Translucent 3d printer filament
Find Translucent PLA Filament Collections – Atomic Filament
Clear / Natural PLA Filament " NO YELLOW HUE"
18 reviews$ 2999
Starry Night Translucent v3 PLA
12 reviews$ 2999
Aqua Gemstone Translucent PLA
20 reviews$ 2999
Table Top Ball Bearing Spool Holder
10 reviews$ 999
Golden Blood Diamond Translucent PLA
21 reviews$ 3299
Gemstone Ruby Red Translucent PLA
18 reviews$ 2999
Emerald Green Gemstone Translucent PLA
14 reviews$ 2999
Translucent Neon Green PLA - UV REACTIVE
18 reviews$ 2999
Translucent Sapphire Blue PLA Filament
15 reviews$ 2999
Magigoo 3D Print Bed Adhesive
13 reviews$ 1995
Sold Out - Click and signup to be notified when available
Amethyst Violet Gemstone Translucent PLA
5 reviews$ 2999
Rose Gold Metallic Translucent PLA
18 reviews$ 3199
Translucent Smoke Black PLA
14 reviews$ 2999
Tropical Sea Iridescent Translucent PLA
10 reviews$ 2999
Galactic Blue Translucent Iridescent PLA
7 reviews$ 3199
Translucent Bright Orange PLA
5 reviews$ 2999
Golden Violet Sparkle Translucent PLA
5 reviews$ 3299
Sold Out - Click and signup to be notified when available
Indigo Golden Sparkle v2 Translucent PLA
3 reviews$ 3249
Translucent Neon Yellow PLA - UV REACTIVE
1 review$ 2999
Pearlescent Translucent Neon Green PLA - UV REACTIVE
7 reviews$ 3299
Translucent Neon Hot Pink PLA - UV REACTIVE
7 reviews$ 2999
Atomic Filament Brand Shirt
3 reviews$ 2495
Shamrock Sparkle PLA
$ 3299
Illusion Cherry Iridescent PLA Filament
1 review$ 2999
Galactic Purple Translucent Iridescent PLA
$ 3199
Translucent Midnight Blue PLA
$ 2999
Pearlescent Translucent Neon Yellow PLA - UV REACTIVE
$ 3299
Which is the Best Clear 3d Filament - Ultimate Guide
Everyone goes through various struggles when choosing the clear filament for the first time. There are several types of clear filament on the list.
So if you have trouble making your decision, you are just getting the start, or you need to test all the material – don’t worry.
You are in the right place. Here are so many plastic materials could be used in 3d printer. The most commonly used clear or transparent 3D printer filaments are PLA, PMMA, PETG, PET, Clear ABS, Polycarbonate, and TPU. Let’sLet’s talk about the positives, negatives, and best printing tips one by one.
The natural PLA resin is not clear. It has a very faint yellow tinge. If you compared with clear PLA filament from different manufacturers, there will be a slight difference. The tip is the process temperature. If the temp setting is higher, PLA resin could be perfect recrystallization. Then the filament will be more transparent.
The transparency is different from the resin manufacturer. There are two manufacturers for PLA raw resin. One is NatureWorks, the other is Hisun, We have made opacity tests with 4032D, 4043D(from Naturelwork), and 190(from Hisun), The opacity of 190 is much better than 4032D and 4043D.
Liking ABS, PLA is a commonly used filament in 3d printing. It is biodegradable and has excellent properties. Translucent PLA filament is one of the easiest to print clearly and get good results. To get the smooth finish of the surface, sanded is needed after printed. The part is close to the clear after filed.
Choose the right sandpaper is essential. This depends on the layer height in the setting. Thicker layers need courser sandpaper. Then use more delicate and finer grits, sanding in a circular motion each time (this bit is crucial because you’re trying to remove all surface imperfections). Start at the start, maybe 800 grit, and upwards in 200 increments from there. Finish with 3000 or higher grit to get a smooth finish.
