What is 3d printing filament made of
What filaments can be used for 3D printing?
David Roberson6 May 2021
Applications
3D printing is a versatile technology. Using it, you can create a wide variety of specialized applications in a wide variety of specialized materials. But before getting started, it’s important to understand what these materials are, what they can do, what they are made of – including plastics, resins, and powders – as well as what results you can expect when using them with your 3D printer.
In this guide, we cover:
What can you do with a 3D printer?
What is 3D printer filament made of?
Printer settings explained
Common 3D printer filaments (PETG, TPU, ABS, PLA)
Metal and wood 3D printing materials
Support materials
Filament, resin, and powder compared
What can you do with a 3D printer?
FFF 3D printing, or fused filament fabrication, is an additive manufacturing process in which thermoplastic material is pushed through a heated nozzle to create objects layer by layer. Key applications for FFF 3D printing include:
Manufacturing aids. With faster lead times than outsourcing and a wide
range of engineering materials, FFF 3D printing is used widely in manufacturing
industries. 3D printers deliver rapid tooling and replacement parts to maintain
maximum uptime and productivity on the production line. And they are used to
flexibly create end-use parts, such as bespoke quality gauges or small batch
first runs, to speed up time to market of a productEnd-use parts. 3D printing can also be used to produce low-volume, customized end-use parts. This offers greater flexibility, enabling businesses to run small batches of parts without the risks involved of manufacturing a larger batch. There’s also scope for "printing on the spot" and creating products for the customer while they wait
Prototyping. Low-cost materials and short lead times make FFF 3D printing ideal for the iterative design process.
3D printed prototypes can be visual – parts that look close to a finished product – or functional – parts that are capable of being tested for technical performance
Education. Affordable and easy-to-use FFF hardware enables a variety of education applications – from engaging younger students with STEAM basics to providing production labs for college and university students to work on engineering projects and develop skills for the modern workplace
A 3D printed end-use part – the nozzle on a movie effects snow machine
A 3D printed prototype – testing a tablet holder device
What is 3D printer filament made of?
The process of creating 3D printing filament is called "compounding". First, raw plastic resin is produced in the form of pellets. These can be mixed with additives to alter the properties.
The mixture is then dried, extruded to the desired width (usually 1.75 or 2.85 mm), and wound on a spool. Once wound, the material is ready to be used in 3D printing.
Settings for 3D printing materials explained
The properties of every material are different. So are the characteristics of every 3D printer on the market – size, enclosure, nozzle type, and many more features will affect how a material prints. The characteristics of your print job will also have an effect, such as your desired print speed or the geometry of your part.
Loading filament on an Ultimaker 3D printer
The next sections of this guide offers basic advice on how to print with some of the most widely used filaments.
Recommended print settings are given as a general guideline for FFF 3D printers and we advise to always check the manufacturer’s recommendations before printing. (If you’re printing with Ultimaker materials, more detailed guidance can be found on our support pages.)
This will help you compare materials and make some choices about which material is best for your chosen application. With a platform like Ultimaker, software comes with preconfigured printing profiles for our printers and materials, with the option to add hundreds more for third-party filaments via our Marketplace. All you need to do is choose your desired speed, quality, or application, and preconfigured profiles take care of the rest.
Ultimaker offers the benefits of a seamless platform, but you can also use third-party materials
What is PETG?
PETG is a 3D printing material that combines the advantages of PLA and ABS filaments. It is tougher than PLA, with high impact strength, mechanical strength, and some flexibility. It also offers temperature, chemical, and wear resistance. When printed, it gives a glossy finish.
In terms of its uses, PETG is a great all-round material to have on hand. Its resistance to wear and harsh environments makes it suitable for creating tools, other end-use parts, and functional prototypes. This versatility makes it easy to scale and standardize across an organization – meaning fewer configuration changeovers and greater productivity.
How to print with PETG
A typical extrusion temperature range for a PETG filament is 225-245 °C. While a heated build plate is not essential for all PETG filaments and printers, it is highly recommended to ensure adhesion and print quality.
What is TPU?
TPU is a semi-flexible material that can be used in a wide variety of engineering applications where performance is more important than aesthetic qualities. TPU is an ideal 3D printing material when durability and flexibility are essential, as it features exceptional wear and tear resistance, and rubber-like flexibility.
You will often see TPU filaments with names that include two letters and a number – for example Ultimaker TPU 95A. This refers to the material’s hardness on a measuring scale known as the Shore scale. So in this case, the filament rates 95 on the Shore A hardness scale.
How to print with TPU
When 3D printing with TPU, most filament manufacturers recommend a nozzle temperature around 220-240 °C. Build plate temperatures can vary, so check the manufacturer’s recommendation. For best adhesion, it is often advised to apply a thin layer of glue to the build plate. A low relative humidity is also recommended to prevent moisture uptake.
If you want to avoid the trial and error that can come with trying to get the right print settings, Ultimaker filaments and those in our Marketplace come with preconfigured printing profiles for Ultimaker printers.
A 3D printed PETG part, showing the smooth and glossy surface finish
TPU's flexibility make it ideal for this pack spinner, which must withstand impact while not damaging products on the line
What is ABS?
ABS is a good choice for creating functional prototypes and end-use parts. It is often one of the first materials people try when they start 3D printing for more technical applications due to its good mechanical and thermal properties.
How to print with ABS
ABS should be printed on a heated build plate. ABS needs higher nozzle temperature than most other filaments, with manufacturers typically recommending between 220-260 °C.
Many ABS filament can be prone to warping when printed, although Ultimaker ABS is specially formulated to minimize this. Additionally, ABS prints best when it is enclosed on all sides, as it can be prone to delamination.
What is PLA?
PLA is one of the most common FFF 3D printing materials. It prints reliably with high dimensional accuracy and a quality surface finish. This makes it an ideal material for a range of visual applications – from detailed prototypes to education models.
How to print with PLA
PLA prints at moderate temperatures, mostly around 190-210 °C. For the build plate, a temperature around 50-60 °C is ideal for heated build plates, but it is also possible to print PLA on a cold build surface.
Click here for a deeper discussion on ABS vs PLA.
A functional part 3D printed with ABS
A visual prototype in two colors, printed in PLA
What's the difference between PLA and PLA+?
Over time, several material products based on PLA have come to the market offering the easy printing experience of PLA filaments combined with additional properties. This is usually done through special additives to create a blend based on PLA.
While some PLA-based filaments do indeed offer extra properties, such as Ultimaker Tough PLA, be sure to do your own research before deciding if a PLA+ filament is right for your needs.
Does the manufacturer promise superior visual quality? Check photographs of their prints to compare results. Does it claim to offer better mechanical properties? Check the material technical data sheets to be sure this claim has been tested.
The chemical composition of a filament should also be made clear in the manufacturer’s data sheets. Checking what a particular PLA+ is made of will also help you understand its true characteristics.
