What is a 3d metal printer
Metal 3D Printing | 3D Printing Technology
Technology
Metal 3D printing, or selective laser melting (SLM), combines the design flexibility of 3D printing with the mechanical properties of high-performance metal alloys to create unique, strong, and lightweight parts, even for the most complex applications. Metal 3D printing is ideal for creating fully functional prototypes and end-use parts that may be impossible to produce using conventional manufacturing methods.
Why work with Materialise Manufacturing?
Producing metal parts with Materialise is all about making the complex simple. From working with our Design & Engineering Team to accessing our industry-leading Metal Competence Center in Bremen, we help you take advantage of the flexibility and speed metal 3D printing offers compared to traditional methods. Whether you need prototypes or full series production, you can count on us from start to finish.
Discover applications of metal 3D printing
Lower manufacturing costs and increased design freedom made metal 3D printing the ideal choice for this redesigned aluminum gripper.
The exceptional thermal resistance of Inconel (IN718) made it an ideal choice for a crucial component in the cooling of a liquid-fueled rocket engine.
Redesigning two production line components for metal 3D printing improved efficiency and saved Philips Lighting almost €90,000 a year.
3D printed in titanium using a topology optimized design, LIFT Aircraft Inc's new ENDY bracket weighed 40% less than the original, without compromising performance.
The interior of this 3D-printed titanium wishbone has a honeycomb structure to reduce weight while maintaining strength.
Technical specifications
Maximum build dimensions | Dimensions are unlimited as components may be composed of several sub-parts. The maximum build envelope is 500 x 280 x 315 mm |
Standard accuracy | Better than or equal to the industry standards:
See design guidelines for more information on standard accuracy. |
Layer thickness | 0.04 – 0.09 mm (material dependent) |
Minimum wall thickness |
|
Surface structure | Unfinished parts are typically rough, but various post-production finishes are possible |
Materials
Choose from a broad selection of materials when you come to Materialise for your metal 3D printing projects.
Material
Aluminum (AlSi₁₀Mg)
Technology
Metal 3D printing
Material
Titanium (Ti₆Al₄V)
Technology
Metal 3D printing
Material
Stainless Steel (SS316L)
Technology
Metal 3D printing
Material
Inconel (IN718)
Technology
Metal 3D printing
Material
Stainless Steel (C465)
Technology
Metal 3D printing
Grades
Balance performance and efficiency in every project with your choice of Standard or Performance grades.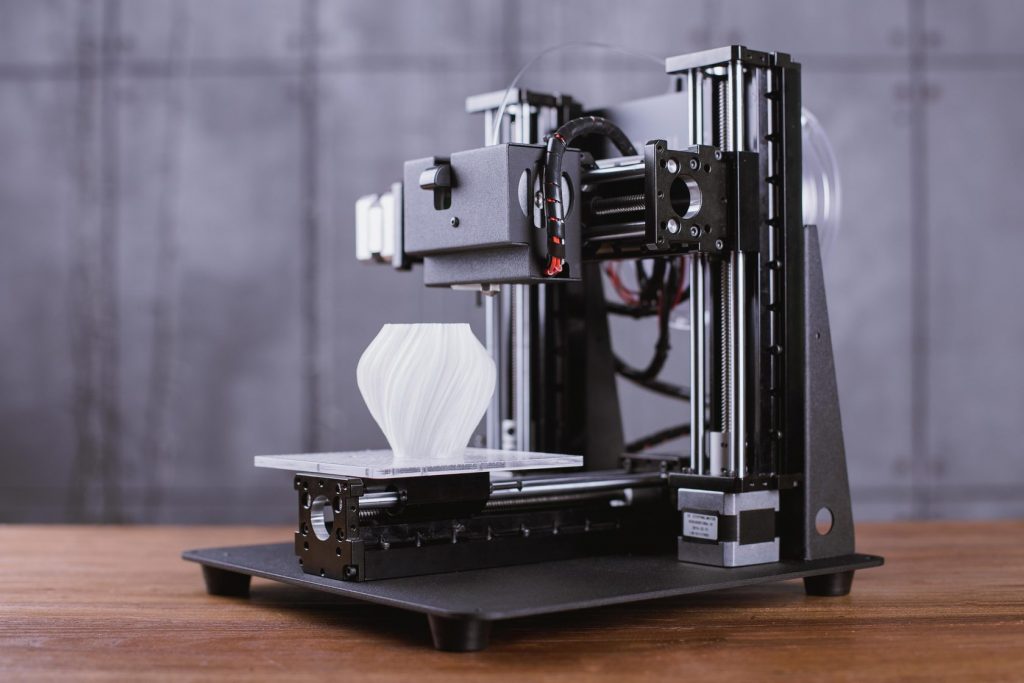
Standard
The all-rounder, where it’s all about technology:
- Ideal for prototypes and simple end-parts
- Form-, fit-, and function-testing
- Strength and density similar to cast parts
- Industry-standard quality requirements
Performance
The specialist, for complex production:
- Ideal for complex metal parts designed for AM
- Preferred for applications in demanding environments
- Suited for series production
- Higher strength and density than casting
- Specialized quality test reports available to your specification
Work with us: discover our products and services
Want to bring metal 3D printing into a future project? Discover the services that can help you do it.