The nature of abs is not transparent. Clear abs are the particular type of abs material. The short name is MBS. Other additives will add to make it clear.
Clear abs filament cannot print as clear as the material. It needs to be post-print finished with Acetone vapor smoothing.
PETG is a durable clear 3D filament with excellent layer adhesion (almost unbreakable) and less shrinkage than other filaments; it’s great for 3D printing clear, big stuff that won’t break under pressure. It is odorless when printing and often produces clear, smooth finishes. Meanwhile, PETG has abs material’s flexibility and PLA’s strength.
PETG can’t smooth with acetone pour, but it can sand. Compared with PLA sanding, PETG printed object is smoother, which means that you need to use higher grit.
PMMA is the most transparent material so far. It has high strength and impact resistance.
PMMA is commonly used to replace glass in a particular application, such as cellphone screen and sunshine glass. The opacity of pmma is about 92%, much more than other clear plastic.
Polycarbonate
Polycarbonate is an extremely durable and optically transparent 3D printing filament that should print in a warm environment. Its durability can be bent repeatedly without cracking, making it great for creating all sorts of hipster jewelry.
But seriously, Polycarbonate (PC) is an immensely underrated material to print. It finishes with a nice glossy sheen to it. It needs a very hot extruder to print it usually, and if you’re looking for translucent results, we’d recommend going even hotter still (300 C+).
A great advantage with PC is that it can smooth with acetone like ABS to bring out more apparent results.
TPU is the only flexible material used for clear parts. It has good elongation and flexibility. Due to this property, Tpu is commonly used in bracelets and use wine and charge wine.
About the Tpu filament, printer settings are different from other materials. The extruder structures are different, and the printing speed is slower. For the details, we will write on the next page.
Summary
PETG is your first choice for clear filament. It has suitable property and is nicely finished. Meanwhile, if you need flexible material, TPU has the advantage.
Need Any Services? Contact Us Now!
How to use a 3D printer in everyday life — experiments with Inno3D Printer D1 – Blog Imena.
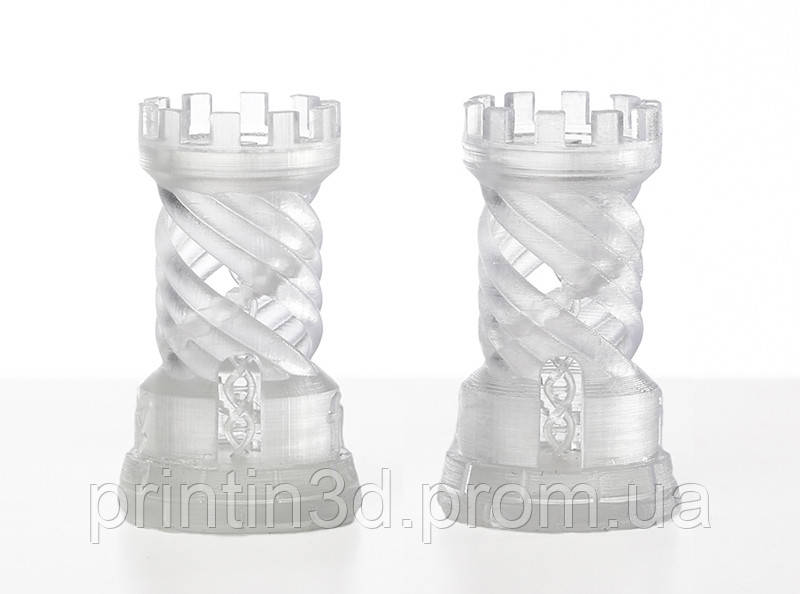
For a long time only specialized companies that felt the need to quickly create prototypes of finished products or produce small batches of products could afford 3D printers. Creating one-of-a-kind products using 3D printing, despite the high cost of 3D printers, is in many cases much cheaper than using expensive molds or molds, or using tool machines.