What is metal 3D printer filament?
Metal 3D printing filament is an FFF filament type made of a metal-polymer composite.
Metal 3D printer material can also be made of aluminum alloys, cobalt-chrome superalloys, inconel (nickel alloys), precious metals such as silver or gold, stainless steel, and titanium alloys. These are more commonly used with powder 3D printing techniques.
How to 3D print with metal
There are multiple ways of printing with metal. For FFF, you will need a metal-polymer composite material. Your 3D printer must also have an appropriate build plate with a temperature between 45-60°C, a specialized hardened extruder nozzle (such as steel or ruby), and a cooling fan.
For other 3D printing technologies such as SLM or DMLS, you will use metal powder. The printer’s build chamber will be filled with an inert gas, which reduces oxidation and enables the chamber to reach the desired temperature. Metal powder then is applied to the build plate. A laser scans the component’s cross-section, fusing the metal particles together to create each layer. When the first layer is complete, another layer of metal powder is applied, and the process is repeated. After printing, leftover powder must be disposed of safely.
A metal-polymer composite part, printed with BASF Ultrafuse 316L filament
Wood-based 3D prints used in an architectural model
What is wood 3D printer filament?
Wood 3D printer filament is filament made out of a polymer-wood composite. Typically, PLA is combined with wood fiber, or cork. A variety of wood 3D printing filaments are available, such as those made from bamboo and pine. 3D printing with wood filament results in a final print that looks and feels like wood.
How to 3D print with wood
Wood 3D printer filament can be printed with similar settings to PLA. Note that a higher nozzle temperature can cause the printed wood to appear darker, as this will burn the wood in the filament. A larger nozzle than 0.4mm is also recommended, as this will help prevent clogging. While in theory wood filament should not be as abrasive as a material like carbon or glass fiber, it is still recommended to use an abrasion-resistant nozzle to be safe.
It is also important to note that there are many more types of 3D printer filament than those listed in this blog, such as ASA, Nylon, PP, TPE, PA, and copolyester. Many of these are covered in our other guides, including wear, temperature, and impact resistant materials, plus ESD-safe, flame retardant, and flexible filaments.
In the materials section of our website, you can browse a wide selection of Ultimaker materials and other filaments with specialized properties that are compatible with our printers.
What is support material?
Support materials literally ‘support’ a part during the printing process if its geometry would make it otherwise impossible to print. This support material needs to be removed before the print can be used.
Soluble support materials like PVA and HIPS are dissolvable, which means there is no risk of damaging the part’s surface as can happen when removing supports manually. PVA support material dissolves in water, while HIPS requires D-limonene solvent.
A material like Ultimaker Breakaway is manually removed. If you are in a hurry to start using your print, this is faster than waiting for material to dissolve. You can read more in our complete guide to support materials.
A gearbox printed with dissolvable PVA support material
After the PVA support material has been dissolved
Filament, resin, and powder compared
Materials come in different forms, depending on the 3D printer technology:
Filaments for FFF printers
Resin for SLA (stereolithography) and DLP (direct light processing)
Powder for fusion technologies like SLS (selective laser sintering)
What is a resin 3D printer?
The most common form of resin 3D printer uses SLA technology to create parts. SLA uses UV-curable resin as a raw material. The resin is poured into a glass-bottomed container, into which a build platform is submerged. A UV laser shines UV light on the resin to selectively harden it into a horizontal layer of the CAD data which forms the part. The platform then raises out of the container, allowing the uncured resin to level out. This process is repeated until a complete object is formed.
What is a powder 3D printer?
The most common form of powder 3D printer uses SLS technology to create parts. SLS uses a powdered raw material, typically a polymer. The powder is stored in a container, where a recoating blade distributes a thin layer of material onto the build area. A high-powered laser fuses the small particles of material together, in order to form a single horizontal layer of the CAD data. The container then moves a fraction of a millimeter to start a new layer, and a recoating blade swipes across the build area to deposit a new layer of raw material. Unfused powder is recycled by sieving and mixing the sieved powder with unused powder. The process is repeated until a complete object is formed.
The Ultimaker S5 Material Station stores filament in optimal conditions and automatically loads the next spool
SLS 3D printing involves removal of leftover powder material when a print is finished
You can learn more about FFF, SLA, and SLS 3D printing technologies – and the differences between them – by reading our dedicated blog on the subject.
Want to know more?
We hope you found this guide to the basics of 3D printing materials useful.
Want to see how businesses are using various materials to unlock cost and time savings? Download a free white paper below and discover five key 3D printing applications.
Understand 3D printing's biggest cost-saving opportunities in this guide, including:
• The 5 most popular applications of 3D printing
• How to go to market quicker than your competition
• Proven examples that bring over 90% savings
• And lots more!
Comparison & List of 3D Materials
Image from FlickrBelow you will find information on 16 different types of 3D printing materials. Chances are that even if you are a 3D printing expert you will learn something new in this guide. You can try magnetic, glow-in-the-dark, or even conductive filaments.
Before we get into 3D materials, it helps to look at the 2D printing process we’ve all come to know. All printers need some kind of substance to print with. For 2D printing, we’re most familiar with inkjet printers that use liquid inks. These machines extrude ink through microscopic nozzles onto papers. 2D laser printers also print to papers. Instead of ink, they use a toner cartridge filled with a special type of fine powder and a heated fuser. 2D printing produces two-dimensional, flat, results that have width and height but no depth (thickness). Pigment-based and solid inks are other materials used for printing in 2D. Today, we can also print in 3D with special machines and printing materials.
2D Printing Compared to 3D Printing
There’s a distinct difference between the two technologies. 3D printers build real-world objects, whereas 2D printers publish text and graphics on papers. Before either machine can print, they need computer-generated, digital files. These files tell the machines what to produce and how to print it based on user preferences. Both types of printers use inks, or materials, to carry out the job. That’s pretty much where the familiarities end. 2D printers can’t build layers to produce real-world objects.
One of the most important parts of 3D printing is to use the right kind of material for the job in hand. In this guide we look at the range of 3D materials, also called filaments, a 3D printer uses, starting with the most popular. We’ll also cover their uses along with pros and cons for each type. This will help you to make better informed decisions when buying your 3D printer filaments. Before you print anything in 3D, there are a few basic questions you should ask yourself, the main ones include:
- Strength: How strong does your printed part have to be?
- Flexibility: How flexible does your part need to be?
- Accuracy: How important is precision to your 3D part?
