Fotocopias 3d print la plata
TRUYOL Digital - Impresión Digital - Imprenta Online
Packaging
0,60 €/ud
500 uds Cajas Extra Segura 8x8x6cm (excl. IVA)
Encuadernación
3,54 € 3,19 €/ud
200 uds Pur 17x24 cm, 100 pág. (excl. IVA)
Cartelería
20,00 € 18,00 €/ud
15 uds Display Metacrilato 3 mm (excl. IVA)
¡El mayor catálogo de productos con el mejor servicio de impresión digital solo en nuestra imprenta online!
4.65
Excelente
Papeles Estucados
31,72 €
100 uds A6 Estucado Mate 300 gr. (excl. IVA)
Roll Ups Estándar
52,27 € 47,04 €/ud
15 uds Roll Ups Estándar 85x200 (excl. IVA)
Póster
61,11 € 54,99 €
100 uds 50x70cm Estuc.Brillo 150- 1/C (excl. IVA)
Flyers
114,49 €
2000 uds Flyers A5 Estuc Brillo170 (excl. IVA)
Cartelería
50,38 € 45,34 €
10 uds 50x70cm Póster Semifotográfico (excl. IVA)
Vinilos
102,61 € 92,35 €
25 uds Vinilo Monom.Blanco Bri 50x70 (excl. IVA)
Cajas Estándar
1,07 €/ud
300 uds Caja Estándar Tecknocard (excl. IVA)
Hojas Offset
53,30 €
100 uds A4 Offset Blanco 300 gr (excl. IVA)
Ver más productos
Lo nuevo del Blog
Aprende a elaborar el arte final para imprimir en Gran Formato
9/Enero/2023
Diseña la estrategia unboxing: de las cajas para eCommerce al mensaje
6/Diciembre/2022
Inspiración de Navidad: tarjetones y decoración para empresas
11/Noviembre/2022
Máxima calidad
garantizada
Resultados de la máxima calidad gracias a la última y más variada tecnología digital para impresiones en hoja, etiquetas en bobina, gran formato, troquelado y aplicación de acabados en alta definición.
Entregas en
tiempo récord
¿Tienes una urgencia? ¡Te enviamos el pedido desde 24h a toda la península! Y si eres de Madrid o alrededores, ¡haz tu pedido en nuestra imprenta online y recógelo en nuestras instalaciones de Alcorcón, Madrid, en un plazo de 3h!
Herramientas
de valor añadido
Si buscas un acabado para potenciar el diseño, una tinta especial para destacar, un soporte creativo
o un papel con textura, ¡estás en la imprenta adecuada! Encuentra la herramienta que necesitas para
elevar el diseño y revalorizar el producto.
Tiradas cortas
a medida
Pedidos con tiradas a medida para que rentabilices cada impresión. Esta fórmula es ideal para todo tipo de negocios, campañas promocionales personalizadas, impresión de material para eventos y ferias, ediciones limitadas, prototipos, etc.
¿Qué opinan nuestros clientes?
1931 Valoraciones
4.65Excelente
Verificada
hace 20 horas
Un diez sobre diez
Un diez sobre diez
Muchísimas gracias por confiar en nosotros, es una satisfacción ver clientes tan contentos. ¡Un saludo!
Verificada
hace 2 días
Excelente calidad, buen precio, magníficos profesionales y gran rapidez. ¿Se puede pedir más?
Excelente calidad, buen precio, magníficos profesionales y gran rapidez. ¿Se puede pedir más?
Gracias por tus palabras, son la mejor recompensa a nuestro trabajo. ¡Feliz semana!
Verificada
hace 3 días
Todo perfecto, si hay alguna pega igual seria que ha veces es difícil poder contactar por teléfono en algún departamento.
Todo perfecto, si hay alguna pega igual seria que ha veces es difícil poder contactar por teléfono en algún departamento.
Buenos días ¡Gracias por tu comentario! Tu visión nos ayuda a mejorar. Un saludo
Verificada
hace 6 días
Habéis sido rápidos y eficaces, además de muy amables cuando he tenido una duda y os he pedido ayuda, Buena calidad, impecable empaquet
Habéis sido rápidos y eficaces, además de muy amables cuando he tenido una duda y os he pedido ayuda, Buena calidad, impecable empaquetado, ha llegado antes de tiempo. Enhorabuena
Muchas gracias por tus palabras, trabajamos para ofreceros la excelencia en calidad y servicio. ¡Feliz fin de semana!
Verificada
hace 7 días
Muchas gracias, Me encanta el resultado.
Muchas gracias, Me encanta el resultado.
¡Gracias por confiar en nosotros! Trabajamos para ofreceros la excelencia en cada impresión. ¡Feliz jueves!
