3D printer organization
3D printed workshop equipment: organizing your stuff
Welcome to the first part of our series on 3D printed workshop equipment. Today we will focus on tidying up our man caves (or woman caves ;-)) with the help of 3D printing.
Actually, your workshop doesn’t really have to look like a cave anymore nowadays. In DIY stores, you can find a neat selection of holders, organizers, racks, and containers. However, chances are you might want to opt for 3D printing, even though it will always be more expensive and time-consuming than buying ready-made stuff.
The customizing and personalizing aspects might be well worth it – pick your favorite color, match the style of organizers you already have, and tailor everything to utilize all the available space…which is somehow never large enough.
Having everything in boxes or drawers is tidy and makes the dusting much easier, however, searching for the right tool in closed containers is time-consuming and distracting.
We really recommend having everything readily accessible, with each thing in its permanent place, preferably right in front of your eyes. Some sort of a wall-mounted storage system is ideal for this.
Mounting all the racks and holders directly on the wall is not very practical. Instead, you should screw or glue them to a desk and then attach the whole desk to the wall. It’s up to you whether you want to use plywood, chipboard, or solid wood.
Another option is a pegboard: a perforated panel with standardized holes. Again, there are various materials: metal, plastic, or hardboard.
There are various types of pegboards with different shapes, sizes, and spacing of the holes. If you want to use downloaded 3D models, plan ahead and make sure they are going to be compatible.
Where to get the models?Speaking of downloading 3D models, there is a whole category of organizers in the PrusaPrinters database. You will also find links to individual models and collections below.
Another option is modeling the parts of the storage system yourself. It might seem daunting at first, however, it is actually an ideal beginner’s project, and also a very rewarding one. All the boxes, racks, and holders are relatively simple geometrical shapes after all. In fact, practical thinking and patience to measure everything twice are going to be much more important than awesome 3D modeling tricks.
We are using the Fusion 360, which we consider a good beginner’s choice: it is very user-friendly for such a sophisticated piece of software.
By the way, consider checking out our article on parametric modeling. Storage systems are a typical application of the parametric approach – it is extremely useful to branch out various types and sizes from a basic model with just a few clicks.
Consider sharing the results of your work with others via PrusaPrinters and enjoy our new system of rewards!
If you don’t feel ready to start from scratch yet, you can begin with remixes and adjustments to existing models (for simple things like deleting pegs, adding holes, etc. , even Tinkercad will do) and slowly work your way through to your own creations.
Finally, let’s move on to the models for download and/or your inspiration.
Screwdriver holder
This one is designed for a pegboard, but you can easily remove the peg mounts and model (or later drill) holes instead.
Pliers holder
Designed to be mounted on a board. Looks primitive, but there is really not much to improve. Works perfectly with pliers of various shapes and sizes.
Drill holders
Drill holders are especially useful as sifting through a pile of them to find a correct diameter is a major PITA. The holes are marked with numbers – it is just a matter of your discipline returning the drills to their correct places immediately 😉
Various paint holders
Organizing your paints is a topic on its own. Few painters and modelers remain faithful to one brand (neither is one brand suitable for all applications), so inevitably, over the years they end up with a motley assortment of oil paint tubes, spray cans, tins, bottles, and pedal bins (or whatever are the Citadel containers properly called ;-)). With 3D printing, you can mix and match your paint rack to accommodate everything efficiently, even if you have only a few pieces of each brand.
The Vallejo (or Vallejo-sized, like AK Interactive, etc.) paint holder comes in various sizes, from 2×3 to 9×6 bottles.
Organizing fasteners
Even though we earlier dismissed boxes and drawers for storing your tools, they are golden for all those nuts, screws, and other small bits. In the link above, there is a whole system of more than 60 models of all sizes that you can stack and attach to each other to completely fill your available storage space.
Here is an interesting organizer, upcycling plastic sides of empty Prusament spools.
By the way, the whole spool is reusable, even the paper tubes!
Last but not least, here is a collection of various small containers.
Our picksThis is a whole system we use in our own modeling workshop. It contains holders for paints, drill bits, small trays, but also less obvious, but useful things like a heat gun holster or a paper towel rack.
And here is another collection of assorted prints we consider interesting and useful.
Stay tuned!We will soon follow up with another article (or two), this time focused on the tools themselves.
In the meantime, please feel free to share your tips and suggestions. Also, you can share photos of your workbench, no matter if it’s neatly organized, or…less so. Let the unofficial quest for the worst place of chaos and despair begin 😉
Happy printing!
3d Printed Organizer - Etsy.de
Etsy is no longer supporting older versions of your web browser in order to ensure that user data remains secure. Please update to the latest version.
Take full advantage of our site features by enabling JavaScript.
Find something memorable, join a community doing good.