- Special conditions: Any other conditions that apply to your 3D model
These are the 3D printing materials that are covered in this guide:
- ABS Filament
- PLA Filament
- PET Filament
- PETT Filament
- Nylon Filament
- PVA Filament
- Sandstone Filament
- Wood Filament
- Metal Filament
- HIPS Filament
- Magnetic Iron Filament
- Conductive Filament
- Carbon Fiber Filament
- TPE Filament
- Glow in the Dark Filament
- Amphora Filament
3D Filament Defined
3D filaments are special types of plastics called thermoplastics. Once heated to the right temperature, thermoplastics become flexible. It’s this pliability that allows the printer to sculpt the filament to create your shapes before it cools down. In 2017, the two common types of 3D filaments are:
- ABS (Acrylonitrile Butadiene Styrene)
- PLA (Polylactic Acid)
Don’t Miss: Best 3D Printing Filament Brands.
These are not the only 3D filaments available. We’ll look at other types later in the guide. For now we’ll focus on ABS and PLA, and see what makes them such popular choices. For each material we’ll start with a short introduction followed by the average price, print temperature, and applications. At the end of each 3D material we’ll list its pros and cons. Also worth noting is that not all 3D printers can utilize both ABS and PLA. Some can, but not all, so you need to know your 3D printer capabilities as well as the abilities of the 3D filaments.
1. ABS 3D Filament
PRICE STARTING FROM: $20 for 1. 75 mm, 1kg spool
ABS is popular for good reasons. It’s tough, and has impact-resistant properties. It’s this strength and moderate flexibility that makes it such a great choice for printing in 3D. It’s also easy to extrude from the printer’s nozzles, which makes it an easy material to work with.
Don’t Miss: Best ABS Filaments.
ABS print temperature range: 210°C – 250°C (high)
Applications
ABS is a great choice for printing plastic automotive parts, moving parts, musical instruments, kitchen appliances, electronic housings, and various toys, like LEGO. It has other applications too, aside from 3D printing. For example, traditional manufacturers use ABS to make plastic wrap, water bottles, and cups, to name a few uses. Despite its popularity for 3D printing, ABS is not the best filament for most home users. This is because it has a high melting point that needs to print on a heated surface, or bed. A heated printer bed is not something a lot of budget-range 3D printers come equipped with. Printing with ABS also produces unpleasant fumes that can irritate some people. Needless to say, good ventilation is essential. These things combined make ABS a material favored more by professionals than amateur users.
Check Price of ABS Filament on Amazon
The Pros
- A durable, strong 3D filament
- Quite flexible and lightweight
- Cheapest thermoplastic available at the time of writing
- Most favored material among professional 3D printers and keen armatures
The Cons
- ABS is petroleum-based, making it a non-biodegradable material
- Needs a high temperature to reach its melting point
- Creates unpleasant fumes, most notable in poorly ventilated spaces
2. PLA 3D Filament
PRICE STARTING FROM: $20 for 1.75 mm, 1kg spool
PLA (Poly Lactic Acid) is popular for amateurs and professionals alike. It’s a special type of thermoplastic made from organic materials, namely cornstarch and sugarcane. The main benefits of PLA are that it’s safer and easier to use, and with no toxic fumes to worry about. Some users even find the sweet smell of the sugar-based filament pleasant. Compared to ABS, PLA produces 3D parts which are more aesthetically pleasing. This finish is thanks to its unique sheen and smooth appearance.
You might think it sounds like the perfect solution, but there are some drawbacks. For one, the melting point of PLA is much lower than ABS, and that makes it weaker. This matters if you’re printing moving parts or exposing the parts to high temperatures. Both of these things can result in the 3D objects, cracking, warping or even melting. If none of the above applies to you and your 3D projects, then PLA should be your filament of choice. It will award you with superior print details and is also less prone to printing errors during the build process.
Don’t Miss: Best PLA Filaments.
PLA print temperature range: 180°C – 230°C (low)
Applications
PLA has wide-ranging uses. At the professional level, PLA filament uses include medical suturing (stitching). We can also see PLA used for various surgical implants, including surgically implanted pins, rods, screws, and mesh. The applications work thanks to the material’s degradable properties. All the aforementioned 3D printed parts break down in the human body. They can take anywhere between six months to two years, depending on the part and its purpose. At the amateur level, PLA filament is great for producing a whole range of consumer items. Other benefits of PLA are that it prints faster than ABS, and there’s no need for a heated printer bed. The end products are a decent strength, durable, and offer some degree of impact resistance. Aside from 3D printing, other products that use PLA include food packaging, disposable tableware, and diapers, as a few examples.
Check Price of PLA Filament on Amazon
The Pros
- No harmful fumes, produces a sweet aroma when heated
- Easier to work with compared to ABS (great material for beginners)
- Compared to ABS, PLA is less prone to warping
- Available in special effects like glow-in-the-dark colors and translucency
The Cons
- Susceptible to clogging the printer nozzle
- Can attract moisture that makes it potentially brittle and more difficult to print
- Less sturdy overall than ABS
3.
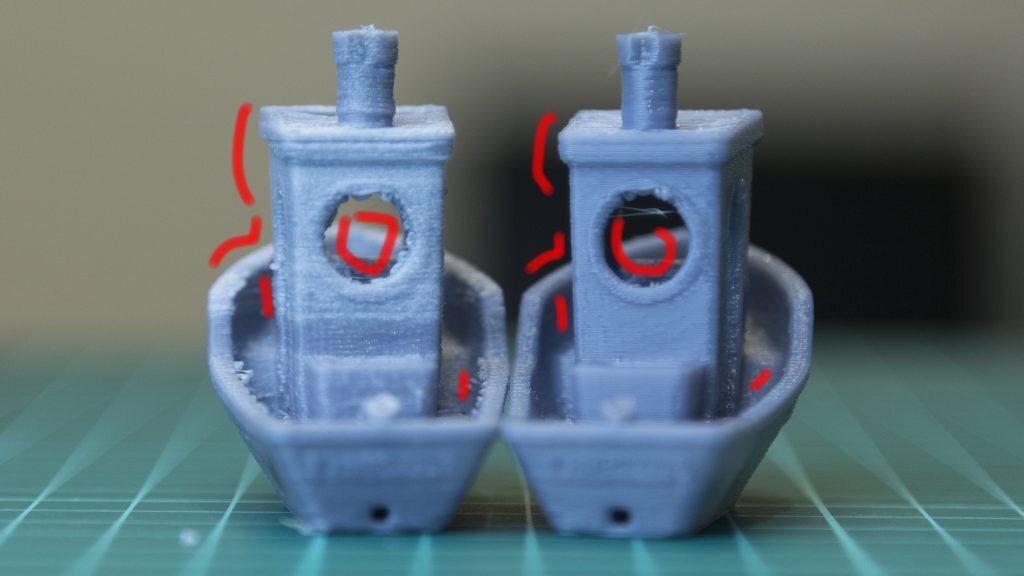
PRICE STARTING FROM: $24.99 for 1.75 mm, 1kg spool
Today, PolyEthylene Terephthalate (PET) is a popular 3D material. Another common use for PET is in everyday plastic bottles. This plastic is both stable and harmless, emits no unpleasant or harmful odors, and is 100% recyclable. In its raw state, the filament has no color and is crystal clear. Once exposed to cold or heat the material quickly changes to a non-transparent state. A more advanced version if PET is a filament called PETG, also marketed as Amphora AM1800.