Verificada
hace 7 días
He trabajado con ellos desde hace unos meses y nunca me han fallado. Tienen las tres Bs: buenos, bonitos y baratos...además de rápidos!!
He trabajado con ellos desde hace unos meses y nunca me han fallado. Tienen las tres Bs: buenos, bonitos y baratos...además de rápidos!!
Muchas gracias por tu confianza y fidelidad, tus palabras son motivación para nosotros. ¡Un saludo!
Verificada
hace 10 días
Poca atención personalizada.
Poca atención personalizada.
¡Buenos días! Para cualquier consulta, puedes dirigirte a [email protected] o a tu comercial de referencia. ¡Un saludo y feliz semana!
Verificada
20/01/2023
Muy rápidos, no fallan.
Muy rápidos, no fallan.
Gracias por confiar en Truyol Digital. ¡Feliz fin de semana!
Verificada
14/01/2023
Sin duda mis compañeros de batalla!! gracias por todo
Sin duda mis compañeros de batalla!! gracias por todo
Muchas gracias por confiar en nosotros, tus palabras son la mejor recompensa a nuestro trabajo. ¡Feliz semana!
Verificada
04/01/2023
Como siempre un trabajo perfecto
Como siempre un trabajo perfecto
Muchas gracias por tus palabras, trabajamos para ofreceros la excelencia en calidad y servicio.
Plantillas personalizables
y dinámicas
¡Plantillas listas para personalizarlas con el diseño! Las plantillas dinámicas están disponibles para libros, revistas y catálogos, y para algunos modelos de packaging señalados. Solo es necesario introducir las dimensiones del producto y descargar la plantilla que se generará a medida.
Impresiones
sostenibles
Elige un papel con certificado FSC y/o PEFC de nuestra imprenta online, solicítanos tu código de certificación e ¡intégralo en el diseño! En el área de gran formato de la imprenta, encontrarás opciones de soportes fabricados a base de materiales reciclados.
Aprende con nuestros
tutoriales
Si necesitas repasar los requisitos para preparar el arte final perfecto para imprenta o no sabes cómo aplicar un acabado o tinta especial, ¡visita la sección de tutoriales de nuestro blog o descárgate la Guía para la Elaboración del PDF!
Inspírate
¿Presupuesto Personalizado?
Si quieres un presupuesto personalizado, envíanos un correo a presupuesto@truyol. com con lo quieras imprimir. Lunes a Viernes, de 8:30 a 18:00h
¿Necesitas ayuda?
Contacta con Atención al Cliente a través del teléfono 91 641 42 81, por correo [email protected], o por nuestra página de contacto. Lunes a Viernes, de 8:30 a 18:00h
En nuestra imprenta online,¡puedes imprimir todo lo que imaginas!
Somos tu imprenta digital de confianza, con sede en Madrid, donde encontrarás todo lo que necesitas para tu proyecto. Te invitamos a navegar por truyol.com y descubrir toda la variedad de productos de pequeño y gran formato y las opciones creativas a tu disposición con tan solo unos clics.
¿Quieres imprimir con nosotros?
Nuevo PresupuestoCrear cuenta
Stratasys Direct Manufacturing | Manufactured Parts on Demand
Stratasys Direct Manufacturing | Manufactured Parts on DemandUSA & Canada
Select your country and region
- Americas
- English
- español (México)
- português (Brasil)
- EMEA
- English (United Kingdom)
- Deutsch
- español (España, alfabetización internacional)
- français
- Italiano
- APAC
- 中文(简体)
- 日本語 (日本)
- 한국어(대한민국)
- English (India)
USA & Canada
Leading companies trust Stratasys Direct for on-demand manufacturing
20+ Million Parts
Manufactured on Demand
300,000+ Projects
Completed from Start to Finish
1.