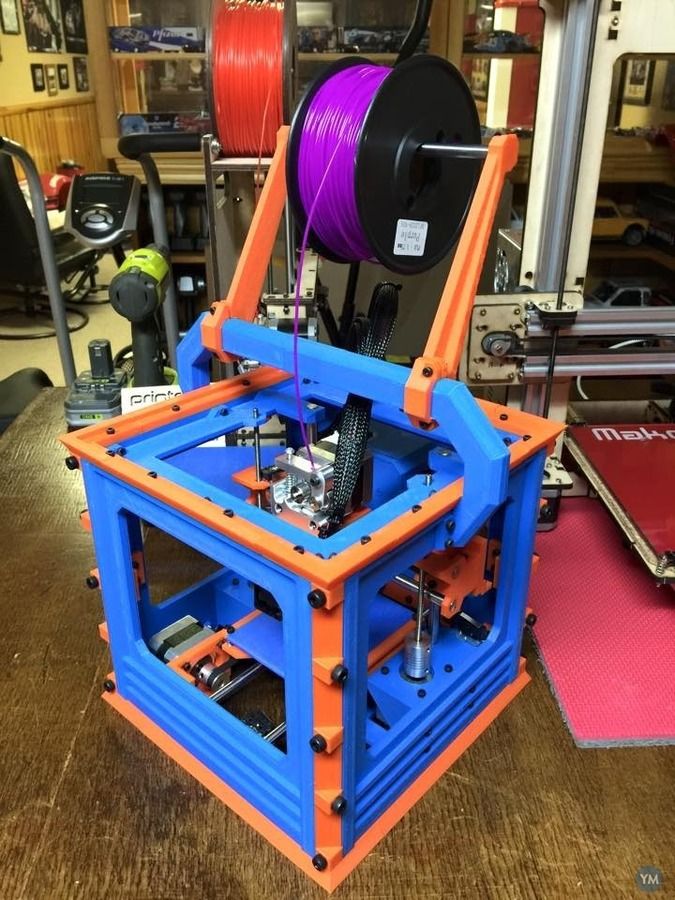
( 1,000+ relevant results, with Ads Sellers looking to grow their business and reach more interested buyers can use Etsy’s advertising platform to promote their items. You’ll see ad results based on factors like relevancy, and the amount sellers pay per click. Learn more. )
Helpful Tips for 3D Printing at Home
You, like many people around the world, may have had to quickly change from working in a workshop or office with many tools at hand to working at home where resources are more limited . During this difficult period, the ability to adapt to new circumstances and challenges helps to reduce production disruptions and avoid disruptions in the organization of the development cycle.
Formlabs desktop stereolithography (SLA) 3D printers are compact in size and can be used from home or outside the office environment. In addition, the ability to use over 30 different materials that mimic everything from silicone and polypropylene to ABS and more increases flexibility, expands the scope and makes it easy to adapt to new tasks as they arise.
Introducing 3D printing technology in-house will help you cut costs and keep your feet on the ground during times of uncertainty, especially if you have previously used or currently use third-party 3D printed models. Our customers are using home 3D printing to reduce costs, improve manufacturing process efficiency, continue developing critical products, and help overcome the COVID-19 crisis..
Dan Kirchgessner, Communications Specialist, and Jake Kapusta, Senior Maintenance Specialist share practical tips for printing at home.
Before the 3D printer is delivered to your home, you need to organize your space and workspace so that you can print, post-process, and finish everything you need. You will need space to house the printer(s), post-processing stations such as Form Wash and Form Cure, workspace to separate and finish parts, and short-term storage space for items such as spare wash solvent, resin reservoirs, cartridges for resins, gloves, post-processing tools, etc.
Alexis Hope, designer and researcher at MIT's Media Lab and MIT's Center for Social Interaction Tools, says that in setting up her home workshop, “getting the printer home was a great incentive to reorganize the workplace. Space is required for flushing and curing systems, as well as space for storing models, so proper organization of space is necessary for productive work. ”
Alexis Hope's home workshop.
Some of the most frequently asked questions about 3D printing at home have to do with environmental factors such as sounds and smells. To account for sensitivity to odors, we advise placing the post-processing station in a well-ventilated area or near an open window. Although the Form 3 is relatively quiet - it produces a noise comparable to that of a microwave oven - you may prefer to place it away from those areas of your home where you don't want to disturb the silence.
Woody Hedberg, Formlabs Print Process Engineer, recently hosted a Form 3L in his apartment for material testing purposes. “As a protective measure, I installed thick cardboard on the floor and walls of the room,” says Hedberg. In addition, for the workplace, he chose a space near an open window and behind a closed door to reduce the penetration of potential smells and sounds.
After preparing the workspace, lay out the items needed for 3D printing, such as wash containers, baskets and bottles, tweezers, spatula, detach tool, wire cutters, disposable nitrile gloves, and any additional tools that you may need during the work 3D printing process.
If you already have a 3D printer, the first thing you should consider is transporting it from your office or workplace to your home. When preparing your Formlabs 3D printer for shipping, first remove the resin cartridge, then remove and clean the platform, and finally remove the resin reservoir and close the lid before placing it in its storage case. Ensure that all accessories containing polymers are securely closed before transport.
Before shipping the Form 3 printer, secure the Light Processing Unit (LPU) with wing screws and latch. Failure to lock the LPU may damage the printer. Contact us if you can't find the screws.
Carefully wrap the printer in protective material and, if possible, place it in the original packaging. Be sure to pack all the accessories you may need for 3D printing and post-processing: Form Wash and Form Cure or post-processing kit and an alternative curing solution and consumables such as resin reservoirs and cartridges, gloves, tools for post-processing, isopropyl alcohol, etc.