Don’t Miss: Best PETG Filament.
PETG print temperature range: 210°C – 230°C
Applications
PETT is on a list of FDA approved polymers. This makes it completely ‘food safe’, meaning it’s safe for products like cups, and plates, etc. Needless to say, common applications for PETT filament include food containers and various kitchen utensils.
Check Price of PETG Filament on Amazon
The Pros
- Strong, flexible, and with biocompatibility
- Does not warp
- Does not shrink
- Does not absorb moisture from the air
- Does not degrade in water
- FDA approved, food safe
- Prices for PETT are falling
The Cons
- Not an easy material for beginners to work with
- Nozzle and printer bed temperatures needs fine-tuning for best results
4.

PRICE STARTING FROM: $25.99 for 1.75 mm, 453.5g spool
PETT, whose long name is PolyEthylene Trimethylene Terephthalate, is what’s known as a T-Glase filament. Like PET (one ‘T’), it’s also a popular 3D printer material that’s food-friendly. The filament is non-biodegradable, though it is a recyclable material.
Don’t Miss: Best PETG Filaments.
PETT Print Temperature Range: 210°C – 230°C
Applications:
PETT is another of those FDA-approved polymers. This makes it safe for use with food. The majority of PETT applications are various food containers and other kitchen utensils.
Check Price of PETT Filament on Amazon
The Pros
- Strong and flexible
- Biocompatibility
- Does not warp or shrink during the printing process
- Does not absorb moisture or water from surrounding air
- Does not degrade in water
- FDA approved, food safe
- Impressive in bridging
- Prices for PETT falling
The cons
- Difficult material for beginners to work with
- Printer nozzle bed temperature requires fine tuning for best results
5.
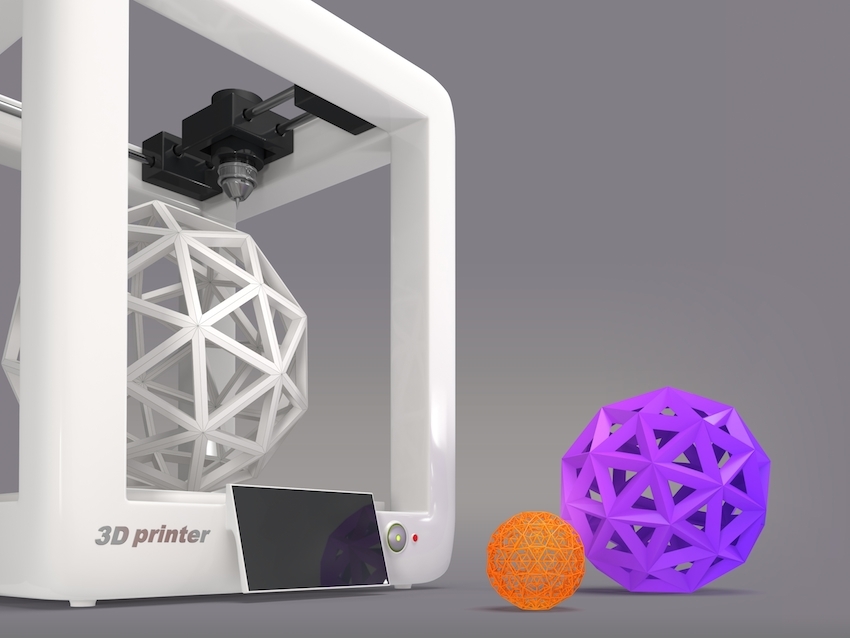
PRICE STARTING FROM: $39.99 for 1.75 mm, 1kg spool
Nylon filament, also called polyamide, is another popular choice. This is a synthetic polymer that’s stronger and more durable than ABS and PLA—and cost-effective. It’s also flexible, light, wear-resistant, and less brittle than both ABS and PLA. There are different kinds of nylon filament available, and what you choose will depend on which one suits your budget and needs. The difference between them is in the filament’s layer bonding abilities, tensile strength, and water absorption. You can also choose nylon filament that has a translucent or opaque finish and reduced shrinkage.
Don’t Miss: Best Nylon Filaments.
Nylon print temperature range: 210°C – 250°C (high)
Applications
Nylon filament is great to use in a whole variety of applications thanks to its strength, flexible properties, and durability. It’s particularly suited for various consumer products, tools, mechanical components, machine parts, structural parts, containers, and a much more.
Check Price of Nylon Filament on Amazon
The Pros
- Strong, durable and flexible
- Less brittle than ABS and PLA
- 100% thermoplastic material
- Filament can be re-melted and used again without any loss of bonding
The Cons
- Needs a high melting temperature
- Breaks down and emits toxic fumes when heated
- Absorbs moisture easily—proper storage is essential
6. PVA Filament
Image from Form FuturaPRICE STARTING FROM: $35.99 for 1.75 mm, 0.5 kg spool
PVA (long name Polyvinyl alcohol) is a good 3D filament that’s typical use is as a support material when printing with ABS or PLA. Support materials are necessary when printing 3D parts with notable overhangs. Without the support, these parts would be impossible to print or perfect. As a support material, PVA works best with printers that have duel extruders. This is a biodegradable, non-toxic material that easily dissolves in tap water. All popular desktop FDM printers can use PVA with a heated build platform as this prevents warping during the build process. For best results as a support material, the print bed temperature should not exceed 200 °C.
PVA print temperature range: 190°C – 220°C (low)
Applications
In 3D printing, PVA works as a support material (see above). Aside from 3D printing, PVA has many other applications. We can find it used as a thickener in paper adhesives, in personal hygiene products, as a mold-release agent, kid’s putty, and freshwater fishing products, to name a few.
Check Price of PVA Filament on Amazon
The Pros
- A biodegradable, non-toxic material
- Water soluble
- Good durability
- Makes otherwise difficult printing easy
The Cons
- Attracts water easily
- Can be difficult to source compared to other materials
- High cost compared to other 3D filaments
7.

PRICE STARTING FROM: $32 for 1.75 mm, 0.25 kg spool
Sandstone filaments offer a unique finish to your 3D printed parts. This is a PLA material that includes a fine chalk powder to produce a stone-like color and texture. It’s also possible to alter the surface characteristics simply by adjusting the printer’s extrusion temperature during the print process. With a little practice, you’ll be able to produce parts that are smooth, rough, or anywhere between the two. 3D sandstone material is a brick filament offered by various suppliers under different product names. The most well-known right now is LayBrick.
Sandstone print temperature range: 165°C – 210°C
Applications
The creative use of 3D sandstone filaments has few limits, though it’s fair to say that it has a pretty niche usage. It’s most popular for things like landscapes and architectural display models.