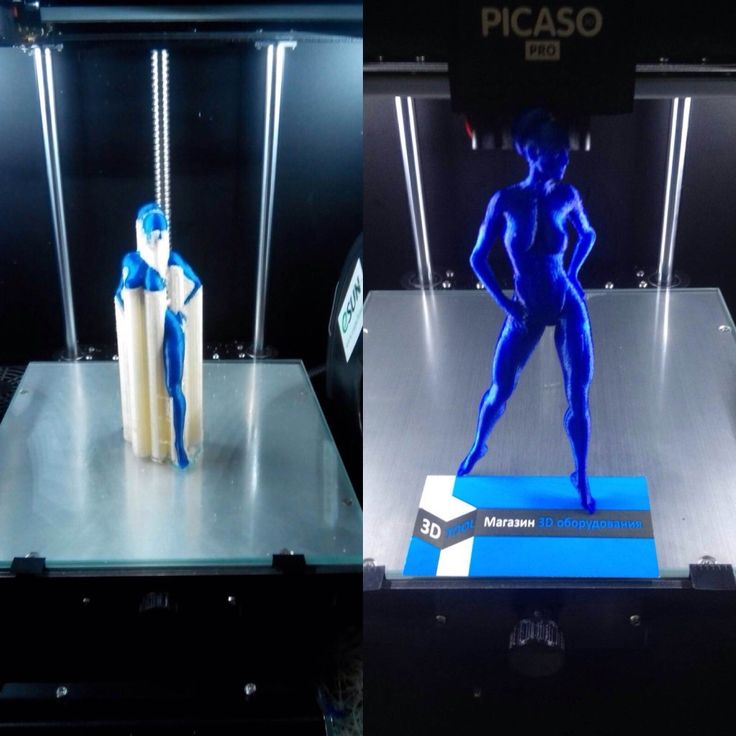
Engineering Time Logged
Industry-Leading Customer Loyalty
Say We're Easy to Do Business With
Feel They Received Value for the Money
Say They Would Buy From Us Again
Would Refer Us to a Friend or Colleague
“3D printing these parts delivered an immediate weight savings benefit. Additionally, the lower part count translated into cost savings on the administrative side including inspection, purchasing, and product support. “Subsequent change incorporation is also much faster and less expensive given that there are no permanent tooling expenses, or tools to be maintained or modified.”
Dinesh Sharma, Bell Helicopter Textron Inc.
Custom Manufacturing Services from Prototypes to Production Parts
3D Printing
Utilize our custom 3D printing services for rapid prototyping and production parts. Take advantage of a range of additive technologies and both plastic and metal materials.
Learn more
Urethane Casting
Create quality, consistent parts using our low-mid volume urethane casting process. We offer innovative master pattern production for fast turnarounds and consistent delivery.
Learn more
CNC Machining
Get CNC machined parts quickly with our efficient operations and experienced CNC manufacturing machinists.
Learn more
Injection Molding
Our fast tooling methods deliver high quantities of injection molded parts. With near-unlimited material choices, injection molding is a reliable choice for fabrication.
Learn more
Design Services
Create designs that leverage the power of the additive manufacturing process. Design Services offers CAD file modifications for optimization and expedited time-to-market.
Learn more
Types of Materials & Manufacturing Technologies we offer
Thermoplastics
Technologies:
- Fused Deposition Modeling
- Injection Molding
- Selective Absorption Fusion
- Multi Jet Fusion
- CNC Machining
- Laser Sintering
Learn more
Photopolymers
Technologies:
- Stereolithography
- PolyJet
- Programmable Photopolymerization (P3)
Learn more
Metals
Technologies:
- Direct Metal Laser Melting
- CNC Machining
Learn more
Urethanes
Technologies:
- Urethane Casting
Learn more
Thermoplastics
Manufacture robust plastic parts with engineering-grade thermoplastics with both industrial 3D printers and conventional manufacturing processes.
3D print your production parts, functional prototypes and manufacturing aids in familiar plastic materials like ABS, PC, high-performance ULTEM™ 9085 resin, and neat and composite nylons.
Browse Thermoplastic Materials
Photopolymers
Make highly detailed, vibrant 3D printed parts with photopolymers.
Photopolymer 3D printing materials are ideal for functional prototypes and concept models that closely resemble finished products.
Browse Photopolymer Materials
Metals
Produce complex geometries in one build with additive manufacturing metals.
3D printed metal parts are dense, corrosive resistant and strong. Our additive metal experts have validated and developed metal materials for unique application needs.
Browse Metal Materials
Urethanes
Create repeatable, cosmetic parts with a large range of urethane casting materials.
With unique combinations of physical properties for parts manufacturing, our proprietary urethane materials are specially formulated to address unique applications.
Browse Urethane Materials
Making Your 3D Printing Ideas a Reality
Product Development Life Cycle
Discover how our custom 3D printing services and manufacturing solutions fit into each of the product development stages.
Whether you’re designing 3D models or are ready for 3D printing production, we have a full suite of on demand manufacturing solutions available.
Learn more
Industries
From take-off to the operating room, each industry needs custom manufacturing services. Utilize a 3D printing service with decades of experience in key markets.
Our broad suite of manufacturing technologies and project engineering expertise enables us to take on your most ambitious challenges.
Learn more
Resources
Explore our resources to learn more about how our advanced manufacturing solutions allow your business to get to market faster.
Our knowledge base contains hundreds of articles, tutorials, case studies, infographics, white papers, design guides, webinars, videos and more.
Learn more
Printed circuit boards using a photopolymer 3D printer / Sudo Null IT News And in the last year or two, thanks to a strong reduction in cost, their photopolymer subspecies is also flourishing.