After unpacking 3D printing supplies at home and before printing, be sure to check that the printer is level and stable in the new location.
Now that your printer is ready to use at home, there are several ways to improve and streamline your workflow.
Schedule the start and end times for printing to fit your work schedule. This way you can load the printer to the maximum. You can schedule the start of your next print using PreForm's Estimated Print Duration feature. Print time-consuming models while you're away from your workspace so you can print while you're away so you can start the next one when you get back.
Kevin Gauthier, Business Development Specialist at Formlabs, found that when working remotely, his team sent models to each other more often: "Never forget to print an instance of an object for yourself so you can refer to it later."
Kevin Gauthier's home workspace.
Continuing the same line, Hedberg suggests documenting and photographing every 3D printed model in detail, especially if your storage space is limited. “Now that we are working remotely, we need a proper documentation system. This does not mean that every 3D printed model should be saved, but carefully documenting the printed models and keeping records for my colleagues, yes,” he says.
Use the Dashboard to monitor the printing process in real time, as well as tank usage and resin consumption. You'll also be able to track quality prints and scrap rates so you know which designs are the best and use them for future iterations.
“Do all the design work you can and prioritize critical physical prototyping tasks for different teams,” says Zach Frew, Formlabs Technical Specialist. Frew says you need to prioritize these tasks, especially when work resources are limited, and share them with your team members.
Follow safety guidelines when using Formlabs products. Handle IPS with nitrile gloves in a well-ventilated area. Keep the IPS away from heat, sparks and open flames. Isopropyl alcohol evaporates quickly, so keep containers covered if possible. For detailed safety information, contact the manufacturer or supplier of this chemical.
As Formlabs Materials Expert Zak Zguris says, “You have to practice good chemical hygiene. Keep everything clean. Wipe up any drops or spilled liquids immediately. To avoid sticky residue, use acetone or isopropyl alcohol. When washing in the IRS, ventilation of the working space with fresh air should be provided. The cabinet is not at all suitable for the active use of a 3D printer or a washing station in an IRS.”
Always wear gloves to protect your skin when handling resin cartridges and containers. Store ink cartridges upright, out of direct sunlight, in a well-ventilated area. Close the cartridge outlet cap to prevent resin leakage.
Liquid or partially cured polymers must not be poured down the drain or disposed of with household waste. Do not pour isopropyl alcohol (IPA) with the polymer dissolved in it down the drain or dispose of it with household waste. All solvents and polymers should, as always, be disposed of in accordance with local regulations and the supplier's MSP. More information about security measures can be found on our technical support website.
Do you have any helpful tips or advice that you could share based on your experience of transitioning to working from home? We'd love to hear about them. We invite you to share them on social media with the tag @formlabs or #EngineeringFromHome or by commenting on our forums.
All about 3D printing. additive manufacturing. Basic concepts.
- 1 Technology
- 2 Terminology
- 3 Fundamentals
- 4 Print Technologies
- 5 3D printers
- 6 Application
- 7 Domestic and hobby use
- 8 Clothing
- 9 3D bioprinting
- 10 3D printing of implants and medical devices
- 11 3D printing services
- 12 Research into new applications
- 13 Intellectual property
- 14 Influence of 3D printing
- 15 Space research
- 16 Social change
- 17 Firearms
Technology
Charles Hull - the father of modern 3D printing
3D printing is based on the concept of building an object in successive layers that display the contours of the model. In fact, 3D printing is the complete opposite of traditional mechanical production and processing methods such as milling or cutting, where the appearance of the product is formed by removing excess material (so-called "subtractive manufacturing").
3D printers are computer-controlled machines that build parts in an additive way. Although 3D printing technology appeared in the 80s of the last century, 3D printers were widely used commercially only in the early 2010s. The first viable 3D printer was created by Charles Hull, one of the founders of 3D Systems Corporation. At the beginning of the 21st century, there was a significant increase in sales, which led to a sharp drop in the cost of devices. According to the consulting firm Wohlers Associates, the global market for 3D printers and related services reached $2.2 billion in 2012, growing by 29%.% compared to 2011.
3D printing technologies are used for prototyping and distributed manufacturing in architecture, construction, industrial design, automotive, aerospace, military, engineering and medical industries, bioengineering (to create artificial fabrics), fashion and footwear, jewelry, education, geographic information systems, food industry and many other areas. According to research, open source home 3D printers will allow you to win back the capital costs of your own purchase through the economy of household production of items.
Terminology
Additive manufacturing involves the construction of objects by adding the necessary material, and not by removing excess, as is the case with subtractive methods
The term "additive manufacturing" refers to the technology of creating objects by applying successive layers material. Models made using the additive method can be used at any stage of production - both for the production of prototypes (so-called rapid prototyping) and as finished products themselves (so-called rapid production).
In manufacturing, especially machining, the term "subtractive" implies more traditional methods and is a retronym coined in recent years to distinguish between traditional methods and new additive methods. Although traditional manufacturing has used essentially "additive" methods for centuries (such as riveting, welding, and screwing), they lack a 3D information technology component. Machining, on the other hand, (the production of parts of an exact shape), as a rule, is based on subtractive methods - filing, milling, drilling and grinding.