Check Price of Sandstone Filament on Amazon
The Pros
- Unmistakable sandstone appearance and finish
- No heated bed needed to print
- No warping or shrinking during the cooling process
The Cons
- Not a particularly durable or flexible material
- Parts can be brittle making them more prone to breaking and snapping
8.
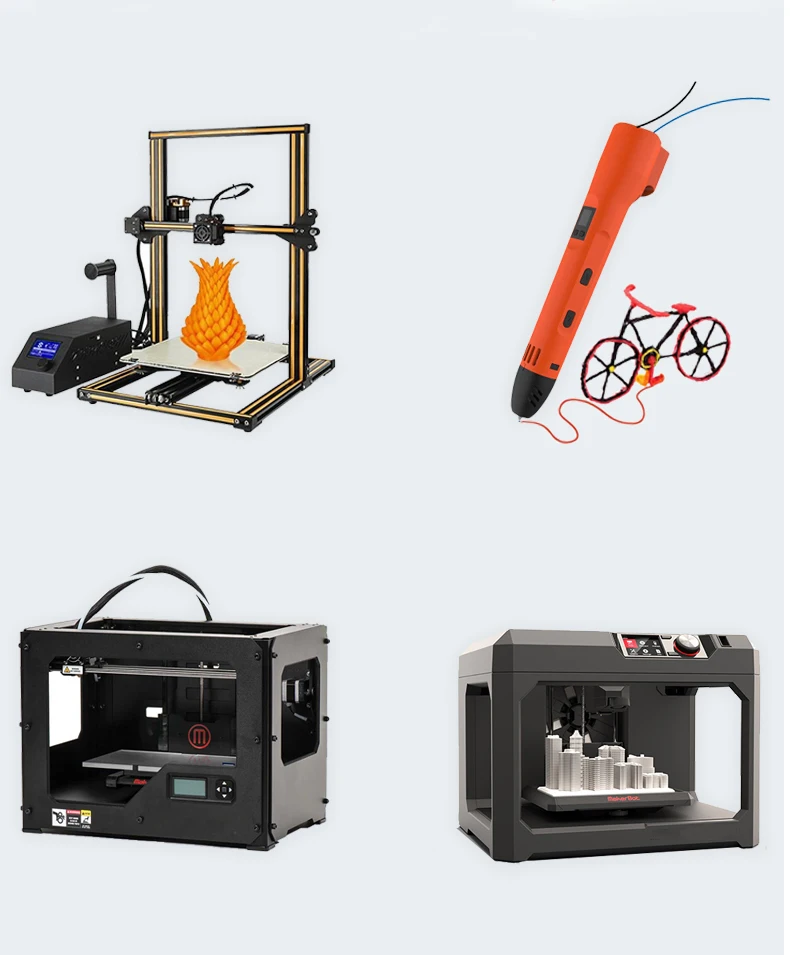
PRICE STARTING FROM: $30 for 1.75 mm, 1kg spool
It seems strange, but yes, 3D wood filaments are very real. It’s a great material for anyone who wants or needs to be more creative with their 3D printed projects. These filaments contain a careful mixture of recycled woods with a special binding polymer. The output model not only looks like real wood, it smells like it too. There’s no shortage of impressive examples online that illustrate the amazing finish wood filaments can produce when printed to perfection.
Wood print temperature range: 200°C – 260°C
Applications
What 3D print enthusiasts use wood filament for has no limits other than their creativity. Use it for décor, ornate boxes, tables and chairs, figurines, and whatever else catches the imagination.
Check Price of Wood Filament on Amazon
The Pros
- Contains actual wood fibers
- Produces unique wood-like objects in various shades and surfaces
- Higher temperatures will produce darker brown shades
- Altering 3D print temperatures stimulates the growth ring effect of trees
- Allows you to easily work with the finished part to achieve the required finish
The Cons
- Weaker, softer material compared to PLA
- Less flexibility and tensile length
- Easily breakable
9.

PRICE STARTING FROM: $29 for 1.75 mm, 1kg spool (prices vary a lot depending on metal)
Metal filaments are in a league of their own—offering some very impressive, unique finishes to 3D printed parts. The materials consist of PLA combined with a higher percentage of fine metallic powders. The 3D printed parts look and feel just as they would if they had been made of 100% metals. Popular choices include aluminum, brass, bronze, copper, and stainless steel. Anyone who wants more of a creative effect can work on the end piece. For example, you can polish the finished part, or tarnish / weather it so that it looks even more genuine. Although they’re not pure 3D metal parts, they’re pretty close to the real thing.
Metal print temperature range: 195°C – 220°C (will vary depending on filament)
Applications
3D metal filament is perfect for hardware products, jewelry items, statues, replicas of artifacts, and much more. What you print with 3D metals depends a lot on the filaments you choose.
Check Price of Metal Filament on Amazon
The Pros
- Extremely durable
- Not soluble
- Unique metallic appearance and finish
- Little to no shrinkage while cooling
- No heated print bed needed
The Cons
- Not easy to print with for the inexperienced
- Need to fine-tune nozzle temperatures
- Need to regulate flow rate
10. HIPS Filament
Image from AdafruitPRICE STARTING FROM: $24.95 for 1.75 mm, 1kg spool
High Impact Polystyrene, HIPS for short, is a bright, white colored 3D biodegradable material. It’s safe to use, meaning it has no harmful effects for users who are in close contact with the filament. It’s safe with pets too. Like PVA, HIPS also works as great secondary (support) material. On its own, it’s tricky to use for creating 3D printed parts, especially with printers that don’t have a heated bed. As a support structure, a colorless solution called liquid hydrocarbon quickly dissolves the filament.
Don’t Miss: Best HIPS Filaments.
HIPS print temperature range: 230°C – 250°C
Applications
For 3D printing, the most common application for HIPS is as a support material for other filaments (see above). Aside from 3D printing, other industries use HIPS because it’s a strong, ridged plastic that they can manipulate to suit their needs. The food industry uses it widely for packaging. Other uses include medicinal trays, signs, all kinds of kid’s toys, and much more.
Check Price of HIPS Filament on Amazon
The Pros
- Acts as an easily removable ABS support material
- When paired with ABS, HIPS is a great dual extrusion support structure
- Non-toxic at close range
The Cons
- Some issues with adhesion and curling
- Not easy to work with without a heated bed
11.