Even when I just learned about the appearance of a new type of photopolymer printers a few years ago - in which the image of the layer for illumination is formed by an LCD, the thought flashed through me already then: "Hmm, what if we substitute a photoresist on a textolite?". But then it was a purely theoretical question - the prices for them were considerable, and the resolution and display area left much to be desired. However, today these printers can already boast of a decent resolution - from 30 microns per pixel, and a completely normal display area. nine0003
And as it turned out, with the help of an inexpensive modern photopolymer printer, it is quite possible to make boards with tracks / gaps from 0.15 mm.
I apologize in advance for such a voluminous graphomaniac, I myself did not expect that the note would get so fat. ..
I foresee the question "But why? In China, they will make normal boards with a mask and silk-screen printing for a penny!" I answer: now, most likely, there will be several iterations of finishing the board to a satisfactory state. I made a board - tested it - made corrections. And so several times. Waiting every time for 2-3 weeks from China is not an option :) But when the final design of the board is determined - then, of course, normal production in China or on Rezonit. nine0003
Now let's get down to business.
Who does not know - here is a brief principle of operation of such a printer The main part of such a printer is an LCD display. Below this display is a 405 nm UV source. Above the display is a bath of photopolymer, which has a thin transparent FEP film as a bottom. A platform is lowered into the bath, on which the model is “grown”. At the beginning of printing, the platform lowers to the height of one layer from the film, the image of the first layer is displayed on the display, and UV illumination is turned on for a specified time. Illumination, getting through the "open" pixels of the display and the film onto the photopolymer, hardens it, so a hardened layer is obtained. The first layer sticks to the platform. Then the illumination is turned off, the platform rises to the height of the next layer, the image of this layer is displayed on the display, and the illumination is turned on. The second layer is cured by welding with the previous layer. And this is repeated over and over until the entire model is printed. nine0003
The idea to try to make a printed circuit board using such a printer came to me again about three years ago, when I bought myself an Anycubic Photon S printer. , then I just forgot about this idea, because and there was no need to make boards. But the other day, the need arose for the manufacture of several small boards, and with a high probability that as tests are made, changes will be made to these boards and it will be necessary to go through several iterations of "manufactured-checked-changed" in a short time. And the idea resurfaced. nine0003
To be honest, I thought that by now the Internet would be filled with the results of such experiments, the idea lies on the surface :) But to my surprise I found that the Internet is almost completely silent on this issue. There are separate notes, but there is no integrity and completeness in them. That's why I decided to publish this post - maybe it will help someone go all the way faster than me, and with less rakes :) nine0003
Well, the most important thing is that you don't need film and you don't have to struggle with increasing the contrast of the template. You also do not need a separate UV source with a place for its installation. And, of course, it is stylish, fashionable, youthful.
There are also disadvantages - the resolution of most modern 3D printers still does not cause much enthusiasm yet - the pixel size of all fluctuates around 0.05 mm. But this is already enough for confident manufacturing of boards with tracks from 0. 2 mm and rather high chances of success with tracks from 0.15 mm. Due to the raster nature of such a template output, the position and size of elements on it can vary + -1 pixel, so I think it’s not even worth counting on tracks of 0.1 mm or less. nine0003
Let's go in order.
Task
It is necessary to make a printed circuit board at home using photoresist. Instead of templates and illumination lamps, use a photopolymer 3D printer that will serve both at the same time.
Let's divide the problem into separate steps-solutions for each moment.
-
Board development
-
Outputting layers in a printer-friendly format
-
Preparation of textolite with photoresist
-
Printer flare
-
Photoresist development, board etching
1. PCB development
Well, there are no questions. Whoever prefers to work in what program - in that one makes boards. The main thing is that the program should be able to display the result in some commonly used form. The easiest way I've come up with is outputting board layers to gerber files that can be fed to an online service. But you can also output to PDF or images. nine0003
2. Converting the CAD output to a printer friendly
This is where the trouble begins. If almost all CADs can output to generally accepted formats - gerberas, DXF, printing to PDF, then 3D printer manufacturers so far categorically refuse to accept any file standard. Everyone is perverted as they can. The situation is largely saved by the fact that many manufacturers use motherboards from one Chinese company, Chitu Systems, in their printers. Thanks to this, many printers on such boards are able to understand one of the basic formats developed by the same company. And even often, if a file has some unique extension, then in fact it has the same basic format, just with a different extension. But it may differ in some details. nine0003
In any case, there is a free UVtools utility known among photopolymerists that can open files in one format and convert them to another format. It understands almost all formats on the market :)
I have tried two ways of preparing files with layers for the printer and I will describe both.