Order online
Get direct 24/7 access to the technologies and materials you need to bring your designs to life. Instant quotes, short lead-times, and easy checkout.
Manufacturing services
Innovate and speed up your manufacturing in collaboration with our experts. Rely on our full range of in-house technologies suitable for all industries and applications.
Prototyping services
Transform your product development cycle and get the best possible products to market faster. Get unbiased advice and dedicated support from teams committed to your success.
Software
Build your success on a platform of software tools that efficiently manage and control the 3D printing process, allowing you to meet the highest standards of the most demanding industries.
Consultancy
Work with our experts to translate your business challenges into 3D printing opportunities and identify the applications that can help you meet your needs.
Get in touch
Would you like to ask a question or begin working on a project? We’d love to hear from you.
Talk to our team
Train and learn
Get more from your next project with helpful resources dedicated to metal 3D printing.
Quick links
How to design for metal 3D printingDiscover metal 3D printingFind related trainingEXPERT INSIGHT
Taking the Plunge: the When, How, and Where of Metal 3D Printing
4 min read
WHITEPAPER
Struggling with Production Costs and Lead Times of Metal Parts?
EXPERT INSIGHT
Taking the Plunge: the When, How, and Where of Metal 3D Printing
4 min read
WHITEPAPER
Struggling with Production Costs and Lead Times of Metal Parts?
© Copyright Materialise 2022
Cookie Statement
Legal terms
Privacy notice
The Metal X 3D Printing System
An accessible end-to-end metal 3D printing solution for functional metal parts, next-day.
Request a Quote
The Metal X System is an accessible way to fabricate complex metal parts in a wide variety of advanced metals.
Simple, Yet Powerful
The Metal X is one of the most intuitive metal 3D printers available today. Print a wide range of materials from stainless steels to copper with minimal training on a closed workflow. Scaling up capacity is easy; just add printers.
Safe and Affordable
The Metal X is designed to be safe to use and accessible for all fabricators. It costs several times less than DMLS metal 3D printing systems and requires no dedicated operator, no powder management system, and minimal PPE.
Quality Parts, Fast
The Metal X is purpose-built for consistent part quality and a seamless user experience. Markforged combines superb software, materials research, and an advanced motion system to deliver industrial-grade parts quickly and reliably.
Specs
From design to fully functional
metal parts in as few as 28 hours.
Physical Dimensions
Width | 575 mm |
Depth | 467 mm |
Height | 1120 mm |
Weight | 75 kg / 165 lbs |
Build Volume
Width | 300 mm |
Depth | 220 mm |
Height | 180 mm |
Printer primary Specs
- Printing Process
- Metal FFF
- Z Layer Resolution
- 50 μm - 125 μm (Post-Sinter)
- Printing Media
- Bound Powder Filament
- Internal Part Geometry
- Closed Cell Infill (Triangular) or Solid Parts
- Print Bed
- Heated, Auto Leveling, Replaceable Print Sheets
Wash & Sinter
Wash-1
- External Dimensions:
- 609 x 685 x 1,067 mm
- Weight:
- 136 kg (300 lbs)
- Washing Time:
- 12-72 hrs typical
- Solvent:
- Opteon SF-79
- Working Volume:
- 356 x 254 x 203 mm
Sinter-2
- External Dimensions:
- 1,200 x 700 x 1,500 mm
- Weight:
- 350 kg (772 lbs)
- Run Time:
- 17-31 hours
- Sintering Volume:
- 18,356 cu cm
- Peak Internal Temp.