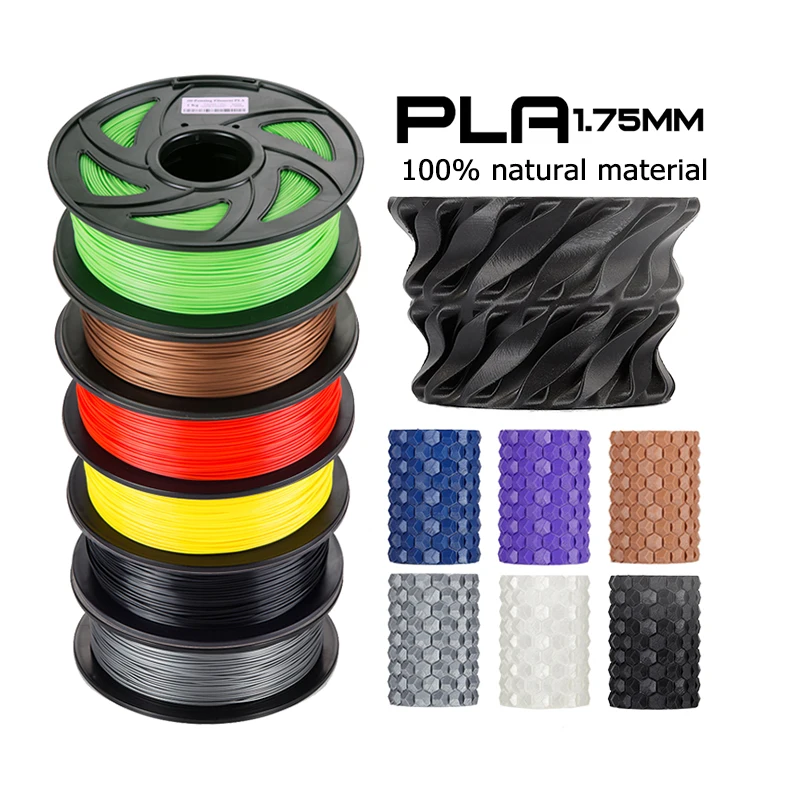
PRICE STARTING FROM: $35 for 1.75 mm, 500 g spool
As the name suggests, magnetic iron PLA filament has magnetic properties. This unique filament is PLA material infused with a powdered iron. It’s these iron particles that give the 3D parts their grainy gunmetal type finish. The objects will also stick to magnets, something that could be useful on various creative projects. It’s a specialist material that few will have a need for, but those who do work with it find PLA iron filament invaluable.
Magnetic iron PLA print temperature range: 195°C – 220°C
Applications
If you want to produce custom made fridge magnets, and other such novelties, magnetic iron PLA is for you. For home users, this is pretty much a novelty material. For more serious uses, magnetic filament is useful for making various DIY projects, sensors, and educational tools, etc.
Check Price of Magnetic Iron Filament on Amazon
The Pros
- Very strong and extremely durable
- Material is not soluble
- Little to no shrinkage during the cooling down process
The Cons
- Nozzle temperature needs fine-tuning
- Inflexible
- Heated bed not needed
- Material is expensive compared to other popular filaments
12.
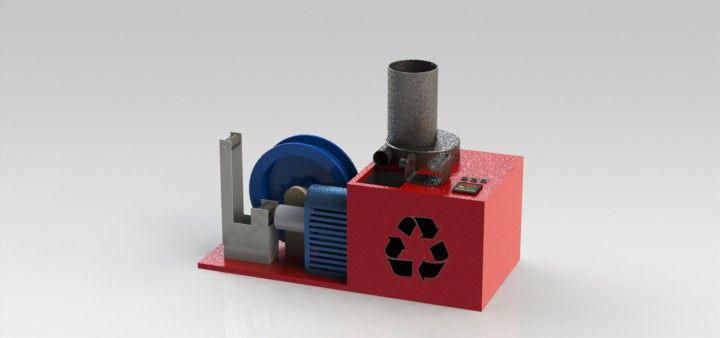
PRICE STARTING FROM: $17.95 for 1.75 mm, 125 g (comes in various weights)
Anyone wanting to broaden their horizons in 3D printing may want to look to conductive PLA 3D printer filament. It’s a special type of 3D material that includes a conductive carbon particulate. Without getting too technical, this means the material is able to print low-voltage electrical circuits. These will typically include sensors and light-emitting diodes (LEDs). When combined with regular PLA filament and a dual-extrusion 3D printer, users can make simple circuit boards direct from the printer’s bed. Note that conductive ABS filament is also available for users who prefer to work with ABS.
Conductive PLA temperature range: 215°C – 230°C
Applications
Conductive PLA filament is perfect for open-source electronics platform Arduino projects. If you want to create circuits, LEDs, sensors, and various low-voltage projects, you’ll want explore this filament.
Check Price of Conductive Filament on Amazon
The Pros
- Users can produce low-voltage electronic circuits
- Not soluble
- Does not need a heated bed, though a heated bed will produce better results
The Cons
- Not very flexible or durable
- Repeated bending may break the material
- Shrinks somewhat during the cooling process
- High cost of filament
13. Carbon Fiber 3D Printer Filament
Image from Color FabbPRICE STARTING FROM: $29.99 for 1.75 mm, 500 g spool
Carbon Fiber PLA is an impressive 3D filament. The material contains tiny strands of carbon fiber which results in a material that has an excellent structure. It’s also rigid and has superior layer adhesion. Carbon Fiber PLA shares similar properties with standard PLA but it’s stiffer. It also offers more dimensional stability, which means warp-free printing. The downside to carbon fiber filament is that its abrasive nature speeds up the wear and tear of printer nozzles, especially those made of brass.
Don’t Miss: Best Carbon Fiber Filaments.
Carbon fiber print temperature range: 190°C – 230°C
Applications
Carbon fiber PLA filament is a great choice for producing high quality and strong objects. This includes items like protective casings, various mechanical parts, and many other high durability uses.
Check Price of Carbon Fiber Filament on Amazon
The Pros
- Prints quality parts
- Soluble and durable
- No heated bed needed
- Little warping and shrinkage during the cooling process
The Cons
- Material contains abrasive strands
- Excessive wear on printer nozzles, especially brass
- Regular users need to invest in harder metals for print nozzles
14. Flexible, TPE Filament
Image from Creative ToolsPRICE STARTING FROM: $31.99 for 1.75 mm, 1kg spool
TPE 3D printer filament is easily the most flexible of all the printer materials. It is ‘super stretchy’ because of the thermoplastic elastomers, or TPE for short. It has such high elasticity properties that it feels like real rubber, easily springing back into shape like an elastic band. TPE is great to use with most FDM 3D printers. If you need to fabricate stretchable 3D parts that can endure more punishment than any regular ABS or PLA, this is your material.
Don’t Miss: Best TPE Filaments.
TPE print temperature range: 225°C – 235°C
Applications
There are wide ranging applications and industries which benefit from TPE filament. We can see it used in household appliances and the automotive sector. It’s also a popular for kid’s toys, wearables, and smartphone cases, etc. For commercial use, TPE is found in medical supplies, weather seals for windows and doors, electrical insulation, and the soles of footwear, to name a few.