2.1 Gerber output and conversion to .photon
The .photon file format is understood by the old Anycubic printers - Photon and Photon S. This is exactly the case when the printer manufacturer took the format from Chitu and changed its extension. In the original, this is the Chituvian .cbddlp format, so you can safely change the extensions of these file types among themselves and the printers will devour them like native ones. nine0003
Since I have a printer that understands this format, this method suited me perfectly. The limitations of this method are that the printer must understand .photon or .cbddlp files and have a standard display for most non-monochrome printers with a resolution of 2560x1440 and a diagonal of 5.5". manuals on how to do this for any CAD that can, in principle, mirror layers or not - it makes no difference, they can be mirrored in the utility during the conversion process. 0003
Now open the online utility for converting gerber files - https://pcbprint.online/ and load the gerberas into it. By the way, this is a utility from a Russian developer who lives here.
It is easy to understand, although it does not contain any information or help. But here is a short guide:
For a single-sided boardUpload your gerbera in the main window with the "Upload file" button:
We made sure that everything is fine and the image meets expectations, if necessary, make a negative or mirror the image with the buttons in the top center, and press the button " Render layout":
Now press "Lauout" at the top right and get into another screen:
Here you first need to go to the settings (gear button at the top right) and there select the format of the output file "photon":
The time in "Exposition" can be left at default and change it to the desired one directly in the printer. But you can immediately put the right one if its value is already known :)
Close the settings and return to the previous screen. Here the output image is on a black space showing the working field of the printer. The image can be moved, aligned. When everything suits, we first press "Render", and when the "Download result" button next to it becomes active, we also press it. And save the proposed .photon file to a convenient location on your computer :)
For double-sided boards, things are a little more complicated due to the need to match them. Therefore, it is necessary to know very exactly the position of the image displayed on the printer's display in order to place the board on the display very accurately in accordance with it.
I had several options for solving this issue, but in the end I decided on the simplest of them, which did not require any mechanical conductors. To do this, I still in CAD in a separate layer (it is possible in the border layer or in any other "unnecessary" layer) I draw a frame around the board with a line of 0.15 mm and indented from the edges of the board by 0.25 mm. As a result, I get three gerberas - the top layer, the bottom layer and a separate empty frame. nine0003
I upload all three gerberas to the above site and then in a few steps I get three files for the printer.
Double-sided board in pcbprint.online/So, all three gerberas have been loaded. All of them are mixed together, but it's not scary:
Now hide the top and bottom layers, leaving only the frame (by clicking on the eyes in the names of the gerberas).
Click "Render layout" and go to the "Layout" screen with the button in the upper right corner. We see an empty frame, drag it to the desired position on the black field of the display, click "Render" and "Download". The first file for the printer is ready. nine0003
Switch back to the gerber screen with the "PCB comose" button. Redisplay the first layer (the frame layer still remains visible), mirror if necessary, and click "Render layout" again. Again we go to the output screen and now there are two pictures hanging on the display field - a separate frame and the first layer with a frame. The frame remained in the same place where we pulled it last time. And now our task is to exactly combine the frame of the first layer and the empty frame:
Click "Increase" and combine in one of the corners. In this case, in no case should you move the empty frame that we set in the last step! nine0003
Combined, click "Render" and "Download", and we have a second file for the printer. Before returning to the gerbera screen, we delete the render layer with the frame, we should again have an empty frame. And now we return to the gerberas, hide the first layer and display the second one, look at the need to mirror, click "Render layout" and go to this screen again. In the same way, we combine the layer frame with an empty frame (which cannot be moved!), then "Render" and "Download".
Everything, all three necessary files for the printer are ready. nine0003
All this hemorrhoids allows you to generate for the printer files of an empty frame and layers with a frame in the same place on the printer display with high accuracy. The empty frame serves to aim the board, more on that below.
If necessary, the resulting .photon files can be converted to the desired format using UVtools :)
2.2 Output layers to PDF or images
The second method is perhaps more confusing, but its great advantage is versatility, it is suitable for any printers, whose formats are supported by UVtools. I will describe it only in general terms, because. There are quite a lot of tools and specific ways to implement it, and everyone can choose them according to their preferences. nine0003
So, the goal of the first step is to get a picture with a size equal to the resolution of the printer's display, preferably in a lossless compression format. In this case, the image of the layer in the picture must correspond to the real size in the scale of the display.
If CAD allows you to output directly to the picture - great, output to it. If the resolution of the output image is configurable - specify the resolution of the printer display. It is elementary to calculate it - we divide the number of pixels across the width of the display by the width of the working area in mm and multiply the result by 25.4, we get the resolution in pixels per inch. If the resolution is not set, then set the image size as large as possible so that there are at least 15-20 pixels per 1 mm of the board. nine0003
If output to image in CAD is not available, then output to PDF. This PDF will need to be opened in another program and converted to an image. Photoshop, Corel, maybe other programs can do this... The requirements for image resolution are the same. For example, in Photoshop, when importing a PDF, you can immediately specify with what resolution to convert to an image. For example, for common displays with a resolution of 2560x1440 and a diagonal of 5.5 "the resolution is approximately 537.566 PPI (pixel size - 0.04725 mm).