:
- 1,300° C / 2,372° F
Materials
Compatible Materials
- Release Material
- Ceramic — Becomes Powder During Sintering Process
- Media (Spools)
- Bound Powder Metal Filament
System Details
Metal X PrinterThe Markforged Metal X is a new kind of metal printer. By printing metal powder bound in a plastic matrix, Markforged has eliminated many of the safety risks associated with traditional metal 3D printers. That means no loose powder, no lasers, and none of the traditional safety precautions. It’s safe to use in a shop environment with minimal facility upgrades.
In practice, the Metal X is essentially a very advanced FFF 3D printer. Featuring a precision machined gantry, a heated chamber and print bed, and advanced extrusion hardware, the Metal X is equipped to reliably print you durable parts. It is intentionally designed, with wear components and consumables — including print sheets, nozzles, and brushes — accessible and trivial to swap.
The Wash-1 is a solvent-based debinding system. It primarily uses Opteon SF-79, a high-performance fluid designed to offer superior cleaning power, higher efficiency, and safety in an environmentally sustainable way — Opteon SF-80 or Tergo Metal Cleaning Fluid can be substituted if needed.
The Wash-1 operates with simple ventilation and features an extremely simple user experience. It’s been tested and verified as a shop-safe system.
Sinter-2 and Sinter-1The Markforged Sinter-2 and Sinter-1 are highly optimized tube furnaces used for sintering 3D printed metal parts. They provide leading edge sintering reliability and run times and are equipped with advanced safety features. The Sinter-2 is more advanced than the Sinter-1 — featuring a larger working volume, more precise temperature control, and a mechanical door interlock.
The Sinter-1 and Sinter-2 typically have run times between 26 and 31 hours. However, the Sinter-2 can process small parts in express mode, where it can sinter up to 250g of parts in just 17 hours.
Download Datasheet
Materials
From stainless steel to copper,
choose from a wide range of strong,
durable, and capable materials.
How metal printing works on a 3D printer
Contents:
- Metal printing on a 3D printer
- How 3D technologies work
- Two main methods
- Video
Metal printing on a 3D printer (two main technologies)
The introduction of innovative technologies opens up new opportunities in various fields of human activity. A modern 3D printer for printing on metal allows you to print high-precision structural elements that are in demand in the space, engineering, and aviation industries.
How 3D technologies work
The production of 3D parts is made using different methods of melting metal powder (using a laser). But the basic principle of operation remains unchanged, so any 3D printer prints with metal in several stages, these are:
- filling the build chamber with an inert gas to minimize the oxidation of the source material;
- heating to the temperature required for the production process.
- powder distribution on the surface of the build platform;
- 3D scanning of the cross section of the starting material with a laser beam;
- melting and sintering of particles, which makes it possible to obtain a hard layer;
- shift of the platform by the amount of the obtained layer for applying the next one (until the object formation is completed).
The moment the metal laser 3D printer completes the process, the product is completely covered in powder. Therefore, until the chamber cools down completely (to avoid deformations), the object on the platform is fixed by the support area.
Two main methods
A modern metal 3D printer can use one of the two most common technologies - selective laser beam melting (SLM) or direct laser sintering (DMLS). Among the main differences between the methods, the principle of gluing the component should be mentioned:
- SLM - occurs as a result of complete melting of the powder;
- DMLS - individual particles are sintered (at lower temperatures compared to SLM) without passing into a liquid substance.
Unlike traditional casting or stamping, DMLS allows objects to be printed without internal stress. This ensures good technical characteristics of the parts. Today, manufacturers offer models that can use several melting options at once.
Among other techniques for bonding powder particles, mention should be made of the UAM (additive ultrasonic) or EBM (electron beam) melting process. Modern equipment - an industrial 3D metal printer is produced by Markforged, ExOne, AurLabs, HP Metal Jet, Stratasys, MX3D, Digital Metal, 3DSLA.RU (the principle of operation of the equipment can be understood by watching the video reviews). Often, the manufactured part requires additional processing: grinding, joining, shaping. Fitting can be done both manually and using automated technologies, one of which is milling on CNC machines, which can significantly reduce the cost of producing serial parts.