Check Price of TPE Filament on Amazon
The Pros
- High elasticity properties and exceptional abrasion-resistance
- Smooth consistent diameter
- Bonds well between layers (vital for high-quality)objects)
- Durable material with little shrinkage during the cooling process
- No heated bed needed
The Cons
- 3D printing with TPE is difficult for the inexperienced
- Print nozzle needs fine-tuning for optimal performance
- Can extrude from nozzle inconsistently
15.

PRICE STARTING FROM: $17.99 for 1.75 mm, 1kg spool
The name needs little introduction as this fun filament does exactly what it says on the label—it glows in the dark. It won’t glow indefinitely though, as the 3D printed object needs exposing to a light source to charge it. Once charged it will emit light in whatever colors you have made your part in. A great use for this material it to decorate children’s bedrooms or to make Halloween themes, and other such creative ideas. It’s a safe, environmentally-friendly filament, making it harmless for everyone to use. One of the major drawbacks is that glow-in-the-dark material is abrasive. The problem with abrasive filaments is that they can quickly wear out nozzles, especially brass. If you plan to use glow-in-the-dark 3D printing material often, be sure to install a hardened steel nozzle.
Glow-in-the-dark print temperature range: 180-240 °C
Applications
Imagination drives many of the uses for this fun material. It’s popular for kid’s toys, wearable gadgets, custom phone cases, and many other novelty items. Some creative artists also find it a great medium to work with for artistic designs. Another, more practical use is for light switches as it makes them easy to find in the dark.
Check Price of Glow in the Dark Filament on Amazon
The Pros
- Environmentally friendly, safe to use, biodegradable
- Low shrinkage during the cooling process
- Durable
- No heated bed needed to print
- Similar to regular PLA, which makes printing easy
The Cons
- Not food safe
16. Amphora 3D Printer Filament
PRICE STARTING FROM: $00 for 1.75 mm, 1kg spool
Amphora is a great filament for anyone who wants to produce objects which are lustrous, bright, and opaque. The Eastman Chemical Company created this fancy material specifically for 3D printing. Most common thermoplastics have uses other than 3D printing technologies, but not this one.
Amphora print temperature range: 220°C – 250°C
Applications
Amphora is more of a specialist type of lightweight, impact-resistant, 3D printer filament. Common applications include mechanical parts and other objects that need a material that is of excellent strength, highly flexible, and durable.
Check Price of Amphora Filament on Amazon
The Pros
- No notable odors during the printing process
- Strong material with a high melting point (higher than regular PLA)
- Better layer adhesion resulting in an improved finish
- Impressive performance for bridging gaps
- Little to no warping, cleaner overhangs overall
- FDA-approved, making Amphora food safe
The Cons
- Not an easy material to print with
- Printer nozzle and bed need fine tuning for best results
Choosing the Right 3D Printer Filament
This guide gives you a good insight into the different 3D printer filaments on the market. There are others, but the ones listed here are the most widespread, easy-to-source materials at the time of writing. Before you choose the right filament for your next job, you need to check a few boxes. For example, as well as knowing what you intend to build, you also need to understand your printer’s capabilities. Not all 3D printers are able of printing in all 3D materials.
You also need to prepare for trial and error if you plan to experiment with some of the more tricky filaments. Another consideration is the diameter of the filament, either 1.75mm or 3mm. If you’re unsure, always opt for 1.75mm as it’s easier to work with. 3D filament storage is another crucial area to think about. These plastics can absorb moisture from the air which can mess with the printing process. When not in use, a good way to store your 3D filament is to use vacuum bags that have a double zipper line for better, airtight sealing.
And finally, don’t allow the cheapest of the cheap filaments tempt you as they could prove to be a false economy. Seriously, low-cost, low-grade 3D printing filaments are more likely to contain chemical impurities. These impurities can result in unsatisfactory printed parts and clogged-up printer nozzles.
It might all sound like a lot absorb, but none of this takes long to pick once you start to dabble.
Warning; 3D printers should never be left unattended. They can pose a firesafety hazard.
Threads in 3D printing
Dear friends, welcome!
This article would like to highlight the appearance of threads in printing. I will try to note the main factors influencing the appearance of threads.
1) Idling speed and acceleration. The idle run consists of the following stages - first there is a retract, then the movement of the extruder, then again a retract. The plastic is spontaneously squeezed out precisely during the idle time, forming various kinds of defects. Now imagine an example if the idling takes zero seconds. Under this condition, the plastic will not have time to spontaneously extrude. Therefore, the higher the speed and acceleration, the less time the idling lasts, which means there will be fewer threads. But speed and acceleration are limited by the motor driver, the motors themselves, and the rigidity of the printer frame.
Therefore, you can try to slightly increase the speed and acceleration with each print, but at the same time make sure that the motors do not overheat, otherwise microsteps may be skipped, which will lead to print rejects.
2) Idling path. Different slicers process parts according to different algorithms, which means that the idling trajectory may differ. Some slicers build more rational extruder motion than others. Therefore, you can try to prepare the same part in several slicers and stop at the option that will be more rational.
3) Feeder dependent, i.e. from the plastic supply system. Printers most often have one of two options: "bowden", i.e. far-distance or "direct", this is when the "feeder" is located near the extruder. Under the same printing conditions with direct, there will always be fewer threads than with bowden. But this does not mean that you can always switch from Bowden to Direct. It may also be that your printer will not be able to work with "direct" for one reason or another. The transition to "direct" must be considered with each printer individually.
4) Retract setting, i.e. plastic rollback - its task is to remove the residual pressure in the extruder during idling. Without retract, the threads will appear more intensely. For most printers, the values are as follows - for direct, the range is from 1 to 6mm, and for bowden, from 4 to 12mm. (the amount of retract also depends on the diameter of the nozzle).
5) Plastic quality. If you are constantly printing only budget plastics and are unhappy with the result, then try to buy plastic in a higher price category, and more importantly, with good reviews. And then compare the print quality. But the main thing - from different manufacturers, compare the same types of plastic - you should not compare, for example, ABS from one manufacturer, and PLA from another.
6) Plastic drying. By the way, this applies to almost all plastics, not just nylon. If you have unnamed or cheap plastic in your hands, it is recommended to dry it after opening it, because. it is not known whether the plastic was dried before packaging.
7) Nozzle diameter. The larger the diameter, the more plastic will spontaneously squeeze out during idling. There is nothing you can do about it, it just needs to be taken into account when choosing a nozzle diameter.
8) Extruder temperature. If you heat the extruder to the upper limit of the recommended range (indicated on the plastic that is being printed), then the fluidity of the plastic will be higher, and it will be more easily extruded from the nozzle. Plastic manufacturers give a temperature range for a reason. If you set the print speed to high, then the extruder temperature should be in the upper limit of the range. But if the print speed is low, then there is no need to heat up the extruder much, otherwise filaments may appear due to overheating of the plastic.