The term "stereolithography" was defined by Charles Hull in a 1984 patent as "a system for generating three-dimensional objects by layering".
Fundamentals
3D printed models
3D models are created by hand-held computer graphic design or 3D scanning. Hand modeling, or the preparation of geometric data for the creation of 3D computer graphics, is somewhat like sculpture. 3D scanning is the automatic collection and analysis of data from a real object, namely shape, color and other characteristics, with subsequent conversion into a digital three-dimensional model.
Both manual and automatic creation of 3D printed models can be difficult for the average user. In this regard, 3D printed marketplaces have become widespread in recent years. Some of the more popular examples include Shapeways, Thingiverse, and Threeding.
3D printing
The following digital models are used as drawings for 3D printed objects , powder, paper or sheet material, building a 3D model from a series of cross sections. These layers, corresponding to virtual cross-sections in the CAD model, are connected or fused together to create an object of a given shape. The main advantage of this method is the ability to create geometric shapes of almost unlimited complexity.
"Resolution" of the printer means the thickness of the applied layers (Z axis) and the accuracy of positioning the print head in the horizontal plane (along the X and Y axes). Resolution is measured in DPI (dots per inch) or micrometers (the obsolete term is "micron"). Typical layer thicknesses are 100µm (250 DPI), although some devices like the Objet Connex and 3D Systems ProJet are capable of printing layers as thin as 16µm (1600 DPI). The resolution on the X and Y axes is similar to that of conventional 2D laser printers. A typical particle size is about 50-100µm (510 to 250 DPI) in diameter.
One of the methods for obtaining a digital model is 3D scanning. Pictured here is a MakerBot Digitizer
3D Scanner Building a model using modern technology can take hours to days, depending on the method used and the size and complexity of the model. Industrial additive systems can typically reduce the time to a few hours, but it all depends on the type of plant, as well as the size and number of models produced at the same time.
Traditional manufacturing methods such as injection molding can be less expensive when producing large batches of polymer products, but additive manufacturing has advantages in small batch production, allowing for higher production rates and design flexibility, along with increased cost per unit produced. In addition, desktop 3D printers allow designers and developers to create concept models and prototypes without leaving the office.
Machining
FDM Type 3D Printers
Although the resolution of the printers is sufficient for most projects, printing slightly oversized objects and then subtractively machining them with high precision tools allows you to create models of increased accuracy.
The LUMEX Avance-25 is an example of devices with a similar combined manufacturing and processing method. Some additive manufacturing methods allow for the use of multiple materials, as well as different colors, within a single production run. Many of the 3D printers use "supports" or "supports" during printing. Supports are needed to build model fragments that are not in contact with the underlying layers or the working platform. The supports themselves are not part of the given model, and upon completion of printing, they either break off (in the case of using the same material as for printing the model itself), or dissolve (usually in water or acetone - depending on the material used to create the supports). ).
Printing technologies
Since the late 1970s, several 3D printing methods have come into being. The first printers were large, expensive and very limited.
Completed skull with supports not yet removed
A wide variety of additive manufacturing methods are now available. The main differences are in the layering method and consumables used. Some methods rely on melting or softening materials to create layers: these include selective laser sintering (SLS), selective laser melting (SLM), direct metal laser sintering (DMLS), fusing deposition printing (FDM or FFF). Another trend has been the production of solid models by polymerization of liquid materials, known as stereolithography (SLA).
In the case of lamination of sheet materials (LOM), thin layers of material are cut to the required contour, and then joined into a single whole. Paper, polymers and metals can be used as LOM materials. Each of these methods has its own advantages and disadvantages, which is why some companies offer a choice of consumables for building a model - polymer or powder. LOM printers often use regular office paper to build durable prototypes. The key points when choosing the right device are the speed of printing, the price of a 3D printer, the cost of printed prototypes, as well as the cost and range of compatible consumables.
Printers that produce full-fledged metal models are quite expensive, but it is possible to use less expensive devices for the production of molds and subsequent casting of metal parts.
The main methods of additive manufacturing are presented in the table:
| ||
Method | Technology | Materials used |
Extrusion | Fused deposition modeling (FDM or FFF) | Thermoplastics (such as polylactide (PLA), acrylonitrile butadiene styrene (ABS), etc.![]() |
Wire | Manufacture of arbitrary shapes by electron beam fusing (EBFȝ) | Virtually all metal alloys |
Powder | Direct Metal Laser Sintering (DMLS) | Virtually all metal alloys |
Electron Beam Melting (EBM) | Titanium alloys | |
Selective laser melting (SLM) | Titanium alloys, cobalt-chromium alloys, stainless steel, aluminum | |
Selective heat sintering (SHS) | Powder thermoplastics | |
Selective laser sintering (SLS) | Thermoplastics, metal powders, ceramic powders | |
Inkjet | 3D Inkjet(3DP) | Gypsum, plastics, metal powders, sand mixtures |
Lamination | Lamination Object Manufacturing (LOM) | Paper, metal foil, plastic film |
Polymerization | Stereolithography (SLA) | Photopolymers |
Digital LED Projection (DLP) | Photopolymers |
Extrusion Printing
Fused Deposition Modeling (FDM/FFF) was developed by S. Scott Trump in the late 1980s and commercialized in the 1990s by Stratasys, a company of which Trump is credited as a founding member. Due to the expiration of the patent, there is a large community of open source 3D printer developers as well as commercial organizations using the technology. As a consequence, the cost of devices has decreased by two orders of magnitude since the invention of the technology.