In recent years, the cost of 3D printers has fallen significantly, which has attracted the attention of ordinary consumers. Manufacturers are diligently stimulating this demand by showing their devices at various exhibitions and conferences. True, the demonstration of the possibilities of three-dimensional printing is reduced to the creation of various artsy knick-knacks. But is it possible to make a 3D printer useful in everyday life and what is needed for this? The Imena.ua Blog editors conducted their own experiment using a budget device Inno3D Printer D1 and high quality consumables Verbatim PLA Filament .
A bit about technologies
Before moving on to the practice of using 3D printers in everyday life, let's list the most common technologies today. For three-dimensional printing (the second name is “rapid prototyping”), various methods and materials are used, but any of them is based on the principle of layer-by-layer build-up of a solid model 0004 .
Developments in the field of rapid prototyping were carried out in the 1980s. However, 3D printers became widely commercialized only in the early 2010s. This was due to the expiration of a number of patents associated with this sharp decrease in the cost of devices, the popularization of technology among the masses and the emergence of relatively affordable and high-quality consumables.
Today, several technologies are widely used at once to create 3D models:
- Stereolithography (SLA). The initial product is a liquid photopolymer to which a special hardener is added.
In its normal state, the material remains liquid, but under the influence of ultraviolet light, it polymerizes and becomes solid.
- Selective laser sintering . The technology is similar to SLA, but instead of a liquid, a powder with a particle size of 50-100 microns is used. The laser beam sinters the next layer, causing it to harden. The advantage of this method is the various starting materials, for example, metal, plastic, ceramics, glass, special wax.
- Multi Jet Modeling (MJM) . Here, by analogy with conventional inkjet printing, the material is fed through small nozzles located on the print head. Plastics, photopolymers, special wax, as well as materials for medical implants can be used as materials for MJM printers. The use of a photopolymer requires the illumination of the printed layer with a UV lamp in order to cure it.
- Laminated Object Manufacturing (LOM) .
Thin sheets of material are cut with a laser beam or a special blade according to a pattern corresponding to a given layer, and then glued together. Not only plastic, but even paper, ceramics or metal can be used to create 3D models.
However, the main reason for the significant reduction in the cost of 3D printers was the invention of layer-by-layer fusing technology - Fused Deposition Modeling (FDM). It is also known as Fusion Filament Manufacturing - Fused Filament Fabrication . It is this method that is most common and accessible to end users today, not least due to the emergence of DIY kits, that allow you to independently and quite cheaply assemble a 3D printer.
Sample DIY 3D printer. By the way, the plastic filament spool is printed on another 3D printer
The essence of the FDM method is melting the plastic filament in a special print head - extruder - which squeezes liquid material through a nozzle and applies it in layers to the desired areas of the product. The smaller the nozzle diameter, the thinner the printed layers will be, and the more accurately the shape of the finished object will match the digital model.
Uses ABS and PLA as a consumable. The first is made from oil, is opaque, easily dyed in different colors. Among its advantages - low cost and rigidity (higher than PLA), because the product retains its shape under heavy loads. ABS requires a reliable heating of the 3D printer platform, the temperature regime of the extruder is 210-270°. The main disadvantage of ABS is its sensitivity to UV rays and precipitation.
In turn, PLA is environmentally friendly polylactide (PLA), which is also used for the production of disposable tableware and medical products. PLA is made from corn and sugar cane. This material is easily degradable in an open environment and is safe for humans , so it is more popular. In addition, the printer does not produce the unpleasant “scorched plastic” odor during operation. There is a drawback: PLA products degrade over time, their average life is about 3-4 years at an ambient temperature of about 25°C.
PLA plastic is an environmentally friendly polylactide (PLA) made from corn and sugar cane. This material easily decomposes in an open environment and is safe for humans
Among the disadvantages of FDM technology: low print speed (however, this is a common drawback for all 3D printing devices) and relatively large layer thickness - about 0.1 mm , which leads to a noticeable roughness/layering of the surface of the product.