Therefore, you can try to reduce the temperature of the extruder as follows - during printing, every couple of minutes, reduce the temperature by 5 degrees over and over and watch the print closely. If the threads disappear, remember the temperature and stick to it. But if the temperature is greatly lowered, then the plastic will not be able to extrude at all. Don't overdo it.
9) Dependence of temperature on the type of extruder. There are many different models of extruders. For example, consider the E3D V6 and E3D V6 Volcano extruder. The E3D V6 Volcano has an extended nozzle and an extended aluminum block. And this means that the zone where the plastic is in the molten state is larger, so it can push through a larger volume of plastic per unit of time. As a result, this extruder will be able to print at higher speeds than the regular E3D V6. But here you need to understand the following - if you have a "powerful" extruder, and you print at low speeds, then the plastic will overheat, which will lead to the appearance of threads. Therefore, for powerful extruders, it is better to set the temperature in the lower limit of the recommended range. And on the contrary - for an extruder that cannot heat up a large amount of plastic, the temperature should be kept in the middle or at the upper limit of the recommended one.
The conclusion here is the following - for different models of extruders, different printing temperatures are needed.
10) Free travel distance. If you are printing multiple parts at once, try to space them closely to reduce the dry travel distance. Well, if a solid part is printed, with individual elements at a great distance from each other, in this case, you can try to change the location of the part in space so that there are fewer idle moves.
11) File analysis before printing. When your G-code is ready, do not be lazy and meticulously analyze it before printing, because. at the verification stage, you can detect unwanted elements that can create various kinds of defects, including the appearance of threads. By the way, in whatever slicer I prepare the file, I almost always check the finished code with the help of “Repetier-Host”, because it shows all the movements that can lead to certain defects.
12) Plastic type. All plastics have both strengths and weaknesses. For example, PETG plastic has a high tendency to filament. ABS, on the other hand, has a low predisposition to threads, but it will have to concentrate on the problem of shrinkage and a low degree of sintering of the layers.
Therefore, before printing, familiarize yourself with the pros and cons of the plastic with which you plan to print.
13) Using the "Lift Z" function. When enabled, a gap will be created between the extruder and the printed part. It is needed so that during idle the extruder does not cling to the outer walls of the part. This feature can significantly reduce the number of threads. But it should be used if the printer has a powerful driver and a motor along the Z axis, as well as a screw with a thread pitch of at least 8mm. This is necessary to achieve high speed and acceleration on the Z axis. Well, if you try to use this function at low speeds, the problem will only get worse and there will be more threads, because. idle time, taking into account "Lift Z", will increase significantly. The idling time with the "Lift Z" function consists of: movement along the Z axis + retraction + idling + retract + movement along the Z axis.
Therefore, you can try to experiment with this function and see the result.
14) Problems with the extruder. Imagine a situation where you put a large retract, but a large plug of melted plastic formed in the thermal barrier between the nozzle and the Teflon tube. In such a situation, no matter how big you put the retract, this plug will not disappear, but will remain in its place. And, therefore, the retract will not be able to completely relieve the pressure in the system. Therefore, keep your extruder clean and in good working order.
15) Problem with the driver on the motor in the feed system (motor on the feeder). It's a rare phenomenon, but it's still there. I've run into a problem where the driver only spins the motor in one direction, regardless of the command, whether it's spinning one way or the other -- the motor only spins in one direction.
And in practice it looks like this: the motor advances the plastic during printing, and at the moment of idling, when a retraction should occur, the motor sharply squeezes out additional plastic (because the driver rotates the motor in only one direction).
As a result, although this phenomenon is rare, it still took place in my practice.
Thank you for your attention, I hope the material was useful, I wish you all the best!
plastic bottle filament, how to make filament
By making filament for 3D printing by yourself, the user can save a lot of money spent on consumables. Plastic filament for printing can be made from PET bottles. Consider which bottles are suitable for this, the procedure for manufacturing a filament, as well as the advantages and disadvantages of this method.
Can plastic for a 3D printer be made from PET bottles?
When making filament for 3D printing, the following types of PET bottles are recommended:
- Blue. Such bottles have the hardest plastic, but when melted, it will be the most fluid of all.
- White and green. The plastic of these bottles is softer than that of the blue ones. In molten form, the material is thicker.
- Brown. These bottles have the softest plastic. When molten, it is highly viscous (similar to ABS filament).
How to make DIY thread and print with plastic bottles?
Preparatory work
Bottles must be unraveled into ribbons before production starts.
Soft bottles have a thinner plastic, so it is better to break them into strips of 10 mm.
Containers with medium hard or harder plastic material can be cut into thin strips, about 7 mm thick.
PET bottle 3D printer filament tools
To create a filament from PET bottles, you will need the following tools:
- utility knife or bottle cutter;
Important! When choosing a bottle cutter, you need to pay attention to the accuracy of cutting plastic. The width of different cut strips should not differ by more than 0.1 mm.
- oven;
- plastic crusher;
- homemade vertical extruder - it has a metal pipe with a drill screw that rotates with a stepper motor, and a nozzle with two heaters from a 3D printer;
- rotary table;
- large basin;
- cold water.
Step-by-step instructions
Production of PET bottle filament for 3D printing is carried out in the following order:
- Cut plastic bottles must be melted in an oven at 180 °C.
The melting time depends on the number of bottles.
Help. It takes approximately 40 minutes to melt 10 plastic bottles.
- After melting, the plastic must be completely cool. All excess moisture will evaporate from the material, and it will crystallize. In appearance, the polymer resembles glass.
- The cooled material must be ground in a crusher to a finer fraction.
- The crushed plastic is then fed into the vertical extruder. The rotating screw moves the ground polymer to the bottom of the device to the nozzle with heaters. The plastic starts to melt.
- Molten PET exits the nozzle into a bowl of cold water placed on the turntable. The rotation of the table will prevent sticking of the material. The thread must be cooled as quickly as possible so that it becomes flexible and transparent. In this case, it can be used for 3D printing.
- Let the homemade filament dry well before printing.
Since in the presence of a large amount of moisture, a thread of molten plastic will exit the extruder in the form of foam. It is recommended to dry the skeins of thread in a closed container with silica gel at a temperature of 50–60 °C. To do this, you can use the oven or simply place the container on the radiator.
There are a few things to keep in mind when using ready-made 3D filament on your printer:
- The product must be printed on a cold table, the temperature of which does not exceed 35 °C. This limitation of the temperature regime is due to the fact that the plastic must quickly cool down to a temperature below 70 ° C. Otherwise, the material may almost completely lose its strength properties.
- Extruder temperature should be around 265°C. But it may differ depending on the printing speed and the type of plastic from which the filament is made.
- If the feed mechanism of the 3D printer is made of brass, then it is better to put a thin-walled rubber hose on the roller.
Learn more