3D printers range from simple do-it-yourself printers to plastic...
Fusion printing process involves the creation of layers by extrusion of a fast-curing material in the form of microdrops or thin jets. Typically, consumable material (such as thermoplastic) comes in the form of spools from which the material is fed into a printhead called an "extruder". The extruder heats the material to its melting temperature, followed by extrusion of the molten mass through a nozzle. The extruder itself is driven by stepper motors or servomotors to position the printhead in three planes. The movement of the extruder is controlled by a manufacturing software (CAM) linked to a microcontroller.
A variety of polymers are used as consumables, including acrylonitrile butadiene styrene (ABS), polycarbonate (PC), polylactide (PLA), high pressure polyethylene (HDPE), polycarbonate-ABS blends, polyphenylene sulfone (PPSU), etc. Typically, polymer supplied in the form of a filler made of pure plastic. There are several projects in the 3D printing enthusiast community that aim to recycle used plastic into materials for 3D printing. The projects are based on the production of consumables using shredders and melters.
FDM/FFF technology has certain limitations on the complexity of the generated geometric shapes. For example, the creation of suspended structures (such as stalactites) is impossible by itself, due to the lack of necessary support. This limitation is compensated by the creation of temporary support structures that are removed after printing is completed.
Powder print
One of the additive manufacturing methods is selective sintering of powder materials. Model layers are drawn (sintered) in a thin layer of powdered material, after which the work platform is lowered and a new layer of powder is applied. The process is repeated until a complete model is obtained. The unused material remains in the working chamber and serves to support the overhanging layers without requiring the creation of special supports.
The most common methods are based on laser sintering: selective laser sintering (SLS) for working with metals and polymers (e.g. polyamide (PA), glass fiber reinforced polyamide (PA-GF), glass fiber (GF), polyetheretherketone) (PEEK), polystyrene (PS), alumide, carbon fiber reinforced polyamide (Carbonmide), elastomers) and direct metal laser sintering (DMLS).
... to expensive industrial plants that work with metals
Selective Laser Sintering (SLS) was developed and patented by Carl Deckard and Joseph Beeman of the University of Texas at Austin in the mid-1080s under the auspices of the Defense Advanced Research Projects Agency (DARPA). A similar method was patented by R. F. Householder in 1979, but has not been commercialized.
Selective laser melting (SLM) is characterized by the fact that it does not sinter, but actually melts the powder at the points of contact with a powerful laser beam, allowing you to create high-density materials that are similar in terms of mechanical characteristics to products made by traditional methods.
Electron beam melting (EBM) is a similar method for the additive manufacturing of metal parts (eg titanium alloys) but using electron beams instead of lasers. EBM is based on melting metal powders layer by layer in a vacuum chamber. In contrast to sintering at temperatures below melting thresholds, models made by electron beam melting are characterized by solidity with a corresponding high strength.
Finally, there is the 3D inkjet printing method. In this case, a binder is applied to thin layers of powder (gypsum or plastic) in accordance with the contours of successive layers of the digital model. The process is repeated until the finished model is obtained. The technology provides a wide range of applications, including the creation of color models, suspended structures, the use of elastomers. The design of models can be strengthened by subsequent impregnation with wax or polymers.
Lamination
FDM 3D printers are the most popular among hobbyists and enthusiasts
Some printers use paper as a material for building models, thereby reducing the cost of printing. Such devices experienced the peak of popularity in the 1990s. The technology consists in cutting out the layers of the model from paper using a carbon dioxide laser with simultaneous lamination of the contours to form the finished product.
In 2005, Mcor Technologies Ltd developed a variant of the technology that uses plain office paper, a tungsten carbide blade instead of a laser, and selective adhesive application.
There are also device variants that laminate thin metal and plastic sheets.
Photopolymerization
3D printing allows you to create functional monolithic parts of complex geometric shapes, like this jet engine nozzle
Stereolithography technology was patented by Charles Hull in 1986. Photopolymerization is primarily used in stereolithography (SLA) to create solid objects from liquid materials. This method differs significantly from previous attempts, from the sculptural portraits of François Willem (1830-1905) to photopolymerization by the Matsubara method (1974).
The Digital Projection Method (DLP) uses liquid photopolymer resins that are cured by exposure to ultraviolet light emitted from digital projectors in a coated working chamber. After the material has hardened, the working platform is immersed to a depth equal to the thickness of one layer, and the liquid polymer is irradiated again. The procedure is repeated until the completion of the model building. An example of a rapid prototyping system using digital LED projectors is the EnvisionTEC Perfactory.
Inkjet printers (eg Objet PolyJet) spray thin layers (16-30µm) of photopolymer onto the build platform until a complete model is obtained. Each layer is irradiated with an ultraviolet beam until hardened. The result is a model ready for immediate use. The gel-like support material used to support the components of geometrically complex models is removed after the model has been handcrafted and washed. The technology allows the use of elastomers.