The resulting image will need to be changed in some image editor, bringing its size to the resolution of the printer's display. In this case, the layer image must be scaled to the real one (taking into account the pixel size of the printer display) or saved without scaling if the PPI of the display was specified when importing the image.
UPD: in the comments @0x3f00 gave a link to his converter of PNG images to files for the .photon printer - https://github.com/0x3f00/PhotonCpp/releases/tag/v1.0.0 . There is also an instruction for using it just for the purpose of manufacturing boards - https://github.com/borelg/PhotonPCB. nine0003
2.3 There is another way, but it is very resource-intensive
You can output layers to PDF, then open this PDF in Corel, convert it, save it in DXF, extract a three-dimensional object from this DXF, which you can push into the printer's slicer.
Necessary transformations in the vector editor:
-
Connect all curves.
-
Convert outlines to objects.
-
Merge intersecting objects.
You can extract a three-dimensional object from DXF, for example, SolidWorks. Fusion360 also seems to be able to. Who else is capable of this - I honestly don't know, but in theory any CAD that can import DXF as a sketch.
Thus, for example, I made a model for determining the exposure time of the photoresist.
3. Preparation of textolite with photoresist
The Internet is simply littered with articles on this topic, but for the sake of integrity and for the sake of some specific points, I will also describe such well-known stages as the preparation and etching of textolite. nine0003
My first experience with such a fabrication was a couple of days ago with a domestic photoresist PF-VShch. Taking into account the last yesterday's experience, I categorically advise not to waste time on this photoresist, but immediately take a decent one - Ordyl Alpha 350(330) :) They say that Kolon is also decent, but I have not tried it. With Ordyl photoresist, the results are much more stable and accurate, it is easier to develop and adheres much better to the foil. And he can forgive those mistakes that will be critical for the PF-VSC. And what is important - it is sold in a bunch of places quite inexpensively. nine0003
3.1 Preparing the textolite
To begin with, the textolite should be smooth, very preferably with a smooth foil without scratches or dents. Otherwise, the chances of success are reduced.
If a double-sided board is being made, then you need to immediately cut the board out of the PCB exactly to size. If there is any CNC router, then you can drill all the holes and cut along the contour in one installation, as I do. If not, then it is better to leave the drilling for later, when the board is etched. nine0003
After this, the textolite blank must be very carefully cleaned and degreased. This can be done with a kitchen abrasive sponge (but not used for washing dishes on which fats have already accumulated) and a scouring powder like Pemolux. Very carefully, slowly three every square millimeter of foil, without touching it with your fingers. In general, I categorically do not advise touching the foil with your fingers after the start of cleaning, there should not be the slightest even the faintest greasy spot on it. After cleaning, rinse thoroughly in running water, shake off excess water and allow to dry. I do not advise blotting or wiping with anything, because. grease can be applied, even from a new napkin. nine0003
3.2 Application of photoresist
Also a fairly common topic on the Internet, so I'll go over it briefly.
Photoresist usually comes in sheets or rolls. It consists of three layers - two protective films and the photoresist itself between them. A piece is cut off from the photoresist according to the size of the board + 5 mm in length and width, then a matte (polyethylene) protective film is removed from it.
the second, glossy (lavsan) must remain on it until the etching stage.
The easiest way to remove the film is with a piece of tape. It is glued with its edge to the corner of the photoresist and then folded back, pulling the protective film along with it.
After removing the matt film, the photoresist is applied to the edge of the board and smoothed along this edge with a finger. The rest of the photoresist is supported by weight, without tension, but in such a way that as little as possible of its area lies on the foil.
Please note that if the Ordyl photoresist falls on a well-prepared textolite, then it can firmly stick to it, and without bubbles it can no longer be rolled. You have to scrape it off and do it all over again. And PF-VShch can fall as much as you like - it definitely won't stick :)
Now the knurling itself. If you have a laminator, in which the textolite will crawl through the thickness, then it's just wonderful. We make an envelope-type strip of paper folded in half, put a textolite with a sticky edge of the photoresist in it, and serve this sandwich into a laminator heated to 100-110 degrees. At the same time, we continue to hold the photoresist so that it comes into contact with the textolite foil only directly at the inlet of the laminator.
That's all for Ordyl, for PF-VShch it will be harmless to roll a couple more times. nine0003
If there is no laminator, then smooth the photoresist to the textolite with your finger from edge to edge, gradually lowering it onto the textolite. The main thing is not to catch the bubbles. After all the photoresist lay on the foil, we take a hair dryer and heat the textolite to 70 degrees, after which we iron the entire photoresist once again.