Video
How metal 3D printers work. Overview of SLM and DMLS technologies. additive manufacturing. 3D metal printing.
Metal 3D printing.
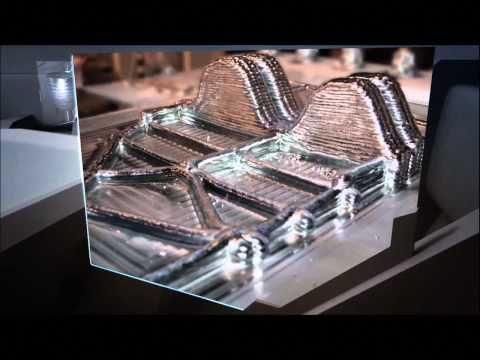
SLM or DMLS: what's the difference?
Hello everyone, Friends! 3DTool is with you!
BLT metal 3D printer catalog
Selective laser melting ( SLM ) and direct metal laser sintering ( DMLS ) are two additive manufacturing processes that belong to the family of 3D printing using the powder layer method. The two technologies have much in common: they both use a laser to selectively melt (or melt) metal powder particles, bonding them together and creating a pattern layer by layer. In addition, the materials used in both processes are metals in granular form.
The differences between SLM and DMLS come down to the basics of the particle bonding process: SLM uses metal powders with a single melting point and completely melts the particles, while in DMLS the powder consists of materials with variable melting points.
Specifically:
SLM produces single metal parts while DMLS produces metal alloy parts.
Both SLM and DMLS technologies are used in industry to create final engineering products. In this article, we will use the term "metal 3D printing" to summarize the 2 technologies. We will also describe the main mechanisms of the manufacturing process that are necessary for engineers to understand the advantages and disadvantages of these technologies.
There are other manufacturing processes for producing dense metal parts, such as electron beam melting (EBM) and ultrasonic additive manufacturing (UAM). Their availability and distribution is rather limited, so they will not be presented in this article.
How 3D printing with SLM or DMLS metal works.
How does metal 3D printing work? The basic manufacturing process for SLM and DMLS is very similar.
1. The printing chamber is first filled with an inert gas (such as argon) to minimize the oxidation of the metal powder. It then heats up to the optimum operating temperature.
2. A layer of powder is spread over the platform, a powerful laser makes passes along a predetermined path in the program, fusing the metal particles together and creating the next layer.
3. When the sintering process is completed, the platform moves down 1 layer. Next, another thin layer of metal powder is applied. The process is repeated until the entire model is printed.
When the printing process is completed, the metal powder already has strong bonds in the structure. Unlike the SLS process, parts are attached to the platform via support structures. The support in metal 3D printing is created from the same material as the base part. This condition is necessary to reduce deformations that may occur due to high processing temperatures.
When the 3D printer's chamber cools down to room temperature, excess powder is removed manually, such as with a brush. The parts are then typically heat treated while they are still attached to the platform. This is done to relieve any residual stresses. They can then be further processed. The removal of the part from the platform occurs by means of sawing.
Scheme of operation of a 3D printer for metal.
In SLM and DMLS, almost all process parameters are set by the manufacturer. The layer height used in metal 3D printing varies from 20 to 50 microns and depends on the properties of the metal powder (fluidity, particle size distribution, shape, etc.).
The basic size of the print area on metal 3D printers is 200 x 150 x 150 mm, but there are also larger sizes of the working area. Printing accuracy is from 50 - 100 microns. As of 2020, metal 3D printers start at $150,000. For example, our company offers 3D metal printers from BLT.
Metal 3D printers can be used for small batch production, but the 3D printing capabilities of such systems are more like those of mass production on FDM or SLA machines.
The metal powder in SLM and DMLS is recyclable: typically less than 5% is consumed. After each impression, the unused powder is collected and sieved, and then topped up with fresh material to the level required for the next production.
Waste in metal printing, are supports (support structures, without which it will not be possible to achieve a successful result). With too much support on the manufactured parts, the cost of the entire production will increase accordingly.
Adhesion between coats.
3D metal printing on BLT 3D printers
SLM and DMLS metal parts have almost isotropic mechanical and thermal properties. They are hard and have very little internal porosity (less than 0.2% in 3D printed condition and virtually non-existent after processing).