Ultra-precise detailing of models can be achieved using multiphoton polymerization. This method is reduced to drawing the contours of a three-dimensional object with a focused laser beam. Due to non-linear photoexcitation, the material solidifies only at the focusing points of the laser beam. This method makes it easy to achieve resolutions above 100 µm, as well as build complex structures with moving and interacting parts.
Another popular method is curing with LED projectors or "projection stereolithography".
Projection stereolithography
This method involves dividing a 3D digital model into horizontal layers, converting each layer into a 2D projection similar to photomasks. The 2D images are projected onto successive layers of photopolymer resin that harden according to the projected contours.
In some systems, the projectors are located at the bottom, helping to level the surface of the photopolymer material when the model moves vertically (in this case, the build platform with the applied layers moves up, rather than sinking into the material) and reduces the production cycle to minutes instead of hours.
The technology allows you to create models with layers of several materials with different curing rates.
Some commercial models, such as the Objet Connex, apply resin using small nozzles.
3D printers
Industrial plants
Industrial adoption of additive manufacturing is proceeding at a rapid pace. For example, US-Israeli joint venture Stratasys supplies $2,000 to $500,000 additive manufacturing machines, while General Electric uses high-end machines to produce gas turbine parts.
Home appliances
LOM takes papier-mâché to the next level The development of 3D printers for home use is being pursued by a growing number of companies and enthusiasts. Most of the work is done by amateurs for their own and public needs, with help from the academic community and hackers.
The oldest and longest running project in the desktop 3D printer category is RepRap. The RepRap project aims to create free and open source (FOSH) 3D printers provided under the GNU General Public License. RepRap devices are capable of printing custom-designed plastic components that can be used to build clones of the original device. Individual RepRap devices have been successfully applied to the production of printed circuit boards and metal parts.
Due to open access to drawings of RepRap printers, many of the projects adopt the technical solutions of analogues, thus creating a semblance of an ecosystem consisting mostly of freely modifiable devices. The wide availability of open source designs only encourages variations. On the other hand, there is a significant variation in the level of quality and complexity of both the designs themselves and the devices manufactured on their basis. The rapid development of open source 3D printers is leading to a rise in popularity and the emergence of public and commercial portals (such as Thingiverse or Cubify) offering a variety of printable 3D designs. In addition, the development of technology contributes to the sustainable development of local economies through the possibility of using locally available materials for the production of printers.
Stereolithographic 3D printers are often used in dental prosthetics
The cost of 3D printers has been declining at a significant rate since about 2010: devices that cost $20,000 at the time are now $1,000 or less. Many companies and individual developers are already offering budget RepRap kits under $500. The Fab@Home open source project has led to the development of general purpose printers capable of printing anything that can be squeezed through a nozzle, from chocolate to silicone putty and chemicals.
Printers based on this design have been available as kits since 2012 for about $2,000. Some 3D printers, including the mUVe 3D and Lumifold, are designed to be as affordable as possible from the outset - for example, the Peachy Printer is priced around $100 .
Professional Kickstarter-funded printers often perform well: Rapide 3D printers are quiet and fumes-free at $1499. 3D Doodler's '3D Printing Pen' Raised $2.3M in Kickstarter donations, with a selling price of $99 for the device itself. True, it is difficult to call the 3D Doodler a full-fledged 3D printer.
3D Systems Cube is a popular consumer 3D printer
As prices fall, 3D printers are becoming more attractive for consumer production. In addition, home use of 3D printing technologies can reduce the environmental footprint of industry by reducing the volume of consumables and the energy and fuel costs of transporting materials and goods.
Parallel to the creation of home 3D-printing devices, the development of devices for processing household waste into printed materials, the so-called. Recyclebot. For example, the commercial model Filastrucer was designed to recycle plastic waste (shampoo bottles, milk containers) into inexpensive consumables for RepRap printers. Such methods of household disposal are not only practical, but also have a positive impact on the ecological situation.
The development and customization of RepRap 3D printers has created a new category of semi-professional printers for small businesses. Manufacturers such as Solidoodle, RoBo and RepRapPro offer kits for under $1,000. The accuracy of these devices is between industrial and consumer printers. Recently, high-performance printers using a delta-shaped coordinate system, or the so-called "delta robots", are gaining popularity. Some companies offer software to support printers made by other companies.
Application
Using LED projectors helps reduce the cost of stereolithography printers. In the illustration DLP printer Nova
Three-dimensional printing allows you to equalize the cost of manufacturing one part and mass production, which poses a threat to large-scale economies. The impact of 3D printing may be similar to the introduction of manufacture. In the 1450s, no one could predict the consequences of the printing press, in the 1750s, no one took the steam engine seriously, and transistors 19The 50s seemed like a curious innovation. But the technology continues to evolve and is likely to have an impact on every scientific and industrial branch with which it comes into contact.
The earliest application of additive manufacturing can be considered rapid prototyping, aimed at reducing the development time of new parts and devices compared to earlier subtractive methods (too slow and expensive). The improvement of additive manufacturing technologies leads to their spread in various fields of science and industry. The production of parts previously only available through machining is now possible through additive methods, and at a better price.
Applications include breadboarding, prototyping, molding, architecture, education, mapping, healthcare, retail, etc.