In addition, sometimes there are difficulties with fixing the model on the desktop, because the first layer, which serves as a foundation for all the others, , must be securely “glued” to the surface of the platform . To solve this problem, manufacturers apply a special coating to the desktop, and also supply it with a heating system. However, sometimes the model still comes off the table during the printing process, which leads to an irreparable marriage.
Consumables
The market situation for 3D printing consumables resembles the market for conventional printers: there are " original consumables " from famous manufacturers and there are cheaper "compatible" products from noname vendors.
3D printers consume plastic filament in two standard diameters: 1.75 and 3mm . The required diameter is determined by the printer specification, and significant deviations from the standard diameter can lead to difficulties in the operation of the printer . The plastic comes in rolls and is sold by weight. PLA is hygroscopic and during storage requires compliance with the humidity regime, otherwise material delamination may begin, which will lead to defects in the manufacture of the model.
For each media type, the operating temperature must be known to which the media must be heated in the printhead. These values will not necessarily be the same for all "consumables" made from the same material. Ideally, the vendor should indicate the optimal temperatures on the label of the coil or in the instructions for use. If there are no such data, they have to be selected experimentally.
Optimum operating temperature of Verbatim plastic is indicated on the label
Verbatim is one of the most reputed manufacturers of high quality polylactic acid plastic . According to the vendor, the thread has a low flammability. In addition, an important advantage is that a heated print platform is not required. Optimum operating temperature is indicated on the label - 200 to 220°C .
Verbatim offers PLA filament in various colors
PLA filament is supplied wound on a spool and packed in a box, which contains special material for moisture absorption . Measurement of the thread diameter in several samples of plastic confirmed the claimed 1.75 mm to within a few hundredths of . Diameter dimensional stability ensures the most uniform fiber structure for optimum quality. The hand bend test also showed good results: the plastic did not break.
Translucent PLA filament for glass-like printing
Inno3D Printer D1 - Affordable 3D printer
For our experiment, we chose the Inno3D Printer D1 - one of the most affordable 3D printers. The device works according to technology of layer-by-layer deposition , its cost is slightly more than 1 thousand euros.
Externally, the Inno3D Printer D1 resembles devices that enthusiasts assemble by hand. There is no protective cover here, the printer has an open design. The lower part of the apparatus is a box made of sheet metal, which contains touch screen control , miniUSB connector, SD card slot and servo to move the worktable along the Y axis. The extruder moves along the X and Z axes thanks to two vertical guides and a horizontal guide connecting them. The spool of plastic thread is attached to the side on three rollers.
The Inno3D Printer D1 features an open design (top view). On the left is a spool with PLA thread, which is fed through the sleeve to the extruder (on the right)
To fix the model on the desktop, special paper is glued to its surface, it is on it that the first layer is laid. It should be noted that this paper can be used repeatedly until it starts to bulge or fray.
Inno3D Printer D1 allows you to print several unrelated objects
The lack of a common protective cover, obviously, negatively affects the performance of the device. The fact is that a 3D printer is a fairly precise mechanism that should ensure that the extruder moves in increments of approximately 0.1 mm along any of the axes. Since all guide tubes are covered with machine oil, and at the same time they are not protected from external influences, dust, dirt, and abrasive can accumulate on them over time. To prevent jamming, the guide elements will have to be cleaned and lubricated from time to time. Better yet, make a homemade protective cover.
3D printing is a long process. It takes about an hour to print a 30 mm high hollow cylinder
The printer allows you to print from a computer via a miniUSB port or from an SD memory card. In the first case, the process runs autonomously from the PC, and in the second case, the computer must work all the time , while is printing. Before work, it is necessary to carry out the procedure of auto-testing and auto-calibration, which can take about 15-20 minutes. These procedures are launched using commands on the touch screen.