After knurling, let the textolite with photoresist lie down for 15-20 minutes, or at least until they cool down to room temperature - according to the recommendation of the photoresist manufacturer. nine0003
And now everything is ready to highlight the layer pattern :)
4. Printer highlights
I want to warn you right away: looking directly into the glowing display of a photopolymer printer may not be very good for the eyes. Although not true UV (405 nm), the brightness is quite noticeable and can be harmful to the eyes. Therefore, I recommend using colored or tinted goggles. I think even sunscreen will do.
First, you need to remove the bath and platform from the printer, they are completely unnecessary for this business and even interfere. This completes the preparation of the printer :)
Lighting also has different options. If you have a one-sided board and the blank is larger than the size required for the board, then everything is simple - throw the file obtained at the preparation stage into the printer and, knowing the approximate place for displaying the image on the display, put a textolite with photoresist in this place. Then start printing the file and wait until it is completed. Everything, the photoresist is exposed, it is possible to develop.
If the workpiece is equal in size to the board being made and the error with the position of the workpiece on the display is unacceptable, then in this case it is necessary to remove the frame during preparation, as is the case for a double-sided board. Illumination also occurs using a frame, similar to a double-sided board, only without the second side and the second layer. nine0003
So, the illumination of the double-sided board. We throw all three files into the printer - with a frame, with the first layer and with the second layer. We put the workpiece next to the printer in quick accessibility. If it is already pre-drilled, it will be useful to make sure that it lies in the correct position so that you can quickly take it and immediately put it on the display. To do this, we run a file with a layer planned for exposure, and compare the layer pattern on the display and the orientation of the board next to the printer.
Printing a file with one frame. As soon as the frame lights up on the printer display, we take the workpiece and put it approximately inside the frame. While the frame is being illuminated, we align the workpiece so that it is exactly in the frame, with the same indentation of the frame from the edges of the workpiece on all sides. nine0003
In the photo, I gave an example with a ready-made board, because I did not take pictures during the manufacturing process. Well, reflections interfere quite strongly, alas... But I think it's understandable :)
That's it, the position of the workpiece is verified, printing of the frame file can be interrupted or wait for it to finish. Without moving the workpiece, run the file with the first layer and wait for it to finish. We illuminate the second layer (the second side) in the same way - we launch the frame, place and align the workpiece, without moving it, we launch the second layer. Before this, just in case, you can make sure that the workpiece will lie in the correct orientation, as before the first layer. nine0003
If the workpiece is not completely flat and does not fit the entire area of the display, then you can press it down from above with some heavy flat piece of iron. You just need to make sure that this piece of iron does not interfere with the platform lever, which will go down with the start of printing - the printer thinks that this is a normal photopolymer print and you need to lower the platform to the bottom of the bath :)
Illumination time can be different from printer to printer . It depends on the power of the emitter, and on the optical illumination system, and on what type of display is worth - monochrome or RGB. Here already it is necessary to select each individually. For orientation, I can say that I got the best result with the Ordyl photoresist at an exposure time of about 90-110 seconds. With photoresist PF-VShch - about 10-13 minutes. Printer with paraled, illumination power slightly less than 50 watts.
After exposure, the workpiece should be allowed to rest for 15 minutes - this is according to the recommendation of the photoresist manufacturer. Ordyl changes the color of the highlights quite noticeably, so it's pretty easy to control the highlights. Unfortunately, the photo did not convey it well, it can be seen better with the eyes.
5. Development, etching
Everything here is according to the recommendation of the photoresist manufacturer and according to the classics of the Internet. nine0003
All necessary chemicals were purchased inexpensively from Auchan. Even hydrogen peroxide 6% - this was a surprise for me, I had never seen it in hypermarkets before, and even in liter bottles.
For one session you need:
-
Soda ash - 1.5 grams
-
Hydrogen peroxide - 150 ml for 3% (or 75 ml for 6% + 75 ml of water)
- citric acid
-
Salt - 7.5 grams
-
Alkali (caustic soda, sodium hydroxide) 5-7% - 100 ml
With the cheapness and ease of buying all the components around the corner, I am in favor of preparing a new solution for each board. Although the etching solution, as they say, is not stored anyway. A solution of soda ash noticeably "poorer" in the process of development. Unless caustic soda can be reused, but is it worth it to keep another bottle ...
Both Ordyl and PF-VSH appear in a weak solution of soda ash. For PF-VShch - 1-2%, for Ordyl - 0.8-1.2%. For Ordyl, we take 150 ml of water and dilute 1.5 grams of soda in it. The solution can be heated up to 30 degrees, this will speed up the development, but it is important not to overdo it, otherwise the illuminated areas may begin to be damaged.