Industrial applications:
Rapid prototyping: Industrial 3D printers have been used for rapid prototyping and research since the early 1980s . As a rule, these are quite large installations using powder metals, sand mixtures, plastics and paper. Such devices are often used by universities and commercial companies.
Advances in rapid prototyping have led to the creation of materials suitable for the production of final products, which in turn has contributed to the development of 3D production of finished products as an alternative to traditional methods. One of the advantages of fast production is the relatively low cost of manufacturing small batches.
Rapid production: Rapid production remains a fairly new technique whose possibilities have not yet been fully explored. Nevertheless, many experts tend to consider rapid production a new level of technology. Some of the most promising areas for rapid prototyping to adapt to rapid manufacturing are selective laser sintering (SLS) and direct metal sintering (DMLS).
Bulk customization: Some companies offer services for customizing objects using simplified software and then creating unique custom 3D models. One of the most popular areas was the manufacture of cell phone cases. In particular, Nokia has made publicly available the designs of its phone cases for user customization and 3D printing.
Mass production: The current low print speed of 3D printers limits their use in mass production. To combat this shortcoming, some FDM devices are equipped with multiple extruders, allowing you to print different colors, different polymers, and even create several models at the same time. In general, this approach increases productivity without requiring the use of multiple printers - a single microcontroller is enough to operate multiple printheads.
Devices with multiple extruders allow the creation of several identical objects from only one digital model, but at the same time allow the use of different materials and colors. The print speed increases in proportion to the number of print heads. In addition, certain energy savings are achieved through the use of a common working chamber, which often requires heating. Together, these two points reduce the cost of the process.
Many printers are equipped with dual printheads, however this configuration is only used for printing single models in different colors and materials.
Consumer and hobby use
Today, consumer 3D printing mainly attracts the attention of enthusiasts and hobbyists, while practical use is rather limited. However, 3D printers have already been used to print working mechanical clocks, woodworking gears, jewelry, and more. Home 3D printing websites often offer designs for hooks, doorknobs, massage tools, and more.
3D printing is also being used in hobby veterinary medicine and zoology – in 2013, a 3D printed prosthesis allowed a duckling to stand up, and hermit crabs love stylish 3D printed shells. 3D printers are widely used for the domestic production of jewelry - necklaces, rings, handbags, etc.
The Fab@Home open project aims to develop general purpose home printers. The devices have been tested in research environments using the latest 3D printing technologies for the production of chemical compounds. The printer can print any material suitable for extrusion from a syringe in the form of a liquid or paste. The development is aimed at the possibility of home production of medicines and household chemicals in remote areas of residence.
Student project OpenReflex resulted in a design for an analog SLR camera suitable for 3D printing.
Clothing
3D printing is gaining ground in the fashion world as couturiers use printers to experiment with swimwear, shoes and dresses. Commercial applications include rapid prototyping and 3D printing of professional athletic shoes - the Vapor Laser Talon for soccer players and New Balance for track and field athletes.
3D bioprinting
EBM titanium medical implants
3D printing is currently being researched by biotech companies and academic institutions. The research is aimed at exploring the possibility of using inkjet/drip 3D printing in tissue engineering to create artificial organs. The technology is based on the application of layers of living cells on a gel substrate or sugar matrix, with a gradual layer-by-layer build-up to create three-dimensional structures, including vascular systems. The first 3D tissue printing production system based on NovoGen bioprinting technology was introduced in 2009year. A number of terms are used to describe this research area: organ printing, bioprinting, computer tissue engineering, etc.
One of the pioneers of 3D printing, research company Organovo, conducts laboratory research and develops the production of functional 3D human tissue samples for use in medical and therapeutic research. For bioprinting, the company uses a NovoGen MMX 3D printer. Organovo believes that bioprinting will speed up the testing of new medicines before clinical trials, saving time and money invested in drug development. In the long term, Organovo hopes to adapt bioprinting technology for graft and surgical applications.
3D printing of implants and medical devices
3D printing is used to create implants and devices used in medicine. Successful surgeries include examples such as titanium pelvic and jaw implants and plastic tracheal splints. The most widespread use of 3D printing is expected in the production of hearing aids and dentistry. In March 2014, Swansea surgeons used 3D printing to reconstruct the face of a motorcyclist who was seriously injured in a road accident.
3D printing services
Some companies offer online 3D printing services available to individuals and industrial companies. The customer is required to upload a 3D design to the site, after which the model is printed using industrial installations. The finished product is either delivered to the customer or subject to pickup.
Exploring new applications
3D printing makes it possible to create fully functional metal products, including weapons.
Future applications of 3D printing may include the creation of open source scientific equipment for use in open laboratories and other scientific applications - fossil reconstruction in paleontology, the creation of duplicates of priceless archaeological artifacts, the reconstruction of bones and body parts for forensic analysis, the reconstruction of heavily damaged evidence collected from crime scenes. The technology is also being considered for application in construction.
In 2005, academic journals began to publish materials on the possibility of using 3D printing technologies in art. In 2007, the Wall Street Journal and Time magazine included 3D design in their list of the 100 most significant achievements of the year. The Victoria and Albert Museum at the London Design Festival in 2011 presented an exhibition by Murray Moss entitled "Industrial Revolution 2.0: how the material world materializes again", dedicated to 3D printing technologies.