To prepare the STL file for printing, use the special software application inno 3 D printer D 1 that comes with the printer. With it, you can change the size and location of the model, its orientation on the desktop. By the way, the printer allows you to print several separate figures at the same time, but you need to place them at a sufficient distance from each other on the desktop. In addition, it is necessary to perform the Build procedure, which carries out the final preparation for printing, separately for each shape.
The inno3D printer D1 application shows the approximate time it will take to print the model. As testing has shown, usually the estimated time is significantly overestimated, especially if the process has just started. But the closer to the finish line, the more accurately the application shows the time it takes to complete the print.
The inno3D printer D1 application shows the approximate time it will take to print the model
The Print button of the application starts the printing process, with the same button, if necessary, you can pause it. It is very important to have enough printing supplies on the spool. If there are not enough of them, then the process of printing the model will be interrupted, since it will not be possible to load the “consumables” right during the process and then print the started figure. It is worth noting that the printer cannot determine that the consumables have run out, or another problem has occurred due to which the plastic filament is no longer supplied. That is, the device continues to “simulate” the printing process, although no more melted plastic comes out of the extruder nozzle.
inno3D printer D1 cannot detect that the consumables have run out and the filament is no longer supplied. It is logical to assume that a layer of 0.3 mm will allow you to print a model much faster, especially since precision printing with a layer of 0.12 mm is not always required. But the problem is that when choosing a layer of 0.3 mm, the threads do not stick together. That is, to obtain a solid three-dimensional model, the user has only one option - 0.12 mm .
In general , the printing process 3 D is quite long , for example, printing a thin-walled cylinder 30 mm high takes about an hour. Larger models can print all day long. The consumption of plastic thread is about 10 cm in 3 minutes.
"Flea market" of finished 3D models. Software for creating your own products
There are three ways to get a virtual 3D model. The first and most accessible - download a ready-made model from one of the specialized Internet portals , which will obviously be just a beautiful trifle, but in some cases, it is possible that it can somehow come in handy on the farm. For example, on the 3Dtoday.ru website, after registration, you can download many ready-made models, both for a fee and for free.
The second way is to create a digital model using 3 D – scan of the finished product. This approach is very effective, but due to the high cost of 3D scanners, it is available only to professional designers.
If you need to print the product according to your own requirements, for practical tasks you will need D -model creation software . Among the easiest to learn and at the same time with good functionality, we can recommend Autodesk 123D and Tinkercad , these are CAD systems in the browser from the Autodesk vendor that do not require installation on a hard drive. Alternatives include 3DTIN, also an in-browser editor with similar functionality to Tinkercad, and Google SketchUp, a fairly simple system for beginners to master 3D graphics from the Internet giant.
If the capabilities of free systems are not enough, we note that professional designers use Autodesk Inventor, Autodesk 3D max, Solidworks, CATIA to create models
Tinkercad is a free and easy-to-learn editor in the browser for creating 3D models
When choosing software, you need to make sure that the application is able to save the file in STL format (all the above applications support STL). It is this format that is used to store three-dimensional models of objects. At its core, STL is a list of triangular faces that describe the surface of the model, and their normals.
3D printing for home use. Own experience
In the process of testing, we set two quite everyday tasks. First, print out two bushings for attaching furniture accessories; secondly, print a special fastening sleeve for the Braun blender to replace the broken one. In the first case, the solution to the problem was dictated by the fact that unique bushings were required for fastening, analogues of which could hardly be found in stores. In the second case, we were guided by the usual desire to save money. Replacing a plastic clutch for a blender in a service center cost about UAH 450, while a brand new blender cost about UAH 850. According to calculations, 3D printing of such a coupling would cost an order of magnitude cheaper.
To create virtual models, a popular editor in the browser Tinkercad was chosen. At the first start, you need to register, after which all created models will be automatically saved in your account. The program is free, easy to learn and quite suitable for creating simple designs .