Ordyl appears rather quickly. Already after 10-15 seconds, the illuminated pattern begins to become more and more contrasty, the unexposed areas gradually dissolve, become thinner and become paler. nine0003
To speed up the process, it is recommended to shake the bath so that the reaction products are washed off the surface of the workpiece. For this I adapted my old 3D printer, its table and shook and heated the bath with the solution during development and etching :) Two minutes passed before there were at least some signs that development had begun. In addition, if Ordyl does dissolve, then PF-VShch first swelled like gelatin and discolored, and only then began to slowly dissolve. nine0003
At the end of development, you can go over the boards with a hard paintbrush (or soft toothbrush) several times in different directions to help flush out any remaining photoresist from tight spots. Ordyl holds on tight, this procedure should not disrupt it, but with PF-VShch you need to be very gentle, even without a brush it strives to exfoliate on thin paths.
After etching, the workpiece must be rinsed in cold water so that the soda residues do not continue to attack the photoresist and so as not to clog the etching solution with them. nine0003
The result should be something like this, maybe even better :)
More detailsScale of the grid square - 0.2 mm:
The scale is the same. Here you can see the raster component of the illumination, the pixels stick out:
Etching was also done according to the traditional recipe, popular on the net:
It is better to heat the solution to 40-50 degrees, then the etching goes much faster. This is my first experience with this solution. I used to poison with ammonium perchlorate, and even earlier - with classic ferric chloride. To be honest, I can't really express how I feel about this solution. On the one hand, it poisons rather quickly, is transparent, does not get dirty, and is relatively safe. On the other hand, it seemed to me that it was easing quite a lot .
.. But maybe it just seemed, I haven’t been making boards for 10 years and I forgot how it all worked when the trees were big :)
After etching, the exposed photoresist must be removed from the workpiece, and this is done in caustic soda. On my bottle of cleaner it says "at least 5% but not more than 15%" and it takes 5-8% to remove the photoresist. I diluted the product 1:1 with water and this solution did the job perfectly. The photoresist does not dissolve in it, it simply peels off the foil after 2-3 minutes and begins to float in tatters in the solution.
After that, the board is thoroughly rinsed under the tap and... The board is ready! nine0003
Summary of my experience
Overall I am satisfied. I did not expect to get tracks / gaps of 0.1 mm and I did not get them. Here, the capabilities of the printer are severely limited (pixel size), and in general, good experience is needed for such results. But I was hoping to get at least 0.2 mm, and if I'm lucky, then 0.
15 mm - and I got it. 0.2 mm confidently, 0.15 mm - well, so-so... If you try, you can achieve :)
There were some flaws - it was not pickled in some areas, and imperfect alignment of layers and holes. But neither is critical. As for the non-mordant - I think that I just hurried to take it out of the developer, I was afraid after PF-VShch that thin paths would begin to peel off. Although in the reviews people write that it is quite difficult to re-develop this Ordyl, you need to try for this. Imperfect alignment of layers and holes is to be expected. From such a simple method of alignment, I expected an error of 0.1-0.2 mm, which I got, but it suits me. nine0003
Thank you for reading.
And finally, a few photos of my results. Exposure time test, from 1 to 2 minutes. Sites displaced relative to the holes are visible.yur9415
Loading
06/10/2022
3567
Technician
Follow the author
Subscribe
Don't want
2
Hello everyone, I decided to add a little convenience to the printer.
Designed and ordered a batch of switching boards.
The board is used for more convenient and quick replacement of the heating element, thermistor and coolers. This board is installed on all printers without fundamental changes in the design of the printer itself.
The board turned out to be universal and fits most printers. nine0003
One card is installed on the head of the printer, and the other in the basement or on the printer body.
The bottom board is connected using screw terminals. The cable and assembly instructions are shown in the video.
This interface board is equipped with flexible stranded wires that will not break during long-term use. In addition, XT2.54 connectors are used for frequently used elements (heating element and thermistor). They provide reliable contact, are easily disconnected (when replacing elements) and have mechanical latches to hold the connector during operation.
This approach is necessary not only to ensure the durability of the elements during regular maintenance of the printer, but also allow for quick replacement of the entire hot end with a different printhead configuration. nine0003
My printer does not have a BL-TOUCh sensor, but I provided the ability to connect it on the board.
If you have any questions please write.
https://www.avito.ru/krasnodar/orgtehnika_i_rashodniki/plata_kommutatsii_3d_printera_2456146034
Article comments
More interesting articles
32
Follow author
Follow
Don't want to
I was a little bored and itched. And then they also had a little effect on the brain regarding the vector...
Read more
2
Subscribe to the author
Subscribe
Don't want
Hello everyone and good day.
Learn more