In 2012, a University of Glasgow pilot project showed that 3D printing could be used to produce chemical compounds, including hitherto unknown ones. The project printed chemical storage vessels into which “chemical ink” was injected using additive machines and then reacted. The viability of the technology was proven by the production of new compounds, but a specific practical application was not pursued during the experiment. Cornell Creative Machines has confirmed the feasibility of creating food products using hydrocolloid 3D printing. Professor Leroy Cronin of the University of Glasgow has suggested using "chemical ink" to print medicines.
The use of 3D scanning technologies makes it possible to create replicas of real objects without the use of casting methods, which are expensive, difficult to perform and can have a destructive effect in cases of precious and fragile objects of cultural heritage.
An additional example of 3D printing technologies being developed is the use of additive manufacturing in construction. This could make it possible to accelerate the pace of construction while reducing costs. In particular, the possibility of using technology to build space colonies is being considered. For example, the Sinterhab project aims to explore the possibility of additive manufacturing of lunar bases using lunar regolith as the main building material. Instead of using binding materials, the possibility of microwave sintering of regolith into solid building blocks is being considered.
Additive manufacturing allows you to create waveguides, sleeves and bends in terahertz devices. The high geometric complexity of such products could not be achieved by traditional production methods. A commercially available professional EDEN 260V setup was used to create structures with a resolution of 100 microns. The printed structures were galvanized with gold to create a terahertz plasmonic apparatus.
China has allocated nearly $500 million. for the development of 10 national institutes for the development of 3D printing technologies. In 2013, Chinese scientists began printing living cartilage, liver and kidney tissue using specialized 3D bioprinters. Researchers at Hangzhou Dianqi University have even developed their own 3D bioprinter for this challenging task, dubbed Regenovo. One of Regenovo's developers, Xu Mingeng, said it takes less than an hour for the printer to produce a small sample of liver tissue or a four to five inch sample of ear cartilage. Xu predicts the emergence of the first full-fledged printed artificial organs within the next 10-20 years. That same year, researchers at the Belgian Hasselt University successfully printed a new jaw for an 83-year-old woman. After the implant is implanted, the patient can chew, talk and breathe normally.
In Bahrain, sandstone-like 3D printing has created unique structures to support coral growth and restore damaged reefs. These structures have a more natural shape than previously used structures and do not have the acidity of concrete.
Intellectual property
Section of liver tissue printed by Organovo, which is working to improve 3D printing technology for the production of artificial organs
3D printing has been around for decades, and many aspects of the technology are subject to patents, copyrights, and trademark protection. However, from a legal point of view, it is not entirely clear how intellectual property protection laws will be applied in practice if 3D printers become widely used.
distribution and will be used in the household production of goods for personal use, non-commercial use or for sale.
Any of the protective measures may negatively affect the distribution of designs used in 3D printing or the sale of printed products. The use of protected technologies may require the permission of the owner, which in turn will require the payment of royalties.
Patents cover certain processes, devices, and materials. The duration of patents varies from country to country.
Often, copyright extends to the expression of ideas in the form of material objects and lasts for the life of the author, plus 70 years. Thus, if someone creates a statue and obtains copyright, it will be illegal to distribute designs for printing of an identical or similar statue.
Influence of 3D printing
Additive manufacturing requires manufacturing companies to be flexible and continually improve on available technologies in order to remain competitive. Advocates of additive manufacturing predict that the opposition between 3D printing and globalization will escalate as home production displaces trade in goods between consumers and large manufacturers. In reality, the integration of additive technologies into commercial production serves as a complement to traditional subtractive methods, rather than a complete replacement for the latter.
Space exploration
In 2010, work began on the application of 3D printing in zero gravity and low gravity. The main goal is to create hand tools and more complex devices "as needed" instead of using valuable cargo volume and fuel to deliver finished products to orbit.
Even NASA is interested in 3D printing
At the same time, NASA is conducting joint tests with Made in Space to assess the potential of 3D printing to reduce the cost and increase the efficiency of space exploration. Nasa's additive-manufactured rocket parts were successfully tested in July 2013, with two fuel injectors performing on par with conventionally produced parts during operational tests subjecting the parts to temperatures of around 3,300°C and high pressure levels. It is noteworthy that NASA is preparing to launch a 3D printer into space: the agency is going to demonstrate the possibility of creating spare parts directly in orbit, instead of expensive transportation from the ground.
Social change
The topic of social and cultural change as a result of the introduction of commercially available additive technologies has been discussed by writers and sociologists since the 1950s. One of the most interesting assumptions was the possible blurring of boundaries between everyday life and workplaces as a result of the massive introduction of 3D printers into the home. It also points to the ease of transferring digital designs, which, in combination with local production, will help reduce the need for global transportation. Finally, copyright protection may change to reflect the ease of additive manufacturing of many products.
Firearms
In 2012, US company Defense Distributed released plans to create a "design of a functional plastic weapon that could be downloaded and played by anyone with access to a 3D printer." Defense Distributed has developed a 3D printed version of the receiver for the AR-15 rifle, capable of withstanding more than 650 shots, and a 30-round magazine for the M-16 rifle.