One of the important advantages of creating structures using a 3D printer is the so-called “right to make mistakes”. That is, if you created a three-dimensional model, printed it out and it didn’t fit, it’s okay, you can always change the parameters of the virtual structure and print it again. Of course, time and consumables will be spent, however, several attempts will certainly achieve the desired result.
One of the plastic sleeves created in a few minutes in Tinkercad and printed on a 3D printer solid . In fact, a model printed on a 3D printer is a kind of “layer cake”, and if the layers were not welded well enough, then the model will have low strength. However, in our test, the plastic product with a thickness of 5 mm was so strong that it was difficult to break without the use of any tools. At the same time, a plastic sheet with a thickness of 1-1.5 mm turned out to be very flexible, not at all rigid. Let's add that the press was made at a temperature of 220 °C.
This unusual vase took about 8 hours to print. The free digital model was downloaded from one of the Internet sites dedicated to 3D technology. Top underprinted - out of PLA filament
By the way, if you have some design experience, you can create and print, for example, a cover for a smartphone, but it will be a little thicker than the factory one, since with a standard thickness of PLA plastic provides insufficient strength.
Rules for constructing 3D models
When designing your own 3D models, please adhere to the following rules.
Minimum overhang. The 3D printer can print vertical elements with ease, but each overhanging element needs a support structure. Let's say you're printing a miniature model of a house with a pitched roof. There will be no problems with printing the foundation and walls, but to recreate the roof, you will need to design support. After the end of the printing process, the support is removed with a sharp knife. Without support, it is allowed to print walls that have tilt angle max. 70° .
Flat base . To get a quality result, the printed model must be securely held on the printer table . If it peels off (and this happens), then you are guaranteed to get a marriage at the exit.
Dimensional limitation . Any printer has limitations on the maximum allowable dimensions of the printed model. If you need to print a product that is larger than these dimensions, it is necessary in the CAD system split into parts to print them separately. Subsequently, these parts can be glued together. To do this, it is recommended to immediately provide for in the design of the connection of the "comb", "thorn" or "dovetail" type.
Summary. The Future of 3D Printers
About two years ago, Cisco Chief Futurist Dave Evans predicted that 3D printers would be able to print anything, even food and clothing . In addition, bioprinters have already appeared that print the 3D structure of organs for stem cell transplantation. Further division, growth and modification of cells ensures the final formation of the object. By the way, back in 2012, one of the scientists working on the creation of this technology printed out a kidney. Moreover, the technology for printing bicycles, turboprop engines, etc. has already been developed. Last year, using a special super-large 3D printer, it was possible to print a two-story house in just 3 hours. Developments are already underway for the construction of multi-storey buildings.
According to forecasts, by 2020 the cost of devices will decrease so much that any family can afford them (although we are talking about an American family). And the 3D printer will become the same essential accessory at home as a microwave oven or a washing machine.
3D printed dentures
What are the realities of today? The use of 3D printers in everyday life is not yet very justified. Yes, if you have design skills, you can create a virtual three-dimensional model in one of the CAD editors and then print it in reality. The advantage of this approach is that it is possible to0003 create a unique product for your own needs in a single copy. The disadvantage is that PLA plastic does not always provide the required strength. In addition, with intensive use outdoors, PLA plastic begins to decompose after a couple of years. Well, let's see how true this is. But most likely, in a few years, new 3D printing technologies will appear that will bring us even closer to the future predicted in this area by futurologists.
Specifications Inno3D Printer D1
- Print technology: Fused deposition modeling (FDM/FFF)
- Number of printheads: 1
- Nozzle diameter: 0.4 mm
- Construction area: 140 x 140 x 150 mm
- Layer thickness: 0.13 – 0.3 mm
- Display: LCD touch screen
- Print media: PLA
- Thread diameter: 1.