Metal printed parts have higher strength and hardness and are often more flexible than traditionally made parts. However, such metal becomes “tired” faster.
3D model support structure and part orientation on the work platform.
Support structures are always required when printing with metal, due to the very high processing temperatures. They are usually built using a lattice pattern.
Supports in metal 3D printing perform 3 functions:
• They form the basis for creating the first layer of the part.
• They secure the part to the platform and prevent it from deforming.
• They act as a heat sink, removing heat from the model.
Parts are often oriented at an angle. However, this will increase the amount of support required, the printing time, and ultimately the overall cost.
Deformation can also be minimized with laser sintering templates. This strategy prevents the accumulation of residual stresses in any particular direction and adds a characteristic surface texture to the part.
Since the cost of metal printing is very high, software simulations are often used to predict how a part will behave during processing. These topology optimization algorithms are otherwise used not only to increase mechanical performance and create lightweight parts, but also to minimize the need for supports and the likelihood of part distortion.
Hollow sections and lightweight structures.
An example of printing on a BLT 3D printer
Unlike polymer powder melt processes such as SLS, large hollow sections are not typically used in metal printing as the support would be very difficult to remove, if at all possible.
For internal channels larger than Ø 8 mm, it is recommended to use diamond or teardrop cross-sections instead of round ones, as they do not require the construction of supports. More detailed recommendations on the design of SLM and DMLS can be found in other articles on this topic.
As an alternative to hollow sections, parts can be made with sheath and cores, which in turn are machined using different laser power and pass speeds, resulting in different material properties. The use of sheath and cores is very useful when making parts with a large solid section, as it greatly reduces printing time and reduces the chance of warping.
The use of a lattice structure is a common strategy in metal 3D printing to reduce part weight. Topology optimization algorithms can also help design organic lightweight shapes.
Consumables for 3D metal printing.
SLM and DMLS technologies can produce parts from a wide range of metals and metal alloys, including aluminum, stainless steel, titanium, cobalt, chromium and inconel. These materials meet the needs of most industrial applications, from aerospace to medical applications. Precious metals such as gold, platinum, palladium and silver can also be processed, but their use is of a minor nature and is mainly limited to jewelry making.
The cost of metal powder is very high. For example, a kilogram of 316 stainless steel powder costs approximately $350-$450. For this reason, minimizing part volume and the need for supports is key to maintaining optimal manufacturing cost.
The main advantage of metal 3D printing is its compatibility with high-strength materials such as nickel or cobalt-chromium superalloys, which are very difficult to machine with traditional methods. Significant cost and time savings can be achieved by using metal 3D printing to create a near-clean shape part. Subsequently, such a part can be processed to a very high surface quality.
Metal post-processing.
Various post methods. treatments are used to improve the mechanical properties, accuracy and appearance of metal printed products.
Mandatory post-processing steps include the removal of loose powder and support structures, while heat treatment (heat annealing) is typically used to relieve residual stresses and improve the mechanical properties of the part.
CNC machining can be used for critical features (such as holes or threads). Sandblasting, plating, polishing, and micro-machining can improve the surface quality and fatigue strength of a metal printed part.
Advantages and disadvantages of metal 3D printing.
Pros:
1. Metal 3D printing can be used to produce complex custom parts, with geometries that traditional manufacturing methods cannot provide.
2. Metal 3D printed parts can be optimized to increase their performance with minimal weight.
3. Metal 3D printed parts have excellent physical properties, metal 3D printers can print a wide range of metals and alloys. Includes difficult-to-machine materials and metal superalloys.
Cons:
1. Manufacturing costs associated with metal 3D printing are high. The cost of consumables is from $ 500 per 1 kg.
2. The size of the working area in metal 3D printers is limited.
Conclusions.
• Metal 3D printing is most suitable for complex, one-piece parts that are difficult or very expensive to manufacture using traditional methods, such as CNC.
• Reducing the need for building supports, will significantly reduce the cost of printing with metal.
• 3D printed metal parts have excellent mechanical properties and can be made from a wide range of engineering materials, including superalloys.
And that's all we have! We hope the article was useful to you.
Catalog of 3D printers for metal BLT
You can purchase metal 3d printers, as well as any other 3d printers and CNC machines, by contacting us:
• By email: Sales@3dtool.