medicine and dentistry
3D modeling in the medical field can not only visually show the patient the course of the operation and future changes (plasty, maxillofacial surgery), but also carry out anatomically accurate modeling of prostheses and implants (application) . Similarly, 3D modeling is used in the field of dentistry. To this end, they work in special dental software that takes into account various anatomical features of the oral cavity, bite and dentition of the patient. nine0087 3D modeling is also used in the manufacture of ear prostheses and earmolds, which must perfectly follow the anatomy of the patient for maximum comfort.
3D modeling in production
3D modeling is actively used in the manufacturing industry in the development of various products. For example, when developing a new collection of furniture, dishes, etc. But the most important 3D modeling will be in the production of various equipment: cars, assemblies, assemblies, equipment, etc. nine0087 Accurate 3D visualization even allows you to develop advanced parts of different equipment, ideally suited to existing conditions.
In modern conditions, the design of the future product plays an important role, starting with the body of the equipment and ending with the body of the car. 3D modeling allows not only to visualize the process, but also to make changes if necessary.
3D modeling in design and architecture
With the help of 3D modeling, not only product design is developed, but also landscape design, architecture, interior design, jewelry, a variety of art objects. The ability to make changes and a preliminary assessment of the project make the process less costly and more efficient. nine0005
Marketing, advertising, animation
In the advertising and marketing field, the use of 3D modeling allows you to create unique designs with original design and execution, embodying even the most complex ideas. The scope of use is not limited to the production part. This also includes commercials created using 3D animation, which is actively used in modern cinema. And 3D graphics has long been an integral part of computer games.
3D modeling is a complex process that requires professionalism, especially in cases with complex objects. Our company offers professional 3D modeling services in various software environments.