75 mm
- Interfaces: USB, SD card slot
- File Format: STL
- Printer dimensions: 39 x 36 x 54 cm
- Weight: 10 kg
#3D printing #3D printer #3D scanner #Inno3D Printer D1 #Verbatim #Verbatim PLA Filament #useful services #test #experiments
PLA plastic for 3D printer from CREOZONE
Greetings to all visitors to the site 3dtoday !
A small test of Chinese plastic CREOZONE PLA Clear (transparent)
Branded plastic, declared as a competitor to domestic premium manufacturers.
Periodically I order plastic from Ali, and the main problem is the cost of delivery. As a rule, orders with a large weight also have a large shipping cost. Often buying offline is cheaper precisely because of the delivery.
I recently found a new store (and the store is really new - they just entered the market) with free delivery of plastic, including from a warehouse in the Russian Federation.
Prices are quite reasonable, especially for WOOD/NYLON/CARBON/PETG.
ABS/PLA and other WOOD/TPU types available
If anything, WOOD is a plastic with inclusions of wood and with a wood texture, for printing imitation of wooden crafts. Usually it is required to install a nozzle slightly larger than the standard one (0.6mm...0.8mm...1.0mm).
TPU - flexible plastic (Flex type), flexible parts can be printed.
Branded packaging, thick polyethylene vacuum-packed coil, silica gel - as expected
Characteristics:
Brand: CREOZONE
Diameter: 1.75mm
Net weight: 1kg
Gross weight: 1.21
Type: PLA
Color: transparent (Clear)
Claimed bar diameter accuracy: PLA: ± 0.03mm stable fluidity (no plugs in the hot end)
Available colors:
PLA: Black, White, Blue, Red, Green, Grey, Yellow, Clear
ABS: Black, White, Clear, Red
TPU: Black
Wood: Wood
Also available in NYLON/CARBON/PETG.
Print temperatures: PLA: 190°C - 210°C
Heated bed allowed up to 50°-60°
I printed on a cold bed (I have adhesive tape)
postal package
Inside the box is packed in pimply polyethylene
Branded cardboard packaging. Manufacturer and plastic information present
Vacuum-packed spool inside the box, sealed with silica gel
Plastic weight on spool 1.2 kg
PLA plastic marking. Recommendations for temperature are indicated
Before printing, I estimated the diameter of the bar: 1.75 ± fractions of a mm, my caliper does not show this to me anymore, I need a micrometer.
Dancing between 1.75 and 1.74 mm. I think the print itself will show here. Declared accuracy ± 0.03 mm
The bar itself is transparent. Reminds me of light guides.
If anything - pieces of the bar can be used as light guides for equipment (from LEDs to panels (plus it is quite flexible (does not break, bends).
Installed on a stand (green BF nearby)
Well, I immediately launched a test print of a fish.
Specifications: Temperature 205°, nozzle 0.4, layer 0.2, infill 20%, speed 50, two perimeters.
Fish, after being removed from the table. If you carefully peel off the tape (without undue zeal, as you can break the locks) - the toys are flexible, or rather, the joints “work”.
Slightly larger photo
The photo shows that the layers are even. The plastic fits well. I think if you print with 1 perimeter, then there will be a generally translucent uniform wall
Printed out a crown for a child
The photo shows traces of a retract when moving. The plastic turned out to be a little watery due to the lack of dye additives (I remind you, this is Clear, that is, transparent / clean). I reduce the temperature to 200 ° (you can set it to 190 .... 195 °).
Slightly increase the retract
Photo of the crown (slightly removed the “hair”)
There is one more princess in the house)))
Then I continue the puppet theme, shoes for Cinderella (Model is scaled to Cinderella).
On Cinderella
Now it's not a pity to lose a shoe, like in a fairy tale)))) and let the prince look for it later))) without supports
After gluing
Let's take advantage of the main advantage of plastic - translucency. A flashlight comes to mind
You can make a children's night light))))
Conclusions : plastic is good.